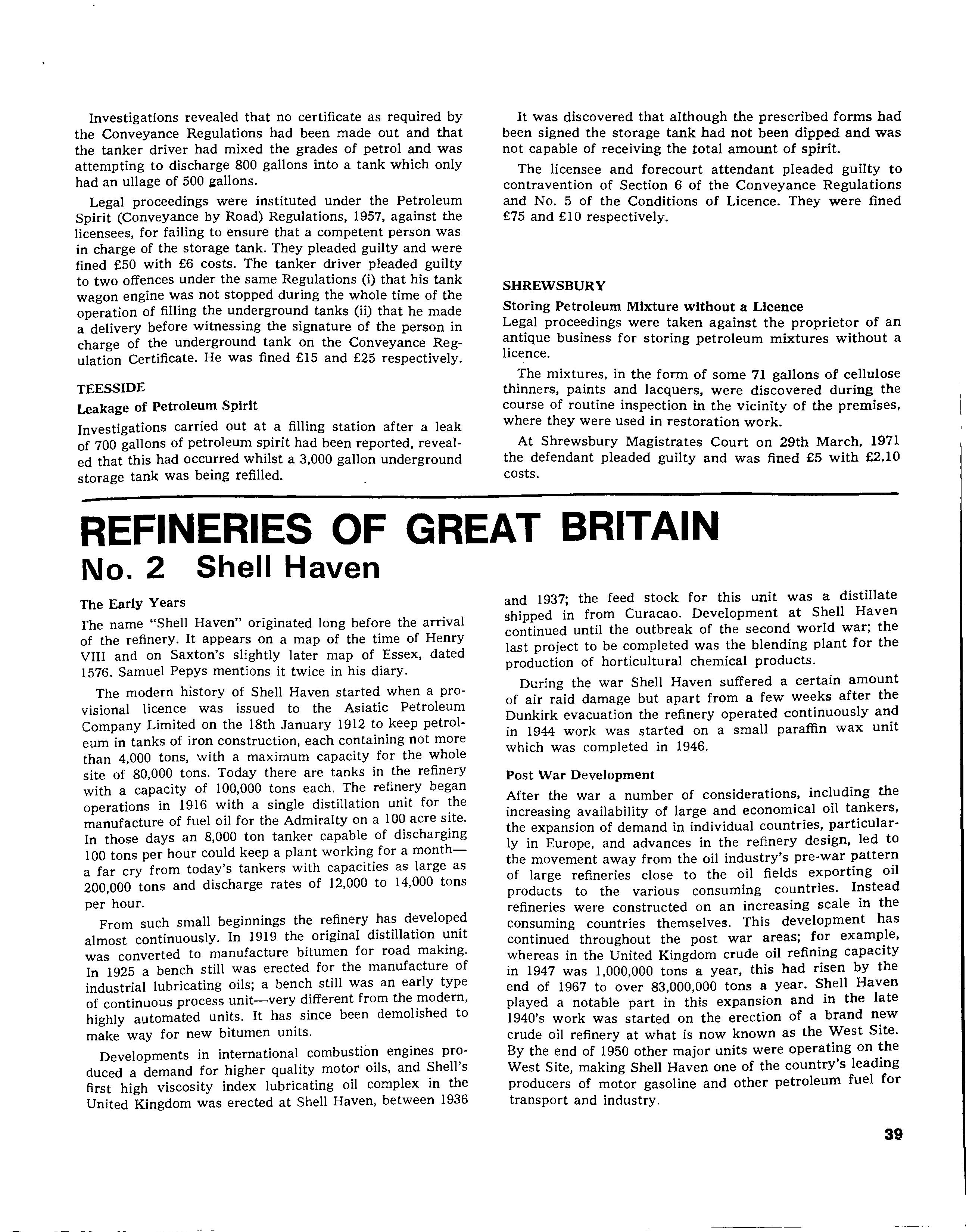
10 minute read
Refineries of Great Britain
from The Bulletin – April 1971
by apeauk
Investigations revealed that no certificate as required by the Conveyance Regulations had been made out and that the tanker driver had mixed the grades of petrol and was attempting to discharge 800 gallons into a tank which only had an ullage of 500 2allons.
Legal proceedings were instituted under the Petroleum Spirit (Conveyance by Road) Regulations, 1957, against the licensees, for failing to ensure that a competent person was in charge of the storage tank. They pleaded guilty and were fined £50 with £6 costs. The tanker driver pleaded guilty to two offences under the same Regulations (i) that his tank wagon engine was not stopped during the whole time of the operation of filling the underground tanks (ii) that he made a delivery before witnessing the signature of the person in charge of the underground tank on the Conveyance Regulation Certificate. He was fined £15 and £25 respectively.
