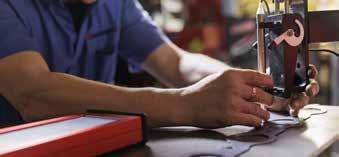
8 minute read
ArcDroid by Ausvex
from AMT DEC/JAN 2023
by AMTIL
ArcDroid
The world’s first CNC portable plasma robot.
The ArcDroid is the world's first portable solution for CNC plasma cutting. This robotic solution from Hare & Forbes is fully functional, easy to use and set up. It features a glove-friendly intuitive touch screen interface and is standard with quick change holders to allow changing from trace to cut mode quickly making it extremely user friendly. Weighing just 16kgs and having a convenient cut envelope of 660mm x 380mm, the ArcDroid operates from a 10 amp 240V supply and is easy to transport and store. This super handy portable plasma robot will appeal to anyone who needs to cut custom shapes and plates. It is ideal for applications such as onsite structural work, agricultural repairs and automotive restoration workshops. Even small fabricators with limited workshop space, or home hobby workshops will benefit from this compact and versatile portable plasma robot. Simple Trace is an easy to use and intuitive interface. Point to point or free hand, trace your template and ArcDroid creates a cut file instantly. Simply use the ArcDroid arm to follow the contours of your template and highly accurate encoders map your every move. Now all your cardboard cut outs are functional cut files. Whether you draw it, download it or just imagine it; you can cut it with ArcDroid. Any table is a plasma table with ArcDroid. Precision encoders and high resolution drives mean ArcDroid accurately reproduces your design. Get fast, accurate and repeatable parts from your plasma cutter. Highly intuitive to use with Simple Trace
For added convenience and productivity no programming experience is needed to use the ArcDroid, thanks to its Simple Trace technology. This makes it a simple matter to produce fast, accurate and repeatable parts. Simple Trace lets you trace your template point to point or freehand, by moving the ArcDroid arm to follow the contours of your template. The high accuracy encoders and high-resolution drives map your every move. When you are finished tracing you can define the cutting order of the component features and instantly create a cut file. The cut file can even be saved to a USB stick for future use. Advanced users
For anyone wanting more control, DXF drawing files can be downloaded directly to the ArcDroid for part processing. The ArcDroid is also compatible with most CAD/CAM packages such as FUSION 360 and SHEETCAM and detailed g-code files can be downloaded directly to the ArcDroid via the USB port. Most air plasma cutters can be used with ArcDroid as long as a two wire switch can be provided for turning on and off the torch. (However, hghi frequency start plasma is not suitable). If you don’t already have a plasma cutter, they are available as an option. Further details and full specifications of the ArcDroid CNC Portable Plasma Robot are available at the Machinery House site.
machineryhouse.com.au
Striving for error-free production
Precise, high-quality machining enhanced by Sandvik Coromant’s CoroMill MH20.
According to PwC’s Industrial Manufacturing report, “The only constant in today’s industrial manufacturing environment is disruption.” Disruptions to supply chains and productivity, caused by the pandemic, have driven manufacturers to diversify to new markets to survive. This creates an increased need for error-free precision machining. Here, Sangram Dash, Product Application Manager for Indexable Milling at Sandvik Coromant, explains how the new CoroMill MH20 high feed milling cutter can support errorfree machining. “To stay competitive, organisations must be able to integrate new business models and technologies to accelerate and adapt,” The PwC goes on to say. For machine shops, adapting includes diversifying product offerings and being ready to satisfy customer demand in new markets. They are also under pressure to diagnose and eliminate product defects through error-proofing. This is a growing challenge, because diversifying into new sectors means handling workpieces made from wider a range of materials like aluminium and heat resistant super alloys (HRSAs). The hardness values of these materials differ enormously from one end of the spectrum to the other. Processes and machining conditions will also vary widely from part-to-part. They include everything from roughing to finishing on out-of-round or near-net-shape cast or forged parts. Certain types of machining also present unique challenges. For instance, when a tool with a long overhang is used to mill deep narrow pockets, the whole setup becomes unstable. This can lead to unpredictable machining and a higher risk of vibrations that, as we’ll explore, can cause tool failures and downtime. Manufacturers instead need tooling solutions that provide secure and predictable machining, with increased metal removal rates, reduced cycle times and quick changes between production batches. Fortunately, a solution does exist. As PwC’s Industrial Manufacturing puts it, “with disruption comes the opportunity to innovate.” Bad vibrations
Why are these innovations necessary? One factor that needs to be overcome is machining vibrations, which negatively affect performance in a variety of ways, including displacement of the tool and imperfections in workpieces. They can even cause tool breakage and unplanned downtime. Another problem with vibrations is the effect on chip formation and chip removal, which are the fundamental occurrences inseparably involved with machining that damage the effectiveness of cutting tools. Another factor in milling tool underperformance is that most inserts have four edges. The reason for having four edges is that, when one edge becomes dulled or chipped, it’s an easy process to rotate or replace the tip. However, the insert’s corners, between the flat edges, are its weakest parts. These radial edges are designed differently to the insert’s flat edges. They are often placed in the cutting zone and, as a consequence, frequently break first. These are the issues Sandvik Coromant’s specialists kept in mind while designing a next generation tool that would meet the stringent requirements of a variety of sectors. Crucially, the invention needed to reduce the number of tools, changeovers and tool handling required during manufacturing, for reduced cycle times and improved manufacturing economics. The result was CoroMill MH20, a new high-feed milling cutter designed for milling cavities, or pockets, in ISO S, M and P materials.

