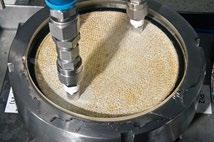
54 minute read
Papeles Técnicos y casos de estudio
procedimientos de limpieza que incluyan mecanismos complementarios pueden proporcionar sin duda una mayor eficacia. En este sentido, existen métodos alternativos para la recuperación de membranas como campos electromagnéticos [6], ósmosis directa a altas salinidades [7], introducción de aire comprimido [8] y combinaciones de limpiezas químicas e hidrodinámicas [9]. De todos estos métodos, la utilización de aire durante las limpiezas resulta ser una de las posibilidades más atractivas, ya que proporcionaría una “agitación” del ensuciamiento que sin duda favorecería su eliminación de forma mucho más efectiva y sin suponer grandes cambios en la configuración de la planta. Aunque esta técnica se puede utilizar en membranas de OI, la mayoría de trabajos en los que se han aplicado estas alternativas lo han hecho con membranas de ultrafiltración (UF). Cuando se utiliza aire comprimido en las membranas de ultrafiltración, las burbujas se expanden y colapsan en las inmediaciones de la superficie de la membrana y se genera un flujo que es capaz de eliminar partículas de la superficie. En la superficie de las membranas de OI, la fina capa de poliamida que las compone se puede dañar con más facilidad y el uso del aire comprimido no es recomendable. Por otro lado, ya se ha comprobado en algunos estudios que la simple introducción de aire para la eliminación de ensuciamientos puede presentar problemas asociados a la velocidad con que se introducen las burbujas y el tamaño de las mismas [10]. El objetivo de este trabajo es presentar los resultados obtenidos en los estudios realizados para desarrollar una tecnología de limpieza que combina la eficacia de limpiadores multifuncionales con aire, aplicándolo de la forma más efectiva posible sin provocar daños en la membrana y sin suponer un gasto de energía adicional en la planta.
2. METODOLOGÍA
Advertisement
Para estudiar el efecto del aire en la limpieza de membranas, se realizaron estudios en células de flujo con una ventana de policarbonato que permitía comprobar la efectividad de la limpieza durante el proceso (ver figura 1). Además, se utilizó una planta piloto que consiste en uno y tres tubos de presión, un tanque de limpieza y un sistema de limpieza (figura 2). Ambos sistemas fueron utilizados para estudiar el efecto de la tecnología de limpieza Genairclean en membranas nuevas y membranas con diferentes ensuciamientos. La descripción en detalle de esta metodología experimental puede encontrarse en otros trabajos publicados y presentados en otras conferencias [1, 2 y 3].
Figura 1: Banco de pruebas de láminas planas con ventana

Figura 2: Planta piloto con sistema CIP
Los elementos principales que fue necesario caracterizar durante este estudio fueron:
2.1. Generador de microburbujas Al comienzo de los estudios se introducía aire en el sistema utilizando un generador especial de microburbujas basado en el efecto venturi. En la actualidad hemos encontrado que es suficiente con el aire aportado durante la recirculación del agua, especialmente en el punto que el rechazo vuelve al tanque de limpieza. Para poder optimizar la limpieza utilizando aire, es preferible utilizar microburbujas [13]. En la siguiente tabla se incluye una descripción de los distintos tamaños de burbujas. Las microburbujas solo pueden obtenerse utilizando productos de limpieza que minimicen la coalescencia de las micro, mino y midi-burbujas en burbujas más grandes.
Descripción Tamaño Producción
Nanoburbujas 0.5-5µm Ultrasonidos, presión Microburbujas 5-50µm Ultrasonidos, presión, venturi, productos químicos Miniburbujas 50-100µm Venturi, productos químicos Midiburbujas 100-500µm Venturi, productos químicos
Tabla 1 : Tamaño de burbujas y método de producción
Se estudiaron diferentes generadores de burbujas e inyectores de aire para crear el tamaño de burbujas y distribución óptima para las limpiezas. Tomando imágenes durante la generación de las burbujas a través de la pantalla de policarbonato de la célula de flujo se comprobó que la más efectiva es la que se muestra en la siguiente figura 3. Para conseguir que el sistema sea dinámico, las burbujas tienen que poder circular por la superficie de la membrana y el material espaciador. La distribución de tamaños óptima se consigue cuando se obtienen del orden de 4 a 6 mini/midi burbujas en el espacio del vexar.
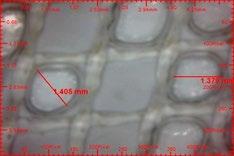
Figura 3: Burbujas generadas en una solución de hidróxido sódico
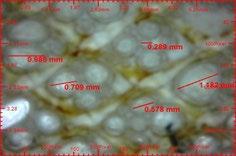
Figura 3: Burbujas generadas en una solución de Genesol 704 Los generadores de burbujas se construyeron utilizando tubos de diferentes tamaños, que permitían controlar el tamaño de las burbujas de forma más exacta. Los experimentos demostraron que las limpiezas con burbujas realizadas en presencia de limpiadores convencionales proporcionaban burbujas grandes e inconsistentes, lo que además provoca paradas de caudal debido a bloqueos por aire en la línea de alimentación 2.2. Agentes de limpieza específicos Para conseguir el efecto deseado con la introducción de aire en los sistemas de ósmosis inversa, fue necesario formular productos de limpieza específicos. Estos productos deben contener suficientes componentes para que se produzcan múltiples mecanismos de limpieza: - Agentes químicos comunes en los productos de limpieza: detergentes, agentes quelantes y tensioactivos. - Componentes que aporten alta fuerza iónica para que pueda tener lugar Ósmosis directa durante la limpieza - Agente efervescente: para conseguir la efervescencia gaseosa que permita obtener burbujas pero que a la vez evite la coalescencia de las mini y midi burbujas. Durante los ensayos realizados para desarrollar la tecnología Genairclean, se pudo comprobar que la conjunción de estos productos con el generador de microburbujas tiene un efecto muy importante en el tamaño de las burbujas. En las siguientes figuras se puede comprobar la formación de burbujas en una solución de hidróxido sódico (figura 4) y con el producto Genesol 704 (figura 5).
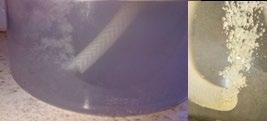
Figura 5: Burbujas de aire producidas en una solución de Genesol 704
A partir del generador de aire seleccionado (Genairator) y los nuevos productos formulados, se procedió a realizar los ensayos en membranas a escala laboratorio, en planta piloto y finalmente aplicándolo en limpieza en una planta real.
3. PARTE EXPERIMENTAL
Como ya se ha comentado, los ensayos realizados para desarrollar la tecnología Genairclean se llevaron a cabo en elementos nuevos y con distintos ensuciamientos utilizando tanto la célula de flujo como una planta piloto. La valoración de la efectividad de las limpiezas se realizó fundamentalmente considerando los aumentos de caudal de permeado, presión, monitorización de la turbiedad de las soluciones de limpieza y análisis de la superficie de las membranas antes y después de las limpiezas.
3.1. Membranas nuevas
Los primeros estudios se realizaron en membranas sin ensuciamiento, para determinar posibles daños en la superficie de las membranas. En la figura 6 se puede comprobar el comportamiento de la membrana Dow Filmtec BW30-LE400 en la planta piloto, y en la figura 7 se han representado gráficamente los datos de caudal de permeado y retención de sales obtenidos para varios cupones de la misma membrana obtenidos en la célula de flujo.

Figura 6: Compatibilidad del aire con membranas nuevas aplicando aire con limpiador C y limpiador D. Resultados obtenidos en planta piloto.
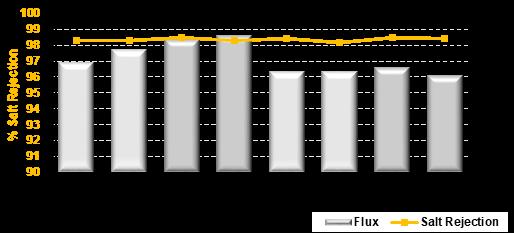
Resultados obtenidos con cupones de membrana en célula de flujo. Además de la variación del caudal de permeado y retención de sales obtenidos en los ensayos realizados con la membrana blanco BW30-LE400, la membrana fue analizada por técnicas analíticas que permitieran confirmar que el contacto de las membranas con las burbujas no produce daños en la capa de poliamida. Además de las imágenes obtenidas al microscopio electrónico (SEM-EDX), se comprobó el estado de la capa de poliamida por ATR-FTIR. En las siguientes microfografías 1 a 4 se puede comprobar el aspecto de las muestras de membrana obtenidas tras los ensayos con aire, en las que no se detectaron daños.
Por otro lado, la figura 8 incluye los espectros obtenidos por IR en las mismas muestras. Como se puede comprobar, no se detectaron cambios significativos en las bandas de poliamida de las muestras obtenidas tras el contacto con aire.
Microfotografía 1.- Membrana BW30-LE400 antes de los ensayos
Microfotografía 2.- Membrana BW30-LE-400 tras contacto con agua + aire - 4 horas Microfotografía 3.- Membrana BW30-LE-400 tras contacto con 1% limpiador Genesol 701 + aire - 4 horas
Microfotografía 4.- Membrana BW30-LE-400 tras contacto con 1% limpiador Genesol 704 + aire - 4 horas
3.2. Membranas con ensuciamiento
Una vez comprobado que el uso del aire durante las limpiezas químicas no provoca daños en la superficie de las membranas, se realizaron diferentes ensayos en cupones de membranas y en módulos completos con diferentes tipos de ensuciamiento. A continuación, se muestran solo algunos de estos ejemplos. Como ya se ha comentado anteriormente, uno de los ensuciamientos más difíciles de eliminar cuando las membranas operan durante más tiempo del deseado en presencia de ensuciamiento, es por materia coloidal. En la siguiente figura 9 se recogen los resultados obtenidos durante la limpieza realizada en diferentes cupones de membrana con este tipo de ensuciamiento. Como se puede comprobar a partir de estos resultados, el uso de aire mejora la eficacia de la limpieza con productos formulados que, por otro lado, es más eficaz que el uso de productos genéricos.