Advertisement
TEESSIDE Leakage of Petroleum Spirit Investigations carried out at a filling station after a leak of 700 gallons of petroleum spirit had been reported, revealed that this had occurred whilst a 3,000 gallon underground storage tank was being refilled.
It was discovered that although the prescribed forms had been signed the storage tank had not been dipped and was not capable of receiving the total amount of spirit.
The licensee and forecourt attendant pleaded guilty to contravention of Section 6 of the Conveyance Regulations and No. 5 of the Conditions of Licence. They were fined £75 and £10 respectively.
SHREWSBURY Storing Petroleum Mixture without a Licence Legal proceedings were taken against the proprietor of an antique business for storing petroleum mixtures without a licence.
The mixtures, in the form of some 71 gallons of cellulose thinners, paints and lacquers, were discovered during the course of routine inspection in the vicinity of the premises, where they were used in restoration work.
At Shrewsbury Magistrates Court on 29th March, 1971 the defendant pleaded guilty and was fined £5 with £2.10 costs.
No. 2 Shell Haven
The Early Years The name "Shell Haven" originated long before the arrival of the refinery. It appears on a map of the time of Henry VIII and on Saxton's slightly later map of Essex, dated 1576. Samuel Pepys mentions it twice in his diary.
The modern history of Shell Haven started when a provisional licence was issued to the Asiatic Petroleum Company Limited on the 18th January 1912 to keep petroleum in tanks of iron construction, each containing not more than 4,000 tons, with a maximum capacity for the whole site of 80,000 tons. Today there are tanks in the refinery with a capacity of 100,000 tons each. The refinery began operations in 1916 with a single distillation unit for manufacture of fuel oil for the Admiralty on a 100 acre site. In those days an 8,000 ton tanker capable of discharging 100 tons per hour could keep a plant working for a montha far cry from today's tankers with capacities as large as 200,000 tons and discharge rates of 12,000 to 14,000 tons per hour.
From such small beginnings the refinery has developed almost continuously. In 1919 the original distillation unit was converted to manufacture bitumen for road making. In 1925 a bench still was erected for the manufacture of industrial lubricating oils; a bench still was an early type of continuous process unit-very different from the modern, highly automated units. It has since been demolished to make way for new bitumen units.
Developments in international combustion engines produced a demand for higher quality motor oils, and Shell's first high viscosity index lubricating oil complex in the United Kingdom was erected at Shell Haven, between 1936 and 1937; the feed stock for this unit was a distillate shipped in from Curacao. Development at Shell Haven continued until the outbreak of the second world war; the last project to be completed was the blending plant for the production of horticultural chemical products.
During the war Shell Haven suffered a certain amount of air raid damage but apart from a few weeks after the Dunkirk evacuation the refinery operated continuously and in 1944 work was started on a small paraffin wax unit which was completed in 1946.
Post War Development After the war a number of considerations, including the increasing availability of large and economical oil tankers, the expansion of demand in individual countries, particularly in Europe, and advances in the refinery design, led to the movement away from the oil industry's pre-war pattern of large refineries close to the oil fields exporting oil products to the various consuming countries. Instead refineries were constructed on an increasing scale in the consuming countries themselves. This development has continued throughout the post war areas; for example, whereas in the United Kingdom crude oil refining capacity in 1947 was 1,000,000 tons a year, this had risen by the end of 1967 to over 83,000,000 tons a year. Shell Haven played a notable part in this expansion and in the late 1940's work was started on the erection of a brand new crude oil refinery at what is now known as the West Site. By the end of 1950 other major units were operating on the West Site, making Shell Haven one of the country's leading producers of motor gasoline and other petroleum fuel for transport and industry.
39
The first of the units was a crude oil distillation unit which has been developed to process 15,000 tons per day. From this unit developed other major plants to deal with fractions produced. These include a high vacuum distillation unit, two platformer units and a hydrodesulphuriser unit. At the beginning of 1959 a major increase in the distillation capacity of the refinery resulted from the starting up of a second crude oil distilling unit, designed to meet the increasing demand for oil products.
In addition to the major process a unit, operating on specially imported feed stocks providing the basic materials for the manufacture of household and commercial detergents, was added to the complex.
It is obvious that a complex such as the Shell Haven Refinery must be supported by a number of ancillary services which are major items in themselves. The steam raising plant has a total capacity of nearly a million pounds of steam per hour. This steam is produced at pressures from 1,500 p.s.i. down to 250 p.s.i. generating 20 megawatts of electricity in the process.
