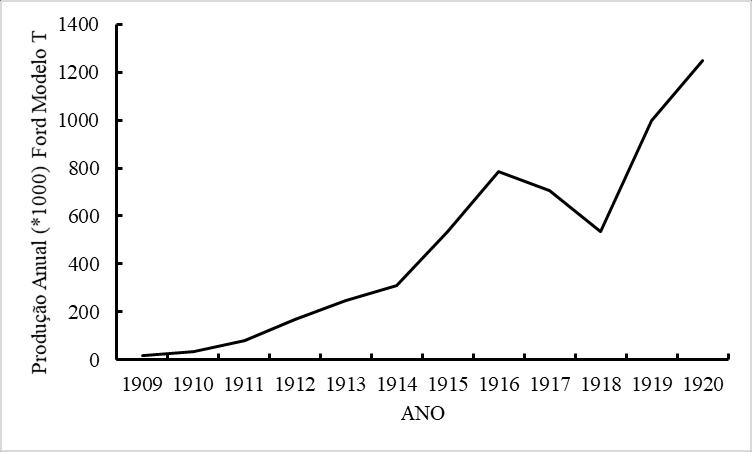
68 minute read
PIONEIRISMO, EXPERIMENTAÇÃO, FRACASSOS E SUCESSOS
AS RAÍZES PROFUNDAS DA PRODUÇÃO ENXUTA - LEAN PRODUCTION: DOS PRIMÓRDIOS DA REVOLUÇÃO INDUSTRIAL AOS DIAS DE HOJE. UMA HISTÓRIA DE PIONEIRISMO, EXPERIMENTAÇÃO, FRACASSOS E SUCESSOS
Marcos Milan
Advertisement
A revolução industrial tem as suas origens nos idos de 1700 na Inglaterra com a indústria têxtil. A atividade processava principalmente o algodão, matéria-prima vinda das colônias, e a água dos rios fornecia a energia necessária para o acionamento das máquinas. Ao longo dos anos, os aperfeiçoamentos introduzidos nas máquinas fizeram da Inglaterra a maior produtora de tecidos à base da fibra do algodão. Nessa mesma época, tem início um processo de grandes modificações na agricultura inglesa, com a incorporação de novos sistemas agrícolas, uso de fertilizantes, novas culturas e a invenção de máquinas e implementos tais como o cultivador mecânico e a semeadora mecânica em linhas, tendo como fonte de potência a tração animal. Como decorrência desses avanços constatou-se que, se em 1700, oitenta por cento da população inglesa dependia da terra para sobreviver, cem anos depois esse valor cairia para quarenta por cento. A população deixava o campo e se concentrava nas cidades à procura de uma oportunidade de trabalho, que a incipiente indústria proporcionava. A economia baseada na terra, mão de obra de baixa especialização, dependente da agricultura e mercados com pouca integração geográfica, começa a se transformar em uma economia fundamentada no capital, na menor dependência da agricultura, na mão de obra especializada e em mercados integrados geograficamente. Um ponto crucial para a aceleração das mudanças foi o aperfeiçoamento do motor a vapor pelo inventor escocês James Watt.
Historicamente, a primeira experiência empregando o vapor como fonte de potência foi a máquina térmica de Heron, eolípila, na Alexandria, Egito, no século I. Ao longo do tempo, foram desenvolvidos outros motores com esse mesmo este princípio, mas as restrições no funcionamento faziam com que as aplicações fossem bem limitadas. Em 1765, Watt apresentou um protótipo de motor a vapor que era um aperfeiçoamento de um modelo aplicado, com várias restrições, no bombeamento de água nas minas de carvão. O protótipo era mais eficiente e prático. Anos mais tarde, Watt introduziu um dispositivo para transformar o movimento retilíneo alternativo em movimento circular, expandindo a sua utilização, inclusive para o acionamento das máquinas na indústria têxtil. Em 1778 patenteou o regulador centrífugo, permitindo, com isso, controlar a velocidade do motor e ampliando as possibilidades de uso. Esses aperfeiçoamentos tornaram possível o desenvolvimento da locomotiva a vapor, máquina que revolucionou o transporte. O motor a vapor, que utilizava como fonte de energia o carvão mineral e a madeira, começa a substituir a energia humana, dos animais, hidráulica e eólica empregadas até então. Sendo mais barato e eficiente, ele impulsiona as indústrias em número e tamanho, o comércio e, consequentemente, a concorrência. A demanda por mão de obra se acentua nas novas fábricas, surgindo novos desafios referentes ao recrutamento, treinamento e motivação das pessoas para um ambiente inédito. A administração passa a ser vista como o quarto fator de produção, somando-se à terra, mão de obra e capital, esse último como fator principal (WREN, 2005), (KREIS, 2017).
O óleo de pedra
Na década de 1850, quando o mundo passava por modificações profundas tanto na economia como pelo aumento da população, um grupo de investidores solicitou a um professor de química da Universidade de Yale a análise de um líquido escuro e viscoso, proveniente do oeste da Pensilvânia, EUA. O líquido, conhecido como “rock oil, óleo de pedra”, ou “óleo de Sêneca”, denominação em referência a uma tribo de índios da região, brotava naturalmente à superfície e era recolhido manualmente. Ao “óleo de pedra” era atribuído o poder de cura, sendo usado para aliviar desde dor de dente a ferimentos em animais. O grupo de investidores sabia que o líquido era inflamável, mas havia dúvidas se poderia ser empregado para a iluminação artificial, que era um problema sério devido aos custos da gordura, animal ou vegetal, e do gás de carvão. Um líquido derivado da terebintina apresentava-se como uma opção mais barata, mas com a desvantagem de ser altamente inflamável. A resposta dada pelo professor foi que o “óleo de pedra”, quando submetido a diversos níveis de ebulição, gerava vários subprodutos e, dentre eles, havia um de alta qualidade para ser empregado na iluminação, mais tarde denominado de querosene. Uma etapa havia sido vencida, mas ainda existia um problema
maior associado à obtenção do “óleo de pedra” para a comercialização, pois a coleta manual não era adequada para os volumes requeridos para essa nova empreitada. Para extrair o “óleo de pedra” em volumes suficientes para atender ao novo negócio surgiu a ideia de aplicar o mesmo princípio da perfuração utilizado na extração do sal. Em 27 de agosto de 1859, após muitas dificuldades, a perfuração deu certo e o petróleo jorrou na região conhecida como “oil creek”, perto do vilarejo de Titusville na Pensilvânia, à época com 125 habitantes. Em 1860 foram extraídos 450 mil barris de “óleo de pedra” e, em 1862, três milhões, dando início a uma nova era na iluminação das cidades. Em fevereiro de 1865 em Cleveland, Ohio, EUA, uma sequência de eventos levou ao estabelecimento da Standard Oil, sob o comando de John D. Rockefeller, que veio a tornar-se a maior empresa de petróleo americana e do mundo. A partir de então, ela dominou o mercado e verticalizou toda a produção desde a extração, refino, transporte até a distribuição. Nas refinarias, além do querosene que era o principal negócio da indústria petrolífera, eram produzidos a nafta, solventes e os lubrificantes para atender às máquinas e locomotivas a vapor que a revolução industrial disseminava. Em 1882, Thomas A. Edison apresentou a lâmpada elétrica para o mundo e oito anos depois, em 1885, existiam aproximadamente 250 mil lâmpadas em uso nos EUA. A tecnologia também se espalhou para a Europa, tornando-se uma ameaça ao querosene e à indústria do “óleo de pedra”, (YERGIN, 2005).
A carruagem sem cavalos
A ameaça da iluminação elétrica ao “óleo de pedra” não durou muito tempo. Em 1876, o engenheiro alemão Nikolaus A. Otto apresentou o motor de combustão interna de quatro tempos, desenvolvido com base nas ideias do engenheiro belga Jean J.E. Lenoir, que queimava no seu interior uma mistura de gás de iluminação e ar e ficou conhecido como motor de ciclo Otto, ou por ignição. Em 1893, Rudolf Diesel obteve a patente de um novo tipo de motor de combustão interna, por compressão, que desde então foi denominado de ciclo Diesel, (BREEZE, 2018). Os novos motores de combustão interna eram mais leves, mais simples de usar e geravam mais potência do que o motor a vapor, tornando-se uma opção ideal para a “carruagem sem cavalos”. Em 1886, Karl F. M. Benz obtém a patente do primeiro automóvel com motor ciclo Otto empregando como combustível a gasolina, um derivado do petróleo, com as vendas ao público iniciadas em 1888. O carvão mineral como fonte de energia e o motor a vapor começam a ser substituídos pelo “óleo de pedra” e o motor de combustão interna. Com isso, a indústria do petróleo passa a dominar o cenário da energia, uma realidade ainda hoje. Vários fabricantes de automóveis surgiram e, embora as características básicas fossem mantidas, cada exemplar era único. A produção era artesanal, a maioria das peças eram produzidas em pequenas oficinas e entregues ao fabricante. Durante a montagem do veículo, que ficava estacionário, era necessário o emprego de mão de obra especializada para fazer os ajustes necessários ao encaixe das peças. Devido às características artesanais da produção, a quantidade era pequena, os veículos eram caros e difíceis de serem mantidos e somente os ricos tinham condições de possuir um. O panorama começa a mudar quando, em 1903, Henry Ford deu início às atividades da Ford Motor Company, com a visão de produzir automóveis baratos e de qualidade, para atender a maior parte da população, uma visão considerada como impossível de ser alcançada de acordo com as opiniões da época. Para ele estava claro que não seria possível produzir bons carros e de baixo custo com os métodos de produção empregados. A Ford Motor Company iniciou a produção como o modelo A e, em 1908, após três anos de pesquisas e testes, lançou o seu vigésimo projeto: o modelo T. Esse modelo de “carruagem sem cavalos” foi concebido para atender o público em geral. Para isso os conceitos adotados eram os de um veículo de baixo custo, construído com material de alta qualidade e resistente, simples de operar, com potência suficiente, confiável, leve e seguro nas diversas condições de operação. Henry Ford descreveu o novo modelo: “...Vou construir um carro para a grande multidão. Será grande o suficiente para a família, mas pequeno o suficiente para um indivíduo usar e cuidar. Será construído com os melhores materiais, pelos melhores homens a serem contratados, segundo os projetos mais simples que a engenharia moderna puder conceber. Mas o preço será tão baixo que nenhum homem com um bom salário será incapaz de ter um e desfrutar com sua família a bênção de horas de prazer nos grandes espaços abertos de Deus...”, (FORD, 2014: p52). Para construir esse carro de acordo com os princípios estabelecidos, a forma de produzir foi alterada e aperfeiçoada ao longo do tempo. A proposta para a montagem dos veículos foi trazer a
operação para a mão de obra, e não o inverso como era o padrão, colocar as ferramentas e a mão de obra em sequência, empregar um meio para levar as partes prontas para a próxima operação na menor distância possível. Os princípios da administração científica, desenvolvidos por Frederick Taylor, foram adaptados e implementados pela engenharia da empresa, envolvendo, dentre outros: a aplicação da metodologia científica para identificar a melhor forma de fazer as coisas, ao invés de confiar na maneira prática ,“rule of thumb”; seleção e treinamento da mão de obra e não simplesmente designar para o trabalho; monitoramento do desempenho; descrição detalhada dos procedimentos; motivação da mão de obra para emitir sugestões visando a melhoria das tarefas. A produção empregava também máquinas dedicadas, o que permitia a fabricação de peças em quantidade, mas diminuía a flexibilidade. A aplicação dos princípios de Taylor envolveu também a divisão de tarefas em etapas de forma que, com treinamento específico, qualquer pessoa fosse capaz de executá-la. A linha de montagem em movimento contínuo, que permitia ao trabalhador permanecer fixo em um local, só foi instalada após alguns anos do início da fabricação do modelo T. A ideia veio de uma visita dos engenheiros da Ford a um frigorífico em Chicago, onde observaram o emprego de carrinhos aéreos no desmembramento das carcaças, com os funcionários ocupando posições fixas, (TAYLOR, 1911; WOMAC et al., 2004; FORD, 2014; TOMAC et al., 2019). Esse novo sistema de produção incorporando técnicas da administração científica, os desenvolvimentos na própria empresa e a linha de montagem em movimento contínuo foram as bases para produção em massa. A produção em massa só foi possível devido à padronização e à intercambialidade das peças. Na produção artesanal, a mão de obra especializada era empregada para fazer os ajustes necessários para que as peças se encaixassem e, no final, um automóvel era diferente do outro. A intercambialidade já era empregada há dois mil anos na China, nos mecanismos de disparo dos arcos utilizados pelos soldados (KIBBLE, 2014). O emprego na indústria foi no período da guerra civil americana nos idos de 1860 para a fabricação dos rifles, mas existem relatos que 10.000 mosquetes foram produzidos com peças intercambiáveis na França em 1785 (STAUFFER, 2003). De acordo com WOMACK et al., (2004: p1415) “...a chave da produção em massa não residia - conforme muitas pessoas acreditavam ou acreditam – na linha de montagem em movimento contínuo. Pelo contrário, consistia na completa e consistente intercambialidade das peças e na facilidade de ajustá-las entre si... Ford insistiu que o mesmo sistema de medidas fosse usado ao longo de todo o processo de fabricação...”. A revolução na indústria de máquinas-ferramenta, originada pelos trabalhos de Taylor com ferramentas de aço rápido na Bethlehem Steel, ao final dos anos 1890, foi outro elemento fundamental para obter a padronização e a intercambialidade de peças de forma econômica, (PAXTON, 2012). Valendo-se das vantagens obtidas por esse novo sistema de fabricação, a Ford aumentou a sua produção, figura 1, e os outros fabricantes de automóveis seguiram por esse caminho. A produção artesanal ficou restrita a nichos, presentes ainda hoje, somente para as pessoas que podiam pagar o preço.
