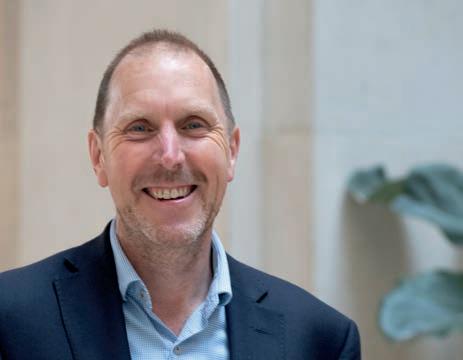
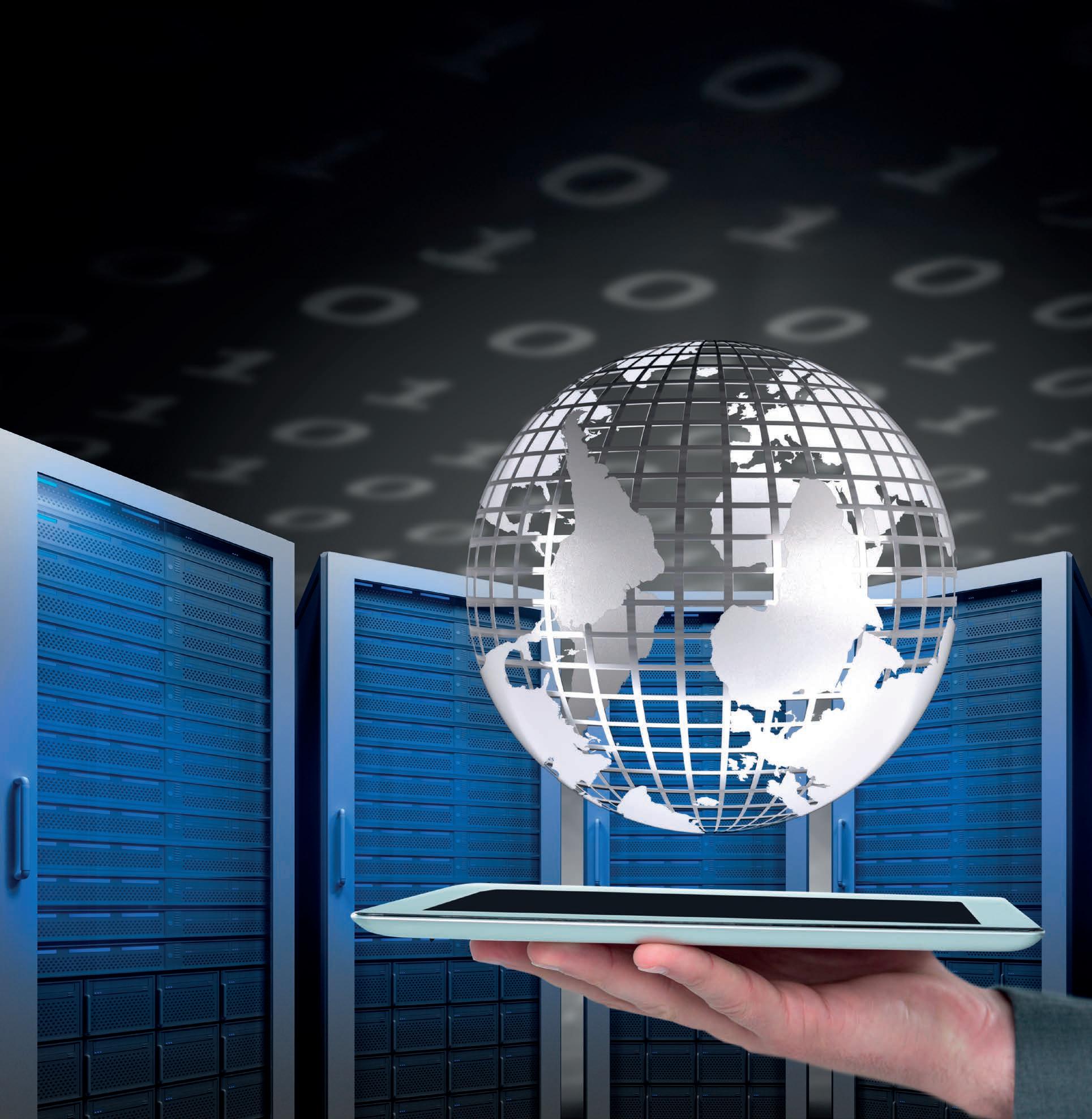
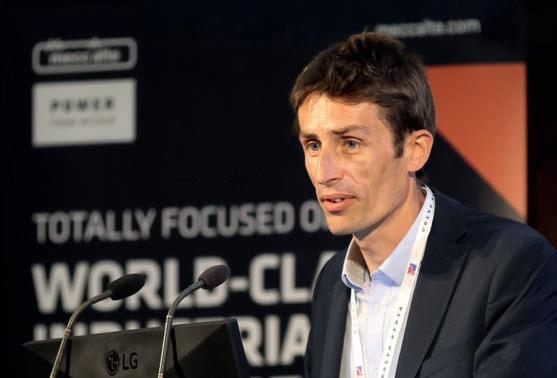

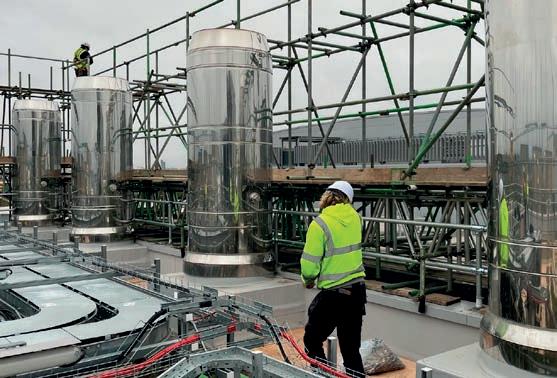
WEDNESDAY 30TH APRIL 2025
Our lunch time speaker is
One of the Goalkeeping GOATS! 574 games for Liverpool – winning 6 league titles and a European Cup. Described as “colourful and charming” with a world of entertaining anecdotes.
PROFESSOR SIMON MICHAUX – Associate Professor at Geological Survey of Finland and Circular Economy Solutions Unit KTR
“Black Swans, White Swans & the Purple Transition – transforming the circular economy”
JAMES DORLING – Senior Consultant, KGP Auto
“Market trends, decarbonisation and emissions impacts for genset manufacturers”
ROB MAY – Keynote and International Business Speaker / UK Ambassador for CyberSecurity at the IoD
BILL ESTERSON MP – Chair of the Energy Security and Net Zero Select Committee
Tickets: £185 + VAT per person or £1,750 + VAT for a table of 10. Numbers are limited.
18: SUSTAINABLE AND RELIABLE POWER
Latest from AKSA Power Generation
20: AMPS’ TECHNICAL COMMITTEE
How the TC is organised for AMPS members
21: SITE POWER MANAGEMENT STUDY
Findings of local authority case study
22: DATA CENTRE EMISSIONS
Extract from WB Power Services’ position paper
24: FROM SHED TO SHOWDOWN
A story of coincidence from Genny Hire Ltd
25: COUPLINGS ARE MAINSTAY FOR GENSET APPLICATIONS
David Proud of Reich Drive Systems UK makes the case
26: DATA CENTRE FUEL FILTRATION
In Norway’s harsh conditions. IPU Group case study
28: ENGINEERING MADE THE WORLD Bernard Gospel on engineering history
30: ACOUSTIC AND EMISSIONS CONTROL
Dürr Universal’s expertise highlighted
32: SELECTIVE CATALYTIC REDUCTION
Agriemach meeting data centres’ SCR needs
34: THE DATA CENTRE MARKET AND BEYOND
Liam Round of Teksan provides his viewpoint
37: AMPS COUNCIL MEMBERS
39: EVENTS DIARY
AMPS partner with PlantWorx exhibition
40: NEW AMPS MEMBERS
Welcome to new member companies
The Heathrow blackout shows data centres aren’t the only facilities that need critical power support.
This issue of AMPS Power is themed around data centres – which have driven the genset market so significantly in recent times. Whilst preparing material for this publication the news broke of the Heathrow shutdown due to a fire at an electricity substation. Heathrow has back-up generators but with insufficient capacity to run the whole facility. A nearby data centre served by the same substation didn’t miss a beat as it has a dozen emergency generators which did their job.
Questions are now being asked about the resilience of airports as part of the critical national infrastructure – as it appears they don’t have the same high standards as data centres.
Director General: Alan Beech – amps@amps.org.uk
AMPS Chair: Louise Hazel - amps@amps.org.uk
AMPS enquiries: amps@amps.org.uk
AMPS Power (editorial & advertising): ampsmagazine@amps.org.uk
This issue of AMPS Power marks the passing of the baton from David Oates to Alan Beech as Director General of AMPS.
David has been an enthusiastic and purposeful DG in in his two years at the helm of the trade association. He has strengthened the profile of AMPS with government contacts at a crucial time when last year’s change of political leadership has brought a new agenda – and the need for a new approach to lobbying and promoting our members’ priorities. To his credit he also clocked up some serious mileage in visiting member companies up and down the country to get their views and support. David has returned to the world of commerce but will remain active in the work of AMPS on a voluntary basis, which is great to know.
We include a profile of our new DG, Alan Beech, in this issue. He will be known by many in our sector for his outstanding support for AMPS for over two decades – as both a Council member and committee leader. He has had a distinguished career working in a variety of roles for some bluechip companies in and around the world of power generation – and AMPS is delighted to welcome him to head up the organisation.
This issue is themed around the exciting growth segment of critical power. Data centres (or centers!) have emerged as the fastest growing market in recent times, with no sign of the exponential thirst for data slackening off. We include some expert contributions on the data centre market, including some case histories and product profiles from AMPS members. It has been a fascinating exercise to receive their expert knowledge and insights for publication.
Finally, at time of writing (despite some cup setbacks) Liverpool FC look set to be crowned Premier League champions for the 2024/25 season. Coincidentally, someone who was a 6-time winner of the league title for Liverpool will join us for the AMPS AGM, Conference & Luncheon on 30th April at One Great George Street, Westminster – when we welcome the legendary goalkeeper, Bruce Grobbelaar.
