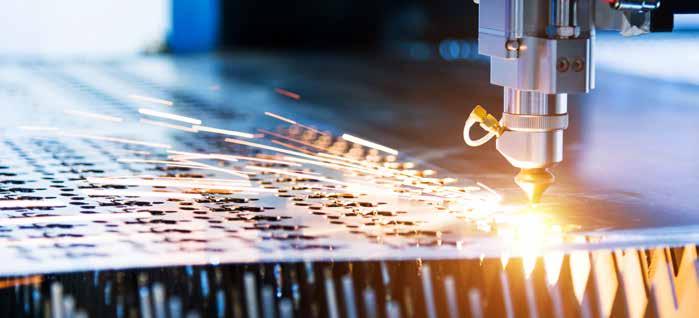
11 minute read
Livetools at CNC
from AMT DEC/JAN 2023
by AMTIL
Intermach laser cutting
At Intermach, we’ve witnessed how laser-cutting machine technology has completely reshaped the engineering and fabrication industries over the last 30 years.
In the mid-1990s, our company sold and serviced the earlyform CO2 lasers. These early machines were primarily supplied by Amada and they came equipped with fixed beams, and the sheets were physically moved along the X and Y axis. Some of them still remain in operation to this day as a living reminder of the superb build-quality we have come to expect from the Japanese manufacturing industry, and the talent that Australian engineers have utilised to keep the machines in premium operating condition over all these years. As the technology has evolved, flying-optic machines with CO2 resonators came to dominate the industry. Machines of this calibre permitted larger sheet sizings to be cut at a fraction of the previous cost. In addition, the maximum power output of these new exciting machines was also rapidly increasing, allowing thicker cutting to be achieved combined with increased cutting speeds. Companies such as Mitsubishi, Amada, Bystronic, Trumpf, Mazak, and many more were the early pioneers of this new technology and they continue to dominate the market today. The technology continued to evolve, but now, fiber laser technology has begun to dominate the global market. The beam-delivery systems now depend on a simple flexible cable, as opposed to a fragile mirror pathway. Consequently, the costs involved in building and maintaining laser-profile cutting machinery have undergone a significant reduction in recent times. IPG is still the market leader in fiber laser technology, accounting for around 40% of all laser source manufacturing. IPG have major manufacturing hubs in the USA, Germany, and Russia. They are trusted enough that even major brands like Bystronic are still comfortable using IPG laser sources instead of an in-house solution. A number of high-end manufacturers, such as Mitsubishi and Amada, instead make their own laser sources with advanced hotswapping functions and beam-shaping technology not yet available or deemed too expensive for mass laser source production, to give them an edge. Lately, Chinese resonators are starting to increase their market share, proving remarkably stable solutions at lower powers. Brands such as Raycus and Max Photonics are leading the way and are starting to appear on some quality machinery. Due to their increase in reliability and functionality as well as the significant cost saving over their American, German and Russian counterparts these manufacturers are becoming increasingly popular. The current fiber laser market is a vast, dynamic and ever-changing ecosystem with a large pool of global manufacturers to choose from. The leading brands remain Japanese and European in origin. Though the machinery is of a higher-quality in these countries, it comes, rather expectedly, at a higher price point. Of course, we’d be remiss in failing to mention the outstanding options that remain available to the more budget-conscious buyer. Over the last decade, top tier Turkish and Chinese companies have started supplying extremely high quality machinery for very reasonable prices. MVD and HSG to name but a few have taken huge strides in their quality and reliability whilst still maintaining that competitive cost advantage over their Japanese and European rivals. So too, we are now starting to see quality offerings coming out of places like India through companies such as SLTL. These organisations are spending exorbitant sums of money on R&D as part of a country-wide manufacturing push pioneered by the Indian government to increase their market share for global laser exports as well as promote local manufacturing and reduce their dependency on imported machines. Currently in India, Chinese fiber laser cutting machines hold a 70% market dominance over their local counterparts, this is something the Indian government is actively trying to balance. In summary, the future of the laser-cutting industry looks particularly bright and extremely exciting. The recent Euroblech Exhibition in Hamburg Germany showcased new-look combination tube and laser-cutting machinery which are very popular in the European Market as well as plate-bevel cutting. Of course, it remains to be seen how these types of machines will fare in the rough and tumble of the Australian market. All the same, we are incredibly excited to see what the future of the industry holds, and our team is excited to be at the forefront of the next technological push. Here at Intermach we pride ourselves on the extensive experience we bring to all types of laser-cutting machines. To that end, our knowledgeable customer service representatives and local expert engineers are ready to collaborate with companies in the hopes of seeking a machine appropriate to their needs. We look forward to carrying the torch alongside you. intermach.com.au
Gühring System 222
New features include reliable part off in stainless steel with Gühring System 222.
