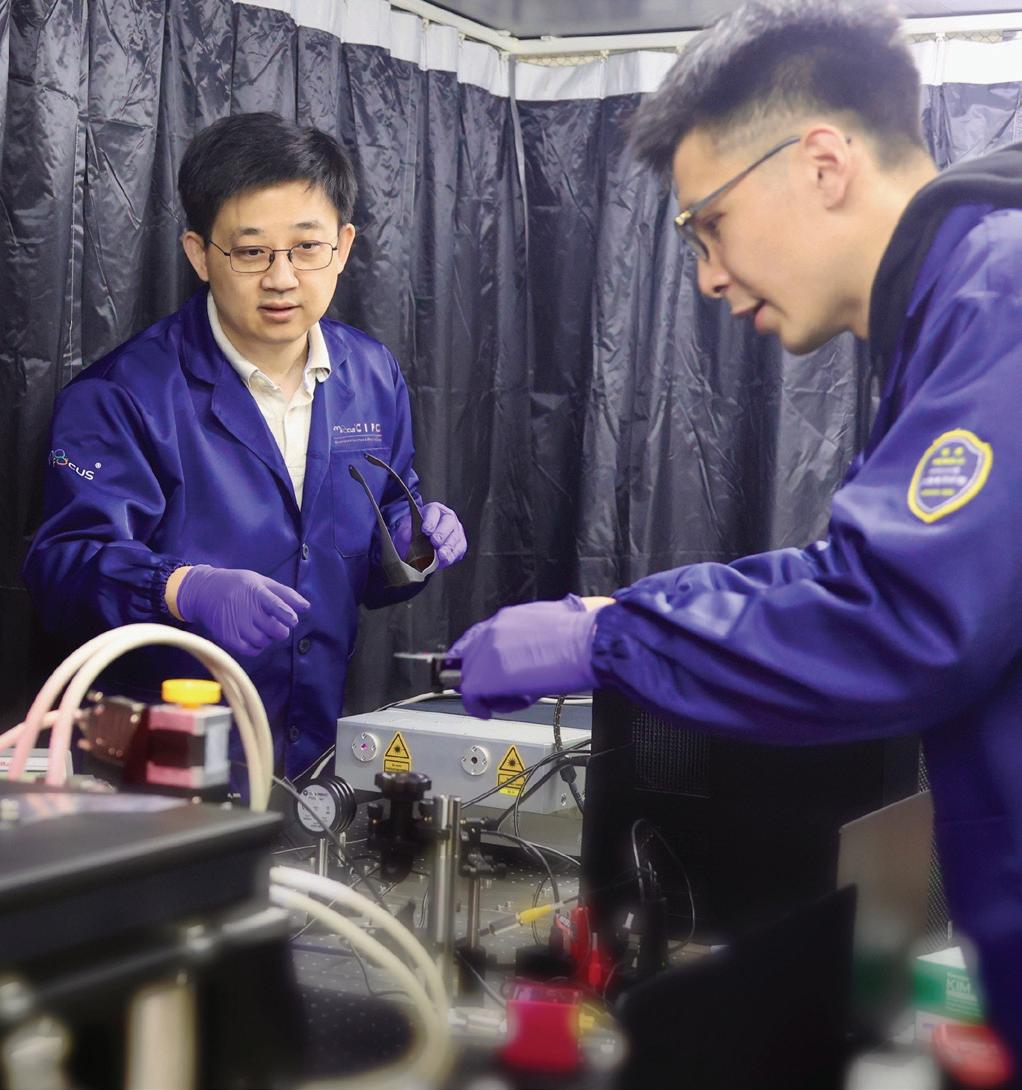
4 minute read
Nanofabrication system
from AMT AUG/SEP 2022
by AMTIL
Innofocus has created the world’s first intelligent 3D laser nano-fabrication system and services both academia and high end industry. Paul Hellard sifts through the tiny details.
