
60 minute read
IMPLEMENTOS AGRÍCOLAS
FMEA DE PROJETO PARA O DIAGNÓSTICO DE FALHAS DE MÁQUINAS E IMPLEMENTOS AGRÍCOLAS
Alessandro de Franceschi Vinicius Kaster Marini Leonardo Nabaes Romano
Advertisement
Introdução
A agricultura conectada impõe desafios ao projeto e ao desenvolvimento de máquinas agrícolas na implementação de recursos de inteligência, comunicação e desempenho para a evolução da produtividade. Para assegurar vantagem competitiva a partir das novas soluções, é necessário evoluir as práticas de projeto e desenvolvimento de máquinas agrícolas incluindo considerações de qualidade e confiabilidade em seus aspectos técnicos e gerenciais. Nesse contexto, as empresas da indústria brasileira de máquinas e implementos agrícolas mostram grandes disparidades: enquanto algumas exercem liderança de mercado em qualidade e inovação, outras lutam para sair da posição de retardatárias pela adoção de boas práticas de engenharia. Em serviço à implementação de práticas de engenharia capazes de servir à garantia da qualidade no desempenho das operações, este capítulo objetiva discutir o projeto de máquinas e implementos agrícolas, com foco nos aspectos de qualidade e confiabilidade, partilhando um exemplo de prática em análise e predição de falhas com a técnica FMEA. Para evitar problemas que podem fazer com que a solução de cultivo agrícola seja um fracasso de mercado, a confiabilidade – a capacidade de um produto funcionar durante a maior parte do tempo em que é necessário – é o atributo central para fornecer um produto de qualidade. Segundo DIAS et al. (2013), as práticas de tratamento de falhas estabelecem quadro de trabalho composto de estruturas e técnicas que definem as modalidades de tratamento das falhas projetadas ou testemunhadas no desempenho dos sistemas técnicos7. No contexto de operação agrícola, é possível emitir a definição de sistemas de cultivo agrícola, considerando máquinas e implementos agrícolas que incluem funções embarcadas de sensoriamento, inteligência, comunicação e controle para além das funções básicas de mecânica, de energia e de estrutura. Uma vez que as operações agrícolas são prescritas para momentos determinados dos ciclos de cultivo8, e têm seu desempenho definido em cada um desses momentos pela operação mecanizada de uma área cultivada em certo intervalo de tempo9, as ocorrências de falha em sistemas de cultivo agrícola podem causar prejuízos significativos aos processos de negócio dos cultivos. Outro aspecto importante das operações agrícolas é o reconhecimento da variabilidade das propriedades dos cultivos em relação à localização10, que determina a necessidade de soluções capazes de adaptar seu funcionamento às necessidades localizadas de tratamento dos cultivos. Dessa forma, ganham particular relevância as práticas de projeto e desenvolvimento de sistemas de cultivo agrícola para mitigar a ocorrência de falhas ao longo do ciclo de vida. Neste cenário, a utilização de técnicas de projeto com foco em confiabilidade requer informações básicas com um nível mínimo de conhecimento técnico para o fim de tratar as ocorrências de falha a partir do projeto do sistema de cultivo agrícola. Esse nível deve ser considerado com base no ciclo de vida pretendido para os sistemas técnicos e refletindo embasamento suficiente nas reais condições de operação (DIAS et al., 2013): primeiramente, considerando o entendimento das funções implementadas no sistema técnico e de como estas são implementadas em subsistemas e grupos de componentes
7 O termo ‘sistemas técnicos’ corresponde à combinação de funções e subsistemas em máquinas e equipamentos, implementados por grupos de componentes em vários domínios de especialidade, tais como mecânica, energia, estruturas, eletroeletrônica, algoritmos e interface de usuário, que executam transformações de energia, material e sinal combinadas para a satisfação de uma necessidade (HUBKA & EDER, 1992). 8 A prescrição de operações agrícolas para momentos determinados dos ciclos de cultivo determina uma característica sazonal para os sistemas de cultivo agrícola, majoritariamente operados em uso intermitente conforme sua concepção habilita à execução de um processo técnico específico para a operação (MIALHE, 1974; MARINI, 2007). 9 A operação mecanizada da área cultivada em certo intervalo de tempo determina uma característica de criticidade do tempo de operação, onde qualquer falha dos sistemas de cultivo agrícola em completar a área cultivada dentro de um tempo prescrito pode incorrer em prejuízos à produtividade dos cultivos. 10 A variabilidade das propriedades dos cultivos com relação à localização determina uma característica de adaptabilidade do sistema de cultivo agrícola mediante sensoriamento, processamento e ajuste autônomo dos parâmetros de funcionamento.
(BAXTER, 2011); e prestando atenção aos diferentes incidentes de gatilho de falha ao longo do ciclo de vida, incluindo aqueles que ocorrem sob operação intermitente (AFFONSO, 2006). Tendo em mente a temática do tratamento de falhas no projeto de sistemas de cultivo agrícola, este capítulo apresenta um exemplo em métodos sistemáticos de projeto servindo à melhoria da confiabilidade e da qualidade em máquinas e implementos agrícolas. Para este propósito, o escopo deste texto abrange uma revisão da literatura quanto ao tratamento da confiabilidade no projeto de máquinas e implementos agrícolas, um exemplo de aplicação da técnica FMEA11 – Failure Mode and Effects Analysis – sobre o projeto de um implemento agrícola, e uma discussão dos benefícios de abordagens preditivas para o projeto de máquinas agrícolas.
Análise de falhas no ciclo de vida de sistemas técnicos
A análise de falhas é um procedimento necessário para garantir a eficácia do processo de projeto, uma vez que envolve a busca de entendimento sobre as características de projeto da solução que asseguram o atendimento às expectativas de seus clientes. Segundo SCHMITT (2013), a análise de falhas é uma das maneiras de se entender o comportamento do equipamento, por exemplo: como falhou, por que falhou, quando falhou, quanto tempo operou até ocorrer a falha. BRAILE & ANDRADE (2013) afirmam que a análise de falhas permite priorizar os modos de falha que causam mais prejuízo, possibilitando indicar a melhor estratégia de manutenção para os equipamentos. Neste sentido, Pedrosa (2014) cita que a análise de falhas envolve uma forma sistemática de hierarquizar informações sobre as falhas dos produtos e processos, ajudando a conceber um sistema de prioridades para ações de melhorias, entre investimento, desenvolvimento e testes de verificação. Nesse contexto, a motivação central para o emprego de abordagens sistemáticas de tratamento de falhas é evitar comportamentos indesejados e falhas de funcionamento nas máquinas e equipamentos, de tal modo que causem incômodo, prejuízos, e danos aos usuários, aos clientes e às partes interessadas no ciclo de vida do produto. Conforme HELMAN & ANDERY (1995), entende-se por confiabilidade a probabilidade de um determinado sistema (máquina, implemento, aparelho, dispositivo etc.) desempenhar sem falhas uma missão (função) durante um período determinado. FRANCESCHI (2015) aborda o ciclo de vida dos sistemas técnicos, identificando os aspectos que guardam as causas de falhas, conforme apresentado na Figura 1. Considerando as atividades desenvolvidas durante as fases de Projeto, Produção e Uso, e os aspectos do sistema técnico nelas considerados, essa abordagem das causas de falha orienta a análise de falhas em direção à causa-raiz.
Ciclo de vida dos sistemas técnicos
Fases do ciclo de vida
Projeto
Produção
Uso
Origens das causas de falhas em sistemas técnicos
Concepção
Dimensionamento
Fabricação
Materiais
Montagem
Usuário
Ambiente Abordagem preditiva
Abordagem retrospectiva
Figura 1: Origens das causas de falhas nos sistemas técnicos – fases do ciclo de vida. Adaptado de FRANCESCHI (2015).
De acordo com ROZENFELD et al. (2006) a fase de Produção objetiva produzir produtos com as mesmas qualidades do protótipo, atendendo aos requisitos dos clientes durante o ciclo de vida do produto. Já na fase de Uso, segundo KAGUEIAMA (2012), a análise de confiabilidade e a aplicação
11 A técnica tem protocolo definido primeiramente pelo departamento de Defesa dos EUA (MIL-STD-1629A, 1978), e regulado atualmente pela Sociedade de Engenheiros Automotivos dos EUA (SAE J1739, 2009) e pela Coordenação de Normas Técnicas da Comunidade Europeia (EN 60812, 2000), respectivamente.
das técnicas de análise de falha podem ser aplicadas quando um produto oferece riscos ao meio ambiente ou à pessoa. Neste sentido, as causas de falhas na fase de Projeto, em circunstâncias reais, podem ocorrer devido a não incorporação de metas de confiabilidade ao produto (KAGUEIAMA, 2012). Uma das práticas conhecidas na literatura é a análise de falhas, cuja execução busca evitar ocorrências subsequentes de falha pela implementação de ações preventivas para alcançar os seguintes objetivos: melhorar a confiabilidade do sistema; reduzir os custos de manutenção; e, reduzir os riscos de acidentes, entre outros (AFFONSO, 2006).
Análise de falhas no processo de projeto de máquinas agrícolas
No contexto da indústria de máquinas e implementos agrícolas, tem-se o conhecimento de que muitos problemas de qualidade advêm, do emprego de práticas de engenharia baseadas em modelos informais de processos de desenvolvimento (ROMANO, 2013; BERGAMO & ROMANO, 2016). Nestes casos, a solução de máquina ou equipamento agrícola resulta de uma composição de soluções em geral existentes no mercado, sem que a concepção do sistema de cultivo agrícola seja desenvolvida completamente sob o ponto de vista do processo de projeto de produtos industriais, e sem que tenha executado os devidos procedimentos de dimensionamento e simulação funcional-geométrico-material dentro desse contexto. Esta forma de desenvolvimento, embora permita a rápida obtenção de um protótipo para testes e ou ensaios de campo, é de alto risco, pois não considera, durante a etapa de desenvolvimento do produto propriamente dita, a análise de falhas de seus sistemas, subsistemas e componentes (SSCs). Fica então o processo de verificação e correção de projetos concentrado na fase de projeto detalhado, como demonstrado a seguir. BERGAMO & ROMANO (2016) mencionam a construção do protótipo de engenharia na fase de projeto detalhado do produto, permitindo a execução de testes em laboratórios ou a campo para avaliar o desempenho do produto e a ocorrência de falhas de componentes, assim como o atendimento das necessidades dos clientes. Esses testes são essenciais para garantir a qualidade das máquinas agrícolas que entram no mercado, quando realizados como ensaios atendendo a critérios de certificação ou homologação da máquina agrícola segundo marco regulatório reconhecido. Nesse sentido, disposições de mercado (OCDE), normas técnicas internacionais (ISO, EN) e nacionais (NBR) determinam procedimentos e critérios de desempenho que constituem indicativos de qualidade para a comercialização de máquinas agrícolas12. A conquista de novos mercados para a indústria nacional de máquinas agrícolas depende de que se incluam normas e procedimentos internacionais como critérios de qualidade na realização de ensaios (CORRÊA & SCHLOSSER, 2011). Após os testes e/ou ensaios – em que é possível evidenciar modos de falha em visão retrospectiva13 –, a avaliação do protótipo pode ser feita em cada componente para identificar outros modos de falha e possíveis desgastes prematuros. Se determinado modo de falha não é mitigado durante as iterações de teste e mudança de engenharia, o usuário final fica sujeito a elevados riscos durante a operação da máquina em campo. Tais ocorrências em serviço, representam altos custos quanto à assistência técnica, a verificação da falha e as mudanças de engenharia envolvidas; adicionalmente, tais incidentes impõem prejuízo à atividade de produção agrícola em relação a perdas nos cultivos, custos de assistência técnica para os produtores, e como consequência, prejuízos à reputação do fabricante no mercado. A abordagem retrospectiva típica da maioria das práticas de qualidade tem base em informações de projeto que ‘chegam atrasadas’ uma vez que a falha já ocorreu, levando à iteração de ciclos projetartestar-consertar-retestar sem fim determinado à vista (YANG & EL-HAIK, 2009). Entretanto, é possível implementar abordagem preditiva em antecipação à prática retrospectiva ainda comum na indústria, com foco no projeto do sistema e baseada em informações preliminares no ensejo de predizer e corrigir potenciais falhas na solução em desenvolvimento (ROMANO, 2003), cujas oportunidades no projeto preliminar são apresentadas na Tabela 1.
