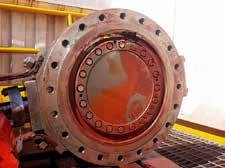
5 minute read
Slurry control valves for abrasive and corrosive slurry
Predictable and costeffective Slurry Flow Control
SlurryFlo Control Valves excel in abrasive and corrosive mining applications, or any process where service life and performance are critical - helping clients save downtime as well as replacement costs. A case study of a recent project in Southern Africa, where SlurryFlo supplied its flagship control valve, illustrated this point.
Advertisement
There is a rule of the thumb in the mining specific slurry pumps: When you get a wrong valve for application in slurry pipes conveying corrosive and abrasive materials, you should expect to spend more on replacement costs, and worse still, to experience long intervals of equipment downtime resulting in loss of potential revenue. That is why it is always advisable to consult slurry valve specialists with a credible track record for informed views on the selection of mining-specific slurry control valves.
SlurryFlo, a company that provides slurry valve solutions to industries in Africa, has been solving complex slurry valve application problems for clients, saving them millions in replacement costs in addition to downtime. The company has been successfully replacing faulty control valves with its rugged SlurryFlo Control Valves for clients.
A problem for an African client
Recently, the team’s Application Engineering Team successfully installed a SlurryFlo valve for a mining client in a country neighbouring South Africa.
The client approached SlurryFlo for a solution to a severe application problem they were experiencing that was costing them dearly due to failure of a 20inch T. This valve would fail after 1 month in service.
Frank Olsen, the local representative for Slurryflo explains how the Engineering Team, approached the major problems the client had encountered, “The application was venting steam vapour from flash vessels. Due to the vapour containing acids and fine particles, the Titanium Butterfly valves would be removed after failure of 1 month and assessed for repair or replacement. This caused lost production due to repeated downtime and high cost of replacement of the valve.” (fig. 1)
Fig. 1
The valves in-line butterfly disc would also accelerate the abrasive fluid towards the downstream pipe walls. This caused premature failure of the client’s titanium pipe. (Fig. 2) further increasing the clients costs due to downtime, repair costs and lost production.
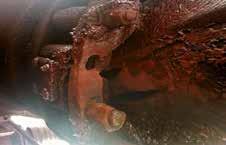
Fig. 2
The Solution
In order to address this problem, the Team’s mandate was to design a solution to prevent the client from replacing their highperformance modulating control Butterfly. With an analysis of the process conditions and modulating history, SlurryFlo’ s engineering team developed a unique ‘dual purpose’ trim (see Fig 3).
As the gate opens, it exposes two small ceramic orifices to vent steam (see Fig 4). Once the flash vessel has been vented, the gate can be retracted further if additional flow is required (see Fig 5). Note that flow is centred within the pipe in both scenarios.

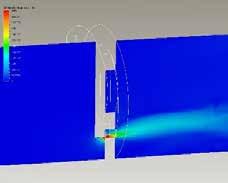
Fig. 4
Return on investment
The benefit of replacing Titanium Butterfly valve with SlurryFlo valves was realised earlier than the client had expected. “Upon replacing their Titanium butterfly valves with SlurryFlo control valve, the client quickly realised a return on investment. During the first inspection (1 month post installation), the maintenance team observed minimal erosion on the wear components,” Olsen narrates.
“As the downstream piping also remained in excellent condition, it was decided to operate the valves for several months between inspections. After 12 months of continuous service, the valve trims are replaced, and the valves are reinstalled,” he adds.
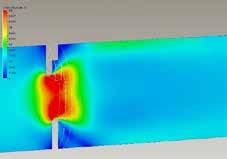
Without question, one area where the benefit of replacing Titanium Butterfly valve with SlurryFlow can be seen is in financial gains.
The financial benefits to the client have been calculated over a period of 5 years - doing a comparative cost of the new engineered Slurryflo Control valve against the Titanium Butterfly valve that was failing prematurely under the severe conditions. Costs for refurbishing the valve and replacement of the butterfly valve based on the history of the plant were taken into account. It was demonstrated that had the client continued with their existing Butterfly Valves, a total cost of $66 million would have been spent.
The SlurryFlo Titanium Control valve over the same period would cost the client $2,1 Million for the initial purchase of new valves and ongoing replacement trims on a 12-month basis. This gives the client a total saving of $63,9 Million over a 5-year period (calculations based on a quantity of 6 valves).

Fig. 6.
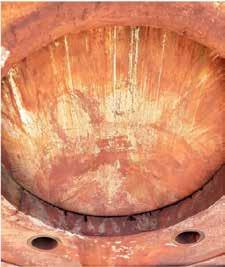
Fig 7.