Figura 1. Produção do modelo T, touring car, período 1909-1920. Adaptado de (FORD, 2014: p100).
O aumento da produção anual de automóveis, de 18.000 em 1909 para 1.250.000 em 1920, demonstra o grande sucesso da empresa na inovação dos seus métodos de produção, atingindo a visão de Henry Ford quanto ao custo, qualidade e acessibilidade à maior parte da população, contrariando as opiniões iniciais. Com essa produção da Ford e de outras como a General Motors e a Chrysler, surge a
necessidade das revendas para atender à demanda de toda uma cadeia de apoio para os automóveis, desde as vendas à manutenção, e dos postos de serviço para o fornecimento de gasolina e outros produtos derivados de petróleo, além do atendimento aos motoristas. A ameaça ao querosene e à indústria do “óleo de pedra”, com a chegada da lâmpada elétrica, ficou no passado e a “carruagem sem cavalos” encontrou a energia, barata e fácil de armazenar, e o motor adequado para transformá-la em movimento.
O treinamento, o processo e o grupo
Alguns anos depois do início da produção em massa, a manufatura de veículos sofreu uma redução devido à participação dos Estados Unidos na Primeira Grande Guerra, conflito iniciado em 28 de julho de 1914 e encerrado em 11 de novembro de 1918. A indústria em geral volta-se à produção de materiais para atender às necessidades da guerra, bem como suprir os produtos cujas importações foram interrompidas pelo conflito. Uma das necessidades mais prementes era construção de navios, mas a atividade encontrava dificuldades pela falta de mão de obra especializada. Ciente do fato, o governo americano, por meio do “Emergency Fleet Board”, criou um comitê para desenvolver um programa de treinamento com objetivo de aumentar em dez vezes o número de trabalhadores especializados. Para tanto, o comitê contatou Charles Allen, um instrutor vocacional que havia desenvolvido um método de treinamento para as indústrias, fundamentado em quatro passos: preparação, apresentação, aplicação e acompanhamento. O primeiro passo prepara o aluno para o aprendizado, no segundo o instrutor fornece as instruções referentes ao trabalho a ser feito, no terceiro o aluno executa e os erros são corrigidos e no quarto passo, acompanhamento, o instrutor verifica se o aluno pode executar a tarefa de modo independente, sem supervisão. Allen destaca que os três fatores necessários para uma produção eficiente são o instrutor, o homem e o trabalho, título de seu livro publicado em 1919, “The instructor, the man and the job”. O aprendizado é assegurado se o instrutor ensinar corretamente e, se bem treinado, o homem realiza um bom trabalho e consequentemente a produção é eficiente (ALLEN, 1919; HUNTZINGER, 2002). Durante o período do conflito, mais precisamente em 1918, Walter Shewhart iniciou sua carreira na empresa Western Electric, um braço da AT&T, originalmente American Telephone and Telegraph Company, e, em 1924, transferiu-se para a Bell Telephone, também pertencente à AT&T, onde encerrou suas atividades em 1956. Shewhart possuía doutorado em física e, dentre importantes contribuições na área estatística desenvolveu a carta ou gráfico de controle, que permite avaliar se as variações que estão ocorrendo em um processo são rotineiras ou especiais. Outra contribuição foi o ciclo PDCA, - Plan, Do, Check, Act (Planejar, Fazer, Checar, Agir) - empregado na solução de problemas, na melhoria de processos e no desdobramento de estratégias. Dois membros da equipe de Shewhart, Dodge e Roming, elaboraram os conceitos referentes à teoria da amostragem, (STAUFFER, 2003). Em uma fábrica de equipamentos da Western Electric, localizada no bairro de Hawthorne, em Chicago, também pertencente ao conglomerado AT&T, teve lugar um dos primeiros experimentos das relações humanas no trabalho, iniciado em 1924 e encerrado em 1932. O objetivo inicial era testar os efeitos da iluminação na produtividade da mão de obra. Os resultados ao longo do período foram inconclusivos, pois, independentemente da intensidade de iluminação, a produtividade dos funcionários não se alterava e, muitas vezes, aumentava, ainda que em condições mais precárias. Em 1928, George Elton Mayo, um professor de Harvard com formação na área de filosofia e lógica, foi convidado a participar e após um período, em uma de suas visitas à fábrica, percebeu que a chave para explicar o que estava acontecendo no local era a atitude mental do grupo, “...Mayo sentiu que a notável mudança de atitude mental no grupo foi o fator chave para explicar o mistério de Hawthorne...”, (WREN, 2005).
As teorias da administração
A revolução industrial foi um divisor de águas para a ciência da administração, que pode ser entendida como a alocação de recursos físicos e humanos para atingir objetivos. Antes dela, a sociedade dependia dos artesões, ou da produção familiar, para obter os produtos para o dia a dia, tais como roupas, sapatos, utensílios e outros. Os artesões envolvidos com a manufatura reuniam-se em grupos, denominados “guildas”, e os seus membros se especializavam anos a fio no ofício. Seus produtos eram identificados com marcas, as hallmarks, que serviam também como um indicador da qualidade do produto. A sociedade era praticamente estática e as organizações desenvolviam as suas atividades para atender aos poderes da época, representados pelos reis e seus direitos divinos, pela igreja com seus
dogmas e pelos militares com a sua disciplina. Com isso havia pouco espaço para o desenvolvimento da administração. (STAUFFER 2003, WREIN, 2005). Com o advento da revolução industrial, as organizações tiveram de lidar com novos desafios, desde o controle dos custos, processos de fabricação, mão de obra e com a preocupação com a produtividade e eficiência no uso dos recursos. Esse período foi denominado pela administração de escola clássica, período no qual a preocupação das organizações estava voltada para a produtividade, ou eficiência, necessária para atender a uma demanda crescente do mercado. Como representantes dessa escola, além de Taylor e Ford, podem ser citados Adam Smith, Max Weber e Henry Fayol. Taylor empregou a metodologia científica para a melhoria do desempenho da mão de obra bem como a seleção e treinamento, bases do que foi denominado de administração científica. Para ele, o crescimento da produtividade traria também a melhoria da qualidade de vida da mão de obra com o aumento dos salários. Das principais contribuições de Ford destacam-se a linha de montagem contínua e, principalmente, a busca incessante pela padronização de componentes, sem a qual não teria sido possível a produção em massa. Adam Smith desenvolve os conceitos de liberalismo na economia, Fayol separa a administração da produção e Weber desenvolve os conceitos sobre a autoridade. Uma corrente dedicada a estudar o homem no ambiente de trabalho teve início com os experimentos de Hawthorne sendo denominada de enfoque comportamental. Ludwig von Bertalanffy, biólogo, observou que um organismo afeta e é afetado pelo ambiente no qual se encontra e que a realidade é feita de sistemas, sendo necessário avaliar as interrelações existentes e não só elementos isolados. Com base nesses princípios que estabeleceram a teoria dos sistemas, desenvolveu-se o conceito do enfoque sistêmico para as organizações, integrando os enfoques produtivo e o comportamental com o ambiente no qual a organização está inserida. O aumento da produção traz também desafios relacionados à qualidade. O artesão verificava um a um os seus produtos na busca por defeitos e as “hallmarks” eram uma espécie de selo de garantia. No início da revolução industrial esse mesmo procedimento era adotado pelos trabalhadores que verificavam os produtos um a um: a era da inspeção. Com os trabalhos de Shewhart e sua equipe nos laboratórios da Bell Telephone, a busca continua, mas passa a ser feita por amostragem e a responsabilidade não é mais do trabalhador, mas de um inspetor ou de um departamento de qualidade, iniciando a era do controle estatístico, (MAXIMIANO, 2000). As ideias da administração científica e produção em massa atraíram o interesse de vários países como a Inglaterra, França, Alemanha, Japão e até da União Soviética. No Japão, os relatos datam de 1912, com a tradução do livro de Taylor para o japonês, dos artigos que descreviam o trabalho de Taylor e Frank B. Gilbreth e a aplicação dos princípios da administração científica na indústria têxtil, (WREN, 2005). Após a primeira grande guerra, os Estados Unidos tornaram-se a maior potência industrial e a administração científica disseminou-se mundialmente. Em 1939, na noite do dia 31 de agosto, um incidente, ou uma encenação, ocorrido na cidade alemã de Gleiwitz, na fronteira com a Polônia, foi usado como justificativa para a invasão desse país pelas tropas alemãs no dia 1 de setembro (GILBERT, 2014). Era o início da II Grande Guerra Mundial, conflito que se alastrou pelo mundo e cujo término ocorreu com a rendição do Japão em 15 de agosto de 1945.
Learn by doing - Aprender fazendo
Em 1940, a preocupação com a guerra na Europa aumentou e o governo americano deu início às providências para reforçar as defesas, fornecer aos aliados armamentos, material, alimentos e, inclusive, o “óleo de pedra”, sendo os EUA, à época, o seu maior produtor. O governo estabeleceu grupos de emergência para lidar com o conflito e adaptar a indústria para atender às necessidades crescentes de produção e à escassez da mão de obra especializada, que essa nova situação traria. Um dos primeiros grupos de emergência foi o “Training Within Industry - TWI”, destinado a treinar a mão de obra para suprir às demandas de produção. O TWI era constituído por programas voltados para o nível de supervisão, três deles iniciando com a letra J de “job”, trabalho. O primeiro, “Job Instruction” -Instrução para o Trabalho – indicado para auxiliar os supervisores das empresas a treinar a mão de obra foi fundamentado nos quatro passos desenvolvidos por Charles Allen em 1919. O segundo, “Job Methods for Process Improvement” - Métodos de Trabalho para a Melhoria de Processos - utilizava os conceitos da administração científica para treinar os supervisores a desenvolver melhorias nos processos e evitar falhas ou melhorias incompletas. O terceiro, “Job Relations” - Relações no Trabalho - ensinava os supervisores a lidar com as pessoas. O quarto, “Program Development” -Desenvolvimento do Programa
- versava sobre como administrar o treinamento dentro da própria empresa usando as instalações e pessoal próprios. O TWI foi liderado por Channing R. Dooley, Walter Dietz, Mike Kane e Willian Conover, que ficaram conhecidos como “The Four Horsemen”, devido à liderança exercida e aos trabalhos desenvolvidos. Com exceção de Conover, os outros três tiveram contato com o método empregado por Charles Allen. Mike Kane havia trabalhado diretamente com Allen, durante o período da I Guerra. No período do conflito, mais de 1,7 milhão de pessoas foram treinadas e mais de 16000 indústrias atendidas, envolvendo tanto as destinadas à fabricação da bomba atômica, como as de petróleo, carvão, aeronáutica, automobilística, naval, ferroviária, entre outras. Os resultados do programa, com base em 600 empresas, mostraram uma melhoria nos seus índices de, no mínimo, vinte e cinco por cento referentes ao aumento da produção, redução de resíduos, reclamações, tempo de treinamento e horas trabalhadas, (DIETZ,1970; ROBINSON & SCHROEDER, 1993; HUNTZINGER, 2002).