12 OCDE: Organisation de Coopération et de Développement Économique– Organization for Organização para Cooperação e Desenvolvimento Econômico. ISO: International Standardization Organization – Organização Internacional de Padronização; EN: Europäische Normen – Norma Européia; NBR: Norma Brasileira. 13 No contexto deste trabalho, visão retrospectiva trata da execução do tratamento de falhas a partir de ocorrências passadas –como testes de protótipo em bancada ou em campo –, evidenciadas por comunicação de testemunho ou registro (ex-post-facto) demonstrando a falha e suas implicações.
Uma análise de falha de caráter preditivo usualmente tem foco no projeto do sistema, baseada em caracterizações preliminares do sistema (EN ISO 31010, 2010; MARINI, 2013). Em relação à caracterização das propriedades funcionais do projeto do sistema técnico, uma das ferramentas mais utilizadas é a técnica de Análise de Modos de Falha e seus Efeitos – FMEA (EN 60812, 2006), que pode ser aplicada com base em informações preliminares para analisar e hierarquizar as falhas potenciais antes mesmo da execução dos testes com o protótipo. Quando esta é utilizada durante o processo de projeto, aplica-se a denominação ‘FMEA de projeto’ – DFMEA (YANG & EL-HAIK, 2009). O uso contínuo da técnica FMEA nos processos de projeto e desenvolvimento é proposto por PEDROSA (2014), ao afirmar que a técnica permite revisar um projeto de produto (máquinas, ferramentas, componentes) antes de aprová-lo para a produção, podendo ainda, que o mesmo deva ou possa ser analisado durante toda a sua vida útil. Considerando o exposto, pode-se afirmar que o estudo das falhas em máquinas e outros sistemas técnicos é de relevância indiscutível, uma vez que a existência de uma falha produz consequências de toda ordem, desde a não execução da operação desejada, perdas de desempenho e riscos à segurança etc.
Entrada Atividade Tarefa Domínio Mecanismo Controle Saída Fase de Projeto Preliminar – Processo de Projeto e Desenvolvimento de Máquinas Agrícolas
Leiaute inicial Desenvolver leiautes alternativos Revisar patentes e considerações sobre aspectos legais e de segurança dos leiautes gerados PP, QU, SE, AF Análise de especialista Banco de dados sobre segurança Patentes Legislação Normas de segurança Leiautes alternativos
Avaliar leiautes gerados... (1) Todos Reunião da equipe de desenvolv. do produto Análise custobenefício Método da função-critério VDI 2225 Planejamento de marketing Especificações de projeto Fatores de influência no projeto da MA
Leiautes alternativos Desenvolver leiaute dimensional da MA
Leiaute dimensional Estabelecer o leiaute final da MA
Informações sobre segurança da MA Realizar análise de segurança sobre o leiaute final da MA
Refinar leiautes alternativos
(otimizar, eliminar pontos fracos, checar pontos críticos, interações e interfaces, etc.) Avaliar leiautes dimensionais /mock-ups (viabilidade técnica do projeto, dos processos de manufatura, da dependabilidade, da compatibilidade trator/implemento, de mercado e econômica)
Revisar o leiaute
dimensional com relação a falhas funcionais, de compatibilidade espacial ou efeitos de fatores perturbadores
Revisar o atendimento às metas de segurança PP Lista de verificação Métodos de otimização DFX (2)
Todos Reunião da equipe de desenvolv. do produto Análise custobenefício Método da função-critério
(3)
VDI 2225
MK, PP, QU, DP, SE, PV Lista de verificação
SE Análise de especialista Requisitos de projeto Especificações de projeto Leiaute dimensional Lista de componentes preliminar
Planejamento de marketing da MA Declaração de escopo do projeto Plano de gerenciamento da qualidade Especificações de projeto da MA Fatores de influência no projeto da MA Plano de gerenciamento da qualidade Leiaute dimensional Informações sobre segurança da MA Metas de dependabilidade Fatores de influência no projeto da MA Política da segurança Leiaute dimensional revisado, *encaminhar leiaute final
Informações sobre segurança da MA
Tabela 1. Atividades de desenvolvimento e de revisão de projeto relacionadas às metas de confiabilidade e segurança para o Desenvolvimento de Máquinas Agrícolas em precedência ao protótipo (ROMANO, 2003).
Os domínios de conhecimento refletem competências organizacionais internas às empresas: PP: Projeto do Produto; QU: Qualidade; DP: Dependabilidade; SE: Segurança; MK: Marketing; AF: Adm-Financeiro; PV: Pós-venda 1: Avaliar leiautes gerados... trata dos atributos pertinentes aos critérios técnicos, econômicos e de mercado, que constituem atributos de viabilidade técnica e econômica para a continuidade do desenvolvimento da máquina/equipamento agrícola. 2: DFX (Projeto para X) trata do uso de várias ferramentas e métodos de projeto com processos lógicos específicos à priorização de atributos de projeto do sistema técnico, tais como confiabilidade, robustez, segurança, custo, fabricação, entre outros. 3: O método da função critério consiste na elaboração de uma matriz em que os atributos são ponderados segundo sua importância e as alternativas são comparadas segundo seu desempenho percebido, em que vence a alternativa com melhor somatória de escores ponderados.
Análise de falhas e sua implementação: uso da técnica FMEA
Partindo de uma análise do sistema em suas funções e respectivos grupos de componentes, a técnica FMEA aponta um caminho de raciocínio aos projetistas para que possam caracterizar as ocorrências de falha de maneira sistemática, e os problemas de projeto que as motivam. Isto é verificado em ALBIERO (2010) que esclarece da possibilidade de obter melhorias significativas no projeto com a mitigação de falhas após a aplicação desta técnica, antes de efetuar a construção física do produto. De acordo com LAURENTI et al. (2012), a FMEA é técnica eficaz para evitar a ocorrência de falhas e quando aplicada corretamente, pode trazer diversos benefícios com redução considerável do retrabalho exigido para corrigir as falhas identificadas – assim como a redução de custos de mão de obra e tempo. Isto é evidenciado em PACIAROTTI et al. (2014) ao afirmarem que a FMEA investiga causas e efeitos dos modos de falha potenciais para garantir a qualidade e a confiabilidade de um produto ou processo. A partir de sua implementação e consolidação nos meios de maior complexidade e avanço tecnológico, tais como os setores de aeronáutica e defesa, a técnica FMEA se tornou uma ferramenta essencial em suporte ao alcance da qualidade no projeto e na operação de sistemas técnicos (DHILLON, 1999). Um aspecto importante da ferramenta é sua base em julgamento especializado quanto à severidade dos modos de falha, baseado em informações colhidas a partir de diretrizes ou avalições de desempenho, ou em perspectivas técnicas refletidas por especialistas a partir de experiência operacional (GLOSSOP, IOANNIDES & GOULD, 2000). Sua implementação cria referencial técnico para analisar as falhas potenciais no projeto e na construção de sistemas técnicos, que embasa a revisão dos procedimentos de operação e dos projetos de sistemas técnicos, existentes ou em desenvolvimento, quanto à proposição de melhorias para prevenir a ocorrência de falhas (ROZENFELD et al., 2006, TOLEDO & AMARAL, 2008, FOGLIATTO & RIBEIRO, 2009). Quanto ao seu uso no processo de projeto, esta técnica se concentra na prevenção de falhas do sistema técnico, mantendo suas funções básicas e atingindo um nível esperado de qualidade com o objetivo de evitar a insatisfação do cliente (FRANK et al., 2014). O uso da FMEA no projeto permite identificar possíveis inconsistências, suas causas e consequências, possibilitando avaliar o risco da sua ocorrência e determinar medidas para reduzir a probabilidade de falha (PETROVSKIY et al., 2015). Dentre as vantagens que se pode obter por meio do uso da técnica FMEA, está a redução de riscos de falhas em novos projetos (PARANHOS et al., 2016), o que justifica o uso da técnica em prevenir novas ocorrências de falha; baseada em técnicas de decomposição de sistema e de relações funcionais dos grupos de componentes (MARINI, 2013; BULIŃSKI & ŁYP-WROŃSKA, 2014), e respectivos mecanismos, FMEA permite identificar e avaliar possíveis falhas em sistemas, projetos, processos e produtos, para uma análise de confiabilidade eficaz (LIU et al., 2015). Quanto à estrutura de informação, PARANHOS et al. (2016) afirmam que esta técnica possibilita identificar pelo menos um modo de falha, permitindo discriminar o seu efeito, a causa da não conformidade, os graus de severidade, ocorrência e detecção, assim como as ações necessárias para evitar a ocorrência. Outro aspecto importante do uso da FMEA, segundo TONDIN et al. (2017), é que esta pode ser aplicada no sentido de identificar e priorizar modos de falha mais importantes, o que permite sugerir e ordenar ações que possibilitem a execução de melhorias no projeto do sistema técnico, a fim de evitar e reduzir falhas. MELO (2017) relata que as zonas de perigo das máquinas e
equipamentos devem possuir sistemas de segurança, caracterizados por proteções fixas, proteções móveis e dispositivos de segurança interligados, que garantam proteção à saúde e à integridade física dos trabalhadores. Nesse sentido, o raciocínio da ferramenta abre caminho para a consideração de provisões de segurança no projeto de máquinas e implementos agrícolas. Neste contexto, a aplicação da técnica FMEA permite a determinação do potencial dos riscos por meio do Número de Prioridade de Risco – NPR14. Este serve para hierarquizar as deficiências do sistema (modos de falha), e corresponde ao produto dos índices de Severidade (S), Ocorrência (O) e Detecção (D). Estes índices definem que a Severidade (gravidade) é classificada com base no efeito da falha, a Ocorrência com base na frequência da falha e a Detecção refere-se à capacidade de detectar a falha (MOURA, 2000; SELVAN et al., 2013; GARCIA, 2013; PACIAROTTI et al., 2014; LIU et al., 2015). Desta forma, ações corretivas podem ser recomendadas para reduzir o risco de falha conforme propõem HELMAN & ANDERY (1995). Portanto, quando os modos de falha estiverem classificados segundo o NPR, devem ser recomendadas ações corretivas para os itens críticos e com altos índices de NPR (PAHL et al., 2005; FOGLIATTO & RIBEIRO, 2009; XIAO, 2011; PACIAROTTI et al. 2014).
