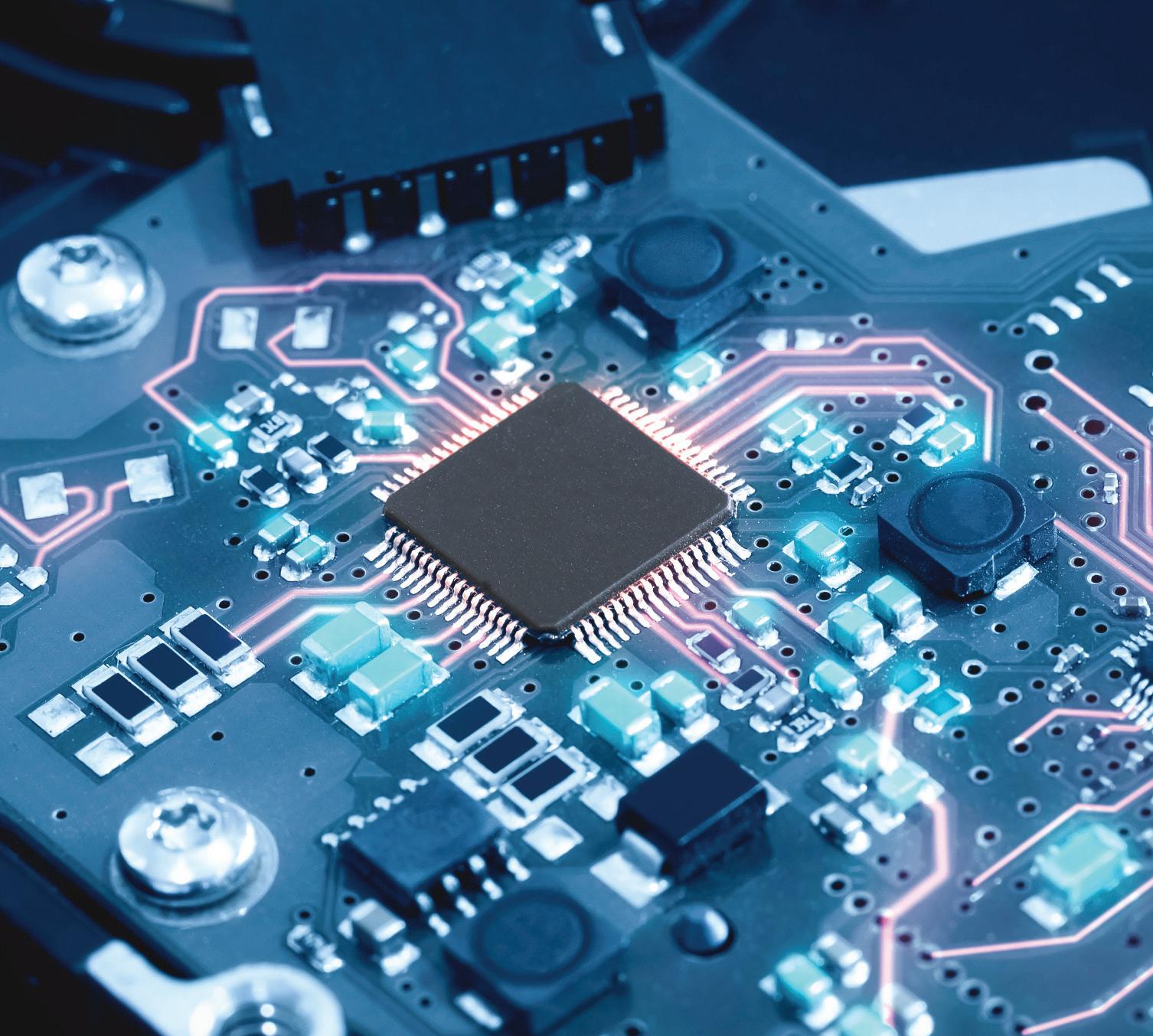
10 minute read
Making smaller better
from AMT AUG/SEP 2022
by AMTIL
CoroDrill 862 with -GM geometry supports quality in small part machining.
