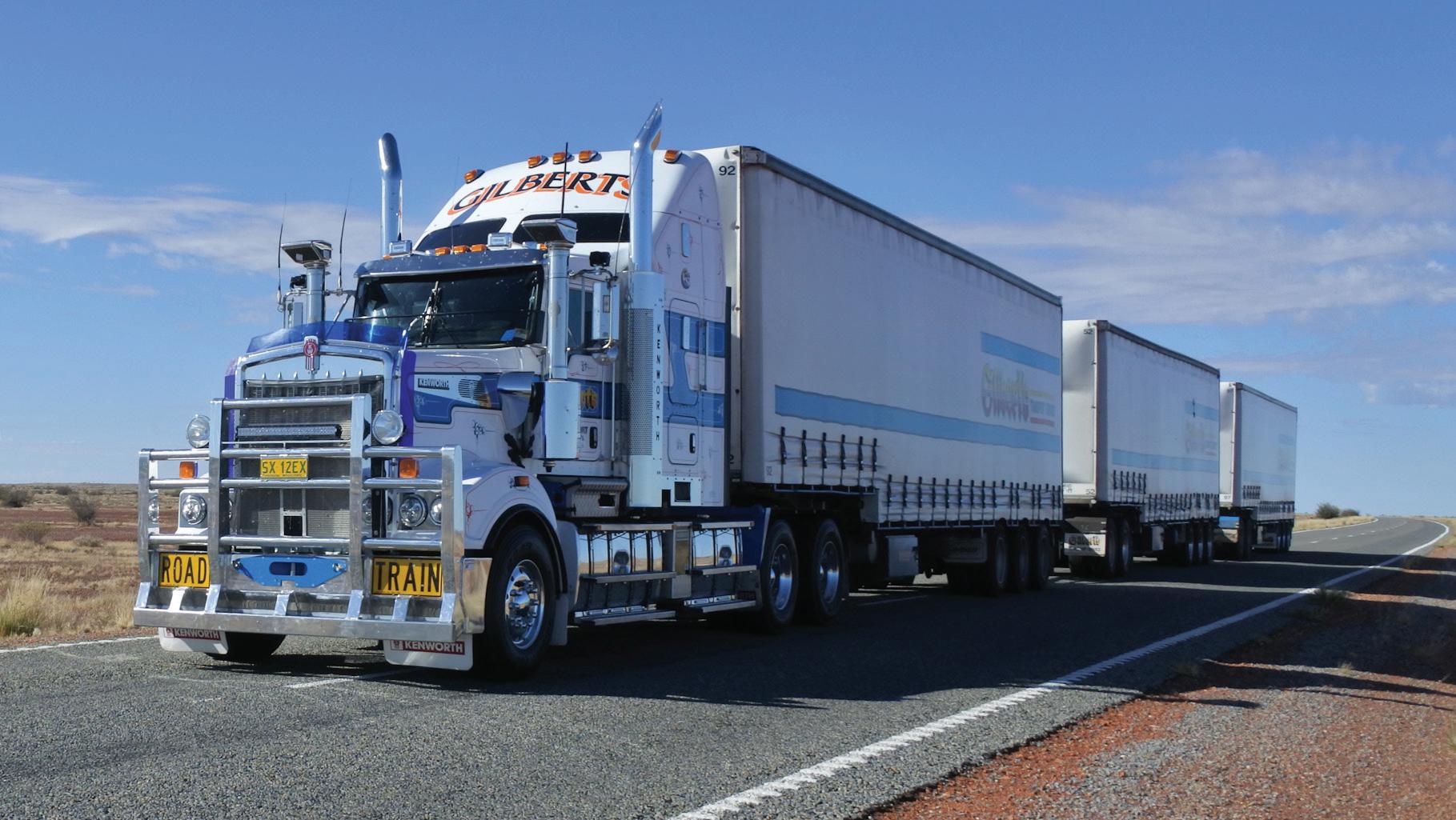
11 minute read
Air spring actuators and airbags
from AMT AUG/SEP 2022
by AMTIL
Air Springs supplier steps up to help break supply chain blockages and rocketing costs besetting mining, energy and heavy transport operations.
