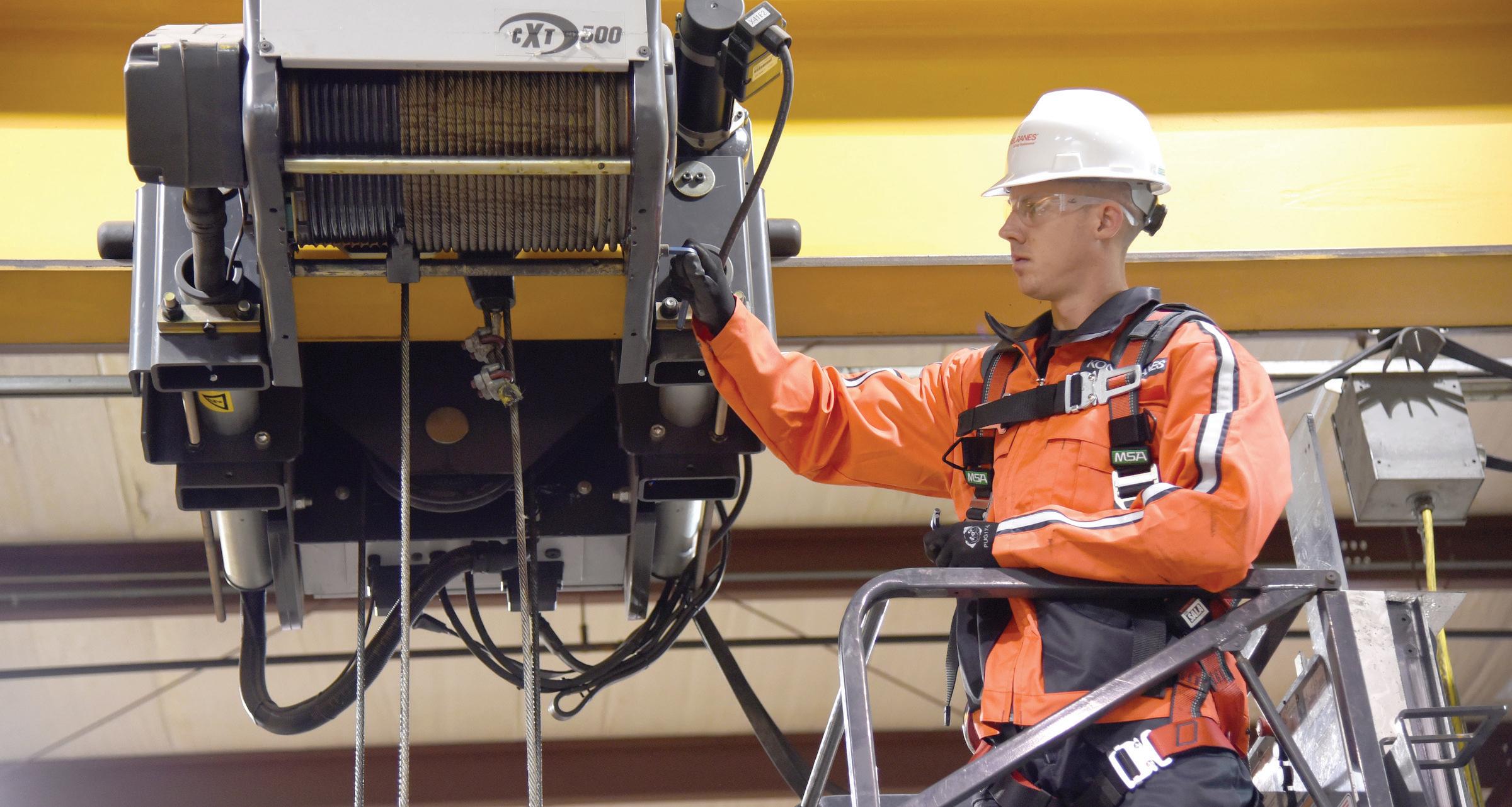
15 minute read
Cranes wired for safety, pre-use tests and digitised insights
from AMT AUG/SEP 2022
by AMTIL
Dropped loads are one of the most frequent safety hazards associated with overhead cranes, says the world’s largest crane service organisation, Konecranes.
