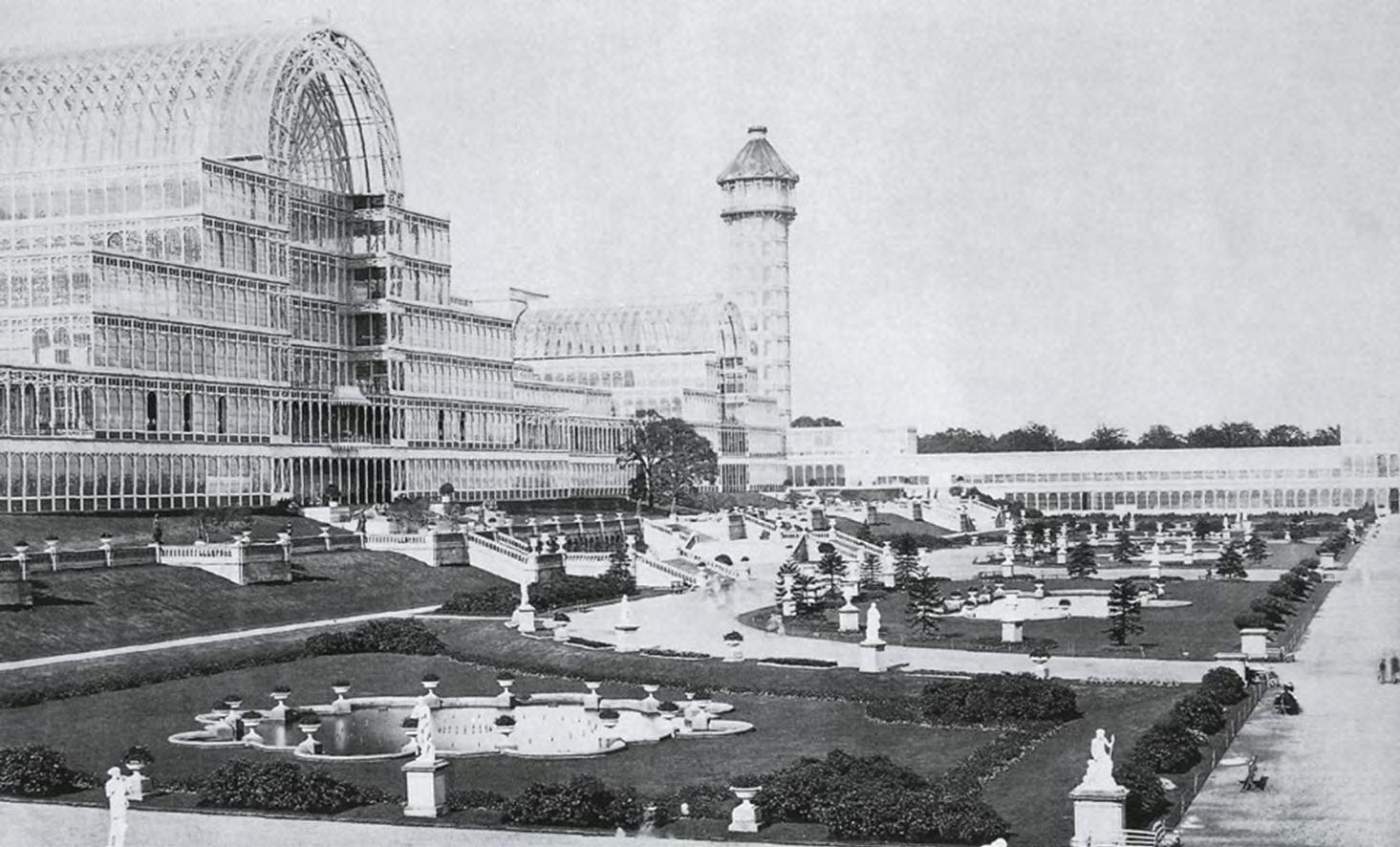
20 minute read
Innovation scenarios in the glass industry in Europe
LUCA TRULLIA
The following article is part of broader doctoral research conducted by the author, concerning innovation and technologies developed in the glass sector. Thus far, glass is one of the most widely used materials in the construction field. The extent of the use of this material is related to the innovations that have transformed the glass industry throughout history, from the industrial process to the final product. The proposed paper aims to retrace past and present innovations through the acknowledgment of contemporary demands with a view to possible future developments of glass, by analysing the current sectoral targets and the critical issues that claim for the development of new models, to reduce the environmental impact of the entire glass life cycle.
