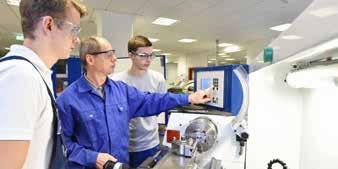
24 minute read
VOICEBOX
from AMT DEC/JAN 2023
by AMTIL
Will manufacturing get results from the Jobs and Skills Summit?
The ‘Jobs and Skills Summit’ will not deliver for the metals manufacturing industry. Coordinator for the Vernier Foundation, Jack Parr says what is needed is new thinking underpinning a radical plan.
Despite all the rhetoric about the importance of Manufacturing to our future economy, its needs were subsumed at the “Jobs and Skills Summit” by wider political interests. The Minister of Science and Industry seems to believe that the summit outcomes around skill shortages work on the basis of “one size fits all”, as manufacturing is not mentioned at all in his last AMT article. However, the summit outcomes on addressing skill shortages will do little for manufacturing, as this sector with its SME dominance, needs a specific plan; a message endorsed by Innes Willox of AIG in his AMT piece, “We need urgent and wholehearted action … on a pipeline of skilled workers for at least the next decade”. What were the summit outcomes and why will they not address manufacturing’s skill challenge? An increase in free TAFE places to boost education and training, an increase in short term skilled migration and the development, initially through an ‘Employment White Paper’, of an overarching roadmap to, “build a bigger, better trained and more productive workforce”. Unfortunately, while the TAFE increases will benefit other sectors of the economy; TAFE training, as it stands, is not a viable solution for advanced manufacturing and engineering skills. They cannot meet industry’s current needs in knowledge and resources, let alone the equipment and people to match the increasing pace of advanced manufacturing and accompanied automation. Some enlightened companies have had to establish their own ‘apprentice training facilities’ to negate this weakness. Relying on migration of those with advanced manufacturing skills is problematic because these skills are already in short supply and high demand in the global marketplace. The White Paper delivery is a year away and in typical political fashion, the terms of reference are so wide and all-embracing that the specific needs of manufacturing will be drowned again. While there are several inspirational companies, manufacturing, in terms of skills, productivity and innovation is now far behind other countries. It needs a focused, radical plan. A plan that will start to deliver world class innovative products and performance. A plan that starts with skills! The first action should be to make a real and substantial investment in STEM in schools. It was recognised in 2016 that STEM education in Australia, lagged many other developed countries, yet it was never funded or prioritised. Schools that prioritise STEM have to self-fund their teacher training and the necessary resources and find time in a too-crowded curriculum. What is needed is a massive injection of investment funds to accelerate STEM education. There are around 3,500 secondary level schools, both public and independent. To give each of these schools a $100,000 start-up grant would only cost $350m. The radical element is that it should be non-conditional. It must be a risk investment with minimum rules and bureaucratic approvals. With the proper industry involvement and guidance, the money could drive a massive acceleration of future skill sets. This acceleration could gain further momentum with industry providing additional expert advice to support the schools STEM teaching. Radical thinking is needed for more immediate solutions. Einstein said, “We cannot solve problems by using the same kind of thinking we used when we created them”. This is what is occurring in TAFEs and tertiary education. If companies sending trainees to TAFE is not a solution; let’s deliver the TAFE to the companies and develop a new type of learning program that delivers appropriate skills and qualifications. In June’s ‘AMT,’ AIG’s Megan Lilly complemented this concept. She argued that, “[Industry] Qualifications need to be able to be designed differently, combined differently and be accessible across contexts in many more ways.” She suggested this “questions funding models, the role of institutions and the relationship between learning and credentialling.” Lilly concluded this would involve a system of collaborative hubs – Centres of Vocational Excellence – with strategies to meet skill needs of all local employers. To make this happen, the manufacturing ‘community’ needs to be united. If they can no longer expect the government to deliver, then they must be prepared to do the lifting themselves. The individual skills, knowledge and expertise that sits with individual companies needs to be shared, such that all parties, companies, educators and representative bodies are collective, collaborative, and participative. A first step would be a pilot scheme where a small group of companies and an education provider, across a range of technologies and skills, form a ‘wheel and hub’ where trainees, both apprentice and mature, move through and across the companies with the qualification provider acting as the spokes and hub to oversee the needs of the current qualification, while also developing a new contextual qualification. Of course, this means the collaborative companies must be prepared to invest time and resources, for the good of the whole industry. The program would be steered by a small team from the collective with additional impartial guidance from other collegiate advisors. This could be an ideal way for advocacy organisations like AIG, ACCI, and locally SEMMA, SEBN and AMTIL to become more integrated and participative with the manufacturers themselves. There is a lot of rhetoric about the value of a strong manufacturing sector but there is a grave danger that while fighting all the current economic ‘alligators’, the government will neglect the real needs of the industry. Presented here are two radical and ambitious ideas; but as the Chinese proverb says, “the longest journey starts with the first step.” What is clear is something must radically change, and governments never take radical, risky steps! Therefore, the industry itself must do more and innovating our skills training model is achievable! It is radical, but without radical rethinking, how is Australia in ten years, going to become a real advanced manufacturing nation!
