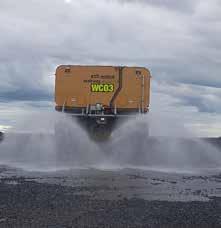
7 minute read
ADE & Austin deliver revolutionary truck tech to NT mine
from AMT AUG/SEPT 2020
by AMTIL
ADE and Austin deliver revolutionary truck technology to NT mine
One of the world’s largest mines, based in the Northern Territory, has introduced revolutionary water spray application technology to improve dust control and enhance mining operation safety; and the benefits are expected to be both swift and significant.
McArthur River Mine, which excavates zinc, lead and silver, required two new water trucks to be added to its operations but, being mindful of improving dust control and ensuring better safety for its workers, decided to have trucks specifically designed that would address these issues. The result was the coming together of local Australian companies – Australian Diversified Engineering and Austin Engineering – that produced two uniquely designed CAT 789 water trucks for the mine patented as “Stairway Access Tank”, with a capacity of 159,000 litres. The exclusive design has produced what is now known as the safest water tank in the mining industry, and is an engineering collaboration of which ADE General Manager Clive Gray says has set the bar for water truck technology to new heights. “Controlling airborne dust on mine sites is incredibly important,” Gray explained. “It minimises the risks to workers, but knowing just how much water to spray has its own challenges and can also become a hazard, leading to unplanned vehicle movement and even worse, closing a haul road for many hours. “We have been manufacturing safety equipment for the mining industry for many years but being able to work together with Austin Engineering has allowed us to deliver an exceptional solution for the McArthur River Mine. We feel confident that they will see positive outcomes in terms of improved safety and better dust control very quickly, making this a great investment.” ADE is world-renowned for its development of the ADE Spray System; a water truck spray control system that can consistently spray a controlled rate of water onto the ground, regardless of speed, to effectively control airborne dust. Road friction measurements can be used to determine the maximum safe water coverage rate which in turn reduces waste and decreases the risk of an unplanned movement. During operations, the system data logs all spray activities which can be used to generate reports and assess operations. Gray says it is this ability to both measure and monitor that makes the ADE Spray System such a game changer: “One of the biggest issues for mine sites is knowing how much water to spray on the road. Too much or too little have equal repercussions,
with safety issues being the greatest concern. Mining operators can quickly and easily monitor and track all aspects of their water truck operations using our on-board data logging system which effectively cuts costs and improves environmental factors in regards to monitoring water usage. “By eliminating over and under-watering, costs, fuel and water usage are naturally reduced, but it is the safety of the mining workers that is at the forefront of our designs. By developing and implementing innovative technologies into mines around Australia we limit the risks involved to mining workers and that is something we are very proud of.” The custom-designed trucks began their journey in Wyoming, USA, where they were initially designed, before then being manufactured in Batam, Indonesia, and finally making their way to Australia where ADE engineers installed their latest safety technology. All ADE products are both designed and manufactured in Australia. The trucks were then delivered to the mine site where ADE engineers arrived to ensure all components were running like clockwork before the trucks started their first day of action. “A haul road can be closed for several hours in the event of an unplanned movement with a mobile operations vehicle, costing both time and money as production is indefinitely halted,” explained Gray. “Our systems are designed to help sites save time, money and improve safety so we will always go above and beyond to ensure a positive experience for all concerned.”
www.austineng.com.au www.ade.net.au
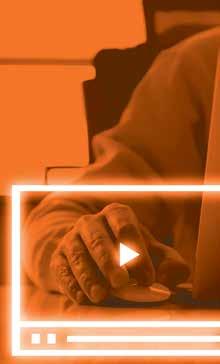
AMTIL PRODUCT E-BLASTS
IT’S ALL IN THE NUMBERS 9OOO TARGETED CONTACTS 18.86% OPEN RATES 12.26% CLICK THRUS STATISTICAL REPORTING
Call Anne Samuelsson to learn more on 0400 115 525 or email asamuelsson@amtil.com.au for all enquiries.
1510AMTIL
Experience and passion the hallmarks of new WA engineering business Experienced machinist Joe Latham has established his new engineering business ProWest Engineering in Western Australia, driven by a passion to succeed in a climate of change in the manufacturing industry.