O CWQC e a Qualidade Total
Terminado o conflito, o mundo apresentava-se totalmente modificado e, sem que ninguém notasse, as bases de uma nova forma de produção industrial estavam lançadas. Novamente, a indústria americana estava em condições de atender às demandas e, sem concorrência, os seus produtos espalharam-se pelo mundo. O programa TWI, desenhado para o tempo de guerra, foi desativado e praticamente desapareceu nos EUA, embora iniciativas da aplicação dos 3 Js fossem registradas em outros países, como por exemplo na Nova Zelândia em 1947, (DIETZ, 1970). Nesse mesmo ano, o plano Marshall foi criado pelo governo americano com finalidades políticas de fazer frente ao regime soviético e de reconstruir a economia dos países após o conflito mundial. Um dos países beneficiados com o plano Marshall foi o Japão. As tropas americanas ocuparam o país entre 1945 e 1952 e um dos seus objetivos era o de recuperar a capacidade industrial, minimizando assim os problemas sociais. A indústria japonesa ao final da guerra operava com menos de dez por cento de sua capacidade em relação ao período de 1935 a 1937. Como muitos dos membros da força de ocupação haviam trabalhado com o programa TWI nos EUA, foi quase que natural que o programa fosse levado para o Japão, o que aconteceu nos idos de 1947 a 1948 sob a responsabilidade de Lowell Mellen, presidente da TWI Inc. Durante a guerra, Mellen organizava os cursos 3 Js e, logo após o término do conflito, criou a empresa para atuar na área de treinamento. Mesmo após a saída das tropas de ocupação do Japão, o programa continuou e mais de um milhão de gerentes e supervisores haviam sido treinados nos conceitos até o ano de 1966 (ROBINSON & SCHROEDER, 1993). Além dos especialistas em TWI, técnicos, engenheiros e cientistas foram convidados para ir ao Japão para auxiliar nas atividades de reconstrução e, dentre eles, dois nomes se destacaram: Willian Edwards Deming e Joseph Moses Juran. As contribuições de Deming e Juran em conjunto com as de Kaoru Ishikawa, e as ideias de Armando Feigenbaum e Philip Bayard Crosby formaram as bases da era da qualidade total. A qualidade total atua de forma sistêmica, com foco na prevenção de defeitos e não na correção, e é voltada para atender às necessidades dos clientes, sendo de responsabilidade de todos na empresa e não somente do inspetor ou de um departamento, (MAXIMIANO, 2000). Deming, com formação na área de física e especialista na área estatística, trabalhou no Departamento de Agricultura, na Agência de Censo Americana e durante a II Guerra treinou, em técnicas de estatística, engenheiros e técnicos envolvidos com a fabricação de equipamentos. Deming conhecia os trabalhos desenvolvidos por Shewhart apresentados em reuniões no ano de 1927 e por uma série de quatro aulas, sobre controle estatístico da qualidade, ministradas por Shewhart em 1938. Deming viajou ao Japão em 1947, enviado pelo governo americano para trabalhar junto às tropas de ocupação. Em 1950, foi convidado pela Union of Japanese Scientists and Engineers, JUSE, - União Japonesa de Cientistas e Engenheiros -estabelecida em 1946, para desenvolver e ministrar treinamentos sobre o controle estatístico da qualidade. Após o término do período de ocupação, Deming continuou a visitar o Japão para consultorias e treinamentos, o que o fez por mais de três décadas. As suas contribuições envolveram o estabelecimento dos 14 princípios da qualidade, a disseminação da carta de controle e do emprego do PDCA, ciclo de Deming, embora a origem do PDCA deva ser creditada a Shewhart. O seu trabalho foi mais voltado para os métodos estatísticos e, em reconhecimento a toda a sua contribuição, a JUSE instituiu o Prêmio Deming, em 1951. Em 1954, Juran recebeu um convite da JUSE para ministrar treinamentos de controle de qualidade e gerenciamento. Formado em engenharia elétrica, iniciou a sua carreira em 1926 na Western Electric, onde tomou contato com as ideias de
Shewhart quanto ao controle estatístico da qualidade. O convite da JUSE foi feito em função, principalmente, da publicação de seu livro, Quality Control Handbook, em que aborda o conceito da trilogia da qualidade: planejamento, controle e melhoria da qualidade. Também elaborou o entendimento de que os problemas críticos devem ser resolvidos primeiro, “poucos vitais e muitos triviais”, princípio de Pareto ou regra 80/20, e que a qualidade é responsabilidade de todos. As contribuições de Juran fizeram com que a JUSE mudasse o foco dos treinamentos, introduzindo a gestão no ambiente extremamente técnico do controle estatístico. Ishikawa, formado em engenharia química, desempenhou um importante papel na área da qualidade no Japão. Em 1949, em uma das primeiras atividades da JUSE, participou de um grupo de pesquisa em controle de qualidade: o Quality Control Research Group, QCRG. Destacou a importância dos círculos de qualidade e a necessidade do treinamento contínuo. Criou o diagrama de causa e efeito, também conhecido como espinha de peixe ou diagrama de Ishikawa, em sua homenagem. Estabeleceu algumas técnicas que todos na empresa deveriam conhecer, as sete ferramentas da qualidade: folha de verificação, histograma, fluxograma, diagrama de causa e efeito, diagrama de Pareto, diagrama de dispersão e carta de controle. Ressaltou que com as sete ferramentas é possível resolver 95% dos problemas. Ishikawa defendia a ideia de que as características de um produto devem ser estabelecidas com base nas necessidades do cliente e não pela engenharia. A frase, “the next process is your customer”, o próximo processo é o seu cliente, é creditada a ele. Feigenbaun empregou o termo “Total Quality Control- TQC”, Controle Total da Qualidade, pela primeira vez em 1950. Desenvolveu a sua carreira na General Electric Company, e um dos pontos principais de sua obra destaca que a qualidade deve ser vista como um sistema, depende e é um problema de todos, e quem a define é o cliente. Crosby introduziu os conceitos do “zero defeito”, qualidade é prevenção e que a qualidade não tem custo, o que custa é não fazer as coisas certas na primeira vez. Iniciou a sua carreira na Crosley Corporation e, a partir de 1965, foi convidado para ser diretor de qualidade da ITT Corporation, (WREN, 2005; KRUGER, 2001; TACHIKI, 2008; TOLEDO et al., 2013). Esse ambiente que permitiu a combinação de várias técnicas e conceitos deu origem ao modelo japonês de administração denominado de Total Quality Control, TQC, Controle da Qualidade Total, que difere do TQC de Feingenbaum por ser um sistema “... baseado na participação de todos os setores da empresa e de todos os empregados no estudo e condução do controle da qualidade...”, (CAMPOS, 1999). O acrônimo TQC japonês causava confusão com o de Feingenbaum e, por isso, a decisão de renomeá-lo como CWQC, Company Wide Quality Control, Controle da Qualidade por Toda a Empresa, (ISHIKAWA, 1986). O CWQC, também conhecido no ocidente como Gestão da Qualidade Total, incorpora os conceitos e técnicas da teoria clássica, dos enfoques comportamental e sistêmico, das eras da qualidade, do TWI -principalmente dos 3 Js - além de outros conceitos. Ele pode ser definido como um sistema de gestão que envolve desde o diretor à mais simples função visando atender às necessidades dos clientes. O sistema é voltado para os clientes, os quais, no sentido mais amplo, são denominados de consumidores, stakeholders, englobando, além do cliente final, acionistas, colaboradores, sociedade e fornecedores. Os produtos devem atender às demandas dos consumidores quanto à qualidade, produtividade, custo, moral e segurança. O CWQC “...é baseado em elementos de várias fontes: emprega o método cartesiano, aproveita muito do trabalho de Taylor, utiliza o controle estatístico do processo cujos fundamentos foram lançados por Shewhart, adota os conceitos sobre o comportamento humano lançados por Maslow e aproveita todo o conhecimento ocidental sobre qualidade, principalmente o trabalho de Juran...é um modelo administrativo...”, (CAMPOS, 1999). Nos meados da década de 1960, de uma situação na qual eram conhecidos no exterior por serem baratos, não confiáveis e descartáveis, os produtos japoneses passam a igualar e a superar, em qualidade, desempenho e preço, os produtos americanos e europeus em vários segmentos, desde o aço, navios, eletrônicos, automóveis, motocicletas, dentre outros. Essa mudança de paradigma levantou a questão, “...O que aconteceu durante as últimas três décadas para permitir que os japoneses alterassem as imagens dos seus produtos passando de má qualidade e inferiores, para de qualidade superior, nos mercados doméstico e internacional...?”, (EBRAHIMPOUR, 1985). A resposta estava no sistema de manufatura, o CWQC. Esse sistema fez com que o Japão se transformasse em um dos grandes players do mercado mundial, mesmo não tendo à disposição recursos naturais como o petróleo e o minério. Em novembro de 1988, vinte executivos europeus iniciaram um tour pelo Japão para visitar nove empresas que eram destaque no emprego do CWQC nos setores automobilístico, têxtil, abastecimento,
siderúrgico, cosmético e eletrônico. Diversos pontos chamaram a atenção e dentre eles a limpeza das instalações, o número anual de sugestões de melhorias fornecidas pelos colaboradores e aproveitadas pela empresa, os estoques reduzidos, a inspeção feita pelo colaborador, a prevenção de defeitos, os dispositivos à prova de erros, a gestão à vista, os grupos de melhoria, a manutenção produtiva total, os treinamentos ministrados pelos supervisores, o Just in Time -JIT-, o uso das ferramentas estatísticas da qualidade, o emprego do Failure Mode and Effects Analysis, FMEA, - Análise do Modo e Efeito de Falha - e do FTA, Fault Tree Analysis, - Análise da Árvore de Falhas , o set-up rápido, o número de componentes com defeitos na ordem de cinco ou seis por milhão, entre outros conceitos e técnicas do CWQC empregados de forma sistêmica, (ATKINSON, 1989).
O T e o D: A criação de uma indústria automobilística
A história de um dos maiores fabricantes de automóveis está ligada à indústria têxtil. O ponto de partida é em 1896 com o desenvolvimento do primeiro tear movido a vapor no Japão por Sakichi Toyoda. Anos mais tarde, em 1914, ele funda a Toyoda Automatic Weaving Factory, que, em 1918, passa a se chamar Toyoda Cotton Spinning & Weaving Co. Em 1924, a empresa lança o primeiro tear automático. Em 1929, com a percepção de que o negócio de teares iria passar por tempos difíceis, decidiu-se investir em um ramo da indústria em pleno crescimento, a fabricação de automóveis. Até esse momento, o mercado japonês era abastecido pelas subsidiárias da Ford e da General Motors instaladas no país em 1920. Em 1930, em uma pequena área dentro da fábrica de teares, as pesquisas sobre o novo negócio começaram e, em 1937, com capital proveniente da empresa, a Toyota Motor Company iniciou as suas atividades, sob o comando de Kiichiro Toyoda, filho de Sakichi. O t substituiu o d como resultado de um concurso público no qual mais de 27000 pessoas participaram da escolha do nome para a nova empresa automobilística. Praticamente dois anos após o início das atividades, fabricando caminhões e automóveis com técnicas consideradas ultrapassadas e com baixa produtividade, a produção da Toyota foi interrompida devido ao começo do segundo conflito mundial. Com o término da guerra, em 1950, as dificuldades econômicas pelas quais a empresa passava e problemas com os trabalhadores levaram à renúncia de Kiichiro, substituído pelo seu primo Eiji Toyoda, engenheiro mecânico. Nesse mesmo ano, Eiji visitou a fábrica da Ford em Detroit que produzia 7.000 carros por dia enquanto a Toyota, em 13 anos, havia produzido aproximadamente 2.700. Eiji voltou com a ideia de implantar a produção em massa, com adaptações, e igualar a produção da Ford em um curto período, mas as dificuldades eram enormes. As empresas americanas produziam grandes quantidades de um número pequeno de modelos para alcançar a economia de escala, tinham muitos recursos e mercados para escoar a produção. O mercado japonês a ser atendido era pequeno, necessitava de diferentes tipos de veículos e os recursos financeiros da empresa eram escassos. Um ponto crucial observado por Eiji na fábrica da Ford foram os desperdícios associados à produção em massa. Na Toyota, havia outra pessoa preocupada com desperdícios: o engenheiro Taiichi Ohno. Ohno se formou em engenharia mecânica e começou a trabalhar na Toyoda Cotton Spinning & Weaving Co em 1932, transferindo-se para a Toyota Motor Company em 1943, como gerente geral de uma planta. Quando ainda estava na Toyoda Cotton, soube que, em geral, eram necessários dez japoneses para produzir o mesmo que um americano. Esta diferença, segundo ele, só poderia ser atribuída ao desperdício, muda em japonês, e se fosse possível eliminá-lo, a produtividade aumentaria em dez vezes. No início dos anos 50, tendo como foco eliminar desperdícios, Eiji e Ohno iniciaram uma jornada que iria a mudar a forma de fabricar veículos. A ideia central estava apoiada em dois pilares, Just-in-Time e auto-activation. Justin-Time significando que, na montagem de um veículo, as peças devem chegar no momento e quantidade certos, eliminando os estoques. A auto-activation, autonomação, refere-se a dispositivos automáticos de parada instalados nas máquinas. A autonomação, jidoka, foi uma invenção de Saikichi aplicada aos teares e trazida por Ohno para a linha de montagem. Se acontece alguma coisa fora do padrão durante o trabalho da máquina ela para, impedindo a fabricação de produtos defeituosos. (OHNO, 1997; DAHLGAARD & DAHLGAARD-PARK, 2006; WADA, 2006; HOLWEG, 2007).