Cooling water is used on a very large scale-about two and a half million gallons per hour, are pumped in from the River Thames through a 9' diameter tunnel.
The refinery never stops. Throughout the twenty-four hours for three hundred and sixty five days a year, its life blood-crude oil-is kept flowing through its many processes by a team of highly trained people, numbering more than 1,800.
With such a large amount of complex and explosive equipment to operate, training in safety and in the large number of operating and maintenance skills is a vital feature.
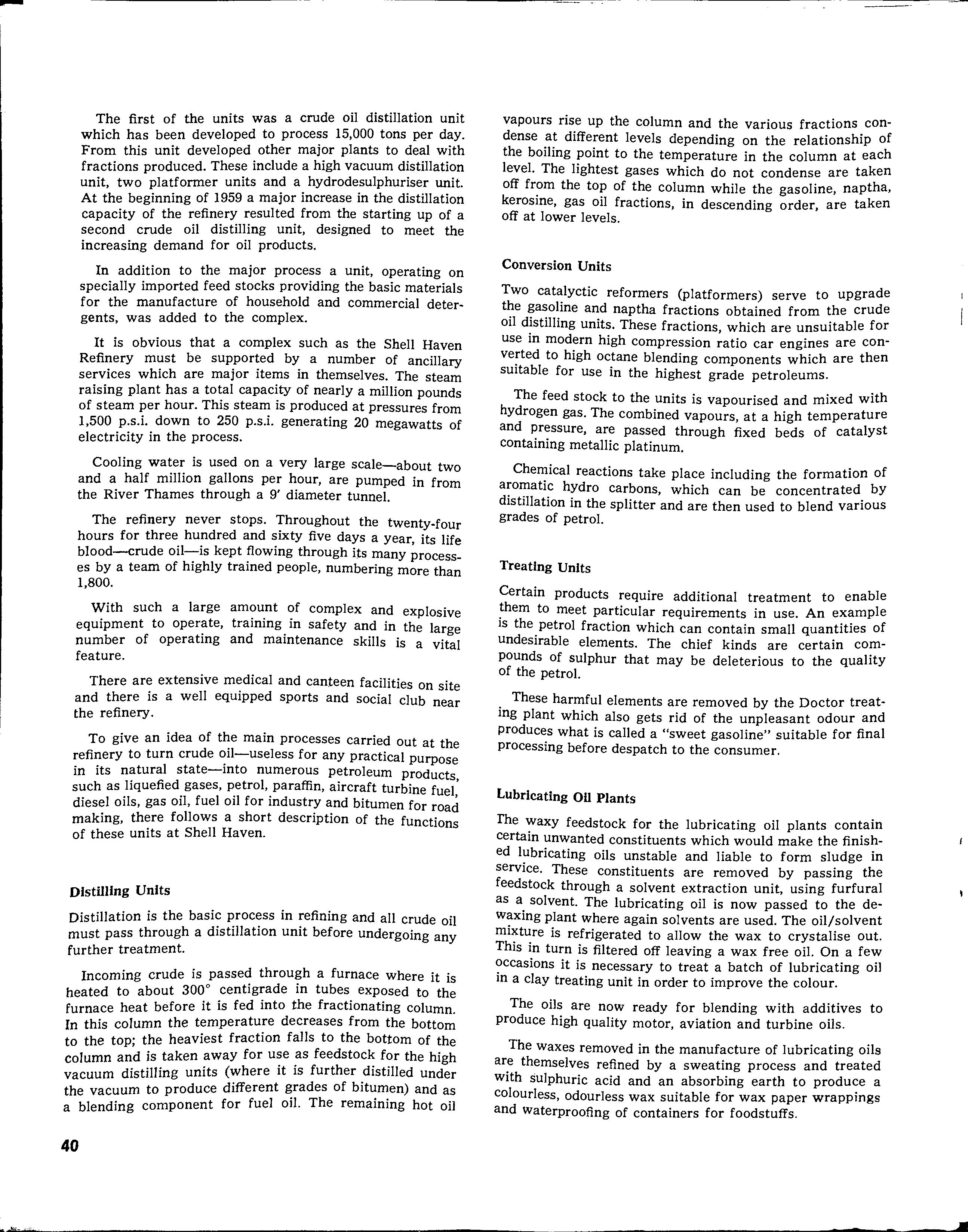
There are extensive medical and canteen facilities on site and there is a well equipped sports and social club near the refinery.
