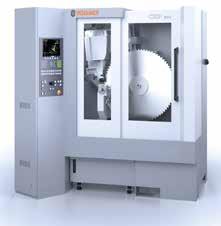
6 minute read
Carving out a path for India’s economic boom
from AMT AUG/SEPT 2020
by AMTIL
Carving out a path for India’s economic boom India’s economy has grown rapidly since the launch of the ‘Make in India’ economic initiative in 2014. One of the key manufacturers taking part in the initiative is Basco Tool Industries, based in Faridabad, south of New Delhi.
The company manufactures carbidetipped circular saw blades and has relied on sharpening technology from Vollmer for more than 15 years. The specialist in grinding and erosion machines has previously supplied seven machines, including sharpening machines from the CP and CHP model series. “We are currently manufacturing around 3000 carbide-tipped circular saw blades a month for companies in the wood and metal industry,” says Vikas Tiwari, CEO of Basco Tool Industries. “Our vision is to not only increase the quality of products and services, but also achieve further growth. Specifically, we want to produce at least 10,000 saw blades per month within a few years.” Basco Tool Industries’ ambitious goals reflect how the Indian economy looks. For two decades, the country’s gross domestic product (GDP) has grown by more than 7% a year. Six years ago, the ‘Make in India’ initiative was established in the country, with the goal to support Indian manufacturers to produce goods in their own nation. Employing around 20 people, Basco Tool Industries develops over 25 variants of carbide-tipped circular saw blades for Indian manufacturers, which they then use to process plywood, solid wood, wood composites, plastics and aluminium. Economic life is booming in the neighbourhood around Basco Tool Industries, with small workshops, mediumsized factories and large manufacturing companies all witnessing prolonged growth. Many global companies have regional subsidiaries in Faridabad, including German companies such as the agricultural machinery manufacturer
Basco Tool Industries manufactures its carbidetipped circular saw blades with machines such as the VOLLMER CHP 840 sharpening machine in a fully automated, around-the-clock process. Employing around 20 people, the Indian company Basco Tool Industries produces its carbide-tipped circular saw blades using seven VOLLMER sharpening machines.
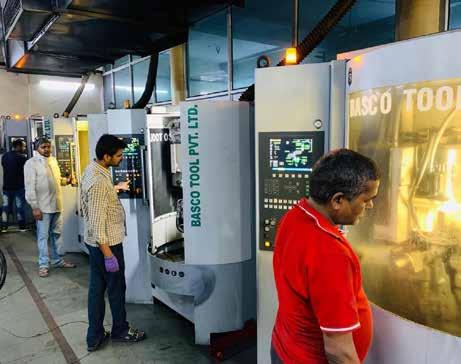
Claas and technology firm Voith. German workmanship also plays a key role at Basco Tool Industries, since the company relies on machines from Vollmer to sharpen its carbide-tipped circular saw blades. “The connections between Faridabad and Germany have been successful and strong for decades,” says Tiwari. “For that reason, it was clear to us from the start that we, too, could rely on German quality for our machines. Our first Vollmer sharpening machine arrived from Biberach (where Vollmer is headquartered) back in 2003. Now there are seven machines that we use to manufacture circular saws and tools around the clock.” Growth with Vollmer sharpening technology Vollmer has sent a range of equipment on the 6,000km journey to Faridabad, including one CHP 840 and two CP 200 sharpening machines. With the CHP 840, carbide-tipped circular saws can be sharpened in a single set-up. Its four CNCcontrolled axes allow complete machining of all common tooth geometries in just one cycle – even when sawing with an axial angle and group toothing. The CP 200 machine is equipped with multi-processor technology and integrated software programs. Consequently, whether its tooth faces or tooth tops, the grinding speed can be freely selected and there’s no need to set tooth pitch or blade thickness. In addition to the sharpening machines, the service technicians at Basco Tool Industries have also received training at Vollmer’s site in Biberach. The customers of Basco Tool Industries are primarily based in the north and east of India. Apart from circular saws and tools, the company also offers a range of services including tool resharpening, tool repairs and technical consultation. The customers from the wood and metal industries are supported with training to help them design efficient and profitable production processes for furniture, window and door technologies from Basco Tool Industries. The aim is to establish additional regional distribution and service centres and ultimately become the leading manufacturer of carbide-tipped circular saws in India. “Basco Tool Industries is a typical example of the customers we have in India; small, agile and innovative,” remarks Dr Stefan Brand, CEO of the Vollmer Group. “In order to fully cater to the needs of Indian companies, we have maintained a presence in the region for many years already; we also founded our own subsidiary in Bangalore in 2013. We are pressing ahead with our internationalisation plans so that we can also support Indian manufacturers in achieving national and global growth over the long term.”
