THE CASMAZ BUILDING SYSTEM DESIGN MANUAL
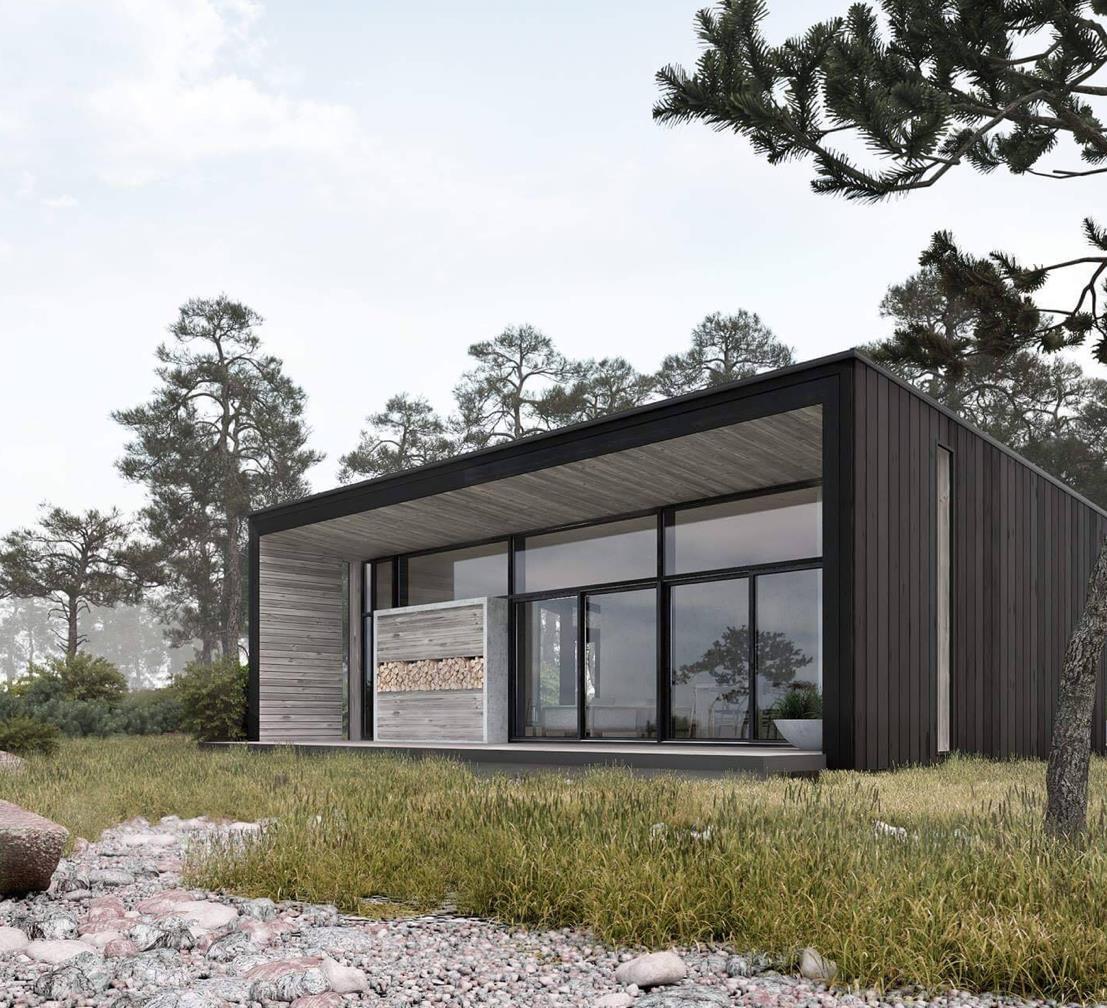

C ecilie Kristensen, s155942
A lina Barun, s202514
S arah Jæger, s154258
M ads Jespersen, s175380
A bdullah Turkmani, s153337
Z ainab Jalal, s165491
C ecilie Kristensen, s155942
A lina Barun, s202514
S arah Jæger, s154258
M ads Jespersen, s175380
A bdullah Turkmani, s153337
Z ainab Jalal, s165491
1.1. introduction 1
1.2. benefits of the CASMAZ building system 2
1.3. CASMAZ building process 3
2.1. introduction 5
2.2. sustainable redesign of concept 6
2.3. final architecture 7
2.4. site plan 8 2.5. the CASMAZ facing 9 2.6. the redesigned leisure house 10
3.1. introduction 14
3.2. structural components 15
3.3. internal components 17
3.4. storage of components 19
4.1. weight and tools 21
4.2. building process 22
4.2.1. floor preparation 22 4.2.2. frame assembly 23 4.2.3. frame lifting 24 4.2.4. external finishes 25 4.2.5. clicking on internal components 26 4.2.6. main entrance 27 4.2.7. windows as gable 28
5.1 key performance indicators 29
5.2 expected maintenance 30
5.3 epilogue 31
A1 structural calculations
A2 bolted connection
A3 model 1:20
A4 snap lock connection
A5 time schedule
A6 cost estimation
A7 energy consumption
A8 weight of components
drawing list
001 plan drawings 002 section drawings
003 elevation drawings 004 floor and roof component detailing 005 wall component detailing 006 connection details
The concept of the CASMAZ building system aims to improve traditional vacation homes by accelerating the often slow and tedious building process. CASMAZ is based on a time saving modular approach that has several advantages such as prefabricated elements, no risk of weather delay, lower volume of waste, and significantly reduced labor costs – because no building prerequisitesare needed!