Preventable hazards are most commonly the result of one or more of the following factors: poor operator training, improper rigging technique, an incorrect lifting device, overloading the hoist, and side pulling. So says the Konecranes Service organisation which services all brands of cranes used globally and is the original service provider for both Konecranes and Demag equipment. The global crane manufacturer and service provider, whose representatives service more than 600,000 items of lifting equipment under contract worldwide, is a world leader in digitisation technologies for crane maintenance, safety and efficiency, including its CheckApp, used for daily inspections. In addition to any tests, training, and inspections required by local laws or regulations, five key basic pre-use recommendations can enhance crane safety and help avoid dropped loads. 1. Test run the crane the full length of the runway and bridge span to ensure no obstructions will interfere with the crane travel motions. Test that all motion’s travel speed match the designed specifications. 2. Turn the crane off, engage the hoist
‘up’ switch: the hook should not rise.
Engage all other motions to ensure no movement is possible. Turn the
mainline switch back on and raise the hook to test the upper limit switch. All travel and hoist motions should match the control labelling directions. 3. Check that the wire rope is properly seated. Ensure that it is not twisted, kinked, or damaged. Check all other limit devices for proper functionality. 4. Train all crane operators on the functionality of all new cranes. 5. Provide proper inspections and maintenance as required by local regulations and recommended by the Original Equipment Manufacturer (OEM). Konecranes CheckApp digitally enhances safety and efficiency
These are just a few of the safety checks that should be performed before operating a crane. Konecranes CheckApp for Daily Inspections is a digitised way to perform these inspections and includes 15 points to check. Daily inspections are a statutory requirement in several countries and good practice for any crane operator. Konecranes CheckApp for Daily Inspections is an easyto-use app for crane users to quickly and easily record their findings when performing pre-shift and/or pre-lift inspections. Inspection results can be viewed on the ‘yourKONECRANES’ customer portal. Besides providing an audit trail of daily inspections, the information can help users recognise potential asset-specific safety or production risk issues and identify workplace improvement opportunities. It can also help identify needs for operator training as well as deviations in following local safety and other site rules. Konecranes CheckApp for Daily Inspections has been designed to help crane users quickly and easily record their findings when performing pre-shift and/or pre-lift inspections. It gives a cost-effective, digitalised way for recording and retrieving daily inspection data that can be used for internal auditing and compliance. Daily inspections are a statutory requirement in several countries. The daily inspection is a user’s – or crane operator’s – own assessment of the condition of an asset and environment for safe use. It is not an expert’s examination of the condition of an asset or component. Konecranes CheckApp for Daily Inspections follows the guidance set in the ISO 9927 standard and in applicable statutory regulations. The app can be downloaded for free on the Apple AppStore and from Google Play for Android devices — on a mobile or tablet. Company personnel can use their own or shared company-provided devices to perform the daily inspections.
konecranes.com
New safety standards for solar installs
Energy Safe Victoria (ESV) has welcomed a new Australian Standard that will strengthen the safety of solar photovoltaic (PV) installations.