To give an idea of the main processes carried out at the refinery to turn crude oil-useless for any practical purpose in its natural state-into numerous petroleum products, such as liquefied gases, petrol, paraffin, aircraft turbine fuel diesel oils, gas oil, fuel oil for industry and bitumen for road making, there follows a short description of the functions of these units at Shell Haven.
Distilling Units Distillation is the basic process in refining and all crude oil must pass through a distillation unit before undergoing any further treatment.
Incoming crude is passed through a furnace where it is heated to about 300 0 centigrade in tubes exposed to the furnace heat before it is fed into the fractionating column. In this column the temperature decreases from the bottom to the top; the heaviest fraction falls to the bottom of the column and is taken away for use as feedstock for the high vacuum distilling units (where it is further distilled under the vacuum to produce different grades of bitumen) and as a blending component for fuel oil. The remaining hot oil vapours rise up the column and the various fractions condense at different levels depending on the relationship of the boiling point to the temperature in the column at each level. The lightest gases which do not condense are taken off from the top of the column while the gasoline, naptha, kerosine, gas oil fractions, in descending order, are taken off at lower levels.
Conversion Units
Two catalyctic reformers (platformers) serve to upgrade the gasoline and naptha fractions obtained from the crude oil distilling units. These fractions, which are unsuitable for use in modern high compression ratio car engines are converted to high octane blending components which are then suitable for use in the highest grade petroleums.
The feed stock to the units is vapourised and mixed with hydrogen gas. The combined vapours, at a high temperature and pressure, are passed through fixed beds of catalyst containing metallic platinum.
Chemical reactions take place including the formation of aromatic hydro carbons, which can be concentrated by distillation in the splitter and are then used to blend various grades of petrol.
Treating Units
Certain products require additional treatment to enable them to meet particular requirements in use. An example is the petrol fraction which can contain small quantities of undesirable elements. The chief kinds are certain compounds of sulphur that may be deleterious to the quality of the petrol.
These harmful elements are removed by the Doctor treating plant which also gets rid of the unpleasant odour and prodUces what is called a "sweet gasoline" suitable for final processing before despatch to the consumer.
Lubricating Oil Plants The waxy feedstock for the lubricating oil plants contain certain unwanted constituents which would make the finished lubricating oils unstable and liable to form sludge in service. These constituents are removed by passing the feedstock through a solvent extraction unit, using furfural as a solvent. The lubricating oil is now passed to the dewaxing plant where again solvents are used. The oil/solvent mixture is refrigerated to allow the wax to crystalise out. This in turn is filtered off leaving a wax free oil. On a few occasions it is necessary to treat a batch of lubricating oil in a clay treating unit in order to improve the colour.
The oils are now ready for blending with additives to produce high quality motor, aviation and turbine oils.
The waxes removed in the manufacture of lubricating oils are themselves refined by a sweating process and treated with sulphuric acid and an absorbing earth to produce a colourless, odourless wax suitable for wax paper wrappings and waterproofing of containers for foodstuffs.
Rapid Flashpoints
with the
LIMITED STATION ROAD CHER TSEY, SURREY ENGLAND
Telephone: Chertsey 4391 PRECISE determinations in a fraction of the time taken using conventional methods.
Produces a GO/NOT GO confirmation of critical flash point in ONE MINUTE. Correlates with ASTM-IP methods.
Requires only 2 ml. Sample. ACCURA TE-RELlABLE-PORTABLE
Telephone: EASt 0428

w. J. FINCH (Installations) Ltd.
Steam ing out and de-gassing petrol tanks; issuing gas free certificates Complete petrol and fuel oil bulk storage tank installations Petrol and fuel oil tank cleaning service Pressure testing tanks and pipe work
369 Victoria Road, Birmingham 6
DR. H. K. BLACK
(B.Sc., Ph.D., D.I.C., F.R.I.C.) Consulting Scientist
(Formerly H.M. Chief Inspector of Explosives, Home Office) 79 POPE'S AVENUE, TWICKENHAM, MIDDX. TELEPHONE: 01-894 5069
This is to announce that following my decision to retire from the post of Her Majesty's Chief Inspector of Explosives at the Home Office, London, I have entered into practice as a Consulting Scientist in the following fields of expertise: EXPLOSIVES: Manufacture, storage and conveyance. PE"IROLEUM: CONVEYANCE OF DANGEROUS CHEMICALS: GAS CYLINDERS AND PRESSURE VESSELS: INDUSTRIAL SAFETY : ACCIDENT INVESTIGATIONS. POLLUTION: EXPERT WITNESS: Storage; site design and lay-out; dispensing systems; licensing problems; conveyance. By road and other forms of transport; modern handling methods· port facilities and lay-out; bye-laws. ' For conveyance of dangerous substances by road. Explosion and fire hazards; general safety. Assessment of hazards; precautionary measures.