Manufacturers are diversifying into new sectors, which means handling workpieces made from wider a range of materials.
Opportunity to innovate
The design of CoroMill MH20 has several innovations. They include a new cutter body material, used for the cylindrical shank bodies, that gives levels of stiffness not seen before in this type of tool. The material minimizes wear and tear during machining and also reduces chip rubbing and coining ― when high stress caused by high cutting forces causes plastic deformation on the insert seat. With this feature, the tip seat remains secure and undeformed which provides better tool life. Next, we have an alternative to the aforementioned four-edge concept: CoroMill® MH20 is designed with a two-edge insert. With the two-edge concept, machining against a corner or wall will not impact the next edge or leading corner, giving an equal performance per edge. The advantages are greater reliability and protection against wear. The edge line of the insert’s main cutting edge and corner radius are also optimized for further process security. Another area of innovation is CoroMill MH20’s insert cutting edge geometry. For the first time in high feed concepts, Sandvik Coromant is introducing dedicated insert geometries for different ISO areas to deliver greater optimized process security and productivity. With CoroMill MH20, a sloped edge design delivers a gradual and lightcutting action, requiring less power consumption suited to the use of smaller machines. Sandvik Coromant’s CoroMill MH20 has exhibited substantiallyimproved tool life over previous-generation tools for its customers — up to 30% in some cases, although this performance will always differ depending on the material. Precision machining
One Sandvik Coromant customer, a large machine shop in Canada that specialises in mold and die manufacturing, wished to upgrade its existing tooling setup. The customer had been using a competitor’s tool, which had been suffering from vibrations that made machining processes unpredictable and insecure. To resolve these issues, the machine shop turned to Sandvik Coromant to test the performance of CoroMill MH20 against its existing tool. Both tools were used to perform rough pocketing on a workpiece made from H13, a popular chromium hot-work steel known for its high toughness and fatigue resistance, to produce a mold. Each milling tool measured 25.4mm (1 inch) and was run at a cutting speed (vc) of 168m/min (550 surface ft/min). CoroMill MH20 was run at a slightly higher feed rate with two inserts, because this allowed the depth of cut to be increased by 35%. The parameters were: a feed per tooth (fz) of 1 mm/tooth (0.04 inch/tooth), feed speed (vf) of 5,080mm/min (200 inch/min) and axial depth of cut (ap) of 0.8mm (0.031 inch). The competing tool was run at an fz of 0.63mm/tooth (0.025 inch/ tooth), vf of 4572mm/min (180 inch/mm) and ap of 0.5mm (0.020 inch). Both tools were run until they showed signs of flank wear. Despite the higher cutting parameters, CoroMill MH20 finished a complete component with no indexing, and a superior surface finish. It exhibited at 50% tool life increase by running for 300 mins, with a 50% cycle time reduction. The competing tool, meanwhile, ran for half the amount of time at 150 min. It required additional indexing because of poor tool life, which further increased the cycle times. The competitor’s insert again suffered from vibrations that caused screws to back out during machining. By upgrading to CoroMill MH20, the customer has achieved a significantly improved tool life and more secure, vibration-free machining processes. Even if, as PwC observes, disruption is the only constant in today’s industrial manufacturing environment, new tooling innovations like CoroMill MH20 support improved tool life and process security. This greatly benefits manufacturers’ competitiveness. sandvik.coromant.com
The CoroMill® MH20, a new high-feed milling cutter from Sandvik Coromant, is designed for milling cavities, or pockets, in ISO S, M and P materials.
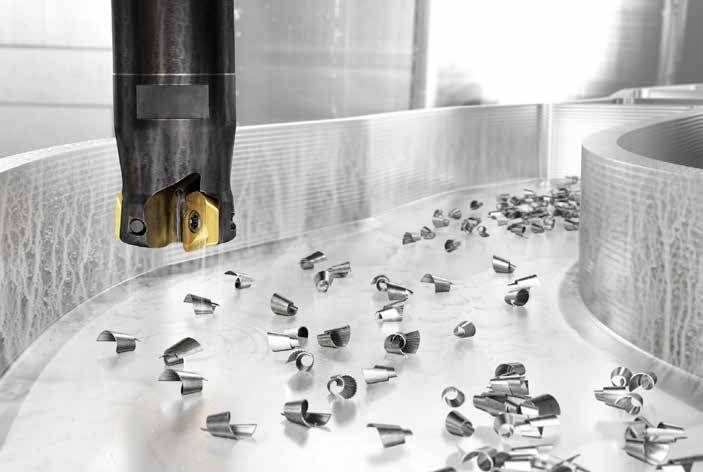