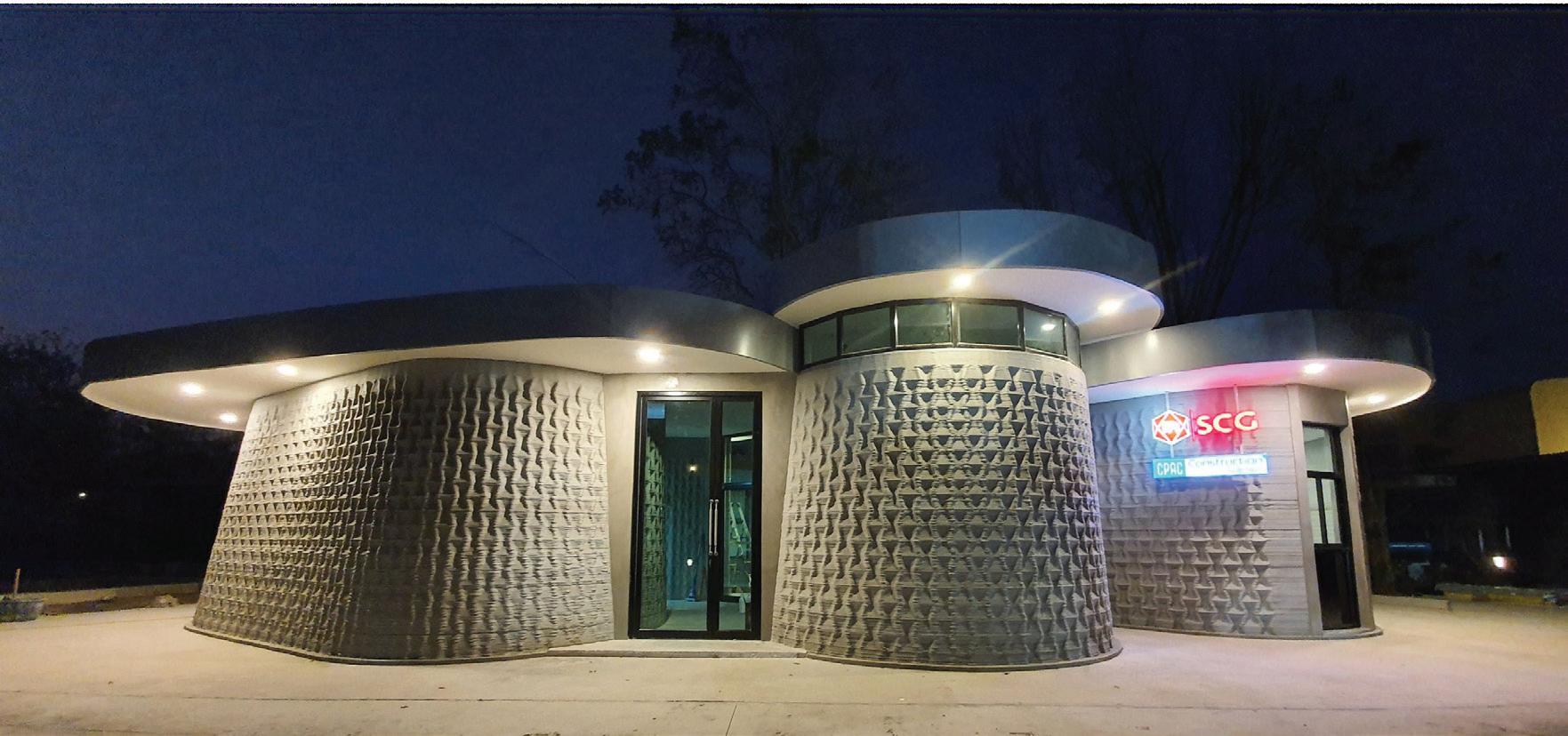
10 minute read
Cloud as the connective tissue of Industry 4.0
from AMT AUG/SEP 2022
by AMTIL
ÖLFLEX Expanded Ambient Temperature cable
LAPP high ambient heat cabling range delivers durability and reliability across diverse process needs.
