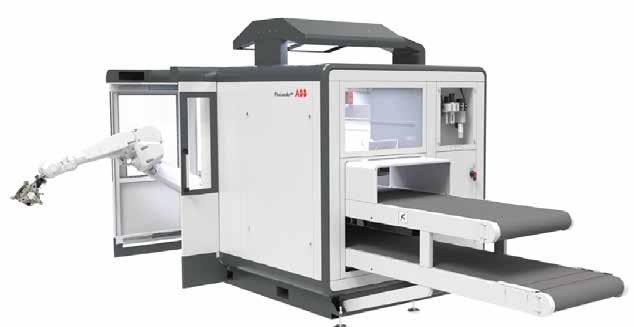
20 minute read
ABB FlexLoader SC 6000
from AMT DEC/JAN 2023
by AMTIL
Grantek on ABB
First robot and flexible multi-operation turn proves to be a big step for Grantek. Established in 1940, Grantek delivers a wide variety of services and Automation opens up opportunities products including manufacturing advanced special parts for industrial applications, reverse engineering, laser engraving, mechanical processing, wire spark, 3D printing, construction and more. The investment in robotic automation has enabled Grantek to transform both its productivity and competitiveness. Rather than being limited to delivering special jobs on demand, the company can For the seven-strong company based in Fagersta, Sweden, investing now manufacture items on a series basis. Automation has opened in its first robot has been a success. opportunities such as manufacturing more challenging items, more "This investment has helped us to greatly enhance our capabilities advanced processing and even being able to run in work shifts, as a company. We can process more orders for more customers allowing Grantek to scale up production if required. and make full use of the hours available in a day, including producing Grantek’s project is proof of the numerous benefits that robotic around the clock if necessary. Now we get requests that we have automation offers small and medium sized enterprises including never had before, so the robot has increased our competitiveness improved consistency and product quality, lower operating costs, considerably,” says Kjell Granqvist, CEO Grantek. increased production output, flexibility, adaptability, agility and Grantek uses an ABB FlexLoaderTM SC 6000, a turnkey solution reduction of waste. By using robots, SMEs can reduce mistakes that has been designed to ensure that the items that are fed from and focus more on increasing profitability, gaining a competitive the production line are ready to be packaged and delivered to the advantage and penetrating new markets. customer. This standard cell contains an ABB IRB 4600 robot, which "We made this investment because we wanted to enter a new uses ABB’s FlexLoader Vision software to enable fast and simple market. Now we can manufacture in a completely different way than teaching of new objects and materials to provide maximum flexibility. was possible before. In the daytime we can run maybe ten to twelve In developing the solution for Grantek, ABB worked closely with special details, then we can change and run series production at machine tool manufacturer DMG MORI to incorporate its CTX beta night. For a small company like ours, the ability to get more out of 1250 TC multi-operation lathe. As a result, Grantek can use a single the hours of the day makes a big difference in competitiveness," cell to handle a wide variety of products, further adding to the overall says Kjell Granqvist. flexibility of the solution. By meeting the exact needs of customers in Grantek was founded as a mechanical workshop by Kjell Granqvist's this way, this type of collaboration is key to creating security in large grandfather in the 1940s. Since then, the level of technology in the investments especially when an application involves implementing company has increased considerably, but the decision to automate new technology. "We decided to opt for a high-end solution that was still a big step to take, both technically and resource-wise. The we knew would withstand tolerances and advanced machining good supplier cooperation around the installation made it easier but with high levels of automation, but at the same time provide the took a lot of programming and many hours of learning to process flexibility to allow the cell to run pieces and prototypes. This solution the details correctly. is absolutely fantastic in that way; it is so flexible that we can run new.abb.com/au manually and in full automation at the same machine," says Kjell Granqvist.
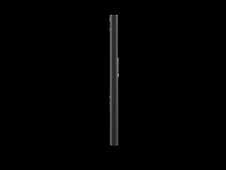
Integra K4.0 Kiosk

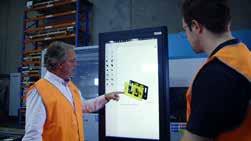
Made by manufacturers for manufacturers, the Integra K4.0 enables your Industry 4.0 ambitions
Touchscreen and touchless options available Floor, wall and desk mounted options available Australiandesigned and made
Hypersonic missile manufacturing
Aerobotix and Automated Solutions Australia announce partnership to deploy robotic systems for hypersonic missile manufacturing.
