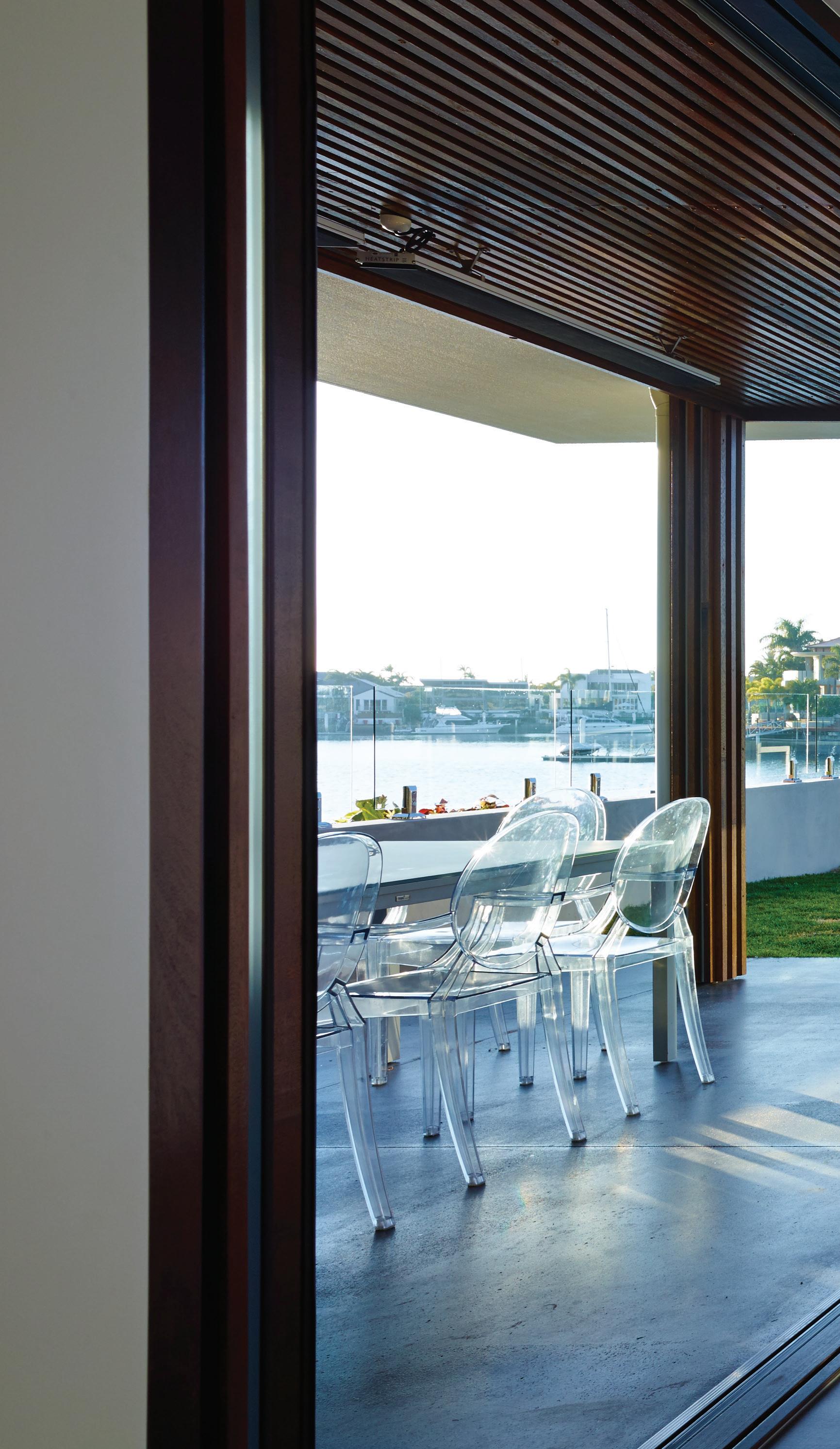
13 minute read
Markforged & Centor Global: A sliding door moment
from AMT AUG/SEP 2022
by AMTIL
Markforged and Centor Global excel in that sliding door moment
Centor Global Services creates doors and windows with precision engineering, while 3D printing the complex pieces in-house with Markforged 3D printers.