A Department of Architecture, Roma Tre University, Italy.
KEYWORDS: GLASS, RECYCLE, INNOVATION
The birth of glass: first applications and processing techniques
The historical reconstruction of the evolution and use of glass by man in architecture is an articulated path that goes beyond the discovery of the material itself and involves, throughout history, investments in research and development, political-strategic decisions, stories of innovation, and the evolution of architectural movements. The origins of this material, as reported by Plinius the Elder (23-79 A.D.) in his encyclopaedic text Naturalis Historia (77-78 A.D.), are due to “natrum” traders who, lighting a makeshift fire on the banks of the Belo River, in Syria, melted its silty sand with the blocks of natrum, generating the release of the first glassy mixture and tracing the origins of this discovery back to a fortuitous case. Since its discovery as a precious material derived from a fusion process, but even earlier as a material of volcanic origin such as obsidian, the use of glass was an elitist prerogative of higher social classes. The first processing techniques can be traced back to the 3rd Century B.C., when Syrian artisans, by introducing the glass-blowing system using an hollow pipe, began to understand the various possible transformation processes of the glass mass, expanding its diffusion to a broader segment of the population (Baratta, 2020). The first process innovations can be dated to the first centuries A.D., when the Romans, by modifying the composition of the vitreous mixture with the addition of oxides, enhanced the transparency of the material, increasing its possible uses. The use of glass achieved resounding success among the Romans, who often used it for mosaics, experimenting with various systems of coloring and discoloration as well as with production, by using the first examples of casting. The first architectural uses of glass can be found in the villas of Pompeii and Herculaneum on wooden frames with limited dimensions of 30 x 50 cm and a thickness of 3 to 6 cm (Schittich et al., 1999). The Roman artistry and use of this material were so relevant to be spread even beyond the Alps. In the Middle Ages, the first guilds were born to guarantee the secrecy of glass processing techniques. In 1291, Venice placed the production and processing of glass on the island of Murano, which became the most important centre in the world between the 15th and 17th centuries. During the Middle Ages, further production centres were born in Italy between Tuscany and Liguria, and new manufacturing methods were developed employing ball-blowing and cylinder-blowing. During these centuries, the production techniques of the various master glassmakers began to have a European spread. The Manufacture Royale des glaces à miroirs was born in the small town of Saint-Gobain (FR) in October 1665, at the behest of King Louis XIV and on the initiative of the finance minister J.B. Colbert, to weaken the Venetian domination of glass. This fact guaranteed financier Nicolas Dunoyer and his partners protections and renewable tax exemptions for twenty years for the production of mirrors. (Saint-Gobain, 2022). Developments in processing
techniques, such as that of casting evolved in 1687 by the Frenchman Perrot, extended the boundaries of glass production to other countries. This material, although still very expensive, began to spread in various countries such as England and Germany, subsequently extending into non-European states such as Ohio (USA), becoming, from the latter half of the 19th Century, an increasingly central element in daily life also thanks to the first worldwide events and earliest systems of industrialization.
The innovations of the twentieth Century
The product and process innovations that characterized the 20th Century have allowed a real breakthrough in the production system of flat glass and its applications in the architectural field. New production systems and new plants for secondary processing have expanded the spread of its use on a global scale, by improving the quality of the product and its properties, contributing to the development of new technologies.
The most important process innovation is certainly the one made by Sir Alastair Pilkington in 1952. The actual innovation introduced by Pilkington, which still represents the modern flat glass production system, consisted in making the vitreous mixture float on a 7 cm thick molten tin bath, after the phases of melting, refining, rest, and conditioning. This advancement allowed the glass mixture to obtain two perfectly coplanar faces of the final slab, the lower one obtained from contact with the tin and the upper one due to the effect of gravity and heat. This system has completely transformed the flat glass supply chain by increasing the quality of the final product, allowing the elimination of further processing aimed at obtaining greater transparency and guaranteeing a significant increase in the size of the plates produced, reaching 6 x 3.21 m. Through the introduction of this new glass production system, there is a shift in the design approach to this material, allowing the creation of works that were previously unrealizable due to the absence of this technology.