There should still be time to score a ticket –details on page 2.
The Editor
We’re thrilled to welcome Alan Beech to his new role as Director General of AMPS. He brings with him an impressive 40 years of experience in the power generation and engine industry. Alan is uniquely positioned to raise AMPS' profile and broaden its reach within the Energy sector and beyond –building on the great work of David Oates.
Alan’s journey began with a technician engineering apprenticeship (HNC) at Simon-Hartley Engineering in Stoke-on-Trent, back when in-house foundries and machine shops were still commonplace in the UK. After gaining invaluable hands-on experience in the engineering design office — in the early days of CAD, and the final days of company telephone exchanges, postal communication and Telex machines — Alan set his sights on the commercial side of the industry. In August 1985, he joined Broadcrown as an export tendering engineer and went on to spend 20 successful years with the company. As Broadcrown grew to become a leader in the UK genset industry, Alan rose through the ranks, serving as UK Project Sales Tendering Engineer, UK & Ireland Sales Manager, Commercial Director, and ultimately Managing Director.
In 2005, Alan joined Cummins UK as General Manager for the Power Systems business, where he oversaw loose G-drive sales, CPG dealer sales across the UK & Ireland, and direct project solutions. His market success and strategic vision earned him a promotion to Director of the Power Systems business, with direct engagement in the CPG EMEAR steering group.
EMAR management board in Cologne, Alan played a key role in driving growth and innovation.
In 2019, Alan returned to his passion for sales and power generation, joining Clarke Energy as Sales Director for the UK & Ireland. During his five years there, he spearheaded the distribution of Jenbacher gasfuelled generators and expanded into emerging energy technologies such as carbon capture, energy storage, hydrogen, biomethane, and micro-grid control.
“Links with your peers help guide your business and personal sanity through both bad and good times, and both have their unique challenges.”
Beyond his impressive career, Alan has been a dedicated advocate for AMPS for over 25 years. Since joining the Council in 1999, he has represented multiple brands and served AMPS in various capacities, including Chairman and Head of the Marketing Committee. Reflecting on his long-standing involvement, Alan says, “I’ve definitely put my personal time and effort where my mouth is — as well as marketing budget — even during recessions. Links with your peers help guide your business and personal sanity through both bad and good times, and both have their unique challenges.”
Three years later, Alan took on the challenge of leading Deutz AG’s UK and Ireland operations during a time of significant market transition and economic turbulence. As Managing Director, he guided diesel, gas, and hybrid system sales across a wide range of sectors — including genset, industrial, rail, and marine — while also overseeing parts, service, and warranty operations. Reporting directly to the
Alan looks forward to engaging with members, old, new and yet to join, and for AMPS to serve the diversity of our membership to the best of our ability, with networking, technical support - and lobbying to protect our interests and that of the society in which we all live. His ambition is simply to remain happy and healthy, and to add value. Mentally he says he’s not ready to fully retire but wants to disengage from his direct corporate roles of the last 40 years and use his experience to help others. This is good news for AMPS and its members!
David Oates has completed his term as Director General of AMPS – and shares his reflections on his time leading the organisation…
I believe that, over the last two years, AMPS has strengthened its voice within the relevant government departments and ensured that the views of our industry have been heard at the appropriate levels. We have been involved in various consultation exercises on topics covering decarbonisation, energy security and the transition strategy from now until 2050. I am delighted to have played a role in supporting the views of member companies during this process. We have managed to raise the profile of AMPS across many other trade associations as well. In particular, we have collaborated on key topics with the Industry Forum and EUROPGEN on both UK and EU matters.
Seeing new members join the Association during this period has given me great pleasure as businesses understand the value that AMPS brings as a trade body. There have also been fun times as well – such as the Awards dinners and AMPS’ luncheon events. We have used these occasions to provide the right professional and social atmosphere for members and guests to meet and enjoy the interactions and networking opportunities which they provide.
Being part of the AMPS’ Awards judging panel was a great honour, as I have seen the effort and ingenuity that members deliver to our industry and to recognise them for their achievements. This was a highlight of my tenure in the role. I hope to stay an active member of AMPS in various capacities, but I will let Alan take up the reins and push us forward to the next level.
Thanks to everyone for the support and advice over the last few years. It is certainly a team game and, without your support, we would not have made the strides forward we have made in many areas. More work to do as always, but we are heading in the right direction!
Members of the AMPS Technical Committee (TC) are sorry to be losing Chris Marsland for the second time. Chris was Committee Chair for some years, before a break and returning to the role in 2023. However, he will now be retiring this summer – with the great thanks of all Committee members and AMPS as a whole.
Fontaine succeeds Vincenzo Perrone who has retired after leading the engines division through some of its most successful years in its more than 100-year history….
Eric Fontaine brings extensive experience in industrial markets, having most recently served as Vice President of the Industrial Components Division at Regal Rexnord Corporation. His career also includes key leadership roles at Danaher Corporation and Brunswick Corporation. Kohler Energy rebranded as Rehlko in September 2024.
Last autumn the UK government added Data Centres to the list of sectors included under the protective umbrella of Critical National Infrastructure (CNI) following on from a consultation started by their Whitehall predecessors. This was done for some good reasons. Rob Oliver MBE reports.
UK CNI constitutes critical elements of infrastructure, where loss or compromise could result in major detrimental impact on essential public services, emergency systems, national security, defence, or the functioning of the state.
DCs now fall under the remit of the National Protective Security Authority (NPSA), previously known as the Centre for Protection of National Infrastructure, and the National Cyber Security Centre (NCSC). Other essential infrastructure sectors include energy, water, transportation, nuclear and telecoms. There are 13 other sectors in all. A visit to the NPSA website provides access to their Catalogue of Security Equipment (CSE), available to help security practitioners identify appropriate physical security equipment. This itself represents a change in policy when circulation of the equivalent catalogue in the past was severely restricted, lest potential terrorists or other miscreants learnt too much about the capabilities of security products designed to keep them at bay.
In announcing DC’s new status, the government were keen to show how they related to the public’s everyday life, stating: “Data including vital NHS, financial, and personal smartphone data is set to be safer from cyber-attacks, environmental disasters, and IT blackouts as part of government’s drive for economic growth”. Articles in this issue of AMPS Power point out the value of the localisation of data centres both in terms of data handling efficiency but also security strategy. In an uncertain world order, it makes sense to house critical facilities on, or near to, home shores. The economic by-product is
the generation of an estimated £4.6 billion in annual revenue, with the UK hosting the largest number of data centres in Western Europe.
A study of planning applications for DCs across more than 250 local authorities in England and Wales identified at least 38 separate applications for the construction of data centres in 2024, a rise of 40.7% compared to the previous year. Expect more this year. Government pledges to relax planning laws have specifically mentioned DCs as a priority area for official support. The underlying message is that the UK is a good place to invest in a significant growth area in an infrastructure sector which combines IT, construction, national security and innovation – with the need for significant support services such as critical power.
The quid pro quo is that NPSA, NCSC and other government agencies may feel that their stake in the future prosperity of DCs will extend to further regulation, amended standards – and, in a counterintuitive way, a possible brake on innovation. A plus point is that a more integrated approach to all aspects of security will open the door to more effective collaboration between suppliers. This is another subject dealt with in this issue of AMPS Power. So, we know that UK-housed data centres are good for national security purposes, are good for GDP growth and align with the government’s priorities. I consulted my AI researcher who confirmed that, “By the end of 2025, there will be 6,111 public data centers worldwide—5,544 colocation sites and 567 hyperscale sites”. Today the UK has around 475 of those
Crestchic is experiencing unprecedented demand for its new 200kW loadbank. The stackable loadbank - which was developed specifically for the data centre market - is designed to make heat load testing of server halls and electrical infrastructure simpler, faster, and more efficient.
Paul Brickman, Commercial Director at Crestchic, explains, “With the sector now expecting 99.999% uptime as standard and higher data centre density becoming the norm, testing cooling systems and performing integrated systems tests is increasingly important. As well as helping to identify any weaknesses before critical equipment is deployed, testing generates valuable data on performance under different loads, providing a baseline for future reference that can support troubleshooting down the line.”
At just 1159mm x 876mm x 983mm the load bank has a small enough footprint for operators to link multiple machines and strategically place them at intervals around the hall. Operators can closely mimic the heat generated by servers, replicating airflow patterns and rack configurations such as hot and cold aisles. Multiple load banks can be configured and controlled using just one LC10 handheld digital
controller, enabling fully remote operation and simple management of incremental loads.
In addition to heat load testing, the units are used to connect to Power Distribution Units (PDUs), facilitating testing of the data centre’s electrical infrastructure, including power to servers, switches, bus track power units, feed tracks, tap offs, and other devices. With heavy-duty casters, the loadbank has been built for easy manoeuvrability and can be positioned at each PDU in the server hall, for full system testing. The units have one of the lowest Delta T rises on the market at below 100°C (at the exhaust face), providing a more accurate test of the cooling system’s ability to handle the actual heat load it will encounter during operation.
Crestchic offers a range of solutions for testing backup diesel generators and UPS, heating, ventilation, and cooling (HVAC) systems, electrical bus and distribution cabling, and PDUs. Load testing at the commissioning stage and at regular maintenance intervals can help ensure that systems remain operational and reduce the risk of unwanted and expensive downtime.
200kW units are available for short and long-term rental and purchase.
Data center applications have become the leading end-use application for diesel generators in terms of revenue and already represent 31% of the European diesel generator market in 2024 (in € value). This share is expected to increase and reach 42% by 2028.
The European data center market is experiencing strong growth, driven by cloud computing, AI, 5G expansion, and increasing data sovereignty regulations. The market is fueled by hyperscale providers (AWS, Microsoft Azure, Google Cloud), colocation operators, and enterprises seeking lowlatency, scalable, and energy-efficient data center solutions.
The European data center market is
expected to grow at a CAGR of 12-15% between 2025 and 2028, with investments increasing in hyperscale facilities, colocation and edge data centers. Major tech companies are expanding their European presence, while government policies—such as the EU’s Digital Decade Strategy—are pushing for data localization and sovereignty.