Centor Global Services is a Brisbane-based private company with a global reach. They manufacture high-end doors, screening systems and door hardware for the housing market world-wide. They manufacture their products at factories around the world, but when it comes to the technical components, they create them quickly on the Markforged 3D printers at a press of a button. Set among industrial roads, railways and overpasses, Centor’s office is an oasis in a lot of respects. Maybe it was quieter seventy years ago when the Centor office opened, but there is a respectable calm about the place when AMT visited just after the Sydney AMW show in June. Dave Chappell, Group Manager, Product and Engineering for Centor Global Services showed us through the facilities. Centor's in-house Product Design Centre is responsible for the design and testing of products available around the world. Centor were the first to come up with designs to make folding doors weatherproof and strong enough for external openings. “That was the mid-90s,” explains Chappell. “Ten years ago we set up distribution in the United Kingdom and a reseller in the US as well.” Centor now manufacture in Brisbane (Australia), Chicago (USA), Stryków (Poland) and Nanjing (China) and distribute products around the world. Centor knew that manufacturing the finest sliding door track would lead to a solid high-end market. They produce in-door screens and the hardware for the doors, with double- and triple-glazed windows. Markforged is a differentiated player in the advanced manufacturing sector and assisted Centor’s engineers and industrial designers to quickly come up with solutions. Initially, when Centor’s engineers wanted to accelerate innovation with R&D prototyping, they were stifled by lead time challenges. The lead times to make each prototype were simply too long, and there was never time to squeeze in enough iterations. They had to bite the bullet much earlier in the design process. But bringing in Markforged printers allowed them to modify prototypes and print new models overnight. Ever since, Centor has been able to arrive at the best design to bring to tooling — allowing them to make better products. When the COVID-19 pandemic started, Centor used additive manufacturing to battle supply chain challenges, with many parts they needed becoming difficult to procure. During this time, they expanded the number of parts they printed, branching out into 3D printing more composite and metal end-use parts than ever. As soon as they jumped into this hugely complex area, they stole a solid market. “We then embarked on a journey we called integrated doors,” says Chappell. “We’re Australian, we love design, we could do everything with eight-gauge wire, we could, pretty much, make 100% of everything. We asked our designers, what would a folding door be like, if you were given no constraints? No limits to the design and construction?” The resulting Centor hardware systems offer architects, and homeowners the innovative products they require. They combine durability and flexibility and from the feedback they receive, the doors continue to operate smoothly for decades. “The doors for the Australian market are designed here in Brisbane and with help from Markforged’s knowhow we are now investigating printing metal parts,” says Chappell. “In order to produce the more complex plastic parts, we of course turn to the Markforged 3D printers, inhouse, because we can just print them.” Centor makes these doors in Chinese factories for the Asian market, in Poland for the European market, and Illinois for the US and Canadian market. They have to make the doors where the customers are, to keep freight costs down. In the assembly line downstairs, the small team is putting together doors with impressive accuracy. There are parts of hinges, cogs, lefts, rights, jambless, doubles and combos, because the range is so heavily customised. The whole system of parts is generated depending on what features are required in the end product, and this is fed through a database when the final quote is provided. “To bring costs down, to accelerate the production speed, we listened to our jig operators down on the floor, here in Brisbane” says Chappell. “We started by generating tool holders and parts for the jigs from our new Markforged 3D printers.” Centor has four factories around the world, and the smart thing to do was to 3D print four times as many, and distribute around the world with a vision to have 3D printers in every factory in the future.
“A normal company would have to deal with five other companies to make these doors, but we do the lot,” he quips. “We’re still very much Australian, but that doesn’t mean we have to do everything here.” Centor aims at the top 5% of the residential market only. There are also many parts of the assembly line down here which have been 3D printed to streamline the construction and passage of the whole range of product that comes past. “Markforged 3D printers aren’t just good at creating parts of the doors,” Chappell explains. “The team get the designers to whip up modifications to the entire workshop.” With the Markforged printers in their office, ready to go, the designers can focus on high-value, end-use manufacturing applications, printed at the point of need. Markforged 3d Printers

When Centor introduced the Markforged 3D printers about nine years ago, it was like opening up the world to the designers. They now have three Composite 3D Printers in the design office. Instead of staring at a 2D plan, or a 3D model on a screen, they could ‘Just Print’. Simplicity of the workflow enables them to focus on the design. “They were a little tentative at first, because consumables cost a little bit, but the immediate payback was an acceleration and accuracy in idea generation. The Markforged 3D printers took no time at all to set up, and they are used a lot more than the paper printer which sits alongside,” says Chappell. “Because there are no constraints to what they can do, they just go for it.” The medium in the Markforged Onyx can be plastic or a carbon fibre-filled nylon, which are both applied from a continuous roll. The designers use the Markforged Digital Forge, the central digital inventory that holds designs that can be printed on demand at any location around the world. Eiger reinforces a work culture of innovation because barriers to testing and trying new designs are reduced. STL files are exported straight out of Solidworks and real-world parts can be ready for handling the morning after pressing the ‘Print’ button. Centor is investigating printing in metal with Markforged 3D printing but for the moment, they do all their plastic 3D printing in-house. Markforged offers real world applications in local manufacturing to overcome supply chain challenges, reduce manufacturing costs, speed up the time to market and increase innovation. Read more about the benefits of 3D Printing for manufacturers, and why now is the time for businesses to invest in additive manufacturing: centor.com markforged.com
FlexLoader M family brings the power of modularity to machine tending
Smart robotic machine tool tending cells with standardised modules offer expansion to meet changing future needs.