Expanded ranges of high-ambient heat cabling are being stocked locally by LAPP Australia to assist companies in their Industry 4.0 digital transformation by shortening delivering times and increasing technical backup services for the globally respected ÖLFLEX range. The LAPP ÖLFLEX Expanded Ambient Temperature cable range is engineered for demanding industrial environments including foundries, commercial baking equipment, food and beverage heat processing technologies, steel mills, mineral processing involving heat processes, glass factories, furnaces, other high temperature applications. LAPP’s heat resistant wire features silicon and finely stranded tinned copper for high quality functionality and high levels of heat protection. “High temperature cable options include resistance to UV-radiation, abrasion, and tears,” says LAPP Australia Managing Director, Simon Pullinger. “Further options include outstanding resistance to oil and weather, and high flame resistance.” “As with the broader ranges of LAPP ÖLFLEX cables, our heat resistant wire cables are flexible and stand up to harsh industrial environments to keep factories and processing plants running,” he says. LAPP Australia high ambient temperature ranges, above, and food and beverage and resources and metals applications, below The Australian branch of the German global leader in cabling and connectivity solutions, LAPP Group, has more than more than doubled its inventory of locally stocked product lines, from 1,500 to more than 4,000, since setting up in this country just four years ago. Over that time, LAPP Australia has also expanded staff nearly fourfold (from six to 22 specialists and growing) to provide industrybest levels of supply service and engineering expertise. The ÖLFLEX HEAT cables feature:
• The ability to maintain electrical and mechanical properties in extreme heat and cold to ensure uninterrupted power in severe conditions. • Durable materials, including cross-linked polymers, silicone, fluoropolymers, and fibreglass. • Cross-linked polymer cables that deliver increased thermal resistance, as well as resistance to corrosion, abrasion and a range of operating fluids like solvents and detergents. • Silicone cables that exhibit hydrolysis and UV resistance. • Resistance to chemicals. The LAPP Australia ÖLFLEX range includes single and multi-core cables in different diameters, weights, temperature ratings, and resistance types. Simon Pullinger says “LAPP’s commitments to the markets it enters are always in-depth, long-term and backed by an uncompromising customer focus and dedication to client service. These values of LAPP globally have remained constant since its establishment by Oskar Lapp in 1959 and through its evolution into a global family of companies bound together with the same strong principles.” LAPP products are sought by customers seeking the assurance of top-quality products and systems that meet global compliance standards and are fully traceable back to the point of manufacture.
lappaustralia.com.au
3D Printers for Additive Manufacturing of Large Parts.
Big Area Addative Manufacturing Large Scale 3D Printing + 5 Axis Machining
Robotic Gantry 3D Printers
VSF Composite
Scan for video and further info
VSF Concrete
Scan for video and further info
Melbourne
2/137-145 Rooks Road Nunawading VIC 3131 +61 3 9417 2820 john_croft@cncdesign.com.au
Sydney
22/457 Victoria Street, Wetherill Park, 2564 T +61 2 9737 825
Brisbane
7/65 Business Street Yatala, QLD 4207 T +61 7 3343 8811
VSF WAX
Scan for video and further info
+61 (0)414 747 636 +61 (03) 9417 2820 john_croft@cncdesign.com.au virtualsmartfactory.com
Master Controllers in next-gen compressed air management systems
Since their inception, master controllers have played an important role in increasing the efficiency of compressed air stations. The latest generation of these intelligent control systems from Kaeser represents a further evolution.