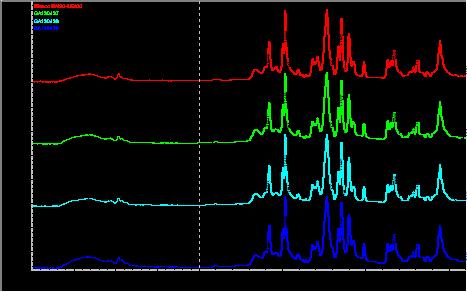
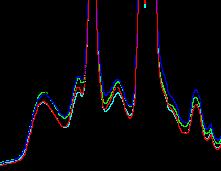
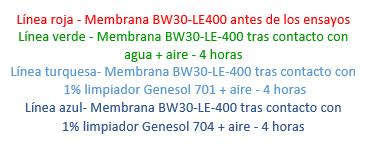
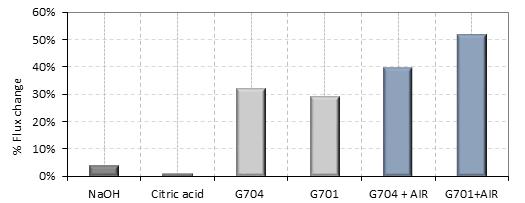
Figura 9: Resultados ensayos limpieza membrana con arcillas y hierro
Figura 10.- Superficie membrana tras 2% NaOH seguido de 2% ácido cítrico
Figura 11.- Superficie membrana tras 1% Genesol 704+aire seguido de 1% Genesol 701+aire
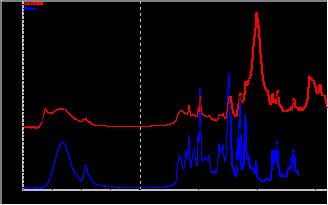
Figura 12.- Superficie membrana antes de limpieza (línea roja) comparada con membrana blanco (azul)
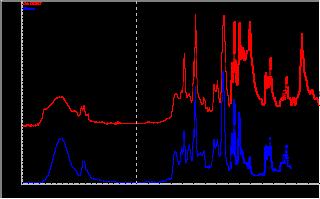
Figura 13.- Superficie membrana tras 1% Genesol 704+aire seguido de 1% Genesol 701+aire (línea roja) comparada con membrana blanco (línea azul) Aunque estas mezclas de compuestos son especialmente difíciles de eliminar, la aplicación del aire con productos especialmente formulados, puede facilitar mucho también la eliminación de biopelícula. En la siguiente figura 13 se incluyen los incrementos de caudal obtenidos para unos cupones de membrana cubiertos de biopelícula. El aumento de caudal obtenido con el Genesol 704 con aire fue tan significativo que incluso superó los resultados obtenidos en una limpieza en tres pasos con Genesol 704 y biocida.
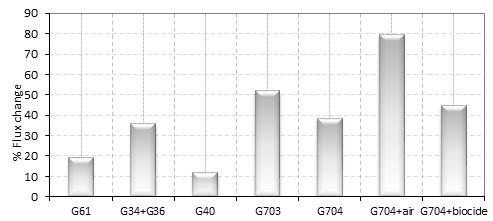
Figura 14: Resultados ensayos limpieza membrana con biopelícula
Figura 15.- Superficie membrana antes de las limpiezas
Figura 16.- Superficie membrana tras Genairclean (2 horas)
3.3. Limpieza membranas en plantas reales Para poder incluir el aire durante el proceso de limpieza en una instalación, no será necesario ningún equipo ni modificación del circuito de limpieza. Los propios ingredientes del detergente serán capaces de crear las microburbujas necesarias. En todas las plantas probadas, las ventajas más significativas frente a tratamientos convencionales fueron la reducción del tiempo de limpieza y la reducción de la frecuencia entre limpiezas. Estas ventajas son consecuencia de una eliminación del ensuciamiento más efectiva que, por otro lado, conlleva un efecto muy importante en la operación de la planta. A continuación, se recogen algunos ejemplos de instalaciones en las que se ha aplicado Genairclean como alternativa de limpieza más efectiva. Para poder comprobar mejor los cambios observados en una planta real tras la aplicación del Genairclean en este estudio se presentan los resultados obtenidos en una instalación que se encuentra ubicada en la mayor empresa productora de ensaladas en Reino Unido (16). El agua que se utiliza para el lavado de las ensaladas contiene fundamentalmente bacteria, tierra y arcillas (aluminosilicatos). Toda el agua que se utiliza en la fábrica se recicla, por lo que el agua es nuevamente contaminada con bacterias, detergentes y limpiadores. La planta de tratamiento de agua residual y reutilización incorpora un biorreactor de membranas (MBR), ultrafiltración (UF) y una planta de ósmosis inversa (OI). A continuación, se muestra una vista aérea en la que se describen los componentes del proceso de tratamiento del agua.
Tipo agua Tratamiento terciario de un efluente municipal UAE (14) Refinería Agua procedente de SAGD Oil Sands para reutilización en caldera de vapor (15) Refinería y producción de productos químicos (UK) Mezcla de agua de estuario 80-90% (con descargas de la refinería) y 10-20% de un bioreactor (15) Capacidad planta Configuración
1ST PASS 2:1:1 2ND PASS 1:1 6 Elements per pressure vessel 36 membranes total Aceites, biopelícula, aluminosilicatos, hierro
Refinería (India) (15) 5.8 MGD Four skids of 1.45 MGD each, normally 2 – 3 are in operation
Tabla 2.- Ejemplos de algunas instalaciones en las que se ha utilizado Genairclean
Tipo ensuciamiento
Aceites y grasas y detergentes.
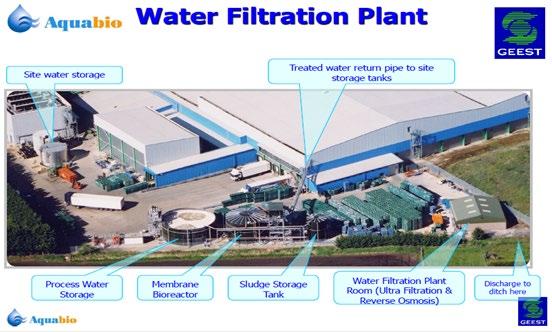
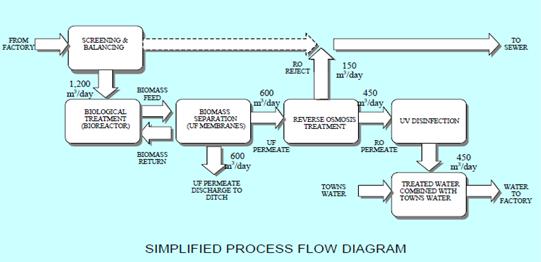
Como ya se ha comentado, la planta de tratamiento se basa en pretratamiento por AMBR, UF, OI y desinfección por ultravioleta (UV). En la fábrica se pueden llegar a producir un total de 1400 m³/día de agua residual que tienen que tratarse. Tras la OI y la desinfección por UV, hasta 450 m³/día del agua tratada alimentan un tanque de mezcla antes de entrar en la planta para el lavado de las ensaladas y el proceso. La planta de OI fue puesta en marcha en 2004 y ha sido propensa a sufrir períodos de ensuciamiento principalmente en los períodos de mayor producción. Los resultados de las autopsias realizadas en membranas y filtros de cartucho de esta instalación, pusieron de manifiesto que el ensuciamiento más habitual es principalmente orgánico y de origen microbiológico. Además, hay presencia de aluminosilicatos y, en ocasiones, ha habido problemas con depósitos de fosfato cálcico.
Las características de las membranas utilizadas en parte de este proceso son las siguientes:
UF Plant
Membrane type Berghof 66.03.i8 V X-Flow BV WFF5385
Size
2
300 x 8mm tubes, 27 m
No. of banks
3 (6 membranes in each) Mini-cleans cleaning chemicals Caustic, Hypochlorite Maintenance cleaning chemicals Ultrasil 88 -RO permeate
RO Plant
Membrane manufacturer Hydranautics Membrane type ESPA2-LD Size 8” Cartridge Filters 5 micron Number of stages 2 Number of vessels 5 (3 x 2 array) Total number of elements 30 Cleaning chemicals used Cleaner B
Las limpiezas más habituales se llevaban a cabo utilizando un biocida y limpiadores alcalinos y ácidos convencionales. Las limpiezas se realizaron cada 7 ó 14 días durante 7 años y las membranas tenían que ser reemplazadas cada 18 ó 24 meses. Para intentar disminuir la frecuencia de las limpiezas, se probó la tecnología Genairclean combinando el producto Genesol 704 con aire tal y como se describió en el diagrama 1. A continuación, la figura 17 muestra la reducción de la presión diferencial normalizada (ndP) en la etapa 1 de la planta de OI. Desde enero 2013 a junio 2013 se realizaron limpiezas convencionales de la planta. Como se puede observar, aunque se conseguía recuperar temporalmente el caudal de permeado y la presión diferencial normalizada, el ensuciamiento volvía a producirse rápidamente y era necesario realizar limpiezas con una periodicidad media de 10.5 días. El 2 de marzo del 2013, se reemplazaron 30 membranas en cinco de los tubos que componen la planta. La ndP que se consiguió inicialmente fue de 1.5 bares, pero en un único día se producto un aumento hasta 2.5 bares y, a partir de ahí, hasta 4 bares el 22 de marzo. En esta fecha, se realizó una limpieza, que no fue muy satisfactoria y tuvo que ser repetida el 26 y 31 de marzo de ese mismo mes.
A partir de ese momento, se realizaron limpiezas periódicas cada 10 días, pero tras tres meses de operación, la ndP superó los 4 bares y fue necesario volver a cambiar membranas. Fue en este momento en el que el cliente accedió a probar los limpiadores especialmente formulados para utilizar con la tecnología Genairclean, pero todavía sin aire. La primera limpieza se realizó 7 días después de la instalación, ya que la ndP durante ese período no aumentó significativamente. Trabajando con estos limpiadores, se observó una mejora bastante significativa con respecto a los limpiadores convencionales, pero, aun así, el ensuciamiento seguía produciéndose más rápidamente de lo deseable y las limpiezas tenían que realizarse cada 13 días. Finalmente, el 3 de octubre se aplicó la tecnología Genairclean en la instalación. Tras tres limpiezas, se observó una mejora en la ndP y se consiguió una media de limpiezas de 12.5 días. Después de tres meses y seis limpiezas, la ndP había sido reducida de 4.5 bares a menos de 1 bar. Desde enero a abril del 2014, la frecuencia de las limpiezas cambió de 10.5 días a 31.6 días. Recientemente, este período se ha conseguido ampliar a 50 días. El efecto tan significativo del Genairclean en la frecuencia de las limpiezas y en que la ndP no aumentara de forma tan drástica es, sin duda, que consigue una limpieza más eficaz de la superficie de las membranas. Por otro lado, los limpiadores también ayudaron a mantener la superficie más tiempo limpia. Cuando se induce aire durante las limpiezas, la superficie se mantiene más limpia, con lo cual se reduce la rugosidad de la superficie y la velocidad de ensuciamiento es menor. Además, con la eliminación de biopelícula se reduce también significativamente la población microbiana y los nutrientes que contribuyen a su crecimiento. Durante estos ensayos, no se detectó en ningún momento un empeoramiento en la retención de sales y el caudal de producción cambió de 15m³/hora a comienzos de 2013 a 24 m³/h en 2014.