Engenharia reversa para análise preditiva de falhas em máquinas agrícolas
Este capítulo tem por objetivo apresentar um exemplo de abordagem de falhas em sistemas de cultivo agrícola, considerando um protótipo de equipamento agrícola distribuidor e incorporador de biofertilizante15 por meio da análise de projeto dos subsistemas que o compõem e dos respectivos componentes. Para efetuar o diagnóstico de falhas do equipamento, são empregadas duas abordagens complementares: uma abordagem retrospectiva a partir da análise de relatórios de testes de campo efetuados por especialistas; e, em complemento a esta, uma abordagem preditiva pela aplicação da técnica FMEA com base nas informações de projeto. A execução de trabalho é suportada pelas seguintes fontes de informação:
I. Análise do protótipo do equipamento agrícola – abrangeu a inspeção do protótipo em laboratório, para identificação dos subsistemas e dos componentes, e a compreensão da configuração funcional estabelecida.
II. Análise dos relatórios de testes – abrangeu o estudo dos relatórios dos testes realizados com o protótipo de equipamento agrícola, com o propósito de determinar as falhas observadas no equipamento durante a execução dos testes.
III. Aplicação da FMEA de projeto – abrangeu o estabelecimento da análise funcional do protótipo, seguida da predição de falhas do sistema e de seus efeitos usando a técnica FMEA. O conteúdo deste trabalho concentra seu interesse na aplicação da técnica FMEA ao projeto do equipamento, suportada pelo conjunto de informações apresentado na Tabela 2.
Tabela 2. Atividades de coleta de dados para execução do trabalho.
Abordagem Objeto Informação
Preditiva Projeto do implemento agrícola Desenhos de Componentes, grupos e subsistemas Peças e montagens tridimensionais dos conjuntos e subsistemas Planilhas de especificações e de montagem dos componentes
Inspeção do protótipo do equipamento Estrutura física, conexões e interfaces dos componentes
Retrospectiva Desempenho do implemento agrícola em teste
Observação dos testes do equipamento Parâmetros, medições e análise do desempenho do equipamento Parâmetros, medições e análise da dosagem do biofertilizante Desempenho da operação pretendida pelo implemento, comportamento dinâmico
Fonte
Acesso concedido à equipe de trabalho pelo fabricante
Acesso às instalações de guarda do equipamento durante os testes
Grupo de pesquisa em ensaio de máquinas agrícolas Grupo de pesquisa em biofertilizantes Acesso aos locais de ensaio do equipamento durante os testes
14 O Número de Prioridade de Risco – NPR – em uso na técnica FMEA tem sua definição a partir do original em língua inglesa: Risk Priority Number – RPN (EN 60812, 2006). 15 Dentre os biofertilizantes, destaca-se o dejeto líquido suíno (DLS) usado a partir da significativa produção de suínos, em particular nos estados da região Sul do Brasil (SCHERER, 2011; MIYAZAWA & BARBOSA, 2015)
As informações apresentadas abaixo alimentam um processo parcial de engenharia reversa (OTTO & WOOD, 1998) baseado em técnicas de decomposição funcional – função global e funções parciais –, e suportado por técnicas de inspeção em relação aos conjuntos de subsistemas e componentes responsáveis pelas funções identificadas. As relações sistemáticas e funcionais envolvendo os subsistemas e componentes foram verificadas por meio da inferência dos fluxos de energia (TDP do trator), material (Biofertilizante) e sinal (Usuário Ajustes e regulagens) a partir da documentação de projeto, validadas por meio da inspeção do protótipo. A consolidação dessas informações permitiu definir a função global do sistema conforme apresentado na Figura 2, que apresenta a formulação total do sistema de maneira independente de quaisquer princípios de solução e/ou componentes utilizados.
Figura 2. Função global do equipamento distribuidor de biofertilizantes. Baseado em FRANCESCHI (2015).
A partir da função global, as análises documentais permitiram a engenharia reversa necessária para obter o diagrama funcional do equipamento, o qual define as funções elementares de cada SSCs e embasa a aplicação da técnica FMEA tendo em mente as funções do sistema distribuidor de biofertilizantes. A engenharia reversa do equipamento resultou no estabelecimento da configuração funcional do equipamento agrícola definida a partir dos seguintes subsistemas: transporte; chassi; reservatório; tubulação; distribuidor, incorporador; e, bomba, conforme representado na Figura 3.
Usuário / tratorista
Ajustes e regulagens
TDP do trator
Biofertilizante DLS
Exportar biofertilizante DLS
Energia perdida
Biofertilizante DLS injetado
Meio Ambiente
Material
Energia Sinal
(I) Chassi
(II) Transporte
(III) Distribuidor
(IV) Incorporador
(V) Reservatório
(VI) Tubulação
Figura 3. Subsistemas do distribuidor de biofertilizantes, “como fabricado”, baseado em Franceschi (2015).
O subsistema de transporte tem como função principal permitir a movimentação do equipamento, assim como a sustentação do chassi e dos demais subsistemas integrados. O reservatório corresponde ao local de armazenamento do biofertilizante que será injetado no solo.
A tubulação é responsável pela movimentação do DLS, sendo constituída por várias conexões, que permitem estabelecer uma relação direta com os subsistemas de interesse: bomba, reservatório, distribuidor e incorporador. O subsistema de tubulação e o subsistema bomba são os responsáveis diretos pela injeção de DLS. Nesse caso, tem-se o envio de DLS do reservatório para o distribuidor, por meio dos subsistemas tubulação e bomba, sendo esta acionada por meio da tomada de potência (TDP) do trator. As uniões entre os subsistemas estavam estabelecidas por tubulações rígidas e flexíveis, fixações soldadas e parafusadas, elementos de apoio e suportes de fixação do cilindro hidráulico e demais subsistemas. Considerando todos estes elementos, pode-se determinar as funções parciais e elementares a partir da função global do equipamento em exportar biofertilizante DLS para o solo. Essas funções parciais são implementadas pelos componentes do implemento, responsáveis por fornecer o desempenho necessário para o cumprimento adequado da operação. Para verificar o desempenho do produto é possível lançar várias técnicas, dentre as quais os testes dinâmicos oferecem a melhor informação acerca de como o equipamento executa suas funções. Tem relevância significativa nesse processo a análise de relatórios de testes dinâmicos com o equipamento agrícola. No caso do equipamento distribuidor de biofertilizante, este procedimento foi feito por um laboratório especializado em ensaios de máquinas agrícolas16 . Normalmente, os relatórios resultantes de testes dinâmicos mencionam uma relação de modos de falha nos principais componentes da máquina ou implemento agrícola. No caso do equipamento distribuidor de biofertilizantes, foram identificados modos de falha em componentes dos subsistemas incorporador, distribuidor e de transporte ou rolamento, bem como problemas conceituais que afetam o desempenho operacional. Esses problemas foram identificados a partir de experimentos de determinação de vazão em cada uma das linhas de distribuição, da análise de demanda de tração e de consumo de combustível. As falhas no protótipo devem ser comprovadas por um protocolo de teste bem delineado, para que se possa sugerir propostas de melhoria no equipamento.
Execução da análise preditiva de falhas com a técnica FMEA
A aplicação da técnica FMEA é realizada a partir da definição da função global e da análise funcional e estrutural do equipamento agrícola. Aplicada em conjunto com resultados de testes dinâmicos, a técnica FMEA permite apresentar maior riqueza de informações na análise de falhas por sistematizar as informações de subsistemas e componentes do equipamento em estudo em todas as fases do ciclo de vida do produto. Assim, no caso do distribuidor de biofertilizantes, a aplicação da técnica FMEA gerou um conjunto de 18 tabelas de análise, referentes às falhas específicas de cada um dos 6 subsistemas e de seus conjuntos de componentes, conforme apresentados na Tabela 3. Tabela 3. Decomposição de subsistemas e grupos de componentes para as análises com FMEA.
Subsistema
I. Chassi
II. Transporte
III. Distribuidor
IV. Incorporador
V. Reservatório
VI. Tubulação
Conjunto/Planilha FMEA
Geral Interface esturutura incorporador Geral Interface conjunto de rolamento Geral Adaptador registro Fixação da tampa Tampa de inspeção Geral Disco de 17” Calibrador/dosador Geral Tampa de inspeção Tampa de visita Fixação da tampa Geral Abraçadeira Bocal
Componentes
4 6 2 3 7 3 6 3 3 10 6 2 3 7 6 11 2 1
16 Na Universidade Federal de Santa Maria, o Laboratório de Agrotecnologia (Agrotec), fundado e dirigido pelo Prof. Dr. José Fernando Schlosser como parte do NEMA – Núcleo de Ensaios de Máquinas Agrícolas – tem competência nacional e internacionalmente reconhecida na execução de testes dinâmicos e de ensaios para a verificação e a validação de desempenho de Máquinas e Implementos Agrícolas.
Dada a complexidade da análise de falhas, é importante que o procedimento de análise de falhas seja executado com a participação de um grupo de pessoas de diferentes áreas, incluindo especialistas em mecanização agrícola, em técnicas de cultivo, em projeto mecânico, em qualidade e confiabilidade, fabricação e suprimentos, entre outras. Tendo em mente a análise dos modos de falha por subsistema e por interface – subsistemas chassi/transporte e subsistema chassi/incorporador – o processo ganha benefício a partir da decomposição do sistema, conforme proposto por BULIŃSKI E ŁYP-WROŃSKA (2014). A aplicação da técnica FMEA a partir de análise documental do projeto do equipamento distribuidor de fertilizantes, validada por inspeção do protótipo em laboratório, permitiu identificar os modos, causas e efeitos das possíveis falhas em 85 componentes do equipamento. A Figura 4 ilustra a hierarquia de informações em que se aplica a técnica FMEA no sistema incorporador do distribuidor de biofertilizantes, sendo este composto pelo conjunto disco 17", e posteriormente aos componentes do conjunto calibrador de vazão. Assim, foram identificados 108 possíveis modos de falhas, sendo estes observados em componentes dos subsistemas (53 modos de falha) e, em componentes dos conjuntos dos subsistemas (55 modos de falha).