Jack Parr is the Coordinator for the Vernier Foundation, a charity aimed at funding and supporting STEM education in schools. The Foundation is the charitable arm of the Vernier Society, an organisation that for nearly 80 years has worked to support Victorian Manufacturing. vernier.org.au
Manufacturing Risk Watchlist
Navigating risks: what to look out for and how to respond. Andrew Curl, National Manager, Global & Corporate at Lockton Australia brings us up to speed.
Post COVID-19 lockdowns, the trading environment has presented significant challenges for manufacturers, exacerbated by labour shortages, global inflationary pressures and the Ukraine invasion. With local weather events, pressure on ports, shipping container shortages and rising energy costs, manufacturers are having to adapt to a new, volatile risk landscape. Lockton’s new Manufacturing Risk Watchlist tool helps the industry understand some of the top risks facing manufacturers today and highlights some of the impacts and responses to think about. 1. Employee risks
Organisations are struggling to recruit enough staff to operate at full capacity. This is creating real competition amongst employers. In addition to better pay and conditions, the most resilient organisations are re-focusing on ‘soft’ employee benefits to add to their attraction/retention strategy. For example, Lockton has seen an uptake in corporate funded private health insurance programs. • What employee benefits can you sponsor? 2. Supply chain risks
Notwithstanding embargos, global shipping and port capacity pressures, the global supply chain is more inter-connected than ever. As a result, manufacturers are increasingly susceptible to supply chain risks. Often, even a small failure in the chain (upstream or downstream) can have significant consequences on the ability to produce. The most resilient manufacturers have an increasing procurement risk focus across their supply chains, which includes a systematic process of supplier reviews, risk identification and risk treatment. • Will you have delays in alternative supplier sourcing? • Is there an increased risk of customer/supplier default? • Are Business Continuity Plans up-to-date? 3. Inflation risks
Numerous factors combine to create an inflationary environment that means insured replacement costs and re-build values are not keeping pace. Fuel prices, labour costs, transport & logistics costs and material price increases are just some issues. As a result, it is not uncommon for buildings insured values to require an uplift of >20% to accurately reflect re-build costs and importantly, avoid punitive insurance penalties for getting values wrong. Similar issues are impacting plant, machinery and equipment costs, with a flow on effect of increased lead times. This means that manufacturers might be paying 20% more for key equipment versus two years ago, with significantly extended delivery times. • Have you reviewed and validated insured values? • Have you reviewed supplier lead time on critical/key equipment? What do delays mean for profit/revenue? 4. Business Interruption Risks
Loss of profit and the additional costs incurred to continue trading following an insured property damage event remains a key risk concern for manufacturers. Inadequate Business Interruption Insurance (BI) cover following a property damage loss can have disastrous consequences for the ongoing viability of a business, particularly if customers go elsewhere, become comfortable with supply from your competitors and are difficult to get back. • Have you conducted a BI Review? • Have these exposures changed in the current trading environment?