The fragility and the quality of the final product have always been two crucial aspects of this material. Before the system introduced by Pilkington and called “float glass”, the production of flat glass, and hence its possible applications, were strongly conditioned by the dimensions of the glass itself and by the subsequent processing necessary to obtain a high-quality product. From the second half of the 18th Century, thanks to the first major global events, glass began to arouse the interest of designers and beyond. Among the most iconic uses of glass in the 19th Century, the Crystal Palace is certainly its maximum expression. Made for the Great Exhibition held in London in 1851, this glass building was designed by Joseph Paxton in collaboration with the engineer Charles Fox and was meant to host the event. The importance of this exhibition, being the first in history, prompted the designer to create a
Fig. 01 Historical photo of the Crystal Palace. Wikicommons
90,000-square meters building, entirely made of steel and glass. The success of this project, besides Paxton’s great capability, was possible thanks to the product and process innovations that the brothers Robert Lucas (1782-1865) and William Chance (1788-1856), of the Chance Brothers Company, brought to their manufacturing system to make the glass of the Crystal Palace.
The London Great Exhibition of 1851 marked the introduction of new building typologies, these being an expression of the development of new technologies, the change of cities, and the way citizens established relations with them. By responding to a new need induced by new trades and manufacturing systems, the industrialization of the city had been a driving force for its development. In these new structures, such as stations, factories, and large pavilions, glass played a central role in the natural lighting of the spaces. The spread of the use of this material, subsequently to the Great Exhibition, profoundly marked the entire 20th Century, characterizing the language of the Modern Movement which gave the glass a strong expressive feature.
The first thirty years of the 20th Century are indeed characterized by two of the most important product innovations made with this material: laminated glass and tempered glass. These techniques, by improving the safety of its application and increasing its mechanical strength, have allowed the use of glass in solutions previously not feasible, with the consequent development of new technologies. The laminated glass, patented in 1903, has been formulated by the French chemist Edouard Benedictus (1878 – 1930), who understood the potential of the interposition of a plastic layer between the
glasses to seal post-break fragments after a laboratory accident. The first uses of this new technology saw the automotive sector as the leading one, which employed it for the replacement of windshields, previously made of annealed glasses, and only later in the building trades. The second product innovation is the one made by the French company Saint-Gobain which, in 1929, began producing safety glasses through the tempering process (Schittich et al., 1999). These two pivot innovations have increased the use of glass in architecture, paving the way for its use as an element for curtain walls or structural glazing, which still uses these two types of glass.
Innovation processes, whether they regard the product or the process, are actions that often respond to an exogenous need induced by the global market. Following the energy crisis of 1973, the approaches to design and particularly the attention to technology, have led to product and process innovations aimed at increasing the performance of products. Within this context, which closely links the economy to the building trade, low-emissivity glass has been developed through incremental innovation. This type of glass is obtained by placing a metallic deposit on one of the two surfaces of the glass. This specific procedure can be carried out during the production of flat glass, through a pyrolysis process, or subsequently through a process called Magnetron Sputtering Deposition (Baratta, 2020). The latter, carried out after the production of the glass sheet, is the most used method to produce lowemission glasses for double-glazing.
These innovations, which characterized the glass sector in the 20th Century, have allowed the spread and use of this material, allowing it to be one of the most used in the building trade due to its qualities and characteristics. The importance and employment of this material are likely to constitute about 50% of the envelope of a building, rising to higher percentages in solutions where the envelope is completely entrusted to technologies that employ this material (Trulli, 2021).
Research and development: new technological solutions using glass
The overall framework of flat glass production is composed of more than 500 furnaces with a production of over 100 million tons and a market of above 270 billion dollars in 2021 (Grand View Research, 2021).