www.vollmer-group.com www.bascotool.in www.camcointl.com
Opening up a clean, green era in the metal tool industry
EcoCooling is a ground-breaking innovation in which ionized air is used to cool and lubricate workpieces and cutting tools, replacing the need for expensive metalworking fluids. The product has the potential to transform the metalworking, machine tool, and metal component manufacturing industries.
EcoCooling is the result of long-term, interdisciplinary R&D from the same team that developed the technology behind Amazon’s ground-breaking family of front-lit Kindle devices. Now the group of scientists, engineers and experienced businesspeople from various disciplines has developed a dry, clean and environmentally friendly method to lubricate metal workpieces with ionised and cooled air, without using any emulsions. “Workshops have wanted to get rid of fluids and many have tried to find a solution to the problem, but with poor results”, says Leo Hatjasalo, co-founder and CEO of EcoCooling. “Now we have the answer to this demand, since EcoCooling can be used even with the hardest known metals like chrome, titanium and tungsten carbides.” The global market value for metalworking fluids is estimated at approximately US$12bn this year. It is growing steadily, with estimates for the global market value for machine tools expected to grow from US$120bn to US$150bn in five years’ time. The growth is driven, for example by the accelerating need for components in the aerospace, automotive and transport sectors. “EcoCooling is based on the fact that ionised air penetrates the cutting zone and forms a dry lubricant that decreases cutting friction and generated heat, at the same time speeding up the oxide layer formation,” Hatjasalo explains. “The process is patented on all continents, and at the moment we are validating it to include all types of machine tools.” Hatjasalo emphasises that EcoCooling is not only a way to cut down the costs of emulsions, but also a way to improve productivity through higher cutting speed, reduced wear of cutting tools and minimised maintenance costs. “Since the metal chips are not contaminated by any fluids, they can also be fully recycled without cleaning,” he says. “Another big advantage is that it eliminates toxic fluid waste and fumes, in addition to minimising CO2 emissions, since no oil is used.” The technology makes it possible to build smaller and cheaper metalworking machines, since the EcoCooling unit is very compact in size. “The unit does not need any service and it has proved to prolong the lifetime of the cutting tools significantly,” Hatjasalo says. “The system can also be easily retrofitted to older machine tools.” During the past few years, EcoCooling has been successfully trialled in numerous commercial tests in demanding surroundings internationally. Now that the process has proved to give excellent results, big savings and substantially less environmental impact, the aim is to create a versatile EcoCooling product family that includes all machine tools in addition to just turning machines. “We are also planning to integrate the system to suit different CNC machine tools and to create optimal solutions for all machine tools and workshop environments,” Hatjasalo says. “However, for that purpose we need more funding than we can raise on our own. Therefore, the next step is to find an industrial partner to help us to commercialise EcoCooling globally and to develop the ways the technology can be used.” www.ecocooling.fi
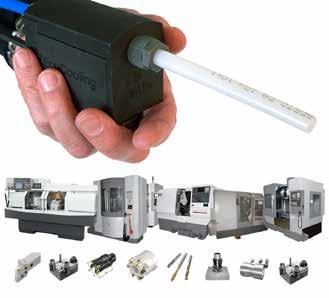
Compact and maintenance-free, the EcoCooling unit facilitates smaller, cheaper metalworking machines.
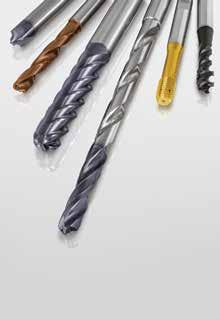
SUPPORTING AUSTRALIAN MANUFACTURERS
• High Performance Solutions • Made & Stocked Right Here • Custom Made Specials Available • Regrinding & Coating • Heat Treatment & Nitriding

Contact us for more information digital@sutton.com.au www.suttontools.com