Workingwith a modulardesignapproachthe CASMAZbuildingsystemhas great flexibilitywithrespectto architecture, since themodulescanbe used in a variety ofboxydesigns.
The CASMAZ building system is for everyone, and its attractivedesign ensures a safeand dryconstruction aswell as outliningthe advantagesofsustainable living.
I Scandinavia bad weather often poses a threat to structural members, since moisture can develop into mold and create a bad and potentially harmful indoor climate. Issues related to moisture in structures can often be significantly reduced by storing materials in a dry area and ensuring an air and watertight buildingas fast as possible.
The CASMAZ building system is delivered on site in a closed container and thereby eliminating the risk of wet structural members. Also, a vapor barrier is implemented into thebuilding components to continuously seal off the structure duringconstruction,which makesthe buildingless exposedtobadweather.
During the recently past years a tendency has arisen in Denmark that leisure houses have become increasingly bigger. From a sustainable point of view there aresignificantbenefits to begained byreducingtheliving area of aperson,since lighting,heating, cooling,and waste managementall dependonbuildingsize.
The CASMAZbuilding system is designed for smaller living to emphasize smaller housesbeingbothsustainableand cozy Also,smaller houses are cheap to build, more easily maintained and use less energy, which makes the CASMAZ building system available to everyone. The CASMAZ building system only has a small impact on the environment, and waste from production is substantially reduced.
By using prefabricated components the building can quickly be assembled and the risk of errors is minimized. The prefabricated components arrive on site in a closed container, and they are thereby sheltered from the weather until they are assembled and raised as frame modules. Each frame is raised and connected to the previous frame, sealing off the building frame by frame to avoid harmful moisture.
Each component arrives prefabricated on site and is easily assembled into frames by simple bolted gusset connections. The frames are raised one by one and attached to the previous frames. The inside of the building also arrives on site prefabricated and can be easily be attached to the structural frames. The internal components are equipped with the vapor barrier that is sealed off by simply removing a strip ofdouble adhesive tape.
The simple build upof the components and thefact that all the frames are ofequal size allowsfor a flexible architectural design. It is possible to adjust the size of the building byvarying the amount of frames that are put together, and furthermore an expansion of the building at a later point is also possible.
By reducing the building size, the amount of materials and the energy consumption decreases. The components and façades are made from durable materials that will last for many years, if they are treated correctly and properly maintained.The large overhang to the south works as a passive solar heating system for the building, saving energy by allowing the winter sun to heat up the building while shading the summer sun.
Decreasing the building size will lower the cost of the building and thereby making it more affordable for a wider range of people. The smaller living area also results in lower costs of heating and energy consumption, and the easy assemblance of frames reduces the need for professional help, which is also a significant expense when building nowadays.
The CASMAZbuilding system facilitates and accelerates the building process with its modular design, that is easily implemented after preparation of the building site.
ADDING FINAL LAYER OF ROOFING ASPHALT
The architectural conceptof the CASMAZ building system has been developed with significant inspiration of the leisure house atHejrevænget in the northern part of Sealand. The one-storey house was built in 2018, and its primary material is wood. The sloped roof of the house allows light to enter, and thereby states that room depth and room height are important factors when creating quality buildings. Different types of wooden materials in varying scales and colors are used throughout the entire leisure house which creates both contrast and coherence, and which is also a modern take on the tradition of building leisure houses in wood. From the perspective of small living the original leisure house at Hejrevænget has been the inspiration for creating functional architecture bya modularcomponentapproach.