The distribution of the production sites sees the Asian continent as the leading one, gathering about half of the worldwide plants, far more than the 48 plants dependent on the ETS, which are located in Europe (Glass for Europe, 2020), producing over 10 million tons of flat glass every year with a turnover of more than 15 billion euros. Alongside the large numbers of turnover and production, the glass sector is one of the ones with the greatest investments in research and development. In Italy alone, approximately 300 million euros were invested in plants in 2018, keeping an active focus on its updating and possible innovations (Assovetro, 2020). Over the last decades,
these huge investments in product, process, and proceeding innovation have led to increasingly performing products, capable of responding to the performance needs dictated by the market.
At the end of the seventies of the 20th Century, many architects began to develop theories on the adaptability of the envelope in response to different climatic conditions. Among the many, Richard Rogers, one of the leading exponents of the hi-tech current, argues that “the skin of the building must be like a chameleon”, that is a skin capable of adapting to different needs (Stevens, 1980, p. 705). In this context began reflections and experimentations on materials capable of changing their performance or appearance, while conditioning the indoor comfort. Among the leading products developed in this direction, chromogenic glasses have contributed to the “chameleon transformation” of a building. Over the last 20 years, following the low-emissive, selective, or reflective solutions, these types of glasses have increasingly seen their use in architectural solutions (Andreotti, 2009). Among the first ones to understand the potential of these materials were Carl Lambert and Claes-Goran Granqvist, who, during the International Congress of Optical Science and Engineering held in Hamburg in 1988, underlined the importance of these materials for their ability to regulate energy flows in the possible applications in doors and windows and envelopes (Lampert and Granqvis, 1990).
These types of glasses can be distinguished between two macro families, based on the activation system. The first, which concerns thermochromic and photochromic glasses, does not need electrical activation and can selfregulate according to the temperature and intensity of the light. The second type is that of electrochromic glasses, which change their state of transparency through an electrical impulse that intervenes on the electrochromic film.
Over the last three decades, the greater energetic efficiency required from the building heritage has characterized many technological areas,
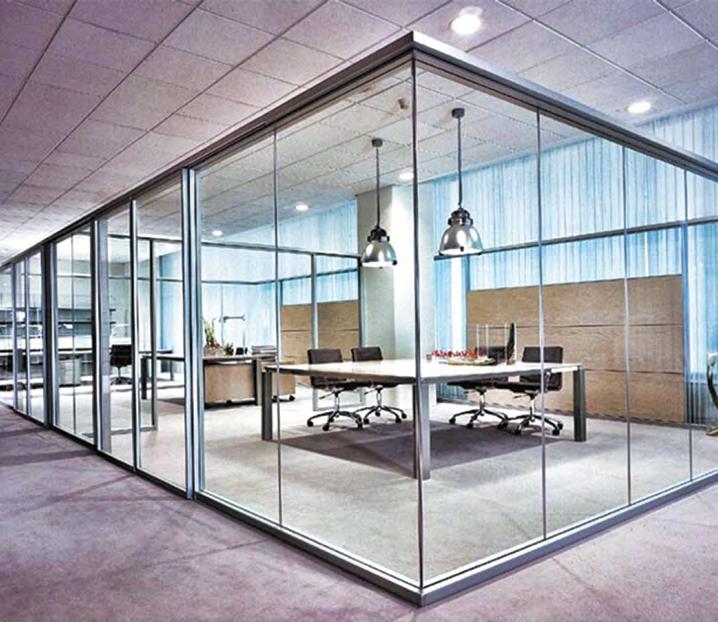
Fig. 02 Electrochromic glass activation. Glassfilm
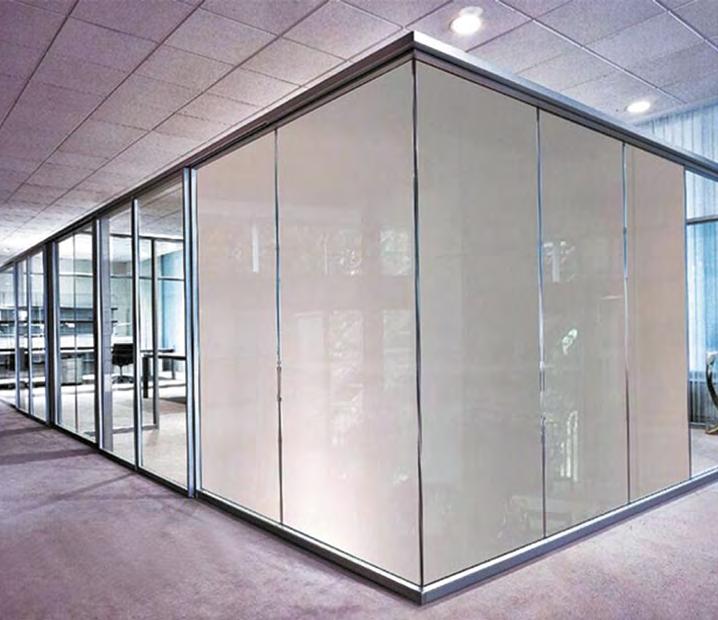