The new Standards are now in effect. They allow solar installers to keep pace with innovations across the solar industry, while reducing the risk of house fires. The key change delivered by Standard AS/NZS 5033 focuses on direct current (DC) isolators, which provide an additional safety mechanism that shuts down solar PV systems in case of an emergency. In Australia, DC isolators are typically installed on roofs next to solar panels, which exposes them to rain, wind and other elements. In some cases, incorrectly installed DC isolators or those damaged over time can pose a potential fire hazard. The new Standards reduce that risk by providing installers with different options on how solar panel systems can be isolated and no longer mandates the installation of an isolator on the roof for all installations. ESV representatives chaired the committee that delivered the new Standard, which was initially published last November, and included a six-month transition period. This period has now expired. Victoria leads the nation in solar installation safety, with stringent, industry-leading standards put in place when Solar Victoria launched in 2018 that prompted a lift in safety standards industry-wide that have set the Australian benchmark. Since the beginning of 2020, audits of solar systems installed under the Victorian Government’s Solar Homes Program have found the number of unsafe installations has dropped from 2.2% to zero due to education and training provided to industry, along with enforcement by Victorian Government agencies including ESV. In March, ESV and Solar Victoria also launched the Show Your Solar Some Love campaign. “As more people take up solar, ESV will continue to work to ensure all solar systems are installed safely and efficiently,” said ESV Commissioner and Chairperson Marnie Williams. “We’ve played a major role in the delivery of these new Standards, which protect Victorians from house fires and damage caused by exposed DC isolators. We’re also calling on all Victorian solar users to ensure their systems are serviced by a licensed A-Grade electrician at least once every two years.” Regular servicing reduces the risk of failure and fire, which is a risk particularly among older, unserviced solar systems. Servicing by a licensed A-Grade electrician at least once every two years mitigates the risk and ensures solar PV systems are working safely and efficiently. Servicing includes electrical testing of the components that make up a solar panel system, as well as a thorough visual inspection to ensure the integrity of equipment and cabling. It also includes the clearing of debris and leaf litter under the solar panels and around the inverter. People should also be aware of unlicensed workers offering solar cleaning or maintenance.
esv.vic.gov.au/campaigns/solar-safety
Four Victorian regulators have taken their Build Aware campaign to the Latrobe Valley, ensuring construction workers are meeting safety, environmental, building and plumbing compliance obligations.
Energy Safe Victoria (ESV), WorkSafe, the Victorian Building Authority (VBA) and Environment Protection Authority Victoria (EPA) visited worksites providing operators with information on laws that protect the community and the environment. The initiative, run between 30 May and 3 June, focused on the Latrobe Valley, working to educate and call out issues. Inspections were carried out across the Latrobe Valley to ensure compliance with safety, environmental, building and plumbing standards. Build Aware has previously targeted regional areas including Shepparton, Bairnsdale, Ballarat, Wodonga, Geelong, Bendigo and Warrnambool. Joint activities delivered by the regulators include industry trade breakfasts, joint inspections and educational presentations to local TAFE students. “The new Environment Protection Act has given EPA greater power to protect the environment and community and every Victorian now has a legal responsibility to take reasonable action to do the same,” said EPA Regional Manager Gippsland Zac Dornom. “You also have the power to report illegal waste disposal – it’s a way of protecting the environment and ridding the industry of the dodgy operators who compete unfairly with legitimate builders.” During the inspection week, ESV compliance officers focused on dangers related to No Go Zones and the need for construction workers and machinery operators to be aware of overhead and underground electrical assets. WorkSafe checked for risks associated with exposure to asbestos and crystalline silica dust and reminded employers and workers of the changes to the OHS regulations, including the requirements to identify ‘highrisk’ crystalline silica work. “Exposure to hazardous materials such as asbestos or crystalline silica dust during demolition or construction work can lead to serious and life-threatening illnesses,” said WorkSafe Director Construction and Earth Resources Matthew Wielgosz. “Duty holders will be reminded that, since 15 May 2022, changes to OHS regulations mean businesses making dust when working with materials containing crystalline silica must identify and document any highrisk silica work and the measures used to control those risks.” The VBA again checked building and plumbing works as part of its Proactive Inspections Program, aiming to reduce non-compliant building and plumbing work. The EPA ensured the construction and demolition industries are aware of their responsibilities when it comes to waste management at building sites.