5. Climate change risks
Recent weather events in Australia and the hurricanes affecting Florida are examples of an undeniable increase in Natural Catastrophe events linked to climate change. The global insurance and reinsurance markets face massive claims costs from these events. Recent estimates suggest the 2022 flooding on the East Coast alone is likely to cost insurers more than $6bn. As a result, insurers are responding by reducing their exposure through lower Nat Cat limits (storm, flood and cyclone), higher deductibles/ excesses and increased premiums. The most resilient businesses are identifying their exposure to these weather-related events and calculating exactly what the impact could be to the balance sheet. This leads to informed decision making, whether this is through traditional insurance products or alternative risk transfer solutions such as Parametric Insurance. • Do you know your actual exposure to natural catastrophe events? And have you considered alternative risk transfer solutions? 6. Reputational risks
Defective products, contaminated products and product recalls all carry significant risks including the cost of managing the events and the ongoing impact of reputational damage. Resilient organisations are responding by conducting reviews of their supply chain, which extends through to final delivery to customer. These reviews identify potential pinch points and lead to the development of robust disaster recovery plans. • Have you conducted a review/workshop to assess what happens in the event faulty/defective products are sold? 7. Technology Risks
The evolution of rapidly changing Operating Technology brings new risk exposures with significant insurance implications for the industry. Recent cyberattacks have highlighted the vulnerabilities of even the most high profile organisations. However, any organisation is at risk. Property insurance policies have traditionally excluded physical damage losses arising from cyber events. For manufacturers, this means significant coverage gaps and/or inadequate protection against these risks, resulting in physical damage and business interruption losses. • Have you reviewed your first and third-party cyber risks?
global.lockton.com/au/en
Getting the best of everything
Why and how should organisations adopt a hybrid IT strategy. Here, Martin Thunman, co-founder and CEO of Crosser, explores why and how organisations should implement a hybrid IT strategy.
Hybrid IT solutions are becoming a widely accepted essential for an organisation’s digital transformation. Despite its necessity, many organisations lack confidence in implementing a hybrid IT infrastructure successfully across on-premise, cloud, edge and software as a service (SaaS) settings. Digital transformation is no longer just a desire, but an absolute for organisations in all industries looking to improve their operational efficiency. A greater business need for data control, the cost effectiveness of cloud-based services, and a desire for greater flexibility have driven many organisations towards a hybrid IT infrastructure. But what does this involve? Defining hybrid
A hybrid IT infrastructure consists of a combination of cloud, edge and on-premise applications and data centres. A business’ enterprise systems and applications are deployed across any of these layers of infrastructure depending on which environment would yield the greatest performance and efficiency. Hybrid IT has emerged as a result of multifaceted technological development. According to Gartner, by 2025, over half of IT spending in application software, infrastructure software, business process services and system infrastructure will shift to cloud-based technologies. An ever-growing range of cloud-based applications means that even the smallest of organisations is likely to use some form of SaaS — be it for anything from sales to asset management or quality control. It’s important to not confuse hybrid IT with hybrid cloud, which exclusively blends private and public cloud services, but doesn’t include other elements like data centres or on-premise infrastructure. Hybrid IT doesn’t just relate to the infrastructure itself, it’s an entire strategy that encapsulates hybrid collaboration, user experience, device compatibility and data formatting. The best of all worlds
Adopting a hybrid IT infrastructure can bring a variety of benefits compared to an entirely cloud or entirely on-premise infrastructure. The key benefits of hybrid centre around the elevated integration and interoperability of the system. According to Mulesoft’s 2022 Connectivity Benchmark Report, some 88% of organisations said integration challenges continue to slow digital transformation initiatives, virtually unchanged from the 2021 report’s figure of 87%. So, while the situation hasn’t worsened, it certainly hasn’t improved. By adopting a hybrid IT strategy, it’s possible for organisations to avoid the complex task of migrating legacy systems and applications to their new cloud-based counterpart. It also creates a stable IT environment where cloud, edge, on-premise and data centre environments can be used in harmony, each for the use cases they’re optimal for. With remote working now taking a permanent seat at the table, it’s also worth considering if a company wants to adopt a bring your own device (BYOD) policy, and if so, how to make certain applications available on external devices. In each of these scenarios, a hybrid IT system is the enabler of successful deployment. Going hybrid-first
It’s possible to elevate hybrid IT infrastructure even further to unlock a more seamless digital transformation by adopting not just a hybrid, but a hybrid-first IT strategy. A comprehensive hybrid IT strategy doesn’t just facilitate interoperability and integration of different systems, but actually optimises the entire system by taking the benefits of each environment to maximise system efficiency and functionality. In contrast to just hybrid, a hybrid-first IT infrastructure doesn’t just involve piecing together different IT environments and hoping for the best, it’s about designing a comprehensive system specifically for hybrid use. By implementing a hybrid-first IT strategy, organisations can create a bespoke blend of IT infrastructure to suit their own priorities – be it efficiency, automation, cost savings, simplicity or overall user experience. By taking the benefits of each environment, businesses can create a system designed specifically for hybrid integration, unlocking the benefits of all IT options.
crosser.io
Automated farm equipment hits the mainstream
Automated farm equipment is no longer a theory, but becoming a competitive necessity. This means that the agricultural world is rapidly changing. Alan Girle, Special Counsel, Macpherson Kelley takes a look at the lay of the land.