While the Data Center Generator market has been dominated by four major competitors, notably in the hyperscale and colocation markets, the competitive landscape could change slightly, notably in the mid-size and peak colocation data centers, with some new alternative offers from other competitors in the 2500+ kVA range (Himoinsa/Yanmar, Moteurs Baudouin).
Note: CAGR = Compound Annual Growth Rate / DG = Diesel Generator.
1. FLAP-D Markets (Frankfurt, London, Amsterdam, Paris, Dublin)
ʝ These cities remain the dominant data center hubs in Europe due to their robust infrastructure, strong connectivity, and presence of cloud providers. However, challenges such as power constraints, land shortages, and stricter regulations are driving operators to secondary markets.
ʝ Frankfurt: Europe’s largest data center hub but facing power grid limitations. Expansion is slowing due to government restrictions on new data center builds.
ʝ London: The UK remains a top data center destination, but rising energy costs and Brexitrelated uncertainties are causing shifts to Manchester and other secondary cities.
ʝ Amsterdam: Growth has resumed after a temporary data center moratorium, with new projects focusing on sustainable and water-efficient designs.
ʝ Paris: Emerging as a key AI and cloud hub, with major expansions from Microsoft and Equinix.
ʝ Dublin: Facing strict government policies on data center growth due to electricity shortages, forcing operators to look for renewable energy solutions.
ʝ With FLAP-D hubs reaching saturation, investment is shifting to secondary markets such as Madrid, Milan, Warsaw, Berlin, and Stockholm. These cities offer lower operational costs, access to renewable energy, and regulatory incentives for data center development.
ʝ Spain (Madrid & Barcelona): Rapidly growing edge computing and AI sectors are attracting hyperscalers.
ʝ Italy (Milan & Rome): Increased cloud adoption and fiber connectivity expansion.
ʝ Nordics (Stockholm, Oslo, Helsinki, Copenhagen): A preferred location for sustainable, green energy-powered data centers, leveraging hydroelectric and wind power.
ʝ Eastern Europe (Warsaw, Prague, Budapest): Rising demand due to cloud migration, fintech growth, and proximity to Western European markets.
We track the path of the demand for data and the consequent growth in size and importance of Data Centres. Our thanks to expert Luca Beltramino from whose presentation to the 2024 EUROGEN conference this article is drawn.
To understand the seismic increase in the generation, and demand for, data, consider the rise of the Zettabyte. It is ten to the power of twenty-one bytes (10^21 bytes) or to put it another way…
A Zettabyte = 1,000,000,000,000,000,000,000 bytes.
Back in the dark ages of data (2010) the world stock of data was 2 zettabytes – rising to 47 in 2020. Fast forward to 2024 and the global volume of data created, captured, copied, and consumed was estimated at 149 zettabytes. By 2030 this figure is estimated to rise
to 612 in 2030 and 2,142 zettabytes in 2035 (Source: Statista). It is further calculated that 90% of the world’s data has been generated in the last two years.
This immense unit of data measurement represents an astronomical amount of information, far beyond what most people can easily conceptualise. Understanding the scale of the zettabyte is crucial for grasping the magnitude of data being processed and stored in modern data centres.
Approximately 250 billion DVDs 36 million years of HD video
2022 global internet traffic was around 4.8 zettabytes
ONE BILLION 1 terrabyte (TB) hard drives to store data
Data Centres are a key pillar for digital transformation, as businesses are rapidly migrating to the cloud and demanding faster data processing. The growth of Cloud Computing is a major driver of data centre demand, as cloud providers need more data centres to support their growing customer base. In addition, Edge Computing is growing rapidly, as businesses are looking to reduce latency and improve performance by bringing computation closer to users. It means bringing data processing and storage closer to the source of the data, like devices and sensors, rather than relying solely on centralized cloud data centres, leading to faster response times and reduced network congestion. In turn other Newer Technologies like Artificial Intelligence (AI), the Internet of Things (IoT) and 5G are driving demand for more powerful data centres with greater capacity and processing power.
The Evolution of the Data Centre market can be charted in four phases:
1. Phase 1: On Premises DCs – 1995 – When enterprises tended to keep their data “at home”.
2. Phase 2: Big Storage Silos – 2000 – Early data centres were big storage silos. They primarily handled data downloads and uploads.
3. Phase 3: Interconnection Hubs – 2020 – DCs evolved into interconnection hubs. They facilitate faster data exchange between various networks.
4. Phase 4: Distributed Data Centres – NOW! – The focus is shifting to distributed data centres. This has improved speed and volume handling capabilities.
The evolving data centre scene means that installations vary in size and distance to their end users. In broad terms they fall into the following power requirement ranges:
ʝ Large International Core DCs – require 100+ MW.
ʝ National Hub DCs – have a requirement in the 20-100 MW range.
Stacks of books
Would stretch from the Earth to Pluto 20 times
ʝ Near Edge DC – Regional Areas / Regional Colocation – 300 kW-20 MW.
ʝ Far Edge Points of Presence (PoPs) / local services, on premises, IoT – 10-300 kW.
The role of generators in data centres is now well established. As a Backup Power Supply generators play a critical role in colocation data centres. They ensure continuous power supply in power outages or grid failures. Uninterrupted Power Supply (UPS) systems kick in immediately to provide short-term power in the event of power failure. Generators start up to take over from the UPS. The two systems must be integrated to ensure that the transition happens seamlessly to avoid downtime. Multiple generators are used to provide redundancy. This means that if one generator fails another one can immediately take over. Redundancy is essential for high availability (99.999% uptime) as required by the data centre’s customers. There are also environmental considerations. These are recognised by the use of lower-emission generators or integration with alternative energy sources such as solar or wind, to complement generator power during outages.
Addressing the data deluge requires innovative approaches to data centre design and management. As Edge Computing brings data processing closer to the end user and AI itself will be used to manage data centres more efficiently to create AI-driven optimization. Quantum computing will become increasingly important in using the principles of quantum physics to perform calculations that are impossible or extremely difficult for classical computers. This will lead to exploring new paradigms for data processing and storage. Meanwhile sustainable design is needed to create energy-efficient data centres for the future.
Luca Beltramino is: Chief Data Center Officer @ Rai Way President of Ge-DIX – Genova Data Internet Exchange Vice President of IDA – the Italian Datacenter Association www.italiandatacenter.com
It proved to be a busy time in March for AMPS and its Member Companies lending their support to two important trade shows held on the same dates. Data Centre World (part of Tech Show London) was held at the Excel exhibition centre and the Distributed Energy Show at the NEC, Birmingham. The respective show dates for 2026 have been released – and supporters of both will be pleased to see that they will be a week apart.
Data Centre World will be held on 4-5 March 2026; and the Distributed Energy Show will be held on 11-12 March 2026.
The UK’s leading manufacturer of industrial generating sets and OEM supplier of CKD engines, alternators and spare parts will head to Dubai for the Middle East Energy exhibition with a new-look brand, new faces and refreshed innovation.
The Allam Power stand will once again present the very best in UK manufacturing, with a range of open and canopied generating sets from its Tempest brand, along with a selection of engines and alternators from its technology partners in the UK and Europe.
David Oates, recently appointed CEO of Allam Power, is looking forward to meeting suppliers and customers at the event, and explained why having a presence at MEE is important:
“We’ve been investing heavily in research and development, working with globally-recognised engine and alternator brands to differentiate Allam Power products from low cost, low quality competition in the market.
The MEE exhibition is a valuable opportunity to support our customer and supplier base, and we’ll even be showing off one of our prototype canopy designs, which I hope will open up discussions around how our products, made in the UK, will continue to keep us in a leading position when it comes to reliable, competitive power solutions for extreme industrial environments all over the world.”
David will be joined at the exhibition by well-recognised and longstanding colleagues from Allam Power and its Tempest brand. Customers and suppliers are encouraged to visit their stand, and email info@allam.com to arrange meetings with individual members of the team.
ai174222530328_BR43442 Allam Power Ltd - March Marketing Support - advert 184x124mm.pdf 1 17/03/2025 15:28
The UK data centre market is changing fast with the rapid advance of digital technologies, the emergence of generative AI and the proliferation of hyperscale data centres. This presents challenges and opportunities for energy consumption, sustainability, and resilience. This article from AMPS members Edina UK sets out how they are tackling the opportunities.
As data centres become more integral to the global economy the demand for power generation and energy storage solutions has never been higher.
Hyperscale data centres, designed to support massive computing and storage requirements, are growing fast and driven by the increase in cloud, big data, and generative AI. They require significant power to maintain servers, cooling, and networking infrastructure, so much so that the National Grid predicts the rise of AI and quantum computing could lead to a sixfold increase in energy use over the next 10 years, placing the grid under considerable strain.
To meet this demand, innovation in generation and grid infrastructure will be required to address this imbalance.
Data centres powered by gas engines can provide operators with increased profitability due to the flexibility of the gas engine asset and improve the security of supply by addressing grid capacity limitations.
Gas engines can provide continuous power to meet uptime requirements and be deployed in remote areas where an electrical connection is absent. Their modularity allows for scalable deployment, making them perfect for rapidly expanding hyperscale facilities.
Gas engines are fuel flexible and use low-carbon natural gas, biogas, biomethane, and hydrogen blends. This fuel flexibility allows data centres to choose a fuel source that aligns with their operational goals and sustainability initiatives.
Gas engines configured for Combined Cooling, Heat, and Power can provide reliable power and mechanical cooling via absorption chilling. This process takes advantage of the waste heat generated by the gas engine. The heat that would typically be released into
the environment is captured and used to drive an absorption chiller, which then produces chilled water or air for cooling applications.
Standby diesel generation is critical to data centres which are the backbone of modern society. Standby generators provide a reliable backup power source during grid outages or power disruptions so servers, cooling systems and other critical equipment keep running.
This prevents data loss, service disruption and financial loss for businesses that rely on 24/7 uptime. With many installations opting for hydrotreated vegetable oil (HVO) fuel to address environmental concerns and sustainability, standby power gives immediate highcapacity power during emergencies and will remain a cornerstone of data centre resilience strategies.
By storing energy during periods of low demand or when renewable energy generation is high, BESS can provide reliable backup power during outages or peak demand times. This ensures continuous operation and stability of data centre infrastructure, which is crucial for maintaining uptime and preventing data loss.