The Gühring System 222 for grooving and parting-off has been expanded: in addition to indexable inserts for steel materials, it now also includes a grade with a width of 3mm for parting-off stainless steel materials. With two cutting edges and a length of 22mm, the new indexable insert is ideally suited for parting-off the most common bar diameters. They also offer an extensive range of clamping holders with and without internal cooling. Many production facilities use a mixture of steel and stainless steel materials. In recent years, there has been a rise in the demand for stainless steel in particular: whether it’s in the medical technology, automotive or general mechanical engineering – across all industries, machinists are increasingly relying on stainless and difficult-to-machine materials. After the successful market launch of the 3mm indexable insert for steel machining, customers frequently asked: when can we expect to see a cutting insert for stainless steel machining? Gühring was happy to meet this demand! In series production, this indexable insert is used for partingoff on lathes with a bar feeder. As parting-off is often the last application on a component, process reliability during parting-off is an important factor. If the tool breaks, the finished component could be damaged. That is why it is important to use an insert whose geometry, cutting material and coating have been specially optimised for this application. Chip breaker for optimal chip control
During development of the new stainless steel insert, the Gühring experts explored the topic of chip breaking extensively. The result is an insert with an extremely effective chip breaker. After all, “Process reliability equals chip breaking and chip breaking equals process reliability,” explains Marco Bücheler, Product Manager for Grooving Tools at Gühring. With grooving and partingoff, a chip breaker has to work hard: it constricts the chip, as the chip has to be narrower than the groove width, it makes the chip roll up and finally, it breaks the chip. Now that’s multitasking! The result is reliable chip removal and good surface finish quality. For safe chip removal, targeted coolant supply is also recommended. In addition, this reduces temperatures during machining, keeps cutting insert wear low and improves surface finish quality. The clamping holders in the System 222 have an internal cooling system for direct coolant supply to the clearance and the rake face. Connecting the coolant can also be done tubeless through the coolant port in the contact area of the holder. 42% cost saving in field tests
The perfect combination of geometry, cutting material and coating is the result of considerable testing in the Gühring test field. A pre-series was then produced and tested in field tests together with Gühring customers. The result: customer feedback was consistently positive as all of the competitors’ tools could be surpassed, customers have permanently switched their parting-off applications to the new Gühring tool. “We have a technically flawless product here,” said Marco Bücheler. “Our field tests have shown that we perform well and are competitive with this insert in a wide range of stainless steel materials.”
guhring.com.au
HSG G4020X PRO INDUSTRIAL FIBER LASER CUTTING MACHINE
- Precitec ProCutter Autofocus Cutting Head - Quality imported German and Japanese components - Automation ready - German IPG Laser Source
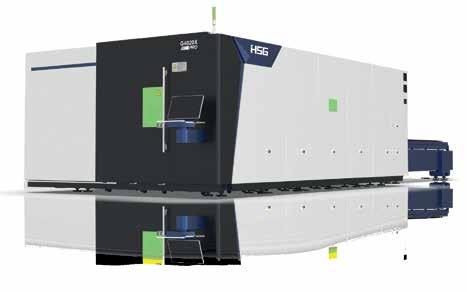
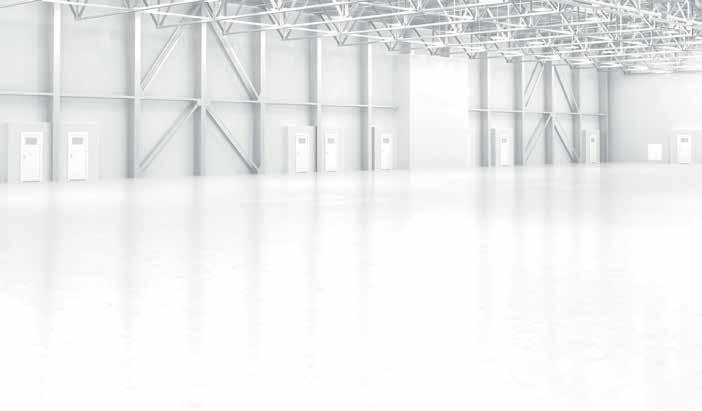
IN STOCK NOW! Demo Available!