That change, whether to partial automation or full driverless automation, is being facilitated by the six major tractor manufacturers operating in Australia, and it is not hard to identify the labour saving and productivity advantages of automation when you’re out working the land. But there are safety considerations. In the agricultural sector, occupational health and safety laws are set at a state and territory level. All states and territories other than Victoria have enacted legislation very similar to the model harmonised laws. Victoria has not adopted the harmonised model laws and has maintained its “Occupational Health and Safety Act 2004”. However, regardless of which legislation applies, the primary duty of employers follows the same general formula: A person conducting a business or undertaking must ensure, so far as is reasonably practicable, the health and safety of— (a) workers engaged, or caused to be engaged by the person; and (b) workers whose activities in carrying out work are influenced or directed by the person; while the workers are at work in the business or undertaking. The introduction of automated farm equipment does not change this primary duty and a breach attracts varying, but usually extremely high, maximum penalties. For example, in Victoria the maximum penalty exceeds $18M. In many states and territories, the offence of “industrial manslaughter” has also been introduced, and those offences also follow a consistent pattern: A person conducting a business or undertaking commits an offence if— (a) a worker— (i) dies in the course of carrying out work for the business or undertaking; or (ii) is injured in the course of carrying out work for the business or undertaking and later dies; and (b) the person’s conduct causes the death of the worker; and (c) the person is negligent about causing the death of the worker by the conduct. If the Courts find that a business entity or its officers were negligent, or that the safety measures put in place were not reasonably practicable, then the business and its officers will be in jeopardy. The use of automated farm equipment does not change this - industrial manslaughter provisions will still apply where fatalities occur as a result of automated equipment. Agriculture machinery at law
There are some specific legislative guides on agricultural machinery, but to date such guidance does not descend into issues surrounding automation. Putting aside the operation of driverless vehicles on public roads, the risks that agricultural businesses should be guarding against, include: • workers becoming entangled in the workings of the machinery; • workers being burnt by the machinery or injured by escaping high pressure hydraulic liquid; • workers being driven over or crushed by the machinery; • tractors rolling over; • tyre explosions; • workers falling from the machinery or objects falling off the machinery onto workers; and • malfunctions in the machinery, making the machinery operate in unusual ways. Guarding against these risks is a challenge and, unlike other businesses, agricultural businesses often have unpredictable factors like children, wildlife, livestock and fallen vegetation to contend with. Notwithstanding these factors, control measures that could be put in place include: • physical barriers both on the machine and for the location in which the machine operates; • deterrent barriers (e.g. electric fences); • proximity detection devices with automated shutdowns; • lockout systems to prevent unintended operation; • systems that allow the machine to fail in a safe way; • supervision; • regular mechanical, electrical and programming maintenance; and/or • administrative controls (e.g. telling workers to keep clear). Risk of machinery malfunctions
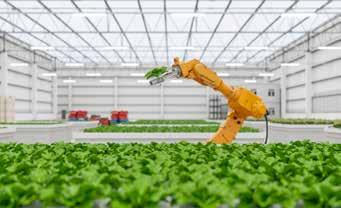
Recently, concern has arisen about malfunctions in the computerised processes behind the automation of farm equipment which could occur for a multitude of reasons. If malfunctions create a risk to humans, then there will be the potential for occupational health and safety regulators prosecuting. The regulators will look to see who was in control of the situation, who had the opportunity to prevent the incident and what action was taken to guard against the risk. Generally, the farm operator is likely to be looked at more closely than the supplier or manufacturer of the machinery. The regulator will ask whether the malfunction was foreseen, foreseeable and preventable. Where an incident does occur, businesses that react quickly to incidents, engage their lawyers immediately and take the actions of regulators very seriously, tend to weather regulatory intervention much better. Automated farm equipment is an inevitable part of the future, but it comes with unique risks. While in some respects the law does not change with automation, the changes in farming practices bring new risks, which must be managed in new ways. Businesses taking on new automated machinery should check in with their safety consultants and have a risk review conducted by their lawyers. mk.com.au
Journey tips the destination
It’s about the journey not the destination: Addressing the manufacturing industry’s customer support. Lindsay Brown, GoTo’s VP in the APJ region speaks about the trip.