encouraging research towards the development of new and increasingly efficient materials. This research, which in some cases has seen the technology transfer from other industries such as the aerospace one, has now led to high-performance technologies. In the glass sector, this need has led to the development of products that see the combination of previously described technologies, such as double glazing with lowemission glasses, and phase-changing materials (PCM). This product innovation is achieved by placing PCMs, like the most common paraffin, within the space left between the two or more glasses. These phasechanging materials, manage to modify their state with the variation of the temperature and can accumulate and release thermal energy, achieving excellent performance in environments where the temperatures and their variations are very large. The diffusion of these glasses on a large scale in the architectural field is currently seeing its first uses but, even today, the high cost of these technologies affects their usage.
Among some of the most recent developments are the experiments for the production of vacuum glasses. The innovation introduced for these glasses exploits the principle of double-glazing but reduces its overall thickness. The substantial difference between double-glazing and vacuum glass is that, in the first case, the glasses are separated by a “duct” sealed on the perimeter in different types of materials, and in the space generated by this duct is placed a gas, generally argon or krypton. These double-glazing units, used in all modern windows with double or triple-glazing solutions, can reach up to an overall thickness of 45-50 mm to obtain good transmittance characteristics. The innovation introduced by vacuum glasses is the elimination of this space between the glasses, reducing it to thicknesses equal to fractions of a millimetre. This glass, which currently has an overall thickness of 6.2, 8.2, and 10.2 mm, is comparable in thickness to a single glass used in double glazing.
The difference is that within this glass thickness of 6.2 mm, made with two glasses of 3 mm, there is a space of 0.2 mm placed under vacuum. This space, even if smaller than a millimetre, can give these “single” glasses high thermal characteristics, with a transmittance that can even reach Ug = 0.7 W/m2K for thicknesses of 10.2 mm (Pilkington, 2022). The advantages that this product innovation has introduced are several, from the total weight reduction of a single window, with a consequent saving of material, to the application of these glasses in contexts of historical and cultural value. This technology, which has been used for years in Japan, must deal with some of its great limitations that have not been promptly settled. Currently, low-emissivity vacuum glasses can reach a maximum production size of 150 x 250 cm, restricting the possible uses in large solutions with wider frames. Further critical issues, which have to be solved, are the presence between the two glasses of small spacers that are not perfectly transparent but are necessary
in order to avoid contact of the two plates when these are placed under a vacuum, and the currently still very high cost, compared to the ongoing technologies.