Figura 4. Vista isométrica do subsistema incorporador, e respectivos componentes. (FRANCESCHI, 2015). Para efeito de executar a análise dos modos de falha potenciais, foram estabelecidas escalas numéricas qualitativas17 para os índices de detecção, severidade e ocorrência, conforme mostradas na Tabela 4. Podem ser identificados ali os valores dos índices atribuídos para Severidade (S), Detecção (D), e Ocorrência (O), estabelecidos de forma independente para cada modo de falha. O valor de severidade foi definido em escala numérica de três (03) diferentes graus, enquanto os valores dos índices de detecção e de ocorrência foram estabelecidos em escalas numéricas com cinco (05) diferentes graus, sendo todas elas valoradas no intervalo de 1 a 10. Em todas as condições o maior grau é atribuído à condição mais crítica, permitindo assim atribuir graus de risco a partir da multiplicação dos valores dos critérios considerados para cada modo de falha e assim estabelecer o Número de Prioridade de Risco – NPR = S*D*O, obtido do produto dos índices S, D e O. A situação de projeto de um produto é malcomportada por natureza perante abordagens estatísticas, uma vez que ali se verifica modificação de configuração de componente ou sistema sujeita a incertezas, com efeito de mudar qualquer quantitativo previamente estabelecido quanto a montantes de prejuízo (severidade) ou probabilidades (ocorrência, detecção) que porventura estivessem previamente disponíveis. Na abordagem do presente trabalho para esses índices, conforme definidos na Tabela 4, na Tabela 5 e na Tabela 6, os escores foram definidos de maneira qualitativa, criando graus de magnitude para distinguir e avaliar a extensão projetada do impacto a partir da ocorrência de falha e a possibilidade de que o processo operacional venha a incluir ocasiões em que os problemas ocorrem e são detectados. De acordo com o modo de falha do componente e respectiva causa, procedeu-se à análise do efeito produzido sobre o desempenho geral do equipamento e/ou sua condição de operação.
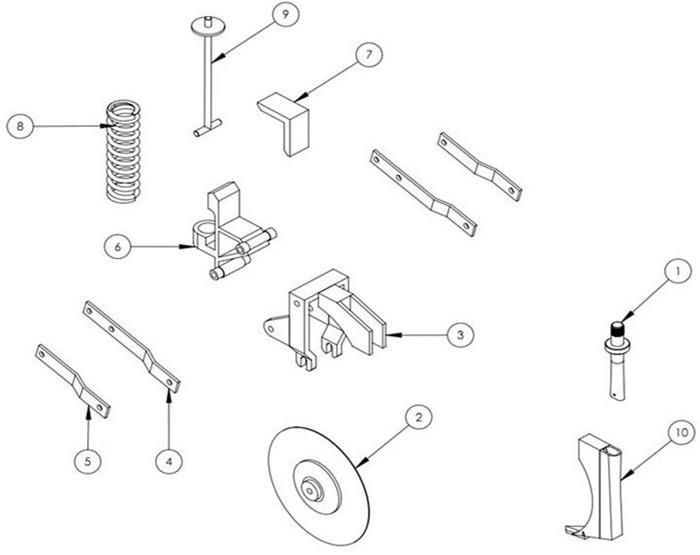
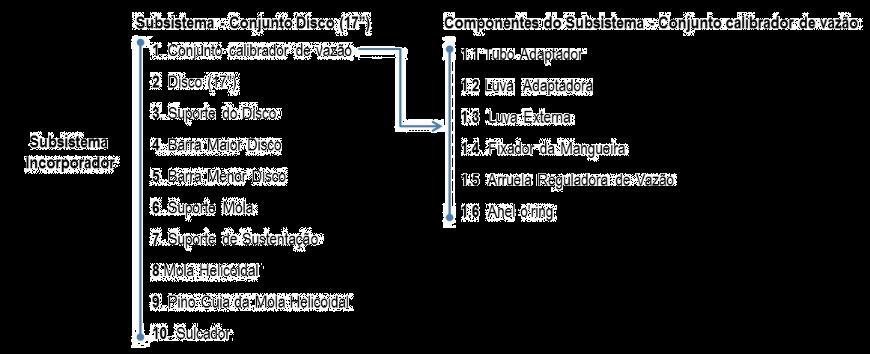
17 A técnica FMEA envolve o uso de escalas qualitativas para a atribuição de risco em razão da indisponibilidade eventual de informações quantitativas que permitam mensurar o critério em análise.
Tabela 4. Graus de severidade, detecção e ocorrência. Baseado em FRANCESCHI (2015).
Escalas de risco dos índices FMEA para o NPR
Severidade Efeito
1 Componente falha sem afetar o desempenho do sistema, produto continua a operar
5 Componente falha e degrada o desempenho funcional do sistema
10 Componente falha e interrompe totalmente a operação do sistema, com maiores danos
Detecção Critério
1 Muito alta – Modo de falha certamente será detectado quando ocorrer 3 Alta – Modo de falha tem elevada probabilidade de ser detectado 5 Moderada – Modo de falha provavelmente será detectado 7 Baixa – Modo de falha provavelmente não será detectado 10 Muito baixa – Modo de falha não será detectado
Ocorrência Critério
1 Remota – Modo de falha é improvável de ocorrer
3 Tolerável – Modo de falha raramente ocorre 5 Ocasional – Modo de falha se manifesta eventualmente 7 Frequente – Modo de falha se manifesta frequentemente 10 Inevitável – Modo de falha certamente irá ocorrer
A determinação dos valores de NPR permite identificar os modos de falha potenciais referentes a cada componente, pertencente a um subsistema e/ou conjunto de componentes do equipamento. A hierarquização dos modos de falha potenciais, no caso do distribuidor de biofertilizantes, foi realizada pela análise dos valores do NPR em que um maior valor indica maior criticidade a partir do modo de falha definido para aquele componente. A técnica FMEA inclui o registro das informações coletadas a partir dos subsistemas e dos componentes da máquina ou equipamento em um processo lógico e documentado que inclui as seguintes etapas, representadas na Tabela 5: a. levantamento e definição dos modos de falha de cada componente; b. definição dos efeitos dos modos de falha; c. definição das causas dos modos de falha; d. definição dos índices de severidade, ocorrência e detecção; e. obtenção do NPR para os modos de falha; f. hierarquização de falhas; g. interpretação dos resultados obtidos; e, h. definição das ações corretivas.
Tabela 5. Formato de planilha de FMEA para o presente exemplo.

Como critério de análise de modo de falha potencial, é relevante a inclusão, pelo menos, dos modos de falha cujo NPR inclua um índice de severidade máxima (S = 10), garantindo que toda e qualquer falha severa que resulte na não operação do equipamento seja considerada. A partir dos 108 modos de falha identificados no caso do equipamento distribuidor de biofertilizantes, 11 foram considerados potenciais sob este critério. Esses modos de falha são detalhados em ordem de prioridade na planilha da técnica FMEA. Destes modos de falha, a Tabela 6 apresenta cinco modos de falha mais relevantes como exemplo da técnica. Para os modos de falha potenciais, é recomendada a execução de ações de melhoria do ponto de vista de projeto do produto, da sua produção e de seu uso em operação, conforme propõe a literatura (PAHL et al., 2005; FOGLIATTO & RIBEIRO, 2009; PACIAROTTI et al. 2014). Para o projeto do distribuidor de biofertilizante, verifica-se que os aspectos mais críticos de confiabilidade – resultantes da análise por meio do NPR – se tratam, respectivamente, da prevenção de falhas de pressurização a partir do projeto do sistema hidráulico para posicionamento do incorporador (NPR = 250), e da garantia de vazão apropriada de biofertilizante pelos dutos por meio de revisão do projeto do acoplamento do conjunto calibrador de vazão.
Tabela 6. Planilha de FMEA com modos de falha potenciais. Adaptado de FRANCESCHI (2015).
SUBSISTEMA / CONJUNTO / INTERFACE COMPONENTE FUNÇÃO MODO DE FALHA S* EFEITO D* CAUSA DE FALHA O* NPR
Chassi / Incorporador Mangueira 1. Conduzir fluido hidráulico 2. Aplicar pressão Vazamento 10 Impedir o deslocamento do incorporador
5
Ruptura da mangueira por má instalação
5 250
Chassi / Incorporador Haste do cilindro hidráulico Permitir o deslocamento do incorporador Empenamento 10 Impedir o deslocamento do incorporador
5
1. Elevado esforço solicitado 2. Erro/falha de análise estrutural
3 150
Subsistema Incorporador Conjunto calibrador de vazão Permitir a calibragem da vazão do DLS Entupi mento 5 Impedir a dosagem do DLS 5 1. Presença de resíduos sólidos de DLS 2. Contato da ponta do calibrador no solo
5 125
Subsistema Distribuidor Crivo interno Reter partículas sólidas Obstrução dos orifícios do crivo interno
5
Permitir o deslocamento de resíduos sólidos de DLS para o subsistema incorporador
5
Excesso de resíduos sólidos de DLS
5 125
Subsistema Chassi Suporte do engate do trator Acoplar o equipamento ao trator Torção do engate 10 Dificuldade de acoplamento e desacoplamento
3
1. Solda mal executada 2. Esforço excessivo 3.Acoplamento mal executado
3 90
* ‘S’ para Severidade, ‘D’ para Detecção, e ‘O’ para Ocorrência. Após a apresentação dos resultados com a hierarquização dos modos de falha potenciais, foram realizadas as interpretações dos resultados através da identificação da (s) fase (s) e/ou etapa (s) em que poderiam ocorrer uma ou mais causas de falha potenciais. Assim, determinados os resultados, inferiuse a quantificação comparativa das falhas. A aplicação do FMEA de projeto revela número expressivo
de falhas que afetam o desempenho funcional do equipamento, o que pode ser verificado antes mesmo da construção e dos testes do protótipo. Deste modo, e segundo o componente e a sua causa de falha, foi observada a fase de sua possível ocorrência. A Tabela 7 apresenta as origens das causas dos modos de falha apresentados na Tabela 6, descrevendo subsistemas, componentes e as respectivas ações corretivas indicadas.
Tabela 7. Origens das causas de falha a partir do ciclo de vida do equipamento, e ações corretivas recomendadas. Baseado em FRANCESCHI (2015).
Origem/Etapa no Componente
Ciclo de Vida Causa Etapa do Ciclo de Vida: Subsistema de falha Ação corretiva
Dimensionamento /Projeto
Montagem /Produção Haste do cilindro hidráulico Erro ou falha de dimensionamento Chassi / Incorporador Projeto: Dimensionar o equipamento para a capacidade de carga disponível a partir do componente.
Suporte de engate do trator Solda mal Chassi
executada Produção: Observar e controlar fatores técnicos do processo de soldagem
Usuário/Uso
Ambiente/Uso Haste do cilindro hidráulico
Suporte de engate do trator
Suporte de engate do trator Elevado esforço solicitado Chassi / Incorporador
Esforço excessivo Chassi
Acoplamento mal Chassi
executado
Mangueira Ruptura da mangueira por má instalação Chassi / Incorporador
Conjunto Calibrador de vazão Causa 1. Presença de resíduos sólidos de DLS
Causa 2. Contato da ponta do tubo adaptador com resíduos do solo Incorporador
Crivo interno Excesso de resíduos sólidos de DLS Distribuidor Uso: Assegurar o uso adequado do equipamento por manual e avisos.