In Denmark a light frame construction is typical for building leisure houses, as is the case for the house at Hejrevænget. All joints are simply assembled by screws, nails and metal brackets. The structural system consists of beams, posts, and roof rafters sloping in one direction, which is beneficial for avoiding waterpondson the roof as well as improving sun light conditions in the leisure house A terrace is created by the roof rafters spanning continuously over three rigid frames with a cantilevered end, which creates an overhang above the terrace. The rigid frames provide the structure with the required stability, and the frames are additionally supported by intermediate posts, which are needed for the installation ofa curtain wall.
For the leisure house at Hejrevænget the building process is rather long, since the structural members all need tobe connected on site.
• The first step is cleaning and preparation of the building site for future building rise.
• When the building site is level workon the foundations can start. All pipes and electrical conduits should be added, and formwork carried out before casting the point foundation.
• In this phase all structural elements are assembled. Also, sheeting is applied to the exterior walls and the roof. When the framing is in place, insulation is added,and windows and doors are installed.
• Installation of ductwork can be made now Also, electricians will install the main circuit panel.
• In the final phase all completion works will be done. After all the final touches house is ready for its users.
• Eventually maintenance will be required such as cleaning the roof, painting the wood,etc.
Ideas about functionality, energy consumption, and space considerations are the starting point of the redesigned concept. When considering energy consumption, the redesigned leisure house itself is not the only thing of importance, as energy is also used in the manufacturing of components and transport to the building site. Therefore, the redesigned leisure house is built of local materials to the widest extent possible, and the fast and dry construction will contribute to a reduction of the energy consumption.
The CASMAZ building system can be varied into countless design options, and factors such as room depth and height are easily adjustable due to the modular frame design approach Thereby space allocation is easily adjusted to the specific need of the user while taking functionality into account.
The idea of passive solar heating is an integral part of the new design, and the large overhang provides shade during summer to prevent overheating Similarly, it allows the low winter sun to enter the leisure house and providenatural heat during winter.
This one story wooden leisure house is the first project to be carried out using the modular CASMAZ building system, and the primary focus of the project proposal is to reduce redundant space while emphasizing the functionality of each part of the redesigned leisure house. For detailed drawings see the drawing appendix 001 003.
AN OVERHANG offers shading during summer
BIG WINDOWS will provide a lot of daylight even during winter and connects the indoor and outdoor environment
WEST FACADE
SMALL WINDOWS provides the bedroom and bathroom with natural light
THE MAIN ENTRANCE is shifted partly inside to allow shelter from bad weather
The versatility of birch plywood as a building material makes it an optimal choice of facing for the internal CASMAZ components. It is simply applied to both flooring, wall, and ceiling components, and it eliminates the need of additional interior facing such as plasterboards or similar products. The use of birchplywood is an easy and practical finish, since plating material is already a part of the internal component, and the birch plywood contributes with natural beauty, texture and strength. The internal components are slightly smaller than the structural components to accommodate tolerances. Furthermore, the small gab between the internal components is a significant part of the architectural expression, because it emphasizes the modular design approach.
In short birch plywood facing utilizes affordable beauty and durability, and it contributes to a shortening of the building process as all interior surfaces are finished when placing the internal components. Also, by using the same facing material throughout all surfaces a clean look is achieved as well as keeping costs and environmental impacts at a bare minimum.
Thermowood has a great list of advantages for use as a cladding material, and appearance, dimensional stability, durability, and overall economy are just a few of them. When considering the environment, it is essential that the treatment method of the wood is gentle and carried out with a low energy consumption. No gases nor chemicals are used in the production of thermowood as the treatment of the wood consists solely of heating with added steam, and this process makes the wood suitable forthe Nordic climate Eventually the wood can bereused or handled as combustible waste.
Due to its benefits thermowood is used for the external facing of the CASMAZ building system, that will provide the final exterior finish to the leisure house. External façade elements are directly attached to the outer structural frame, and the ‘click in’ system makes the fastening process quick and straight forward with no need of electrical tools.
BIG WINDOWS ENSURE A LOT OF LIGHT IN THE HOUSE
TERRACE IS A COZY PLACE FOR SPENDING FREE TIME
MAIN ENTRANCE TO THE LEISURE HOUSE
NORTHERN WINDOWS BRING LIGHT TO KITCHEN, BEDROOM AND BATHROOM
The CASMAZ building system consists of multiple components with the purpose of accelerating and facilitating the common/prevailing building process. Components are to be prefabricated with great precision in manufacturing facilities with necessary tools and materials, preferably located strategically close to materials to minimize transportation and thereby environmental and economic impact. The system can be divided into three main categories; wall (x2), floor and roof, which are each subdivided into 3 subcomponents; structural, internal and external components. For simplicity and recognizabilityallcomponents aremadeusingthesameprinciple.