O choque do “óleo de pedra” e o segredo
O Oriente Médio já havia ultrapassado os Estados Unidos como maior produtor mundial de petróleo quando, em outubro de 1973, tem início a guerra do Yom Kippur e o petróleo foi empregado pela primeira vez como arma, na forma de um embargo. De uma commodity abundante e barata, que havia impulsionado a economia global ao longo das décadas, principalmente de 1950 e 1960, o embargo
da principal fonte de energia fez com que o preço do barril praticamente quadruplicasse, afetando profundamente os países. Este foi o primeiro choque do petróleo. O segundo choque veio com a renúncia e o exílio do Xá Mohammed Reza Pahlavi do Irã, em janeiro de 1979, e a implantação do regime dos Aiatolás, a Revolução Islâmica. A produção de petróleo do Irã, um dos maiores produtores do Oriente Médio, praticamente cessou e os preços aumentaram em 30%, com novos reflexos na economia, que ainda mal se recuperava do primeiro choque, (YERGIN, 2010).
Mais uma vez o “óleo de pedra” interfere, agora de forma indireta, com a indústria do automóvel. Se na primeira vez foi devido à forma líquida, abundante e barata da fonte de energia para alimentar os motores das “carruagens sem cavalos”, agora o foi pela escassez e preços. Mesmo antes da crise do petróleo, a preocupação no mundo ocidental com a concorrência já era uma realidade, principalmente com produtos vindos do Japão e se estendia à indústria automobilística americana bem como à europeia. Em 1980, a participação nas vendas dos veículos importados atingia aproximadamente 22% do mercado, principalmente de carros japoneses. Várias justificativas eram dadas para esse domínio, e dentre elas que o custo da mão de obra era menor, a relação iene-dólar era favorável, a cultura e a dedicação do povo que permitia uma eficiência maior nas fábricas, a política de exportação do governo japonês, o emprego da automação e até a sorte, pois os carros eram mais eficientes no uso do combustível justamente na época da crise do petróleo, (HOLWEG, 2006).
De acordo com Ohno, a realidade era outra: “...A crise do petróleo no outono de 1973, seguida pela recessão, afetou governos, empresas e sociedades no mundo inteiro. Em 1974, a economia japonesa havia caído para um nível de crescimento zero e muitas empresas estavam com problemas. Mas na Toyota, embora os lucros tivessem diminuído, os ganhos eram maiores do que os de outras empresas e foram mantidos em 1975, 1976 e 1977. A diferença cada vez maior entre ela e as outras fez com que as pessoas perguntassem sobre o que estaria acontecendo na Toyota. Antes da crise do petróleo, quando conversava com as pessoas sobre tecnologia de fabricação e o sistema de produção da Toyota, o tema despertava pouco interesse....”, OHNO (1997). O segredo do aumento das vendas não estava relacionado ao custo da mão de obra, à cultura, ou à automação, mas sim ao método de fabricação dos carros. No dia a dia, a opinião dos usuários americanos era que os carros tinham preços competitivos, apresentavam um bom desempenho, não quebravam, e, em tempos de combustível caro, consumir menos fazia toda a diferença. Uma pesquisa revelou que de 38 modelos mais confiáveis do mercado americano, 15 eram da marca Toyota ou Lexus, esta última, marca de carros de luxo da empresa. O recall de veículos da Toyota por problemas de pósvenda era 72% e 92% menor do que os da Ford e da Chrysler respectivamente. Enquanto o mundo ocidental continuava com a produção em massa, as ideias de Eiji, Ohno e seus colaboradores, iniciadas há mais de 20 anos antes do primeiro choque do petróleo, tinham criado uma forma diferente de fabricar veículos: o Toyota Production System, TPS - Sistema Toyota de Produção, STP. A ideia central do sistema de eliminar desperdícios, muda, estava dando os seus frutos. Superprodução, espera (tempo sem trabalho), transporte ou movimentação desnecessários, super processamento ou processamento incorreto, excesso de estoque, movimento desnecessário e defeitos foram os sete desperdícios identificados pela Toyota aos quais Jeffrey Liker acrescentou mais um: o desperdício da criatividade dos funcionários. O STP não é um conjunto de ferramentas aplicado aleatoriamente. Ele é um modo de produção integrado a um modelo, sistêmico, o modelo Toyota, que é dividido em quatro categorias denominadas 4 Ps, iniciais das palavras em inglês: Philosophy - Filosofia; Process - Processo; People/Partners - Funcionários e Parceiros; Problem Solving - Solução de Problemas. Os Ps contêm os 14 princípios que norteiam a Toyota. O primeiro, filosofia, estabelece que as decisões administrativas têm de ser tomadas visando objetivos de longo prazo e não apenas retornos imediatos. O segundo P, processo, contém os princípios do STP para a eliminação de desperdícios. O terceiro trata dos princípios aplicados ao desenvolvimento das pessoas e fornecedores e o quarto à aprendizagem organizacional e à melhoria contínua. Os 14 princípios contidos nos Ps representam a base para o desenvolvimento dos conceitos e técnicas do STP como a gestão à vista, os processos estáveis, a produção nivelada, - hinjuka -, o conceito do takt-time que determina o ritmo da demanda associado ao just-in-time, o conceito andon para comunicar problemas e relacionado à autonomação (automação com toque humano), o gengi genbutsu cujo significado é “ver por si mesmo para entender a situação” e associado à redução de perdas, entre outros. Os 4 Ps e os conceitos e técnicas do STP, figura 2, fornecem o suporte para atingir os objetivos de melhor qualidade, menor custo, menor lead-time - menor tempo de ciclo -, mais segurança e moral alto, (LIKER, 2005).
Melhor qualidade-Menor Custo-Menor lead-time_ Mais Segurança-Moral Alto
através da redução do fluxo de produção pela eliminação de perdas
Just-in-time
Peça certa, Quantidade certa, Tempo certo
Pessoas e Equipes de Trabalho
_Seleção _Ringi na Decisão _Metas Comuns _Treinamento
Autonomação (Qualidade no setor) Tornar os problemas visíveis
_Planejamento takt time _Fluxo contínuo _Sistema puxado _Troca Rápida _Logística Integrada
Melhoria Contínua
Redução de perdas
_Gengi Genbutsu _Visão de perdas _5 porquês _Solução de Problemas
Produção nivelada (heinjuka)
Processos estáveis e padronizados Gerenciamento Visual _Parada automática _Andon _Separação pessoamáquina _Verificação de erro _Controle de qualidade no setor _Solução na origem dos problemas (5 porquês)
P_Problem Solving - SOLUÇÃO DE PROBLEMAS: Aprendizagem e melhoria contínua P_People/Partners - FUNCIONÁRIOS E PARCEIROS: Respeitar, Desafiar e Desenvolver. P_Process - PROCESSO: Eliminação de perdas P_Philosophy - FILOSOFIA: Pensamento de longo prazo
Figura 2. Fundamentos do modelo Toyota, 4Ps e o Sistema Toyota de Produção, STP. (Adaptado de LIKER, 2005).
Da mesma forma que a Ford mudou o sistema de produção de automóveis, de artesanal para a produção em massa, por meio do aprendizado, desenvolvimento e aperfeiçoamento de técnicas de produção e gestão, a Toyota também o fez, aperfeiçoando o seu modelo ao longo dos anos e mudou a forma de produzir automóveis. Eiji e Ohno foram aos EUA por diversas vezes para estudar as técnicas empregadas, principalmente na Ford e em indústrias de outros setores. Ohno, além dos conhecimentos que trouxe da indústria têxtil, adaptou a forma de trabalho dos supermercados americanos no desenvolvimento do justin-time: o cliente escolhe as coisas de que precisa, no momento e na quantidade desejados. Ele também desenvolveu os “5 Por Quês?” para encontrar a causa raiz do problema (OHNO 1997). A troca rápida de ferramentas, set-up rápido, desenvolvida pelo professor Shigeo Shingo, consultor da Toyota, é uma das principais técnicas do STP com relação à flexibilidade na linha de produção (SHINGO, 1996). Além da visão, das ideias e do trabalho desenvolvido por Eiji e Ohno, o modelo emprega os princípios da escola clássica com as ideias de Taylor relacionadas à administração científica e as de Ford com a produção em massa. Os conceitos do enfoque comportamental, no qual Hawthorne foi um marco, são aplicados com base nas hierarquias das necessidades de Abraham A. Maslow e na teoria dos dois fatores de Frederick Herzberg, (LIKER, 2005). É importante destacar o programa TWI e o papel da JUSE no aumento da competitividade dos produtos japoneses, principalmente da Toyota. A empresa foi uma das primeiras a participar do TWI e dos treinamentos em controle estatístico da qualidade. Em 1950, durante a crise que levou à renúncia do seu presidente e fundador, um dos requisitos do acordo com sindicato foi criar uma forma de treinar e desenvolver os supervisores. O programa TWI foi escolhido pela empresa e, em 1951, o primeiro curso foi introduzido, First Job Instruction - JI -, em 1952 Job Methods - JM -e em 1953 Job Relations - JR. Mais de 300 pessoas foram treinadas em cada um deles. A partir desses cursos, a empresa desenvolveu a sua própria versão do programa, Toyota Training Within Industry, TTWI, com o JI considerado como o mais importante dos Js por conter: método para divisão do trabalho; quatro passos necessários para o treinamento; desenvolvimento de uma matriz de planejamento de habilidades multifuncional. Devido à
falta de profundidade nos conceitos sobre eliminação de desperdícios e por não ter conexão com takttime, com a produção puxada e o fluxo de trabalho, o JM foi substituído pelos P-courses, com base nas ideias ministradas por Shigeo Shingo para a Toyota, (Kato, 2006). Materiais empregados no treinamento TWI no Japão foram encontrados na fábrica da New United Motor Manufacturing Inc, NUMMI, dos Estados Unidos, uma joint venturi entre a General Motors e a Toyota, que iniciou as atividades em 1984. O método de treinamento desenvolvido por Charles Allen em 1919, quatro passos, e incluído no programa TWI durante a II Grande Guerra, “Job Instruction”, foi encontrado nos materiais de treinamento de uma empresa de consultoria, juntamente com as perguntas do 5W1H: “Why?” - Por Que?”; “What?- O Que?” ; “How?- Como?”; “Who?-Quem?”; “Where?- Onde?”; “When?- Quando?”. A empresa era formada por pessoas que vieram da Toyota, (HUNTZINGER, 2002). O CWQC tem parte de suas raízes no TWI, além de incorporar os ensinamentos de Deming, Juran, Ishikawa e outros. Juran foi um dos primeiros a destacar as diferentes formas de desperdício, denominando-as de “the gold in the mine”, - o ouro na mina - e, mais tarde, de custo da não qualidade, (DAALGHARD & DAALGHARD-PARK 2006). O CWQC revolucionou o modo de trabalho das empresas japonesas, o que fez com que os produtos deste país, em diversos segmentos, conquistassem o mundo. O modelo Toyota, desenvolvido e aprimorado ao longo dos anos, emprega os princípios do CWQC além de outras técnicas desenvolvidas na própria empresa, muitas delas na forma de tentativa e erro. O termo “Fordismo” descreve o modo de gestão empregado pela Ford na produção de veículos a produção em massa - que pode ser considerado a primeira revolução automobilística, substituto da produção artesanal. Womack et al, (2004), em uma pesquisa sobre o futuro do automóvel realizada no Massachusetts Institute of Technology – MIT , apresentam na capa do livro “A Máquina que Mudou o Mundo”, que descreve os resultados dos trabalhos, uma frase que caracteriza a mudança na forma de produzir veículos: “A arma secreta do Japão, da produção em massa para a produção enxuta: a segunda revolução automobilística”. A segunda revolução foi o “Toyotismo”.
