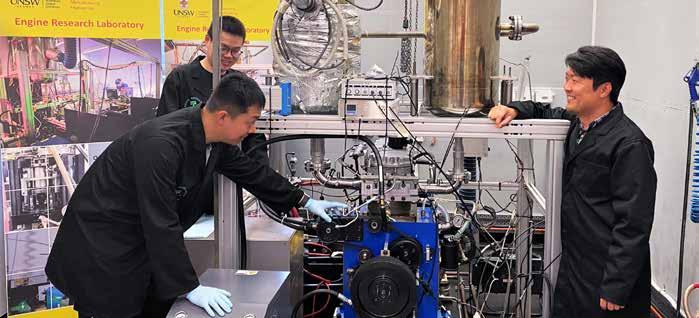
7 minute read
UNSW on Hydrogen
from AMT DEC/JAN 2023
by AMTIL
Retrofitted diesel engines run on hydrogen
Team from UNSW Engine Research Laboratory develop new Hydrogen-Diesel Direct Injection Dual-Fuel System that significantly cuts carbon emissions.
Engineers from UNSW Sydney have successfully converted a diesel engine to run as a hydrogen-diesel hybrid engine – reducing CO2 emissions by more than 85% in the process. The team, led by Professor Shawn Kook from the School of Mechanical and Manufacturing Engineering, spent around 18-months developing the Hydrogen-Diesel Direct Injection DualFuel System that means existing diesel engines can run using 90% hydrogen as fuel. The researchers say that any diesel engine used in trucks and power equipment in the transportation, agriculture and mining industries could ultimately be retrofitted to the new hybrid system in just a couple of months. Green hydrogen, which is produced using clean renewable energy sources such as wind and solar, is much more environmentally friendly than diesel. And in a paper published in the International Journal of Hydrogen Energy, Prof. Kook’s team show that using their patented hydrogen injection system reduces CO2 emissions to just 90g/kWh – 85.9% below the amount produced by the diesel powered engine. “This new technology significantly reduces CO2 emissions from existing diesel engines, so it could play a big part in making our carbon footprint much smaller, especially in Australia with all our mining, agriculture and other heavy industries where diesel engines are widely used,” says Prof. Kook. “We have shown that we can take those existing diesel engines and convert them into cleaner engines that burn hydrogen fuel. “Being able to retrofit diesel engines that are already out there is much quicker than waiting for the development of completely new fuel cell systems that might not be commercially available at a larger scale for at least a decade. “With the problem of carbon emissions and climate change, we need some more immediate solutions to deal with the issue of these many diesel engines currently in use.” High-pressure hydrogen direct injection
The UNSW team’s solution to the problem maintains the original diesel injection into the engine, but adds a hydrogen fuel injection directly into the cylinder. The collaborative research, performed with Dr Shaun Chan and Professor Evatt Hawkes, found that specifically-timed hydrogen direct injection controls the mixture condition inside the cylinder of the engine, which resolves the problem of harmful nitrogen oxide emissions that have been a major hurdle for commercialisation of hydrogen engines. “If you just put hydrogen into the engine and let it all mix together you will get a lot of nitrogen oxide (NOx) emissions, which is a significant cause of air pollution and acid rain,” Prof. Kook says. “But we have shown in our system if you make it stratified – that is in some areas there is more hydrogen and in others there is less hydrogen – then we can reduce the NOx emissions below that of a purely diesel engine.” Importantly, the new Hydrogen-Diesel Direct Injection Dual-Fuel System does not require extremely high purity hydrogen which must be used in alternative hydrogen fuel cell systems and is more expensive to produce. And compared to existing diesel engines, an efficiency improvement of more than 26 per cent has been shown in the diesel-hydrogen hybrid. That improved efficiency is achieved by independent control of hydrogen direct injection timing, as well as diesel injection timing, enabling full control of combustion modes – premixed or mixingcontrolled hydrogen combustion. The research team hope to be able to commercialise the new system in the next year or two and are keen to consult with prospective investors. They say the most immediate potential use for the new technology is in industrial locations where permanent hydrogen fuel supply lines are already in place. That includes mining sites, where studies have shown that about 30% of greenhouse-gas emissions are caused by the use of diesel engines in such items as mining vehicles and power generators. And the Australian market for diesel-only power generators is currently estimated to be worth around $765m. “At mining sites, where hydrogen is piped in, we can convert the existing diesel engines that are used to generate power,” says Prof. Kook. “In terms of applications where the hydrogen fuel would need to be stored and moved around, for example in a truck engine that currently runs purely on diesel, then we would also need to implement a hydrogen storage system to be integrated into our injection system. I do think the general technology with regards to mobile hydrogen storage needs to be developed further because at the moment that is quite a challenge.” unsw.edu.au
Savic Motorcycles
Savic Motorcycles hits two major milestones on the road to imminent commercial production.