Additionally, BESS enables data centres to perform peak shavingusing stored energy to reduce electricity consumption during peak periods when energy prices are highest. This practice significantly lowers demand charges on electricity bills, resulting in substantial
Edina installed four 1500kVA HVO standby diesel generators at a data hosting facility in Dublin, Ireland. The project included detailed design, engineering, and build, including the design of the main generator plant room to meet 55dBA at 10m noise guidelines. Edina’s team installed and commissioned the standby generators and grid protection controls to provide backup power and enhance the facility’s energy resilience.
cost savings. The BESS asset can also participate in grid services, offering additional revenue streams and contributing to grid stability.
To optimise performance, efficiency, and resilience, gas engines can co-locate alongside battery energy storage systems, standby generation, and renewable energy technologies to complement the data centre power infrastructure. This integration addresses site loads and alleviates grid constraints so data centres can meet their operational demands while contributing to a sustainable energy future.
Microgrids using multiple forms of low-carbon and renewable on-site generation, standby power, and energy storage can provide a robust framework for continuous power supply. Controlled by a sophisticated energy management system, microgrids offer enhanced energy resilience, sustainability, and reliability, and can scale with future growing energy demands.
Edina is an EPC contractor specialising in the engineering, installation and asset care support for on-site power generation and battery energy storage systems.
With over 40 years of experience, Edina has delivered 1.1GW of electrical contracted projects in the commercial and industrial sectors and almost 650MW of large-scale grid infrastructure projects.
We are the official distributor for MWM gas engines – built for performance, efficiency, and availability.
We can also provide Uptime Institute-compliant diesel/HVO standby power generation gensets with engine after-treatment engineered for high performance, adaptability, and emissions compliance, Tier-1 battery energy storage systems with integrated energy management controls and interfacing – delivered from a single point of contact.
Delivering Power Solutions to the Next Generation – visit us at www.edina.eu.
To enhance the grid’s capacity for integrating renewable energy, Edina provided an EPC solution for a new energy centre featuring 10 MWM TCG 2020 V20 gas engines. As part of the scope of works, Edina designed, engineered, project managed, commissioned, and provides long-term asset-care support. The high-efficiency, fast-start MWM gas engines were installed in a custom-built energy centre, designed to offer grid-balancing services, ensuring continuous power supply. By stabilising the grid, these engines are essential for accelerating the growth of renewable energy, ultimately contributing to a reliable and sustainable power supply.
AKSA Power Generation, a global leader in energy solutions, proudly announces its latest advancements in the European market with two groundbreaking product series: the Stage V Series and the RP Series. Both series are tailored to meet the evolving demands of sustainability, reliability, and regulatory compliance, ensuring AKSA continues to be a trusted partner in power generation across the region.
Manufactured in AKSA's state-of-the-art facility in Spain, the Stage V Series exemplifies the company’s dedication to producing cutting-edge solutions aligned with stringent EU Stage V emissions standards. This series combines advanced engineering with sustainability-focused design, meeting the diverse needs of industries while reducing environmental impact.
1. Unparalleled Reliability: The Stage V Series is designed to operate seamlessly under various conditions, making it a dependable choice for critical applications.
2. Low Noise Levels: With noise emissions as low as 62 dBA at 7 meters in select models, this series offers one of the quietest operations in its class, ensuring minimal disruption in residential or commercial environments.
3. Local Adaptability: The Stage V units are versatile and can be customized to meet country-specific requirements for markets like the UK, Germany, and Switzerland, providing localized solutions for a wide array of applications.
4. Sustainability Advantages: These units align with AKSA’s commitment to eco-friendly practices, featuring reduced emissions, efficient fuel consumption, and long service intervals, all contributing to a lower carbon footprint.
5. Made in EU: Manufactured entirely in Europe, the Stage V Series underscores AKSA’s investment in the region, ensuring highquality standards and compliance with local regulations.
RP Series: Robust Outdoor Power for Diverse Applications.
In addition to the Stage V Series, AKSA introduces the RP Series, a new line of backup power solutions specifically engineered for outdoor applications. Designed with durability and practicality in mind, this series is ideal for industries requiring reliable power in challenging environments.
1. Solid and Durable Canopy: The RP Series features a robust canopy that ensures optimal performance in outdoor conditions. Its sturdy construction provides enhanced protection against environmental elements, ensuring longevity and reliability.
2. Leakage Protection: Advanced solid leakage protection systems
make this series suitable for sensitive outdoor spaces, reducing the risk of spills and environmental damage.
3. Low Noise Emissions: Operating at just 65 dBA at 7 meters, the RP Series is designed to minimize noise pollution, making it an excellent choice for residential, commercial, and industrial applications.
4. Flexible Engine Options: The RP Series is available with Baudouin, Cummins, and Doosan engines, offering customers a range of trusted power sources to suit specific operational needs.
5. EU Compliance: Fully compliant with EU regulations, this series provides peace of mind for customers looking to invest in futureproof power solutions.
To meet the demands of its growing customer base, AKSA Power Generation has established robust distribution channels in the UK and the Netherlands, ensuring that both the Stage V and RP Series are readily available for immediate shipping. This strategic presence enables faster delivery times and enhanced support for clients across Europe.
As industries across Europe face increasing pressure to adopt sustainable practices, AKSA Power Generation remains at the forefront of innovation, offering solutions that balance performance with environmental responsibility. The Stage V Series and RP Series
represent AKSA’s ongoing commitment to delivering products that not only meet but exceed the expectations of modern power users.
By combining cutting-edge technology, regulatory compliance, and a focus on sustainability, AKSA Power Generation continues to set new standards in the industry. Whether it’s powering critical infrastructure, supporting businesses, or enabling remote operations, AKSA is the name industries can trust for dependable and ecofriendly energy solutions.
For more information about the Stage V Series, the RP Series, or to place an order, contact AKSA Power Generation today – sales@aksauk.com
One of the key AMPS’ membership benefits is derived from the work of the Association’s Technical Committee. In this article, AMPS’ Technical Secretary, Bernard Gospel, provides a briefing on how the Committee functions…
To provide AMPS with clear technical guidance on national and international standards that are relevant to their businesses together with access to industry experts to provide advice on technical matters.
The Technical Committee aims to be involved with National and International standards bodies, Government and regulatory authorities, to represent AMPS members’ interests and by influencing, communicating and understanding the relevant technical standards for our industry.
The Committee’s brief is technical only, we do not discuss anything commercial, at the start of each meeting the Chairman reads the following, which is repeated in the agenda:
“Attendees are reminded that AMPS is committed to complying with all anti-trust and competition laws and regulations. To this end the Association has adopted a competition compliance code. Conformity with the code is a condition of AMPS membership. Failure to abide by anti-trust and competition laws can have grave consequences for the Association, member companies and individuals concerned. Copies of the Code of Conduct are in the possession of all member companies and further copies are available on request”.
Some other key points from the Committee’s
The Technical Committee (TC) represents the interests of all members of AMPS. The TC Members do not just represent their own company, they have to consider the interests of the whole membership. The requirement to inform and consult with the whole membership is done via Current Thinking E-shots from the Technical Secretary, AMPS Power magazine articles and presentations at Regional Events.
The Technical Committee should have a membership proportional to the size of AMPS Membership and should have members’ representatives of major product areas (consideration being given to the practical limits of the size of the Committee).
So, the membership of the TC is proportional to the size of the membership and should represent the major product areas, e.g. generating sets, engines, generators, radiators, switchboards and control panels, transformers, fuel tanks and consultancy services, to list but a few!
However, there is a practical limit to the size of the committee, which is about 20 attendees at meetings. To minimise costs (AMPS Members’ subscriptions!), most meetings are held at members’ premises. Twenty seems to be about the maximum size of members’ meeting rooms. This is one reason why we may have to limit or prevent the invitation of members and guests to the meetings, which is becoming a more frequent occurrence.
To enable AMPS Members to have a personal insight into the major issues which the TC is working on, without them attending meetings,
we have instituted seminars, and other means of bringing TC members to the AMPS Membership at large. This is one of the Technical Secretary’s remits: to publicise the Technical Committee.
The TC meets four times per year, generally in January, April, July and October. The two ‘winter’ meetings are now held by video call, the summer meetings face-to-face only.
So where does the Technical Secretary fit into this? His specified duties include:
ʝ Assistance to the AMPS TC Working Groups to facilitate timely responses and publishable reports.
ʝ Managing the AMPS technical helpline queries from member/ non-members in conjunction with the AMPS’ TC and Secretariat.
ʝ Compilation and recording of agendas and minutes of TC. Any necessary reports for the AMPS Council meetings as appropriate on any respective technical issues.
ʝ Any necessary reports for the AMPS Council meetings as appropriate on any respective technical issues.
ʝ Work with AMPS Marketing Committee to maintain Jargon Buster and ensure other high quality Technical Committee output including website and email newsletters.
ʝ Be a literature member for relevant standards committees.
ʝ Management of the response to Technical Queries.
ʝ Management of consultations in areas relevant to AMPS Members.
The Working Groups are the core of the committee, since the majority of the work is undertaken by the Workgroups, working as a team or by representation on BSI and other committees. Workgroups rarely meet face to face but usually communicate by conference call or email.
The Workgroup Leaders each normally issue a report to the TC before each meeting, this is then presented to the TC at the meeting, with any discussion recorded. This then enables the actual TC meeting to be shorter and more focussed. It will be noted that membership of a TC Workgroup, and /or an external committee, such as BSI, or other entity is a requirement of TC Membership, as defined in the TC Constitution. We will look closer at the Working Groups in a future article.
The Construction Plant-hire Association (CPA) reports on a local authority case study highlighting the need to focus on Site Power Management to help tackle air quality and carbon.
Generators on construction sites are typically oversized or underloaded. A bigger generator means more fuel consumption, and lower load means less fuel efficiency, a perfect recipe for high CO2 emissions. However, decarbonising generators is no easy task, as they provide power to site when grid connections are not available.
The Regulatory Services Partnership of Merton, Richmond and Wandsworth Councils carried out an independent case study into the potential carbon and air quality savings in managing site power through Battery Energy Storage Systems (BESS). The study recognises that these machines will remain reliant on fossil fuels and HVO for some time to come and highlights the need for a new focus on power management on construction and demolition sites to minimise consumption of these fuels. It recommends power management as a key consideration at the planning stage, having independently estimated a 57% fuel saving and 85% reduction in engine run time on this particular application.