vba.vic.gov.au worksafe.vic.gov.au esv.vic.gov.au www.epa.vic.gov.au
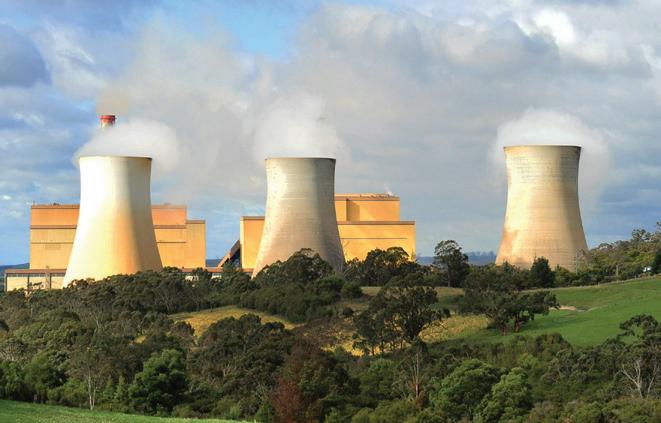
Look up for safety’s sake
ESV repeats powerline safety message following serious Bendigo incident.
Energy Safe Victoria (ESV) is pleading with Victorians to look up and be aware of their surroundings following an incident northwest of Bendigo, where a farmer contacted with overhead high voltage powerlines. For the past decade, ESV’s Look Up and Live campaign, has warned machinery operators – especially farmers - to be aware of their work environment and check for powerlines before work commences. “We are thinking about the farmer and his family and hope he’s able to make a full recovery. Unfortunately, this incident could have been avoided if he’d been more aware of his surroundings before starting work,” stated ESV Commissioner and Chairperson Marnie Williams. “It’s so easy to forget that the simple act of looking up before you start work, could save your life or the life of a co-worker.” Recently, ESV launched its 2022 Look Up and Live campaign, after 58 powerline-related incidents took place in January and February. In 2021, ESV also reported 214 incidents, 34 of which involved high voltage lines and four causing serious injury. Of that 214, a total of 141 involved overhead powerlines and 73 underground. Below are a few simple safety tips to avoid an incident occurring: • Understanding No Go Zones, rules and distances for safety clearances near overhead powerlines. • Ensure an ESV-registered spotter is on hand when working near overhead powerlines. • Display Look Up and Live stickers on any machinery or equipment which is raised overhead. • Remember that powerlines are more difficult to see at dawn and dusk and that electricity can jump gaps. • Be extra aware in rural areas as overhead powerlines are predominantly single conductor lines that are difficult to see and easy to forget. • If machinery does hit powerlines, operators should stay inside the vehicle and call for help. • If it is not safe, for example in case of fire, jump clear from the vehicle, keep legs and feet close together and landing both feet on the ground. Then shuffle with both feet staying close together to a distance more than 10m away. NEVER touch the vehicle and the ground at the same time. • Bystanders and spotters should also stay at least eight metres away, as they can still be shocked when approaching the vehicle.
esv.vic.gov.au
Enmin’s SAT and FAT tests for safety
Enmin’s rigorous focus on compliance ensures minimal rectification work and maximum operator safety.