Melbourne has another quiet achiever in nano-manufacturing. Researchers at Innofocus Photonics Technology have developed the world’s first 3D Insitu Refractive Index Characterisation System for Nano-fabrication, the world’s first Intelligent laser nano-manufacturing system, the world’s first fully encrypted nanocolourful digital ID tags system, and also the world’s first nanoprinted cooling film which runs without power. Frank Yao is the CEO of Innofocus Photonics Technology. As a cutting-edge technology company, Innofocus is committed to creating greater value for scientific research, green energy alternative solutions, advanced manufacturing transformation, and new material applications. The typical application domains Innofocus is in, include ultrathin flat lenses, digital colourful ID tags, nanophotonic devices, miniature micro-optical components, graphene photothermal materials and solutions. Building an entirely new area of photonic laser creatives, Innofocus prints in 3D at the nanoscale. Fabricating with complete IP rights and independent manufacturing capabilities in the fields of optics, photonics, electromechanics, optoelectronics and automated software systems. AMT spoke to Yao at the AMW show in Sydney. A lot of manufacturing in Australia is either very traditional big manufacturing projects, using laser to cut product or conduct additive manufacturing. But actually there's another area, and Yao likes to call it nanomanufacturing. “Nanomanufacturing really can shape a new foundation. I think Australia has this cool capability and we want to jump into this to be a leader in this area,” he said. The efficient fabrication technology developed and adopted by Innofocus can produce highly accurate, cost-effective and highly stable graphene films based on the principle of photo-reduction. This technology can develop broader prospects for scientific research in the fields of optical device fabrication, solar power thermal conversion, information encryption, sensing and optical communications and the development of new energy technologies. “We have a