Adaptable and easy to operate, Master Controllers are able to monitor and control an entire compressed air system, whilst producing data that can be utilised for numerous purposes. The result? Reduced energy costs, increased convenience, enhanced operational security and additional functionality - such as predictive maintenance and life-cycle management. The drive towards efficiency, reliability and energy savings and sustainable usage of resources, increasingly compels developers and users to optimise existing compressed air solutions ever further. Modern air stations are comprehensive systems, including compressors, cooling systems, dryers and filters. Even the individual components have auxiliary systems, such as ventilation or coolingwater systems. Moreover, stations are often incorporated into heat recovery processes to achieve optimal use of the available energy. The range and number of individual components that make up a complete compressed air system can therefore be considerable. Complex systems such as these require an organising hand to guide them, which is where master controllers such as the Sigma Air Manager 4.0 come into play. By monitoring the individual components and optimally coordinating the interaction between them, these controllers transform the individual ‘players’ into a truly cohesive team that operates reliably and efficiently. Latest generation of management systems
The very latest controllers are true management systems which act like master controllers, yet are capable of much more. They gather information regarding the connected components, measurement points via Ethernet and can transfer a limitless amount of such data to a centralised control system for evaluation. The various methods used to gather information means that the data can be used in a range of ways, with the ultimate aim of optimising the compressed air system. For example, whilst also ensuring maximum operational reliability and efficiency, the compressors and treatment components are switched on and off as needed, or operate at partial load, so that compressed air volumes and quality always remain in step with actual demand. Management systems additionally monitor all other relevant system parameters, such as the temperature and pressures in the compressor and compressed air treatment system, as well as ambient conditions. This means the control system can also check whether the compressor cooling is performing as required and whether environmental conditions (temperature, pressure) are consistent with requirements. Where heat recovery systems are used, all associated parameters are also integrated into the management system. Predictive maintenance
However, progress is not restricted to system operation alone. Maintenance represents a key area to consider when it comes to maximising cost-effective compressed air production. It goes without saying that poorly maintained systems with contaminated coolers or filters, for example, also operate with impaired specific package input power. The latest management systems therefore also take maintenance parameters into account and include them in overall optimisation strategies. Over the long-term, predictive maintenance not only reduces both energy consumption and costs, but also helps boost value-retention of the system as a whole. Moreover, complex
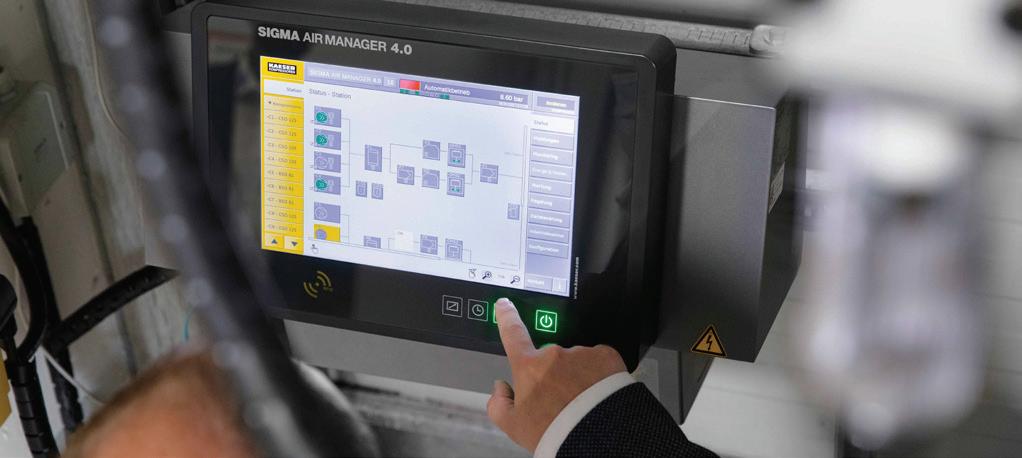
Compressed air management systems such as the Sigma Air Manager 4.0 are the centrepiece of a modern air station.
