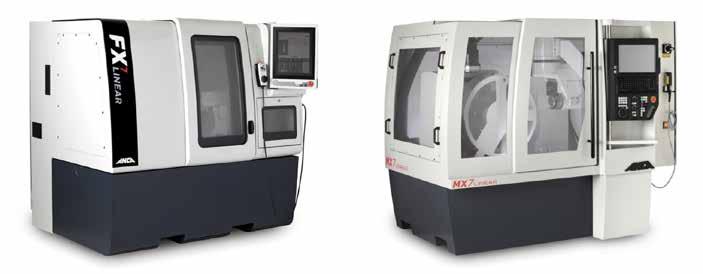
22 minute read
INDUSTRY NEWS
from AMT DEC/JAN 2023
by AMTIL
LinX Linear Motor
Superior performance machines powered by ANCA Motion’s LinX® Linear Motor.
ANCA Machine Tools has been servicing customers manufacturing precision cutting tools and components across a diverse range of industries around the globe, including automotive, aerospace, electronics and medical, for nearly 50 years. Founded by Pat Boland and Pat McCluskey 48 years ago in Melbourne, ANCA Motion Tools has grown into a truly global organisation with manufacturing sites and branch offices in all the major continents. Today, ANCA Machine Tools (hereafter referred to as AMT) is a market leader in quality CNC grinding machines. AMT’s success results from its continuous development of cutting-edge technology and a focus on innovation. Continuing in that tradition, AMT launched several new machines during the past eight years, aiming to strengthen the value proposition they offer customers. Significant inclusion to their range are the FX Linear and MX Linear machines. Both machines are powered by LinX® Linear Motor (International Patent Pending) developed by ANCA Motion, a sister company of AMT. Before FX Linear and MX Linear machines, AMT had been silent observers of linear motor technology for many years. “AMT was aware of the benefits that linear motors can bring. Over time the ball screws can wear even on the best machines, and you have to consider backlash and the loss of preload.” Simon Richardson, AMT MX platform product manager said, “When installing and aligning a ball screw on a machine, tighter tolerances are required over the entire length of the ball screw when compared to fitment of linear motors.” However, AMT has resisted using linear motors for quite a long time. “The traditional linear motor is flat in construction, which creates many issues when implementing these motors on machines,” said Philip Wysocki, the electrical systems engineer in AMT. “Machines with flatbed linear motors typically require a separate chiller for thermal stability, and the attractive force between coil and magnet bed creates tremendous downforces on the bearings, making everything wear faster and decreasing efficiency. In addition, flatbed style linear motors used in grinding machines typically have a backiron in their magnetic circuit, further increasing the downforces and creating cogging.” Until the arrival of breakthrough innovation, ANCA Motion’s cylindrical LinX Linear Motor, AMT believes that they saw a technology they felt confident to adopt into their tool grinding machines. LinX Linear Motor overcomes all the problems related to flatbed linear motor and delivers superior performance thanks to its state-of-art cylindrical design. ANCA Motion’s LinX Linear Motor consists of a shaft containing magnets and a forcer containing wound copper coils. The symmetric design results in zero attractive forces between the forcer and shaft, significantly reducing the loading requirement on support bearings. The thermal barrier design separates and removes heat from the motor, eradicating thermal growth for the machine. “Thanks to its excellent standalone thermal stability, AMT’s machines don’t require a dedicated chiller for the LinX Linear Motor. This is a huge advantage over competitors’ flatbed motorbased machines, significantly reducing the power usage and space occupation,” said Richardson. With LinX’s simple construction, non-critical air gap and no physical contact between shaft and forcer, machine manufacturers can significantly simplify installation, reduce maintenance and extend machine life. The LinX’s design allows it to replace ball screws in existing machines easily and makes the machine design process a lot smoother. “Due to its simple construction, the shaft ends will only require one or two supports depending on their orientation. Not only has the axis installation time been significantly reduced by more than 200% compared to ball screws, but the installation of LinX motors is much safer than flatbed linear motors,” Wysocki continued. The ironless design of ANCA Motion’s LinX Linear Motor and even force over the entire stroke bring out unprecedented motion performance, and because of its direct drive nature, the motor can track motion commands more accurately and repetitively to achieve a much better surface finish. With LinX linear motor, you don’t need to worry about cogging, backlash or reversal error. The tool’s surface finish ground