I am available for consultation at the above address.
EAST MIDLANDS
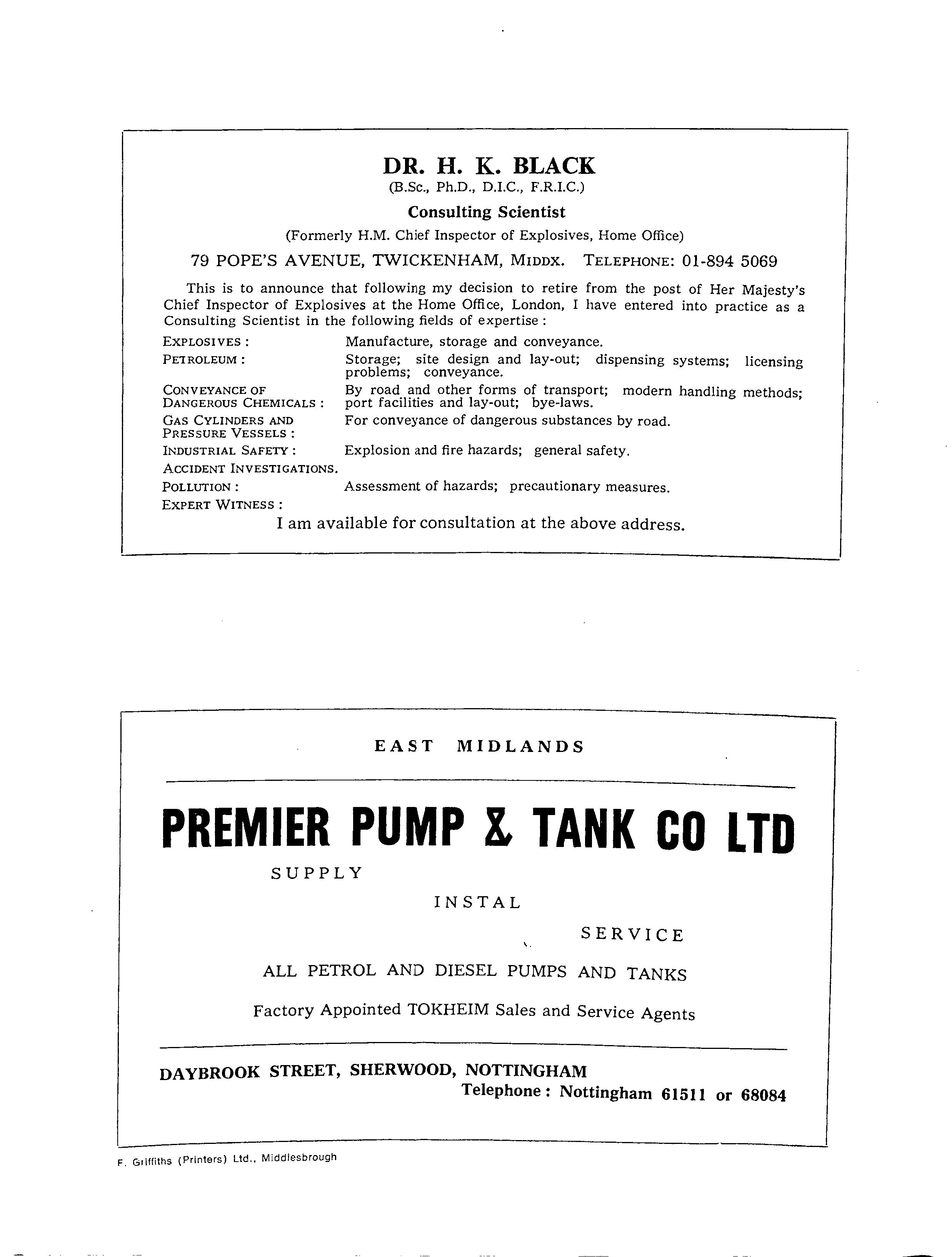
PREMIER PUMP 1 TANK CO LID
SUPPLY
INSTAL
SERVICE
ALL PETROL AND DIESEL PUMPS AND TANKS
Factory Appointed TOKHEIM Sales and Service Agents
DA YBROOK STREET, SHERWOOD, NOTTINGHAM Telephone: Nottingham 6151 I or 68084
F. Griffiths (Printers) Ltd .• Middlesbrough