The latest generation of compressed air management systems, such as the Sigma Air Manager 4.0, now provide a range of enhanced benefits with a view to achieving optimisation of the entire system. Photo credit: Kaeser monitoring enables the creation of predictive maintenance schedules. Monitoring can take place either internally within the company, or via an external service provider. For some years now, providers of compressed air systems have offered operators the option of remote monitoring. This means that they not only benefit from continuous monitoring of the operating parameters for their daily compressed air generation, but the system is also constantly checked and rechecked from a life-cycle management point of view. In this way, any increase or decrease in requirements can be identified early on and the air station optimised accordingly. Documentation and management
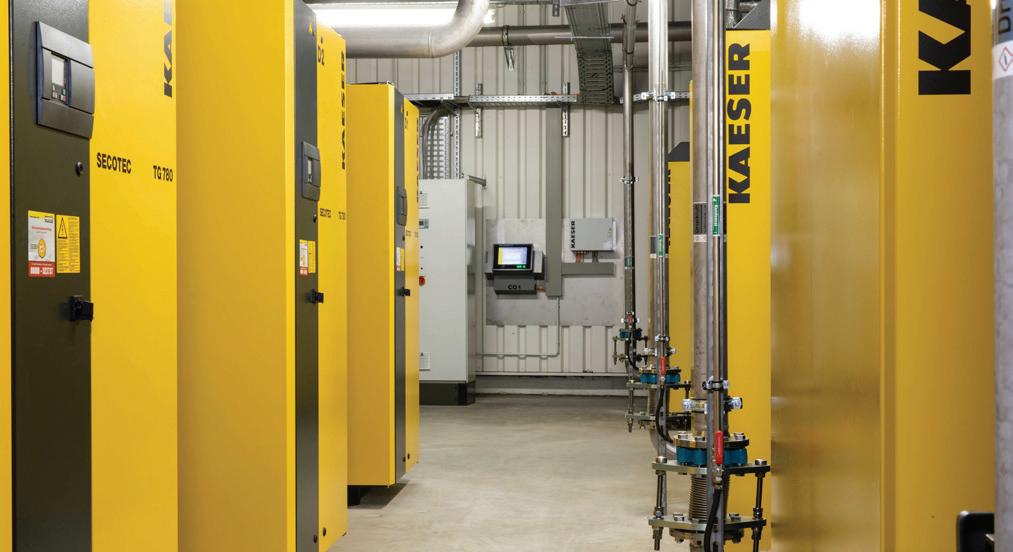
Management systems collect data regarding air consumption and heat recovery. Based on such data, costs are automatically calculated and can be assigned once again to the various individual components within the system. These functions, including visualisation, are accessed via the web using standard browsers without the need for any additional software. Conclusion
Compressed air management systems such as the Sigma Air Manager 4.0 optimise the compressed air supply and require no additional software to provide valuable cost-monitoring information. Such management systems not only control the compressors in accordance with compressed air demand, but also monitor the compressed air system as a whole, as well as any associated auxiliary systems, for optimum efficiency. They also offer enhanced data evaluation options, coupled with predictive maintenance, remote monitoring and life-cycle cost management, which in turn delivers improved reliability.
au.kaeser.com
Protect your compressor
Changing your air compressor filter will protect your system.
Just as our lungs filter out contaminants in the air we breathe, air compressors rely on air filters to remove large debris, dirt, and other atmospheric air contaminants. Because of this, air filtration is critical for producing clean compressed air and ensuring a long product life for your compressed air system. Aside from oxygen, atmospheric air contains water vapor, dust, dirt, and various other particles dependent on your operating environment. Additional contamination occurs if you are operating an oil-lubricated, reciprocating, or rotary screw compressor instead of compressor technology that delivers oil-free air, like a centrifugal air compressor. Since one cubic foot of compressed air contains millions of dirt particles, removing this contamination through a high-quality air filter will avoid damage to your compressor and keep valves from swelling. Otherwise, this will inevitably lead to increased vibration and a reduction in service life. Understanding air filter terminology
Below are the standard terms you will find when reviewing and comparing air filter elements.
Particle Size Efficiency (PSE)
This measures the specific micron sizes in diameter and determines the air filter's ability to remove particles.
Micron (micrometre)
This is a unit of measurement (one-millionth of a metre). For a particulate to be visible to the human eye, it needs to be at least five microns large. Therefore, the efficiency at which an air filter can capture microns is one of the most critical aspects when choosing an air filter.
Arrestance
The percentage of debris or dust, by weight, that a filter element can stop.
USA MERV (Minimum Efficiency Reporting Value)
This rating indicates how efficient a filter is at removing particulates and preventing them from entering the air stream. The higher the MERV rating, the more effective the filter is at trapping smaller particulates. However, it comes at the cost of creating more resistance to airflow, thus reducing system efficiency. The lower the MERV rating, the less effective the filter is at removing smaller particulates, but there is also less disruption in the airflow with these lower-rated filters.