by a LinX powered machine is significantly better than the result from a best-performance ball screw machine. You can see the tangible difference easily. This is just unbelievable when you are talking about microns! In addition to the improved surface finish, the LinX Linear Motor enhances the cycle time due to its higher acceleration and faster traverse speed. Overall, ANCA Motion’s innovative LinX Linear Motor provides improved performance at a lower cost and efficiency than ball screws and flatbed linear motors. The standalone thermal stability, high speed and acceleration, zero down forces and the ability to achieve IP67 protection make LinX an ideal solution for machine tools. After the launch of FX Linear and MX Linear machines, LinX powered machines have been installed in various regions worldwide. AMT customers are delighted with the performance of these machines. As a designer and manufacturer of flexible motion control systems, ANCA Motion will continue to deliver innovative products to support its customers’ ongoing success. motion.anca.com
Direct sound printing
New platform uses ultrasound waves to create complex and precise objects a potential game-changer in 3D printing.
Most 3D printing methods currently in use rely either on photo (light)- or thermo (heat)-activated reactions to achieve precise manipulation of polymers. The development of a new platform technology called direct sound printing (DSP), which uses soundwaves to produce new objects, may offer a third option. The process shows how focused ultrasound waves can be used to create sonochemical reactions in minuscule cavitation regions — essentially tiny bubbles. Extremes of temperature and pressure lasting trillionths of a second can generate pre-designed complex geometries that cannot be made with existing techniques. “Ultrasonic frequencies are already being used in destructive procedures like laser ablation of tissues and tumours. We wanted to use them to create something,” says Muthukumaran Packirisamy, a professor and Concordia Research Chair in the Department of Mechanical, Industrial and Aerospace Engineering at the Gina Cody School of Engineering and Computer Science. He is the paper’s corresponding author. Ultraprecise reactions
As the researchers explain, DSP relies on chemical reactions created by fluctuating pressure inside tiny bubbles suspended in a liquid polymer solution. “We found that if we use a certain type of ultrasound with a certain frequency and power, we can create very local, very focused chemically reactive regions,” Habibi says. “Basically, the bubbles can be used as reactors to drive chemical reactions to transform liquid resin into solids or semi-solids.” The reactions caused by ultrasound-wave-directed oscillation inside the micro-sized bubbles are intense, though they only last picoseconds. The temperature inside the cavity shoots up to around 15,000 Kelvin and pressure exceeds 1,000 bar (the Earth’s surface pressure at sea level is around one bar). The reaction time is so brief the surrounding material is not affected. The researchers experimented on a polymer used in additive manufacturing called polydimethylsiloxane (PDMS). They used a transducer to generate an ultrasonic field that passes through the build material’s shell and solidifies the targeted liquid resin and deposits it onto a platform or another previously solidified object. The transducer moves along a predetermined path, eventually creating the desired product pixel by pixel. The microstructure’s parameters can be manipulated by adjusting the duration of the ultrasound wave’s frequency and the viscosity of the material being used. Versatile and specific
The authors believe that DSP’s versatility will benefit industries that rely on highly specific and delicate equipment. The polymer PDMS, for instance, is widely used in the microfluidics industry, where manufacturers require controlled environments (cleanrooms) and sophisticated lithographic technique to create medical devices and biosensors. “We proved that we can print multiple materials, including polymers and ceramics,” Packirisamy says. “We are going to try polymermetal composites next, and eventually we want to get to printing metal using this method.” concordia.ca/ginacody
Replace awkward ballscrews with Lifgo innovative gear units and precision racks
When fast, precise and synchronised linear motion is required, our Lifgo rack and pinion gear units have proven to be reliable in many industry sectors around the world.