The structural components are of a rigid "bookcase" nature. Together, the structural components form a rigid frame, and structural stability of both the individual component and the entire frame is of great importance. Since the modules must be erected by two people, having a stiff structure is crucial for the safe handling of the structure The stability of each component is ensured by having structural elements in all three directions.
The thermal envelope is a key element in a sustainable house, as it prevents heat transfer from the interior to the exterior. The CASMAZ building system is in compliance with the applicable regulations from BR20 once the pre cut insulation and internal components are installed To avoid heat loss through untight places and moisture in the structure, it is important that joints and connections are tight. Tightness is ensured by the minimum of 100 mm overlapping of the vapour barrier.
In order to fast and fully achieve the desired architectural expression of the building, the external cladding is also prefabricated. The external wall components comprise the vertical Thermowood panels that gives the building its warm appearance and durable nature The roof is covered in 2 layers of roofing asphalt and has a slope of 1:40, which is necessary to lead water off the roof structure
The structural components of the CASMAZ building system are made of wooden elements and the purpose is to create a reliable and light structure. For simplicity and recognizability the structural components are all made from the same principle of a stable "bookcase" structure. For detailed manufacturing drawings regarding the roof and floor components see drawing 004
45x220mm C18 rafter, length 5970mm (2 pcs)
600x6006mm Plywood plate, thickness 18mm
510x220mm Plywood plate, thickness 18mm (8 pcs)
- 12x12mm Wood battens, length 220mm (16 pcs)
45x220mm C18 rafter, length 5970mm (2 pcs)
600x6006mm Plywood plate, thickness 18mm
510x220mm Plywood plate, thickness 18mm (8 pcs)
12x12mm Wood battens, length 220mm (16 pcs)
The wall components are created from the same principles as the roof and flooring components. For detailed manufacturing drawings regarding the wall components see drawing 005.
45x120mm C18 stud, length 2600mm (2 pcs)
600x2820mm Windstopper plate, thickness 10mm
510x120mm Plywood plate, thickness 18mm (5 pcs)
12x12mm Wood battens, length 120mm (10 pcs)
STRUCTURAL WALL COMPONENT (TYPE B)
45x120mm C18 stud, length 2730mm (2 pcs)
600x2964mm Windstopper plate, thickness 10mm
510x120mm Plywood plate, thickness 18mm (5 pcs)
12x12mm Wood battens, length 120mm (10 pcs)
The CASMAZ internal component is an important part of the building system as it ensures a low heat loss transfer and contains the vapor barrier, that keeps the structure safe from moisture The vapor barrier is placed onto 45mm mineral wool on the backside of the component, allowing occupants to drill pictures etc into the wall without perforating the vapor barrier. The vapor barrier should be installed tightly and thus also keeping the insulation into place, when the internal component is clicked into place. Finally, the internal component gives the building its warm interior finish. In order to facilitate installation, tolerances have been accounted for by making the internal component 10mm smaller than the structural components. For detailed manufacturing drawings regarding the internal components see drawing 004 and 005.
- 45x45mm
Wood rafter, length 590mm (5 pcs)
- 590x535mm Rockwool Flexibatts, thickness 45mm (4 pcs) + end insulation
590x2500mm
Internal cladding , thickness 12mm
700x2700mm Polyethylene vapor barrier, 0.2mm
2500mm
Double sided adhesive tape
700mm Double sided adhesive tape (2 pcs)
120x590mm Pre cut insulation to fill voids in structural components (5 pcs)
+ end insulation
45x45mm Wood rafter, length 590mm (5 pcs)
- 590x535mm Rockwool Flexibatts, thickness 45mm (4 pcs) + end insulation
590x2630mm Internal cladding , thickness 12mm
700x2830mm Polyethylene vapor barrier, 0.2mm
2630mm Double sided adhesive tape
700mm Double sided adhesive tape (2 pcs)
120x590mm
Pre cut insulation to fill voids in structural components (5 pcs)
+ end insulation
45x45mm Wood rafter, length 590mm (9 pcs)
590x600mm Rockwool Flexibatts, thickness 45mm (8 pcs) + end insulation
590x5460mm Internal cladding, thickness 12mm
700x6000mm Polyethylene vapor barrier, 0,2mm
- 5460mm Double-sided adhesive tape
700mm Double sided adhesive tape (2pcs)
295x555mm Pre cut insulation to fill voids in structural components (9 pcs) + end insulation
The CASMAZ external component gives the building is final external finish. Vertical Thermwood panels gives the façade a natural warm and durable appearance. As for the interior components, the exterior components are slightly shorter than the structural components in order to facilitate installation and account for tolerances. In contrast to the internal components, these tolerances will not be visible. For detailed manufacturing drawings regarding the external wall components see drawing 005.