EXAPRESS PBH PRESSBRAKES
-Bosch-Rexroth Hydraulic System (Germany) -Fully Annealed Frames -European-Style Tooling System -Siemens Electrics
EXPERTS IN FLATBED AND TUBE FIBER LASER CUTTING MACHINERY
CALL US TODAY: 03 9132 5223
info@intermach.com.au www.intermach.com.au
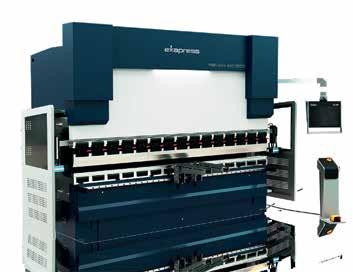
Planning for tool failures
Proactive planning for predictable tool failure. How to establish a controlled process to maintain tool life.
Tool life is often a top priority when working in a high production environment. To some degree, it does not matter if you have the fastest or the best tool; it is more important to have a tool that fails consistently in the exact same way, but the question then becomes how do you achieve this? How can you proactively plan for predictable tool failure? There are many factors that contribute to failing consistently from the tools themselves to outside factors like coolant, machine maintenance, material hardness, etc. While it is unrealistic to hit 100% repeatability, it is key to keep as many factors as you can the same from job to job and part to part. Establishing repeatability makes it easier to prevent catastrophic failure that will damage the workpiece and tooling, which becomes much more expensive than just taking the tool out early even if that is before it is completely worn out. Therefore, cost savings is one of the biggest benefits of consistent tool life. It is better to change an insert out ahead of time instead of pushing it to max life and potentially damaging components of the tool or components of the machine—causing more setup time and more machine downtime. Given the benefits that establishing a controlled process can provide, below are some tips to help you better achieve this. • Proper coolant maintenance and filtration. From bacteria and machine lubricants to acidity and cutting debris, coolant contaminants can hinder the protective layer coolant provides for both the material and the cutting edge of the tools. Whether using a refractometer to evaluate concentration levels or water test strips to measure pH levels, it is always cheaper to maintain coolant than replace the entire system or risk damaging tools. • Perform preventive maintenance. To achieve consistent tool life, it is necessary to perform preventive maintenance of the machine tool components and fixtures. Vibrations and lack of rigidity due to worn out components can be detrimental to new carbide tooling that shops are encountering in modern manufacturing. Overall, it is important to schedule and maintain records to save in tooling and machine downtime. • Source materials from consistent vendors. While it is difficult to buy materials from the same vendors because of COVID and supply chain issues, it is important to try to buy from the same vendors because differences in materials cause tools to work differently. When sourcing from different vendors, it is important to monitor incoming Mill Turn Reports (MTR) to ensure chemical compositions are comparable and make the necessary changes to programs to prolong tool life. • Focus on tool holders. With general purpose machining, tool holders are typically not the driving factor leading to a reduction in tool life. Nevertheless, for consistent results at higher spindle speeds, it is necessary to have a balanced tool holder and assure that the tool is assembled with minimal total indicator runout (TIR) in order to yield positive results. The cleaning of tool holders as well as the actual spindle of the machine are also important aspects of tool holding components as a layer of oil drying on these surfaces can induce TIR to the assembly, which creates additional radial loads to the tools and can cause failures and inconsistent results. • Consistent tooling means consistent results. In order to do this, it is key to source tools from manufacturers that have good quality systems to produce parts of the same quality every time.
If there is a switch in manufacturers, processes will be affected even if the tools are dimensionally the same because quality and performance standards will vary depending on manufacturer. Aside from these top factors to consider when planning for predictive tool failure, you can also work to baseline your tools. Whenever you are running off a project for the first time, the first couple of tools you are putting into the part need to be monitored to ensure that speeds and feeds are optimized and that repeatability is established. If it repeats after a couple of tools, that is your baseline; you can reach “x” amount of parts per tool. Other things to consider are load limiters and part counters. For predictive tool failure in job shops, use load limiters. If one tool is consistently running at 80% load, when load begins to steadily climb to the upper end, you will know when inserts are dull and need to be changed. Part counters can be integrated into the programs. By establishing a baseline as discussed above, you will know what the tool can do and then program that into the machine. Because the actual program is counting as parts are processed, there is no error like if an operator is counting the parts; the program will stop, and no additional parts can be run unless the tool is changed. Ultimately, not all shops are using or are capable of using predictive tool failure in their processes, but collecting data and tracking tools is a good starting point. If you are not tracking tool life or keeping a log, it is challenging to determine how long tools last or how to make them last longer. Simply tracking data and running spot checks on tools could save shops money and time in addition to establishing a method for predictive tool failure. Knowing your limitations in addition to simply being prepared are key in predictive tool failure. It may sound simple, but exceeding the limits of the machine, operator, process, tools or application will result in a less than satisfied result. Being more knowledgeable about an application—whether that is through data collection or proper training—allows you to better establish the desired repeatability. alliedmachine.com