Aerobotix and Automated Solutions Australia (ASA) has announced a robotic automation international partnership between the two companies for the development, testing and manufacturing of hypersonic missiles. The partnership follows the 2021 signing of the AUKUS security pact between the US, UK and Australian Governments, which includes provisions for the allies to work together on hypersonic and counter-hypersonic capabilities. The Aerobotix-ASA collaboration will enable the Australian defense sector and Australian defense contractors to more easily access both companies’ expertise in automation. The two companies became acquainted through their mutual capabilities in the robotic coating automation industry and are now working together to pursue projects for which a sovereign presence is required. “We’ll work with the US State Department for approval of any technology transfer for ASA,” said Josh Tuttle, Aerobotix Business Development Manager. “We’ll also help ASA in other ways. For example, we can save them years of costly development work by sharing how to robotically spray FIREX™ RX-2390 Thermal Protection System coatings for missile manufacturing.” Aerobotix and ASA are both turn-key robotic integration companies with specialised capabilities in the precise application of paints and performance coatings. Aerobotix has accumulated invaluable experience in the use of robotics to scan, sand, measure and paint hypersonic missiles on multiple successful missile programs. ASA’s relationship with FANUC has resulted in the installation of more than 100 FANUC painting robots in Australia. Now, with the backing of Aerobotix, ASA has the expertise and technical capability to overcome the most difficult automation challenges in precision coating applications. “Aerobotix has already deployed several production robotic systems for hypersonics,” said Nathan Jones, ASA General Manager. “They’re even making critical test parts for programs that haven’t had time to build production facilities. Their willingness to support our company, and Australia, is going to significantly reduce costs, schedule delays and program risk.” With 20 years of robotic coating automation experience in Australia, ASA is uniquely positioned to provide sovereign capability and assist in the rapid development of hypersonic capability on Australian shores. Headquartered in Huntsville, Alabama, Aerobotix is an innovative leader in advanced metrology and robotic solutions for the aerospace and defense industries. Automated Solutions Australia (ASA) brings world class, flexible robotic automation to Australian shores.
automatedsolutions.com.au

MEGA addition to the Agile Flex range
Expanding even further on the success of the Australian made Agile Flex range of CNC machine tending products, Agile Robotic Systems is proud to introduce the Agile Flex MEGA.
The Agile Flex MEGA can be matched equally well to both smaller CNC machine tools with longer unmanned production requirements or larger machines able to process heavier components, with a choice of Fanuc robots and payloads. The four to eight drawer system has an increased part capacity of up to 100% per drawer compared to the Agile Flex 35D. Just one drawer can accommodate 200 x Ø1”/Ø25mm billets. Designed and built with a focus on strength and rigidity, the Flex MEGA can hold 400kg per drawer, allowing for much longer unmanned production on larger CNC lathes and multi-tasking machine tools. The new drawer system with a relatively small footprint allows for much taller parts than its smaller cousins with maximum part height of 240mm in the four-drawer variant and 100mm in the eight-drawer chest. The Flex MEGA retains all of the best features of the existing Flex range including datum and turn-over stations, part cleaning and drying stations, QC options as well as the state-of-the-art AgileGo Controller. The AgileGo Controller allows for new parts with complex robot motion and sequences to be configured in just minutes. Specifically designed to be intuitive for the CNC machine tool operator, the parametricstyle, wizard-guided system requires no robot programming knowledge. Developed to add lights-out machining to any brand of CNC machine, the Agile Flex range now consists of six models and boasts a workpiece capacity which is superior to competitive machine tool loading products. Agile Robotic Systems is part of the John Hart group and draws upon a heritage of more than 70 years in machine tools and close to 40 years in automation and robotics to deliver Australian-designed and Australian-made agility to CNC automation.
agilerobotics.com johnhart.com.au
Robots for AW Fraser
ASA helps to automate making old alloys new again at AW Fraser over in NZ.