Smart and robust modular units offer designers the opportunity to tailor projects to meet unique needs at low cost. Lifgo enables rapid design and ease of system development for complex projects. Offers reliability and capabilities that transcend traditional product designs and boundaries, securing a competitive advantage.

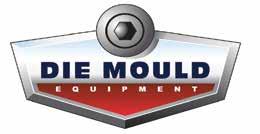
Lifting, Guiding and PositioningMaximising operational efficiencies and unlimited
combinations for various applications.
Industry sectors include: • Foodservice • Medical • Warehousing • Transportation • Forestry • Automotive

Ph 02 9987 2900 sales@diemouldequipment.com.au www.diemouldequipment.com.au
Beverage manufacturing
Major investment secures beverage manufacturing in South-East Queensland.
A $55m investment in an upgraded manufacturing site outside Ipswich will secure Asahi Beverages as a major manufacturing presence in South-East Queensland for the long-term. It brings Asahi’s investment in the beverages plant to around $100m in the past five years. The Asahi plant in Wulkuraka will now produce 300m litres of nonalcoholic beverages each year. Some of Queensland’s best-loved drinks including Schweppes, Solo and Pepsi Max are already made at the site. The new upgrade means other leading beverages will be produced there too including Cool Ridge water, Lipton Iced Tea and Pop Tops juice. The upgraded plant was officially opened by Mr Atsushi Katsuki, global President and CEO of Asahi Group Holdings, Mr Roland van Bommel, Chairman of Asahi Holdings Australia, and Mr Robert Iervasi, Asahi Beverages Group CEO. “Our $55 million investment has created a world-class Queensland manufacturing site,” Robert Iervasi, said. “It has also nearly doubled the sites annual production capacity to 300m litres. It shows Asahi Beverages’ confidence in the long-term future of manufacturing in Australia and in Queensland specifically. “Perhaps the upgrade’s most exciting part is the new hot-fill and blow-fill line, which will make Lipton Iced Tea and Pop Tops. The line’s innovative design means these drinks will be made without preservatives and using bottles inflated on-site from small pieces of preformed plastic. These are more sustainable than pre-inflated bottles because many more can be delivered to site per truckload – significantly reducing truck trips and carbon emissions. “This will help Asahi Beverages reach its sustainability goal of reducing Scope 3 carbon emissions across its entire supply chain by 30% by 2030. Asahi Beverages will also reduce carbon emissions in its operations by 50% by 2025.” The upgrade includes two new bottling lines and a 39-metre-high warehouse from where drinks are transported across Australia. The facility will operate 24/7. Premier Annastacia Palaszczuk welcomed the company’s vote of confidence in Queensland. “We are about promoting and providing good jobs, better services and the best lifestyle,” the Premier said. “This decision provides all of those things.” Mr Iervasi added: “This upgrade brings the number of quality fulltime manufacturing jobs at Wulkuraka to around 130, with more than a dozen new full-time jobs created. Our investment at the site to around $100m in the past five years. In addition to new jobs within the facility, more than 170 jobs were created during construction with dozens of Queensland companies involved. “We are unbelievably proud of this new facility, the many Asahi employees who made it happen and the jobs we provide in Wulkuraka and other parts of Queensland.” asahi.com.au
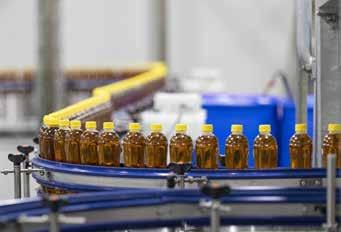
BOC Victoria
BOC to build carbon dioxide facility in Victoria, to produce more than 60,000T of liquid CO2 annually.