EXTERNAL WALL COMPONENT (TYPE A)
25x25 mm Wood rafter, length 590mm (7 pcs)
140x2940 mm Thermowood cladding , thickness 26mm
EXTERNAL WALL COMPONENT (TYPE B)
25x25mm Wood rafter, length 590mm (7 pcs)
140x3255 mm Thermowood cladding , thickness 26mm
The roof is to be covered with minimum two layers of roofing asphalt of which one is preinstalled on the structural roof component.
To ensure the durability of the building components it is essential to keep the structure dry during the construction. The components of the CAZMAZ system will arrive on site packed in flat boxes in closed containers. Since the components are stored dry the building process of the CASMAZ system is accelerated as there is no waiting time required for drying of elements and the external envelope will be closed frame by frame.
The components will come in two containers; one container with all structural components and one with pre cut insulation, internal and external components The second container will arrive when the structural elements are assembled by the costumer The containers are high cube containers that have the following measurements:
External measurements (L x W x H) 12100 x 2440 x 2890
Internal measurements (L x W x H) 12020 x 2330 x 2690
CONTENTS OF CONTAINER 1
OF CONTAINER 2
frame
-Externalwall element 25.5kg
Internalwall element 12.5kg
-Externalroofelement 91kg
Internalroofelement 26.5kg
PREPARATION OF SITE, FOUNDATION, AND PLUMBING
STRUCTURAL FRAMING
WINDOWS AND DOORS
EXTERNAL ENVELOPE HVAC INSTALLATION
INSULATION AND INTERNAL FACING FINAL WALK THROUGH
WEEK 1 WEEK 2 WEEK 3 WEEK 4 WEEK 5 WEEK 6
CASMAZ
1. Place beams on point foundation.
3. Insert insulation batts into floor components, except the last 3 rows which are part of the uninsulated terrace.
figure 1 PB
2. Place structural floor components on beams and mount with angle brackets as seen on figure 1.
4. Place the plywood board, PB, on the floor components 600 mm from the outer edge of the side. This plate ensures a flat working surface for the frame assembly.
23 COSTUMER MANUAL STEP 5
W.E.A W.E.BR.E.
5. Place structural wall frame W.E.A, roof frame R.E. and structural wall component W.E.B on plywood plate PB.
STEP 6
P. PB figure 2
STEP 7
7. Connect plywood P. to the bottom of the frame.
P.
6. Use bolts, as shown on figure 2, to bolt the components together.
STEP 8
figure 3
F.1 B1
figure 4
8. Lift the first frame F.1 so that it fits the outer corner of the floor.
10. Use bolt B1 to connect the bottom of the frame to the floor. Use same type of bolt to connect frames to each other.
9. Assemble the next frame, lift it and place next to the first one.
11. Repeat process until all the structural frames are in place.
12. Placingfinal layer roofing asphalt. The asphalt should be burned on top of the existing layer making sure it overlaps between frames.
13. External wall components are clicked upon the outside of the building.
14. Placeinsulation in the voids of the structural wall components. The insulation is already pre cut and fits perfectly.
15. The internal wall components are installed, by removing the strip of double sided adhesive tape and ensuring the 100mm overlapping vapor barrier and clickingthe component into place.
16. Placeinsulation in the voids of the structural roof components. The insulation is pre cut and fits perfectly.
17. Assemble the special entrance frame in same manner as the previous frames.
19. Windows will be placed in the special frame that will be part of the CASMAZ system.
18. The entrance door is added after assembly of the frame.
20. More detailed information will be added from window company.
The main goal ofthe CASMAZ building system is to facilitate and accelerate the regular building process.
To compare the price of the original building and the CAZMAZ building, there has been made cost estimation for each house. The CAZMAZ building’s price is approximately 80% cheaper than the original house There has not been used professionals to build the CAZMAZ building like the original building, instead the components are made at the manufacturer. It is cheaper to build the CAZMAZ building, because the components are similar in the whole house.