Projeto: Dimensionar para a capacidade de carga do componente, assegurar o uso adequado do equipamento.
Uso: Assegurar o uso adequado do equipamento por manual e avisos
Projeto: Reposicionar a saída das mangueiras sobre o pistão.
Projeto: Fixar as mangueiras de pressão ao conjunto do equipamento. Causa 1. Projeto: Verificar dimensionamento do crivo e do calibrador de vazão;
Causa 2. Projeto: Incluir dispositivo de proteção e/ou limpeza da ponteira do duto do calibrador de vazão;
Causa 2. Uso: Incluir procedimento de revisão e limpeza antes e após o uso.
Uso: Incluir especificação de qualidade do biofertilizante para aplicação;
Projeto: Incluir dispositivo de pré-filtragem do DLS após a bomba.
É importante salientar que cada causa de falha poderá direcionar ações corretivas em diferentes etapas do ciclo de vida do produto: cada uma delas deverá ser abordada com ação corretiva específica em direção às partes envolvidas em cada etapa: o projetista, os operadores de produção, o agente de assistência técnica, e o operador da máquina. Este detalhamento das causas de falha dos componentes é contextualizado por MELO (2017) que entende a utilização da FMEA para assegurar que os modos de falha potenciais, suas causas e mecanismos, sejam abordados durante o projeto do produto. As causas de falha, rastreadas segundo a origem, permitem identificar as seguintes informações: primeiramente, os elementos de atenção para as melhorias necessárias; e então, o tipo de ação corretiva que deve ser implementada no ciclo de vida do equipamento. Após efetuar as alterações necessárias ao projeto de engenharia, novas análises podem ser efetuadas para verificar a eficácia das alterações de projeto na redução do risco (novo cálculo do NPR a partir da análise do componente modificado) dos modos de falha. Essa abordagem auxilia na detecção
antecipada de problemas potenciais, evitando que falhas ocorram durante a execução do protótipo final, bem como registra o histórico de melhorias no projeto do produto.
Práticas de suporte à predição de falhas no projeto
Um dos elementos centrais do processo de projeto é a elaboração de uma solução que cumpra as necessidades das partes envolvidas para o seu ciclo de vida (ROMANO, 2013). Como as especificações de projeto determinam a satisfação das necessidades dos clientes do ciclo de vida (FONSECA, 2000), a confiabilidade é um dos atributos de desempenho da solução em cumpri-las. Conforme DIAS et al. (2013), esse atributo engloba quatro características essenciais: • Probabilidade: grau qualitativo ou relação temporal que expressa a possibilidade de ocorrência de um evento; neste trabalho, ela é estabelecida em termos da evidência de falha a partir dos testes executados por especialistas em comparação com o julgamento de possibilidade de falha pela equipe de engenharia usando FMEA; • Comportamento adequado: conjunto de características e parâmetros que estabelece referencial para o desempenho de um sistema; neste trabalho, este elemento trata do desempenho do equipamento sob protocolos e critérios de ensaio pré-estabelecidos em comparação à predição de interferências ou danos a componentes baseada em conhecimento de engenharia; • Período de uso: normalmente expresso em continuidade ou intermitência em função do tempo de operação; neste trabalho, o período de uso é elemento subjacente quanto à predição da operação do equipamento (intermitente, sazonal) em cumprimento ao comportamento adequado; • Condição de uso: depende de aspectos técnicos e humanos que determinam as solicitações sobre o sistema em serviço; neste trabalho, a condição de uso é manifestada nos protocolos de ensaio executados com o protótipo, em comparação com o julgamento preditivo baseado em experiência e conhecimento pessoais. O estabelecimento dessas características no projeto de sistemas técnicos – dentre eles, máquinas e implementos agrícolas – tem pré-condições relacionadas ao progresso do projeto do sistema em direção à modelagem de seus princípios de solução, da arquitetura construtiva, e do detalhamento de geometrias e materiais. Primeiramente, a predição de falhas requer um entendimento das métricas de desempenho pretendidas para o produto, e das possíveis interferências sobre seu desempenho. As especificações de projeto do sistema técnico (FONSECA, 2000; PAHL et al., 2005) incluem a definição de métricas, de valores-alvo e faixas de tolerância que traduzem as necessidades dos clientes. Esse entendimento deve incluir os fatores de influência no projeto (MARINI & ROMANO, 2009), por seu potencial de determinar as faixas de preferência em especificações de projeto ou interferir sobre as funções pretendidas do sistema de cultivo agrícola. No exemplo deste trabalho, o ranqueamento do NPR permite identificar os grupos de componentes mais sensíveis à ocorrência de falhas, de tal forma que se possibilita apontar os elementos que requerem ações corretivas no sentido de prevenir a ocorrência de falhas em operação. Para efeito de ilustração, a Figura 5 mostra os modos de falha com NPR >= 125, equivalente à atribuição de índice 5 para os critérios de severidade (S), ocorrência (O), e detecção (D), o tratamento dos problemas se dará com prioridade para os problemas de maior NPR, ponderando entre os custos potenciais do risco envolvido e os recursos disponíveis para implementar a solução dos problemas, entre todos os modos de falha diagnosticados. A regularidade da vazão de biofertilizante através do subsistema calibrador de vazão está sujeita à entrada de elementos de solo que interferem com a entrega do produto ao solo – conforme apresentado na Tabela 6 quanto ao entupimento do conjunto calibrador de vazão. Também para o caso do crivo interno do distribuidor, é possível a ocorrência de falha a partir de resíduos sólidos que possivelmente componham o biofertilizante. Para exemplos como esse, é essencial o entendimento dos elementos solo e biofertilizante e das suas propriedades, cuja incerteza em associação com os mecanismos de falha apresentados determina sua consideração como fatores de influência no projeto (MARINI, 2007; MARINI & ROMANO, 2009).
NPR =250 Vazamento de fluido hidráulico
NPR =150 Haste do cilindro hidráulico
NPR =125 Calibrador de vazão
NPR =125 Crivo interno do distribuidor
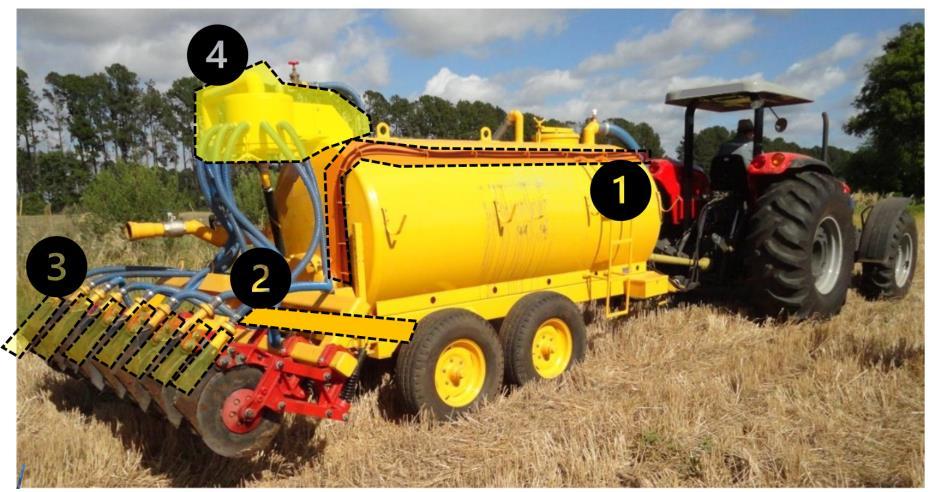
Figura 5. Equipamento distribuidor de biofertilizantes, conjuntos de componentes sujeitos a modos de falha de maior prioridade segundo ranqueamento do NPR, baseado em FRANCESCHI(2015).
O papel do método de análise funcional (PAHL et al., 2005) em suporte à predição de falhas é demonstrado no exemplo do equipamento distribuidor DLS, auxiliando em esclarecer a construção do conjunto em submontagens de componentes com funções específicas. Essas informações criam os fundamentos para a abordagem preditiva de diagnóstico de falhas, inclusive quanto ao uso da técnica FMEA: primeiramente, pelo papel dos fatores de influência na definição de diretrizes para decompor funções no processo de desenvolvimento de máquinas agrícolas (ROMANO et al., 2005); e, então, pelo efetivo uso desses fatores em suportando a modelagem funcional incluindo as funções parciais e os fluxos de grandezas (MARINI, 2007). Nesse contexto, os fatores de influência no projeto fornecem entradas à verificação das funções e das cadeias de fluxo – transformações de energia, material e sinal – necessárias à operação de distribuir fertilizantes sobre o solo (MARINI, ROMANO & DALLMEYER, 2007). Uma vez que constituem base para o diagnóstico preditivo, as funções e os fluxos são usados juntamente com informações do projeto para o uso da técnica FMEA (BORGMANN, 2007). As informações pertinentes ao distribuidor incluem o conjunto dos fatores de influência no projeto (Tabela 8), a estrutura de funções (Figura 6), e o diagnóstico de falhas (Tabela 9). A transparência das funções quanto aos elementos transformados e aos estados de entrada e saída torna acessível a interpretação heurística dos diagramas de estrutura funcional, pelos fluxos de energia, material e sinal (STONE, WOOD & CRAWFORD, 2000), e a definição de cadeias de funções dominantes quanto ao processamento do cultivo e aos auxílios de potência, de comandos e ajustes, e de suporte (MARINI, 2007). Esse aspecto é importante para estabelecer as características do sistema técnico que influenciam a confiabilidade, pois a operação pretendida progride e muda em relação ao tempo (BLANCHARD, 2004), o que motiva a relevância da análise das etapas de uso para entender os possíveis estados operacionais do sistema técnico, e dali predizer os possíveis modos de falha (BREIING, ENGELMANN & GUTOWSKI, 2007). Por último, o princípio de operação para cada função pretendida pode ser expresso na forma de esboço ou de um diagrama de corpo livre, representando o funcionamento do sistema sob análise (KROLL, CONDOOR & JANSSON, 2001; PAHL et al., 2005).
Tabela 8. Fatores de influência no projeto para um distribuidor centrífugo de fertilizantes - classe de interferências e limites (MARINI, 2007).
Classe A13 Interferências e limites
STARA (2020)
Propriedade Informação Descrição
A131 Elementos operadores
Ser humano
Sistema de informação e controle - Determinar as dosagens de fertilizante aplicadas; - Ajustar dimensões de sustentação para o cultivo; - Acoplar a máquina a uma fonte de potência ;
- Processar prescrições de aplicação; - Controlar a taxa de dosagem aplicada;
A132 Elementos ambientais
Solo
Planta
A133 Época do ano
Inverno
Verão
A134 Tempo para execução
A135 Freqüência de execução
Estádios prescritos para aplicação de fertilizantes Ver prescrições agronômicas específicas à cultura e ao solo, dependendo do fertilizante. Estimativa de tempo disponível para cada aplicação – máximo 2 dias.
Estádios prescritos para aplicação de fertilizantes Ver prescrições agronômicas específicas à cultura e ao solo, dependendo do fertilizante. Estimativa de freqüência média: 3 vezes por temporada.