Titanium Butterfly Valve
1 Month of Service
Titanium SlurryFlo Valve
6 Months of Service
SlurryFlo’s development in Slurry
Control Valves As illustrated above, SlurryFlo’s patented design centre’s flow like no other control valve, centered orifice design keeps abrasive flow away from pipe walls, flow is directed through the center of the valve, protecting the valve’s body and downstream pipe. In general, SlurryFlo control valves excel in abrasive mining applications, or any process where service life and performance are critical.
“The variable orifice technology will outlast all control valves in severe slurry service, giving the client a quantum leap in service life, lasting three to ten times longer than any other “Severe Service” control valve. After a long service life, a simple trim replacement resets the clock,” Olsen guarantees on SlurryFlow’s performance.
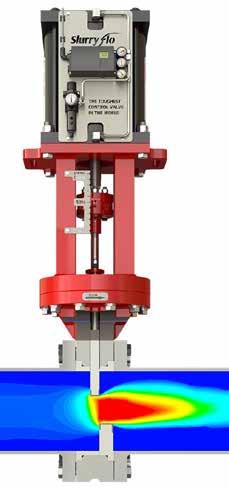
A valve design tailored for the client’s application
SlurryFlo’s engineers tailor a design for the client’s application which is Custom trim Geometry, Client application specific.
SlurryFlo control valves are available for 2” to 60” pipe diameters, and are manufactured to CWP, ANSI 150, ANSI 300 and ANSI 600 standards, provide Class IV shut-off when new, and deep into their service life. SlurryFlo’s unique seating surfaces maintain Class IV, even after substantial wear.
All valves are designed and manufactured in house in North America. SlurryFlo’s African customers are supported locally by Coral Valves based in South Africa.
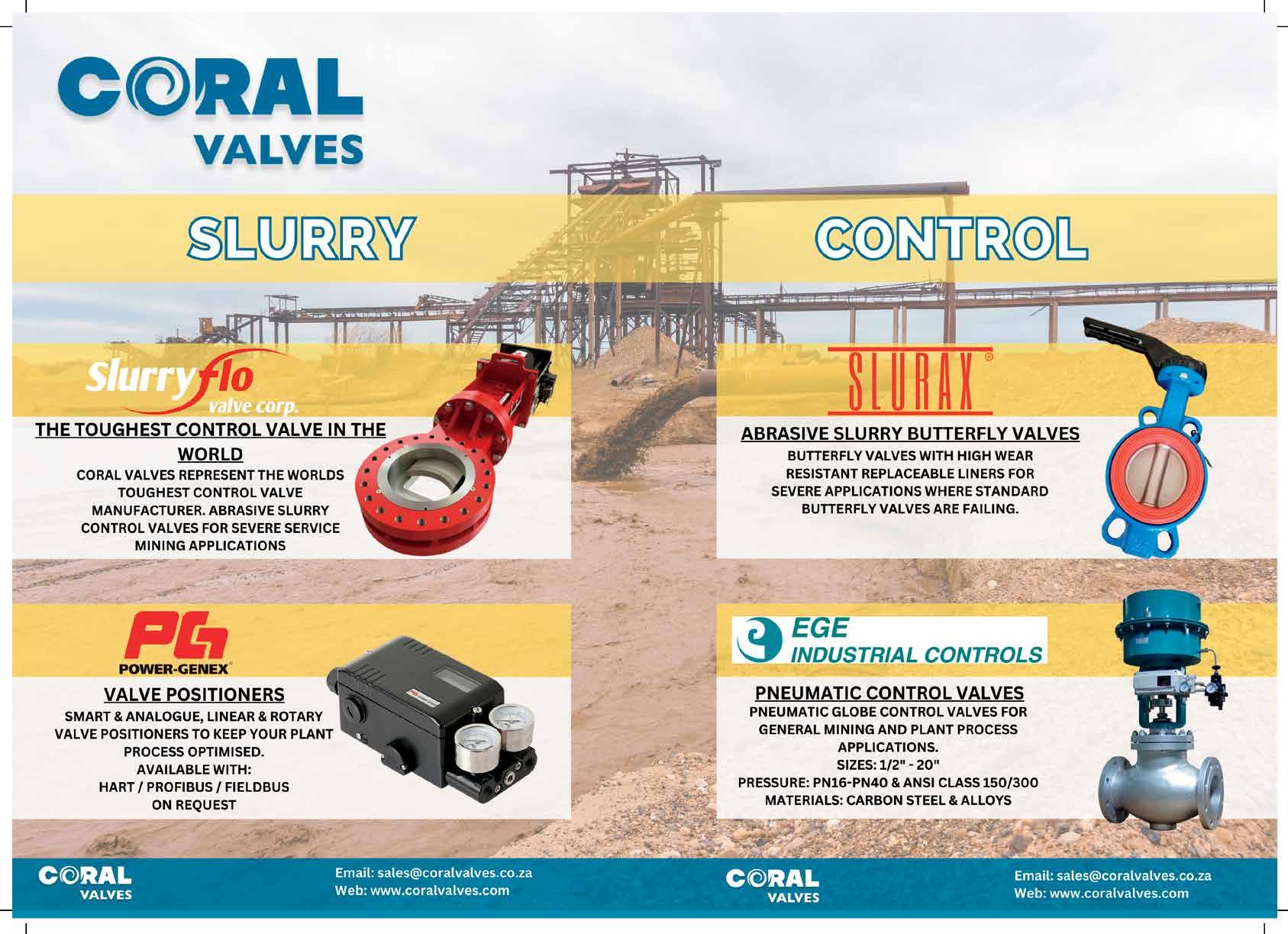
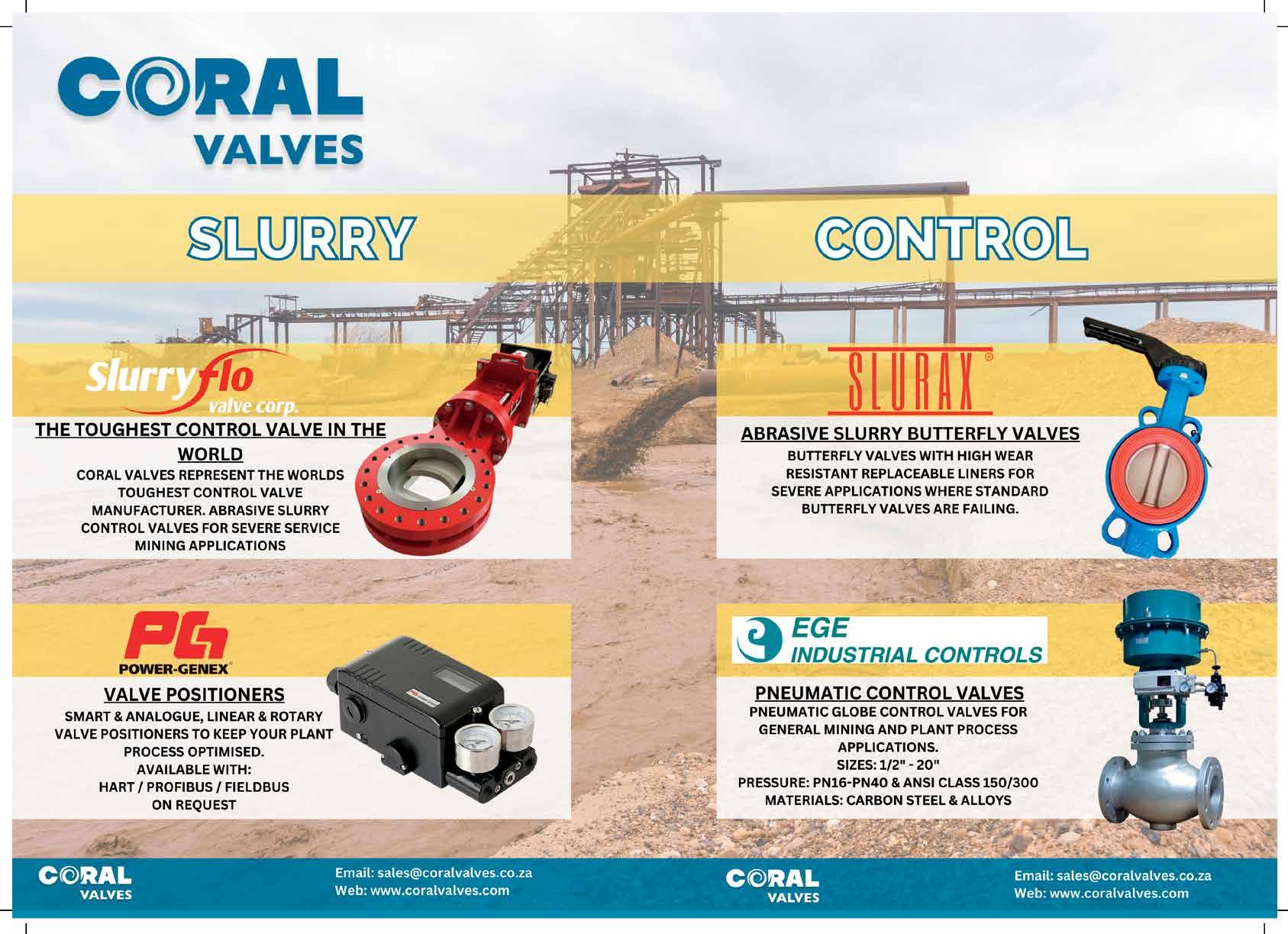