Leading gas and engineering company BOC, has announced it will build a multi-million dollar carbon dioxide processing facility in Longford, Victoria as part of a new long-term CO2 supply agreement with the Gippsland Basin Joint Venture. The new facility will have the capacity to produce more than 60,000 tonnes of beverage- grade liquid CO2 annually, making it the largest merchant CO2 production facility in the South Pacific. It will significantly increase long-term CO2 reliability and supply for many Australian industries. The Gippsland Basin Joint Venture is a 50/50 joint venture between Esso Australia Resources Pty Ltd (Esso) and Woodside Energy Pty Ltd. Under the agreement, the Gippsland Basin Joint Venture will capture and send CO2 from its Longford Gas Conditioning Plant directly to BOC’s new facility. John Evans, Managing Director of BOC South Pacific said the new facility would increase BOC’s capacity to supply the highest standard of carbon dioxide to customers in Australia and New Zealand. “BOC is building new infrastructure to ensure long-term supply security of an essential gas used in many industries including food processing and packaging, beverage, hospitality, desalination, medical, manufacturing and water treatment,” said Mr Evans. “This significant investment is part of our commitment to develop local supply partnerships and expand our production capability to meet the future needs of our customers and support growth across the South Pacific Region. “With the latest technologies and processes in quality control and efficiency, BOC’s new CO2 facility will exceed internationally recognised food and beverage standards.” Esso Australia Chairman Dylan Pugh said the agreement demonstrates how Esso is taking a leading role in decarbonising its operations while still providing products that are essential for everyday life. “Through this partnership with BOC, we will transform what is effectively a waste stream into a product of beneficial use for Australian businesses in the food, beverage, hospitality, manufacturing and medical industries,” said Mr Pugh. “Esso has a long history of providing reliable energy to Australia, whether it’s powering industry, heating our homes, or fuelling our barbecues, and this partnership will also see Gippsland put the fizz in our drinks.” Woodside Energy Executive Vice President Marketing and Trading Mark Abbotsford said the new agreement was a great example of how businesses can work together to improve societal and environmental outcomes. “Beyond providing energy to keep lights on and support industry, this is one of the many ways that Woodside Energy is collaborating to ensure the reliable and sustainable supply of essential products the community needs and enjoys,” said Mr Abbotsford. Scoping for the project is well underway with construction expected to commence in 2022, subject to regulatory approvals. Around 60 jobs will be created during the construction phase, with the facility expected to be operational in 2024. boc-limited.com.au
Muscle robots
Engineers develop a new class of smart textiles that can shape-shift, turning a two-dimensional material into 3D structures.
The team from UNSW Sydney’s Graduate School of Biomedical Engineering, and Tyree Foundation Institute of Health Engineering (Tyree iHealthE), led by Dr Thanh Nho Do, have produced a material which is constructed from tiny soft artificial ‘muscles’ – which are long silicon tubes filled with fluid which are manipulated to move via hydraulics. These artificial muscles, which are surrounded by a helical coil of traditional fibres, can be programmed to contract or expand into a variety of shapes depending on its initial structure. The research team, who published their latest findings in Scientific Reports and Soft Robotics journals said that the new smart textile could have a wide range of applications in many different fields. These potentially include use as a compression garment in medical and health scenarios, as a wearable assistive device for those needing help with movement, and even as shape-shifting soft robots which can aid the recovery of people trapped in confined spaces. Active fabric
The UNSW Medical Robotics Lab team’s smart textile can either be attached to existing passive material, or the artificial muscles can be inter-woven with traditional yarn to create an active fabric. “These ‘smart fluid textiles’ take the advantage of hydraulic pressure and add the fast response, lightweight, high flexibility and small size of soft artificial muscles. In effect, we have given our smart textiles the expansion and contraction ability in the exact same way as human muscle fibres,” said Scientia Senior Lecturer Dr Do. “Our smart textiles can be programmed to perform various desired motions and deformations such as shape-shifting structures from 2D to 3D. This material has significant benefits as it is made from miniature soft artificial muscles which offer a thin, flexible, and highly conformable structure.” The