Crushers, conveyors, belt sweepers, vibratory equipment are areas where air springs are used in challenging applications where reliability and resistance to grime are critical. The same highly robust air springs go into the suspensions of big trucks working on the same mining, quarrying, materials handling, ports and energy sites. A company that has spent more than 40 years building up its national network to supply air springs used to process and transport goods is now helping industry avoid the need to expensively import urgently needed components as they wear out and need replacement. Air Springs Supply P/L supplies global quality brands of air spring actuators, isolators and air suspension components including Firestone Airride™ airbags used as OEM equipment by major truck manufacturers, as well as original and crossover replacement actuators and isolators for conveying and processing equipment. The company - which is Australia’s leading supplier of air springs for heavy transport and industrial use – has worked hand-inhand with industry over the past two years to help ensure supply in difficult times so Australian companies can maintain production in the face of surging container prices that have risen more than 500% in some cases. These rises and other costs have hit the mining, quarrying, transport, ports and bulk handling industry and their contractors hard - “For the first time, the cost of shipping a container on the world's busiest shipping routes, such as those from China to Europe, surpassed nearly $A14,000 over the last year, a rise of more than 500% on the year before,“ says Air Springs Supply Technical Product Manager James Maslin. “High demand for physical goods - thanks to government stimulus, easing of coronavirus travel restrictions, consumer demand from people staying at home and a global shortage of cargo containers - has increased congestion and delays at the world's ports and pushed up shipping costs to our customers. “This is the last thing our industry customers needed, because they have had it all in the last 12 months – COVID disruptions, labour shortages, road, rail and port bottlenecks, floods, climate disruption and international instability pushing up energy and transport costs,” says Maslin. Firestone air spring types, including rolling sleeve and convoluted models, left, and Air Springs Supply’s latest and expanded national headquarters in Sydney in which it invested to help ensure continuity of supply of OEM and replacement air springs. The company has a nationwide service, supply and technical backup network established more than 40 years. In response, Air Springs Supply has kept its supply lines open and operating as closely to normal as possible, even during the severest covid lockdowns and in the face of ensuring the best-available levels of its own stock from the US and Europe. Despite the ongoing issues, the company has benefitted from strong investment in reinforcing its coast-to-coast supply chains in recent years, including a national headquarters twice as big as previously in which it has built up inventories and supply chain resilience. OEM and crossover types
This in turn has benefited the company’s air springs supply network – the country’s biggest – in supplying the scores of types of actuators, isolators and airbags used throughout the industry for applications ranging from conveyors, crushers, vibratory equipment and processing plant, through to the Arride™ suspension isolators of a type that that are used to keep the country’s biggest trucks rolling safety down the highway. “Not only does Firestone technology naturally replace Firestone brand products in a wide range of OEM truck suspension and process machinery actuation and isolation equipment applications, but also premium quality Firestone parts often easily cross over with Goodyear, Conti, Rexroth, Norgren and similar components incorporated globally by other OEM manufacturers,” says Maslin. Firestone air springs also replace damaged or worn out traditional actuators for motion and fluid control applications that previously used pneumatic or hydraulic cylinders involving internal moving parts that can break or wear, particularly in grimy or wet environments. Air springs have no such internal moving parts. This product interchangeability helps companies adapt to changing circumstances without breaks in production - “We all need to be self-reliant in industry because we know a lot of the current problems aren’t going to go away tomorrow: virus outbreaks are something we have to learn to live with, climate change is an ongoing challenge and international political disruption is something we are all too aware of.” Maslin says simplicity is one of the many reasons why cost-efficient Firestone air springs, in individual load capacities from 40-40,000 kg, offer top reliability for fixed and mobile plant including: • Conveyors • Crushers • Processing plant • Belt scrapers • Lift tables • Vibrating packers and screens • Shaker tables • Solating technology • Heavy vehicle and work vehicle suspensions Maslin says that if heavy industry wants to improve uptime performance – while also solving noise pollution issues in busy grimy plant – Air Springs Supply offers easilyinstalled alternatives to brittle, breakable and noisy metal springs.
airsprings.com.au
Kaeser FBS 720: Next milestone
Kaeser recently expanded its FBS series of rotary screw blowers with the inclusion of the FBS 720 models.