Other key findings from the study include:
ʝ Generators are more polluting than any other type of NRMM, representing 11% of the fleet, but 36% of the tailpipe CO2 emissions.
ʝ Telematics is an extremely helpful tool to monitor and optimise fuel savings.
ʝ Engineered solutions to conserve power, such as timed sockets, further reduce fuel consumption and make it easier for sites to transition to these battery systems.
ʝ The use of BESS brings generator loading up to a much healthier level, reducing the risk of maintenance issues.
The report concludes that power management on construction sites is a logical progression on the pathway to cleaner equipment, but requires external drivers to ensure demand, and provides recommendations on how this could be implemented through Local Authorities.
The CPA welcomes this case study as a significant first step in the acknowledgement of efficiencies and pragmatism in the journey to decarbonise. There are a broad range of options to reduce fuel consumption that can be included in these considerations, such as;
ʝ Being more mindful of generator sizing.
ʝ Reducing power consumption so a smaller generator can be used.
ʝ Load on demand, with two or more smaller generators coming on and off as required instead of one big generator running all the time.
ʝ Using flybrid to cover spikes in power demand.
ʝ Using BESS to hybridise a regular generator, or enhance a small grid connection.
ʝ Using transportable battery systems to replace traditional trolley generators.
ʝ Generating power with on-site renewables such as wind or solar, to reduce dependency on conventional fuels.
ʝ Fuel additives that improve fuel efficiency.
ʝ Using a combination of the above.
The public sector could lead by example by exploring these options in their own procurement and pricing them into jobs.
These solutions are site specific, there is not one solution that will fit all sites and some approaches are more advanced than others. Expectations must be reasonable, taking into account availability, suitability and cost. Power management will usually save sites money, but not always, and some options still require substantial up-front investment. The current economic environment makes any such investments very challenging for most businesses.
We encourage local authorities to include CPA and the wider industry in the formation of any guidance and frameworks being considered, to ensure that those proposals are deliverable.
This article reproduced by kind permission of the CPA.
A recent WB Power Services position paper, authored by AMPS Council member, Geoff Halliday , highlights how existing legislation is not a good fit for standby generators at Data Centres. The paper looks at the impact of the Industrial Emissions Directive and Medium Combustion Plant Directive on Data Centre emissions permitting.
We reproduce extracts from the document below – for the full paper, email ampsmagazine@amps.org.uk
Introduction
Air quality in the UK is a massively important issue, with pollutants such as oxides of nitrogen (NOx), known to be injurious to health are problem particularly in urban areas. Data centres, even those located within urban areas, make a negligible contribution to overall levels of pollutants like NOx, but certainly have the potential to. This potential is directly linked to the significant amount of standby diesel generating capacity required should there be a failure of the grid/
DNO power supply. As this plant is installed for emergency/standby use only any impact from running the sets would only have a relative short-term impact on local air quality.
The Industrial Emissions Directive 2010 (IED) is an EU directive that aims to control pollution from a wide range of industrial emissions of air pollutants, discharges of wastewater and generation of waste which includes emissions from standby generators, but it is poorly designed for standby generators particularly when they are installed in large data centres. As a result, it is of itself disproportionately burdensome for operators to comply with particularly when combined with the requirements of other legislation such as the
Medium Combustion Plant Directive (MCPD), The Clean Air Act other regional or local requirements e.g. ULEZ etc.
The Environment Agency (and other devolved organisations such as National Resources Wales) is rightly insisting that operators meet the requirements of these directives particularly those relating to Nox emissions which can be the costliest to implement but not always as effective as believed. Neither the Data Centre operators or Generator dealers / installers were not involved in the original consultation process and hence from an operational point of view these requirements have never been the subject to proper due diligence or the rigors of a thorough cost benefit analysis process, have not been formally discussed or consulted on with either the supply chain or the data centre industry, so there is no real clarity as to if these measures are working effectively or are appropriate for the sector. Operators do not appear to be arguing against the need to mitigate air quality impacts, nor against the additional costs that procuring compliant plant will impose in future, but against the lack of any formal communication, clarity of objectives, consistence in how rules are seemingly being applied and the lack of any formal notice all of which make it very difficult for UK operators to meet their formal obligations.
Emissions controls and permitting of Data Centres in England is managed by the Environment Agency (EA), in Wales it is managed by National Resources Wales (NRW), in Scotland Environment Scotland and in Northern Ireland it is the responsibility of the Northern Ireland Climate Commissioner. Both of the legislative documents (IED and MCPD) discussed in this paper are “directives” and as such are open to interpretation as to how they are implemented from jurisdiction to jurisdiction and even within a jurisdiction.
Both the IED and MCPD were developed to achieve an overall reduction in levels of emissions(predominantly Nitrous Oxides or NOx from) power generation plant that is embedded within the countries’ infrastructure. Whilst this approach is hugely important and to be commended is often the case that there are some unintended consequences that flow from it. Some of those unintended consequences are linked to an inconsistent approach to either the advice given, or requirements imposed, a “belts and braces, can’t get this wrong” approach to the problem or a type of installation which was never envisaged at the time of drafting becomes a challenge or misfit in the permitting system. It is the latter that seems to apply in part to hyperscale data centres; they are somehow a misfit in the system.
By way of some simple examples give an indication to the nature of the problem.
ʝ Early recommendation of the adoption of generators able to meet TA-Luft2g as a benchmark for meeting the emissions target. Engine manufacturers had for many years been focused on reducing fuel consumption. Meeting the TA-Luft2g meant burning more fuel to reduce NOx.
ʝ Producing engines that are fuel optimised (FO engines), rather than NOx optimised actually are better suited to the fitment of a Selective Catalytic Reduction (SCR) system. If you have to fit an SCR anyway you might as well reduce the amount of fuel you burn too
ʝ Many large data centres are now fitting SCRs as standard whilst at the same time being pushed to reduce overall fuel consumption and or hours run at full load by the generators for test purposes. Running a generating set at no load means that the engine and SCR will never achieve the operating temperatures required for the catalytic process to take place which enable the NOx to be removed from the exhaust by the SCR. Thus, negating SCR operation all together.
The sector needs a collective voice on how best we can move forward to achieve a common objective within a defined and clear timetable. It is the author’s view that:-
ʝ All stakeholders need to work together to develop a bespoke Industry Code of Practice for Generating Plant.
ʝ The code of practice needs to be presented to the appropriate government body for approval and formally announced to operators and the supply chain through government websites and industry associations.
ʝ A clear timetable for compliance needs to be agreed with operators and the supply chain.
ʝ Government to confirm full details of how site testing and monitoring is to be implemented and run.
For Cameron Black, rallying was never just a hobby—it was in his blood. Born in 1996 into a Mazda rally family, there was little hope he’d avoid the motorsport bug. But neither he nor Genny Hire Ltd could have predicted just how closely their paths would align.
A Blind Buy, A Big Surprise: on 26th October 2019, Cameron Black took a chance, purchasing what was advertised as a "spares shell" from an online auction. His only plan was to strip it for parts to keep his dad’s rally car running. A week later he collected the car, steering it onto the trailer using vice grips. But once he saw the condition of the chassis, he had a new plan—this wasn’t just spare parts; this could be a full rally car rebuild.
The shell was stored in the Black Motorsport Shed until May 2020, when COVID boredom struck. With plenty of time and nowhere to go, Cameron got to work. Over months of self-isolation in the shed, the car was stripped down to a bare shell, bodywork corrected and painted. Sourcing parts from as far as Austria, he rebuilt the engine and gearbox.
First Run, First Hurdle: by July 2020, it was time for the first test at Crail Raceway. It didn’t last long—the head gasket blew. Another rebuild followed over winter and spring 2021, as Cameron continued fine-tuning the car, eagerly waiting for rally events to return after COVID restrictions.
Then, fate intervened.
A Connection to Peter Emslie and Genny Hire: in June 2021, an off-hand conversation between Cameron and his dad revealed an astonishing fact—the car had once belonged to Peter Emslie, the late founder of Genny Hire Ltd. Excited by the discovery, Cameron’s dad sent photos of the rebuild to Genny Hire MD Lorna Clark, sharing Cameron’s dream of competing in the Scottish Rally Championship. Just weeks later the
Mazda was back at Genny Hire—a full-circle moment that reconnected Cameron with the company that would soon become a major part of his life. On 14th August 2021, Cameron made his competitive debut at the Grampian Forest Rally, and from there, the rallying journey accelerated. Supported by Genny Hire, he competed in 2021 and 2022, securing 3rd in class overall for the 2022 championship.
From the Rally Stage to the Genny Hire Team: in February 2023, Cameron found himself on the job market and reached out to Lorna. The response? "You’re Nae allowed to leave!" He joined Genny Hire Ltd as a technician, working his way up to Operations Supervisor while continuing his rallying career. By September 2023, he had achieved his best result yet—18th overall and 1st in class at the Galloway Hills Rally.
Full Circle - the 2025 Season Awaits: Now, in 2025, the story has come full circle. Genny Hire, founded by the man who once owned Cameron’s rally car, now sponsors both him and the Mazda, ensuring Peter’s legacy continues. From an abandoned shell to a championship-contending machine, the journey is proof that the right car, the right team, and a bit of fate can take you further than you ever imagined. With Genny Hire behind him, Cameron is ready to hit the stages once again keeping the spirit of Peter, the Mazda, and Genny Hire alive in the world of rallying.
Based in Kintore, Aberdeenshire, Genny Hire were highly commended in the AMPS Member Company of the Year Award 2024. Find out more about them at www.gennyhire.com
Data Centres house and process the data that the world now relies on to keep it moving.
For the Generator Set Manufacturers that provide their sets into Data Centres it is critical that they can rely on the components in their sets to function and perform when needed.
In this article, David Proud, General Manager of Reich Drive Systems UK, explains why their Arcusaflex coupling, which is just one part of a comprehensive range, is still the mainstay of Generator Set applications to connect the engine to the alternator, even although it was first introduced some 40 years ago.
of run time in the field, a significant achievement in itself and one which reinforces the reputation for reliability. The philosophy of manufacturing both the elastomers and machined components inhouse also ensures ongoing and ready availability of spare parts.