ABB has launched a new family of modular machine tending application cells for the metals industry aimed at maximising flexibility and machine utilisation while minimising lost productivity caused by unforeseen production stoppages. Featuring six different versions, the FlexLoader M family offers a variety of ways of loading and unloading machines based on the size, shapes and amount of the workpieces being handled, making it ideal for applications such as foundries and die casting operations producing multiple types of products in varying quantities. “As customers demand greater variety and shorter delivery times, metals producers need to have a manufacturing process that can respond quickly and offer the flexibility to achieve high mix, low volume and batch size one production,” says Andrea Cassoni, Managing Director for business line General Industry for ABB Robotics. “FlexLoader M is accelerating this move by providing a single unified machine tool tending platform offering the flexibility needed for handling a wide variety of production demands, whilst also improving productivity by eliminating the time, cost and disruption traditionally associated with production changes.” The launch starts with Tray and Conveyor variants, with further variants due for release over the coming months. The FlexLoader M Conveyor uses a simple but powerful vision system to enable easy loading of workpieces with complex shapes, providing the flexibility to handle a variety of workpieces with a single cell. The FlexLoader M Tray is a drawer solution offering easy machine tending. With a minimal footprint that allows it to be located almost anywhere, it is ideal for handling a variety of workpieces with variable shapes such as cubes, cylinders, plates and pipes. Featuring standardised interchangeable modules, the FlexLoader M offers a flexible and expandable solution for a wide variety of machine tending applications including lathes, mills, CNC and machining centres. A key benefit is the ability to use the same base machine, exchanging in and out feed modules as requirements change. The FlexLoader M’s modular approach makes upgrading and scaling up easy, with just one to two days needed on average for installation and commissioning. The FlexLoader M meets the demand from manufacturers for a simple automated solution that produces more workpieces in less time. The FlexLoader M robot cells are extremely user friendly and quick to program, even without specific robotics expertise. A smart wizard enables new workpieces to be programmed in less than five minutes with no vision programming expertise required, while changeover between pieces which are already programmed is possible in less than one minute, making “Batch Size One” production a reality. The simplicity of the programming software means that full operator training can be completed in less than half a day, further reducing the time needed to put the cell into operation. The FlexLoader M can reduce labour costs for machine tending processes by up to 90%, with one operator able to handle up to 10 cells simultaneously. The automated system delivers machine utilisation of over 97%, compared to 40-60% in manually operated machines. All the variants can be equipped with a vision system that identifies the workpiece’s position and gives commands to the robot, machine tools and other cell equipment such as air cleaning stations, part marking, deburring and measurement systems. The vision system can use either a 2D camera or 3D sensor depending on the application. The FlexLoader M also incorporates data-based optimisation features, including remote monitoring, enabling operators to monitor, troubleshoot and optimise their robot systems, while its vision software provides added functions including condition monitoring, fleet management and performance and order management. The FlexLoader M will replace ABB’s current family of FlexLoader cells, which have established a reputation for providing reliable and predictable output. Delivering benefits including higher machine tool utilisation and the opportunity for lights out production through unmanned operation, FlexLoader cells have proven their ability to deliver a much faster return on investment whilst giving users a sustainable competitive advantage.