4. CONCLUSIONES •La combinación de diferentes componentes de alta fuerza iónica, propiedades efervescentes y microburbujas mejora de forma muy significativa la eficacia de los métodos de limpieza convencionales, sin afectar la integridad de la membrana. •El tiempo de limpieza se ve reducido. •Al conseguir una limpieza más efectiva de la superficie de las membranas, la frecuencia de las limpiezas también se reduce.
•Al aumentar el tiempo de vida de las membranas y reducir el tiempo de limpieza, se consigue un ahorro significativo en los costes asociados tanto a paradas como a problemas de operación de la planta.
Figura 17: Resultados ensayos limpieza antes y después del uso de Genairclean
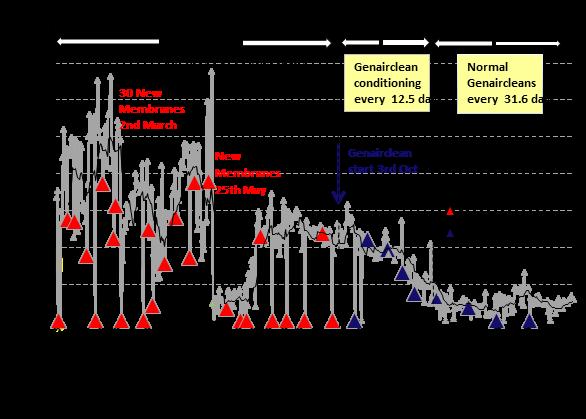
5. REFERENCIAS
1. Air bubbles enhance membrane cleaning: a future perspective R. Wilson, M. Fazel, S.Chesters The
International Desalination Association (IDA) World
Congress on Desalination and Water Reuse REF:
IDAWC/TIAN13-225 2. Autopsy results confirm safe and effective use of microbubbles for removal of ro membrane scaling and fouling M. Fazel, S.Chesters, R. Wilson, The
International Desalination Association (IDA) World
Congress on Desalination and Water Reuse REF:
IDAWC/TIAN13-140 3. RO membrane cleaning, past, present, future – innovations for improving ro plant operating efficiency
S. Chesters, M. Fazel, M. Armstrong The International
Desalination Association (IDA) World Congress on
Desalination and Water Reuse REF: IDAWC/TIAN13-204 4. N. Peña, S. Gallego, F. del Vigo, S.P. Chesters.
Evaluating impact of fouling on reverse Ósmosis membrane performance.EDS Conf Barcelona 2012 5. Wui Seng Ang, Ngai Yin Yip, Alberto Tiraferri,
Menachem Elimelech. Chemical cleaning of RO membranes fouled by wastewater effluent: Achieving higher efficiency with dual-step cleaning 6. Journal of Membrane Science 382 (2011) 100– 106 7. Ng, H. Y. and Winters, H., A Novel 16-Inch RO System for Water Reuse and Desalination. Israel Desalination
Society Annual Conference, 19-20 December, 2006. 8. Liberman, B., Methods of direct Ósmosis membrane cleaning online for high SDI feed after pretreatment,
IDA Workshop,Tampa – San Diego, 22-26/03/04. 9. Labib Mohamed E, Elgin Ernest, Lai Richard C Y,
Murawski Joseph, Tabani Yacoob, Weitzel,Steven A. 10. Pilot Scale Testing of Membrane Desalination
System Utilizing Novel Two-Phase Cleaning Technology
Desalination and Water Purification Research and
Development Program Report No. 121 May 2008 11. S.A. Avlonitis, K. Kouroumbas, N. Vlachakis, Energy consumption and membrane replacement cost for seawater RO desalination plants. Desalination Volume 157, Issues 1–3, 1 August 2003, Pages 151–8 12. P. Willems, A.J.B. Kemperman, R.G.H.
Lammertink,∗, M.Wessling, M. van Sint Annaland,
N.G. Deen, J.A.M. Kuipers,W.G.J. van der Meer Bubbles in spacers: Direct observation of bubble behavior in spacer filled membrane channels. Journal of Membrane
Science 333 (2009) 38–44 13. A. Fujiwara, S. Takagi, K. Watanabe, Y. Matsumoto.
Experimental study on the new micro-bubble generator and its application to water purification system. 4th
Proceeding ASME/JSME Honolulu US 2003. 14. RO Membrane Cleaning Using Microbubbles at 6,800m³/day Wastewater RO Plant in UAE. M Fazel, EDS Limassol – May 2014, Cyprus 2014 15. Practical examples of new ways to clean oil fouled membranes. Stephen Chesters. AMTA/CCMA Joint
Technology Transfer Workshop. Houston TX. April 26-28, 2016
16. RO – Innovations in Membrane Cleaning Stephen P. Chesters and Matthew W. Armstrong Industrial Water Treatment, July/August 2015, Volume 32, Number 4
Productos químicos de Especialidad, componentes y consumibles para el mercado de desalinización y reutilización de agua
– La nueva estructura de H2O Innovation.
Con el objetivo de crear un solo grupo con una visión común, tres líneas de negocios de H2O Innovation, PWT™, Genesys® y Piedmont se unieron en julio de 2022 para formar una línea de negocios única dedicada a productos químicos, componentes y consumibles. Estos negocios respaldan la base global de clientes de la compañía mediante la entrega de equipos, consumibles y piezas de repuesto que se centran en la optimización de sistemas de tratamiento de aguas, efluentes y reúso. Ya sea que los clientes estén buscando acoplamientos ranurados o carcasas de filtros de cartucho de Piedmont, la línea completa de productos químicos de especialidad para membranas de Genesys y PWT, nuestro equipo siempre está listo para ayudar. Este nuevo grupo está compuesto por un equipo de ventas unificado y global, así como equipos técnicos y de ejecución unidos, lo que resultará en un apoyo aún mayor de la red global de distribuidores de H2O Innovation, una mejor atención al cliente y una mayor satisfacción. La combinación también permitirá que salgan a la luz más innovaciones disruptivas, en línea con los estándares ESG (Environmental, Social & Governance) requeridos por los clientes, y que la empresa tenga una oferta única en los mercados de desalinización y reúso de agua.
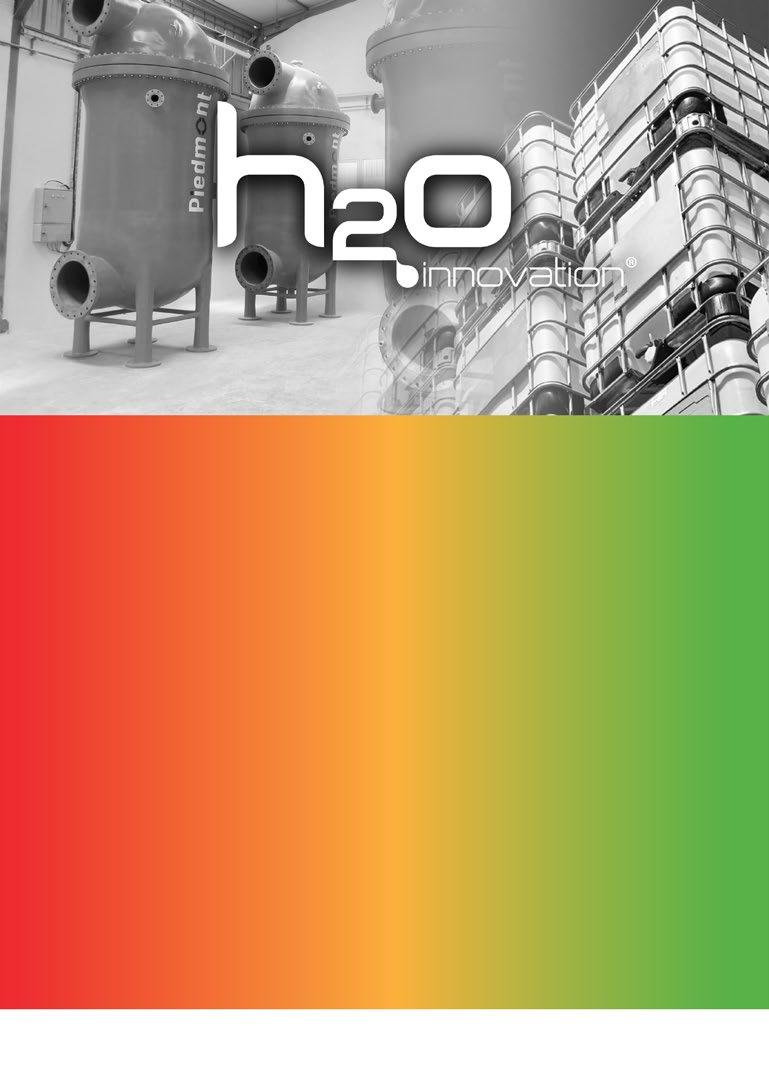
El Tamaño Importa
Resinas de intercambio iónico en Hidrometalurgia:
Son hechas de perlas poliméricas diminutas, la mayoría de ellas con menos de un milímetro de diámetro. Las resinas de intercambio iónico son indispensables en el tratamiento de aguas de procesos. Por décadas, ellas han probado ser invaluables en los procesos de desalinización, así como para suavización total o parcial de agua potable y de procesos, agua residual desafiante, recuperación de materiales reusables, y absorción de sustancias orgánicas. La marca Lewatit de LANXESS comprende numerosos tipos diseñados para un gran rango de aplicaciones. Unas resinas de intercambio iónico de especialidad constan de grupos funcionales quelantes que selectivamente se enlazan ellos mismos como pinzas a iones metálicos específicos, juegan un papel vital en varias aplicaciones como tratamiento de aguas de proceso. Esta capacidad ofrece también un amplio potencial en el campo de la hidrometalurgia – tales como para procesamiento de minerales, refinería y extracción de iones metálicos de soluciones acuosas, “Este tipo de resinas pueden ser utilizadas para extracción de litio, níquel y cobalto, requeridos para incrementar la producción de baterías de Litio para avanzar en electro movilidad, y, a su vez, en la transición de energía”, dice el Dr. Dirk Steinhilber, Gerente de Marketing Técnico para Liquid Purification Technologies (LPT) en LANXESS Deutschland GmbH.