Advancements in automation, AI and digital transformation has reshaped the way customers view the manufacturing industry. Customers are now holding the industry to a higher standard as they look for fast, personalised connections with businesses. As a result, the manufacturing industry has been forced to evolve – like many businesses today - to provide high quality customer support for this new heightened expectation. According to GoTo’s recent survey, many organisations are looking to improve the customer experience they provide as a key differentiator. 52% of ANZ organisations rated improving customer experience and ease of service as one of its top goals in the next 12 months. The top goal for organisations is shortening the time it takes to resolve a customer’s issue, with 56% highlighted improving the speed of problem resolution as their number one goal. For manufacturing organisations to successfully meet these goals, they need to ensure that their customer support technology is reliable, easily manageable, and rich in services, but equally, easily integrated into current operations. 38% of manufacturing organisations are investing new technologies to support growth as they look to digitally transform their business for the better and become more appealing to customers. One solution, endless connection for customers
Australia has highly skilled manufacturing capabilities that positions the nation to compete on value rather than on cost alone. The key is getting manufacturers to scale-up and to use the right technology to create value for their customers. Consolidating multiple legacy customer support systems and technology into one support solution can greatly assist manufacturers in achieving a strong connection with their customers and driving value in the customer engagement process. According to the same survey, 70% of organisations said they are very likely to consolidate their current technology stack within the next 12 months to reduce complexities of using multiple tools to resolve even the simplest of support tasks, with IT function responsible for managing these overlapping tools while leveraging only a fraction of their functionality. When consolidating to a single support solution, businesses are provided with a simplified solution where remote access, remote support, conversational ticketing, visual engagement and remote monitoring and management can be managed though one interface. 72% believe the simplicity and reduced technology sprawl will be beneficial for enhancing collaboration between different parts of the business, which can assist in connecting customers with the right experts quickly to maximise satisfaction and revenue generating opportunities. For example, although phone, email and on-site support will always be essential aspects of customer service, the use of chatbots to address real time questions can help manufacturing organisations sustain momentum in supporting the customer’s interactions with the organisation. The consolidation of support tools will also enhance and ease integration with customer relationship management (CRM) and other back-end technology. When manufacturers can easily manage all technology applications on one interface, they are able to quickly and effectively address their customer’s needs thereby decreasing resolution time. In doing so, manufacturers are able to streamline operations internally and externally for the customer. This improves their customer journey and helps them meet the heightened expectations. Customer expectations will continue to change, and as the manufacturing industry progresses further with digital transformation, customers will only expect greater benefits and flexibility from businesses. Consolidating to one support tool will allow manufacturing businesses to provide the best customer experience and achieve its customer goals. By understanding customers’ demands and employing the right tools and processes that ensures a customer feels heard, manufacturers will be able to deliver a better customer experience to attract new ones while retaining existing customers in the long run. goto.com
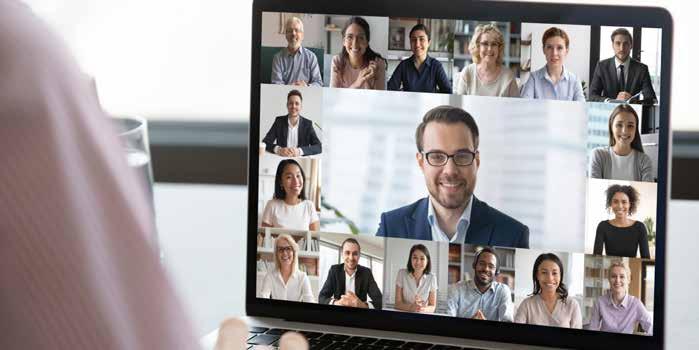
Mitigating The Domino Effect
Ever since COVID-19 wreaked havoc across the world, the global logistics industry has struggled to manage staff shortages. Frank Baldrighi, Business Development Manager at Getac ANZ talks about the effects and solutions.
