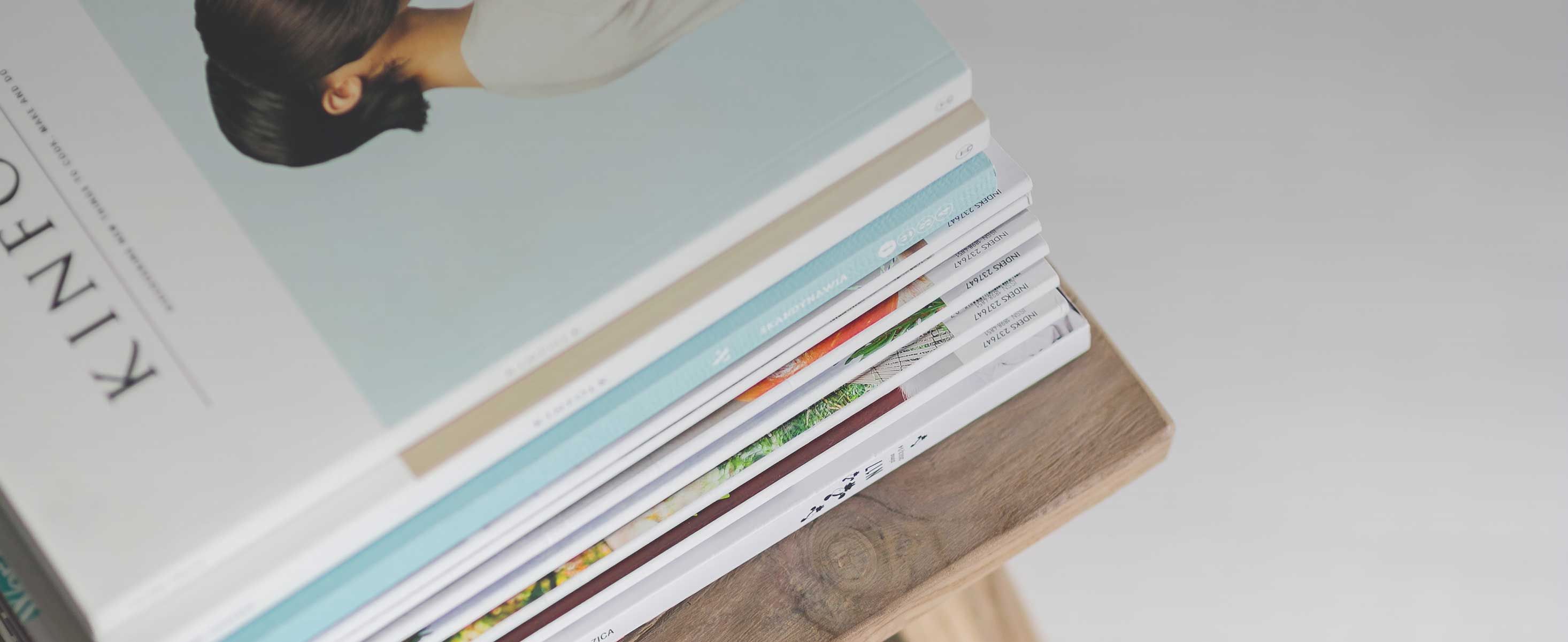
14 minute read
Innovative consumables for mass finishing operations
from AMT AUG/SEP 2022
by AMTIL
Simple steps to improve finishing results, sustainability and efficiency. When it comes to achieving the required quality of products by Mass finishing without foaming surface refinement, mass finishing technology can be used for a broad range of different finishing tasks. With its comprehensive R&D activities, Rösler Oberflächentechnik GmbH continues to generate new technical highlights not only for the machine technology but also for the respective mass finishing consumables. Three recently introduced products make it possible to significantly improve the finishing results, the process consistency, the cost-efficiency and sustainability of mass finishing operations. At the same time, they open the door for new applications, for example, the finishing of complex, cup-shaped work pieces. Unwanted foam is a common phenomenon in mass finishing processes with plastic media, even with foam-reduced media versions. Foaming can be problematic because, acting as a buffer between the work pieces and media, it reduces the grinding performance and material removal rate. This can diminish the process stability, and the processing aim can frequently no longer be achieved within the defined cycle time. Moreover, the foam containing metal and media fines contaminates the surface of the finished work pieces. The foam also causes a deterioration of the process water cleanliness, requiring a higher compound dosing rate Mass finishing technology can handle all kinds of surface finishing and forcing the user to replace the process water more frequently. tasks ranging from the simple deburring/edge radiusing and Last-but-not-least, foam discharged from the mass finishing surface grinding to high gloss polishing of mass- produced bulk machine contaminates the working environment. In the past the goods and single components. It can even create special effects on users tried to control the foaming by adding special chemical the surface of the work pieces. Of course, like any other industrial compounds. But this was not very successful, caused additional processes, mass finishing operations must comply with all kinds costs and reduced the process sustainability. of requirements such as high-quality standards, process stability, work piece traceability and cost-efficiency. More recently optimal resource use and sustainability have become a focal point in numerous industries. And finally, the rapidly growing automation and digitisation of manufacturing operations also calls for specially adapted solutions for mass finishing operations. With its non-foaming plastic media, the so-called “N” version, the R&D Department at Rösler has now developed a better solution. “Prior to introducing the product in the market, we conducted extensive field trials with special pilot users,” says Christian Höhn, Head of Technology Management at Rösler. “The trials proved convincingly that the non-foaming plastic media has the same For decades Rösler Oberflächentechnik GmbH has met these grinding characteristics and performance as the standard product.” challenges with comprehensive research and development in The trials also demonstrated that with the newly developed media, the equipment sector as well as in the fields of process and the mass finishing processes are running much more stable, and automation technology and consumables. Rösler is producing the required results are achieved in shorter cycle times. This positive all its consumables in-house. “We study the technical trends and effect regarding cost-efficiency and sustainability is augmented by requirements in numerous industries and markets extensively,” says a longer usable life of the media and process water and a reduced Rüdiger Böhm, global R&D Manager at Rösler. “Our findings are then compound usage.” systematically utilised for