With more than 19 years’ experience in the industry, this awardwinning engineer with trophies for Top World Skills Machinist for Western Australia and a top ten World Skills entrant for Australia, has a business theme of ‘If you can dream it, we can machine it’. When establishing a new green-field site with a pristine engineering workshop, Latham’s first purchase has been a brand new Okuma Model Genos L3000e-MY x 1000 CNC lathe. “Over the years I have worked on a wide range of CNC machines and I love the Okuma machines for the easy interface and the outstanding finish they achieve,” says Latham. “The back-up service that Okuma provides is also outstanding from people who really care. This machine is a very big investment for us; however the new plant layout is planned for additional machines and I already know the next Okuma machine model I want.” In following his dream, Latham has held a passion to start his own engineering business for some time, but the loss of a close family member was the catalyst for moving his plans forward to the start of 2020. While just an ‘Army of Two’ team with his wife Jasmine at start-up, Latham is keen to take on an apprentice as soon as possible and to grow the business. As ProWest kicks off, Latham is confident that business from clients in the broad market segments of mining, automotive, energy, marine and general engineering will grow rapidly, amid renewed confidence and support for manufacturing in Australia and concerns regarding an over-reliance on offshore manufacturing. John Dale, Branch Manager – Western Australia for Okuma, commented: “Joe is supported by Okuma’s 12 months bottomless training support from our Western Australian team, along with access to our network of service and applications engineers Australia-wide”. by the Australian Defence Force. WarpSPEE3D is the world’s first large-format metal 3D printer to use patented cold spray technology that enables significantly faster and more cost-effective metal part production than traditional manufacturing. Developed by Australian manufacturer SPEE3D, the printer is capable of printing large metal parts up to 40kg at a recordbreaking speed of 100 grams per minute. The printer arrived in Darwin in early June. Little over a week after being installed at Robertson Barracks, soldiers from the 1st Combat Service Support Battalion (1 CSSB) trucked the printer out to the bush for a three-day trial at the Mount Bundey field training area, 120km south-east of Darwin. The WarpSPEE3D was manoeuvred to various locations and different terrains. It was unloaded ready to print within 30 minutes, producing a variety of parts. SPEE3D printers make metal parts the fastest way possible, leveraging metal cold spray technology to produce industrial-quality metal parts in minutes, rather than days or weeks. The process harnesses the power of kinetic energy, rather than high-power lasers and expensive gasses, allowing 3D metal printing in the field at affordable costs.
ProWest’s Joe Latham and the new Okuma machine.

Latham’s impressive engineering background and the pristine presentation of his workshop and machining centre cannot help but impress, and is sure to draw new and existing clients to this exciting engineering operation. “At Okuma we are excited to be part of a new enterprise such as ProWest Engineering and to support its growth with the latest technology and machines,” said Okuma Australia Managing Director Dean McCarroll. “ProWest and all our customers can be assured of our on-going support.”
www.okumaaustralia.com.au
Australian Army put pedal to metal with SPEE3D field trial
In a world-first, a WarpSPEE3D metal 3D printer was put through its paces by the Australian Army during a field exercise in the Northern Territory in June, demonstrating the potential for this technology to be deployed to the field
www.facebook.com/ProWestEngineering
The Army announced a $1.5m investment in a pilot of SPEE3D technology in February, with a 12-month trial designed to test the feasibility of deploying 3D metal printers on base and in the field. The program aims to increase the availability of unique parts to the Army. SPEE3D CEO Byron Kennedy said: “The first field deployment of WarpSPEE3D was an important milestone for SPEE3D. While initially designed for industrial use, this trial proved our equipment is actually very robust and can endure harsh conditions and rough handling very well. We look forward to future exercises and continuing to learn how we best serve the Australian Army and defence industry.” 1 CSSB Commanding Officer, Lieutenant Colonel Kane Wright, added: “This phase has seen the 3D printing capability deployed to the field, alongside vital military equipment, contributing to the mission during this training cycle. The ability to print repair parts in an environment like this has the potential to significantly reduce our footprint and repair damaged equipment – on the spot – to get us back to our main priority.” www.spee3d.com