Not only was the logistics industry forced to breaking point, so too were many of the industries relying on it. The problems faced by the logistics industry only compounded the problems already stifling the entire world’s supply chain, including the widely publicised shortage of semi-conductors vital for manufacturing everything from electric cars to mobile phones. To complicate this further, as global lockdowns were lifted, consumers wanted to spend the money saved during their time locked indoors, which meant demand for logistics services increased dramatically. Shortages soon began to appear in almost every major industry including food, leading to critical supply issues and rapidly increasing prices. The blockage which closed the Suez Canal for only the fifth time in its history only exacerbated the problems. All of these challenges have forced the industry to reassess how it operates on a daily basis and attempt to find efficiencies wherever possible. One area is the digitisation of infrastructure. Time is the crucial element in the supply chain. Without products being delivered on time a domino effect is often set in motion. Products along the supply chain can be further delayed exponentially when one small piece of the network falls out of sequence. This can include delays at ports, trucks breaking down, rail freight affected by weather or even warehouses missing deliveries through administrative errors. Many of these issues are caused by pen and paper forms being misplaced, mis-read or data being incorrectly recorded. Unfortunately, regardless of how hard we work and how efficient we aim to be, human beings are not as well versed at monotonous tasks as machines. Take for example the Ever-Given Suez crisis. A combination of a few untimely errors led to billions of dollars of freight getting stuck and a further few billions more behind – all going nowhere. The blockage to the Suez Canal meant that $9bn of trade was disrupted every day. Whilst the ensuing delays and backlogs caused by such an unprecedented event could not have been prevented by computers, having the right technology to hand could have reduced the impact on day to day operations. The benefit of digitisation is the centralisation of paper work and documentation. In a multinational port or transport hub such as Amsterdam or Heathrow, operators using pen and paper must record consignment details and then pass that single piece of paper up the chain until it eventually, through many iterations, reaches the consignee as a Bill of Lading. That means thousands of slips of paper passing through multiple hands every minute of every day. Similar to the age-old game of Chinese whispers, as paper is passed from hand to hand, illegible handwriting, a rainy-day causing ink to run or even paper getting torn can cause information to be distorted or lost. With digital systems, the port-side operator inputs data into a tablet which is then centrally stored for anyone with authorisation to access at any time. More importantly, it can provide real-time data at any point along the journey. For the haulier, it provides real insight as to where the supply chain is faltering, and they can quickly adjust their processes to make sure their teams have the right tools to reduce cargo loss, improve delivery times and, in a crisis, adjust delivery timelines. This means they can keep customers in the know at all times, as well as reducing costs associated with waste. Overall, this helps minimize stress at all points along the supply chain, including the operators on the docks or at the ports, who over the past year have no doubt felt the weight of the world on their shoulders. What the future holds
As the industry comes full circle and recovers from the crisis of 2021/2022, businesses will begin to reassess the tools at their disposal, and no doubt invest in new technology to ensure future losses, delays and unnecessary costs are limited as much as possible. One area for future development is Artificial Intelligence (AI) which is already transforming many industries. AI will allow the transport and logistics industry to not only reduce delays and lost cargo, but improve efficiencies and workforce management. It will enable cargo and freight businesses to assign high-priority or high-risk cargo to specific individuals who have the necessary training and skillset. It will also be able to keep customers updated automatically ensuring promise times are always accurate. Additionally, the software will enable other processes to be improved such as warehouse workers updating truck drivers in real-time about delays or cancellations in the receipt of goods on-site, meaning less time and fuel are wasted. All of these, simple, yet intricate tasks will be improved through AI. Hauliers all over the world can improve systems at every point in the supply chain, so the next time a link fails, whether it be at port, in the cab of a truck or at the point of final delivery, the domino effect can be avoided. In truth, AI will revitalise an industry that’s been pushed to the brink over the past few years and provide it with the opportunity to not only recover but to reinvent itself.
getac.com/en/industries/transport-logistics/
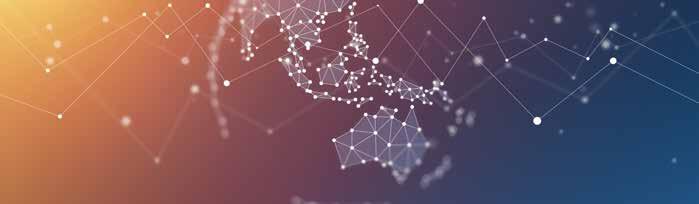