Steve Jobs’ philosophy that “We’ve got to make the smalls things unforgettable” is getting truer each year as big electronics players like Intel, Samsung and TSMC squeeze more functionality into the smaller devices and printed circuit boards (PCB) they produce. But this progress presents challenges in applications like micro drilling, as manufacturers must strike a balance between quality and productivity when machining tiny components. Here, James Thorpe, Global Product Manager at the leader in metal cutting Sandvik Coromant, explains how the new CoroDrill range of micro drills can help. According to Fortune Business Insights, the global market for electronic manufacturing services (EMS) is expected to rise from $504.22bn in 2022 to $797.94bn by 2029. At the same time, electronic parts are getting smaller. The need for shrinking digital circuits is clear as they can do more processing in less time and pack more storage space in the same volume. Other examples include consumer demand for higher resolution screen displays that are achieved with smaller and more numerous pixels. The growing need for smaller electronic parts presents real challenges for manufacturers, including in processes like micro drilling that involves producing holes smaller than 3mm in diameter. Micro drilling techniques are used to produce components ranging from aerospace components, hydraulic valves, watch cases and medical devices to surgical instruments, electronics, actuators, sensors, navigational systems and more. But what are the challenges? In particular, manufacturers are increasingly required to machine small, intricate components from difficult-to-machine materials like Inconel, stainless steel, ceramics and titanium. It can be difficult to machine these materials cost-effectively while maintaining the utmost quality – indeed, flawless surface finishes are as important for aerospace components as for fibre optic connectors. To compete in the growing EMS markets, manufacturers must maintain the highest levels of quality control, while also reducing any issues in the production process that can cause excess scrap or downtime. How can manufacturers rise to these challenges, while remaining competitive? The answer lies in high performance drilling solutions. Longer-lasting tools
Manufacturers have found that micro drills can exhibit inadequate tool life when machining tough workpieces, like those
Shrinking digital circuits can do more processing in less time, and pack more storage space in the same volume.
made from ISO M materials. In these cases, the design, geometry and type of coating of the drill significantly impacted their performance and durability. In response, Sandvik Coromant has introduced two new micro drills: CoroDrill 462 with -XM geometry and CoroDrill 862 with -GM geometry. The tools are ideal for precision drilling in industries that deal with small parts such as medical, aerospace, automotive, general engineering, electronics and watch-making among others. This range of micro drills are available to support machining in all ISO materials, P, M, K, S, O and H. The new geometries offer a wide range of cutting diameters and lengths. In other words, the quality of the micro drill makes all the difference to quality of the final machined product. But to what extent? To answer this question, Sandvik Coromant performed a test. Quality output
Sandvik Coromant tooling specialists compared the performance of a major micro drill competitor’s tool against the CoroDrill 862 with -GM geometry. Each tool was run in a DMG Mori Seiki Milltap 700 machine, for the purpose of drilling blind holes in an ISO M 316L stainless steel workpiece. The same tool setting was used in each case, a cutting diameter of 2.5 mm (Dc) with a speed (vc) of 40 m/min and a feed rate of 0.04 (fn) mm/z. The result was the competitor’s tool produced 630 holes before reaching tool life. CoroDrill 862 meanwhile produced 1,260 holes, a more than 100% increase in tool life over the competitor’s drill. Sandvik Coromant’s engineers recommend that customers seeking to drill micro-sized holes in notoriously difficult-to-machine materials, such as titanium, aluminium, glass and ceramics, should consider polycrystalline diamond (PCD) coating for extended tool life in these demanding applications. It’s also critical to have quality coolant to effectively evacuate chips when performing deep-hole drilling with micro tools. These features have clear advantages for manufacturers’ overall operational expenditure (OPEX), and can also help manufacturers strike a balance between quality versus productivity when micro drilling tough materials like ISO M. In doing so, to paraphrase Steve Jobs, they can ensure the small things are unforgettable for all the right reasons.
sandvik.coromant.com
SS Engineering Services commissions its third Okuma machine
Expanding engineering company located in Bundaberg, Queensland has commissioned its third Okuma machine.