Perda de fertilizante - Receber diretamente e incorporar o fertilizante distribuído pela máquina; - Receber solicitações físicas de compressão e cisalhamento a partir do deslocamento da máquina; - Processar o fertilizante incorporado ao solo, dele se alimentando para desenvolver-se; - Receber efeitos secundários da máquina a partir de interação física em estádios mais avançados; Maio até agosto: inverno ou estação seca: - temperaturas menores, menor umidade absoluta; Novembro até fevereiro: verão ou estação de chuva: - temperaturas maiores, maior umidade absoluta;
Distribuição do fertilizante não é feita sobre a área pretendida de modo uniforme e completo.
Torroamento do fertilizante
A136 Riscos de execução
Plastificação do fertilizante
Segregação do fertilizante
Deposição de ferfilizante fora da área
Desgaste dos componentes Ocorre a formação de torrões, que impedem a distribuição uniforme, a partir da agregação de partículas de fertilizante. Modificação da consistência física do fertilizante quanto ao ângulo de repouso e à resistência ao cisalhamento em termos de atrito e aderência. Separação de faixas de fertilizante aplicado em razão das propriedades físicas dos elementos do composto. Deposição de fertilizante em áreas onde a aplicação da substância implica em contaminação do meio.
Desgaste dos órgãos da máquina em razão das propriedades abrasivas e/ou corrosivas do composto.
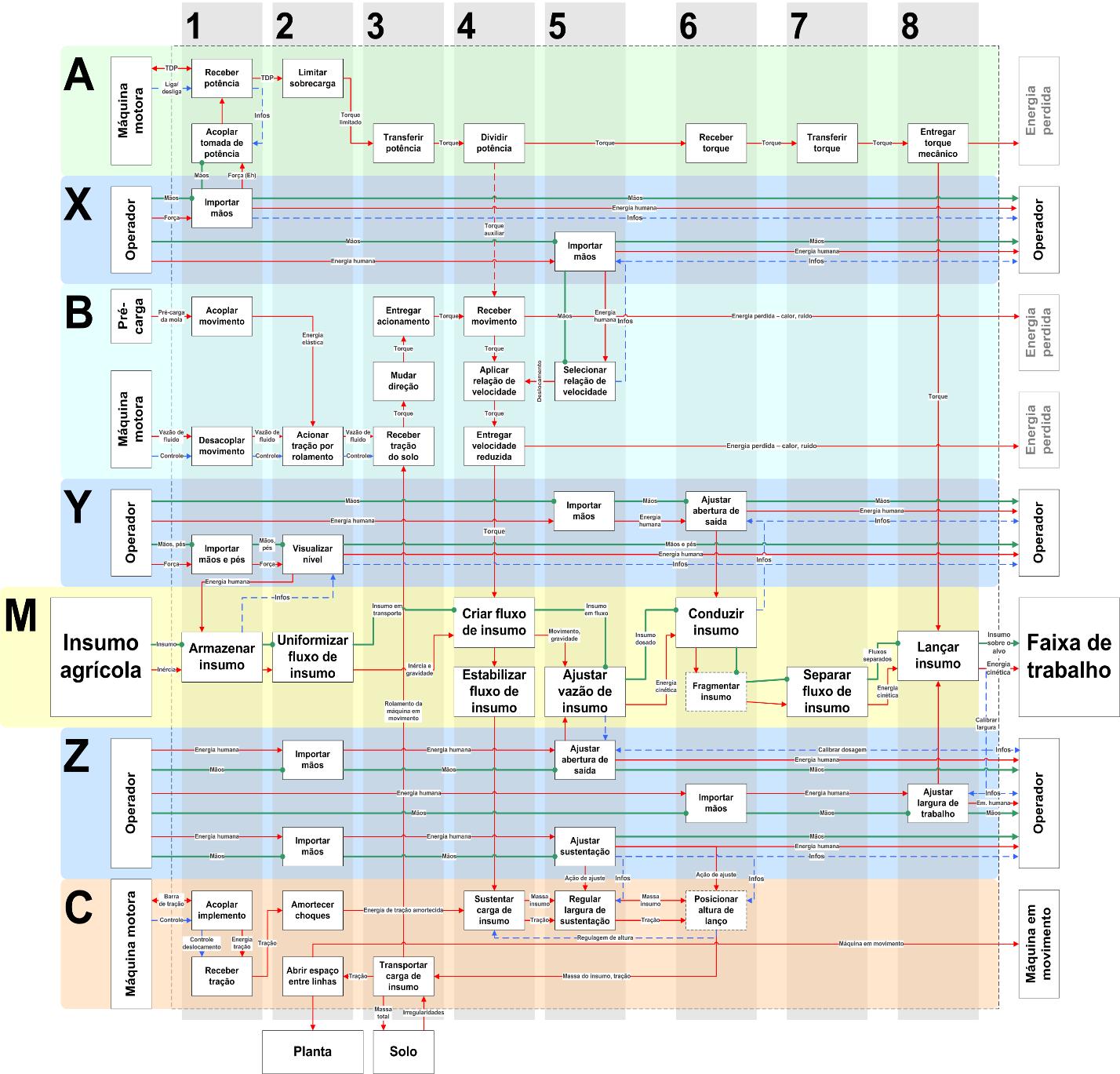
Figura 6. Estrutura funcional matricial de um distribuidor centrífugo de fertilizantes, orientada em torno de fluxos parciais em suporte ao fluxo central de processamento do cultivo agrícola (MARINI, 2007).
A consideração agregada de todas as informações em nível de sistema, desde as especificações de projeto até as definições de princípios de componentes fornece embasamento para a execução da FMEA de projeto18. Para o caso do distribuidor centrífugo de fertilizantes, um exemplo de FMEA com funções parciais é mostrado na Tabela 9: as funções são referidas por números e letras correspondentes ao posicionamento matricial apresentado na Figura 6.
18 A técnica FMEA aplicada ao projeto do produto é comumente designada como DFMEA (Design FMEA) na metodologia de projeto para Seis Sigma (DFSS, Design for Six Sigma).
Tabela 9. Análise de modo de falhas e seus efeitos para fluxo de acoplamento e movimento (funções linha C19) do distribuidor centrífugo de fertilizantes. Adaptado de BORGMANN (2007).
FMEA 01 - Subsistemas Auxiliares
Item: Subsistema de Acoplamento - Sistema de Engate Equipe FMEA: Tobias, Cleiton, Mateus
Descrição Função Controles Atuais Modos de Falha
3. Conjunto engate Acoplar
Implemento Posição: 1C Fábrica:
* Ensaios virtuais de esforço * Inspeção do Controle de Qualidade
Operador:
* Controle visual * Treinamento
Ruptura do engate (a) Possíveis Causas
* Erro de montagem * Solda mal executada * Peça com defeito * Esforço excessivo * Acoplamento mal executado FMEA de Produto
Data: 22/01/2007 Revisão: 13/02/2007
Efeitos de Falha Índices
S* O* D* RPN
Parada da máquina 10 2 1 20
Danos à transmissão 8 2 1 16
Danos a pessoas próximas 10 1 1 10
4. Conjunto Mangueira ¼” x 3800
Ajustar abertura de saída: Ajustar vazão de insumo Posição: 5Z Fábrica:
* Inspeção do Controle de Qualidade
Operador:
*Treinamento * Controle visual
Torção do conjunto (b)
Vazamento (a)
Entupimento (b)
* Esforço excessivo * Acoplamento mal executado *Solda mal executada
*Desgaste da vedação *Acoplamento mal-executado *Conector defeituoso *Conector nãocompatível Dosagem irregular de insumo 10 2 1 20
*Acoplamento mal-executado *Entrada de sujeira Danos à transmissão 8 2 3 48
Dosagem irregular de insumo 10 1 1 10
Falha de abertura das comportas 10 1 1 10
Não-abertura das comportas (c)
*Acoplamento mal-executado *Não há óleo no sistema *Vazamentos *Entupimento Não há dosagem de insumo 10 2 3 60
A sistematização das informações do projeto do sistema de cultivo agrícola em especificações de projeto –inclusos os fatores de influência –, declarações de função do sistema, e grupos de componentes da arquitetura física torna acessível aos projetistas o entendimento dos possíveis incidentes à integridade dos componentes a partir das informações de projeto ‘como-pretendido’ dos sistemas de cultivo agrícola – facilitando o diagnóstico preditivo de falhas. Essa abordagem de sistema faz parte do exemplo apresentado, que demonstra sua eficácia em facilitar a sistematização das informações coletadas a partir das inspeções de protótipo em conjunto com a análise de documentos de projeto. Para além das especificações de projeto e das funções do sistema técnico, a predição de falhas também depende de entendimento em relação à operação pretendida do equipamento, e de suas etapas. Mesmo que as informações de materiais, geometrias localizadas e de tolerâncias ainda precisem ser trabalhadas no processo de projeto para integralizar a análise de modos de falha em projeto com
FMEA, o uso de práticas sistemáticas no processo de projeto – como a definição das especificações de projeto, a investigação dos fatores de influência no projeto, a análise funcional, a FMEA de projeto, entre outras – tem papel significativo em abrir caminho para o raciocínio dos projetistas, de tal maneira que grande parte das potenciais falhas ainda podem ser identificadas. Com isso, conclui-se que é possível a execução de atividades de predição de falha durante o processo de projeto, antes de comprometer recursos mais significativos com a execução de protótipos de engenharia para a identificação posterior de evidência de modo de falha.
As observações deste trabalho tratam de exemplificar o uso da técnica FMEA usando impressões e informações de projeto a partir de modelos estáticos documentados embasando método de análise de falhas. Esta discussão acerca da predição de falhas no processo de projeto parte da caracterização dos exemplos de máquinas e equipamentos agrícolas apresentados neste capítulo com a técnica FMEA de projeto e reflete sobre sua eficácia tomando por base o estado da arte na prática do processo de projeto nas comunidades de projeto de engenharia e desenvolvimento de produtos. Nesse contexto, é possível estabelecer distinção entre a análise de falhas no projeto após evidenciadas no protótipo construído, e a predição de falhas pela modelagem de projeto e projeção de comportamentos razoavelmente previsíveis. Observando o processo de projeto como uma linha do tempo, entende-se que as fases mais precoces se caracterizam por maior incerteza, menor custo de execução e maior liberdade de escolha; e as fases mais tardias, por maior complexidade e detalhamento, custos mais elevados, e significativa possibilidade de conflitos, podendo incorrer em custos exponencialmente maiores (ULLMAN, 2010). Dois entendimentos são importantes nesse contexto: primeiramente, o efeito das decisões precoces nas etapas tardias, e em seguida, o aprendizado a partir de ciclos projetar-construir-e-testar no desenvolvimento das máquinas e implementos agrícolas. De um lado, decisões tomadas em um dado escopo de competência no processo de projeto manifestam efeitos ao desempenho e à execução das atividades posteriores em um escopo expandido, incluindo o escopo de competência original e outras áreas importantes da organização envolvidas no processo (ANDREASEN & OLESEN, 1990; ANDREASEN, 2011). No caso do equipamento distribuidor de biofertilizantes, pode ocorrer que a decisão de reduzir custo retirando suportes de tubulação hidráulica da estrutura do equipamento pode causar problemas significativos quanto à retenção do fluxo de fluido, assim como identificados com a técnica FMEA no exemplo apresentado neste capítulo. A Figura 7 representa o problema em relação ao contexto de falhas de projeto.