For over 40 years, Enmin has been designing and building an extensive range of vibratory equipment and materials handling solutions for a myriad of applications and environments. The company’s vast knowledge and expertise in this area has seen their list of customers grow to include most of Australia’s leading food industry manufacturers. Since its inception, Enmin has taken a no compromise approach to safety and its extensive experience of the materials handling industry has seen it develop products that have safety at its core. All the equipment that Enmin manufactures at its factory in Braeside is designed with a clear focus on operator and electrical safety and ergonomic design to maximise operator efficiency and minimise fatigue. “There are a number of Australian industry safety standards that need to be met. In addition to that, all our customers have additional requirements to suit their particular operating environment – different sites have different needs. Our aim is to accommodate all possible standards,” said Enmin General Manager, Anthony Gallaher. “Because we are a local manufacturer we can offer a Factory Acceptance Test (FAT) where a customer can come and inspect the equipment and make any minor changes before being shipped; this includes supplying our own risk assessment certificate for further peace of mind. As a result, this ensures that when customers run their own SAT (Site Acceptance Test) we find minimal or no rectification work is required to get it ‘system ready,’” he added. “Certain countries will be designing and building equipment with only price in mind. Very often this does not meet even the most basic safety standards. Couple that with little on-the-ground support, and it will ultimately cause a lot of problems which often delays the installation of the equipment leading to unproductive hold-ups and additional costs,” Gallaher continued. Enmin’s Hopper Feeder and Mi-CON elevating conveyor are two of the company’s most popular products and are perfect examples of the company’s safetyfirst focus. “Very often companies may think that imported equipment meets the Australian standards, but that is often not the case. Also, whilst it may be fit for a company’s needs today it may not be right for the long term as their business evolves,” Gallaher added. “Whilst lower cost equipment from overseas may initially seem an attractive proposition, it is ultimately false economy. The rectification costs and time involved to ensure the unit meets Australian safety standards is significant. And if a company does decide to cut corners on operator safety, they are literally walking a tightrope – things can go horribly wrong. Getting the right safety up front is a small price to pay for security and safety long term,” Gallaher said. “Many other benefits accrue when buying locally made equipment: prompt delivery turnaround, the ability to work closely with us during every phase of the project and the opportunity to easily add to or modify equipment years later as production needs change. And of course, being a local manufacturer means we are only a quick phone call away to immediately respond to any customer technical query or provide service and parts support throughout Australia,” he summed up. “The reassurance that comes with having safety built in and the knowledge that the equipment is fit for purpose from the start far outweighs any price difference. In terms of peace of mind, time savings and return on investment, there is simply no comparison,” Gallaher concluded. enmin.com.au
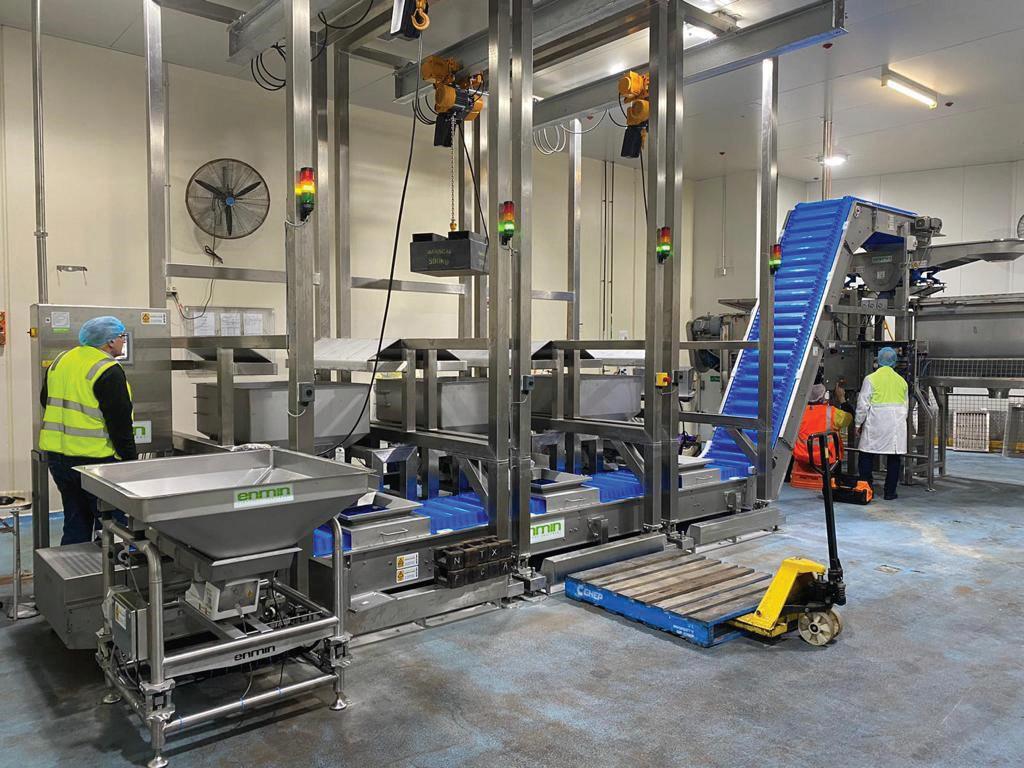
Reven industrial air cleaning vital for R&I Instrument & Gear
Reven air cleaners keeps both CNC parts and the air clean at R&I Instrument and Gear.