the development of innovative products to provide a significant incremental value to our customers and to expand the application range for the mass finishing technology.” “Because of the disruptive foaming many users had been using ceramic media, even though this was not the best option. For these users the non-foaming plastic media version is a great opportunity MultiShape makes the impossible possible to optimise their finishing processes,” concludes Höhn. All plastic Such an innovation is the new MultiShape ceramic media. media in the comprehensive Rösler portfolio are available in the Compared to all other products currently available in the market, non-foaming “N” version. this media has a patented shape without any flat, parallel surface Dust-free drying with organic drying media areas. On the one hand this unique design prevents media lodging in the work pieces, which can occur particularly in case of complex work pieces. Such lodged media can severely affect the finishing process and must frequently be removed by hand. On the other hand, the shape with its rounded surface allows the surface refinement of work pieces, which to-date could not be handled by mass finishing at all or only with very complicated operational setups. This includes components with difficult-to-reach surface areas like tight radii, undercuts, notches, and slits, which can frequently be found in stamped and bent components. The unusual ceramic media also allows the effective and homogeneous finishing of external and internal surface areas on tube segments and cup- shaped components like housings and deep drawn parts. The third new development in the consumables sector in 2021 allows a significant reduction of the dust occurring during drying processes utilising organic drying media such as maizorb. Even in small quantities the liquid, easily dispensable, Anti-Dust additive significantly reduces the formation of dust. Depending on the operating times and work pieces, the additive can be manually added or dosed fully automatically. The Anti-Dust additive is employed in drying operations for metal and plastic components, whenever organic drying media is used. Without negatively impacting the drying performance it guarantees absolutely spotfree surface finishes. At the same time, dust residues on the finished work pieces and the surrounding area are minimized. This also represents a huge step towards a clean, low-dust working Compared to traditional ceramic media, the new product is also environment. characterised by a faster and more dynamic motion of the work piece/media mix and a higher material removal rate. This results in up to 10% shorter finishing times. The new media represents a significant contribution towards higher productivity and costefficiency. Another important attribute of the MultiShape media are its uniform wear characteristics. This excellent shape retention feature allows a longer media use, which is positively affecting the operating costs. The grinding intensity can be adjusted to the respective finishing application through different ceramic compositions. “Because it is purely organic and complies with the prevailing food standards, the Anti-Dust additive also represents a significant contribution towards a cleaner environment,” says Rainer Schindhelm, Division Manager of consumables production. Increasing the productivity of the mass finishing technology, improving overall sustainability and reducing CO2 emissions; these are the main goals of the development work at Rösler in the year 2022. Various solutions from the sectors equipment technology and consumables are already being tested by various customers.
rosler.com
New government’s proposed workplace relations reforms
Stephanie Shahine and Simone Caylock outline many of the proposed reforms which will require amendments to the Fair Work Act 2009 (Cth) (FW Act) and in turn, changes to the role of the Fair Work Commission (Commission).