The Kaeser FBS 720 represents the next milestone in the development of oil-free compression blower technology, designed especially with water industry applications in mind.With a flow rate of 18 to 72 m³/min and pressure differentials from 0.3 to 1.1 bar, as well as a selection of motors ranging from 45 to 110 kW, the innovative FBS series continues the success story of its smaller sibling, the EBS series, whilst setting new standards in terms of energy efficiency, space-saving design and automation. The SFC version is equipped with a frequency converter and a synchronous reluctance motor – a slip-free design that combines all the advantages of highefficiency permanent-magnet motors with those of robust, service-friendly asynchronous motors. Thanks to variable speed control, the flow rate can be adjusted as required and a control range of 1:4 is achieved, allowing exceptionally dynamic operation. The STC version is now equipped with an energy-saving IE4 Super Premium Efficiency motor, which reduces energy consumption and therefore costs, making the STC version more efficient than ever before. On both versions, power transmission from the motor to the airend takes place via lossfree and maintenance-free gearing, which results in an improvement of up to 7% in specific package input power as compared to the previous model. The complete machine achieves an efficiency range that represents the pinnacle of performance for this particular segment. In order to ensure that the specified performance figures are translated into reality, Kaeser guarantees performance in accordance with the strict tolerances of the ISO 1217-C/E standard. Furthermore, efficiency remains constant across the entire control range and flow rate is virtually unaffected by pressure fluctuations. This allows the blowers to be precisely regulated and adjusted at all times via the master control system, achieving even greater energy savings and ensuring seamless integration with other control technologies. Despite the compact dimensions of the FBS, Kaeser has succeeded in dispensing with the requirement for maintenance access from one side, thereby permitting side-by-side installation. This results in considerable space savings, particularly when operating multiple blower systems. FBS rotary screw blowers are delivered ready for immediate connection, including controller and frequency converter or stardelta starter. All units are CE and EMCcertified, thereby minimising the planning, construction, certification, documentation and commissioning costs for planners, operators and plant manufacturers. Last but not least, highly effective sound and pulsation damping ensure exceptionally quiet operation. kaeser.com The one stop online shop for engineering plastics Wide range of engineering plastics Free delivery nationwide for orders over $150.00+ gst 24 hour operations for live orders Best business to business pricing
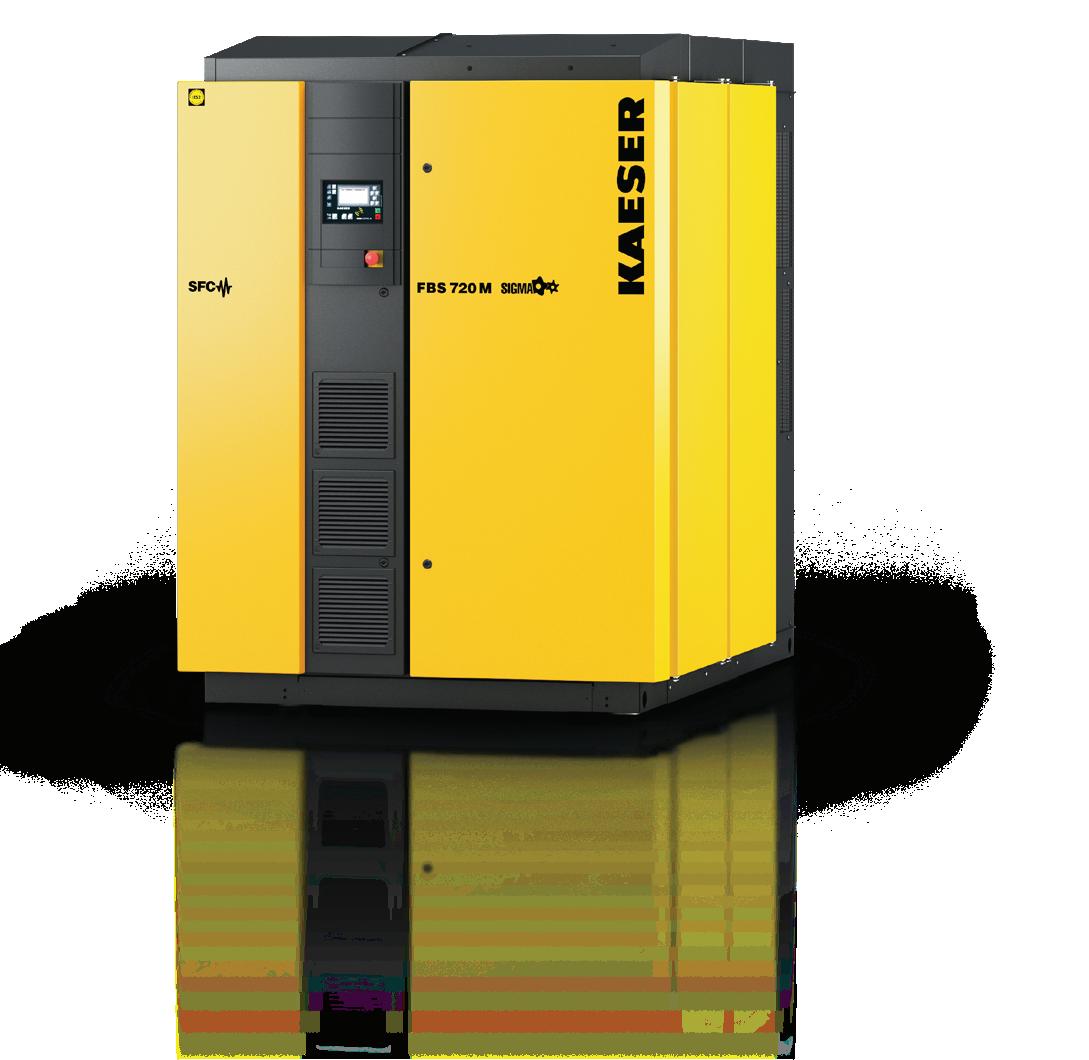
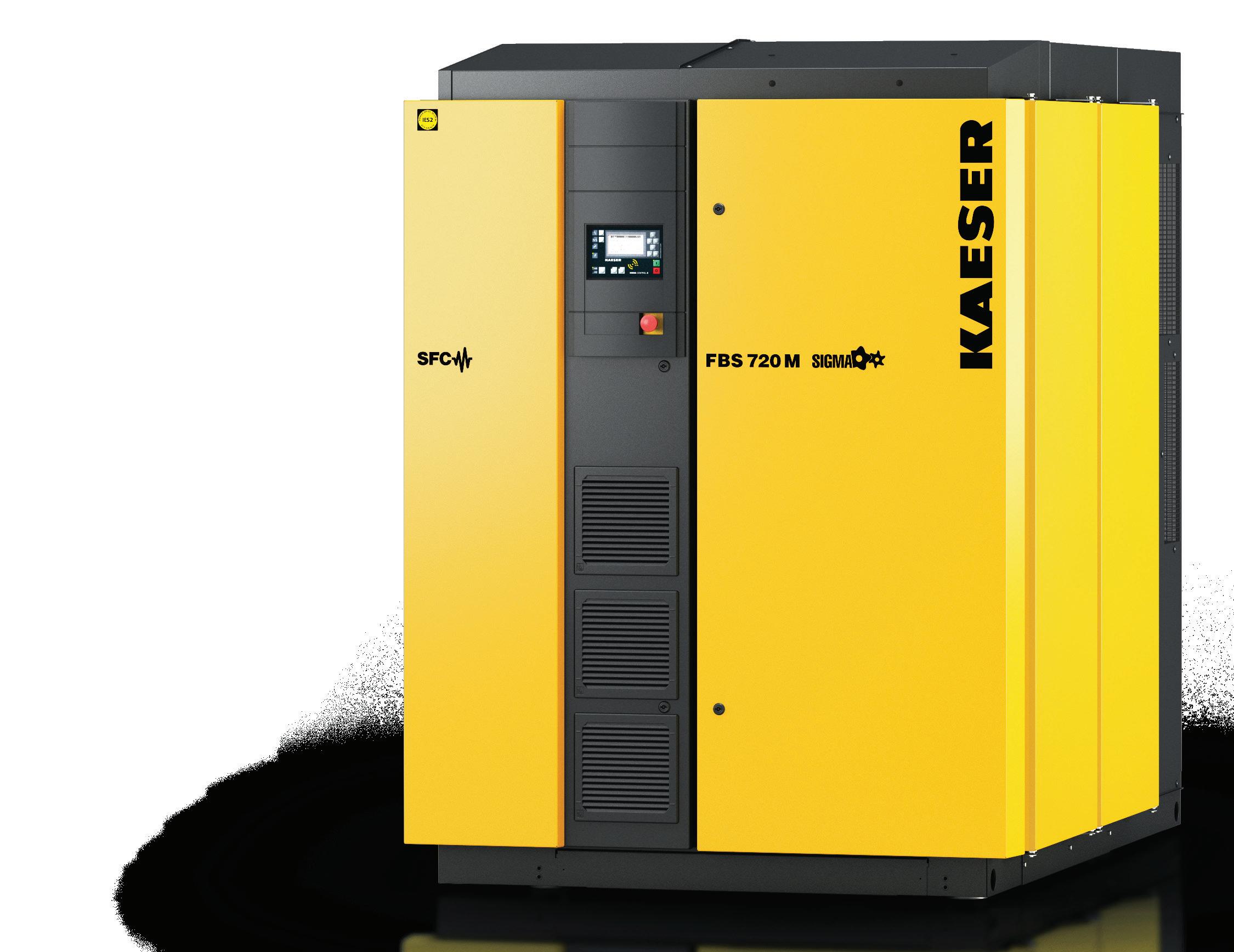

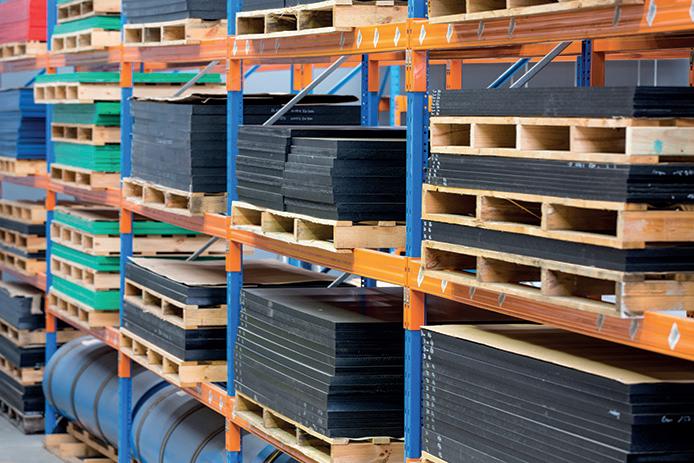
Acetal Cast nylon 6 HDPE PTFE UHMWPE Poly Carbonate – AR2 abrasion resistant 2 sides PEEK
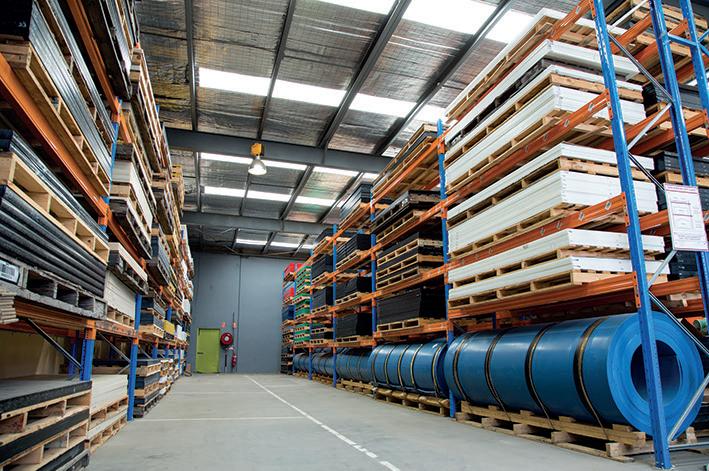
1800 215 216 www.epol.net.au
Product innovations for the future
Combined friction stir welding and machining processes, scalable manufacturing system for micro-technology and high-productivity twin-spindle machining – are just three of the new product innovations by the CHIRON Group that focus on productivity, efficiency and sustainability.
High dynamics and stability plus a large working chamber with a twin-spindle concept and a spindle distance up to 1,200mm – this is the 22, 25 and 28 Series from the CHIRON Group. Offered by ETG, the new machines are primed to set a new benchmark in terms of productivity and precision in this size range. In addition to double-spindle applications such as battery and e-motor housing manufacturing, these new series are also fully capable of massive machining applications starting with solid blocks. The extremely stable portal design forms the basis for high precision while the well-thought-out working area and user ergonomics enable flexible integration of a wide range of automation solutions for production process reliability. The CHIRON Group and ETG are now offering a ground-breaking manufacturing system for the microtechnology sector that provides high-precision automated machining of workpieces with maximum dimensions of 50 x 50 x 50mm. The combination of a Micro5 with a Feed5 handling system will form an ideal plug-and-play solution once it enters series production. Feed5 offers increased autonomy for automated workpiece handling with a six-axis robot. Capacities for Micro5 and Feed5 projects are currently being expanded.