Melbourne-based R&I Instrument & Gear is a precision machining/ engineering company that supplies a range of specialised components to OEMs in a number of niche markets including medical and scientific instruments, defence and aerospace industries. The company is a registered Quality Endorsed Company meeting both requirements for ISO 9001:2015 and AS9100D. Established in 1948 by Bob Brown, Jeff Rowell and his wife Joyce took over the business in 1978. In 1993 their son Andrew Rowell took over as the Operations Manager and is currently General Manager. In 1999 the company came under the control of the Hardman family as a sister company to Hardman Bros Pty Ltd – a company that is involved in industrial type power transmission applications. Some of the high-precision parts that R&I manufacture are used in medical devices such as automated blood testing and laser eye surgery machines. In addition, a variety of components for the aerospace industry are manufactured; these include search lights for rescue helicopters along with a range of other defence-related products. The company prides itself on the many long-term relationships they have established over the decades. These include Agilent Technologies, Aim Lab Automation and Ellex Medical. A customer of Dimac for a number of years, R&I recently purchased their second Reven Compact cleaning table. Reven has been specialising in industrial air cleaning for decades and the company’s knowledge in the field of air cleaning has grown continuously. Their expertise is reflected in numerous internationally protected patents, design protection rights and unique technologies. All Reven products are designed and constructed in Germany. “The compact Reven table is particularly versatile due to the fact that it does not require any electric power supply as the cleaning is performed by compressed air - making it ideal for the cleaning and inspection work of CNC parts,” Jeff Rowell said. One of the key features of the Reven cleaning table is that it features Reven’s patented high-performance X-CYCLONE separating system which is integrated into the table. The X-CYCLONE technology, now into its fifth generation, was developed for the separation of airborne substances including fluid and fine dusts. The system is entirely mechanical without any auxiliary energy required and contains no disposable products or filters that need to be replaced. It is a sustainable air-cleaning concept thanks to the use of cleanable separators. As a result, the operating and maintenance costs are considerably lower compared with conventional air cleaners. A lifetime guarantee is offered on the X-CYCLONE basic separator elements and the corrosion-resistance of the enclosure. “The health and safety of our workers is critical for us. We use solvents to clean parts and Reven’s integrated air cleaner ensures that fumes and other invisible superfine particles are filtered. This aspect was a key reason for us selecting the Reven brand,” Rowell continued. “In addition, when parts are being cleaned by the air blast, the residue coolant and chips from the workpiece are also captured, with coolant recovered, therefore keeping the work area clean from coolant and chips,” he added. “We’re really pleased with the Revens. They’re very user-friendly and simple to operate. It ensures the workspace air is kept clean, improves operator safety, and has boosted our productivity. Best of all they cost nothing to run.” In addition to the cleaning tables, R&I have a number of Reven mist extractors fitted to various machines. They also purchase other workholding products from Dimac including Lang Technik MakroGrip 5-axis vises. “I’ve always received great service and support from Dimac and the fact they’re a local supplier with a long-established history and range of quality brands are the key reasons I’ll continue to use them,” Rowell concluded.
