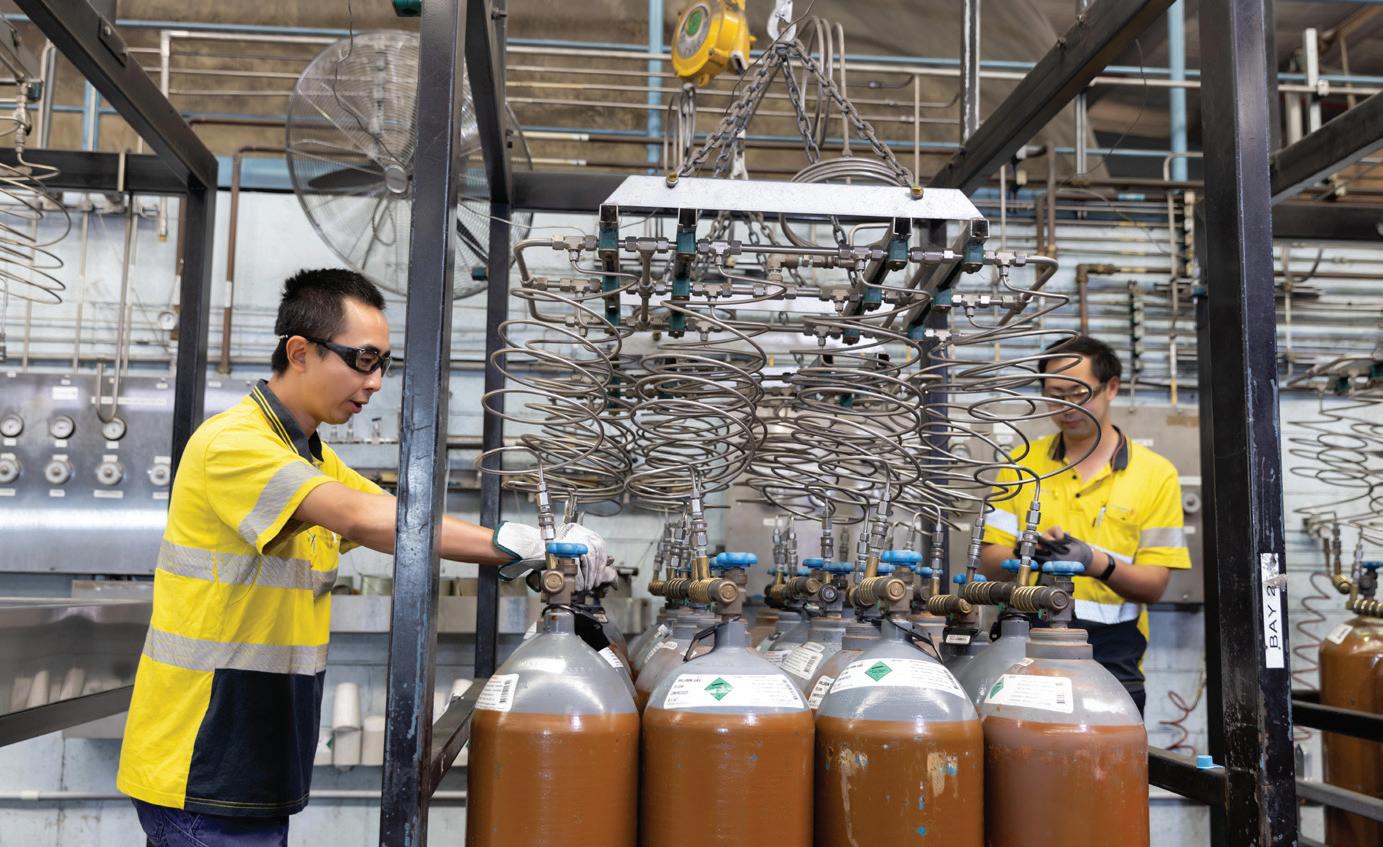
8 minute read
Specialty gas, Australian made for energy security
from AMT AUG/SEP 2022
by AMTIL
Mitigating supply risk in hydrocarbon processing for Australian companies.