Tamaño de Partícula Ajustable Para obtener metales “ultra puros” – especialmente a través de separación electrolítica – por mecanismos de hidrometalurgia, los iones que pudiesen interferir en la extracción tienen que ser removidos a niveles mínimos de trazas. Esto presenta especiales requerimientos relativos a selectividad, capacidad y velocidad de intercambio. El tamaño de las perlas de resina juega un papel clave aquí. EN LANXESS, el tamaño de partícula de las resinas monodispersas – aquellas con un tamaño de perla uniforme – es ajustado con alta precisión por mecanismos de atomización continua a través de un plato perforado en el proceso de producción. En una suspensión acuosa que contiene las gotas de monómero de tamaño uniforme, las perlas de resina son formadas mediante polimerización (Figura 1). Este método permite la creación de perlas en diferentes tamaños, de manera flexible y reproducible – un prerrequisito vital para la producción a gran escala. Las resinas macroporosas con una estructura similar a la de una esponja y una gran área superficial interior son usualmente las que se aplican en hidrometalurgia. Las perlas poliméricas de tipo estándar miden entre 0.5 mm y 0.7 mm. Adicional al tipo de grupo funcional en el polímero, su idoneidad para una tarea de separación específica depende de su número y rango de otras propiedades y características. Los parámetros de proceso como pH, temperatura y caudal también influyen en el desempeño de la separación. Los procesos de intercambio iónico usualmente toman lugar en columnas simples, o en una serie de columnas que se llenan con la resina y a través de las cuales las soluciones a ser tratadas fluyen. Los procesos de “Resina en pulpa” (RIP) han sido desarrollados también, en donde las resina en la solución o suspensión a ser tratadas se suspenden y luego se separan previo a su regeneración.
Pequeñas perlas con un gran efecto Las perlas de resina pequeñas con un diámetro de apenas 0.3 mm a 0.4 mm – también conocidas como resinas MDS (por su sigla en inglés Mono-Disperse Small) – exhiben propiedades muy diferentes y características a las perlas de resina de tamaño estándar. Gracias a su tamaño más pequeño y, unas rutas más cortas de difusión, exhiben cinéticas más rápidas durante el intercambio iónico y la regeneración. “No solo es por su alta densidad de empaque lo que las hace ideales para separación cromatográfica, sino que ellas también tienen una utilización de la capacidad de intercambio mayor, lo que implica, más larga vida de servicio con menor requerimiento de productos químicos para regeneración” dice Steinhilber. Sin embargo, la alta densidad de empaque también resulta en una caída de presión más alta, un factor que tiene que ser considerado cuando se diseña la planta. Una comparación del desempeño de carga (Figura 2) de una resina quelante, del tipo MDS, de ácido iminodiacético (IDA por su sigla en Inglés) (a la izquierda) con iones de cobre (azul) muestra claras diferencias con respecto a la resina monodispersa (MD, en medio) y la heterodispersa (HD, a la derecha) con un más amplio rango de distribución de tamaño de partícula. Adicional a la retención más alta, las resinas MDS exhiben una exacta y precisa zona de adsorción definida. Esto previene la ruptura o saturación prematura observada especialmente con resinas HD. Las propiedades benéficas de las resinas MDS pueden ser aprovechadas por varias operaciones prácticas como la purificación de salmuera de litio. Este es un paso vital en el proceso de producción de carbonato de litio ultra puro, una materia prima crucial para la manufactura de baterías de litio de alta calidad. Incluso en presencia de altas cantidades de cloruro de litio y cloruro de sodio (61.1
g/l / 60 g/l), la resina – Lewatit MDS TP 208 en este caso – ayuda a remover casi la totalidad de trazas de calcio y magnesio desde un nivel inicial de 10 ppm. De particular interés, las resinas MDS reducen el calcio residual significativamente a niveles de trazas menores a 1 ppb. La salmuera de litio ultrapura obtenida de esta manera, es necesaria principalmente para la electrólisis con el fin de proteger las celdas de membrana. Adicionalmente, la capacidad operativa excede a la de la resina equivalente de tipo MD hasta en un 87% (Figura 3). Durante la extracción industrial de cobalto – otro metal esencial en la producción de baterías de litio – las resinas MDS pueden ser capaces de desempeñarse muy bien en esta tarea de separación. Con Lewatit MDS TP 220, que contiene grupos de bispicolilamina, alrededor de 300 ppm de níquel pueden ser completamente removidos de una solución salina concentrada de cobalto en un ambiente altamente ácido (Figura 4).
Grande, más grande, la más grande para procesos “resina en pulpa” El antes mencionado proceso RIP, por sus siglas en inglés, impone requerimientos diferentes. Una suspensión de lodo mineral que contiene iones, es mezclada con las perlas de resina. Luego de un periodo, la resina absorbe los iones y se separa nuevamente. Para incrementar la eficiencia, se posicionan reactores múltiples en un arreglo de cascada, y la suspensión mineral es tratada con la resina de intercambio en contraflujo (Figura 5, continuo RIP). Durante este proceso, la mayoría de iones metálicos del lodo se adhieren o enlazan a la resina y pueden ser separados de esta cuando la resina es regenerada. “En el campo de hidrometalurgia, los procesos de intercambio iónico tales como estos están reemplazando a lo procesos de decantación de suspensiones en grandes tanques de agua, ya que estos no solo requieren un gran espacio, sino que también son muy exigentes en tiempo de proceso e intensivos en costo” dice Steinhilber. Para que la separación y transferencia sea lo más eficiente posible, las resinas de intercambio iónico deben de ser mecánicamente muy estables. Esto ayuda a prevenir el rompimiento prematuro de la resina durante su extracción. Una diferencia de tamaño suficiente entre la resina y las partículas del lodo mineral es también esencial para la separación eficiente. Por esta razón, LANXESS ha desarrollado dos tipos de resina Lewatit TP 209 altamente estables: Una resina monodispersa con un diámetro de partícula estándar de 0.85 mm (Lewatit TP 209 XL) y una resina heterodispersa con un tamaño de partícula promedio de 1.10 mm (± 0.1) (Lewatit TP 209 XXL). Debido a los requerimientos del proceso RIP respecto a la estabilidad mecánica y elasticidad de las perlas de resina, estas propiedades deben ser determinadas a detalle en el laboratorio de calidad. Las medidas comparativas con respecto a los productos de la competencia, revelan unos perfiles de superior desempeño tanto para los tipos XL como para la XXL. Estos fueron demostrados en un test llamado Chatillon, que determina la elasticidad de las perlas de resina mediante la deformación repetida de perlas individuales hasta que se rompen. También se prueba con una evaluación de rodillo, en el que un rodillo de metal se pasa sobre una capa de perlas de resina veinte veces (Figura 6). El número de perlas que están todavía intactas después de la prueba sirve como una medida relativa de su estabilidad y resiliencia. Las aplicaciones potenciales de procesos RIP son tantas y tan variadas como los coeficientes de selectividad de las resinas adecuadas para estos procesos. Lewatit MonoPlus TP 209 XXL ha sido utilizada en los últimos diez años en una planta de procesamiento en Kazajistán, donde el proceso se implementó para la producción de cobre. Otra planta diseñada para una separación de gran escala, de iones divalentes – principalmente níquel y cobalto – seguida de una lixiviación ácida a alta presión (HPAL por su sigla en inglés) a partir de depósitos de laterita de níquel y cobalto, está planeada en la actualidad para Australia. En el proceso, seguido a la neutralización, el hierro debe ser separado mediante precipitación. Una vez los iones divalentes han sido aislados por mecanismos de cRIP, una mezcla cruda de sulfato de níquel y cobalto se obtiene del lixiviado (Figura 7). Esta mezcla es separada mediante la extracción líquida. Luego – nuevamente en un proceso de intercambio iónico – las trazas de impurezas son removidas. El proceso de cristalización finalmente resulta en hidratos de sulfato de níquel y cobalto puros, que pueden ser usados para recuperar los metales mediante un proceso electroquímico. “Este proceso, ilustra el enorme potencial que hay para aplicaciones de intercambio iónico en procesos de hidrometalurgia” dice Steinhilber.
Aproximadamente 6,400 caracteres – incluido espacios. Autor:
Dr. Thomas Schmidt, Oficina Editorial para Wirtschaft, Wissenschaft y Technik (WW+T), Solingen
Figuras (Fuente: LANXESS)
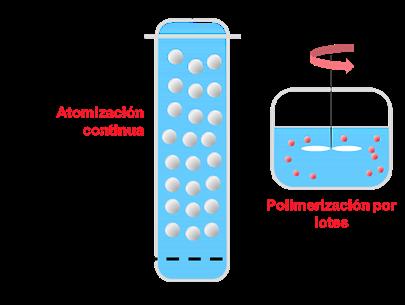
Figura 1. Producción en dos etapas para las resinas de intercambio iónico monodispersas a través de atomización continua seguida de una polimerización por lotes. (Fuente: LANXESS) Figura 2. Desempeño de carga con iones de cobre a idénticas condiciones de reacción para resinas de intercambio iónico MDS, MD y HD.

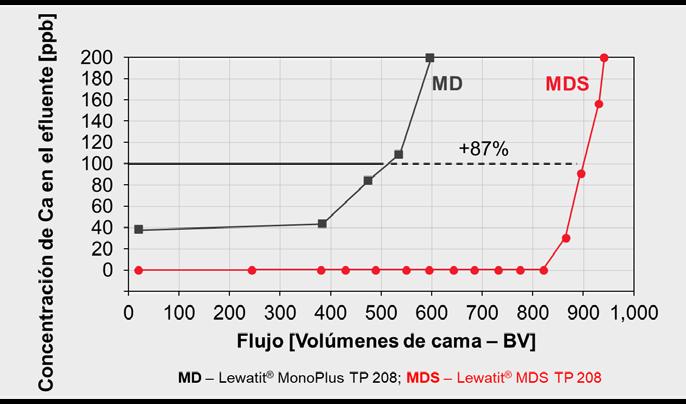
Figura 3. Comparación de resinas MDS y MD para suavización de salmuera de litio (60 °C; flujo: 10 BV/h; punto de quiebre a 100 ppb Ca).
