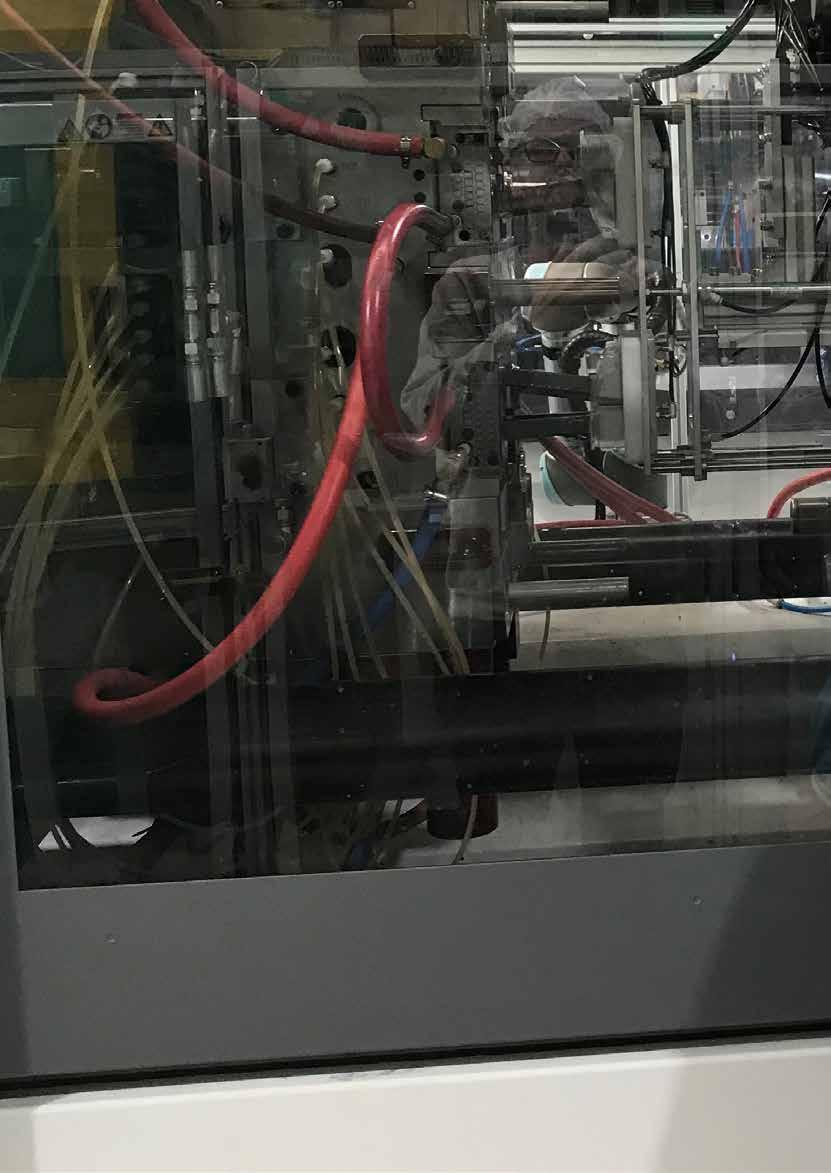
7 minute read
ONE ON ONE
from AMT DEC/JAN 2023
by AMTIL
Like every sector of manufacturing, plastics production has faced headwinds over the past few years. What does the future look like for this immense industry? The AMT Editor Paul Hellard speaks with Grahame Aston, President of the Plastics Industry Manufacturers of Australia (PIMA).
