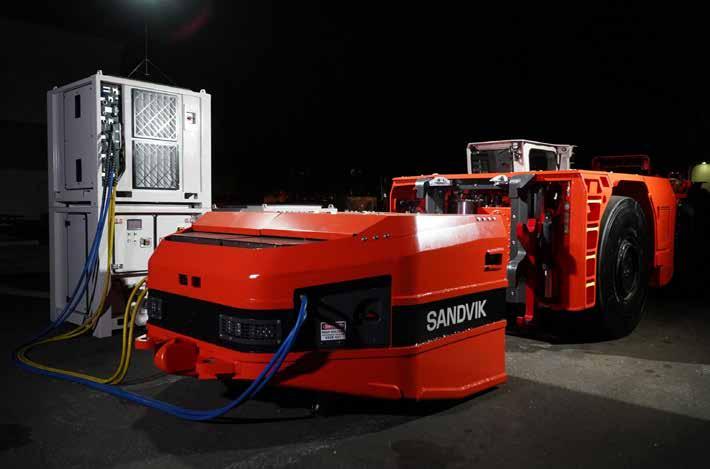
4 minute read
Greener, Safer and Productive Vision for Underground Mining
Underground mining exposes workers and equipment to some of the harshest working environments imaginable. The deepest mines for instance bottom out at over 3km with temperatures reaching 45 degrees centrigrade. However, the advancement of technology is slowly improving the working conditions in these hostile environments. Several mining equipment manufacturing companies are investing in state-of-the art equipment that meet various needs in underground mining.
Each type of mining equipment comes with its own set of mining activities. The most common types of mining equipment vary depending whether the work is being carried out above or below ground or mining for gold, metals, coal or crude oil. From drilling machines to excavators, crushing and grinding equipment – the mining industry comes complete with all the right tools.
Advertisement
Underground mining is carried out when rocks or minerals are located at a fair distance beneath the ground. But then they need to be brought to the surface. Underground specialized mining equipment such as trucks, loaders, diggers etc. are used to excavate the material and are normally hauled to the surface with skips or lifts for further processing. Underground mining techniques have progressed significantly over the past years.
Apart from cost per ton ratio and durability, emissions levels are also a huge factor when deciding on underground machinery. Moreover, recent changes in regulation obligate mining companies to reduce greenhouse gas emissions and improve working conditions in underground environments in which they have operations. Conveniently, advances in electric vehicle technology have made converting a fleet of vehicles from diesel driven to electric to achieve these two critical objectives an attractive proposition.
Companies like Sandvik and Schar, have invested in the manufacturing of battery electric vehicles (BEVs) which promise to be a big part of the future of underground mining. BEVs are poised to play a leading role in improving health and safety, boosting efficiencies and achieving sustainability goals. According to Deon Lambert, business line manager for load and haul at Sandvik Mining and Rock Solutions, the introduction of BEVs in Southern African mines has placed the industry in a vantage point in terms of sustainability.
“For mines who are working towards carbon neutrality, there are options to combine on-mine renewable energy generation with BEVs,” says Lambert. “In countries where grid power is unreliable, this strategy also holds the promise of more streamlined and uninterrupted operations,” he adds.