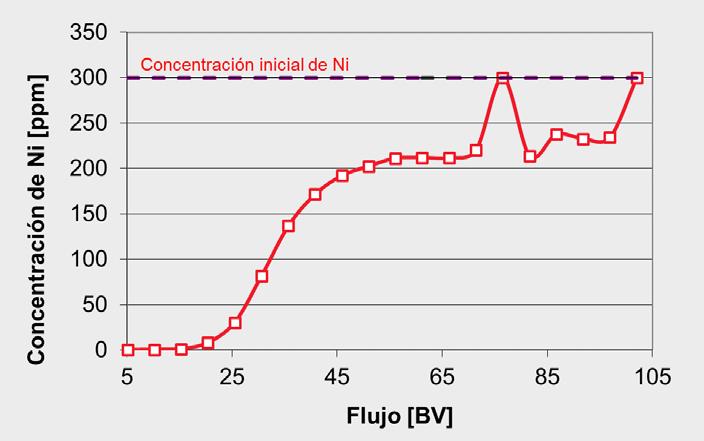
Figura 4. Remoción de iones de niquel de una disolución de cobalto (aprox. 37 g/L Co) con Lewatit MDS TP 220 (60 °C; flujo: 5 BV/h; pH 2)
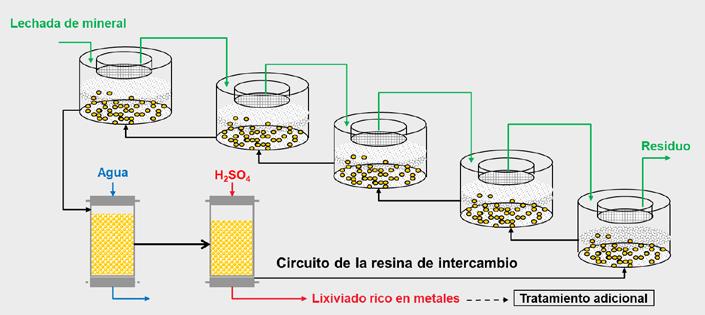
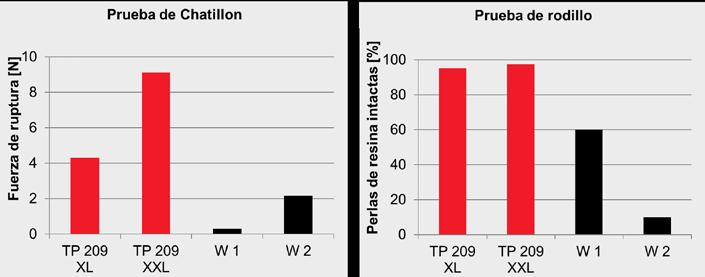
Figura 6. Resiliencia mecánica para Lewatit TP 209 XL y XXL comparada con dos productos de la competencia (W 1/W 2) en Prueba de Chatillon y Prueba de rodillo. (Análisis: LANXESS)
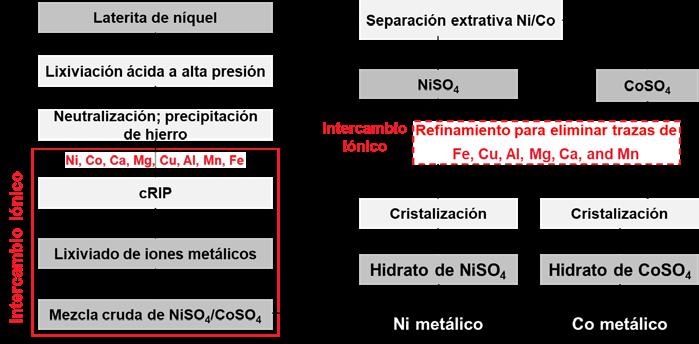
Figura 7. Proceso esquemático cRIP para obtener fracción de Ni/Co seguido de HPAL.
Desarrollo de una solución de sistema de monitoreo digital - la importancia del enfoque de doble estrategia
Autores: Mateus Nicoladelli de Oliveira1, Thiago Barbosa2
1WEG Digital Solutions, Desarrollo de negocios digitales, Brasil, nicoladelli@weg.net 2WEG International Division, Gerente Desarrollo de Agua y Saneamiento, América Latina, thiagob@weg.net
Introducción En la última década, WEG ha trabajado en el desarrollo de soluciones para la Industria 4.0, tanto para uso interno, en sus líneas de producción, como para ofrecer al mercado. Esta estrategia dual ha generado ganancias en eficiencia operativa y, más recientemente, ha incrementado el negocio de la empresa. Este trabajo pretende mostrar un caso con un motor eléctrico de 150kW de detección de fallas en rodamientos con algoritmo de inteligencia artificial y la reducción del TCO (Total Cost of Ownership) de una planta industrial.
I. La importancia de la estrategia dual para la industria 4.0 La gestión de activos y equipos está pasando por una importante revolución por causa de las soluciones digitales industriales, que tiene como base la computación en nube, el uso de sensores inteligentes inalámbricos y la adopción de metodologías de mantenimiento 4.0. Si bien anteriormente se han monitoreado activos grandes y críticos, la nueva solución técnica permite el monitoreo inteligente de toda la flota de equipos a un costo asequible, elevando el nivel de gestión y mantenimiento de activos. El resultado final se observa en el aumento de la disponibilidad de máquinas y plantas, reducción de averías inesperadas y reducción del costo operativo de la flota, es decir, la reducción del TCO. Como productor altamente verticalizado con una amplia, extensa y completa gama de productos y soluciones, la estrategia dual también permitió a WEG desarrollar el Motion Fleet Management y su familia de productos de soluciones digitales aprovechando su propia experiencia y lanzando un producto maduro a sus clientes. en todo el mundo. La fábrica piloto de la Industria 4.0 de WEG es la fábrica de cables, en la sede de Jaraguá do Sul, Santa Catarina, Brasil. El proyecto en esta fábrica se inició en 2017 y las principales acciones de la empresa fueron: - Instalación del sistema WEG Shop Floor Management (WSFM) en los centros de producción; - Adopción de la metodología WEG Manufacturing System (WMS) para reducción de pérdidas; - Uso de mantenimiento 4.0 e instalación del sensor WEG
Motor Scan en los activos; - Monitoreo en línea y gestión de activos con Motion Fleet
Management (MFM).
Actualmente, el MFM aplicado en la fábrica de cables cuenta con 348 activos monitoreados, brindando información precisa para el mantenimiento con base en la condición operativa del activo (conditionbased maintenance), lo cual es fundamental para el mantenimiento predictivo. Los principales activos monitoreados por el MFM son: motores, variadores de frecuencia, arrancadores suaves, reductores, motorreductores, compresores, bombas, ventiladores, entre otros. La Figura 1 muestra el monitoreo de cuatro motores eléctricos (a) y la aplicación del portal para la recolección autónoma de datos (b).
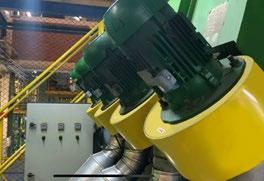
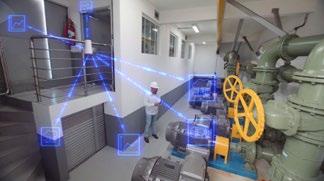
Figura 1: monitoreo online de flotas con tecnología 4.0. (a) Motores eléctricos utilizando sensores WEG Motor Scan (b) Gateway para la recolección de datos autónomos
II. Monitoreo online con solución en la nube El MFM tiene como base la computación en la nube, operando sobre la plataforma WEGnology, por lo que puede ser utilizado en cualquier local del mundo. El MFM permite comprobar el estado de funcionamiento de motores y generadores de baja y media tensión, VFDs y soft-starters (drives) de baja y media tensión, sistemas de arranque con relés inteligentes, reductores, motorreductores, compresores y otros activos instalados en cualquier tipo de industria o instalaciones. Mediante la recopilación periódica de datos y el procesamiento avanzado de datos, tanto en el borde (Edge) como en la nube, se obtienen valiosos conocimientos. Así, es posible establecer planes de mantenimiento predictivo teniendo en cuenta el estado de funcionamiento de la flota (mantenimiento con base en condiciones). El MFM adopta el concepto de capas (Figura 2), y la primera capa incluye los activos industriales que pueden ser monitoreados con el MFM. La segunda capa está destinada a la digitalización de activos y la conectividad en la nube a través de WEG Scans y Gateways. Ambos son capas de hardware. La tercera es una capa de software, y es la aplicación principal: la capa de Gestión. En esta capa, los datos se almacenan durante 1 año y se presentan a través de gráficos, informes, notificaciones y otros medios. Algunas de las características de esta capa son: dashboard para análisis de vibraciones, módulo para gestión de mantenimiento con características de CMMS (sistema de gestión de mantenimiento computarizado), backup de parámetros de la unidad, aplicación celular de notificación y gestión (WEG Digital Notify APP), procesamiento de datos optimizado en el borde (Edge) y en la nube, vista de eventos de activos en la línea de tiempo, etc. Los módulos Specialist y Exchange pertenecen a la cuarta capa. El módulo Specialist tiene funciones avanzadas para cada activo monitoreado por el MFM, lo que permite diagnósticos autónomos de fallas y análisis de consumo de energía mediante análisis avanzado de datos con algoritmos de inteligencia artificial basados en la experiencia de WEG. El módulo Exchange se utiliza para la integración (a través de la API REST) con sistemas de terceros.
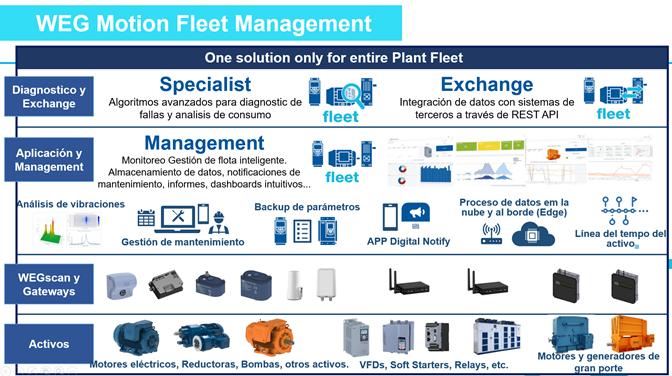
Figura 2: Concepto de capas de la solución WEG Motion Fleet Management

Figura 3: Arquitectura simplificada de la solución MFM
El MFM es una solución digital que cumple con altos estándares de ciberseguridad, asegurando que la información esté segura, ya que hace uso de estándares, mecanismos y herramientas de seguridad de vanguardia, tales como: encriptación de datos transportados y almacenados, tokens de seguridad para cada dispositivo y control y acceso segmentado, además de contar con funciones de balanceo de carga y redundancia, lo que permite que la aplicación cumpla con sus objetivos de operación y disponibilidad de información y seguridad. La solución MFM opera en la plataforma WEGnology con la siguiente arquitectura básica, Figura 3. Las autenticaciones con tokens de acceso generados por la propia aplicación se utilizan para conectar puertas de enlace, dispositivos de borde o APP móvil al MFM (Figura 4), lo que garantiza que los dispositivos que cuenten con dicho token puedan consumir y publicar datos en la solución MFM.