The European goals: engine for an ecological transition
Among the goals imposed by the European Union for the reduction of 55% of greenhouse gases by 2030, to become the first climate-neutral continent in 2050 (European Commission, 2021), glass plays a leading role. According to the report drawn up by the Building Performance Institute Europe, the condition of about 75% of buildings in Europe is inefficient from an energetic point of view, and measures will be required in more than 90% of the buildings to reach the 2050 goals (BPIE, 2017). These measures will necessarily intervene on the envelopes of the buildings themselves, affecting all the transparent parts that are now inefficient. According to an estimate conducted by the European Commission, the average performance of windows and doors in Europe is equivalent to Uw 3.4 W/m2K (Glass for Europe, 2020), still far from the values returned by the most recent product innovations for these technologies. The interventions, necessary for this energy efficiency, will trigger a total or partial replacement of the current doors and windows, returning an enormous amount of materials destined for recycling. The glass recycling system is among the most active and efficient in Europe. In 2019, according to the European Container Glass Federation (FEVE), the average rate of hollow glass collection for recycling in Europe reached 78% of the total (FEVE, 2021). These percentages, because of the 2030 European goals, aim to reach 90% of the total weight of products placed on the market, thanks to the expansion of the network of stakeholders involved in the recycling process. The quantity of glass produced in Europe, in the year 2020, exceeded 35 million tons. Of this amount, about 22 million tons are hollow glasses, such as containers and bottles, and just under 11 million are flat glasses, with the residual quantity addressed to the market of domestic glass, wool, and rows (Glass Alliance Europe, 2022). The percentage data related to the glass recycling rate in Europe, as previously reported, only consider the recycling of hollow glass, returning a strong interest in recycling but giving an inaccurate view of the amount of recycled flat glass. Flat glass, unlike hollow glass, poses greater difficulties in recycling due to the high quality required by aspects such as transparency.
The presence of polymeric layers, such as polyvinyl butyral, or silicone materials, makes its recycling for reuse as a secondary raw material a process that is still developing. Another aspect that differentiates hollow glass from flat glass is the duration and permanence time of the two different products, as the flat glass used for windows has a life cycle of about 20-30 years before being removed and destined for a recycling process.
Conclusion
Investments in research and development in this sector have led, over the years, to increasingly performing products with a view to energy and material saving.
The European green deal, with its targeted goals, will be the main engine for a gradual efficiency improvement of the present buildings (European Commission, 2018), with the replacement of millions of tons of glass that will necessarily have to be put into a recycling process. These aspects, closely linked to each other, must aim at the development of two main aspects: • the increase of the recycling procedure of flat glass with process innovations aimed at eliminating polluting materials and reusing it as a secondary raw material, increasing the percentages of reuse in the production process, currently between 25% and 40%, with a consequent reduction of extractions for the supply of raw materials; • the encouragement in the use of high-performance technologies such as vacuum glasses, phase-change glasses, and chromogenic glasses, contributing to the enhancement and further development of these and normalisation of costs for use.
The replacement of doors and windows with new products suited to the new needs as well as the recycling of outdated materials will be just two of the strategies the glass supply chain will need to pursue in order to contribute to the achievement of European goals. Considering Europe, current flat glass production systems affect 0.65% of the CO2 industrial emissions: a very low percentage, which can be further reduced.
In Italy, the Divina project was born in 2021, which sees the collaboration of public and private bodies to reduce CO2 emissions through the use of a hydrogen-natural gas mix for the production of glass (SNAM, 2021). This process innovation, even if at the beginning, has opened a way toward the possible future uses of new energy sources for a lower environmental impact. This “circular” system, besides reaching the goal of making the glass production process, its use, and recycling a closed system, would certainly be a driving force for the economy in the construction sector, dragging further interventions aimed at improving the efficiency of envelopes towards buildings with ever lower emissions. Only in Italy, according to what was reported by the National Union of Metallic Construction Industries of the Envelope and Windows (UNICMI) based on Istat data, in 2021 the sector of doors and windows and curtain walls for both residential and non-residential buildings, has generated demand for equal to € 5.2 billion.
Further future developments of glass extend beyond its classic known uses, thanks to research conducted by institutes and academics concerning the use of recycled glass as a replacement for fine aggregates in mortars and concretes. In the last decade, research such as those conducted by professors Luigi Mollo and Rosa Agliata of the University of Campania “Luigi Vanvitelli” on
the use of recycled glass as a substitute for fine aggregates in mortars, has shown how this new design mix exceeded the mechanical requirements of the NTC 2008 (Mollo and Agliata, 2015).
The evolution that this material has had throughout history, with its countless technological and scientific innovations, leads today to materials and technologies with very high performance used in various sectors in addition to construction. Millions of euros in annual investments show how much attention is paid to this sector, which daily improves its products and processes in an incremental perspective for its performance and reduction for the environmental impact.