SS Engineering Services Pty Ltd first opened its doors in 2009. It is located in Kensington, Bundaberg and has steadily developed over the years. The treasured family business has just commissioned its third Okuma machine a GENOS M660 Vertical Machining centre with OSP300MA Control. Okuma was the machine of choice with reliability and accuracy the principle factors. Owner, Scott Svensson had worked on Okuma machines during his apprenticeship and knew how reliable and accurate they were and this has become more important given the clients the company has established over the past thirteen years. Providing clients with engineering services including CNC Turning and CNC Milling, fabrication, product development, prototype design and reverse engineering plus general engineering services, the company today services a diverse range of clients. These include mining, agriculture, aviation, horticulture, earthmoving, automotive, medical, also the renewable energy sector plus general engineering. Svensson and his team also take full advantage of the 12 months’ unlimited training offered by Okuma and the Queensland Okuma team provide fast and reliable service from their Brisbane base. “My engineers know the Okuma machines well allowing job sharing and flexibility. The new machine will give us increased capacity which will be a great help, especially at present when we have a mountain of work on. It also opens up new markets where we could not quote on in the past,” Svensson said. “Retiring an older alternative brand machine, the selection process for the new machine considered a number of factors and we couldn’t go past the back-up service, spare parts availability, quality and reputation of Okuma in the market, echoed by other engineering shops in Queensland,” he said. “Our Okuma Queensland branch is proud to work with SS Engineering in the supply of quality machine tool options, service and application support,” said Queensland Branch Manager John Baker. “We are looking forward to working with Scott and his team to achieve the full potential of the new GENOS M660” he said. SS Engineering Services currently has a busy workload supporting the industries in the area but is always open to further opportunities and Svensson has plans in the longer term to add another two machinists to supplement the current workforce he employs at the facility. okumaaustralia.com.au ssengineeringservices.com.au

BeAM Machines
Introducing DED or Directed Energy Deposition is making a difference to the life and usability of parts. DED focuses thermal energy to fuse materials by melting them as they are being deposited. Materials such as Stainless steels, Titanium alloys, Nickel alloys and Stellites can all be applied using this process. But the real advantages of DED processes is in the variety of industrial applications including extending the life of parts by providing wear resistant coatings, repairing broken or damaged parts, multi-material applications, creating additional structures on pre-existing parts, and building new parts from precise complex geometry. The system that fulfills this task are BeAM Machines, first developed in France with recent operations commencing in Cincinatti USA with AddUp who offers a complimentary technology of Laser Powder Bed Fusion (L-PBF) systems. BeAM provide two models, the Modulo 400 and Magic 800. These 5 axis machines have been designed and manufactured for industrial purposes and sympathetic to customer requests. They are modular, upgradable and offer high performance. Modulo 400 for example, has a 640 x 400 x 400 mm build volume, a process module with 5-axis kinematics, the DED deposition nozzle, powder tight enclosure and air extractor and filtration unit offering exceptional safety operational standards. Additional peripherals of extra hoppers, an automatic tool changer, controlled atmosphere and a touch probed can be added in. The whole system able to fit into a shipping container, enabling transportation and operation in remote locations. BeAM’s DED process can produce metal parts in ‘near net shape finish’ that require no supports during the build. While the advantage of this process means less post processing and less material waste a key advantage is in fabrication. New sections can be formed, added on to old parts giving them a new purpose or worn pieces can be replaced to extend the part life. Recently, a hybrid part was produced to demonstrate the exceptional use of DED. First, using an AddUp PBF system to build the base skirt of a piston out of steel using lattice structures to reduce weight but not performance. Then BeAM DED