El hardware digital (sensores y puertas de enlace) y las soluciones de software para el monitoreo en línea se ofrecen actualmente como una solución lista para usar. Por lo tanto, el tiempo y el costo de implementación se reducen drásticamente y las ganancias se notan rápidamente. Adoptando esta tecnología, el equipo de mantenimiento de WEG reduce el número de paradas no planificadas, optimiza las acciones de reparación y agiliza la toma de decisiones. En la Figura 5 se muestra la pantalla (dashboard) de la solución en la nube MFM para la planta de cables, la cual muestra el layout de la fábrica con la posición y estado de cada activo: verde saludable, amarillo alerta y rojo nivel crítico para acciones de mantenimiento.
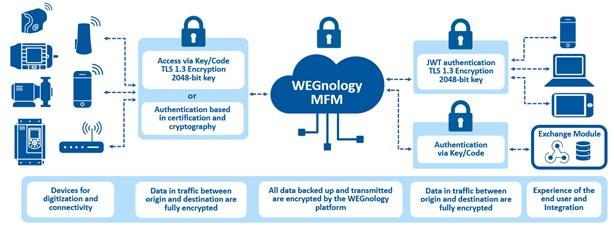

Figura 5: Visualización del dashboard de la solución MFM para la planta de WEG PFII - Fábrica de Cables
En un caso real, el equipo de mantenimiento evitó una condición de calentamiento en un motor trifásico de 1,1kW/3600RPM. En este caso, el equipo de mantenimiento recibió una notificación por correo electrónico, verificó el historial de datos (figura 6) y realizó una limpieza simple de la cubierta del ventilador.
III. Diagnóstico de fallos con inteligencia artificial Otro impulsor del desarrollo de la solución MFM es incorporar el conocimiento adquirido por la empresa durante más de 60 años fabricando equipos eléctricos y mecánicos en un módulo que proporciona un alto valor para el usuario, con el módulo Specialist. La Figura 7 muestra el flujo de trabajo básico utilizado para construir el algoritmo autónomo de diagnóstico de fallas, que requiere la interacción entre los expertos en análisis de vibraciones, detección de vibraciones (incluidos MEMS, sistemas mecánicos microelectrónicos) y ciencia de datos. En otro caso real, se logró evitar la parada inesperada de un compresor de aire de 150kW (Figura 8). En este caso, el algoritmo avanzado de análisis de datos (módulo WEG Motor Specialist) detectó la falla de un rodamiento incluso antes de que aumentaran los niveles de vibración. La Figura 9 muestra el dashboard de este módulo Specialist con dicha indicación. Hay módulos especializados para motores eléctricos,
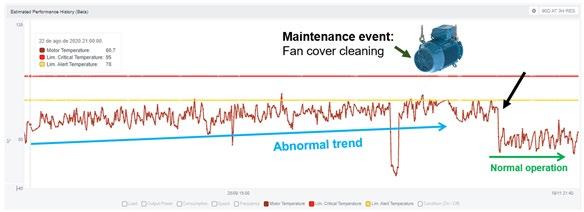
Figura 6: Caso real de exceso de temperatura y detección con Motor Scan y MFM
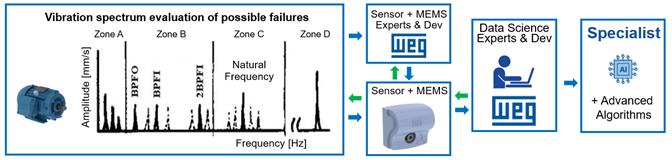
Figura 7: Flujo de trabajo básico para crear inteligencia artificial para el análisis de vibraciones
variadores de frecuencia de baja y media tensión y arrancadores suaves y cajas reductoras / motorreductores. Los módulos Specialist aplican inteligencia artificial y aprendizaje autónomo para respaldar la solución de problemas, de manera autónoma y temprana. El módulo Specialist en motores, por ejemplo, utiliza medidas de campo magnético para inferir el consumo de energía del motor y datos de vibración en los tres ejes para indicar fallas en los cojinetes, desequilibrio del motor, desalineación o vibración externa. Con esa tecnología, el equipo de mantenimiento de WEG sabe mejor qué repuestos deben solicitarse para las órdenes de servicio y cuánto tiempo durarán las actividades.
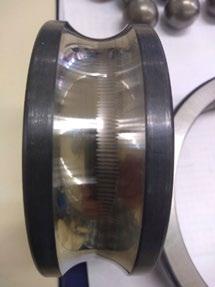
Figura 8: Caso real de monitoreo en línea y detección de fallas con WEG Motor Specialist y MFM (a) Compresor con motor WEG de 150kW (b) Detalle de la falla detectada en la pista interior del cojinete
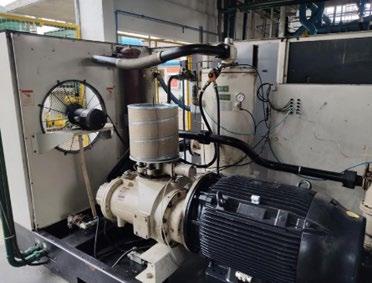
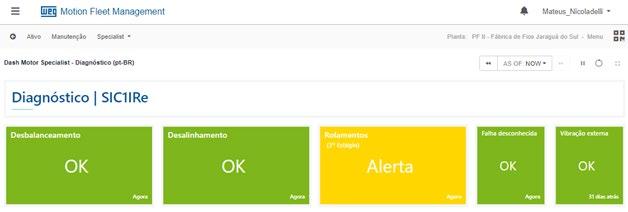
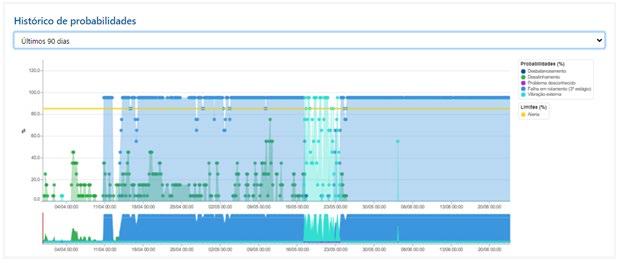
Figura 8: Caso real de monitoreo en línea y detección de fallas con WEG Motor Specialist y MFM (a) Compresor con motor WEG de 150kW (b) Detalle de la falla detectada en la pista interior del cojinete
IV. Conclusiones – ganancias reales Además de los resultados inmediatos y directos de implementar un sistema de monitoreo digital de activos mediante la reducción de interrupciones inesperadas de la producción, las modificaciones adicionales en la agenda y los procedimientos de mantenimiento permitieron reducir aún más los costos de mantenimiento, los tiempos de inactividad de la producción y aumentar la disponibilidad de la máquina. Todos los aspectos relacionados con la reducción del TCO. En un caso particular de la fábrica de cables, se programaba un mantenimiento preventivo anual. Retirar diez motores de la estructura de la máquina, promover el mantenimiento y reinstalar motores exigió una semana de agenda de mantenimiento. Con la mayor confianza que brinda la solución MFM, que permite la detección temprana de fallas, se modificó el mantenimiento preventivo anual. Actualmente, la máquina y los motores funcionan de manera continua y el mantenimiento de un motor en particular se programa solo cuando el sistema MFM identifica una tendencia o un problema futuro en el motor. El OEE (Eficacia general del equipo) es una métrica de buenas prácticas para evaluar la producción de la instalación. Proporciona una gran comprensión de las pérdidas en el proceso de fabricación al dividirlas en tres factores: disponibilidad (A), rendimiento (P) y calidad (Q). Si bien un sistema de monitoreo de activos en línea no afecta la pérdida de calidad, que está más relacionada con un correcto control de procesos, sí afecta directamente la pérdida de rendimiento e incluso la pérdida de disponibilidad. En 2018, la tecnología de punta y el control de procesos permitieron que P & Q estuviera en el rango del 98 %, un estado de clase mundial. Al implementar el sistema de gestión y monitoreo de la salud de los activos, A mejoró alrededor de un 10 % en tres años, demostrando un impacto positivo significativo. En 2020, el enfoque de monitoreo en línea y mantenimiento 4.0 evitó 49 paradas de producción no programadas, un ahorro en costos de mantenimiento del orden del 6%. Se redujo alrededor de un 10% el número de horas-hombre en órdenes de trabajo para acciones correctivas eléctricas y mecánicas, además de acciones preventivas y predictivas. La reducción de gastos de mantenimiento por hora máquina programada en el ERP de la empresa es del 23%. Con las iniciativas de Industria 4.0 en la fábrica de cables, se observó un aumento del 5% en OEE en este departamento de fabricación en particular. Esa ganancia eliminó la necesidad de invertir en nuevas líneas de producción, algo que representaría una inversión del orden de R$ 14 millones. La estrategia dual ha generado ganancias de eficiencia operativa y buenos negocios para la empresa. El uso interno de esa tecnología permite a WEG mejorar también las características y robustez del WEG Motion Fleet Management, en términos de escala y calidad del producto. Esta solución digital ha recibido mejoras continuas, tanto desde el punto de vista del hardware como del software. Dichos avances tienen como base la hoja de ruta (roadmap) estratégica del producto y en los comentarios de los clientes internos y externos, algunos de los cuales del segmento de agua y bombeo.
V. Referencias
[1] SCHUH, Günther et al. Industrie 4.0 maturity index. Managing the digital transformation of companies (Acatech Study). Munich: Herbert Utz, 2017.
Informe extracción sustentable Litio 2022
El litio es un metal liviano que no se encuentra en estado puro naturalmente, sino que se obtiene a partir de soluciones en cuerpos de salmuera dentro de salares, agua de mar, salmueras geotermales o contenido dentro de minerales estables en forma de rocas duras.