The Arcusaflex range of drive couplings have been at the heart of the Reich portfolio for decades and are still in demand across a wide range of sectors for arduous applications, due to their impressive track record for performance and reliability. The coupling element can be subjected to high torsional loads and can compensate for misalignment. During operation the coupling is backlash free, and the toothed profile design provides a failsafe mechanism in the event of an overload situation, protecting the drive train elements either side of the coupling from damage. These key characteristics and attributes are the same as they were on day one when the product was first introduced and have stood the test of time extremely well.
Each of the more than 1 Million couplings installed in the field have been designed using a range of torsional vibration calculations. For Generator Set applications Reich perform a free of charge 2 mass Torsional Vibration Calculation based on the specific engine mass elastic data and the inertia of the alternator to ensure optimum performance. The product selection is then verified by taking into account the individual customer application criteria such as loads, frequencies, temperatures and other environmental considerations. Arcusaflex couplings have to date clocked up over 20 Billion hours
Reich can rightly be proud of the achievements of this long-standing part of their product range, and even although some have tried and failed to replicate it in one way or another, the fact that it is still very much in demand today, speaks for itself. The Arcusaflex proves that in certain cases the established and field proven product is still very much today’s solution.
Even with such an impressive heritage the Arcusaflex coupling range, in keeping with all Reich products, is subject to ongoing product development to ensure that it stays ahead of changing demands from different industry sectors. Examples of this include the product lifecycle within hot environments, plus approvals and certifications for ATEX use within explosive environments - and several others specific to the marine and rail sectors. These enhancements have all been achieved using the original Arcusaflex coupling design concept. In addition to the comprehensive standard range of Arcusaflex couplings, Reich also offers a D2C - Design to Customer solution.
Find out more at www.reich-uk.com.
IPU Group explain how they tackled the effect of extreme weather conditions on fuel quality to ensure Data Centre resilience…
Standby power is the backbone of data centre resilience, ensuring uninterrupted operations even when the grid fails. But in extreme environments like Norway, where winter temperatures plunge well below freezing and heavy snowfall can last for months, maintaining reliable backup power is about more than just having generators in place. One of the most critical – and often underestimated – factors is fuel quality.
IPU Group’s latest project at a Norwegian data centre demanded a fuel filtration solution capable of withstanding the region’s unforgiving conditions. With 120 bespoke fuel polishers designed and manufactured in West Bromwich and delivered directly to site, IPU ensured that the standby generators had access to clean, contamination-free fuel at all times, safeguarding against the costly and potentially catastrophic consequences of generator failure.
Long-term fuel storage in extreme climates poses a significant challenge. Diesel stored in backup fuel tanks for extended periods is highly susceptible to degradation, water ingress, and microbial contamination, all of which can have serious repercussions for standby power reliability. In Norway’s frigid winters, condensation forms more readily inside fuel tanks, accelerating water accumulation. This moisture creates the perfect breeding ground for microbial growth – commonly known as diesel bug – which can lead to clogged filters, fuel line blockages, and engine failure when power is needed most.
The consequences of compromised fuel quality can be severe:
ʝ Generator failure during an outage, leading to unplanned downtime and loss of critical data centre operations.
ʝ Increased maintenance costs, as clogged filters and degraded fuel require frequent servicing and replacement.
ʝ Potential environmental hazards, such as leaks or spills caused by fuel degradation and tank corrosion.
To combat these risks, IPU Group supplied a comprehensive, highperformance fuel polishing system tailored to the data centre’s operational and environmental challenges. Each of the 120 polishers featured:
ʝ IPU’s high-efficiency Filtasorb filters, designed to remove water and particulates, ensuring fuel integrity.
ʝ Integration with the site’s Building Management System (BMS), allowing for real-time monitoring and automated alerts for any anomalies.
ʝ Weather packs, enabling operation in both extreme cold and high-temperature environments.
Additionally, IPU’s Electrical and Software Engineer visited the site to oversee installation and provide a full system configuration overview, ensuring that every element of the filtration system was seamlessly integrated into the data centre’s power infrastructure.
Delivering and installing this bespoke solution in Norway required careful logistical planning. IPU worked closely with its Norwegian distributor (who also services Denmark, Sweden, and Finland) to manage the transportation and deployment of the equipment. The polishers were delivered in double crates, optimising efficiency and cost savings while ensuring safe arrival at the remote site.
Harsh weather conditions posed additional challenges. Snowcovered roads, unpredictable storms, and limited daylight hours made site access difficult, requiring precise coordination between transport teams, installation engineers, and data centre operators. Despite these obstacles, the polishers were successfully installed and brought online, providing the data centre with a future-proof fuel filtration system capable of supporting its standby power needs for years to come.
In an industry where uptime is paramount, any compromise on fuel quality carries significant risks. A poorly maintained or inadequate fuel filtration system can result in sludge build-up, microbial contamination, and water ingress, ultimately leading to generator failure. If standby power fails in a data centre, the fallout can include:
ʝ Data loss and system corruption, jeopardising business continuity.
ʝ Reputational damage and financial penalties, as downtime can breach SLAs and contractual obligations.
ʝ Severe operational disruption, especially for industries reliant on real-time data processing.
By investing in advanced fuel filtration technology, data centre operators can significantly de-risk their standby power infrastructure and protect against these costly failures.
The global surge in data centre construction has seen growing demand for large-scale fuel polishing solutions, and IPU Group is at the forefront of delivering cutting-edge systems to meet this need. The company is currently preparing two additional fuel polishers for another data centre, each capable of handling over 1 million litres of fuel per unit. As data centres continue to scale up their operations, ensuring that standby generators receive clean, high-quality fuel will remain a critical priority.
With data centre inquiries pouring in from every corner of the globe, it’s clear that operators are recognising the vital role of robust fuel management in standby power reliability. IPU Group’s expertise in delivering bespoke, climate-adapted fuel polishing systems is helping data centres worldwide mitigate risks, reduce maintenance costs, and ensure uninterrupted operations.
By combining precision engineering, expert logistical planning, and proven filtration technology, IPU Group is ensuring that standby power infrastructure remains resilient – even in the most extreme environments
Bernard Gospel
Technical Committee
Secretary TechSec@AMPS.org.uk
This
is a series of articles on the topic of the history of engineering from AMPS ’ Technical Secretary Bernard Gospel . The articles are loosely based on the BBC radio programmes and podcasts ‘A History of The World In 100 objects’ and ‘50 Things That Made the Modern Economy’.
Following Marcus’ sudden transfer from Rome to Naples and introduction to the curator and a review of the Naples aqueduct Aqua Augusta, Marcus awoke early in his lodgings. He went to the depot to talk to the workers again, had lunch in the street, then met his clerk at the office. He hired a boy from the crowd to help the clerk carry the rolls of documents and plans to the meeting.
Marcus waited outside until a slave summoned him in, the clerk following, carrying the rolls...
There was a table, with men around it, one of them was the curator. Marcus stood at the end of the table and announced himself formally “Marcus Drusus Sulla, Aquarius of
the Aqua Augusta, appointed under decree of the Curator Aquarum, Silvanus Staberius Flavinus in Rome.”
There was a silence as this was digested. The Napoli curator spoke first. “Titus Quintus Severus, Curator Aquarum Napoli.” The others gave their names and titles adding their status, Councillor, except for the last an elderly corpulent man sat away from the others, who gave one name “Pliny”.
Marcus glanced at him, Pliny, head of the Roman Navy based at Misenum, this was important, as a direct appointee by the emperor he could outvote the others, despite their status as councillors. Marcus realised why his predecessor might have been
banished to Syria, had he discomforted Pliny?
The curator addressed Marcus. “Did you study the documents in your office?” he asked, “and have you satisfied yourself with the construction of the aqueduct?”
Marcus paused, he knew the curator would not be an engineer, his duty was financial, to collect dues for supply of water, pay for the maintenance and on behalf of the emperor agree for new supply points. The final one being potentially lucrative for both emperor and curator. He replied with care:
“I have studied the plans of the system as constructed, they follow the principles established and followed in Rome. The maintenance records appear to be complete and up to date. I have inspected the maintenance staff in the Naples office, and they appear as competent as the staff under me in Rome.” He paused, then continued, “I have not yet had the opportunity to examine the whole ninety miles of the system, most of which will be buried underground and not visible.”
“You are here, Aquarius, because there have been, suggestions…. Rumours of unofficial abstraction of water from the aqueduct, could this be possible?” asked the curator. Marcus noticed that some of the councillors gave an expression of unease. Pliny remained still.
‘So that was it,’ thought Marcus, ‘the water belonged to the emperor until passed to a certified recipient, stealing from the emperor was …. unwise to say the least. If his predecessor had been involved in this, then banishment to Syria might have been better than the emperor’s wrath.’ “It is always possible,” replied Marcus firmly, “with ninety miles of aqueduct, most in the country, then it would not be easy to add another abstraction but once done it might not be detected for many years.”
Pliny took notice, “But it would eventually be detected? Is that what you are saying?” he asked.
“Yes,” replied Marcus, “We have to maintain the aqueduct section by section, there are schedules in the records.” Pliny was more practical than the others. “What do you mean by maintain?” he asked, “there are many items to maintain on a ship, some are cleaned and painted, like the ship’s structure, others like the blocks used to pull ropes have to be lubricated with tallow.”
“Apart from dealing with settlement and cracks in the structure,” Marcus replied, “there are two main areas, we have Castella, tanks, at the spring where sand and small pebbles can fall out. These have to be emptied at regular intervals. We usually have two Castella side by side, so that one can be cleaned whilst the other is used for the supply.” He looked at Pliny who nodded, understanding. The rest of the table were baffled, they were politicians, not engineers. “Also, we have to clean the walls of the aqueduct of travertine deposits.” Marcus continued.
Pliny interrupted. “Deposits? What of? You have castella to allow dirt to fall out of the water, then deposits mysteriously appear? Why it’s nearly Neptunalia, shall we sacrifice a bull to keep our aqueduct clear?” he laughed, the others joined in. Marcus was an engineer and took little note of deities himself, but knew others had belief in these things, and best be sympathetic to their supporters. Neptune was the god of water and was obviously the favourite of the head of the Roman navy!