new.abb.com/products/robotics/application-cells/flexloader

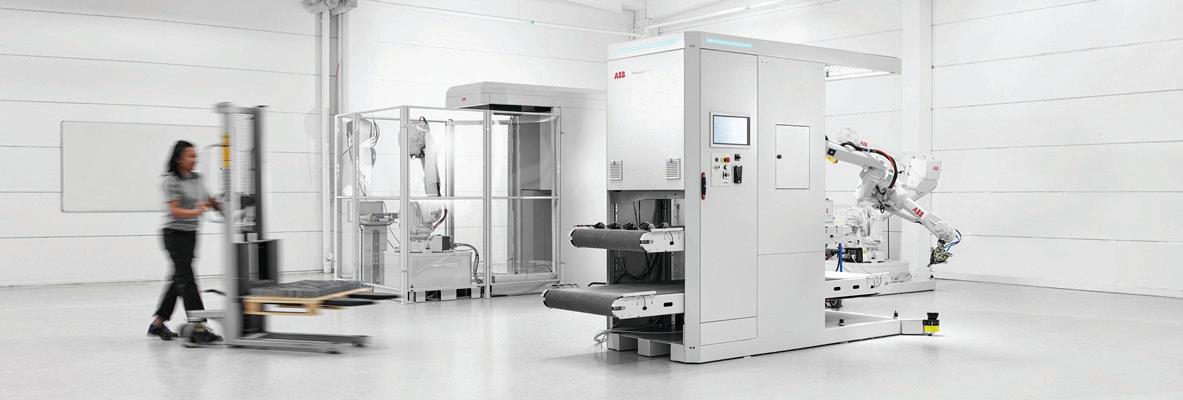
Plug-and-play conveyor
Interroll presents new plug-and-play conveyor platform for automated production environments.
With the new Light Conveyor Platform (LCP), Interroll is expanding its range of products with a platform-based material-flow solution that significantly increases the productivity of manufacturing processes. Designed as a plug-and-play modular system, the LCP allows all system integrators to implement scalable belt conveyor sections very easily in order to quickly meet customer-specific automation requirements for material flow. The high quality and availability of this solution is ensured by, among other things, the use of technical products that have already proven themselves hundreds of thousands of times with users worldwide. Efficient material feed and discharge play a crucial role in realising the productivity potential of manufacturing cells, assembly and packaging stations. At the same time, rapidly changing process environments in many other industries require flexible conveyor solutions that can easily adapt to new requirements. This is what the Interroll’s new material flow solution for system integrators and plant engineers achieves: Corresponding LCP-based belt conveyors can be easily assembled from factory-preassembled and predefined modules without any engineering effort, and can be put into operation quickly and safely via an autonomous machine control system, optionally without an additional programmable logic controller (PLC). Depending on customer requirements and application, however, connection to an external PLC with userspecific programming is also possible. Interroll's LCP is designed to transport smaller conveyed goods, as well as boxes or polybags weighing up to 50kgs. The conveyors, which can also handle inclines or declines, are driven by compact and energy-efficient drum motors that have an efficiency of over 85%, keeping energy consumption and energy costs very low. The fully modular system can be planned and assembled very easily and conveniently on the PC monitor using Interroll's popular Layouter tool. This drastically reduces project lead times and the necessary effort for system integrators. In addition, the predefined module sizes in different lengths and widths create the best conditions for fast production and delivery times.
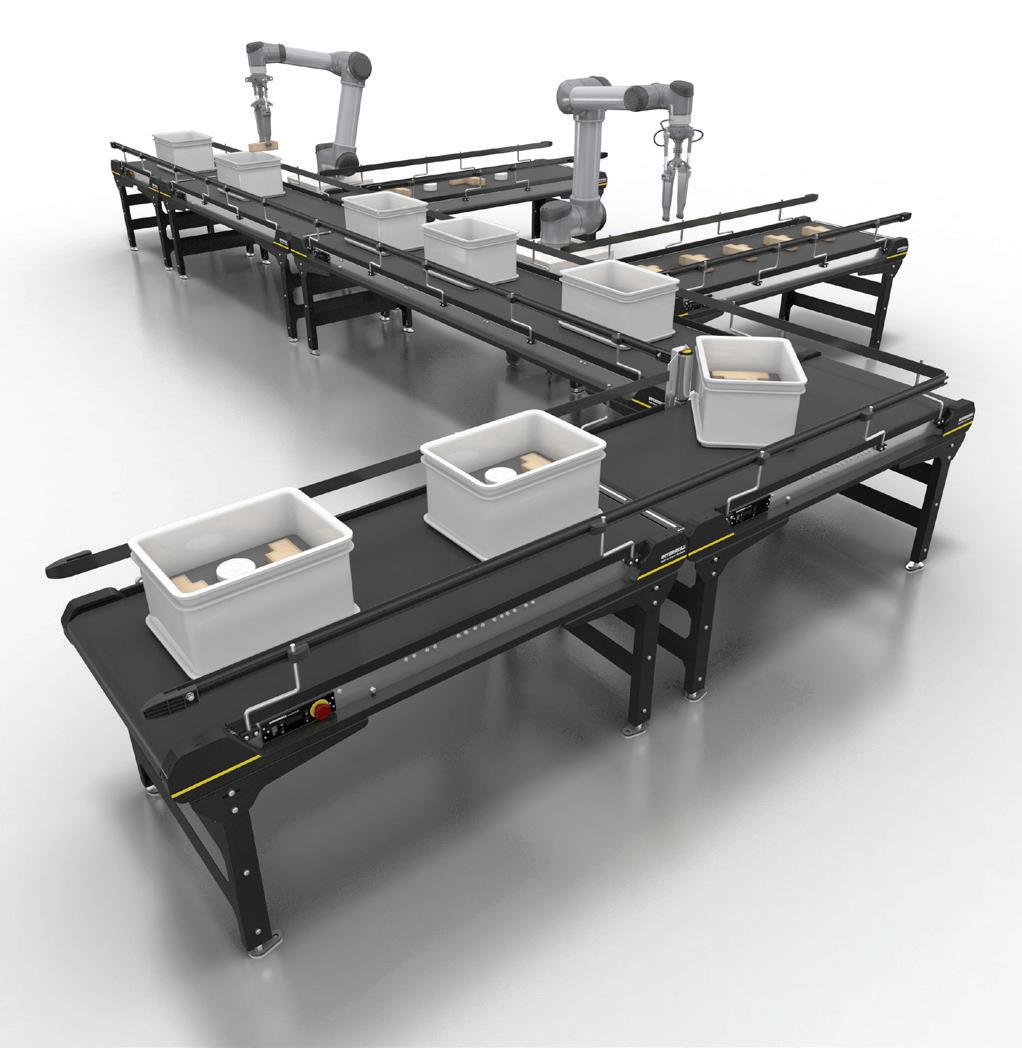
Interroll's LCP offers perfect conditions for decisively increasing the productivity of production cells as well as assembly and packaging stations through efficient material feed and discharge.