The original building project is a complex and time consuming process since all elements must be cut and joints are to be connected on site by a professional craftsman Furthermore, due to the long building process without coverage, the building willbe exposed to wind and weather, which makes the duration of execution time significantly longer. With the CASMAZ building system, the house will be built up and 'closed off' easy, fast and simple and a non experienced person can easily build the house by the help of the customer manual. The estimated execution time for the original house is around 4months and for the CASMAZhouse 1,5months
Studies show that offsite manufacturing can greatly reduce the waste in the construction industry. This is partly because the processes in the factory are more efficient and predictable Materials can be ordered to precisely calculated requirements and the handling of waste is both easier and cheaper in a factory setting. In a traditional building process, adjustments usually have to be made to elements on site, which leads to more waste.
The original building is only a couple of years old, which makes optimization of energy consumption more difficult since new and high performing materials were used for the building One of the focus areas of the CASMAZ building system is therefore to minimize the size of the living area of the typical leisure house. A smaller living area means less energy consumption since less area needs to be heated or cooled to ensure a comfortable indoor environment. The energy consumption of the original house for heating and cooling has been simulated to be 6531 kWh/year while the CASMAZ building has a consumption of3600 kWh/year
Proper maintenance can prolong the expected lifetime of buildings. With the CASMAZ building system no professional help is required for maintaining the building The materials used in the CASMAZ system are the same as the materials used in the original building, thus the lifespans of the buildings are equal.
Done correctly, a two layered asphalt roofing can last at least 50 years Asphalt roofing is maintenance free, but the service life can be further extended by visually inspecting the roof twice annually, keeping it clean and making small repairs [1].
The heat treated Thermowood facade requires neither surface treatment nor environmentally harmful chemistry of any kind to withstand wind and weather. Expect a minimum 30 years service life for an untreated Thermowood façade [2].
The Thermowood terrasse has an expected lifetime of 15 20 years. Maintenance involves inspecting and cleaning the wood once a year to avoid moisture and fungi [3].
With regular maintenance newer windows in the Danish climate will last for 30 50years. Maintenance involves cleaning windows and frames andchecking for damages Frames should berepainted with 5 7 years intervals [4]
Internal components can be exchanged throughout the lifespan of the building. The tolerances between the internal components make it possible to remove and replace a single component as long as the vapor barrier is correctly sealed off before adding the new component.
Problem: From building the scaled model it was confirmed that each component has to be very precisely manufactured in order for the frames to becorrectly attached.
Suggested solution: The CASMAZ building system requires a manufacturer with the needed experience and equipment to precisely cut and build the components for the building system tobe successfull.
Problem: When assembling the model, interior components were installed before the external components The construction phase is sensitive to and can always be delayed because of weather conditions. In the time period where the building is not ‘sealed off', there is a risk of moisture getting into the structure and introducing a risk ofmold and bad indoor climate.
Suggested solution: By installing the external envelope before the interior, the house is ‘sealed off ' much faster and thereby unthreaded by bad weather and moisture earlier in the building process.
Problem: When the frames are placed next to each other there will be the double number of columns and beams needed, and the load carrying capacity will not be sufficiently utilized when using standardized sizes. The configuration of the elements that cause double beams and columns is chosen in order to stabilize each individual element but will inevitably cause ‘material waste’ seeing that utilization is low with standard measurements.
Suggested solution: Using the optimum size for the elements would mean choosing non-standardized sizes. In the start-up face of the project this could lead to higher costs but would ultimately lower the costs as less material is needed.
Problem: During the assembly of the scaled model, it became apparent that the maintenance of the internal components was more complicated than expected. The initial thought was that damaged internal components could simply be "unclicked" and swapped with a new element. However, this is not possible due to the vapor barriers being taped.
Suggested solution: The vapor barrier is not fixed to the internal components and must be installed in a separately. The building process would be extended and moremanual compared to the present component solution.
A structural 3D FEM model has been designed in Autodesk Robot Structural Analysis for the purpose of investigating the deflection of the frames. For a conservatory result, the frame is modeled to have 3 line supports instead of 4. Loads and load combinations were applied to the model and the maximum section forces in ULS are shown below. Live load on the roof have been accounted for to allow for access to the roof. Deflection is shown for SLS.