“It is little understood,” Marcus replied, “water in this part of Italy has something in it which partly comes out with boiling and partly by time. Cooking pots used for boiling water can have a white deposit after a while which can be removed by energetic cleaning, even without this, deposits can be left on the aqueduct walls which could eventually block the channel, we call it travertine, it looks and behaves like the rock the water springs from.”
“How quickly does this grow?” asked Pliny. Marcus thought, “In parts of Rome about a fingernail thickness every month.” He replied. Pliny examined a fingernail, “In two years you could have a finger’s thickness,” he ruminated. “In five years, a hand’s width, and this is on both sides and the bottom,” added Marcus, “but not all water springs are as bad as this. Sometimes the water changes for better or worse. So, we remove the deposits every five years for this aqueduct. Otherwise, the water flow could be reduced.” Pliny picked this comment up immediately. “How is it removed?” he asked.
“The deposit is only up to the top of the water level, the worker places a flat bladed chisel to the join, and taps it with a mallet, it breaks away cleanly. The major effort is to remove the debris through the nearest manhole. When the section has been cleared
the exposed surface is examined and any damaged areas cemented and polished.” Explained Marcus. One of the Councillors noticed that only Pliny was questioning the Aquarius and realised there was a question to ask. “Why is the aqueduct polished?” he asked. ‘Good question from a politician,’ thought Marcus.
“After the section of Aqueduct has been constructed, the interior surface, both sides and bottom are covered with a layer of Opus Caementicium, waterproof mortar, which is finished and smoothed like the plaster on these walls.” Marcus looked about him at the ornate paintings on the walls. “Experience has shown that the travertine forms a skin on a polished surface which can easily be removed, if the surface is not polished the travertine sticks to the mortar which means the mortar can break with the travertine’s removal.” “How is the surface polished?” asked another councillor.
“The slaves do it by rubbing the surface with a flat stone,” Marcus responded, “the supervisor checks the finish before they move to the next section.” Another councillor joined the discussion. “Why is the aqueduct outside the city, the one on arches, laid level, would it not be better to have it sloping” he angled his hand to show what he meant, “so the water would run free?” The man was only considering what he saw, not the whole system, Marcus realised, he turned to the clerk, who was ready with the correct roll, as he expected.
“The tops of aqueducts like you see, may be level or not, depending on what was decided at the time of construction.” Replied Marcus calmly, “but the bottom of the aqueduct slopes from the spring to each terminus at an agreed slope, as determined by the Librator following his survey. The contractor will build to these levels.” Marcus took the roll from the clerk’s outstretched hand and continued. “If the aqueduct was constructed as you suggest, with steep slopes, the water would rush to the terminus and overflow, probably bursting open the structure with the force of the water. If conversely the slope was too shallow, the water would stagnate and become poisoned and be unfit for drinking or indeed bathing.” He opened the roll and placed it in in front of Pliny, who studied it intently.
Marcus’ interrogation had not yet finished. To be continued…
For more than half a century, OEMs, EPCs, packagers and end-users have relied on Dürr Universal to engineer acoustic and emission filtration systems to meet their specific needs.
In industries such as power generation, oil and gas, industrial processing, and rail transportation, managing noise and emissions is a crucial challenge. Regulatory frameworks around the world continue to impose stricter limits on environmental impact, requiring companies to adopt increasingly sophisticated technologies to meet compliance standards. At the same time, efficiency and cost remain pressing concerns, as businesses seek solutions that not only reduce emissions and noise but also improve operational performance.
Acoustic management in industrial settings is a highly technical field, where sound attenuation must be balanced against factors such as airflow, energy efficiency, and durability. Industrial silencers, for instance, must be carefully designed to reduce noise levels while allowing engines and turbines to function optimally. Various silencer types—including absorptive, reactive, and combination designs—are used depending on the frequency and intensity of the noise being controlled. Spark arrestors, another essential component in industrial exhaust systems, serve a critical safety function by preventing the emission of flammable particles that could ignite fires in hazardous environments.
Emissions control presents an equally complex challenge. Diesel and natural gas engines, commonly used in industrial power generation, must comply with strict air quality regulations governing pollutants such as nitrogen oxides, particulate matter, and carbon monoxide.
Filtration systems, like SCR units, DPF Filters and Catalysts, play a crucial role in capturing harmful emissions before they are released into the atmosphere. Meanwhile, the integration of dampers and diverters helps optimize airflow and gas treatment processes, further enhancing efficiency and compliance.
As industrial operations become more globalized, companies must navigate the complexities of international regulatory landscapes. Acoustic and emissions control systems must be designed to meet varying standards across different regions while remaining costeffective to manufacture and transport. Engineering strategies that focus on modular and containerized designs help mitigate logistical challenges, allowing large-scale systems to be shipped efficiently while maintaining structural integrity.
For more than 50 years, Dürr Universal has been at the forefront of engineering solutions in this field, supplying OEMs, EPCs, packagers, and end-users with bespoke noise and emissions control systems. With a global presence, including the UK, USA, Australia, Mexico, India, Singapore and Norway, the company has built an international reputation for delivering high-quality solutions that align with industry regulations and operational demands. The UK office, based in Hinckley, Leicestershire, plays a vital role in project management and design, ensuring that products meet both local and international requirements.
Looking to the future, the evolution of industrial noise and emissions management will be influenced by several emerging trends. The increasing adoption of alternative fuels, such as hydrogen and biofuels, will require new approaches to exhaust system design. Advances in materials science may lead to the development of lighter, more efficient silencing and filtration components, improving both performance and sustainability. At the same time, regulatory bodies are expected to introduce even stricter environmental limits, necessitating continued innovation in noise and emissions mitigation technologies.
In this evolving landscape, the challenge for industry is not only to comply with regulations but to do so in a way that enhances efficiency, reduces costs, and minimizes environmental impact. Dürr Universal will continue to play a critical role in shaping the future of acoustic and emissions control, ensuring that industrial operations remain both sustainable and economically viable.
ʝ Dürr traces its history back to 1959 – with the founding of Universal Silencer.
ʝ Our head office today is in Stoughton, Massachusetts.
ʝ Our company manufactures in the UK, USA, Mexico & India.
ʝ Our UK-based distribution facility of 1,700 sq. ft. serves the European market.
ʝ The company serves over 25 export markets.
+44 1455 894488
It has been a busy start to 2025 for Agriemach's emissions team with their NOxMASTER™ SCR systems being installed and commissioned across various UK data centre sites - along with more bespoke systems being designed for delivery over the coming months.
AMPS member Agriemach Ltd specialises in supplying a bespoke service for the design, manufacture, installation, project management and ongoing service of Selective Catalytic Reduction Technology. The company offers a wealth of experience and a global knowledge base, providing full system design, dosing system upgrades, catalyst replacement and the supply of all ancillary equipment required from bulk urea tanks to heat and sound insulation materials. Agriemach's technical team has experience dealing with many different fuel types and the issues associated with them - from natural gas to biofuels - and is able to provide a solution for the most challenging applications. The company also offers a full 3D CAD drawing service along with Computational Fluid Dynamics (CFD) to ensure its solutions meet client requirements.
Agriemach's NOxMASTER™ technology is considered second-tonone in terms of efficiency and reliability. The need for reducing exhaust gas emissions in line with environmental permit conditions is an ongoing requirement in the power generation sector. Agriemach, having been in the market since 1976 (that’s right, we have a 50th party due next year) has the longest UK reference list for bespoke design solutions in exhaust gas aftertreatment.
Nitrogen Oxides are a hazard to human health. Scientific evidence links NO2 (Nitrogen Dioxide) exposure, ranging from 30 minutes to 24 hours, with adverse respiratory effects including airway inflammation in healthy people – to increased respiratory symptoms in people with asthma. Ozone or smog is formed when NOx and Volatile Organic Compounds (VOCs) react in the presence of heat and sunlight. These particles affect anyone that comes into contact with them – they get deep into the respiratory system and alter lung tissue; causing a long term effect on human health. Most susceptible to these are children, the elderly and people with existing lung disease. This is the motivation for legislators to lower the limits.
Agriemach is acknowledged for their expertise in Selective Catalytic Reduction Technology. This is a means of converting Nitrogen Oxides (NOx) into Nitrogen and Water, using an Atomised Injection of urea with the aid of a Catalyst. The reduction is called “Selective” as it is only targeting the NOx emissions using the reagent and Catalyst. Agriemach's technology takes the Raw NOx emissions and reduces it down to the Target Value (ELV – Emissions Limit Value). For example, Raw NOx of 4355mg reduced to 84mg during a recent commissioning is a 98% reduction.
This is achieved through:
1. Controlled Atomising Injection of Urea - Dosing
2. Efficient Mixing in the Exhaust Stream – Static Mixers
3. Vanadium Coated Catalyst Surface - Reactor
A PLC (Control Panel) monitors and controls the entire system:
ʝ Engine Running
ʝ Engine Load levels
ʝ Raw NOx Level
ʝ Treated NOx Level
ʝ Exhaust Gas Temperature
ʝ Exhaust Backpressure
ʝ AdBlue Level
ʝ Dosing Pump/s
Most emissions targets are challenging – some more challenging than others - but all are achievable.
The Agriemach emissions team likes a challenge and with certain applications having a 98% NOx reduction & 60dB(A)@1m silencing requirement along with very little space, we work with our clients to design suitable solutions and overcome these site challenges. We also provide a countrywide support service where an Agriemach Engineer can be onsite the very same day in some cases, if the need should arise. Coupled with our AdBlue tank telemetry and AdBlue delivery service, this also means that the team will ensure that systems are healthy and tanks are topped up.