Lean Production e Lean Six Sigma
O Lean Production, Produção Enxuta, surge como uma denominação para as novas técnicas empregadas pela indústria japonesa, diferenciando-as da produção em massa da indústria automobilística ocidental. O termo foi criado por John Krafcik que trabalhou na NUMMI e depois foi pesquisador junto ao International Motor Vehicle Program – IMVP , do MIT, quando cunhou a expressão. Iniciado em 1985, o programa IMVP foi desenvolvido para analisar as razões por trás do sucesso da indústria automobilística japonesa que, em plena recessão causada pelos choques do petróleo, estava invadindo o mercado mundial. Os fabricantes japoneses produziam os veículos sob demanda por meio da produção puxada, empregando máquinas flexíveis, profissionais atuando em funções múltiplas, estoques reduzidos ocupando menos espaços, set-up rápido, produzindo grandes quantidades de diversos modelos, com custo inferior e qualidade superior em relação aos métodos vigentes na época. Por produzir somente o necessário e sem desperdícios, como na produção artesanal, suscitou a denominação Lean Production dada por Krafick. Enquanto isso, os grandes fabricantes tradicionais empregavam os conceitos da produção em massa, operando com máquinas e profissionais especializados, instalações produzindo grandes quantidades de poucos modelos, produção empurrada, com várias folgas no sistema abrangendo desde material a pessoas e espaço, a um custo maior e com qualidade inferior, (WOMACK et al, 2004). No princípio, o Lean Production foi associado ao modo de manufatura utilizado no Japão sobretudo em relação ao TPS, Toyota Production System, que se tornou um referencial, benchmark. O termo passou a ser conhecido após a publicação do livro “A Máquina que Mudou o Mundo” e, com o tempo, ganhou forma própria sendo empregado para caracterizar o modo de manufatura, difundido em praticamente todos os segmentos ao redor do mundo, desde o eletrônico, automobilístico, têxtil, alimentício, financeiro, entre outros, (Bhamu & Sangwan, 2014). Inicialmente, o termo foi empregado para designar um conjunto de técnicas aplicadas à produção, como 5Ss, kanban, padronização da rotina e set-up rápido. Porém, sem resultados promissores, houve a percepção de que a aplicação do Lean deveria ser realizada de forma sistêmica, com foco na mudança da cultura organizacional, utilizando fundamentos básicos norteadores: identificar, mapear e criar o fluxo de valor, sistema puxado e redução de desperdícios, (YAMAMOTO & BELLGRAN, 2010). O Lean Production tem de ser entendido como um sistema de gestão, e empregado dessa forma. Para que a organização alcance os resultados desejados, ela deve desenvolver a cultura da eliminação
de desperdícios e melhoria contínua, figura 3. O cliente e o processo constituem o foco da organização. A base do sistema está fundamentada em conceitos e ferramentas de forma estruturada, sistêmica, como a padronização dos processos, troca rápida, organização dos espaços, produção flexível, envolvimento das equipes, gestão à vista, dispositivos à prova de erros, células de trabalho, programação uniforme de modelos mistos. Esses mesmos conceitos e ferramentas fornecem o suporte para os pilares constituídos pelo seis sigma, design robusto, fluxo unitário, kanban, manutenção produtiva total (TPM) e parceria com os fornecedores. A implantação não precisa ser de forma semelhante à construção de um prédio, da base para o topo, mas pela escolha das ferramentas da base e dos pilares de acordo com a situação da organização e desenvolvida aos poucos, com constância de propósito (NICHOLAS & SONI, 2006).
FOCONO CLIENTE
FOCONO PROCESSO
Eliminar Desperdícios Melhoria Contínua
Design Robusto
Seis Sigma Fluxo Unitário Manutenção Produtiva Total
Kanban
Parceria Fornecedores
Dispositivos à prova de erros Células de trabalho Programação uniforme de modelos mistos
Produção flexível Envolvimento das equipes Gestão à Vista
Padronização dos processos Troca rápida Organização dos espaços
Figura 3. Sistema Lean Production- Produção Enxuta (Adaptado de NICHOLAS & SONI, 2006).
Em um dos pilares do sistema Lean aparece o six sigma, seis sigma, metodologia estatística que foi introduzida nos Estados Unidos em 1985 pela Florida Electric Power (FPL), quando a empresa buscou o apoio da JUSE para participar do prêmio Deming. O six sigma passa a ter contornos de um sistema de gestão na Motorola, quando a metodologia foi expandida e ganhou destaque de um programa, denominado de “seis passos para o seis sigma” ou “mapa para atingir o seis sigma”. O objetivo era reduzir a variabilidade e limitar os defeitos em uma escala de 3,4 por milhão, (DAHLGAARD & DAHLGAARD-PARK, 2006). O projeto foi desenvolvido na Motorola por Bill Smith para melhorar a qualidade e reduzir os defeitos dos produtos e, devido ao sucesso alcançado, foi aplicado a todos os setores da empresa, a partir de 1990, sob a liderança do presidente Bob Galvin. Com o apoio desse programa, considerado como sendo a primeira geração, a Motorola foi a vencedora do Prêmio Malcolm Baldrige em 1988, o que impulsionou o emprego do six sigma nas empresas. A segunda geração, além da redução da variabilidade e limitação de defeitos, adicionou a melhoria no design e a redução de custos. A General Electric foi uma referência dessa geração. A terceira incluiu a criação de valor para a organização e seus consumidores, stakeholders, tendo a Caterpillar e o Bank of America como destaques. De um conceito estatístico, o seis sigma passou a ser um modelo de gestão, denominado de lean six sigma acompanhando as tendências de eliminar desperdícios. Nele estão incluídas a cultura de entender as necessidades dos clientes, de identificar e focar no que é crítico e de valor para o cliente, de desenvolver a melhoria contínua envolvendo as pessoas, aceitar mudanças de maneira assertiva e gerenciar com fatos e dados. O modelo utiliza cinco fases fundamentais, empregadas pela maioria das organizações, conhecidas pelo acrônimo DMAIC: define, measure, analyze, improve and control definir, medir, analisar, melhorar e controlar. O DMAIC é uma generalização do PDCA de Shewhart, figura 4, (MONTGOMERY & WOODALL, 2008).
D_DEFINE (DEFINIR) Definir o Problema
C_CONTROL (CONTROLAR) Manter a Solução
DMAIC AGIR
M_MEASURE _Corrigir (MEDIR) Quantificar o Problema _Melhorar
CHECAR _Verificar
A
ACT
P PLAN
C
CHECK
D
DO
PLANEJAR
_Identificar o problema _Objetivo/Meta _Método
FAZER _Treinar _Executar
I_IMPROVE
A_ANALYSE (MELHORAR) (ANALISAR) Implementar e Verificar a Solução Identificar a Causa do Problema
Figura 4. DMAIC e PDCA.
Em linhas gerais, em um projeto desenvolvido com base no DMAIC ou no PDCA é necessário definir o problema e o objetivo. A partir do objetivo, o método é estabelecido e com base nele, o projeto é realizado. Os resultados são analisados e uma decisão tem de ser tomada em relação ao objetivo. Se foi atingido, as opções são o encerramento, a padronização ou dar início às melhorias. Caso contrário, é necessário fazer uma revisão do que deu errado e recomeçar. O PDCA, que Shewhart desenvolveu na década de 1920, é a representação do método científico por meio de uma figura, facilitando o entendimento e a aplicação para os diversos níveis da empresa. O método científico envolve, resumidamente, formular e identificar o problema e definir o objetivo. É com base no objetivo que as etapas, ações, para atendê-lo devem ser definidas, metodologia. Valendo-se da metodologia o experimento é conduzido e os dados, resultados, obtidos. Os dados são transformados em informações, por meio de tabelas e/ou gráficos, e é pela análise dessas informações que o conhecimento sobre o problema avança, concluindo-se se o objetivo foi ou não alcançado. O emprego do PDCA é semelhante ao método científico. Existe um problema a ser resolvido - a justificativa, “por que fazer?”. A partir desse problema é definido o objetivo – “o que fazer?” - e o método, etapas, - “como fazer?”. A justificativa, o objetivo e o método correspondem à fase PLAN – P - do PDCA. A seguir, com base no método, são executadas as etapas previstas para atender ao objetivo, DO -D- obtendo-se os resultados, os quais são interpretados para verificar se atingiram ou não ao objetivo CHECK – C. Então vem a fase ACT – A - na qual se conclui sobre encerrar, melhorar ou corrigir. “...O método PDCA é a alma do Sistema Toyota de Produção...O método PDCA parece muito simples à primeira vista e, de fato, é simples. No entanto, quem utiliza este método com aplicação percebe ao longo dos anos que, quanto mais se aprofunda em seu uso por toda a empresa, mais se percebe a sua complexidade. Muitas vezes concluo que, após décadas, ainda percebo que estou aprendendo o PDCA...Este método viabiliza o gerenciamento científico da organização...O PDCA transforma uma organização numa escola pois a busca por resultados é paralela à busca do conhecimento...” CAMPOS (2009). O Lean tem as suas raízes no método científico, cartesiano. SPEAR & BOWEN (1999) descrevem a aplicação do método científico na Toyota por meio de quatro regras: todo o trabalho deve ser altamente especificado; toda a relação cliente fornecedor deve ser direta; o caminho para qualquer produto ou serviço deve ser simples e direto; qualquer melhoria deve ser realizada de acordo com o método científico, sob a orientação de um supervisor e no menor nível dentro da organização.