Geometry
Height h = 220mm
Width b = 45mm
Span L = 6000mm
Area A = 9900mm2
Moment of inertia y direction Iy 1/12·b·h3 = 39930000mm4
Section modulus Wy 1/6·b·h2 = 3,63E+05mm3
Moment of inertia z direction Iz 1/12·h·b3 = 1670625mm4
Material Material C18
Service class 1
Bending fm,k = 18Mpa
Shear fv,k = 3,4Mpa
Compression Ʇ fibre direction fc,90,k = 0,5Mpa Compression ‖ fibre direction fc,0,k = 18MPa
E modulus ‖ fiber direction E0,k = 6000Mpa
E modulus ‖ fiber direction E0 = 9000MPa
Shear Modulus mean G = 560Mpa
Shear Modulus characteristic Gk G·E0,k/E0 = 373,33Mpa
Structural timber γM γM= γ1·γ2·γ3·γ4, hvor γ1·γ2·γ3=1 og γ4=1,3 = 1,35
I load
Moment My = 1,73kNm
Shear force Fz = 1,67kN
Normal force N = 0,38kN
Moment σm,y,d
Bending stresses fm,d My / Wy = 4,77MPa
Design strength kmod = 1,1 = 14,67MPa
Failure criteria m,y,d / fm,d ≤ 1 = 0,32ok
Shear kcr
Width reduction factor bef In denmark = 1
Effective width τd,max kcr·b = 45mm
Shear stress fv,k 3/2 · fz / bef·h = 0,25Mpa
Design strength kmod = 1,1 = 2,77MPa
Failure criteria τd,max / fv,d ≤ 1 = 0,09ok
Contact pressure l
Support length
Aeff = 200mm
Effective area σc,90,d b*(l+30mm) = 15000mm2
Compressive stress kc,90 Fz / Aeff = 0,11Mpa
Load configuration factor fc,90,d For gluelam = 1,75
Design strength kmod = 1,1 = 0,41MPa
Failure criteria
c,90,d / kc,90 · fc,90,d ≤ 1 = -0,16ok
Compression stresses σc,0,d Fx/A = 0,04Mpa
Design strength fc,0,d kmod = 1,1 = 14,67MPa
Failure criteria
Failure criteria
c,0,d / fc,0,d ≤ 1 = 0,00ok
c,0,d / fc,0,d )2 + m,y,d / fm,d ≤ 1 0,32ok
Torsional moment of inertia Itor h·b3/3 · (1 0,63b/h) = 5821368,8mm4
Effective length lef 0,9·L+2·h = 5840mm
Critical bending stress σm,crit (π · sqrt(E0,k·Iz·Gk·Itor)) / (lef·Wy) = 6,92Mpa
Relative slenderness λrel,m sqrt(fm,y,k m,crit) = 1,61
Buckling factor kcrit for λrel,m ≤ 0,75 = 1
Failure criteria m,y,d / fm,d ≤ kcrit = 0,32ok
Dimension Width w1 = 45mm
Hight h = 120mm
Area of one column A1 w1·h 5400mm2
Length L = 3000mm
Effective buckling length ls = 3000mm
Section modulus Wy 1/6·w1·h2 = 40500mm3
Strength properties
E modulus ‖ fiber direction E0,k = 6000MPa
E modulus ‖ fiber direction E0 = 9000MPa
Shear Modulus mean G = 560Mpa
Shear Modulus characteristic Gk G·E0,k/E0 = 373Mpa
Compression ‖ fibre direction fc,0,k skal slettes og henvise til general = 18MPa
Bending fm,k = 18MPa
Structural timber
Column behavior in y direction for 1 column
hvor
=1,3 = 1,35
Moment of inertia Iy 1/8 ·w1·h3 = 9720000mm4
Radius of gyration i sqrt(Iy / A1) = 42,43mm
Slenderness ratio λ ls/i = 70,71
Relative slenderness ratio λrel λ/π·sqrt(fc,0,k/Ek) = 1,23
Glulam timber β = 0,10 k 0,5·(1+β(λrel-0,3)+λrel 2) = 1,31 kcy 1/(k+sqrt(k2 λrel 2)) = 0,57
Column behavior in z direction for 1 column
Moment of inertia Iz 1/8 ·h·w1 3 = 1,37E+06mm4
Radius of gyration i sqrt(Iz/ A1) = 15,91mm
Slenderness ratio λ ls/i = 188,56
Relative slenderness ratio λrel λ/π·sqrt(fc,0,k/Ek) = 3,29
Glulam timber β = 0,10 k 0,5·(1+β(λrel 0,3)+λrel 2) = 6,05 kcz 1/(k+sqrt(k2 λrel 2)) = 0,09
Column P Load
Modification factor
Kmod, p = 0,6
Normal force N1 = 1,81kN
Compression stresses σc,d N1/A = 0,33518 5Mpa
Design strength fc,0,d fc,0,d ·Kmod,p / γM = 8,30769 2Mpa
Failure criteria 1 σc,d/(kcy·fc,0,d) = 0,07ok
Failure criteria 1 σc,d/(kcz·fc,0,d) 0,45ok
S Load
Modification factor
Kmod,s = 0,9
Normal force N1 = 1,81kN
Compression stresses σc,d N1/A = 0,34Mpa
