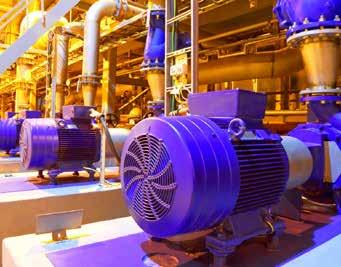
4 minute read
The old and new in motor maintenance
from AMT FEB/MAR 2022
by AMTIL
From pumps to fans, machine tools to conveyor belts, motors are the backbone of manufacturing in many sectors. However, the annual cost of running a motor can be up to 10 times the purchase price. John Young looks at four key areas where you can improve your motor maintenance.
In any industry, motors are major consumers of cost and energy. In addition to the high maintenance costs, it is estimated that more than 65% of electrical energy in industry is consumed by motors. Manufacturers of motors are working hard to produce ever more efficient motors and governments the world over are introducing regulations to encourage their uptake. Whether you are looking to lower the cost of running your facility, reduce the risk of unplanned downtime, or reduce the carbon footprint of your manufacturing operations, here are some useful factors to consider when maintaining your motor. A need for speed control
Variable speed drives (VSDs) are an increasingly popular way of allowing manufacturers to achieve cost savings and energy efficiency gains. Without a VSD, the motor will always operate at full speed but the use of a VSD will match the speed to the application. A VSD also prevents current surges and the potential damage that these can cause. Although the initial cost of a VSD might seem high, they can reduce electricity consumption by up to 55%, therefore providing a substantial return on investment in the long run. In addition to energy and cost savings, VSDs help extend the service life of your motor and reduce the maintenance costs. Perhaps you are still put off by the higher upfront cost, or maybe space requirements mean there is less room for a VSD? In this instance, a soft starter may be a good option, depending on your application. These typically cost half or a third as much as VSDs and are smaller too. As the name suggests, soft starters are limited to the start-up, where they provide a smoother acceleration, allowing the motor to start more gradually. They do this by limiting and controlling the initial inrush of current. Across-the-line starting of induction motors is accompanied by inrush currents of up to seven times higher than running current and starting torque of up to three times higher than running torque. The increased torque results in sudden mechanical stress on the machine. As with VSDs, greater control over the speed can help promote the longevity of your motor. Smarten up monitoring
An experienced plant engineer can monitor the condition of a motor to look for signs of potential problems. Temperature, vibration and noise levels are all things that can indicate both the cause and symptom of a problem. Excessive heat can be a cause of problems. In fact, the majority of the most common motor problems can be traced to overheating. One thing to bear in mind is that the life of the motor winding insulation is halved for every 10deg Celsius of additional heat to the windings. While experienced plant engineers are attuned to the signs and symptoms of potential issues, the latest connected devices can take condition monitoring to another level, reducing the risk of unplanned downtime from motor failure. This is especially beneficial in safety-related systems that are designed for 100% machine availability. Having devices that can constantly monitor key indicators can provide more timely warnings of potential problems, as well as further insights into equipment performance, complementing traditional condition monitoring. For example, the Omron K6CM motor condition monitoring device constantly monitors the condition of three-phase induction motors and detects in advance errors that might have resulted from ageing and wear. It does this by monitoring temperature, vibration, current and insulation resistance. Stay clean and warm
Many of the staples of a traditional maintenance program still hold their value, despite the added benefits of technology like smart sensors. Keeping your motors and the environment they operate in clean and dry will always play a vital role in ensuring a long service life. Dust and other particles can contaminate the motor. Abrasive particles will wear down components over time. If they are conductive, they can also interfere with the current. An obstruction in the fan, such as dirt and grime on the heatsink, can lead to overheating. In liquid-cooled motors, excessive dirt can clog piping, also leading to overheating. Motors should be kept warm as well as clean. As a motor cools, moisture can enter. Moisture and humidity can contribute to corrosion of the components. Moisture also has the potential to weaken the insulating material, so steps must be taken to reduce this risk. Find a reliable parts supplier
When things do go wrong, you need to be able to act quickly. Whether it is an obsolete component or an entire motor that needs replacing, time spent waiting for new parts to arrive is prohibitively expensive. The cost of downtime is especially high in those industries, like food & beverage, where the product risks being spoiled. In these instances, partnering with a supplier that has a track record of quickly sourcing and delivering parts is not only beneficial, but essential. If your maintenance program incorporates the tips included above, you will hopefully not be needing to order replacement parts too frequently. However, it is always best to make sure that when something needs replacing, you have the partnerships in place to resolve issues swiftly.