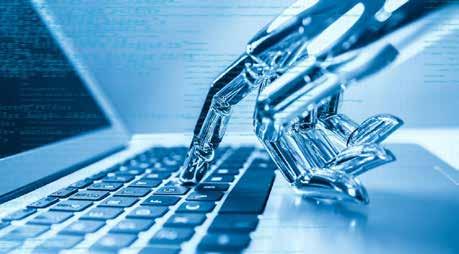
7 minute read
Manufacturing under COVID-19: Overcoming challenges
from AMT AUG/SEPT 2020
by AMTIL
Manufacturing under COVID-19: Overcoming challenges in a crisis The COVID-19 crisis has presented significant difficulties for the manufacturing industry. To overcome these issues, manufacturers must embrace Industry 4.0. By Eddie Stefanescu.
The challenges posed by the COVID-19 pandemic are numerous. The requirement for social distancing has led to a surge in remote working. With supply chains disrupted, the demand for some products has shrunk, making it difficult to keep up with demand. Moreover, we’ve seen many production facilities be rapidly repurposed, such as distilleries that switched to making hand sanitiser, and car manufacturers that pivoted to making ventilators. In order to rise to these challenges, manufacturers have to adopt the modern technologies of Industry 4.0, such as automation and robotics, large-scale monitoring systems that provide real-time information about production processes, and flexible systems that can be quickly adapted to produce modified or different products. A prerequisite for Industry 4.0, and for an effective response to COVID-19, is for manufacturers to have tightly integrated operational technology (OT) and information technology (IT). At a foundational level, tight OT/IT integration enables better business planning and management. It enables production systems to be more responsive to business priorities and customer requirements, and to be more effectively managed remotely. However, there are many barriers to effectively integrating OT and IT systems. First and foremost is the considerable challenge of ensuring robust and manageable security. OT networks run on proprietary protocols and typically use a lot of legacy equipment, which is incompatible with and inaccessible by the traditional IT security tools used in IT enterprise environments. As a result, IT security tools are unable to gather the necessary data from OT networks that is essential for risk calculation and mitigation. Previously, OT networks have remained largely isolated from corporate IT networks – meaning they have also been isolated from the internet and the global community of hackers and cyber-criminals that it harbours. When OT and IT networks are suddenly integrated, the whole network becomes vulnerable and exposed to these threats. As OT systems often control or monitor real-time processes, manufacturers can’t afford to have any system outages. The consequences of such an outage could
be catastrophic, such as in the case of a power plant. However, you cannot protect what you cannot see. Therefore, it is recommended that manufacturers have security tools that provide them with deep visibility into their networks, in order to identify all connected devices and network processes. How can manufacturers overcome these challenges? There is no single solution to these challenges, but an essential first step is network segmentation: by allowing only necessary connections to the network, manufacturers can reduce the risk of unsuspecting devices being used as attack routes. There have been numerous instances where vulnerable – and in some cases trivial – devices have given access to a company’s ‘crown jewels.’ Take, for example, the casino that was hacked through the smart thermometer in its lobby aquarium, giving the attackers access to its database of ‘high-roller’ customers. A comprehensive approach that addresses all the potential weaknesses in the security of integrated IT/OT networks is required to overcome these challenges and ensure robust security. In particular, there are two important considerations to ensure robust OT network security: 1. Security professionals should aim to have a complete inventory of connected assets and the communication paths between them.
Fortunately, there are numerous
OT-specific security tools readily available in the market that enable manufacturers to easily monitor all activity between their equipment. 2. It is crucial to define normal network operation – by monitoring the network and understanding how all devices interact with each other, any suspicious activities can be detected and shut down before an attack occurs. Security tools can assist manufacturers by monitoring all assets and communications on their networks, establishing a baseline of normal behaviour, and detecting any anomalies. Factoring in the world’s increasingly remote workforce – a trend which has been consolidated by COVID-19 – investing in security tools that can support secure remote access to the network is highly recommended. By tracking and auditing all remote accesses, security tools can prevent any unauthorised access from bad actors. The pandemic will eventually pass; however many of the changes it has imposed are likely to endure. The COVID-19 crisis has created a strong incentive for manufacturers to accelerate OT/IT integration and their take-up of Industry 4.0, but in order to do this as securely as possible, manufacturers need to deploy security tools that thoroughly protect their networks.