team suggests this material can be used to develop new medical compression devices. Low-profile devices which would lead to better medical outcomes. Patients with poor blood circulation could benefit from smart garments that contract to apply desired pressure to superficial veins and assist blood supply. “Athletes also use compression garments to recover at a faster rate and reduce muscle soreness after training, and our smart textile has potential to be utilised in that area. “We envision our material could be used to develop soft exoskeletons to enable people with disabilities to walk again or augment the human performance. “Most existing technologies in that field are still based around rigid robotic suits, but it is our hope that we could create a lightweight, soft exoskeleton that looks and feels just like leggings which can be worn like normal clothing. Soft robots
As well as wearable devices, the team - including PhD students at the UNSW Medical Robotics Lab including the study’s first author Phuoc Thien Phan and his collaborators, Scientia Professor Nigel Lovell, Head of the Graduate School of Biomedical Engineering and Director of Tyree iHealthE, and Dr Hoang-Phuong Phan from the School of Mechanical and Manufacturing Engineering - are also excited by the opportunity to develop so-called soft robots which can perform a range of useful tasks. “Traditional robots are effective when working in structured environments, but they are quite rigid and encounter problems dealing with unknown contexts of changing environments,” Phuoc Thien Phan said. “Normal robots cannot change their shape or start off as a twodimensional flat material to be able to access small spaces and then morph into a three-dimensional object Scientia Professor Nigel Lovell said: “Soft robots utilising our smart textile can shape shift and be implemented as a lifting mechanism, such as when rescuing people from collapsed buildings or other hazardous environments, or as a soft tubular gripper – in our experiments we could lift objects around 346 times the material’s own weight.” The UNSW team have a patent cooperation treaty (PCT) application around the new technology and is continuing to work on further developments, including the integration of a soft miniature pump and wireless communication modules which will enable an untethered system. Clinical validation is also ongoing with regards to smart compression garments, wearable assistive devices, and soft haptic interfaces. Dr Do has also received funding from the National Heart Foundation of Australia and the new smart textile has potential to assist in helping failing hearts pump blood around the body, especially if it can be automatically synchronised with the heartbeat to augment the cardiac function.
unsw.edu.au/engineering/our-schools/biomedical-engineering
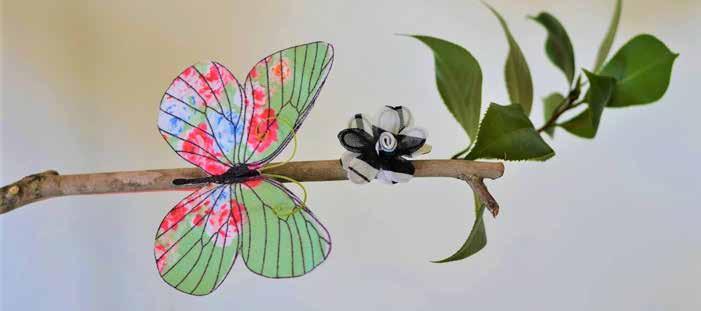
Ebusco home
Zero emissions bus manufacturer Ebusco makes Melbourne home.
Electric bus developer Ebusco has chosen Melbourne for its Asia Pacific operational headquarters creating new jobs and supporting the Andrews Labor Government’s Climate Change Strategy. Minister for Industry Support and Recovery Ben Carroll yesterday welcomed the company’s announcement at the launch of the Ebusco 2.2 battery electric bus for right hand drive markets including Australia, New Zealand and Japan. The Dutch company has been producing zero emissions buses since 2012, with more than 450 of its buses operating across seven European countries, including in major cities such as Amsterdam, Frankfurt and Munich. Although Ebusco’s production takes place overseas, the company is considering future manufacturing opportunities in Victoria and is currently working with Deakin University to develop composite materials and aerospace technologies to make its vehicles. As part of Victoria’s Bus Plan, all new buses from 2025 will be zero emission vehicles. To support this transition, the Labor Government has invested $20 million in a state-wide trial of zero emission buses. “Today marks an enormous step for our company as we launch our buses and services in the Australian marketplace,” said Ebusco CEO and Founder Peter Bijvelds. “Soon our buses will contribute to Australian cities reducing their transport emissions.” The Government’s Low-Carbon Manufacturing Grant Program will help Victorian manufacturers compete globally for renewable energy components, powering the state’s transition to net zero and creating new jobs. “Ebusco’s decision to set up its Asia-Pacific headquarters in Melbourne is a vote of confidence in our state’s nation-leading innovation and advanced manufacturing capabilities, as well as our leadership in cutting emissions,” said the Victorian Minister for Industry Support and Recovery Ben Carroll. Internships supported by the Government’s Digital Jobs for Manufacturing program will help train, support and prepare 300 Victorian workers transition to new jobs that will be created as part of the state’s push to net zero.