Modelos e Prêmios
Os modelos, conceitos e técnicas do CWQC, STP, lean production e six sigma são consagrados na estruturação da gestão das organizações, cada qual com suas particularidades. O modelo da Toyota teve início na década de 1950 e, até hoje, é utilizado e aperfeiçoado pela empresa com resultados expressivos: uma criação de Eichi Toyoda, Taiichi Ohno e colaboradores que mudou a forma de fabricar veículos. Ele emprega também os conceitos do CWQC desenvolvido na JUSE com apoio de Deming,
Juran, Ishikawa e outros. O CWQC, por sua vez, tem parte de suas origens nos conceitos do TWI desenvolvidos na II Grande Guerra e, dentre eles, o learn by doing de Walter Dietz e equipe. Parte do learn by doing teve como base os quatro passos de Charles Allen aplicados nos treinamentos durante a I Grande Guerra. Esses modelos foram estruturados empregando a teoria clássica, os enfoques comportamental e sistêmico, e o controle estatístico do processo. As teorias e enfoques abrangem a produção em massa de Henry Ford, os trabalhos de Taylor, Mayo, Bertalanffy, Shewhart, Adam Smith, Weber, Fayol, Gilberth e tantos outros. O STP, Lean Production e Six Sigma têm raízes profundas: raízes que nasceram e se desenvolveram ao longo do tempo por maio do emprego de teorias, conceitos, técnicas e práticas. Além desses modelos, os prêmios da qualidade podem ser empregados para a estruturação da gestão. Eles existem para promover e aprimorar as melhores práticas de gestão e ajudam no aumento da competitividade das organizações. O prêmio Deming foi criado no Japão em 1951 para reconhecer o empenho das empresas japonesas na aplicação das práticas de gestão pela qualidade. Ele é prescritivo na medida em que indica as práticas que devem ser implementadas. O prêmio Malcolm Baldrige, estabelecido em 1987 nos EUA, promove uma perspectiva sistêmica para o entendimento do desempenho da administração e não prescreve práticas. Com base no Malcolm Baldrige, outros foram criados, como o Prêmio Europeu da Qualidade em 1989 e o Prêmio Nacional de Qualidade (PNQ) no Brasil em 1991, pela Fundação Nacional da Qualidade (FNQ), cujas bases podem ser encontradas no Modelo de Excelência da Gestão, MEG. O objetivo do PNQ é contribuir para o aumento da competitividade e apresenta três aspectos principais: auxilia a melhoria das práticas de gestão, do desempenho e da capacitação; facilita a comunicação e o compartilhamento das melhores práticas entre todos os tipos de organizações; serve como modelo de referência para melhorar o entendimento e a aplicação das práticas de gestão. Os prêmios funcionam como auditorias do sistema de gestão para as empresas. As normas ISO da série 9000 estabelecem as diretrizes para estruturar sistemas de gestão da qualidade, sendo reconhecidas mundialmente, (TOLEDO et al., 2003). O Modelo de Excelência da Gestão -MEG – estabelece os fundamentos que devem ser atendidos para que uma empresa seja reconhecida como “de classe mundial”: pensamento sistêmico, aprendizado organizacional, cultura de inovação, liderança e constância de propósitos, orientação por processos e informações, visão de futuro, valorização das pessoas, conhecimento sobre o cliente e o mercado, desenvolvimento de parcerias, responsabilidade social. Os fundamentos são traduzidos na forma de requisitos mensuráveis, agrupados em oito critérios, que permitem entender a lógica do modelo: Liderança; Clientes; Sociedade; Estratégias e Planos; Pessoas; Processos; Resultados; Informação e Conhecimento. A liderança tem como responsabilidades, entre outras, estabelecer o rumo da organização, desenvolver as pessoas e estabelecer as diretrizes básicas: missão, visão e valores. A missão define o que a empresa faz, a visão o que ela pretende atingir e os valores, princípios éticos, são os códigos de conduta aos quais ela não renuncia para atingir os seus objetivos. A missão, a visão e os valores sustentam e norteiam o desenvolvimento das estratégias e dos planos de ação. As necessidades e anseios dos clientes criam a demanda por produtos ou serviços e é essa demanda que define o nascimento, o crescimento e o desaparecimento das organizações. No tocante à sociedade, além do relacionamento, o foco é eliminar ou mitigar o impacto que as atividades possam causar ao ambiente. As estratégias devem atender à missão e à visão e são de responsabilidade do nível estratégico, apoiado pelo tático, gerencial, e, em empresas mais abertas, o nível operacional também é chamado para contribuir. As estratégias são desenvolvidas e desdobradas em planos de ação para satisfazer aos consumidores, stakeholders, com base na análise dos ambientes nos quais a organização está inserida e no entendimento das necessidades dos clientes e da sociedade. Os planos de ação são realizados por pessoas, por meio de processos, e as pessoas precisam de um ambiente adequado para desenvolver os seus potenciais. Os processos devem ser estruturados e padronizados, por meio de procedimentos operacionais, visando atender aos requisitos dos clientes, internos e externos. Os resultados precisam ser monitorados o que gera a necessidade de um sistema de informação que atenda ao nível estratégico, tático e operacional, (FNQ, 2008). Da mesma forma que os conceitos e técnicas do CWQC, STP, Lean, Six Sigma, ISO 9000, Modelo de Excelência da Gestão -MEG – e outros se disseminaram pelos setores da indústria e serviços, eles começam a adentrar no setor agrícola, porém com alguma defasagem. Somente nos últimos anos, o emprego dessas técnicas de gestão passou a ser adotado, desde a aplicação do controle estatístico do processo até implantação de modelos, expondo todas as suas vantagens. O Brasil é um dos líderes
mundiais do agronegócio, liderança esta conquistada pelo trabalho duro no campo, condições naturais de solo e clima, disponibilidade de áreas e emprego da tecnologia envolvendo as máquinas agrícolas, agricultura de precisão, informática, entre outras. A revolução industrial (RI) que teve início com a máquina a vapor (RI_1.0) chega agora à sua quarta etapa (RI_4.0) com o advento dos drones, robôs, inteligência artificial, “big data” entre outros, figura 5. Da mesma forma que a agricultura foi influenciada ao longo das etapas da RI, agora ela está passando por profundas modificações: a agricultura 4.0.
Figura 5. As etapas da Revolução Industrial (RI).
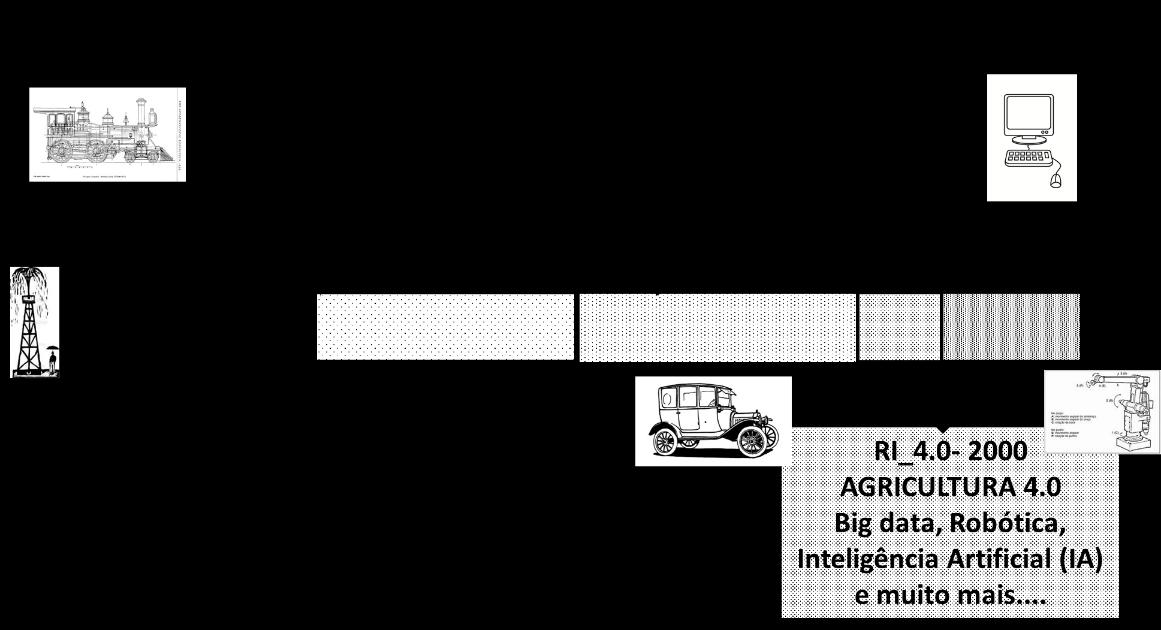
Estruturando a Empresa
Essas mudanças colocam ainda mais em evidência a necessidade de a agricultura apoiar-se também no pilar da gestão para consolidar cada vez mais a posição de destaque. Isso passa pelo entendimento e aplicação, de forma sistêmica, dos conceitos e técnicas da gestão desenvolvidos e testados ao longo dos tempos em outras atividades. É necessário pensar nos caminhos a serem escolhidos para concentrar os esforços a fim de realizar a missão e materializar a visão da empresa, com a finalidade de garantir a sobrevivência e o crescimento. Definir “quem somos”, “como estamos”, “para onde queremos ir” e “como chegaremos lá”, figura 6, é fundamental para uma empresa de qualquer tamanho, seja ela uma pequena propriedade de administração familiar ou uma grande empresa agrícola administrada por executivo.
QUEM SOMOS?
CONHECENDO A ORGANIZAÇÃO MISSÃO;
VISÃO; VALORES.
COMO ESTAMOS ?
ANÁLISE AMBIENTAL
PARA ONDE QUEREMOS IR?
ESTRATÉGIA_1 ou Objetivo Estratégico_1
ESTRATÉGIA_2 ou Objetivo Estratégico_2
ESTRATÉGIA_N ou Objetivo Estratégico_N OBJETIVO_1.1 COMO CHEGAREMOS LÁ?
Objetivo 1.1.1
Objetivo 1.2.1
OBJETIVO_2.1 Objetivo 2.1.1
OBJETIVO_2.2
PLANO DE AÇÃO 2.2
OBJETIVO_2.3 Objetivo 2.3.1
OBJETIVO_N.1 Objetivo N.1.1
OBJETIVO_N.n PLANO DE AÇÃO N.n PLANO DE AÇÃO 1.1.1
PLANO DE AÇÃO 1.2.1
PLANO DE AÇÃO 1.2.2
PLANO DE AÇÃO 2.1.1
PLANO DE AÇÃO 2.3.1
PLANO DE AÇÃO 2.3.2
PLANO DE AÇÃO 2.3.3
PLANO DE AÇÃO N.1.1
ACOMPANHAMENTO (Tomada de Decisão)
COMO ESTAMOS INDO?
COMO CORRIGIR?
Figura 6. Estratégias, desdobramentos e planos de ação. (Adaptada de ABRAPP 2007).
Definir “quem somos” é realizado por meio do estabelecimento das diretrizes básicas: missão, visão e valores. A missão é o que a empresa faz, a visão define os rumos e os valores estabelecem o código de conduta.
Uma das formas para saber “como estamos” é analisar os ambientes nos quais a organização está inserida: macro, operacional e interno. O macroambiente envolve os aspectos políticos, sociais, econômicos e tecnológicos, enquanto o operacional refere-se ao mercado alvo, clientes, concorrentes e fornecedores. Esses dois ambientes influem na empresa, que não tem domínio sobre eles, e trazem tanto oportunidades como riscos. A alta do dólar pode favorecer o exportador de commodities agrícolas ao mesmo tempo em que pode encarecer os insumos básicos como fertilizantes e defensivos. As mudanças climáticas podem afetar não só a produtividade da cultura, mas a viabilidade, em longo prazo, de continuar produzindo no local. O ambiente interno reflete os pontos fortes e fracos da empresa. Um ponto forte pode ser o índice baixo de turn-over, enquanto um ponto fraco, como a ausência de treinamento, leva à instabilidade nos processos e consequentemente a um maior custo de produção. Uma das ferramentas empregadas na análise dos ambientes, para apoiar o desenvolvimento das estratégias, é a matriz SWOT, acrônimo para Strenghts, Weaknesses, Opportunities, Threats, ou matriz FOFA –Forças, Oportunidades, Fraquezas e Ameaças. As estratégias - objetivos estratégicos ou objetivos gerais - representam os caminhos escolhidos para levar a organização de uma situação atual para uma situação desejada no futuro, “para onde queremos ir”, e devem estar alinhadas às diretrizes básicas: missão e visão. Elas são desenvolvidas de modo a combinar os efeitos das oportunidades e dos pontos fortes e evitar, ou minimizar, as fraquezas e ameaças e traduzem os compromissos de longo prazo com os consumidores, em termos de qualidade, custos, produtividade, segurança e ambiente. Representam a área de eficácia: fazer o que tem de ser feito.
Desdobrar as estratégias é o caminho para que o “Como chegaremos lá” aconteça. Desdobrar, em linhas gerais, significa “quebrar” as estratégias em objetivos e estes, se necessário, em outros menores, específicos. O encadeamento lógico dos objetivos nos diferentes níveis – estratégico, tático e operacional - leva ao atendimento da estratégia e o PDCA é uma das ferramentas empregadas para percorrer os caminhos, figura 7.