Eddie Stefanescu is Regional Vice-President, Business – Asia Pacific & Japan at Claroty. www.claroty.com
Growing the business with speed and efficiency
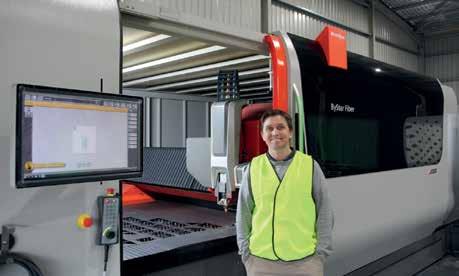
David Errington, proudly shows his new ByStar fiber 12kW
We often overlook the amount of manufacturing that occurs in regional Australia. Case in point is Apollo Engineering. Situated in Tamworth north western New South Wales the second largest inland city.
Apollo Engineering. has been in operation but with a strong relationship with another since the early 1990s and today manufactures customer, he was able to visit and see the an extensive range of parts washes for the ByStar 12 kW with automation in operation. automotive industry. Over time Apollo has diversified into manufacture of components Impressed with the machine and automation to the waste equipment manufacturing and with the federal government‘s recent industry and more recently into food waste initiatives around the purchase of capital processing equipment for the hospitality, equipment, it was all David needed to not wholesale food, and commercial food only purchase the laser machine, but also the manufacturing industry. automation for loading and unloading, which will be key for his business growth. With a team of 35 staff and in-house design capabilities coupled with the latest in The laser will be used primarily in the machining technologies that include four production of in-house parts. But word is out dual spindle CNC lathes with machine tending amongst local manufacturers that Apollo can cobots, horizontal machining centres, produce parts in a more cost-effective manner fabrication, and a sheet metal workshop, compared to overseas competitors. This also Apollo is poised for further growth. has the additional benefit of reducing the need for outlay capital for his customers. To continue to provide innovation within the
business David Errington, Apollo‘s managing ” David director has the philosophy of continued investment in the latest equipment to keep While the speed of the his business ahead of the curve. This includes machine improves our his most recent acquisition of Bystronic’s ByStar 12kW fibre laser complete with cutting times by 70%, the real ByTrans Extended Automation. advantage comes in coupling While chasing down spare parts for his that with the native BySoft 7 older model CO2 to laser, provided him with nesting software. This allows a chance meeting with another Bystronic customer. David explains “I had travelled to our total processing time Ballarat as sourcing new parts for our existing machine was becoming harder, and the company down there had the same model as our old machine which had been mothballed. We got into talking about what laser he from concept to customer to be much more efficient. Another real value with the BySoft software is ” is currently using and I was overwhelmed its ability to integrate with ERP systems which with how enthusiastically they spoke about is key for us. the Bystronic ByStar Fiber. Not only did the laser perform for them, they also heaped When asked after testing what was the thing high praise for the backup and support from that most surprised him about ByStar fiber’s Bystronic Australia. performance, the response was “The Wow factor, I still find myself looking through the Having only dealt with agents before, the idea glass into the machine and being blown away of dealing directly with the manufacturer was by the speed that it cuts.” also a really attractive proposition to me.” With the Covid restrictions in place, David Not only is the performance of the machine was unable to travel to the experience centre, quick, so was the delivery of the machine ”Everything happened quickly. Bystronic was quick to arrange the reference customer visit which helped reinforce that this is the machine we need. From there, it took only four weeks from the order placement to the machine delivery. The biggest challenge we had was preparing for the arrival of the new laser.”
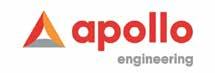
“Working with Bystronic’s technicians during the install was easy. They arrived before the containers did and within three weeks, had the machine up and running, along with our people trained in both software and the operation of the laser machine. As with any new equipment we are learning new things every day and are very comfortable with the support that Bystronic is able to provide through their hotline. We have taken advantage of it on numerous occasions as questions arise as with any new equipment when you have just started using it.
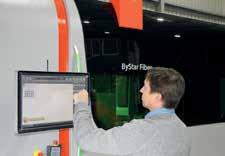
Right: Cut parts processed swiftly and efficiently Bottom: Easy operator interface with ByVison Cutting.