It has now been over two months since the Australian Labor Party (ALP) was successfully elected into Parliament. As part of the ALP’s pre-election campaign, they proposed a number of reforms in the workplace and industrial relations space which, given the election outcome, the Albanese government is now likely to pursue. These proposed reforms are outlined below. Gig workers
The ALP has promised to expand the jurisdiction of the Commission to allow it to hear matters which pertain to all forms of work which are ‘employee-like’, including ‘gig workers’. This means the Commission may soon be able to make orders on the minimum standards of work for those workers and determine what rights and obligations may apply to the engagement. Casual employees
Currently, if there is no firm advance commitment to ongoing work and if the employee and employer agree to this, then the employment relationship will be defined as casual under the FW Act. The ALP is seeking to amend the definition of a casual employee to restore the common law definition which takes into account the employee’s actual pattern of work. Labour-hire
Under the ‘Same job, same pay’ campaign the ALP proposed that workers who are engaged via labour-hire companies should receive the same rate of pay and conditions as workers who are employed directly by the host employer. It remains unclear at this stage how this proposal would be implemented however, in order for it to be enforceable the jurisdiction of the Commission and/or Fair Work Ombudsman will need to be expanded to allow for enforceability and accountability. Fixed-term contracts
The ALP intends to implement a cap on the length of fixed-term contracts of 24 months. In order to implement this, the FW Act will need to be amended. It remains unclear what will be included in this provision of the FW Act if this legislative change is adopted. The ALP has flagged that this provision will prevent employers from employing an individual on a fixed-term contract if it exceeds 24 months. Or this provision will limit fixed-term contracts for the same role to two consecutive contracts, including renewals, of two years. There will be a mechanism for exceptions in limited circumstances however, it remains unclear what those exceptional circumstances may be or how they would operate in practice. Superannuation
Currently, any unpaid superannuation entitlements must be pursued through the Australian Taxation Office (ATO). The ALP has proposed legislating superannuation into the National Employment Standards (NES) in the FW Act which would enable the Fair Work Ombudsman to pursue unpaid superannuation on behalf of workers. Secure Australian Jobs code
A Secure Australian Jobs Code will be introduced which would apply to government contracts. This Code will include guidelines regarding job security, fair and reasonable wages and conditions and compliance with the Workplace Gender Equality Act 2012. New federal ‘wage theft’ laws
Currently, only the State of Victoria has ‘wage theft’ laws which are in force. The ALP is seeking to pass national ‘wage theft’ laws which will result in criminal penalties for all Australian employers if they are found to be deliberately and dishonestly underpaying employees. Implementing the remaining recommendations in the Respect@Work Report
The Morrison Government implemented some of the recommendations arising from the Respect@Work Report and introduced the Sex Discrimination and Fair Work (Respect at Work) Amendment Act 2021 as a result (see related article here). The ALP intends to implement the remainder of the recommendations in the Respect@Work Report and seek to legislate the right to 10 days paid family and domestic violence leave in the NES. Measures to address the gender pay gap
The ALP is seeking to strengthen the ability of the Commission to order pay increases for workers in low-paid, female-dominated industries. It is also seeking to close the gender pay gap by introducing legislation which will impact employers with more than 250 employees. Employers in this category will need to report their gender pay gap publicly, prohibit pay secrecy clauses in employment contracts and/or policies and give employees the right to disclose their pay if they so choose to. Consultation on portable entitlement schemes for certain industries
In consultation with state and territory governments, unions and industry, the ALP is seeking to develop portable entitlement schemes for Australians in certain industries. Specifically, it is focusing on industries which have high instances of ‘insecure work’. Another key point to note is that the ALP is seeking to abolish the Registered Organisations Commission (ROC) and the Australian Building and Construction Commission (ABCC). What’s next
While it currently remains unclear how these reforms would be implemented, we expect further details on the proposed legislative reforms to be released after the Federal Government has consulted with business, employer groups and unions in the coming months.
Rigby Cooke Lawyers’ Workplace Relations team can assist you to better understand how these developments could impact your business and assist with understanding your obligations as an employer. Stephanie Shahine is Associate, Workplace Relations, Rigby Cooke Lawyers. T: +61 3 9321 7839 E: SShahine@rigbycooke.com.au Simone Caylock is Partner, Workplace Relations, Rigby Cooke Lawyers. T: +61 3 9321 7894 E: SCaylock@rigbycooke.com.au rigbycooke.com.au
The wait is over: a glance at Western Australia's WHS Act
The Work Health & Safety changes reflect perhaps the largest transformation of WHS laws in WA to date. Ian Bennett and Aimee Dash explain.