On any given day in Christchurch, New Zealand, you’ll find old car radiators, tangled electrical wire, taps and other trinkets, slowly bubbling away inside a furnace at temperatures around 1500 degrees Celsius. Once these items are reduced to a molten form, they are converted into forty types of specialised bronze and brass alloys, which can then be transformed by on-site machining processes into precision components such as valves, engine parts, gears and even bushes and other critical components within wind turbines. Such is a day in the life of AW Fraser. Since the 1930’s, AW Fraser have been offering an end-to-end solution for high grade metal components. Since then, the company has become a global leader in supplying bronze and brass components to over 35 countries globally. Metal comes to AW Fraser and is sent to the scrap bay, where it is sorted, graded, and turned into a form the foundry can use, referred to as a charge. Each charge is issued per alloy of what AW Fraser are trying to make. Products are cast into horizontal castings, vertical castings and centrifugal castings, where they are then cut efficiently and to the highest quality standard. Once the bar has been cast, it will head off to the machine shop for external customers to make final machined components out of the cast metal. If the raw stock reaches the onsite machine shop, the CNC machines turn the raw material into precision machined products that are then measured by CMM to ensure the most stringent tolerances and quality targets are met. Recently, AW Fraser invested in three automation cells with Automated Solutions Australia (ASA). “From conception through to commissioning, this project was never a transaction, it was a collaboration,” said Jody Tuckwell, Operations Manager at AW Fraser in working with ASA. “Both parties came to the table with the utmost respect for each other’s skills and experience and as a result the outcome has been phenomenal.” The first two cells are tending two of AW Fraser’s recently installed multitasking turn and mill machines, a DMG Mori NTX 3000 and an NTX 2500. ASA coupled each of these machines with a Fanuc R2000iC/270F, increasing throughput significantly by tending to the machine around the clock to unload machined parts and reload raw stock as soon as the machine is ready. ASA designed each cell with a floor mounted robot and five infeed bays, designed to receive AW Fraser’s ingenious parts trollies and work pallets. The work pallets are designed to glide on a cushion of air from the trolley onto the CMM, allowing a 150kg bush to be taken from machining, through inspection and onto packaging without having to sling, lift or slide it. Each robot can access multiple grippers to load and unload parts from the machine, automatically performing gripper changes between the load and unload if required. The more common grippers are duplicated in each cell, but the specialised, extremely heavy grippers are able to be moved between the cells as required. The third cell is nearly a duplicate of the second cell with their third Fanuc R2000iC/270F tender yet another DMG Mori NTX 2500. The proven trolley and pallet configuration is being employed again as is the flexible gripper configuration, however the available workshop space dictates a slightly different layout and access to the previous two cells. Each cell was designed by ASA after close consultation with AW Fraser to understand the existing pain points and desired outcomes from this investment. Each Fanuc robot cell is equipped with Automated Solutions’ CNC Toolroom software. The software allows the machine tending sequence to operate in a number of ways, each selectable to suit the part being machined. “To eliminate the risk of operator error, the ASA team encapsulated everything into a fully customised touch screen and simplified the PLC system,” said Tuckwell. For a conventional machining process with raw part in, finished part out, the robot picks the raw bronze billets up from a work pallet and loads them into either the main spindle or the sub spindle of the machine depending on the loading operation that has been setup for the part. When the machining cycle has finished, the robot then unloads the machined part from either the main spindle or the sub spindle and places this finished part back onto the infeed trolley. Most jobs operate this way with twin spindle machines. AW Fraser also have parts that use the raw part in, multiple finished parts out machining process. In this method, the robot loads the raw billet into the main spindle and progressively unloads nine finished parts from the sub spindle before finally unloading the remnant piece left over from the machining process. After unloading the remnant and placing it adjacent to the nine finished pieces, the robot loads the next raw billet and repeats the process. Tuckwell remembers the first day of operation fondly “When we were originally conceptualising the project, I dreamt about the day we might one day run twenty-four hours straight. Then, when that happened and we continued running unmanned for 48hours uninterrupted, it was the stuff dreams are made of,” he recalls. From start to finish, this fascinating process offers a brief insight into a full circle recycling process; following scrap metal through the furnace, into the foundry and extrusion plant, before being turned into high quality precision components in the machine shop. Perhaps equally as fascinating is the unique position AW Fraser finds themselves in, having been in business so long and now seeing components they’ve already recycled, return years later to be recycled again, a truly sustainable manufacturing process.
automatedsolutions.com.au awfraser.co.nz
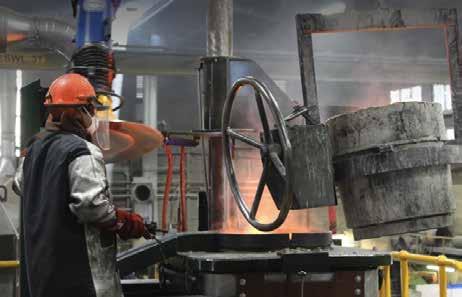
Top five applications for cobots
Automation trailblazers – collaborative robots, or cobots – are unleashing their potential across an array of applications commonly carried out on the factory floor.