rigear.com.au dimac.com.au
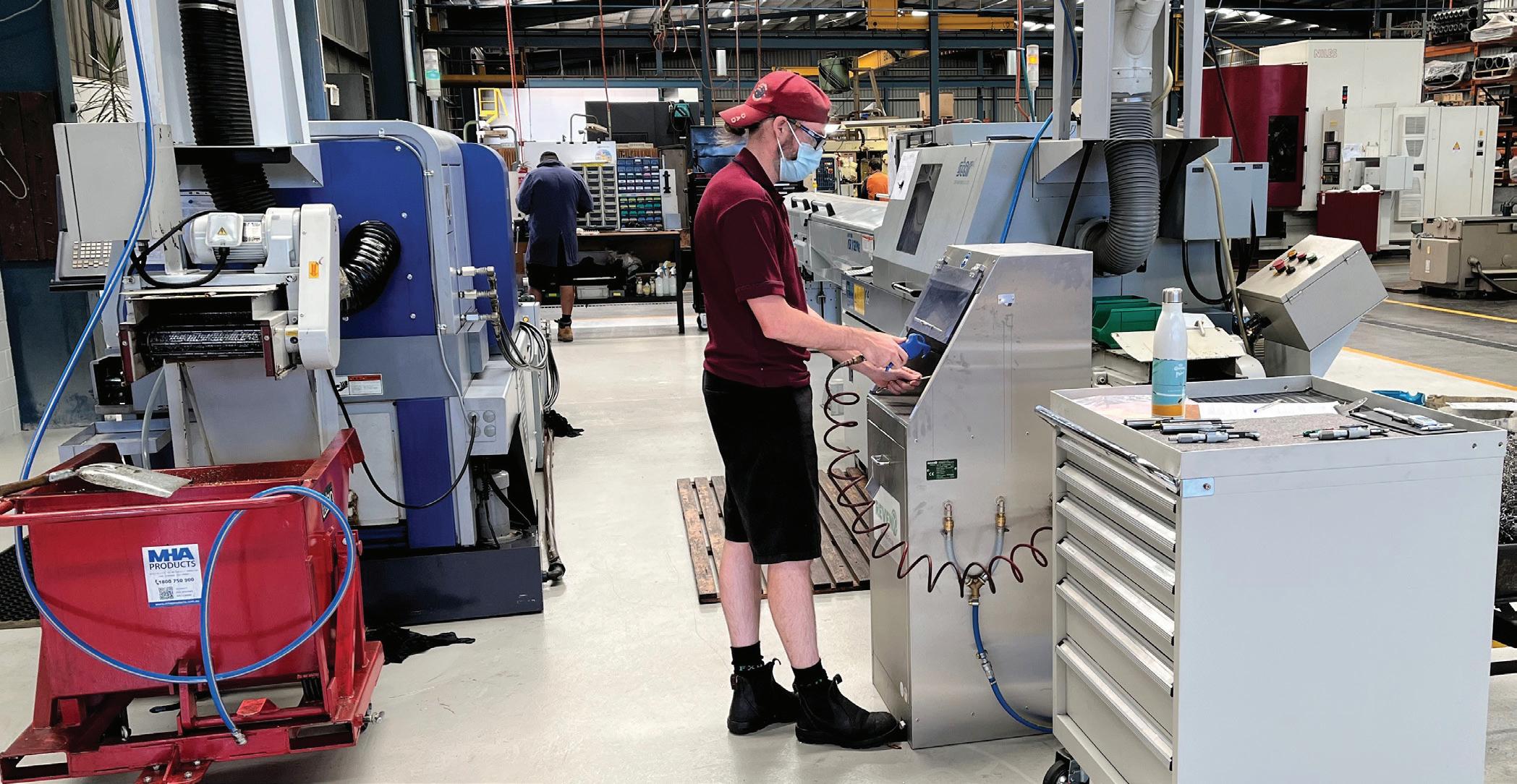