ebusco.com/au/
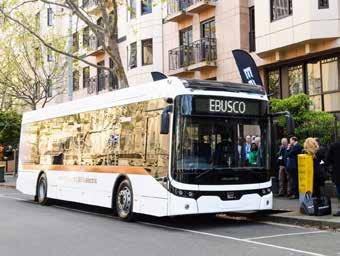
QLD Energy Plan
Queensland’s new Energy and Jobs Plan represents a great leap forward in delivering clean energy, thousands of jobs, and multimillion dollar economic opportunities for the Sunshine State, the Climate Council says. “Queensland has substantially raised its renewable energy target to 70% by 2032, with a $62bn investment in regional communities, good jobs and clean power for all Queenslanders. This is a big step forward for the Sunshine State,” Amanda McKenzie, CEO of the Climate Council said. “With its Energy Plan, Queensland has set itself up to cash in on the global transition away from polluting coal and gas, while bringing coal workers and regional communities along on the inevitable journey. It’s great to see that 95% of the $62bn spent on this plan will be invested in the regions. “This now puts Queensland ahead of the big states for their 2030 renewable energy targets. Queensland is now aiming for 60% by 2030, compared to Victoria which has pledged 50% by 2030 and New South Wales with no specific target. Queenslanders have already suffered enormously from climate change-fueled floods and fires. In fact, during the announcement, the Queensland Premier Annastacia Palaszczuk says the state is facing a ‘climate emergency’. Palaszczuk said her government was committing an extra $4bn to transform the state’s energy system and by 2030 there would be at least 2,000 more wind turbines and 35 million more solar panels in the state. “By 2035, there would be eight times more renewable energy generation than today,” she said. In a speech in Brisbane, Palaszczuk said: “It’s about changing the game. Action on climate change. Action on our economy. Action we can all take part in and action we can all be proud of. Queensland – it’s our time to shine.” “The great work Queensland has started today must be accelerated with a rapid replacement of coal and gas-fired power by clean, cheap renewables over this decade,” continued McKenzie. “There will also be no need for any new fossil fuel projects.” “The sense of momentum towards a clean future in Australia is inspiring. Every Australian state is now in a race to the front of the net zero emissions, clean energy pack. The further and faster states go on reducing emissions, investing in clean energy technologies like renewables, storage and energy efficiency and phasing out fossil fuels, the more benefits they’ll unlock,” said McKenzie.
qld.gov.au climatecouncil.org.au
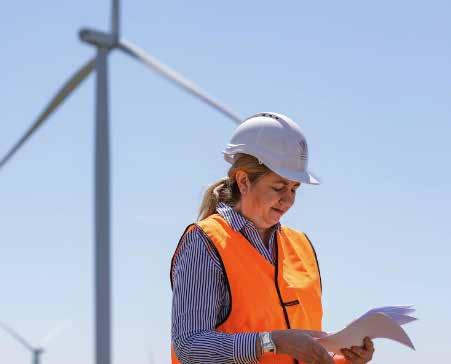
Monitoring biodiversity
DNA reference library a game-changer for environmental monitoring.