Cobots can be used to automate millions of tasks – from detailed work right through to palletising. “Each cobot model is better suited to certain tasks and it’s our job to work alongside our customers to determine what will work best for them,” explains Masayuki Mase, Country Manager for Universal Robots Oceania. “For instance, a UR3e is a tabletop model that will suit a business looking to automate non-load-bearing tasks, while a larger cobot arm such as the UR10e can be used to automate heavier jobs,” he says. Versatility all the way
For a small business, the fact that cobots have many uses remains one of their biggest assets. They can be reprogrammed to fill gaps that emerge in virtually any area of the business, from palletising to production line, in very little time. And one core component is responsible for cobots’ versatility: their end effectors. “End effectors, also known as end of arm tooling (EOAT), are a vital component of all cobots,” Masa explains. “They are attached to the end of the robotic arm and allow it to carry out specific tasks. One cobot could handle upwards of a dozen tasks over the course of a working week - depending on a business’s needs.” Other reasons to opt for cobots:
Compared to the large and bulky industrial machines, cobots are designed to safely operate near humans to complete tasks. Traditional industrial robots are often mammoth-sized machines that are static and difficult to repurpose and reprogram. By contrast, cobots are compact and flexible and can operate without safety cages or fencing directly alongside people (upon risk assessment), thereby reducing footprint and space usage. Cobots, unlike humans, do not suffer from fatigue and can work 24/7, 365 days per year, repeating each task in the same way. Therefore, with none of the human errors caused by fatigue, cobots provide higher business productivity, efficiency, and product quality. Cobots are highly flexible, allowing them to be reprogrammed for different tasks if manufacturing processes change, making them more investment worthy. Top five cobot applications unpacked
While cobots can be used for everything from soldering to screwing and sanding, 70% of the applications fall within three categories, namely: ‘pick and place’, assembly and material handling - closely followed by welding and palletising. Masa helps to unpack these applications as follows:
1. Pick and place
Forming part of material handling, cobots performing pick and place tasks work quickly and accurately and can be programmed to select the right parts and reject unsatisfactory pieces. “Commonly used in the electronics industry to solder parts onto printed circuit boards (PCBs), cobots work with great speed and accuracy – 24/7.” Masa adds. “This helps to boost capacity whilst keeping production costs low.”
2. Assembly
While some tasks on an assembly line require skills, attention to detail and the careful eye of a human, others are monotonous or even dangerous. “Using cobots on an assembly line can increase the pace of production, protect workers from harm and ensure the irreplaceable people in your business are being utilised in the most effective way.” says
Masa.
3. Material handling
In manufacturing, material handling refers to the movement, protection, storage and control of materials and products throughout manufacturing, warehousing, distribution, consumption, and disposal. This is often one of the most dangerous jobs in manufacturing as materials such as metals, plastics, and other substances can pose a great risk to human workers. Additionally, many material handling tasks are repetitive, which can give rise to repetitive strain injury and errors due to fatigue. “Interestingly, manufacturing plants that use robots see significantly fewer workplace injuries.”
4. Welding
Universal Robots has cited a recent uptick in welding application demand. “A cobot adds flexibility, efficiency, and freedom to welding processes. In addition, when the task is completed, it can be easily redeployed to other areas where it can add value.”
5. Palletising
Palletising applications take place at vast majority of manufacturers across the globe and require many final products be moved onto a palette as quickly and efficiently as possible. “The demand to automate palletising tasks has increased exponentially over the years, largely due to the strain and overexertion that it places on workers. To conclude, Masa says that cobots are growing in presence and popularity around the globe. “This is largely driven by their budget-friendly price tag, easier programming which reduces implementation and training time, and safety qualities.”
universal-robots.com
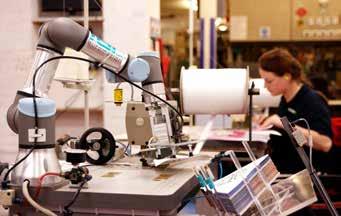
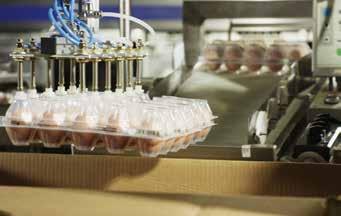
Robotics and automation
Matthew Hunter, innovation product marketing manager, Konica Minolta Australia explains how robotics and automation support manufacturing lines to operate at full capacity.