cross-disciplinary team with skills and experience in AI vision, machine learning, precision control, laser nanofabrication, opto-electronics, and photonics,” said Yao. “We’ve put all these technologies and engineering experience together and built a machine that can print miniature devices and new materials with nanoscale structures.” Now in the fifth year of running his company, Yao is visibly proud the team has more products launched. “With the several days of communication with customers, industry partners and government sectors here at the AMW show, we’ve found that people are starting to understand what nanofabrication is,” said Yao. “Now we can talk about why we need nanofabrication and how nanofabrication can change people’s daily lives.” Innofocus would like to push a new era of nanomanufacturing. When they used to talk about nanofabrication, people thought it was still in the laboratory. But now they have the technology and the enabling equipment, and fabrication is being done on a broad range of materials to create different applications, using this nanotechnology. “We would like to reinvent manufacturing with nanoscale precision to really kickstart a nanomanufacturing era,” stated Yao.
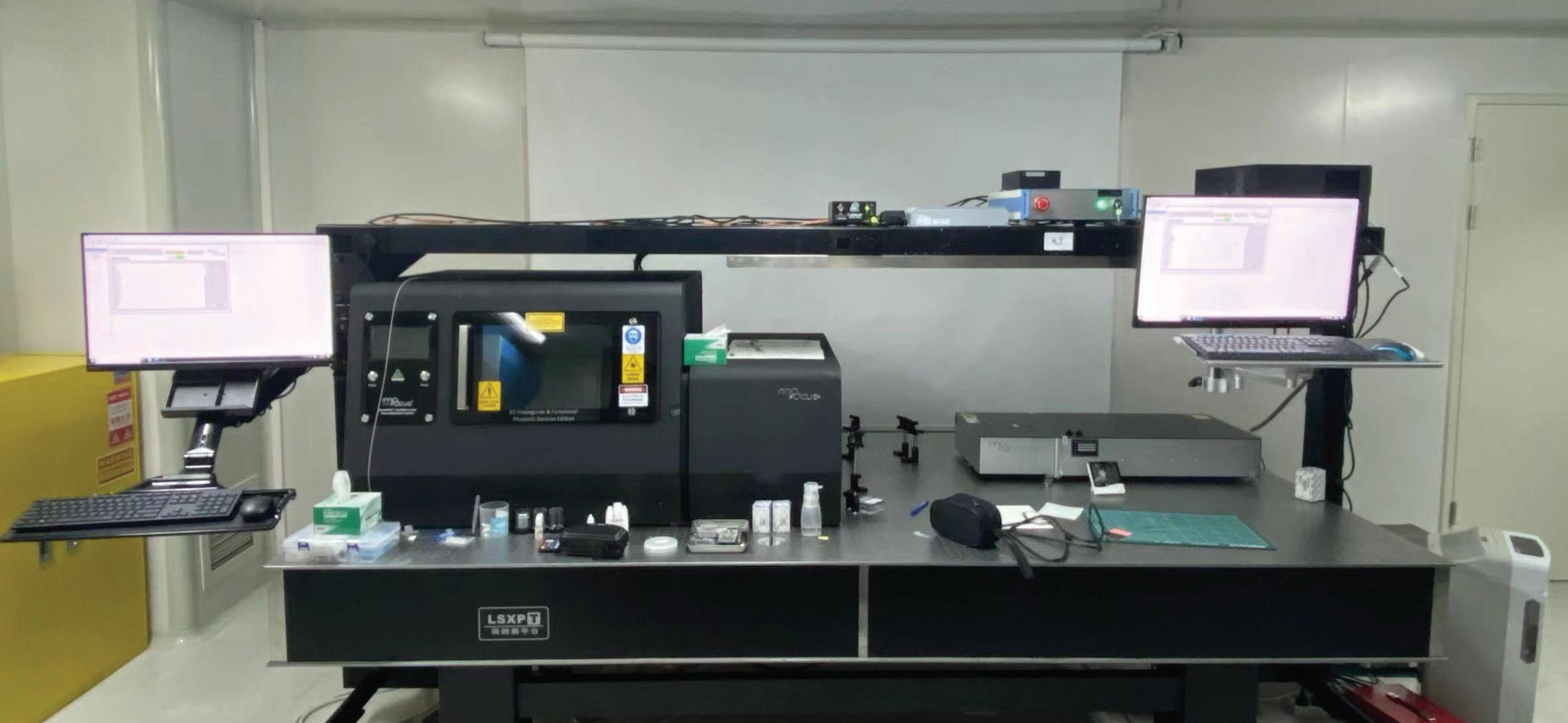
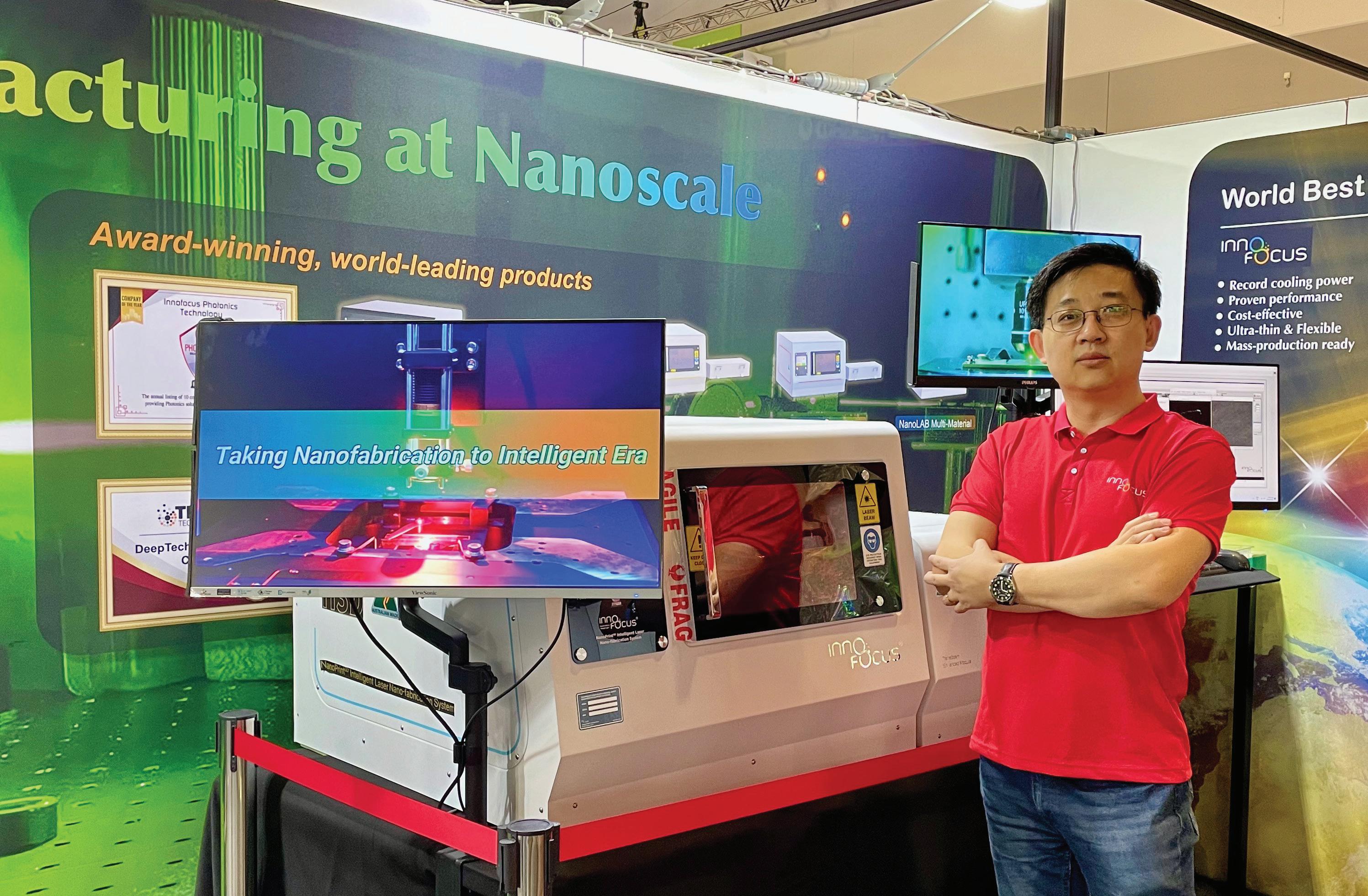
Cooling film
The difference between the other manufacturing capabilities and nanofabrication is that this is not reshaping the material. An entriely new material with different characteristics is being created. The process is introducing 2D and/or 3D nanostructures into a material like polymer, ceramic, glass, crystal, diamond and graphene. “The fundamental difference is we change the characteristics of the material,” Yao explained. “We are creating new materials and functions not achievable before.” The cooling film works without electricity consumption, because Innofocus has fabricated nanostructures in the film. So, it can continuously do what is called radiative cooling or passive cooling. The cooling film continuously emits heat from its surface. This material reflects more than 99.7% of