Energy’s centrality to Australia’s economic growth is well recognised, and the importance of securing an uninterrupted energy supply vital for numerous local businesses where hydrocarbon processing is part of their supply chain. Examples of hydrocarbon processing are found in the compressed natural gas (CNG) and liquified natural gas (LNG) sectors. Specialty gases as utilised in the hydrocarbon process for safety, process control and compliance, have historically been imported into Australia, however, global supply chain issues are now affecting Australian companies that have traditionally relied on overseas suppliers. Steps to safeguard supply security include generating awareness of domestic specialty gas production to ensure a more energysecure future for Australian businesses. Coregas is the only Australian industrial gases company manufacturing locally and distributing specialty gases throughout Australia and New Zealand, including calibration gases, chemical gases, process gases, purging/inerting gases, electronic gases and instrumentation gases. “No other sector Coregas serves has such a diverse and precise range of requirements, and we have invested many years in developing our quality product range, certification, expertise and responsiveness to serve the needs of this industry,” said Alan Watkins, Executive General Manager at Coregas in Australia. Forecast to grow at a healthy compound annual growth rate (CAGR) of 5.9%, specialty gases are critical in Australia, being used in industries ranging from heavy industry and manufacturing, to healthcare and laboratories. “The global supply chain continues to be impacted by current devastating events and recovery from Covid-19 lockdowns. These world events are increasing global supply chain pressures with significant shipping delays, increased freight costs, forex fluctuations and shutdown of factories. Producer prices are also expected to soar and to flow onto the end consumer. Without access to specialty gases, businesses are being forced to stop operation as they are unable to calibrate and certify their plant equipment is operating correctly,” said Watkins. “As an Australian gas manufacturer which meets all Australian and globally recognised standards, Coregas can ensure supply of critical specialty gases with comparatively significantly less lead time compared to importing. For example, a 20-parts component hydrocarbon gas mixture can be produced within three weeks locally compared to three months from importing. It makes sense to support local Australian businesses.” Coregas supplies a range of specialty gases and related gas control equipment used in the hydrocarbon processing industry. Applications include high purity gases for laboratory analysers; ISO17034 accredited calibration gas mixtures for emissions monitoring and process control; bump test gases for gas detection safety equipment and high precision gas control equipment to deliver gases securely from the cylinder to point of use. Coregas’ pedigree in specialty gases for hydrocarbon processing applications is unrivalled in Australia. “The Coregas team has been Australia’s specialty gases experts for over 25 years. We have more than 100 years of accumulated experience in our team of NATA-approved signatories for our ISO17025 and ISO17034 accreditations,” says Watkins. In addition, Coregas’ sales and customer service teams both have experts dedicated to specialty gases who can assist with technical queries and offer product selection advice. It is this level of expertise, along with Coregas’ Australian made gases, speed of delivery, and package sizes that differentiates them from other suppliers. In other hydrocarbon processing applications such as crude oil refining, it is common to use liquid mixtures to calibrate analytical instrumentation. Coregas’ broad range of hydrocarbons can be used to produce liquid hydrocarbon mixtures in cylinders. The huge range of specialty gases that Coregas can offer to various hydrocarbon processing operations are, importantly, Australian-made. “We produce the gas components for many of them at our air separation unit located in Port Kembla,” said Watkins. “From those pure gases, we then fill a range of high purity gases or gas mixtures in cylinders in our advanced technology laboratory in Yennora. From this location, near Sydney, we transport the gas cylinders to locations across the country, and export to international markets.” In the environmental monitoring and analytical calibration market, speed of delivery is often as important as quality. Coregas has standardised certain high volume products to be made from stock and are available for despatch next day. Coregas has also tailored its production and ordering processes for calibration gases that are made to order to ensure conformance to customer bespoke requirements, to minimise the wait time for delivery. Package size is a critical, and often forgotten aspect of the specialty gas supply chain. “For the laboratory, a larger floor-standing calibration gas mixture (G size) cylinder will be preferred. This allows the technician to run as many tests as possible from a single cylinder,” said Watkins. “For in situ testing, users prefer portable cylinders. For these smaller packages we now find that there is market preference for high pressure refillable gas cylinders because they are much more environmentally sustainable than so-called ‘disposable’ cylinders.” The move towards buying locally has never been more important for Australian companies, as supply chain issues put critical capabilities at risk. Coregas has jumped at the challenge to meet the demands of Australian specialty gas users and actively encourages businesses to reduce the risks from future disruptions that are certain to occur, and mitigate global supply chain risks by buying Australian.
coregas.com.au
Pilot Air for Luna Park
Sydney’s Luna Park ride development team called on Pilot Air to upgrade its compressed air system.