Figura 7. Disposição de projeto em antecipação aos modos de falha, baseado em ANDREASEN & OLESEN (1990).
Conhecimento de confiabilidade
Alvos da disposição:
Regras
Padrões
Dados
Disposição
Tarefas: Metas Critérios
Informação Dados Informação Dados
Projeto detalhado
Testes de protótipo Análise de falhas
DECISÃO
Projeto preliminar do grupo de componentes
Como exemplo, uma vez que se elege que o projeto preliminar da barra de tração do distribuidor de biofertilizantes não inclua a definição dos suportes da tubulação hidráulica, o que criará risco quanto à ocorrência de vazamento de fluido hidráulico da tubulação naquela posição, após testado o protótipo. O conhecimento prévio dessa possibilidade sugere a disposição de configurar a tubulação hidráulica com suportes que previnem o modo de falha considerado. Tal problemática impõe desafios às equipes de engenharia, uma vez que a liberdade de projetar corresponde a lacunas e incertezas na caracterização do problema de projeto (SCHRADER, RIGGS & SMITH, 1993; DE WECK, ECKERT & CLARKSON, 2010) –a necessidade operacional a ser atendida. Por outro lado, o processo de projeto progride em ciclos projetar-construir-e-testar (síntese-análise) até que as incertezas das relações de causa & efeito entre componentes sejam resolvidas em relação às funções pretendidas (WHEELWRIGHT & CLARK, 1992; ULLMAN, 2010). Esse progresso inclui análises que podem levar a uma das duas conclusões: (a) identificar falhas, entender os erros e iterar considerando ações corretivas; ou (b) concluir que o desempenho da implementação testada é satisfatório e prosseguir com projeto para sua conclusão (THOMKE, 1998). Os exemplos de máquinas e implementos agrícolas apresentados neste capítulo demonstram a necessidade das práticas de projeto e desenvolvimento de máquinas agrícolas em satisfazer dados prérequisitos para habilitar à predição dos possíveis modos de falha para o implemento. Essa dinâmica do processo de projeto é representada na Figura 8. Em sucessivos ciclos de projetar-construir-e-testar, toda abordagem de falha acaba tendo caráter de análise em relação a um esforço já comprometido na solução de incertezas e problemas, e terá caráter de predição em relação a um esforço futuro de maior detalhamento e liberdade de ação mais reduzida.
Figura 8. Usando FMEA no processo de projeto (ROMANO, 2013) e abordagens de falha.
Tendo em mente o ‘atraso’ da evidência de falha a partir dos testes, busca-se antecipar a solução de problemas por recursos de engenharia virtual e construção rápida (BABA & NOBEOKA, 1998; THOMKE & FUJIMOTO, 2000). A complexidade das informações necessárias para levantar as cadeias de eventos que caracterizam os modos de falha requer detalhamento suficiente do projeto do produto para deixar transparentes os mecanismos de falha (MARINI et al., 2010). Como demonstrado com o exemplo do distribuidor centrífugo, esse levantamento é potencializado pelo emprego de práticas e métodos sistemáticos de projeto que facilitem a reflexão acerca das funções pretendidas do sistema técnico e das interferências que este irá encontrar em campo.
Projeto informacional PROJETAÇÃO
Projeto conceitual Projeto preliminar Projeto detalhado IMPLEMENTAÇÃO
Preparação da produção Lança mento Validação
Projetar
Construir
Testar Projetar
Construir
Testar Projetar
Construir
Testar Projetar
Construir
Testar
Analisar
Especificações de projeto
Projeto do conceito
Leiaute finalizado Detalhamento e protótipo
Homologação do produto
Métricas de desempenho Sistema e princípios de solução
Análise de falha
Pré-requisitos de sistema Retrospectiva
Arquitetura funcional e construtiva Detalhamento de subsistemas e componentes
Predição de falha
Antecipação de soluções
Preditiva
Certificação da solução de cultivo agrícola
Além disso, os seguintes fatores demonstram os benefícios de antecipar a modelagem funcional e a predição de falha no processo de projeto: 1. Primeiramente, o aumento da complexidade e dos custos das ações corretivas, em que as ações tardias demandam maior número de procedimentos e transações para sua conclusão em proporção ao detalhamento do projeto (TAN, OTTO & WOOD, 2017); 2. Em seguida, a influência de decisões precoces quanto ao curso de ação do projeto, somada à liberdade de escolha de soluções pela indeterminação momentânea das características do projeto (ANDREASEN & OLESEN, 1990; DERELÖV, 2008); 3. Além destes, a responsabilidade do produto mediante falha por defeito de projeto, exposição a perigos por ausência de proteções, e negligência de outros usos possíveis além do uso pretendido (ULLMAN, 2010); 4. Ainda em responsabilidade do produto, o vínculo legal das normas técnicas determina a observação de falhas como não-conformidades sujeitas à lei e incentiva à prevenção de falhas nos produtos (POLINSKY & SHAVELL, 2009). A complexidade das fases de projeto detalhado e de preparação da produção (1) cria uma barreira ao progresso do projeto rumo à entrega do produto ao mercado em que haja a necessidade de correções a partir de alterações de engenharia do produto. Por outro lado, a liberdade de ação (2) na fase de projeto conceitual diminui progressivamente conforme se evolui na geração de leiautes durante o projeto preliminar, o que favorece a execução de diagnósticos preditivos precoces para suportar encaminhamentos de projeto. A responsabilidade legal do produto por jurisprudência (3) e por normas técnicas (4) impõe critérios mínimos de aceitação do projeto para construção e teste para verificação de atendimento já nas fases de projeto conceitual e preliminar, o que incentiva o diagnóstico de falhas potenciais já nessas fases pois a verificação de não-conformidades no projeto detalhado e sua correção é muito cara.
Conclusão
O exemplo apresentado neste capítulo com a análise de modos de falha do distribuidor de biofertilizante, e complementado pelo caso do distribuidor centrífugo de fertilizantes, permite refletir acerca da eficácia do uso de métodos sistemáticos quanto à predição de falhas em máquinas e implementos agrícolas em vários aspectos. Primeiramente, quanto ao tempo da avaliação em relação ao comprometimento de recursos no processo de projeto, viu-se que a abordagem retrospectiva evidencia os problemas com ‘atraso’ em relação à sua ocorrência, e que a abordagem preditiva traz benefícios pelo diagnóstico de falhas potenciais com o uso de documentos e inspeções (feitas com o protótipo no caso do distribuidor de biofertilizante, são aplicáveis a mock-ups e modelos virtuais). Ao mesmo tempo, a abordagem retrospectiva em relação ao protótipo requer investimentos significativos para evidenciar características do projeto da solução (como falhas e perturbações de funcionamento) desfavoráveis às especificações de projeto; a abordagem preditiva, antecipando o uso da ferramenta para o projeto preliminar, auxilia na antecipação de problemas em relação aos comprometimentos maiores de recursos. O estudo também demonstra a possibilidade de explorar maiores informações acerca do ciclo de vida do equipamento: a abordagem retrospectiva ficou restrita à observação do protótipo na fase de “Uso”, por conseguinte, durante as etapas de “Usuário e Ambiente”, não identificando falhas originadas nas fases de “Projeto e Produção” do produto. A análise realizada na abordagem preditiva permitiu evidenciar as causas de falhas potenciais, cujas origens são respectivas a todas as fases do produto (Projeto, Produção e Uso), o que resulta em um diagnóstico preciso de falhas sobre o ciclo de vida do produto. Assim, diante dos resultados obtidos, conclui-se que a realização de testes e experimentos permite obter dados sob condições específicas de operação, ou seja, durante a fase de uso, possibilitando eliminar ou atenuar falhas em condições reais de trabalho. Esta abordagem implica em custos elevados por requerer o uso de um protótipo para análise a ser efetuada por gente qualificada em testes de cultivo, e que exigirá, caso alguma falha seja identificada, alteração de projeto do produto de SSCs, e modificações sobre o projeto do protótipo para que novos testes sejam realizados buscando a sua aprovação.
Com a aplicação da técnica FMEA de projeto a partir da fase de projeto preliminar do equipamento, é possível efetuar o diagnóstico de falhas e estabelecer as ações de melhoria antes de construir o protótipo final. Esse mecanismo proporciona menor custo para a solução de problemas por meio da antecipação dos potenciais modos de falha, colaborando também para um menor prazo de desenvolvimento pela redução das iterações de construção e teste de protótipos. Uma vez que reduz a complexidade de inspeções, testes e verificações, a predição de falhas com FMEA colabora para um aumento de qualidade no produto final entregue ao mercado. Assim, quando da avaliação do protótipo em testes e experimentos, este se apresenta mais robusto de modo a permitir a liberação da produção do produto em escala industrial, garantindo a qualidade durante a vida útil do produto, uma vez que podem ser planejadas as manutenções preventivas para componentes específicos, reduzindo a manutenção corretiva. Portanto, o desenvolvimento de uma metodologia de análise de falhas – empregando a abordagem preditiva – vem contribuir para a construção de uma cultura de qualidade em empresas que não realizam este procedimento, mitigando as possíveis falhas no projeto final da máquina agrícola.
Referências
AFFONSO LOA (2006) Machinery Failure Analysis Handbook – Sustain your Operations and Maximize Uptime. Houston: Gulf Publishing Company. ALBIERO D, MACIEL AJS, MILAN M, MION RL, VILIOTTI CA (2010) Análise do Modo e Efeito de Falhas (FMEA) no desenvolvimento de semeadora multifuncional conservacionista para a agricultura familiar. INGEPRO - Inovação, Gestão e Produção, 2 (11): 026-037. ANDREASEN MM, OLESEN, J (1990) The concept of dispositions. Journal of Engineering Design, 1(1): 17-36. ANDREASEN MM (2011) 45 years with design methodology. Journal of Engineering Design, 22(5): 293-332. BABA Y, NOBEOKA K (1998) Towards knowledge-based product development: the 3-D CAD model of knowledge creation. Research Policy, 26: 643-659. BAXTER M (2011) Projeto de Produto: Guia prático para o desenvolvimento de novos produtos. 3ª. Edição. São Paulo: Edgard Blücher. BERGAMO RL, ROMANO LN (2016) Agricultural machinery and implements design process: guidelines for small and mid-sized businesses. Engenharia Agrícola, 36(1): 206-216. BORGMANN T (2007) Aplicação do Método FMEA no subsistema de dosagem de fertilizantes do distribuidor centrífugo Stara Tornado 3500/5500. Monografia (Graduação em Engenharia Mecânica) –Curso de Engenharia Mecânica, Universidade Federal de Santa Maria. BLANCHARD BS (2004) System engineering management. John Wiley & Sons. BRAILE NA, ANDRADE JJO (2013) Estudo de falhas em equipamentos de costura industriais utilizando o FMEA e a análise de confiabilidade. In: ENEGEP, Salvador. BREIING A, ENGELMANN F, GUTOWSKI T (2009) Engineering design. In: Grote, K. H., & Antonsson, E. K. (Eds.). Springer handbook of mechanical engineering (Vol. 10). Springer Science & Business Media. BULIŃSKI J, ŁYP-WROŃSKA K (2014) Methods for analysis of the failures in agricultural machinery. Annals of Warsaw University of Life Sciences - SGGW. Agriculture 64: 59 - 67. CORRÊA, IM, SCHLOSSER JF (2011) Perspectiva de ensaios de máquinas agrícolas no Brasil. AgriWorld 2(3), 100-106. DE WECK, O, ECKERT CM, CLARKSON, PJ (2007) A classification of uncertainty for early product and system design. In: Proceedings of ICED 2007, the 16th International Conference on Engineering Design, Paris, France, (159-160). DERELÖV M (2008) Qualitative modelling of potential failures: on evaluation of conceptual design. Journal of Engineering Design, 19(3): 201-225.
