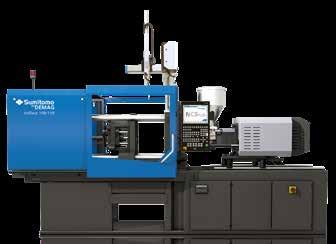
3 minute read
Tasman Electric Injection
from AMT DEC/JAN 2023
by AMTIL
058 PLASTICS, COMPOSITES & ADVANCED MATERIALS
All-Electric injection moulding
Tasman Machinery has led the Australian market in sales of electric injection moulding machines for 20 years. Below, Dermid McKinley, Managing Director of Tasman Machinery outlines some simple reasons why all electrics should be your next purchase for an injection moulding machine.
In the early years it was only a few adopters who were willing to consider all electrics. The time it took a customer to move from a hydraulic machine to an all-electric was very long. That time has now passed and sales of all electrics continue to grow at an ever accelerating rate. 1. Shorter cycle times.
In contrast to its hydraulic counterpart, an all-electric injection moulding machine can perform several tasks simultaneously in parallel operation. Highly dynamic Sumitomo designed drive motors ensure fast, ultra-precise movements. Sumitomo’s switching times are in the low millisecond range due to the advanced drive technology such as frequency converters, control modules and drive motors. If there is cycle time to be saved in an injection moulding process, an all electric injection moulding machine will find it. Time = money! 2. Maximum performance improves product quality.
Highly dynamic movements not only help to shorten the cycle time but are also responsible for increased product quality. Within the greater Sumitomo Group is Sumitomo Drives, one of the world’s largest manufacturers of industrial drives for industry. This means Sumitomo is the only injection moulding machine manufacturer able to design and build a drive system specifically for injection moulding. The end result is a direct drive system which ensures the highest performance in terms of dynamics and precision, while providing maximum energy efficiency and durability. 3. KISS. Keep-it-Simple-Stupid!
The great advantage of all-electrics is their simplicity. In a Sumitomo all-electric injection moulding machine there are four drives (injection, plasticising, ejection, and clamping); all direct drive systems. No valves, no pumps, cylinders, oil coolers, filters etc. Any deviations occuring due to wear of the hydraulic system, valves or changes in oil quality over the lifetime of the machine are simply not possible with all electrics. Even on a day-to-day basis hydraulic machines can have changes occur due to changes in ambient temperatures. With all electrics again this is not a consideration. All you will get is ultra-precise production with unerring repeatability. 4. More efficient use of energy
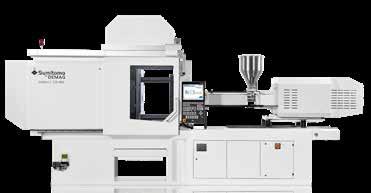
customers for all electrics. Compared to hydraulic machines, the specifically developed drives of our all-electric injection moulding machines only consume electricity when necessary. In addition, the kinetic braking energy is recovered by means of recuperation technology. There is not a more energy efficient injection moulding machine available in the market. 5. Low maintenance cost and less downtime
Compared to hydraulic machines, allelectric machines have fewer mechanical components that are subject to wear and tear. No oil changes, no filters, no o-rings, no cylinders, no oil coolers. All this maintenance is now removed. Less downtime = more uptime. More uptime = more parts = more profit. 6. Environmental credentials
With ever-increasing societal expectations, government regulations and incentives for companies to consider and document the environmental impacts of their operations; I cannot think of a simpler way for an injection moulding company to implement what is fast becoming a critical part of their operations. An investment all electric injection moulding machine ticks so many boxes that this alone is reason enough.
7.Industry proven technology.
Since 1995 Sumitomo has manufactured all electric injection moulding machines to be the acknowledged world leader. With over 85,000 machines sold into the market, Sumitomo’s technology is truly cemented. Across Australia and NZ, this same market acceptance has been replicated with over 300 all electrics sold into our market. From thin walled packaging to medical, to technical injection moulding the advantages of all electrics are being seen by an ever growing customer base. 8. Improved factory environment.
One of the intangibles many of our customers comment on when they first purchase an all-electric injection moulding machine is how quiet they are, and how little heat they push into the factory environment. For staff working in the factory, while this may seem a simple thing, any way that you can improve their work environment can only but help their overall performance. All electric machines provide you faster cycle times; reduced energy consumption; reduced downtime; high quality parts; better factory working environment & improved environmental credentials.