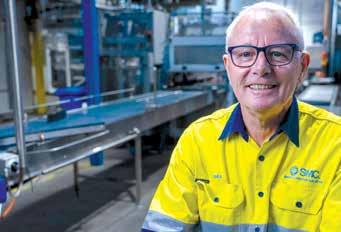
4 minute read
Insider energy saving information
from AMT FEB/MAR 2022
by AMTIL
‘Release the Pressure’ – Insider energy saving information
Pneumatic processes account for around 20% of all factory power consumption. However, when air is optimised, it becomes a gamechanger that is proven to improve energy efficiency.
In a recent white paper, SMC’s Industry Projects Manager for Energy (EU), Andy Still, shared his thoughts on how companies can optimise their energy efficiency in-line with one of the industry’s best-kept secrets. While it is possible to introduce compressed air efficiencies, today, some plants still suffer from 20 to 50% leakage rates as well as other forms of wastage. It’s common knowledge that the typical operating pressure (for main compressed air lines) in industrial plants is around 7 bar. However, not so commonly known is that by simply lowering the pressure to 5 bar, facilities can reduce their energy consumption up to 15%. Dropping the pressure to 4 bar offers savings of up to 29%. “The global understanding of pressure reduction is that it will affect performance,” Still explains. “Although this statement is true for some equipment, it must be said that most processes can operate efficiently at reduced pressures.” Bill Blyth, Energy Conservation Group Manager at SMC Corporation ANZ, echoes this sentiment saying that while performance remains critical in every plant, SMC has found an effective and reliable way to reduce pressure without compromising output: “The objective is to make sure that 1) the available power is utilised in an optimised way and 2) to smooth the demand peaks.” Identifying the issues
Globally, SMC’s energy saving team can carry out an energy saving audit designed to address these opportunities. In just a few days, without interrupting operations, an audit is carried out. “The first step is to evaluate the compressor’s operations and address the filtration components and air distribution to ensure the system will not exhibit unnecessary pressure drops and deliver efficient flow across the entire pneumatic circuit,” says Still. SMC determines the air quality by carrying out an air quality analysis. “Then, we investigate various process operations throughout the site, identify opportunities and quantify existing waste. Finally, our experts investigate any equipment exhibiting increased air demand, and identify compressed air inefficiencies and energy costs.” These initiatives determine any existing conditions as well as existing and potential minimum pressure requirements for a plant’s compressed air system. Based on the outcome of the energy saving audit, SMC provides recommendations and solutions – including estimated costs to eliminate inefficiencies and assure system reliability when reducing pressure and flowrates. “So often, companies think that the outcome of an audit will incur significant expenditure,” says Blyth. “This is not always the case. In many instances, it is possible to reduce the operating pressure, reduce the flowrates and eliminate waste without the need for any significant system upgrades.” Still adds that the order of priority must be: 1. The elimination of waste (including leaks). 2. The smoothing of flow peaks. 3. The reduction in excess pressure. 4. The realisation of improved energy efficiency at each of the components.
Bill Blyth, Energy Conservation Group Manager at SMC Corporation ANZ.
The elimination process
“Much like a car in need of a service, if a pneumatic system is not properly maintained, costly issues can arise” Blyth explains. Regarding the elimination process, Still says: “We identify waste, often simply by repairing seals or tubing for instance. However, this action only acts as a temporary improvement. Further leaks will inevitably occur, and small leaks will eventually become larger ones. There needs to be a policy in place that assures leak repair as an ongoing, continuous project. A leak detection system (as simple as an inline flow monitor) can easily identify future leakage with associated costs and wasted energy.” When looking to components that generate excessive compressed air demand, Andy says that air blow systems must be considered. “These can account for around 42% of global compressed air consumption and if not optimised can compromise the entire plant system efficiency. To help counter this issue, as an example, we can provide a solution that reduces air blow consumption up to 85%, through more efficient air control technology or investigate alternatives to replace the air blow system.” This choice involves a small investment, but the fast return is due to the typically high consumption of air blow equipment. It is also important to consider vacuum systems, which represent 9% of global consumption. Example being a vacuum unit featuring SMC’s energy-saving digital pressure switching enables plants to reduce air usage by 93%. “A next step, and not such a complicated one, will be to optimise any single machine components” says Still. “Small improvements can generate big gains.” “Consider the stroke, connections and the mounting of a cylinder. The correct sizing here is key,” adds Blyth. The installation of a digital gap checker in machining applications (for workpiece placement confirmation) can also make a notable difference as it provides a 60% reduction in air consumption. This detection principle ensures a flow rate of 0 L/min when the workpiece is seated in its fixture. The combination of reduced operating pressure and system improvements brings huge savings in energy consumption – usually around 75%.