EV pioneer Savic Motorcycles has achieved two major manufacturing milestones on the road to commercial production, with the successful completion of their customised Anti-lock Braking System (ABS) with Bosch Australia, and the first all-weather road tests on urban and semi-rural roads. Within Australia, it is a legal requirement for all road vehicles to be fitted with ABS units, and Savic chose to partner with the industryleading team at Bosch Australia to develop the ABS for its highperformance C-Series motorcycles – which are due to arrive on Australian roads later this year. “Bosch will be providing a motorcycle-specific ABS module for us, which will be used in every 11+ kW electric motorcycle that Savic Motorcycles will produce, starting with the C-Series,” said Dennis Savic, CEO and founder of Savic Motorcycles. “Partnering with Bosch enabled us to develop an innovative program using their existing ABS9.1MP system and a current C-Series prototype to produce specific software tailored to our requirements.” Development of the ABS program involved handing a 2022 C-Series prototype over to Bosch, which was fitted with the ABS module, an extensive range of sensors, and computing hardware and outriggers to safely test the braking system. The ABS tuning phase was carried out over several months involving countless braking manoeuvres over a wide range of surfaces and speeds. Through an iterative process of testing, the ABS calibration is honed to provide the optimal balance of robustness, stability, performance, and comfort, ensuring a faultless and dependable ABS braking system. “Our team enjoyed the challenge of integrating our ABS system with the EV tech on the Savic C-Series prototype.” said Joseph Cavallaro, Chassis Controls Engineering Manager, Bosch Australia. “We were also eager to help support homegrown Australian product development and manufacturing – and we look forward to further supporting Savic as they continue developing into the future.” The ABS program was a significant undertaking for Savic Motorcycles, starting in March 2022 and culminating in an approval that allows the leadership team to take the C-Series through the final milestone of Australian Design Rules (ADR) Government Compliance before commercial production commences and the first customers start receiving their motorcycles. C-Series aces first comprehensive road tests
The C-Series prototype has passed its first comprehensive road test program with flying colours, providing an effortless commute in Melbourne’s traffic and a confidence-boosting blast in challenging conditions on the winding roads of the Yarra and Dandenong Ranges. Savic Motorcycles’ assembly technician Adam Wilson, who took the C-Series on its first spin back in October 2021, described the new 2022 prototype’s performance in its latest and most wide-ranging series of test rides as “flawless”. “Melbourne laid on typically diverse weather for our first series of comprehensive road tests, which included dry-weather commutes in heavy traffic to wet-weather rides with some fog and sleet on the looping roads of the Black Spur,” said Mr Wilson. “Within a few kilometres, we had high-speed dry straights and tight turns in a downpour, and the bike didn’t even notice. We got to do everything, some durability, some wet-weather riding, and the bike was flawless and didn’t put up a single complaint. “We even had charge left over at the end of a very full day – which gives us a lot of confidence that the C-Series will look after even the most dedicated and enthusiastic riders.” Mr Wilson described the C-Series’ city performance as “a continuing revelation”, even after dozens of rides. “When it comes to stop-start riding on busy roads, the bike does the job really well,” he said. “It’s so easy to put it where you want it and just twist, and off you go. “I’m still inspired by how effortless it is to just jump on and go. There’s no start up, warm up, or putting it in gear… you just twist the throttle and away you go. It’s so simple.” Completion of the ABS program and the latest road tests have enabled Savic Motorcycles to progress component acquisition and tooling in readiness for imminent production, together with a busy schedule of ADR tests and vehicle certification over the coming months. It’s a positive step towards bringing manufacturing back to Australia and having fun while doing it.
savicmotorcycles.com
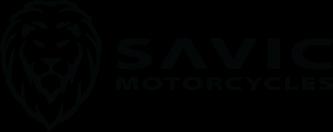
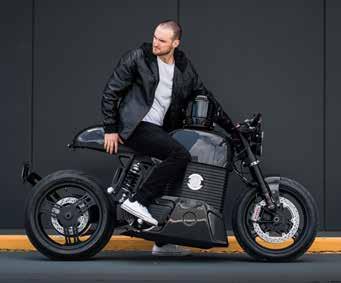