Western Australia’s Work Health and Safety Act 2020 (WA) (WHS Act) is now in operation. After much anticipation and a delay in commencement, Western Australia has now joined all other Australian jurisdictions (except Victoria) in the adoption of harmonised work health and safety (WHS) laws which took effect on 31 March. The new WHS Act repeals WA’s previously enforced Occupational Safety and Health Act 1984 (WA) (OSH Act) applying to most workplaces and associated safety provisions for other specific work environments. The WHS framework adopted in WA is largely aligned with the national model WHS laws that have been in operation and progressively implemented in other jurisdictions since 2012. The primary aims of the model scheme include greater consistency and consolidation of obligations in ensuring workplace safety, reducing regulatory burdens and offering stronger protection to workers. The changes reflect perhaps the largest transformation of WHS laws in the state to date. Overview
The WHS Act is directed to requiring all persons (corporate or otherwise) involved in a work arrangement to do what is reasonably practicable to address potential risks to health, safety and wellbeing. In this regard, the framework adopts broader notions of a ‘person conducting a business or undertaking’ (PCBU), ‘officers’ and ‘workers’, as attracting duties, which is a move away from traditional concepts of employment as being the genesis for obligations given that work relationships can now take a myriad of forms. There are also ‘up’ and ‘down’ stream obligations on persons: involved with control of workplaces, fixtures, fittings or plant at workplaces; persons who design, manufacturer, import, supply, install, construct and/or commission plant, substances and/or structures, and persons who provide services relating to WHS matters. Duty Holders
The persons who hold duties are slightly different by virtue of the utilisation of broader concepts and notions under the WHS Act that include: • a PCBU that may include a sole trader, partnership, company, unincorporated association or government department, and the duty is to take all reasonably practicable steps to ensure the health and safety of workers • an officer is an individual that may include a director or secretary of a corporation and a person who makes or participates in making decisions that affect a whole or substantial part of the business or undertaking, and the duty is to exercise due diligence, and • a worker is an individual that may include an employee, volunteer, contractor, sub-contractor, apprentice, trainee or student on work experience and workers have a duty to take reasonable care. Significant changes and developments
The WHS Act imposes a more expansive obligation on ‘officers’ (which is not limited to individuals holding particular formal titles). Ultimately, an officer’s potential liability is not contingent upon that of the PCBU. An officer is expected to demonstrate ongoing ‘due diligence’ by virtue of six specified components: • acquiring and keeping up to date with WHS matters • understanding the nature of the PCBU’s activities, hazards and risk • ensuring the availability of appropriate and adequate resources and processes • receiving and responding to information about risks and incidents in a timely manner • implementing processes for ensuring compliance with applicable WHS duties and obligations, and • verifying the effectiveness of the systems, processes and resources utilised. Introduction of offence of industrial manslaughter
Although not a ‘default’ feature of the model WHS laws, the WHS Act has introduced the offence of ‘industrial manslaughter’ in WA (joining other model jurisdictions including Qld, the ACT and the NT). The most serious potential penalties under the WHS Act apply with respect to the offence of industrial manslaughter, which may be up to a maximum of 20 years imprisonment and a fine of $5m for an individual, and a $10m fine for a body corporate. Preclusion on insurance for penalties
The WHS Act expressly precludes and prohibits insuring against WHS penalties that may flow from offences. In this regard, it is an offence to purchase insurance or indemnify another for WHS fines. However, this does not preclude insurance products that may support and assist with associated costs (such as legal expenses). Regulatory and enforcement powers WorkSafe remains the relevant regulator under the WHS Act and has many of the same powers to monitor, investigate and enforce compliance with respect to workplace health and safety. Additionally, the limitation period for the commencement of prosecutions is two years from the date of the offence (one year less from that which existed under the OSH Act). The new WHS framework in WA represents a significant change and it may take some time for adjustment and associated compliance. Accordingly WorkSafe has also issued a Statement of Regulatory Intent - emphasising that it will be adopting a predominantly ‘supportive and educative approach’ to potential compliance issues over the next year. Now is an opportune moment for workplaces to reflect on existing governance systems and consider any potential enhancements. There may be a need to update current procedures to reflect the new WHS laws in place in WA.