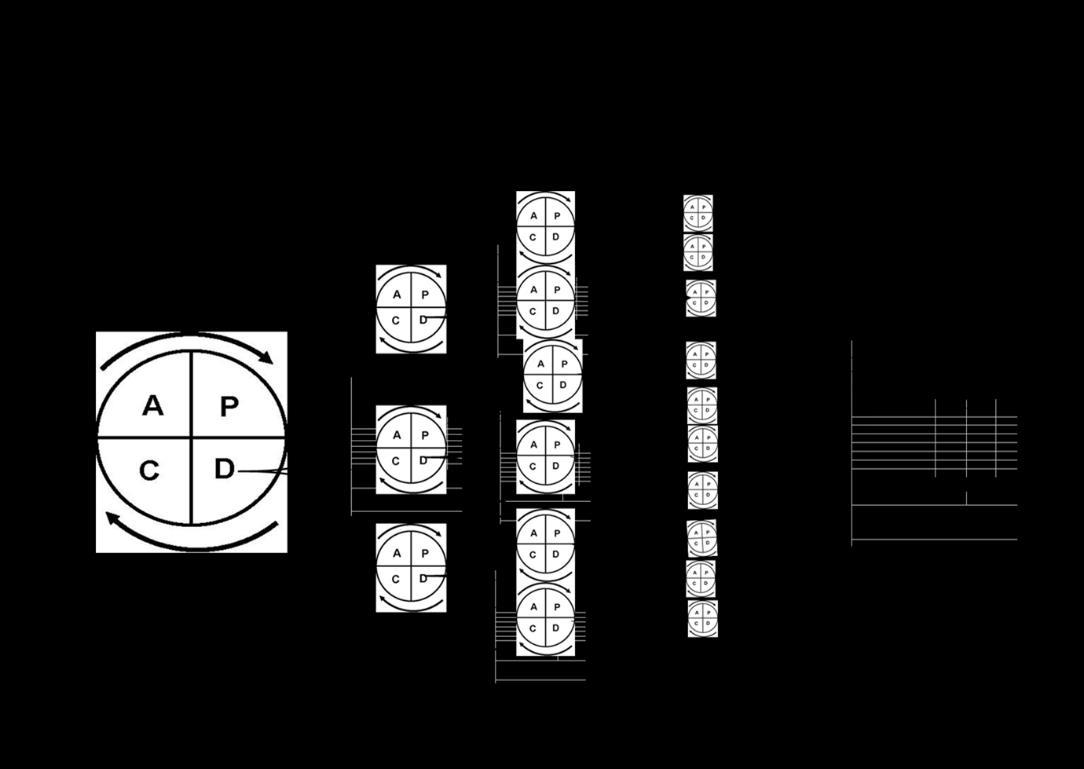
Figura 7. Desdobramento da estratégia (objetivo estratégico) por meio do PDCA.
Com base nos PDCAs e seus objetivos, os planos de ação são elaborados, figura 8. O plano deve conter as metas e as ações necessárias para atingir ao objetivo.
LOGO PLANO DE AÇÃO
Estratégia (Objetivo Estratégico) Num. (Cod.)
Objetivo:
Meta:
Ação Descrição Método
Evidência Responsável Data
Figura 8. Exemplo de um formulário básico de Plano de Ação.
Um plano de ação contém a estratégia a ser atendida, “Por que fazer?” -justificativa -e o objetivo para atendê-la – “O que fazer?”. A meta é o objetivo transformado em valor(es) e data. No método são descritas as ações para atender ao objetivo “Como fazer?”. Os três itens, estratégia, objetivo e método, são associados à fase P (Plan) do PDCA. No plano também existem as informações dos responsáveis pelas ações “Quem?”, as datas “Quando” e o local “Onde” as ações vão ocorrer. “Por Que?, O Que?, Como? , Quem?, Quando?, Onde?” correspondem ao 5W1H. Com a execução das ações (D-DO) é necessário verificar se os resultados atendem ao objetivo (C-Check) e agir (A-Act) para decidir se o plano é encerrado, aplicar medidas corretivas ou desenvolver melhorias. É o PDCA de Shewhart, o método científico, em ação.
Se as estratégias representam a área de eficácia, “fazer o que tem de ser feito”, a rotina é a de eficiência - “fazer bem-feito” -, sendo associada à missão. Uma das prioridades para assegurar a sobrevivência de uma organização é padronizar a rotina, de forma que os resultados com relação aos produtos ou serviços realizados sejam previsíveis, constantes. A padronização garante a qualidade do produto/serviço para o cliente, aumenta a produtividade, assegura que a tecnologia de produção fique registrada e seja de domínio da empresa, auxilia no treinamento dos colaboradores e garante um padrão na execução dos trabalhos. Garantir o padrão é um dos pontos principais da gestão e deve fazer parte das estratégias. As melhorias só acontecem quando existir um padrão para melhorar. De nada adianta ajustar as estratégias para a visão, crescimento, se o dia a dia, a rotina, não está funcionando adequadamente. Padronizar a rotina refere-se aos processos desenvolvidos na empresa, principais ou de apoio. Um processo é entendido como uma sequência de atividades realizadas para a geração de resultados para o cliente, interno e/ou externo ou, de acordo com a ABNT (2015), “um conjunto de atividades interrelacionadas ou interativas que utilizam entradas para entregar um resultado pretendido”, figura 9.
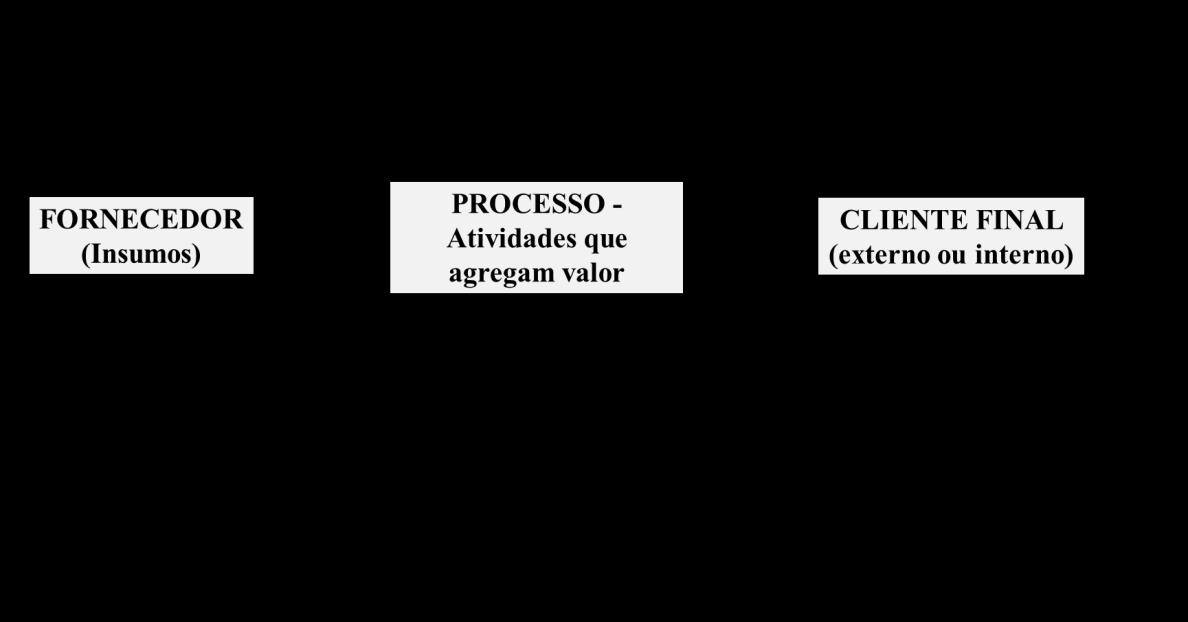
Figura 9. Processo.
Cada processo tem um objetivo específico que ao ser levado em conta no conjunto das atividades da organização, colabora para o alcance dos objetivos finais. A saída, produtos ou serviços é a entrega que ocorre ao final de cada processo e deve atender à necessidade do cliente final, externo ou interno. As entradas, “inputs”, são os insumos que serão modificados no decorrer do processo para agregar valor. Esses insumos têm origem no fornecedor, interno ou externo à organização. O processo é ligado à missão da empresa: caso contrário é preciso avaliar a razão para ele existir. A equipe responsável pelo processo conta com os meios de produção necessários para desenvolver as ações. A equipe tem autonomia para utilizar os meios e a responsabilidade de cumprir o(s) objetivo(s)/meta(s). Os itens de controle referemse aos requisitos a serem atendidos, e os de verificação são os itens que devem ser monitorados no processo e no fornecedor. As entradas e o processo determinam o produto ou serviço, saída. Assegurar os padrões dos itens de verificação, é garantir que o produto ou serviço saiam de acordo com o determinado. A metodologia para a padronização da rotina normalmente envolve o mapeamento dos processos, desenvolvimento dos procedimentos operacionais padrão (POPs) e monitoramento dos processos. Mapear é rastrear os processos que uma empresa desenvolve rotineiramente para atender às necessidades de seus clientes, utilizando os insumos entregues pelos fornecedores. É analisar o fluxo das atividades obtendo uma fotografia do estado atual dos processos de forma a entender como funcionam e possibilitar desenvolver as melhorias. Ao desenvolver o mapeamento deve-se ter em mente que o próximo processo é seu cliente: “the next process is your customer”. O cliente do processo de preparo do solo, por exemplo, é a semeadura. O fornecedor, preparo do solo, deve entregar o produto - solo preparado – de acordo com as necessidades do cliente. O que é um bom preparo? Pergunte para o cliente. Na agricultura muitas vezes é necessário considerar a planta como cliente, pois será ela a responsável pela “fabricação do produto” a ser entregue ao cliente final. Sendo um ser vivo, ela tem necessidades a serem atendidas para poder expressar o potencial genético em termos de produtividade e qualidade. Para a semeadura, o processo de preparo do solo deve considerar dois aspectos principais: leito da semente e leito da raiz. Para o leito de semente é importante que haja um contato adequado semente-solo para que a germinação ocorra. No caso do leito de raiz o objetivo é que não existam impedimentos no solo para o desenvolvimento da raiz. Outros clientes também podem ser considerados como, por exemplo, a sociedade. O preparo deve causar o menor dano possível ao ambiente e a erosão é um dano a ser mitigado. O proprietário (acionista) deseja um preparo com menor custo, mas com boa produtividade e qualidade das lavouras. O procedimento operacional padrão (POP) é um documento no qual as atividades críticas para a realização do processo - “como fazer” – são detalhadas, figura 10. Em termos simples, é uma “receita de bolo” e a aderência da equipe a essa receita é fundamental para que a rotina mantenha um padrão.
LOGO
Procedimento Operacional Padrão (POP) Criação Data Revisão Revisão Número
Título (nome) da Tarefa
Por que fazer?
O que fazer?
Requisitos
Ação Num Como Fazer (Método)
Descrição POP Número
Itens Críticos do Como
Preventivas
Ações Corretivas
Equipe Responsável Aprovação
Data Supervisor
Data Chefia
Data
Figura 10. Exemplo de um Procedimento Operacional Padrão -POP.
O cabeçalho do POP deve conter as informações básicas como as datas de criação e revisão e o número da revisão. Efetuar revisões nos procedimentos é fundamental, pois é dessa forma que as melhorias são incorporadas ao processo. A justificativa “por que fazer?”, e o objetivo “o que fazer?” devem ser descritos e os requisitos para atender o cliente especificados. O método contém as ações críticas do “como fazer”, ações necessárias para atingir ao objetivo. Com isso, a fase P do PDCA está atendida. Executa-se o procedimento, fase D (Do), e os resultados são avaliados com base nos requisitos C (Check). Se tudo estiver correto o processo continua, e se houver problemas é necessário corrigir A (Action). O 5W1H também está presente no POP pois a equipe responsável está definida – “Quem” – e concordou com o procedimento. Com isto, o local “Onde” também está estabelecido, junto com as datas “Quando” momento a partir do qual o procedimento passa a ser válido. Por ser o procedimento uma forma que estabelece um padrão para a execução da rotina, é comum denominar a fase P (Plan) como S de “Standard”, padrão. A avaliação do processo com base nos requisitos, C (Check), é realizada empregando as sete ferramentas da qualidade propostas por Ishikawa, dentre outras. Os resultados precisam ser apresentados em tempo real por meio da Gestão à Vista, permitindo que a equipe faça as correções assim que algo sair fora do esperado. Nesse caso, é possível empregar o diagrama de causa e efeito para levantar as possíveis causas e priorizá-las utilizando o diagrama de Pareto. O emprego do gráfico de controle, desenvolvido por Shewhart, permite analisar se um processo atende ou não às especificações do cliente. Os itens de especificação (requisitos da qualidade, voz do cliente), não podem ser mais rígidos do que os valores que o processo pode oferecer, voz do processo, calculados estatisticamente, figura 11, (WHEELER 2001).