Combining FSW and machining
One process that may not be particularly well known is Friction Stir Welding (FSW): reliable, efficient and sustainable manufacturing technology for creating pressure-tight and media-tight connections between two materials. FSW is fundamentally suitable for applications involving the joining of aluminium or unrelated materials. Friction stir welding technology also enables car manufacturers to relocate electrical modules to the wet areas of vehicles. The first CHIRON Group projects using this combination are already underway at a technology partner company, resulting in the first turnkey machining centres such as the MILL 2000 machining centre that offers combined FSW and milling technology.
chiron-group.com
Emission Statement
Australia submits new emissions target to UNFCCC.
The Australian Government has lodged an updated Nationally Determined Contribution (NDC) with the United Nations Framework Convention on Climate Change (UNFCCC) secretariat. This is part of Australia’s obligations under the Paris Agreement. The updated NDC commits Australia to a more ambitious 2030 target. We are going to reduce greenhouse gas emissions by 43% below 2005 levels by 2030, which is a 15% increase on Australia’s previous 2030 target. This also reaffirms Australia’s commitment to net zero emissions by 2050; it commits the government to providing an annual statement to parliament on progress towards these targets; restores Australia’s Climate Change Authority as a source of independent policy advice. It reflects the government’s resolve to urgently step up action and work alongside global partners to tackle the climate crisis. The government will implement new policies across the economy to drive the transition to net zero. This formalises Australia’s pledge to reduce greenhouse gas emissions by 43% below 2005 levels by 2030, and will put Australia on track to achieve net zero emissions by 2050. When Parliament resumes, the Government will seek to enshrine these targets in legislation, providing the certainty industry and investors have been seeking. This plan will create more than 604,000 jobs, most new jobs to be created in the regions, and will spur $76bn of investment. “Updating Australia’s 2030 emissions reduction target is a promise our Government made to the Australian people,” said the Prime Minister of Australia, Anthony Albanese. The Government’s comprehensive set of policies include: $20bn investment in Australia’s electricity grid to accelerate the decarbonisation of the grid; an additional $300m to deliver community batteries and solar banks across Australia; up to $3bn investment in the new National Reconstruction Fund to support renewables manufacturing and low emissions technologies; powering the Regions Fund to support the development of new clean energy industries and the decarbonisation priorities of existing industry; a further $100m to train 10,000 New Energy Apprentices in the jobs of the future; $10m New Energy Skills Program to provide additional training pathways; the introduction of declining emission baselines for Australia’s major emitters, under the existing Safeguard Mechanism. Also, Australia’s first National Electric Vehicle Strategy, to reduce emissions and accelerate the uptake of electric vehicle; doubling the existing investment in electric vehicle charging and establish hydrogen refuelling infrastructure – to $500m; the application of new standardised and internationally-aligned reporting requirements for climate risks and opportunities for large businesses; a commitment to reduce the emissions of Commonwealth Government agencies to net zero by 2030; restoring the role of the Climate Change Authority, while keeping decision-making and accountability with Government and introducing new annual Parliamentary reporting by the Minister; and a bid to host a future Conference of the Parties in Australia with an offer to Pacific partner countries to co-host. “The new target reflects my Government’s resolve to urgently step up the pace of action, and work alongside global partners and particularly with our Pacific family, to tackle the climate crisis and keep 1.5-degrees within reach,” the Prime Minister concluded. industry.gov.au
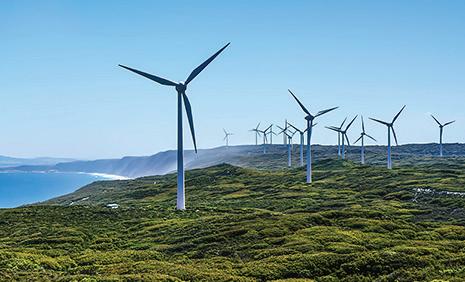