Scharf’s Managing Director, Shaun Amos, mentions that that BEV’s have emerged as capable alternatives to conventional diesel-powered vehicles in terms of performance and environmental compliance (reducing greenhouse emissions) due to the following features: • Battery equipment does not emit greenhouse gasses during operation; • BEV’s have better performance capabilities due to the advantageous
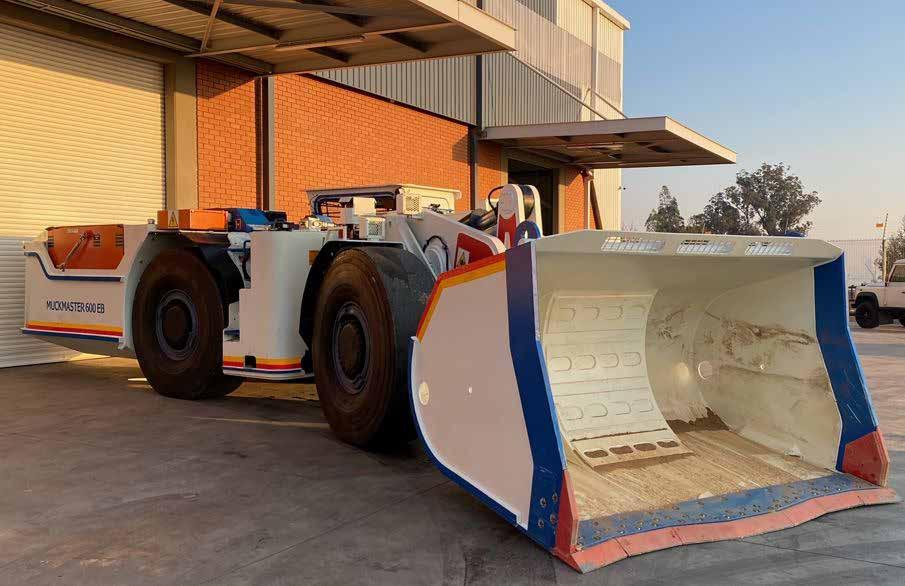
torque curves of electrical motors, which allows for improved tractive effort; • Battery-electrical motor systems are far more energy efficient than fuel/
ICE systems, reducing the generated heat within confined mining spaces.
This drastically reduces the ventilation requirements; • BEV’s have less vibration and noise, which improves operator comfort; and • BEV’s incorporate energy regeneration brake systems to charge the batteries when driving down declines.
He further advises mine operators to take a long-term view when considering adopting battery-powered vehicles as part of their fleet in the underground mining environments. “The ventilation cost saving is the largest benefit when migrating to a battery powered fleet. Ever increasing diesel emission regulations result in more expensive mine ventilation requirements, an issue that BEV’s can completely solve,” he add
With a solid reference base of its batterypowered LHDs and trucks already operating in the field, Sandvik Mining and Rock Solutions has made considerable progress in introducing BEV technology into mines. From 4 t LHDs in 2 to 3 m tunnels to 65 t trucks in 5 to 6 m tunnels, the BEV proposition is well-proven. Mr. Lambert says the key is to ensure that there is the right level of site readiness before bringing any innovation into an existing process.
“For instance, it is clear that BEVs cannot on their own improve on the carbon footprint of an older, cable-trailing fleet if the mine’s source of electricity is still a coal-fired power grid,” he notes. Key to the enabling infrastructure for a productive BEV fleet is the necessary expertise for maintaining and servicing all technical aspects to achieve the expected performance levels.
According to Mr. Scharf, in order to survive in the current mining sector, mines and mining houses need to constantly evolve together with the latest technology to improve productivity, reduce costs and improve mine safety. Excessive conservative mining companies have the large risk of falling behind in terms of productivity and Environmental, Social and Governance (ESG) requirements.
“BEV’s offer the same traditional familiar functionality and flexibility as its conservative diesel counterparts, but with many added benefits. Without a doubt, BEV’s are an avenue which can enable mine operators to be environmentally compliant, safe, and, most importantly, remain profitable businesses,” he affirms.
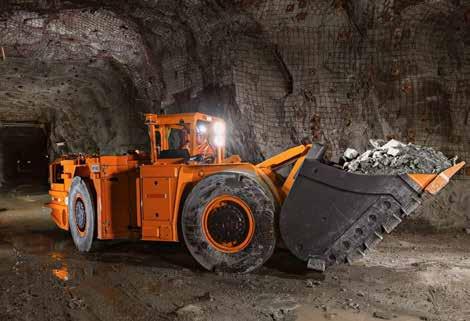
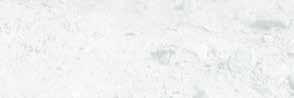
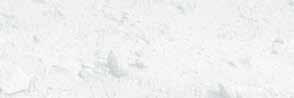