European Efficiency Class EN1822:2019, EN779:2012 & EN779:2002
Similar to MERV, this rating was created for consistent air filter testing. The factory test ensures the air filter achieves the specified efficiency of removing debris. Types of filters
For most compressed air systems, there is a primary or pre-filter element and a secondary or final filter element. The primary filter is the first line of defense against debris and is typically replaced more often to ensure the highest level of contamination is removed. The secondary filter serves as the second defense catching the smaller particles that made it through the primary filter. High dust environments like paper mills and textile factories will benefit from higher efficiency and higher micron filters to ensure the air going into the air compressor is free from the debris generated within the factory. Environments with low dust can use standard air compressor filtration elements with a longer product life than the higher efficiency and higher micron level filters. New FS-Elliott air filter solutions
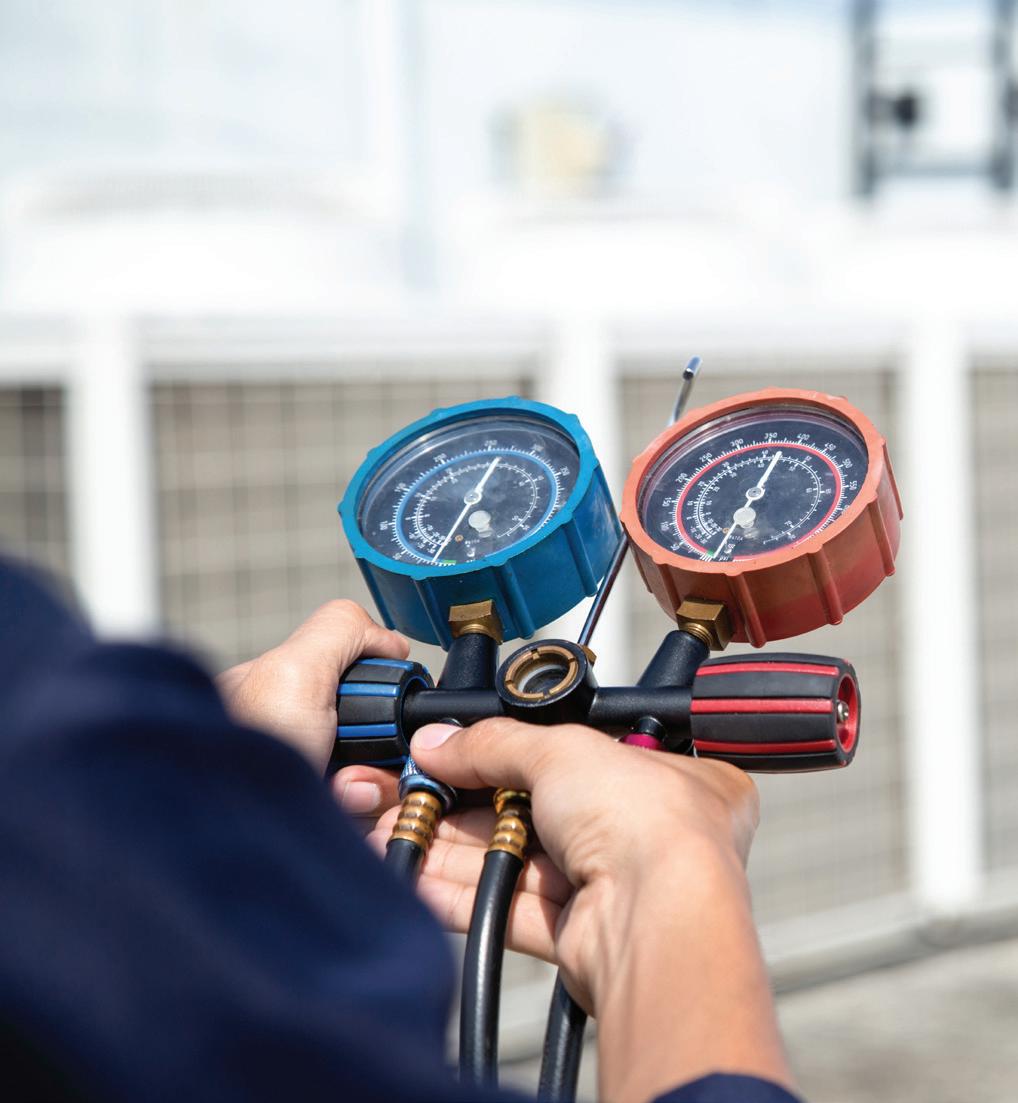
We have recently launched our Change on the Go filters, which allow operators to change the filters without turning off the compressor and disrupting production. These filters are available in standard or extended life options. Keep in mind that when purchasing an air filter, paying attention to the efficiency rating, filter material, and the efficiency of trapping microns will save you money both in the short and long run. And following OEM guidelines for replacing filters is essential to protecting your investment as well as maintaining air pressure and reliable system operation. Select the right air filter for your application
Determining which air filter is right for you depends on your compressor application, what products you produce, the amount of pollution in your operating environment, and specific industry regulations.
fs-elliott.com
Does reporting SLOW YOU DOWN?
Book a FREE demo and find out how JOBBOSS2 can help.
Scan to book