the UV away (tested and certified by ARPANSA, Australian Radiation Protection and Nuclear Safety Agency (www.arpansa.gov.au/uv), and this generates sustainable cooling power 24/7 without using electricity. The cooling film cools down the object inside where it is wrapped. An example of its broad applications is perhaps on a truck or on sea freight containers, or an energy storage system, data centres, or like huge battery banks. The cooling film would always be cooling down the object inside and protecting the life cycle of the product inside. This will save energy. Another suggested example is a boarding bridge at an airport. That is a huge power consumption. Think about the energy used in refrigerated energy storage containers in the field. They have four large 15-kilowatt air conditioning units. Putting the cooling film onto them is not only saving energy. In a disaster location, the power may well be cut, but the film works all the time with no power. The power of this cooling film is an equivalent of 150 watts per square metre in specific environments, and will dynamically increase if the object to be cooled is working at a high temperature. “It is an entirely green manufacturing process,” adds Yao. “We are very proud to have the mass production ready for this cooling film in Australia. We are collaborating with many more industry partners to facilitate the application tests and formulating commercial solutions. As long as you can take the heat away from the surface, your product underneath will stay cool.” So many more applications, more materials can be made. The structures on the surface are incredibly small, they visually diffract white light into a rainbow. A demonstration of wearable cooling device they showed is a vest and a hat for using outdoor under the hot sun. While it can be used in many miniature devices, it can also create huge applications. Innofocus’ Nanoprint 3D Intelligent Laser Nanofabrication System is at the stage of developing the technology to now manufacturing products. innofocus.com.au
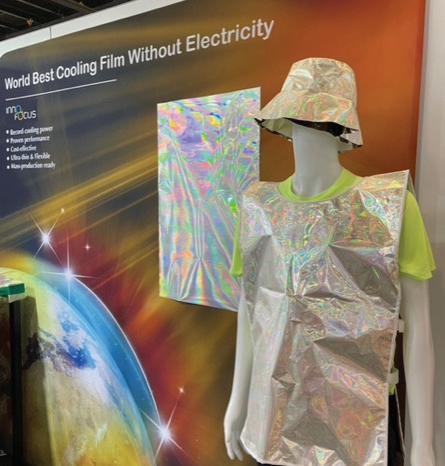