When it comes to serious quality and reliability, Pilot Air has built a reputation that sees large operators turn to them for all their compressed air needs. The team at Sydney’s Luna Park ride development did just that when two of the big-ticket rides needed the supply, installation and commissioning of air compressor systems and pipework. Tendering began in February 2021 for a number of ride upgrades, and Pilot Air was engaged to create an air compressor system and air pipework solutions for two of the park’s most iconic and popular ride attractions. The team conducted a comprehensive site visit, undertaking a diagnostic discovery of the park’s Boomerang ride. As a feature ride with dynamic size to weight ratios and high-velocity execution, the complex air compressor system and air pipework needed to be intrinsically accurate with a robust system that would successfully perform under the stresses and demands of the ride’s platform. “Luna Park Sydney has a long and very successful relationship with Pilot Air. We have full faith in the air compressor systems supplied by Pilot Air, so when it came time for the large-scale ride development process at Luna Park Sydney, naturally we turned to them for their expertise and thorough understanding of our needs and the demands of our equipment,” said Chris Pierce, Maintenance Manager at Luna Park Sydney. Providing air compressor systems for heavy-duty needs
Armed with the technical specifications from the ride’s technical experts, Pilot Air supplied a 5.5Kw Rotary screw compressor with a 600L vertical air receiver and TFD 15 dryer. Additionally, the installation required all the associated pipework and fittings. Pilot Air created a customised plug-andplay air compressor system that met the demands of the project and delivered it within the tight scheduling constraints. Pilot Air followed the successful installation of the air compressor system for the Luna Park Boomerang ride with a larger and more complex installation for one of the park’s most popular and iconic rides – the famous Big Dipper. “These guys have an excellent reputation,” said Pierce. “They are very proactive in their preventative maintenance activities, which ensures minimal downtime. They provide clear information on the asset lifecycle and complete transparency on any new development and capital expenditure. Having this level of knowledge is critical to our asset planning and budgeting requirements.” The Big Dipper required a robust and powerful air compressor system. The team at Pilot Air customised a solution that not only filled the specifications but also solved a spatial and access problem. Due to the ride’s location within the site, they needed to supply a customised 37Kw variable speed rotary screw compressor with a 1000L verticle air receiver. Additionally, the system required the TFD72 Dryer and approximately 120m of pipework and fittings. The Big Dipper air compressor installation was a significant process that required a number of days. Complicating the installation was the delivery timeframe of the unit. Made in Italy, the customised system was overdue on delivery and Pilot Air was fast to act. “We installed a temporary solution for the park’s operator that could manage the demands of the Big Dipper until the unit arrived. The installation workaround created by the team was highly effective in solving a difficult problem and keeping the project on track. The team needed to work in collaboration with other trades and technicians who had been contracted to complete other works. The Pilot Air team was instrumental in assisting other contractors in fulfilling their obligations and the project showcased our teamwork skills and knowledge of complex installations,” said Tony Featherstone, National Sales Manager at Pilot Air. Pilot Air has been servicing industry and business for over 40 years. Many members of the team have been with the company for the best part of two or more decades. Delivering projects like this one for Luna Park are opportunities for Pilot Air and the team to showcase their experience and expertise in providing outstanding solutions for compressed air needs. “Pilot Air has the infrastructure to supply, install and commission air compressor assets, making them the subject matter experts in this space. Their service levels and communication strategies enable any installation to be handled seamlessly,” said Pierce. With air compressors through to compressed air storage, treatment and distribution, combined with our comprehensive spare parts inventory, Pilot Air will have what you require. If the standard compressed air products aren’t suitable, the crew offer custom-built solutions to meet individual requirements.
pilotair.com.au