The manufacturing industry has transformed over recent years, with manufacturers implementing new technology, such as automation and robotics, and leveraging these technological advancements to reap benefits across productivity, efficiency, and human safety. The coronavirus pandemic presented many challenges for the industry; however, 84% of manufacturers adapted well to these hurdles and seized the opportunities during this time. Digital transformation was accelerated by 72% of Australian manufacturers, with 74% planning to increase their investment in technology across the next year, and 65% poised to concentrate on business growth in 2022. Robotics and automation have rapidly become a key part of keeping manufacturing facilities operational in a time when human resources have been stretched like never before. COVID-19 changed the way manufacturing plants run due to ongoing restrictions and staff shortages due to infection, isolation requirements, and a lack of overseas casual labour to tap into. Robots can help keep operations physically distanced and even contactless, while reducing strain and fatigue for human workers. Mid-sized organisations with a turnover between $20m and $200m were particularly affected by worker shortages and supply chain issues. A recent Manufacturing Insights report from CommBank also found that some of the barriers to growth included: increasing supplier costs (55%); supply chain issues (54%); attracting and retaining skilled staff (46%); ongoing COVID-19 restrictions (36%); and increasing capacity to keep up with demand (31%). While manufacturing lines are now largely automated, a shortage of workers can mean the difference between success and failure. There is still a heavy reliance on manual materials handling including feeding raw materials into the production line, then taking finished goods off at the other end and preparing them for distribution. This is where the benefits of robotics and automation can come into effect and aid manufacturing lines to continue at full capacity. Automation
Throughout the volatile environment of the past two years, manufacturers needed to find a way to not only reduce some of the pressure on workers, but also provide employees with technology that could make their jobs easier. By removing much of the manual work from manufacturing operations, manufacturers can potentially redirect those people towards more valuable, growth-oriented activities while cutting the costs of production. By automating workflows and implementing technology that can streamline processes, manufacturers can make operations run more effectively and smoothly. This can improve the quality of outcomes with fewer costly mistakes by reallocating the repetitive and mindless tasks to automated technology and machines. Humans can then be redeployed to more valuable tasks, ensuring that manufacturing organisations can continue to run at full capacity. The investment from manufacturing organisations in adopting automation will only increase, with 42% of Australian manufacturers planning to adopt intelligent automation and robotic process automation in the next two to three years. Autonomous mobile robots (AMRs)
AMRs provide a powerful solution for moving items and stock in warehouses and around manufacturing lines. AMRs can deliver significant benefits productivity and safety benefits in the manufacturing facility. For example, AMRs can move materials around the facility without requiring human intervention. This reduces the time it takes for line operators to replenish materials so they can keep the line moving. Instead, the AMR automatically delivers more materials when required so the operator doesn’t have to leave their position. Likewise, when the process is finished, AMRs can transport them to the next station, further eliminating the need for operators to walk around the facility. This approach can reduce the amount of walking required for manufacturing workers, which in turn reduces their fatigue and makes them more productive with less effort. AMRs can be easily programmed to the layout of the warehouse and customised to suit whatever the item or product is that it is carrying. They are also flexible in their application. For example, an AMR might be used to substitute a conveyor, and, if a workflow changes the AMR can easily adapt to that. In the next few years, 36% of Australian manufacturers will invest in autonomous machines and vehicles. (4) Using AMRs can help manufacturing facilities overcome staff shortages and maintain physical distancing between staff members (since the robot can ferry materials and finished goods from station to station). AMRs can also be used to do the heaviest lifting, which reduces the chance of worker injuries due to lifting heavy objects or repetitive motions. And, AMRs are designed to avoid collisions with humans and other obstacles, making them incredibly safe for people to work near. Part of Australia’s Advanced Manufacturing Roadmap is to support the industry’s growth through significant technology innovations. Some of the key science and technology areas outlined in this include smart robotics and automation, additive manufacturing (3D printing), and augmented and virtual reality. (5) Although the manufacturing industry has already seen a rapid acceleration in adopting advanced technology, this will continue well into the future as manufacturers shore up supply lines and operations. Especially with the government funding and grants currently available, Australia’s manufacturing industry is primed for growth. Automation and robotics are at the forefront of providing manufacturers with new capabilities and opportunities to build a strong, successful future.
commbank.com.au/content/dam/commbank-assets/business/ industries/2022-03/manufacturing_thought_leadership_ march-2022.pdf csiro.au/en/work-with-us/industries/manufacturing/advancedmanufacturing-roadmap