Debido a sus propiedades beneficiosas como su potencial electromagnético y sus características fundentes y catalíticas, la demanda de litio ha crecido enormemente en los últimos años a causa de, principalmente, el crecimiento del mercado de los dispositivos móviles y los vehículos eléctricos. Teniendo en cuenta el contexto actual de transición energética, es necesario que la oferta de litio crezca de manera sostenida implementando tecnologías que hagan más eficiente el proceso de obtención y atendiendo a los principales puntos críticos como el consumo de agua, la sustentabilidad de la operación y los costos asociados a la extracción responsable. El litio se extrae a partir de tres tipos de depósitos: salmueras, pegmatitas y rocas sedimentarias. En particular, los depósitos de salmuera representan alrededor del 66% de los recursos de litio a nivel mundial y se encuentran principalmente en las salinas de Chile, Argentina y Bolivia, región denominada como el triángulo del litio debido a que poseen salares con niveles de concentración altamente rentables. La composición de las salmueras varía considerablemente por lo que el tratamiento a emplear para la obtención del litio depende de la presencia de otros elementos tales como potasio, sodio, calcio, magnesio, entre otros. Las tecnologías tradicionales utilizadas para la extracción de litio de las salmueras están basadas principalmente en evaporadores naturales (Figura 1) donde se eleva la concentración de las sales haciendo que algunas como el cloruro de sodio (NaCl) y el cloruro de potasio (KCl) lleguen a saturarse y precipitar. La actualidad del mercado está impulsando a las industrias mineras a implementar soluciones de recuperación más eficientes que permitan reducir los tiempos necesarios para la obtención del producto final y que, a su vez, sean convenientes desde el punto de vista económico.
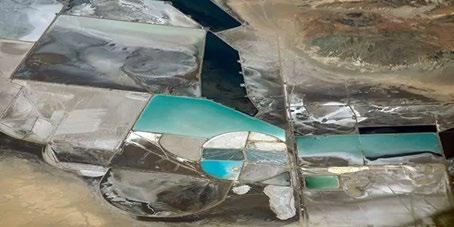
Figura 1. Piletas evaporadoras para la concentración de salmuera de Litio. Fuente: dsearls/CCby2.0
Una de las formas de procesamiento de la salmuera de litio es, vez obtenida la salmuera concentrada, someterla a una etapa de pulido (polishing) donde se purifica el producto removiendo de la solución minerales como el Hierro, Zinc, Calcio, Magnesio y Boro a partir de diferentes reacciones. La salmuera tratada ingresa a un separador líquido-sólido donde se separa el precipitado de las sales indeseadas. Luego, la solución obtenida ingresa a un reactor donde se produce la carbonatación del litio. Por último, se separa el carbonato de litio de la solución, se seca y se compacta para su empaque y almacenamiento. Los procesos mineros consumen grandes cantidades de agua y es importante considerar el reúso del recurso para contribuir al cuidado del medioambiente y, además, por el potencial beneficio económico asociado. Para dar una dimensión, se estima que se necesitan aproximadamente dos millones de litros de agua para producir una tonelada de litio por lo que el problema que se plantean los investigadores y las entidades ambientalistas es que se hace uso de un recurso natural escaso como el agua en zonas comúnmente áridas donde se realizan las extracciones. Teniendo en cuenta esto, si bien la minería del litio tiene potencial para desarrollarse y consolidarse en el mercado global, se enfrenta al gran desafío de mejorar la eficiencia y la sustentabilidad ambiental de las técnicas de extracción y de diseñar procesos innovadores que permitan optimizar el consumo de recursos como el agua y la energía involucrada. Las tecnologías que actualmente están revolucionando el proceso se basan principalmente en ósmosis inversa, nanofiltración, intercambio iónico y otros tratamientos fisicoquímicos. Estas tecnologías proveen soluciones específicas dependiendo del requerimiento de las empresas y pueden generar ventajas en términos ambientales. Dentro de las aplicaciones más comunes se encuentran la producción de agua tratada para servicios dentro del campo minero, tratamiento de efluentes o bien, aplicar distintas tecnologías dentro del procesamiento de la salmuera para reducir tiempos de producción, disminuir el consumo neto de agua o reducir el volumen de descarga. La cartera de proyectos de Fluence incluye la implementación de estas tecnologías para diversos fines entre los cuales se pueden destacar los siguientes casos: - Tratamiento de agua de pozo para producción de agua permeada por ósmosis inversa para su uso en los procesos de extracción / purificación de la salmuera de litio. - Tratamiento de salmuera de litio por nanofiltración a baja presión para la remoción selectiva de dureza (contaminantes), obteniendo una salmuera de mayor pureza. - Tratamiento de efluentes producto de la explotación minera implementando un tratamiento por ultrafiltración y ósmosis inversa, produciendo agua tratada que se utiliza como fuente de agua para el lavado de maquinaria utilizada dentro del proceso de extracción y/o actividades de riego. - Tratamiento de agua de pozo para consumo en las instalaciones implementando tecnologías de ultrafiltración y ósmosis inversa. - Concentración de salmuera de litio aplicando tecnología de ósmosis inversa de alta presión. - Remoción de dureza de salmuera de litio por intercambio iónico. - Oxidación y precipitación de hierro y arsénico en la salmuera curda. - Descarbonatación de salmuera de litio. - Plantas piloto de tecnologías de ultrafiltración, nanofiltración, ósmosis inversa, intercambio iónico y otros.

Figura 2. Equipo de ósmosis inversa montado en contenedor provisto por Fluence para la empresa Ady Resources Limited en sus instalaciones del Salar del Rincón, Salta, Argentina.
Además, dependiendo de las características del proceso, los equipos pueden diseñarse para operar dentro de contenedores de manera de facilitar el transporte, instalación y operación en los campamentos mineros. Una solución de estas características se empleó para la empresa Ady Resources Limited, donde se diseñó un sistema de ósmosis inversa dentro de un contenedor para la producción de agua permeada utilizada en el proceso productivo del carbonato de litio. Un ejemplo de aplicación de estas tecnologías es utilizar un tratamiento por ósmosis inversa para la concentración de salmuera de litio. Como se mencionó anteriormente, la concentración de las salmueras extraídas de los salares se realiza en mayor medida a partir de la evaporación del agua en piletas de gran extensión. Este proceso puede tardar de 18 a 24 meses dependiendo de las condiciones climáticas lo que implica un cuello de botella en la producción de carbonato de litio debido al tiempo necesario para el tratamiento de la salmuera. Fluence Argentina ofrece el diseño y la aplicación de tecnologías de ósmosis inversa de alta presión para la concentración de salmuera de litio. Este proceso continuo tiene el mismo objetivo que las piletas de evaporación, pero con la ventaja de reducir el tiempo involucrado en esta etapa del proceso a la vez que se obtiene agua tratada al concentrar la salmuera hasta los niveles deseados. La utilización de tecnologías de membrana para la concentración de salmuera de litio tiene asociada una gran ventaja además de reducir el tiempo de la etapa de concentración. Al producir continuamente agua tratada, la misma se puede reinyectar al salar o acondicionarse según se requiera para ser reutilizada en el proceso global ya sea como agua de servicios, lavado de maquinaria o agua de riego entre otros usos. Este aprovechamiento del recurso otorga una posición competitiva en cuanto al cuidado ambiental y el consumo de agua del proyecto. También, es posible implementar equipos de intercambio iónico para la etapa de purificación de salmuera de litio de manera de remover diferentes contaminantes y obtener la calidad de producto deseada. Un caso de estas características se implementó para Minera EXAR (Figura 3) donde fueron provistos los siguientes proyectos: - Planta de tratamiento de agua potable. - Planta piloto de intercambio iónico para procesamiento de salmuera. - Plantas de intercambio iónico para remoción de dureza, pulido de salmuera de litio y remoción de dureza de ceniza de soda. - Sistema de Ozonización.
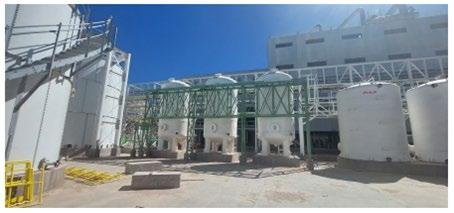
Figura 3. Lechos de intercambio iónico diseñados por Fluence para el procesamiento de salmuera en Minera EXAR.
Teniendo en cuenta que el contexto ambiental actual es el principal impulsor del mercado del litio, la sustentabilidad del proceso de extracción se considera un factor importante para el comienzo de las nuevas operaciones de minería y para la ampliación de las plantas existentes. Fluence ofrece el diseño, construcción, puesta en marcha y asistencia operativa de las diferentes tecnologías de tratamiento de agua aplicables a la minería moderna donde el ahorro del recurso hídrico es fundamental para realizar una extracción responsable y consolidarse en el mercado donde los tiempos asociados en las diferentes etapas del proceso juegan un rol importante para la producción de la planta.
Bibliografía - https://salesdejujuy.com/espanol/litio/ - https://panorama-minero.com/litio/litio-y-tecnologiacomo-obtener-mas-valor-de-las-salmueras/ - https://www.mckinsey.com/featured-insights/ destacados/la-mineria-del-litio-como-las-nuevastecnologias-de-produccion-podrian-impulsar-larevolucion-mundial-de-los-vehiculos-electricos/es - https://condorchem.com/es/blog/extraccionrecuperacion-litio/ - https://www.argentina.gob.ar/noticias/mineria-urbanay-biomineria-para-recuperacion-de-litio - https://www.fuerzaminera.com/post/argentina-todo-loque-hay-que-saber-sobre-el-litio-en-el-pa%C3%ADs - https://www.horizonteminero.com/tecnologiasplantas-tratamiento-agua/#:~:text=Las%20 tecnolog%C3%ADas%20de%20tratamiento%20 de,requisitos%20de%20cumplimiento%20en%20los - https://www.perfil.com/noticias/economia/impactoambiental-del-litio-el-uso-de-agua-dulce-y-el-desecho-deresiduos-toxicos-genera-discordia.phtml - https://es.euronews.com/green/2022/02/03/loscampos-de-litio-en-sudamerica-revelan-el-lado-oscurode-nuestro-futuro-verde
Victoria Vasini Gerente de Procesos, Sudamérica vvasini@fluencecorp.com
El Boro es un mineral que se encuentra de forma natural en el ambiente. Puede causar efectos nocivos tanto para para los seres humanos como para el entorno dependiendo de la concentración a la que se encuentra. Por esta razón, la ley fija según el Código Alimentario Argentino un límite para la producción de agua potable de 0,5 ppm de Boro y, según la resolución 336/03 de la Provincia de Buenos Aires un límite de vuelco < 2 ppm procurando la supervivencia de todos los seres vivos y el cuidado del ambiente.
