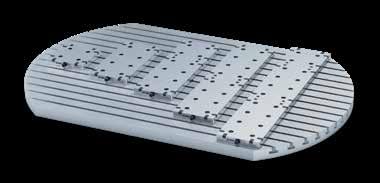
4 minute read
Lang Modular Plates: Improved ergonomics
from AMT APR/MAY 2022
by AMTIL
New Lang Modular Plates offer improved ergonomics and quicker installation
Lang Technik’s Quick-Point zero-point clamping system has established itself as the benchmark for direct clamping of workpieces and fixtures offering improved productivity and maximum flexibility.
As an interface between the machine table and clamping device, Quick-Point is characterised by an enormous range of variations and high repeatability. The system provides a solution for just about every application and can be used universally in vertical, horizontal and five-axis machining centres. Quick-Point clamping studs connect the zero-point system and Lang workholding devices. They can be also mounted directly to a workpiece in order to clamp it directly without a workholding device. With an actuation torque of 30 Nm (60 Nm for four-fold grid plates) holding forces of up to 6,000kg can be achieved. Due to a very small number of wear-free parts the system is reliable and virtually maintenance free. One of the key benefits of Lang’s QuickPoint zero-point clamping system is that it allows for a one-time installation. Once the base plate is mounted and aligned to the machine tool table and the zero point is defined, workpieces and fixtures can be built quickly and accurately. “The zero-point system provides a huge boost to productivity, reducing typical changeover times from 1-2 hours to just several minutes,” says Matthew Williams, General Manager of Dimac Tooling, Lang Technik’s agents for Australia and New Zealand. Now Lang Technik has added another dose of productivity with its latest development: Quick-Point Modular Plates. Previous plates operated on a combination of an Allen key and Hex nuts, so the operator needed different tools. The previous system also had a screw for each individual vice. The new Modular system features a single screw for the plate enabling the operator to lock down multiple vices at a time. The new system also uses just a single hex nut – further speeding up the installation process. “You no longer have to awkwardly lean over to locate the back screw or rotate the plate to clamp to reach the other side,” Williams adds. “The Modular system takes a large step forward in terms of ergonomics and speed coupled with high repeatability.” Over the years the Lang Technik has been responsible for numerous workholding innovations that reduce costly changeover time, reduce operator workload and maximise productivity. “These new products reinforce Lang Technik’s reputation as the worldwide leader in design and development of workholding solutions for almost any clamping requirement from raw material to the finished workpiece,” Williams concludes. “Because all Lang products come from the one place, they are perfectly matched and interfacing problems with other systems do not exist. The modular building system and the multitude of combinations and capabilities are the reason that their workholding systems can be used in almost any machining centre.” www.dimac.com.au
The MSP and MSPD power clamping spindles from JAKOB offer the ability to clamp the largest and heaviest workpieces with ease.
Workpieces up to approximately 50cm are usually mechanically and manually clamped with three- or four-jaw chucks, or automatically by pneumatic or hydraulic equipment. If, however, the workpieces to be machined are larger, then planar disks are used, which can also hold much larger parts safely on site with jaw boxes and tensioning spindles. As a user, you have the choice between seven standard thread sizes from TR 50 to TR 200, with which, due to the proven principle of force multiplication by means of wedge clamping systems, clamping forces of up to 500kN can be achieved. In addition, selflocking is achieved in each tensioning position as well as a high degree of stiffness. The power clamping spindles are equipped with an internal switchover to switch between external and internal clamping. The MSP / MSPD power clamping spindles from JAKOB Antriebstechnik offer very high clamping forces, a large clamping range and easy operation and assembly. This ensures maximum operational safety. In order to guarantee this permanently, JAKOB recommends (depending on the frequency of the clamping cycles) a regular inspection of the spindles once or twice a year. JAKOB’s force measuring systems, such as the hydraulic, autarkic force transducer HMD, are particularly simple. The intelligent clamping claw FMS even allows a constant clamping force control during the machining of the workpieces. The determined data can be transmitted wirelessly directly to a handheld display device or PC. If the clamping forces deviate from the stated nominal values by approximately 25% to 30%, an overhaul is recommended. Maintenance can be carried out directly by JAKOB. Alternatively, JAKOB also offers training courses to certify participants as operating or maintenance personnel. This means that installation and maintenance can be carried out in the company;s own operation in the future. www.jakob-gruppe.de
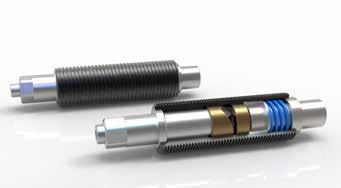