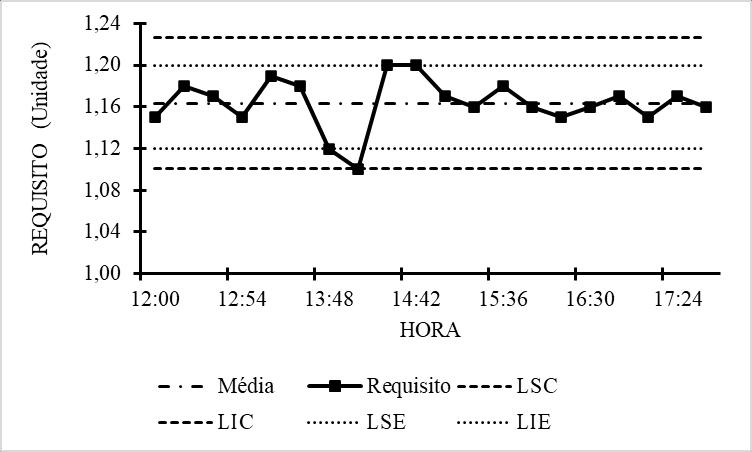
Figura 11. Limites de especificação e de controle. (LSC-Limite Superior de Controle; LIC-Limite Inferior de Controle; LSE- Limite Superior de Especificação; LIE- Limite Inferior de Especificação).
No caso, o valor médio da variável é de 1,16 unidades com um Limite Superior de Controle (LSC), calculado estatisticamente, de 1,23 e inferior (LIC) de 1,10. O requisito da qualidade foi especificado tendo como maior valor, Limite Superior de Especificação (LSE), de 1,20 unidades e o menor, LIE, de 1,12. O processo não consegue atender à voz do cliente. Dos muitos exemplos que existem na agricultura, um deles é o da colheita mecanizada de cana de açúcar, para a qual os requisitos para as perdas de matéria prima são especificados. A altura de toco normalmente é limitada a cinco centímetros – limite de especificação ou “voz do cliente”. Porém, é necessário questionar se o processo de colheita permite atender a essa exigência, Limites de Controle (LC) ou “voz do processo”. Se o gestor especificar limites que um processo não consegue atender, o resultado será eternizar o atrito entre a equipe e ele. Nesse caso, ou altera-se os requisitos, limites de especificação, ou muda-se o processo.
Considerações finais
Quando a empresa faz a opção por implantar um modelo de gestão, qualquer que seja ele, a liderança deve estar ciente de que deverá seguir rigorosamente um dos princípios básicos propostos por Deming: constância de propósito. Normalmente, os resultados só aparecem de forma mais consolidada após cinco anos e vencendo muitos desafios, principalmente aqueles relacionados às resistências às mudanças. Um fato relatado por Atkinson (1989), na visita ao Japão, realizada por ele e um grupo de empresários em 1988, ilustra a necessidade da constância de propósitos e de iniciar o quanto antes. Um dos membros do grupo perguntou a um funcionário que os acompanhava na visita a uma empresa: “...por que vocês abriram as portas das empresas, falaram francamente sobre as técnicas e os seus segredos?...”. A resposta foi que “...levará 10 anos para vocês alcançarem o estágio em que estamos hoje e daqui a dez anos estaremos mais à frente...”. O pior sistema de gestão que uma organização pode adotar é a ausência dele, pois nada pode ser melhorado se não existir. Retardar a implantação significa ficar atrás da concorrência e arcar com os custos da não qualidade. Não é possível pular etapas para acelerar o processo, pois este depende de aprendizado. O papel da liderança é fundamental para minimizar as resistências, desenvolver e consolidar a cultura de eliminar os desperdícios, melhoria contínua e do aprendizado organizacional. Na Western Electric, Hawthorne, ao final da década de 1920, uma das lições deixadas pelos experimentos foi que a produtividade depende da atenção que a liderança dá aos funcionários, (WREIN 2005). Em um cenário cujo foco da liderança é voltado a criar um ambiente adequado para o desenvolvimento das pessoas, existe mais participação na solução de problemas, forte cooperação entre pessoas e áreas e comprometimento com o desempenho das atividades. Esses fatores geram a motivação e a inovação e, consequentemente, o aumento da competitividade. Ainda hoje, para muitas lideranças, a realidade é colocar a produtividade em primeiro lugar e depois a motivação das pessoas. A gestão é centrada no poder, com as decisões do nível mais alto para a base, sem a participação das pessoas. Resta a elas receberem ordens e cumpri-las, sem espaço para a criatividade, o que leva à desmotivação e à
impossibilidade da autorrealização no trabalho, (ANDRIANI, 2003). A ausência da motivação impede o desenvolvimento de melhorias e leva a uma queda de competitividade colocando em risco a sobrevivência da organização. Para a agricultura 4.0, o desafio na área de gestão é desenvolver a cultura da eliminação dos desperdícios, da melhoria contínua e do aprendizado. O papel da liderança à frente da organização é fundamental para que isso aconteça.
Referências
ASSOCIAÇÃO BRASILEIRA DAS ENTIDADES FECHADAS DE PREVIDÊNCIA COMPLEMENTAR (ABRAPP) (2007) Planejamento Estratégico. São Paulo. ASSOCIAÇÃO BRASILEIRA DE NORMAS TÉCNICAS (ABNT NBR, ISO 9000) (2015) Sistemas de gestão da qualidade -Fundamentos e vocabulário. Rio de Janeiro, 2015. ALLEN CR (1919) The instructor the man and the job: a handbook for instructors of industrial and vocational subjects. Philadelphia, J.B. Lippincott Company. 373p. ANDRIANI CS (2003) Gestão sistêmica com base nos valores humanos. Campinas, Dialivros Editora. 184p. ATKINSON P (1989) TQM fact finding mission to Japan. The TQM Magazine 1(2):120-124. DOI: https://doi-org.ez67.periodicos.capes.gov.br/10.1108/EUM0000000003001 BHAMU J, SANGWAN KS (2014) Lean manufacturing: literature review and research issues. International Journal of Operations & production Management 34(7):876-940. DOI:10.1108/IJOPM08-2012-0315 BREEZE P (2018) Piston engine-based power plants, Imprint Academic Press. 102p. DOI: https//doi.org/10.1016/C2016-0-03647-1 CAMPOS VF (1999) TQC-Controle da Qualidade Total (no estilo japonês). Editora de Desenvolvimento Gerencial, Belo Horizonte. 230p. CAMPOS, VF O verdadeiro poder. INDG Tecnologia e Serviços Ltda, Nova Lima, p24-25. DAHLGAARD J, DAHLGAARD-PARK SM (2006) Lean production, six sigma quality, TQM and company culture. The TQM Magazine 18(3) 263-281. DOI 10.1108/09544780610659998 DIETZ W, BEVENS BW (1970) Learn by doing: the story of training within industry. Summit, New Jersey. 114p. EBRAHIMPOUR M (1985) An examination of quality management in Japan: implications for management in the United States. Journal of Operational Management 5(4):419-431. FORD H (2014) My life and work; an autobiography of Henry Ford. Snowball Publishing, Lexington, KY. 187p. FUNDAÇÃO NACIONAL DA QUALIDADE (2008) Cadernos Rumo à Excelência®: Introdução ao Modelo de Excelência da Gestão ® (MEG) / Fundação Nacional da Qualidade, Série Cadernos Rumo à Excelência. Fundação Nacional da Qualidade, São Paulo. 21p. GILBERT M (2014) A Segunda Grande Guerra: os 2147 dias que mudaram o mundo. Rio de Janeiro, Casa da Palavra, p7. HOLWEG M (2007) The genealogy of lean production. Journal of Operations Management 25(2):420436. DOI: 10.1016/j.jom.2006.04.001 HUNTZINGER J (2002) The roots of lean- Training within industry: The origin of kaizen. Target 18(1):6-19 ISHIKAWA K (1986) How to apply company-wide quality control in foreign countries. Center for quality and productivity improvement. Report No15 University of Wisconsin, Madison.12p. KATO I (2006), TWI Influence on TPS & Kaizen, Summary notes from Art Smalley. Interview with Mr Isao Kato. Art of Lean, Inc. www.ArtofLean.com KIBBLE B (2014) The measuring stick came before the wheel. IEEE Instrumentation & Measurement Magazine. 17(3):28-29. KREIS S (2017) Lecture 17: The Origins of the industrial revolution in England. The History Guide: Lectures on Modern European Intellectual History. Available: http://www.historyguide.org/intellect/lecture17a.html. Accessed Jun 06, 2020.
KRÜGER V (2001) Main Schools of TQM: “the big five”. The TQM Magazine.13(3):146-155. LIKKER JK (2005) O modelo Toyota: 14 princípios de gestão do maior fabricante do mundo. Porto Alegre, Bookman. 316p. MAXIMIANO ACA (2000) Introdução a administração. São Paulo, Atlas. 541 p. MONTGOMERY DC, WOODALL WH (2008) An overview of Six Sigma. International Statistical Review 76(3):329-346. DOI:10.1111/j.1751-5823.2008.00061.x NICHOLAS J, SONI A (2006) The Portal to lean production: principles and practices for doing more with less. Auerbach Publications, Boca Raton, FL. 310p. OHNO T (1997) O Sistema Toyota de produção: além da produção em larga escala. Porto Alegre, Bookman. 129p. PAXTON J (2012) Mr. Taylor, Mr Ford, and the advent of high-volume mass production: 1900-1912. Economics & Business Journal: Inquires &Perspectives.4(1):74-90. ROBINSON AG, SCHROEDER DM (1993) Training, continuous improvement, and human relations: The U.S. TWI programs and the Japanese management style. California Management Review.35(2):3557. SHINGO S (1996) O Sistema Toyota de Produção do ponto de vista da Engenharia de Produção. Porto Alegre, Bookman. p81. SPEAR S, BOWEN HK (1999) Decoding the DNA of the Toyota Production System. Harvard Business Review.77(5):1-12. STAUFFER, J (2003) SQC before Deming: the works of Walter Shewhart. The Journal of Applied Management and Entrepreneurship. 8(4):86-94. TACHIKI DS (2008) TQM in Japan Deming, Juran and Ishikawa. Project for Enhancing the Capacity of Public Service Training in Bangladesh; Hosei University. Available: https://www.researchgate.net/publication/273382233_TQM_IN_JAPAN_Deming_Juran_and_Ishikaw a. Accessed Jul 02, 2020. TAYLOR, FW (1911) The principles of scientific management. New York, Harper & Brothers. Available: http://strategy.sjsu.edu/www.stable/pdf/Taylor,%20F.%20W.%20(1911).%20New%20York,%20Harp er%20&%20Brothers.pdf. Accessed Jul 02, 2020. TOLEDO JC, BORRÁS MÁA, MERGULHÃO RC, MENDES GHS (2013) Qualidade: Gestão e Métodos. Rio de Janeiro, LCT. 397p. TOMAC N, RADONJA R, BONATO J (2019) Analysis of Henry Ford´s contribution to production and management. Scientific Journal of Maritime Research, 33, p34-35. DOI: https://doi.org/10.31217/p.33.1.4. WADA K (2006) The fable of the birth of the Japanese automobile industry: A reconsideration of the Toyoda–Platt agreement of 1929. Business History. 48(1):90-118. DOI:10.1080/00076790500204768 WHEELER DJ (2001) Entendendo a variação: a chave para administrar o caos. Rio de Janeiro, Qualitymark. 152p. WOMACK JP, JONES DT, ROOS D (2004) A máquina que mudou o mundo: baseado no estudo do Massachusetts Institute of Technology sobre o futuro do automóvel. Rio de Janeiro, Elsevier. 332p. WREN DA (2005) The history of management thought. John Wiley &Sons, Inc., Hoboken. 519p. YAMAMOTO Y, BELLGRAN, M (2010) Fundamental mindset that drives improvement towards lean production. Assembly Automation, 30(2). DOI: 101108/01445151011029754. YERGIN, D (2010) O petróleo: Uma história mundial de conquistas, poder e dinheiro. São Paulo, Paz e Terra. 1077p.