During the development of the new platform, great importance was also attached to maximum workplace safety and a pleasant working environment. The new LCP was extensively tested before market launch, subjected to extreme endurance and load tests, and developed according to Design for Manufacture and Assembly (DMFA) standards. It features an integrated emergency shutdown at the push of a button, complies with all relevant safety regulations and has a quiet noise level during operation.
interroll.com
New grades offer higher wear resistance and longer tool life, increasing productivity in cast iron and compacted graphite cast iron machining.
Kennametal has introduced the KCK20B and KCKP10 indexable milling grades for higher wear resistance and up to 30% longer tool life when machining cast iron and compacted graphite iron components. Both grades offer higher productivity and consistent, repeatable performance during roughing, semi-finishing, and finishing operations. Available for many indexable milling product lines, the new grades come with a golden top layer for fast, easy wear identification, ensuring maximum tool life for each cutting edge. “The new grades feature High-Power Impulse Magnetron Sputtering (High-PIMS) technology that provides a smoother insert surface and optimal layer adhesion for less flank wear – one of the leading causes of insert failure,” says Gil Getz, Product Manager, Kennametal. He notes that the new coating technology also increases cutting edge strength. “The result is high-performance milling in a broad range of cast iron alloys, including grey cast iron, ductile cast iron, and compacted graphite cast iron.” Flank wear comparison: KCK20B on the left and another grade on the right. Flank wear limits tool life when machining cast iron and compacted graphite cast iron. KCK20B and KCKP10 grades provide longer tool life, boosting productivity significantly. KCK20B and KCKP10 are suitable for wet or dry cuts. These include rotor hubs used in windmills, pump housings, steering knuckles and gear housings for heavy equipment, and automotive components like crankshafts and cylinder heads. While KCK20B delivers higher productivity in roughing and semi-finishing operations, KCKP10 is applicable for finishing operations, but also works exceptionally well when profiling and copy milling cast iron and steels up to 45HRC. “For customers where high tooling cost and downtime associated with tool changes are especially important, KCK20B and KCKP10 grades promise to increase tool life tremendously,” says Getz. “And for those who wish to increase throughput, the new grades deliver there as well. Either way, it is a win-win for any shop machining cast iron.” kennametal.com