Frente a estos lineamientos AdeS (Alimentos de Soja), empresa que pertenece al grupo The Coca Cola Company, recurrió a Fluence Argentina para desarrollar una solución para tratar agua proveniente del acuífero Hipopuelche, que contiene una cantidad mayor de Boro a la permitida, para obtener agua potable. El contexto actual de la Provincia implica la necesidad de remover Boro casi indefectiblemente ya que no se habilitan más permisos de extracción del acuífero Puelche (< 0,5 ppm de B) y el agua del acuífero Hipopuelche tiene una concentración de Boro del orden de 3 ppm, siendo el límite de vuelco 2 ppm: es decir que la mera extracción de agua ya implica la necesidad de tratamiento para poder cumplir con el vuelco. Se plantearon como objetivos obtener agua con menos de 0,5 ppm de Boro apta para consumo y eliminar la masa de Boro requerida para cumplir con el límite de vuelco legal. Como se dispone de un efluente industrial con bajo contenido de Boro es posible diluir el vertido de la planta y por lo tanto no es necesario remover la totalidad del Boro. Removiendo un 50% de B en la planta diseñada se alcanza el límite de vuelco establecido por la Provincia, en la mezcla de las corrientes de descarte. Es necesario evaluar cada caso particular para determinar la cantidad de Boro a remover, ya que depende de los efluentes disponibles y de las concentraciones que presenta el agua cruda y los descartes. Se diseñó entonces una planta que incluye una primera etapa de producción de agua potable y una segunda etapa donde se tratan los efluentes producidos en la primera (con alto contenido de B). A continuación, se muestra un diagrama simplificado del sistema de tratamiento para la remoción de Boro implementado por Fluence en las instalaciones de AdeS en Pilar, Provincia de Buenos Aires. Cuenta con una capacidad de producción de 70 m³/h con < 0,2 ppm B en producto y la planta de tratamiento de Boro opera en forma Batch con una producción de 65 kg de lodo húmedo por día. Las tecnologías utilizadas incluyen: intercambio iónico, coagulación y Ultrafiltración, floculación y deshidratación de lodo.
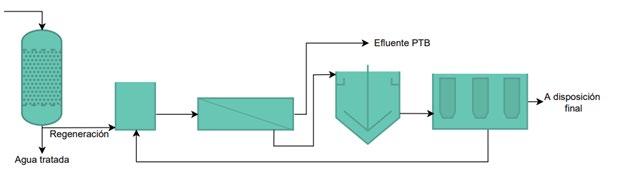
Diagrama de Proceso. 1.De izquierda a derecha, columna de intercambio iónico, tanque de recepción, Coagulación y Ultrafiltración, floculador y filtro deshidratador.

Diagrama de Proceso. 2.Mezcla de las corrientes a vuelco final con < 2 ppm de B.
El intercambio iónico se basa en la retención de iones utilizando resinas selectivas a diferentes compuestos. Consiste en la permutación del ion del grupo funcional de la resina por el ion presente en la solución, que se desea eliminar. Al saturarse la resina es necesario regenerarla, en general con ácido y base. Los químicos utilizados remueven el boro retenido en los sitios activos permitiendo restaurar el lecho para continuar con la operación. Esta tecnología permite obtener agua con una composición menor a 0,5 ppm de Boro. De cualquier manera, debido a la presencia de otras especies en mayor concentración de la permitida por el CAA, en la planta de AdeS se emplea un equipo de Ósmosis Inversa (OI) para lograr la calidad apta para consumo. El concentrado de la OI es enviado a vuelco y como posee bajo contenido de B contribuye a la dilución de la mezcla. El efluente de la regeneración es la corriente de entrada a la segunda etapa donde se elimina el boro para cumplir con el límite de vuelco establecido por la ley. Se decidió emplear técnicas de coagulación, Ultrafiltración, floculación y deshidratación de lodos para separar los sólidos de la corriente. Para facilitar la eliminación de las partículas coloides se agregan agentes coagulantes que permiten maximizar la remoción. Una de las premisas que se adoptó para reducir la inversión en la planta de tratamiento y los costos operativos fue minimizar el volumen de efluente a tratar. Se seleccionó un corte del efluente de regeneración de forma de obtener un menor volumen a tratar y la solución más concentrada en Boro que, además, es la forma más eficiente de precipitarlo. La fracción elegida esta ligada a las etapas de regeneración que efectivamente eliminan el compuesto de los sitios activos de la resina, el pasaje de ácido, y no a los de enjuague para puesta a punto de la columna ni a la conversión con soda cáustica.
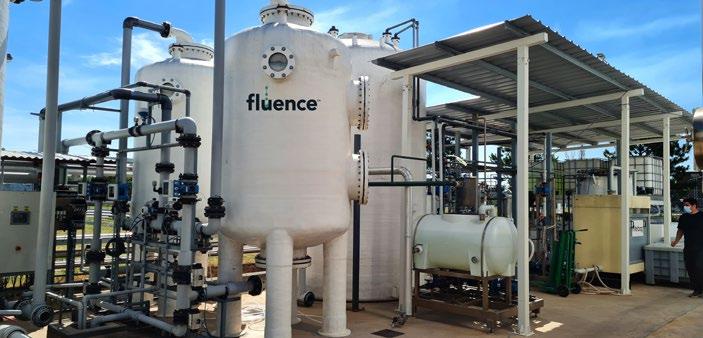
El sistema de Ultrafiltración (UF) en Cros-Flow actúa como una barrera a los sólidos en suspensión; es un proceso de separación por membranas semipermeables en el cual se obtienen dos corrientes el concentro y el permeado. Como el Boro se debe encontrar en partículas de tamaño mayor a 30 nm para ser retenido, se incorpora previo al ingreso a la UF un coagulante que permite generar sólidos suspendidos de boro para poder separarlos. Se seleccionó Policloruro de Aluminio, PAC, un coagulante ampliamente utilizado, sobre todo en la industria de tratamiento de agua. Este insumo disminuye el pH de la solución y se debe tener en cuenta que existe un óptimo para la coagulación del Boro. Por esto se incluye, previo al agregado de PAC, la dosificación de Hidróxido de Sodio para regular el pH. El concentrado de esta etapa pasa a un sedimentador donde se agrega un agente floculador para favorecer la etapa de filtrado posterior. La elección del agente se determinó por pruebas Jar test, seleccionando los químicos que mejor resultado dieron para la formación y consistencia de los flocs. El último equipo utilizado es una batería de filtros bolsa donde se separan los lodos del filtrado. Se recircula el agua filtrada al tanque de recepción para su tratamiento dado que es posible que el Boro se redisuelva. Por último los lodos son enviados a disposición final. La planta opera de forma totalmente automática y es una solución robusta para resolver una situación compleja que es que la mera extracción de agua del Acuífero disponible en la provincia de Buenos Aires, donde se radican una enorme cantidad de industrias, ya representa la contaminación de los ríos donde se vuelcan los efluentes tratados. Con esta solución, al removerse físicamente el Boro en forma sólida, se logra verter agua en los cuerpos receptores cumpliendo con los límites de vuelco. Teniendo en cuenta los resultados obtenidos en la planta instalada, la solución a la problemática planteada por el cliente fue resuelta de forma exitosa por Fluence Argentina. Se obtuvo un diseño innovador que permite cumplir con los objetivos establecidos y con los límites del Código Alimentario Argentino y de la resolución 336/03 de la Provincia de Buenos Aires. Fluence ofrece el diseño, construcción, puesta en marcha y asistencia operativa de las tecnologías de tratamiento de agua aplicables a la remoción de Boro donde el ahorro del recurso hídrico y el cuidado de los seres vivos y ambiente es fundamental. En Fluence trabajamos día a día para garantizar la gestión sostenible del recurso natural más valioso con el que contamos. El acceso a agua, saneamiento e higiene es un derecho humano con el cual nos sentimos muy comprometidos, es así que involucramos a todo nuestro equipo profesional y tecnológico en la mejora continua de las soluciones de calidad que brindamos en el tratamiento y reúso de aguas y efluentes. ¡Te invitamos a conocernos y hacernos parte de tu equipo, para seguir promoviendo juntos un futuro más sustentable!
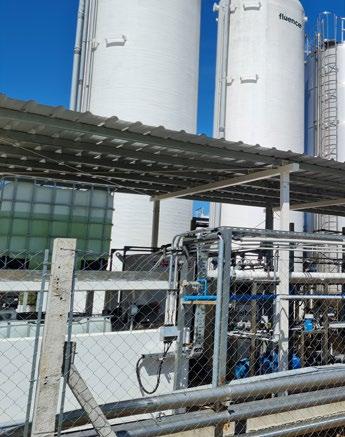
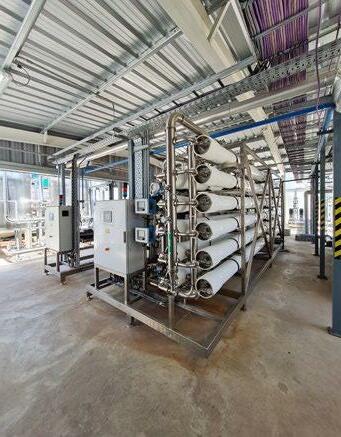
Wilo celebra 25 años de trayectoria en Latinoamérica La gala que conmemoró vigésimo quinto aniversario de la llegada de la empresa alemana a América Latina tuvo lugar en la Ciudad Autónoma de Buenos Aires en el prestigioso barrio de Puerto Madero el pasado 25 de agosto. “Con la apertura de la filial en Argentina en 1997, el Grupo Wilo, empresa socia ALADYR, sentó las bases para el desarrollo de las actividades comerciales en América Latina. Desde entonces, el Grupo Wilo ha ampliado enormemente su presencia en la región y hoy atiende a todo el continente latinoamericano con sedes en Argentina, Brasil, México, Chile, Colombia, Ecuador, República Dominicana y Cuba”, dijo Svenja Ahlburg, Directora América Latina & Directora General Wilo México, en su discurso de apertura. La recepción de los 150 invitados con presencia de ALADYR, comenzó con la puesta de sol y degustaciones al aire libre en una estructura que flota sobre el canal que atraviesa a Puerto Madero, locación ideal que representa la importancia que la empresa da al agua y saneamiento. La ceremonia tuvo como invitado especial al embajador adjunto de la República Federal de Alemania en Argentina, el Sr. Peter Neven. En su discurso destacó, entre otras cosas, la relevancia de América Latina para la economía alemana y la futura importancia estratégica de la región como socio energético europeo. A la bienvenida le sucedió un compendio de bailes típicos de los países latinoamericanos en los que tiene presencia la empresa junto a una demostración folklórica alemana, cuya puesta en escena y vestuario fueron impecables y del total agrado de los espectadores.