Agriemach has been a specialist in the emissions field since 1990. It is important that when new legislation is introduced, that operators who do not necessarily understand SCR technology, do not get misled and find themselves falling into a money pit of extras after the project has started. We offer complete solutions, services and aftersales support. We are always here to advise our customers and ensure that the information being provided to them is accurate –this is why we offer our live site visits and presentations, in order to make our customers feel completely comfortable with what they have been asked for in emissions compliance. We have example installations across the UK and Europe and have our engineering department at the disposal of clients to offer them the best design for their application. Agriemach has chemical engineers on hand to recalculate the confusing NOx limits that we see time and time again, all with different oxygen and flow reference. Finally, we have our site service engineers available to assist you if you ever have a question or concern.
www.agriemach.com
Agriemach offers a fully comprehensive service for the design, manufacture, installation, commissioning, project management and ongoing service/support of selective catalytic reduction systems and can provide the following:
ʝ NOx Reduction to as much as 99%
ʝ Options for reciprocating engines, gas turbines & boilers
ʝ Fuel Types
ʝ Natural Gas
ʝ Bio-Gas – Landfill, Waste Water, Digester (May require pre-cleaning)
ʝ Diesel
ʝ Bio-Diesel
ʝ HFO – Heavy Fuel Oil
ʝ Combined Silencer/SCR Assemblies
ʝ Oxidation Catalysts
ʝ Soot Filters
ʝ Bespoke Heat & Acoustic Insulation – Application Specific
ʝ Bulk Urea Tanks
ʝ Remote Monitoring
ʝ Installation and Commissioning
ʝ Service Contracts
ʝ UK Training and Support
In this opinion piece Teksan’s Liam Round looks at the development of the data centre market – and gives his views on
other trends that will influence the future of genset sales.
This issue of AMPS Power is themed around the data centre market. I firmly believe that this is a market which will further develop to provide a golden opportunity for previously non-preferred suppliers, such as Teksan, to really make an impact. The market has been well supported for over 20 years by what we could call the “power five” big suppliers which have dominated around 80% of the market and I think this status quo will decrease given long term agreements and supply chain challenges. Going forward I think things are going to change significantly over the next 5 to 10 years. There will be two drivers behind this, with engineering flexibility being one – the ability to offer bespoke options to customers. Client requirements are becoming more sophisticated which opens the door for supplier collaboration in offering packages which go beyond a power generator to include fire suppression
systems, secure card entry systems and more. The designation of data centres as critical national infrastructure aligns with this approach where the whole security piece becomes even more important. It’s all about being a solutions provider, which I believe we do well at Teksan.
I think we are all familiar with ISO 85281:2018 (which deals with application, ratings and performance of RIC generating sets). It remains a very good base document as guidance for designers and manufacturers. However, technology and client requirements move on. For example, a Tier 4 data centre, designed for complete fault tolerance, is expected to have an uptime of 99.995%, meaning a maximum of 26.3 minutes of downtime per year. In response to this tough requirement, specifiers and suppliers are oversizing generators by not just 30% but up to 40% of a generator’s capability.
I think the key consideration here is although these products are robust, issues such as wet stacking really come to the fore regardless of running hours or time on load. DCs have learnt from this and are actively hiring generator SME’s and going against Uptime Institute advice by downsizing and getting better equipped in the controls segment to manage these multi-MW campuses and the generators that back them up.
Any review of demand in our sector will pick up on power sources and the possible competition for diesel. For some years politicians have latched on to electric as the power source of the future, heavily influenced by how they envisaged the
evolution of motor vehicles. Yet we can see today that the EV revolution is stuttering. For example, it has been recently announced that an Audi factory in Brussels billed as the 'cradle' of the German carmaker's electric drive will shut production for good with the loss of 3,000 jobs. In the UK EV sales remain behind government targets. Do I believe in battery technology? Yes, I do. Do I think the technology will be mature enough to dominate all applications within the next 20 years? No, I don’t.
There are similar arguments around the use of hydrogen as a pure fuel source for generators – which I believe is not going to happen. There are well known storage and transportation issues. In my understanding it is also almost a “disease gas” in an industrial sense as it can eat its way through anything. So consider the condition of the engine itself and the consequence of the creation of leaks. Clearly not good for generator lifecycles given a typical diesel, or even gas, engine can last in excess of 30 years with good periodical maintenance. There is also no hiding from the fact that hydrogen is an explosive gas, and I know that key global business centres veto its use for this reason. Let’s also not detract from the cost vs diesel at 100kVa let alone 3Mva.
I think fuel cells can be an interesting technology but again they’re not ready to offer to the scale of data centre developments today with 50MW campuses being mooted almost every week in many different places around the world. There is, of course, an opportunity for gas, mostly on the gas turbine side but that comes with a huge cost challenge and step load issues on gas generators has been why
the industry remains cautious when you consider the opening point on uptime. HVO has great possibilities and it should be considered in terms of complementing the overall solution with Diesel Particulate Filters (DPFs) and Selective Catalytic Reduction (SCR). Combining both could, at an estimate, reduce emissions by upwards of 30% whilst only derating the generator by around 12% from its published power output. This is an area which Teksan is becoming more involved in and surely sacrificing load acceptance for improved emissions is far more beneficial long term with a time proven technology.
My company brief includes African markets – Teksan has been operating there since our inception some 30 years ago. What has changed over that time is a real uptick in engineering standards. It is no longer a continent just happy to take second hand or older technology equipment. There is far more activity there from US and European consultants and EPC’s who are helping to drive up standards. I was out in Kenya last
autumn and I was impressed at the huge growth and investment in data centres there and the recognition of critical national infrastructure priorities. At Teksan we are very proud to be at the forefront of these opportunities and continue to partner across the continent.
To summarise. For me, to be a success in data centres is about the two key words “solutions” and “collaboration”. To be a solution provider to the data centre market you have to demonstrate the ability and the capability to collaborate across supply chains. It is up to us as manufacturers to work with industry partners, peers and friends to do this. There is plenty for everyone to go for and the industry is only now ramping up. The industry doesn’t need races to the bottom it needs robust, resilient and reliable partners to ensure maximum uptime and future proof solutions. Teksan are committed to being a part of it.
For more about Teksan: www.teksan.com
Liam P. Round is the Regional Director for Europe & Africa at Teksan Global and MD of Teksan UK. He is responsible for the operations for the region as well as the development and growth of the power sector including critical infrastructure, hybrid readiness, renewable power solutions (TESS) and advisory services. Liam has more than 24 years of experience in power generation and has worked in the Middle East, the Americas and Europe. Prior to joining Teksan, Liam worked for companies including DEIF, Caterpillar, Sulzer, and MAN on some of the world’s biggest and most challenging projects in military, airport, hospital, and data centre applications.
CHAIR
LOUISE HAZEL
IPU GROUP
COUNCIL MEMBER
PAUL AITKEN GET POWER SOLUTIONS
COUNCIL MEMBER ANDREW BELL
MECC ALTE UK
COUNCIL MEMBER CHRIS CALDWELL CRESTCHIC
COUNCIL MEMBER
PAUL CAMPBELL INDUSTRIAL POWER SYSTEMS LTD
COUNCIL MEMBER
RICHARD A COLLMAN
ACOUSTICAL CONTROL ENGINEERS
COUNCIL MEMBER KÖKEN GUNES
AKSA POWER GENERATION
COUNCIL MEMBER
GEOFF HALLIDAY WBPS LTD
COUNCIL MEMBER
GAVIN HEPBURN DALE POWER SOLUTIONS
COUNCIL MEMBER
RICHARD RUSSETT REHLKO POWER SOLUTIONS EMEA
COUNCIL MEMBER
RICCARDO SARDELLI VOLVO GROUP
COUNCIL MEMBER NEIL SMITH
CATERPILLAR RETAIL ELECTRIC POWER SOLUTIONS
COUNCIL MEMBER CARLOS VICENTE EMINOX LTD
COUNCIL MEMBER LISA WILSHAW GREENSHIELDS JCB To
TECHNICAL COMMITTEE: CHRIS MARSLAND (CHAIRMAN) BERNARD GOSPEL (SECRETARY)
MARKETING COMMITTEE: RICCARDO SARDELLI (CHAIRMAN)
FINANCE COMMITTEE: RICHARD A COLLMAN (CHAIRMAN)
SECRETARIAT LEAD: JOANNA OLIVER MBE
BAUMA – 7-13 April: Munich, Germany
Middle East Energy – 7-9 April: Dubai
AMPS AGM, CONFERENCE & LUNCH
– 30 April: One Great George Street, London
AMPS GOLF DAY – 2 June: Forest Pines (Brigg)
International Power & Generating Sets Expo – 11-13 June: Shanghai, China
Executive Hire Show – 11-12 February: CBS Arena, Coventry.
DATA CENTRE WORLD – 4-5 March: ExCel, London
DISTRIBUTED ENERGY SHOW – 11-12 March: NEC, Birmingham
PLANTWORX – 23-25 September: Newark (UK)
SOLAR & STORAGE – 24-26 September: NEC, Birmingham
Healthcare Estates (IHEEM) – 21-22 October: Manchester
The Showman’s Show – 22-23 October: Newbury
AMPS AWARDS FOR EXCELLENCE GALA DINNER – 19 November: The Lowry Hotel, Salford
To be confirmed: October – AMPS INDUSTRY DAY
Key: AMPS events highlighted in RED. Events with an AMPS’ presence are shown in BOLD CAPITALS
The organisers of this year’s PlantWorx exhibition have partnered with AMPS to offer an exclusive opportunity for its members. Taking place at Newark Showground from 23rd to 25th September, the event will host a meeting of the AMPS Council, and AMPS members will benefit from a 10% discount on exhibition stand bookings.
PlantWorx will showcase a diverse range of leading manufacturers and distributors of construction and site equipment, with a strong emphasis on technological advancements and product innovation. Marketing Lead for PlantWorx, Anna Jackson, highlighted the significance of this year’s event:
“This is the first time PlantWorx will be held in the autumn, and the timing could not be more strategic. It allows UK visitors an early opportunity to experience new equipment following its international debut at Bauma in Germany earlier in the year. Additionally, as government plans for infrastructure investment and planning reform take shape, industry forecasts predict a notable increase in project
starts and construction output by 2026. Contractors, specifiers, and plant hire companies must ensure they have the right equipment in place to meet this growing demand.”
With visitor registration now open, PlantWorx has kicked off its 2025 campaign with a powerful webinar series. Each session features industry leaders tackling key construction challenges and uncovering opportunities for 2026 and beyond.
The latest session on plant hire procurement strategies attracted 500 construction professionals. For further details and to register, visit www.plantworx.co.uk.