AMT: Tell me about the history of PIMA. How broad was the plastics industry in Australia when PIMA was established? Grahame Aston: PIMA began around 1992 after the chemical industry took over the PIA and created PACIA with a greater focus on chemicals rather than plastics. At that time, there were about 700 moulding companies of various sizes in NSW. PIMA began with approximately 70 members at that time and was known back then as the Plastic Injection Moulders Association with an obvious focus on the Injection moulders. As time passed and we lost many members through retirements and acquisitions, we had also seen our members base expand from just injection moulders to now cover all facets of the plastics industry, convertors, materials, ancillary equipment, consultants, in fact anyone that has any business within the plastics industry, which is why we are now known as the Plastics Industry Manufacturers of Australia. Currently PIMA has around 60 business members that are spread over three categories. AMT: How do you see the future of the plastics industry in Australia? GA: Right now, the industry is enjoying a resurgence, of sorts. Many larger companies are now looking to what we know as re-shoring the skills of our industry, the call to bring the job of manufactured products back here to Australia. With geopolitical uncertainty and the increased cost of goods transportation in the world right now has seen an increased appetite for locally produced products. Most of our members today are seeing increased orders and demands on their businesses, which is great news. Plastics do get a lot of negative publicity out there, but I can assure that all of our members take their responsibility seriously of ensuring that we have a sustainable and healthy industry. Not one of our members would be throwing away raw materials and they ensure any waste going to landfill is minimised and a great majority is sent be recycled. AMT: Where does someone find training in the chemistry, engineering, and production of plastics in Australia? GA: There are some very good VET training courses in these subjects, as well as university level courses. A lot of the VET courses have just been updated with a focus on what industry needs from the participants of these courses. That said, PIMA also sees an opportunity in offering Industry recognised training to fill some of the gaps that we know are there. These would be designed around specific, short term courses that could run for approx. six to twelve weeks part time. These would be designed to deliver basic skillsets to the industry. AMT: Can you talk about some of the newer regulations introduced into the plastics production industry here, like the Extended Producer Responsibility (EPR), and the extension of Product Stewardship measures? GA: These schemes are good when set up correctly and the perfect example of this is the ‘return-and-earn’ systems that are in place in most states in Australia for drink containers. The difficulty with these schemes is that you have to pick the correct level of where to introduce them. If you were to bring them in at the moulders level, you would only capture the materials and products that are moulded in the country, under that scheme. All the imported products would not be covered by that scheme. For these schemes to work I believe it needs to be set at the same level as the ‘return-and-earn’ scheme. AMT: What are the biggest markets for the plastics industry here in Australia? GA: There is a lot of volume of material being moulded here in Australia. I would say the large markets are for the built environment, medical, mining, automotive, and products for retail consumption. AMT: There is a big plastic elephant in the room. Microplastics, the plastics waste problem. Are there ready answers? GA: There are a couple of answers but whether they are viable right now needs to be assessed. The first is to understand exactly where microplastics are generated. Once this is correctly known, systems can be developed to overcome or reduce this problem. Some of these systems could be recycling, reduction or elimination of the types of plastics that produced the majority of the microplastics. These plastics could be engineered out of the areas where they are used. I do feel recycling is the answer, as the jury is still out on biodegradables and their effect on the microplastic situation. For recycling to work, there must be a concerted effort to set up working systems to collect, segregate and process these materials. Education is critical for the people who use plastics, to teach them put it all in the recycling system, and this is the majority of the population. Next is how they are collected and transported, then how the waste collection systems segregate and handle the various types of plastic materials and how they are then processed and put back into the marketplace. The majority of moulders are told what plastic to use when producing a product. A lot of designers will not specify recycled material where it is quite suitable for the end product. Once again, education in this area is critical. Another critical area of education is understanding how the plastics can be presented to the waste collection organisations so it can be recycled. Currently there is a lot of plastics presented to the waste collection system that goes to landfill because it presented to the system in a state that they cannot handle. Products turn up presented in a plastic bag for instance. AMT: Let's talk about the technology of plastics. GA: Plastics technology has come a long way over the years not only in the way and where they are used but also in the processing of materials. Plastics can also be very stable. Everyone reading this must have played with Lego blocks at some point in their childhood. If you have a block from when you were a child, in my case nearly 50 years ago, it will still fit into blocks produced today. Cars are another example of how far the technology of plastics has come. It’s not just the fittings inside the cabin. Volkswagen were certainly pioneers in utilising the benfits of plastic parts over metal. If it wasn’t for plastics used in cars, we wouldn’t have the fuel economy that we have today. In air travel, it’s all about payload versus fuel economy and plastics have been used fairly widely to substitute metals. Train travel is an example of how strong plastics can be. Many people wouldn’t realise but rail tracks are held in place using plastics. NASA used light-weight plastics in many parts of the International Space Station, the Space Shuttle and other space probes due to extreme heat resistance. Technology not only
shines through in the designed use of plastics, but it then turns full circle once it’s past the use-by date. It can then be recycled and turned into something new! How exciting is that! AMT: Clearly, plastics are a huge part in Australian manufacturing. Tell me how you get the word out. GA: PIMA was part of Australian Manufacturing Week (AMW) 2022 held at the Sydney ICC which we found was huge success. So many people visited our stand with a wide range of questions from all areas of industry. This was fantastic and PIMA will again be a part of AMW 2023 in Melbourne. Australia needs trade shows for companies to meet and display new technologies they have embraced. Being there to discuss directly with exhibitors is so important as it gives everyone the opportunity to work out first-hand if they are the right fit for your product or if they are someone to do business with. I would certainly encourage anyone that has services to offer to get on board and let everyone know what it is you do and how you can assist in getting their thoughts into reality. AMT: What motivates you and the PIMA members? GA: Plastics do make a real difference in our lives today. They can save a life through the use of respirators and defibrillators. Next time you visit a hospital, look around and see just how many products in any ward are made from plastics. I was in the supermarket the other day and on the back of the shirts worn proudly stated that the garment was made from recycled PET bottles. I get motivated by taking a piece of steel and turning it into a work of art through an injection mould, then seeing this work of art have plastic injected into it and have it produce what might be a life saving product. You know, we begin each of our days with plastic in our toothbrush, and then do the same at the back end of our day. The clothes we wear, the carpet we walk on, the cars we drive, the homes we live in, just about everything we do in a regular day, we rely on plastics in some way. I know that I’m proud to be a part of it and I’m sure that our members also feel the same way.