DIAS, A, CALIL LFP, RIGONI E, OGLIARI A, SAKURADA EY, KAGUEIAMA, HA (2011) Metodologia para análise de risco: mitigação de perda de SF6 em disjuntores. Florianópolis: Universidade Federal de Santa Catarina, Eletrobras/Eletrosul, P&D ANEEL. DHILLON, BS (1999) Design Reliabiliity: Fundamentals and Applications. Boca Raton: CRC Press. EN 60812 (2006). Analysis techniques for system reliability - Procedure for failure mode and effects analysis (FMEA). Bruxelas: European Committee for Eletrotechnical Standardization - CENELEC. FOGLIATTO FS, RIBEIRO JLD (2009). Confiabilidade e Manutenção Industrial. São Paulo: CampusElsevier, 288 p. FONSECA AJH (2000) Sistematização do Processo de Obtenção das Especificações de Projeto de Produtos Industriais e sua Implementação Computacional. Florianópolis. Tese (Doutorado em Engenharia Mecânica) – Programa de Pós-Graduação em Engenharia Mecânica, Universidade Federal de Santa Catarina. FRANCESCHI A DE (2015). Sistemática de análise de falhas do equipamento agrícola sob a ótica de projeto do produto. 144f. Tese (Doutorado em Engenharia Agrícola), Universidade Federal de Santa Maria, RS. FRANK AG, PEDRINI DC, ECHEVESTE, ME, RIBEIRO JLD (2014). Integração do QFD e da FMEA por meio de uma sistemática para tomada de decisões no processo de desenvolvimento de produtos. Production, 24(2): 295-310. GARCIA, PAA (2013) Uma abordagem via análise envoltória de dados para o estabelecimento de melhorias em segurança baseadas na FMEA. Gestão Produção, São Carlos, 20(1): 87-97. GLOSSOP M, IOANNIDES A, GOULD J (2000) Review of Hazard Identification Techniques. London: Health & Safety Executive, Report no. 2005/58. HELMAN H, ANDERY PRP (1995) Análise de Falhas (Aplicação dos Métodos de FMEA e FTA). 1ª edição. Belo Horizonte: Fundação Christiano Ottoni, 156 p. HUBKA, V., EDER, W. E. (1992) Engineering design: General procedural model of engineering design. Heurista, 1992. EN ISO 31010 (2010) Risk management – Risk assessment techniques. Bruxelas: Comitê Europeu de Normalização Eletrotécnica - CENELEC. LAURENTI R, VILLARI BD, ROZENFELD H (2012) Problemas e melhorias do método FMEA: uma revisão sistemática da literatura. Pesquisa & Desenvolvimento Engenharia de Produção, 10: 59-70. LIU, HC, YOU JX, SHAN MM, SHAO LN (2015) Failure mode and effects analysis using intuitionistic fuzzy hybrid TOPSIS approach. Soft Computing, 4(19): 1085-1098. MARINI VK, ROMANO LN, DALLMEYER AU (2007) The function structure as a tool for analysing an existing concept of a centrifugal fertilizer spreader. In: Proceedings of COBEM 2007, the 19th International Congress of Mechanical Engineering, Brasília. MARINI VK, ROMANO LN (2009) Influencing factors in agricultural machinery design. Product: Management & Development, 7(2), 111-130. MARINI VK, RESTREPO J, AHMED S. (2010) Evaluation of information requirements of reliability methods in engineering design. Proceedings of the DESIGN 2010 Conference. Zagreb: The Design Society. MARINI VK (2013) Information about Robustness, Reliability and Safety in Early Design Phases: Current methods, industrial case study and knowledge-based support. PhD Thesis, Department of Mechanical Engineering, Technical University of Denmark. MELO RP (2017) Desenvolvimento e avaliação de uma semeadora puncionadora para agricultura familiar. 134 f. Centro de Ciências Agrárias. Programa de Pós-Graduação em Engenharia Agrícola Universidade Federal do Ceará, CE. MIYAZAWA M, BARBOSA, GMC (2015) Dejeto Líquido de Suíno como Fertilizante Orgânico. 32 f. Instituto Agronômico do Paraná. Londrina, PR.
MIL-STD 1629A (1980) Procedures for performing a failure mode, effects and criticality analysis. Washington: Departamento de Defesa dos Estados Unidos da América. MOURA C (2000) Análise de Modo de Falha e Efeitos de Falha Potencial (FMEA). [S.I.: s.n.], 40 p. (Manual de referência). OTTO KN, WOOD KL (1998) Product evolution: a reverse engineering and redesign methodology, Research in Engineering Design, 10 (4): 226-243. PACIAROTTI C, MAZZUTO G, D’ETTORE D (2014) A revised FMEA application to the quality control management. International Journal of Quality & Reliability Management, 31(7): 788–810. PAHL G, BEITZ W, FELDHUSEN J, GROTE KH (2005). Projeto na engenharia: Fundamentos do desenvolvimento eficaz de produtos, métodos e aplicações. São Paulo: Edgard Blucher, 412 p. PARANHOS MM, BACHEGA SJ, TAVARES DM, CALIFE NFS (2016) Aplicação da análise de modo e efeitos de falha para o gerenciamento de riscos de um projeto. Sistemas & Gestão, 11(4): 444454. PEDROSA BMM (2014) Análise dos Modos de Falha e seus Efeitos (FMEA) aplicada a um Secador Industrial. 98f. Dissertação (Mestrado em Engenharia Mecânica) - Instituto Superior de Engenharia de Lisboa. PETROVSKIY EA, FEDOR AB, BUKHTIYAROV VV, SAVICH IV, GAGINA MV (2015) The FMEA -Risk Analysis of Oil and Gas Process Facilities with Hazard Assessment Based on Fuzzy Logic, Modern Applied Science, 9(5): 25-31. POLINSKY AM, SHAVELL S (2009) The uneasy case for product liability. Harvard Law Review, 123: 1437. KAGUEIAMA, HA (2012) Sistematização de técnicas de análise de falha e projeto para confiabilidade. 124 f. Dissertação (Mestrado em Engenharia Mecânica) - Universidade Federal de Santa Catarina, Florianópolis. KROLL E, CONDOOR SS, JANSSON DG (2001) Innovative conceptual design: theory and application of parameter analysis. Cambridge University Press. ROMANO, LN (2003) Modelo de Referência para o Processo de Desenvolvimento de Máquinas Agrícolas. 321f. Tese (Doutorado em Engenharia Mecânica) - Universidade Federal de Santa Catarina, Florianópolis. ROMANO LN, BACK N, OGLIARI A, MARINI VK (2005) An introduction to the reference model for the agricultural machinery development process. Product: Management & Development, 3(2), 109132 ROMANO LN (2013) Desenvolvimento de máquinas agrícolas: planejamento, projeto e produção. São Paulo: Blucher Acadêmico.
ROZENFELD H, FORCELLINI FA, AMARAL DC, TOLEDO JC, SILVA SL, ALLIPRANDINI, DH, SCALICE RK (2006) Gestão de desenvolvimento de produtos: uma referência para a melhoria do processo. São Paulo: Saraiva. SELVAN TA, JEGADHEESAN C, ASHOKA VP, SENTHILKUMAR KM (2013) A Novel FMEA approach for ranking mould designs in foundries. Life Science Journal, 10(2): 51-60. SCHERER EE (2011) O uso dos dejetos de suínos como fertilizante: sustentabilidade da atividade em propriedades familiares da região Oeste de SC. Jornal Dia de Campo, Publicado em 07 de Novembro de 2011, Disponível em http://www.diadecampo.com.br/zpublisher/materias/Materia.asp?id=25456&secao=Colunas%20e%20 Artigos, acesso em 16 de junho de 2020. SCHMITT JC (2013) Método de análise de falha utilizando a integração das ferramentas DMAIC, RCA, FTA E FMEA. 111 f. Dissertação (Mestrado em Engenharia de Produção) - Faculdade de Engenharia, Arquitetura e Urbanismo, Universidade Metodista de Piracicaba, Santa Bárbara d’Oeste. SCHRADER S, RIGGS WM, SMITH RP (1993) Choice over uncertainty and ambiguity in technical problem solving. Cambridge: MIT Sloan School of Management (WP #3533-93-BPS).
STARA S.A. (2020) Distribuidor de Arrasto à Lanço, Twister 5500 APS. Não-Me-Toque: Stara S. A. Disponível em https://stara.com.br/produto/twister-5500-ap/, acesso em 16 de junho de 2020. STONE RB, WOOD KL, CRAWFORD RH (2000) A heuristic method for identifying modules for product architectures. Design Studies, 21(1): 5-31. TAN JJ, OTTO KN, WOOD KL (2017) Relative impact of early versus late design decisions in systems development. Design Science, 3(1): 1-27. THOMKE SH (1998) Simulation, learning and R&D performance: Evidence from automotive development. Research Policy, 27(1): 55-74. THOMKE S, FUJIMOTO T (2000) The effect of “front‐loading” problem‐solving on product development performance. Journal of Product Innovation Management, 17(2): 128-142. TOLEDO JC, AMARAL DC (2008) FMEA - Análise do tipo e efeito de falha. São Carlos: GEPEQ/UFSCar. TONDIN R, DREGES AA, BARBOSA LA (2017) Melhoria no desenvolvimento de produto: uma aplicação da ferramenta FMEA, Espacios, 38(6): 18-34. ULLMAN DG (2010) The mechanical design process. New York: McGraw-Hill. XIAO N, HUANG HZ, LI Y, HE L, JIN T (2011) Multiple failure modes analysis and weighted risk priority number evaluation in FMEA. Engineering Failure Analysis, 18(4): 1162-1170. YANG K, EL-HAIK BS (2009) Design for Six Sigma: A Roadmap for Product Development. 2nd Edition. New York: McGraw-Hill. WHEELWRIGHT SC, CLARK KB (1992) Revolutionizing product development: quantum leaps in speed, efficiency, and quality. Simon and Schuster.