Design strength fc,0,d fc,0,d ·Kmod,s / γM = 32,64Mpa
Failure criteria 1 σc,d/(kcy·fc,0,d) = 0,02ok
Failure criteria 1 σc,d/(kcz·fc,0,d) 0,11ok
Structural wood, C18 service class = 1 Bolts, M14 strength class = 6,8 fub ultimate tensile strength = 600,0 MPa d shaft diameter = 14,0 mm n number of bolts = 6
Base plate, Ø50 tbp thickness = 5,0 mm
Plate fy yield strength = 235,0 MPa t thickness = 10,0 mm
Forces acting on the bolted connection
Shear force V = 2,9 kN
Normal force N = 0,4 kN Moment M = 0,8 kNm
Space requirements
Parallel to the grain a = 0,0 mm
Perpendicular to the grain
a1 (4 cos(a)) d = 84,0 mm
a2 4 d < 100 mm = 56,0 mm
Loaded end distance a3t 90 < max(7 d, 80 mm) < 90 = 90,0 mm
Unloaded end distance a3c 90 < (1+6 sin(90+40) d) < 90 = 76,0 mm
Loaded edge distance a4t max((2+2 sin(90) d), 3 d) = 56,0 mm
Unloaded edge distance a4c 3 d = 42,0 mm
Polar moment of inertia Ip 2・502 + 4 (1002 + 1002) = 81800,0 mm2
Rotation centre coordinate X = 47,0 mm
Rotation centre coordinate Y = 7,0 mm Distance from RC to bolt R sqrt((100mm + 47 mm)2 + (60 mm + 7 mm)2 = 162,0 mm Resulting force
Double shear connection
M
=
= 1,6 kN/bolt
= 171872,1
=
=
steel
Double
Thick steel
Double shear Connection
=
=
=
=
= 19,0
=
The snap lock connection is designed specifically for the CASMAZ building system. It will be made of a durable and strong type of steel, and therefore it will be able to ensure the required strength. The snap lock will make adding internal elements easy and fast
A cost estimation is carried out in Sigma for theoriginal building and the CAZMAZbuilding system.Working hours are implemented asestimations with500 DKK/hour for professionals in the original building and 333 DKK/hour for the manufacturer of the CAZMAZ building components due to the ability of mass production. It is assumed that the price for manufacturer is 2/3 ofthe price for the professionals and the manufacturer will work 75 hours to make the components.
ORIGINAL
Foundation
Foundation
Floor
Terrain
Roof
Floor 81.330,22DKK
Wall(TypeA)
Roof 372.804,03DKK
Facade 388.914,97DKK
Gables 628.123,90DKK
Manufacturer
Innerwalls 481.137,07DKK
Windowsand doors 159.101,63DKK
The energy consumption has been simulated using the Ladybug tool and Honeybee plugin for Grasshopper and has been carried out using the CAD software Rhinoceros 3D. The parameters used for the energy simulation have not been changed since the CASMAZ building uses the same materials as the original building
The graph shows the energy consumption for heating and cooling of the CASMAZbuilding.
Parameters used for the energy simulation:
U values (W/m^2*K):
Wall: 0.25
Roof: 0.12
Floor: 0.1 Window: 0.6
Heating setpoint: 20 C
Cooling setpoint: 25 C
[1] Phønix Tag Materialer, Vedligeholdelse af dittagpaptag: sådan får du det til at holde (næsten) evigt, (20 01 21)
https://www.phonixtagmaterialer.dk/nyheder/vedligeholdelse af dit tagpaptag s dan f r du det til holde n sten evigt
[2] Södra Danmark, Facader af Thermowood kræver ingen vedligeholdelse, (20 01 21)
https://wwwsodra dk/Facader af Thermowood kraever ingen vedligeholdelse
[3] BergstenThermo Deck, Drift & vedligehold af Bergsten Thermo deck terassebrædder I ubehandlet tgermo træ, (20 01 21)
https://www.bergstentimber.dk/files/Drift-og-vedligehold-Bergsten-Thermo-Deck-1.pdf
[4] Dansk Vindues Verification, Levetid, (20 01 2021)
https://dvv dk/vinduer/levetid/ 1 pdf&usg=AOvVaw2GmY4lODvf7aVjWfbdf