A new DNA reference library which is set to transform how Australia monitors biodiversity was announced today by CSIRO, Australia’s national science agency, along with the library’s first campaign which is supported by founding partner, Minderoo Foundation. The National Biodiversity DNA Library (NBDL) aims to create a complete collection of DNA reference sequences for all known Australian animal and plant species. Just like COVID wastewater testing, it will enable DNA detected in the environment to be assigned to the species to which it belongs. CSIRO Director of the NBDL Jenny Giles said environmental DNA (eDNA) analysis has the potential to create a revolution in biodiversity monitoring. “Monitoring biodiversity and detecting pests is extremely important, but it’s hard to do and is expensive in a country as large as Australia. eDNA surveys could change that by allowing us to detect animals, plants and other organisms from traces of DNA left behind in the environment, but only if we can reliably assign this DNA to species,” Dr Giles said. “People may be surprised to realise that there are tiny pieces of DNA shed by animals, plants, and other life forms left in the air, soil, and water around us. “eDNA surveys are increasingly being used to detect and monitor species, but only a tiny fraction of Australian species have sufficient reference data available to support this approach. This means most eDNA we collect can’t currently be assigned to a species. “Our National Biodiversity DNA Library aims to provide this missing data through an open access online portal, that will allow Australian state and federal governments, industry, researchers and citizen scientists to take full advantage of this powerful technique to describe and detect changes in our environment,” she said. Minderoo Foundation is partnering with CSIRO to fund the first part of this DNA reference library, focusing on all species of Australian marine vertebrates, including fishes, whales, dolphins, seals, turtles, sea snakes and inshore sea and aquatic birds. Minderoo Foundation Director of the OceanOmics program Steve Burnell said eDNA approaches will transform how we monitor marine biodiversity and help manage and conserve marine species. “The NBDL will help our program and other researchers to detect and map marine vertebrate species around Australia, improving the speed, scale and precision at which we can provide information to resource managers,” Dr Burnell said. “We’re proud to support this powerful conservation tool – the surveillance of marine ecosystems using eDNA provides an exciting and non-invasive means to measure biodiversity and monitor the health of our oceans.” Dr Giles said the library will be built using unique laboratory techniques developed by CSIRO. “This technology enables the large-scale generation of DNA reference sequences from preserved specimens of any organism. This miniaturised, high-throughput approach can unlock genetic information from the millions of scientific specimens preserved in Australian research collections,” she said. CSIRO will work with Bioplatforms Australia, enabled by the Commonwealth Government National Collaborative Research Infrastructure Strategy, and Australian natural history collections to rapidly increase the DNA reference sequences available for Australian marine vertebrates. These data will be generated from expertly identified specimens held in collections including CSIRO’s Australian National Fish Collection and Australian National Wildlife Collection. The NBDL collaboration between CSIRO, its partners, and our nation’s vast research collections will result in greater understanding of Australia’s animal and plant species and will support industries across fisheries, agriculture, environmental management and tourism. The library’s first online data release is expected to occur by early 2024.
csiro.au bioplatforms.com
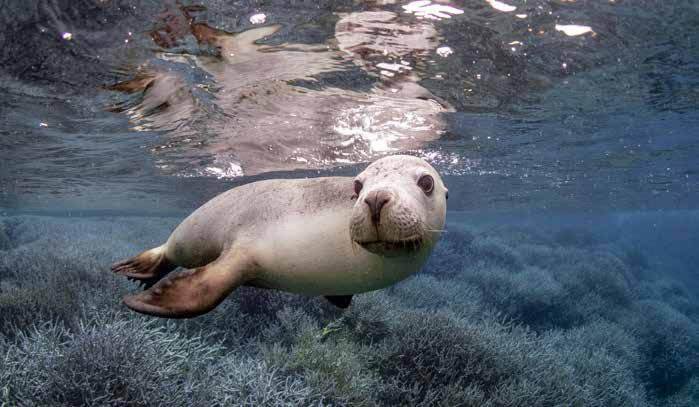