pima-org.net
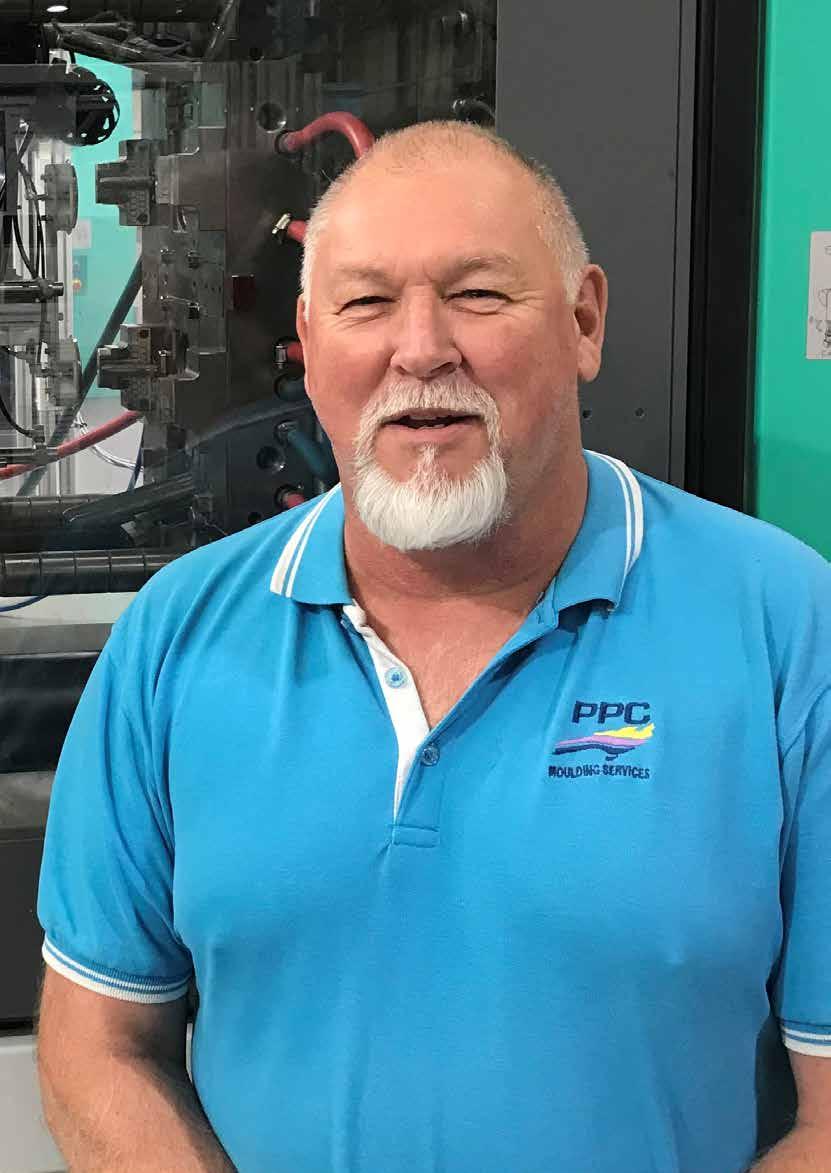