References
Andreotti, G. (2009). Il vetro. In Sinopoli, N., Tatano, V. (ed.), Sulle tracce dell’innovazione: tra tecniche e architettura. Milano: Franco Angeli, pp. 175-186. Assovetro (2020). Rapporto di sostenibilità 2020 (online). In https://www.assovetro.it/wp-content/uploads/2020/02/report-completo-low-min2.pdf (last accessed August 2022). Baratta, A. F. L. (2020). Materiali per l’architettura. Napoli: Clean. Building Performance Institute Europe – BPIE (2017). State of the building stock (online). In https://www.bpie.eu/wp-content/ uploads/2017/12/State-of-the-building-stock-briefing_Dic6.pdf (last accessed August 2022). European Commission (2018). A Clean Planet for all: A European strategic long-term vision for a prosperous, modern, competitive and climate neutral economy (online). In https://eur-lex.europa.eu/legal-content/EN/TXT/?uri=CELEX%3A52018DC0773 (last accessed August 2022). European Commission (2021). Green Deal europeo: La Commissione propone di trasformare l’economia e la società dell’UE al fine di concretizzare le ambizioni in materia di clima (online). In www.ec.europa.eu/commission/presscorner/detail/it/ ip_21_3541 (last accessed May 2022). FEVE (2021). La raccolta record di contenitori di vetro per il riciclaggio raggiunge il 78% nell’UE (online). In https://www.federvini.it/studi-e-ricerche-cat/3860-ricerca-bottiglie-in-vetro-piu-sostenibili-del-bag-in-box (last accessed May 2022). Glass Alliance Europe (2022). GAE Glass Production (online). In www.glassallianceeurope.eu/images/cont/gae-glass-production-2021_file.pdf (last accessed May 2022). Glass for Europe (2020). 2050. Il vetro piano nell’Europa a emissioni zero (online). In https://glassforeurope.com/wp-content/ uploads/2020/10/Decarb_broch_ITALIAN_for_WEB.pdf (last accessed May 2022). Grand View Research (2021). Flat glass market size & share report, 2022-2030 (online). In www.grandviewresearch.com/industry-analysis/global-flat-glass-market# (last accessed May 2022). Lampert, C. M., Granqvist, C. G. (1990). Large-area chromogenics: Materials and devices for transmittance control. Volume IS 4. United States. Mollo, L., Agliata, R. (2015). Il rottame di vetro: da rifiuto a risorsa. In Baratta, A. F. L., Catalano, A. (ed.), Il riciclaggio come pratica virtuosa per il progetto sostenibile. Pisa: ETS, pp.158-171. Pilkington (2022). Pilkington Spacia (online). In https://www.pilkington.com/it-it/it/prodotti/categorie-prodotti/isolamento-termico/pilkington-spacia (last accessed May 2022). Saint-Gobain (2022). 1655: Louis XIV fonde la Manifacture royale des glaces à miroirs à l’instigation de son ministre Colbert (online). In https://archives.saint-gobain.com/ressource/xviie/1665/1665-louis-xiv-fonde-la-manufacture-royale-desglaces-miroirs-linstigation-de (last accessed May 2022). Schittich, C., Staib, G., Sobek, W., Schuler, M., Balkow, D. (1999). Atlante del vetro. Torino: Utet. Snam (2021). Idrogeno: avviato progetto italiano per la decarbonizzazione dell’industria del vetro (online). In www.snam.it/ export/sites/snam-rp/repository/file/Media/Comunicati_stampa/2021/CS-Divina_RINA_Snam_BORMIOLI.pdf (last accessed May 2022). Stevens, T. (1980). Putting the tech into architecture. New scientist, vol. 88, No 1231. London: Reed Business Information Ltd, pp. 704-706. Trulli, L. (2021). Il riciclaggio come propulsore innovativo nel settore produttivo del vetro. In Baratta, A. F. L. (ed.), PRE|FREE – UP|DOWN – RE|CYCLE Traditional solutions and innovative technologies for the end of waste, 4th International Conference. Conegliano: Anteferma, pp.182-193.