technology was applied to add rings to the top of the piston in Inconel 625, a different material providing better performance at a higher temperature. All BeAM machines offer automated quality assurance software that displays real-time data on a screen, compatible with 4.0 platforms. Some 80 different parameters can be observed including gas flow, torque, powder consumption, porosity, and so on. Should a spike in the data output be observed, the print can be halted, and the problem fixed. In this way the sensors act as a monitoring device in real time. BeAM DED can be used for component repair, adding features, multi-material applications and producing near-net shaped parts and components. The machine utilizes traditional CNC controls and ISO G-code, meaning the tools your skilled workforce is already accustomed to using are built in.
raymax.com.au
IMCRC project brings ANCA and CSIRO together
ANCA and CSIRO developing novel 3D printing technology to manufacture cutting tools
Australian industry will soon have access to an innovative cutting tool manufacturing platform, thanks to a research collaboration between leading tool manufacturer ANCA and Australia’s national science agency CSIRO. The nine-month, $928,000 project, which is supported by the Innovative Manufacturing Cooperative Research Centre (IMCRC), is developing a new additive manufacturing process for tungstencarbide tools. The additive manufacturing technology will enable affordable, high-performance tools to be manufactured using one platform, replacing the current production process of mould pressing, sintering, brazing and grinding. Now in the advanced phase, the research is focused on refining the additive manufacturing technology ahead of ANCA taking the hybrid manufacturing platform to market. Dean McBain, Research & Technology Manager at ANCA, said the project had the potential to transform the way tungsten-carbide brazed insert tools were made in Australia and across the world. “ANCA’s collaboration with IMCRC and CSIRO has accelerated the development of an innovative additive manufacturing technology which we believe has the potential to disrupt the $2.2B global cutting tool market,” he said. “Successful completion of this project will allow ANCA to commercialise the new hybrid additive manufacturing machine platform, grow our workforce and revenue and fill a significant gap in the global tooling market.” Dr Kathie McGregor, Research Director for Advanced Materials and Processes at CSIRO, said the project would make metallic additive manufacturing technologies more accessible to Australian industry. “In keeping with CSIRO’s role of providing high-end research and development (R&D) support to the Australian industry using state-of-the-art equipment and world class know-how, we have collaborated with ANCA to further develop a unique technology,” she said. “We expect the outcomes may enable ANCA to diversify and grow its business and provide a boost to the local economy in terms of additional job opportunities and export income.” Dr Matthew Young, IMCRC’s Manufacturing Innovation Manager, said IMCRC was pleased to be supporting ANCA’s innovation, and in turn, contributing to the growth of Australia’s advanced manufacturing ecosystem. “As ANCA and CSIRO’s R&D partnership demonstrates, additive manufacturing can generate significant benefits for Australian manufacturers, reducing costs and improving speed to market,” he said. “Once developed, this revolutionary technology can be applied to a range of cutting applications, creating significant global export opportunities and furthering ANCA’s position as a market-leading manufacturer of cutting tools and equipment.” imcrc.org anca.com
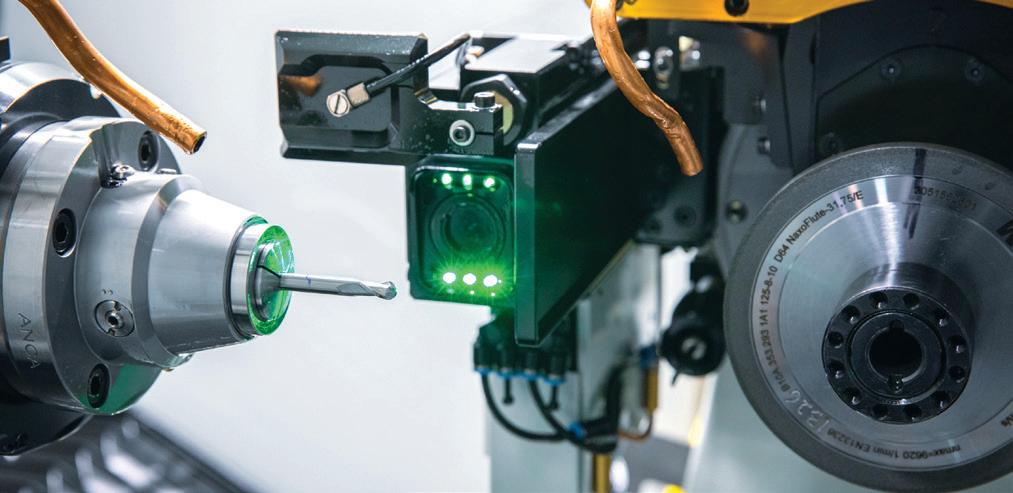
Replace awkward ballscrews with Lifgo innovative gear units and precision racks
When fast, precise and synchronised linear motion is required, our Lifgo rack and pinion gear units have proven to be reliable in many industry sectors around the world.
Smart and robust modular units offer designers the opportunity to tailor projects to meet unique needs at low cost. Lifgo enables rapid design and ease of system development for complex projects. Offers reliability and capabilities that transcend traditional product designs and boundaries, securing a competitive advantage.

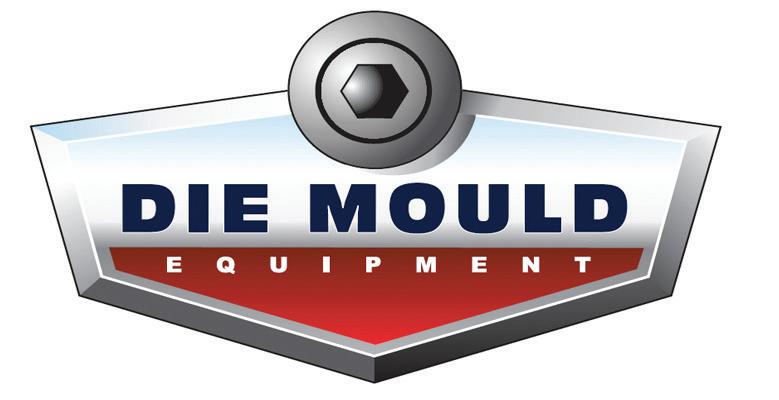
Lifting, Guiding and PositioningMaximising operational efficiencies and unlimited
combinations for various applications.
Industry sectors include: • Foodservice • Medical • Warehousing • Transportation • Forestry • Automotive
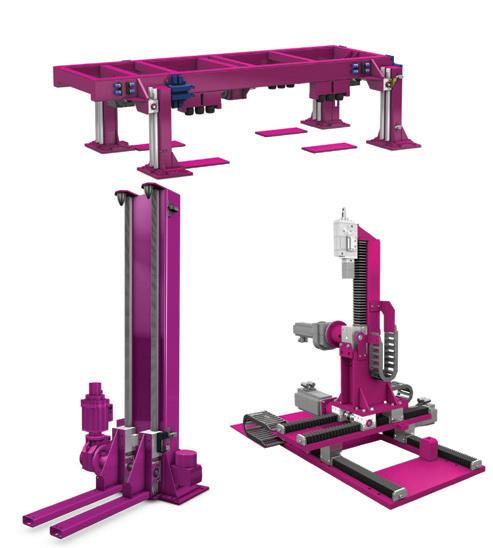
