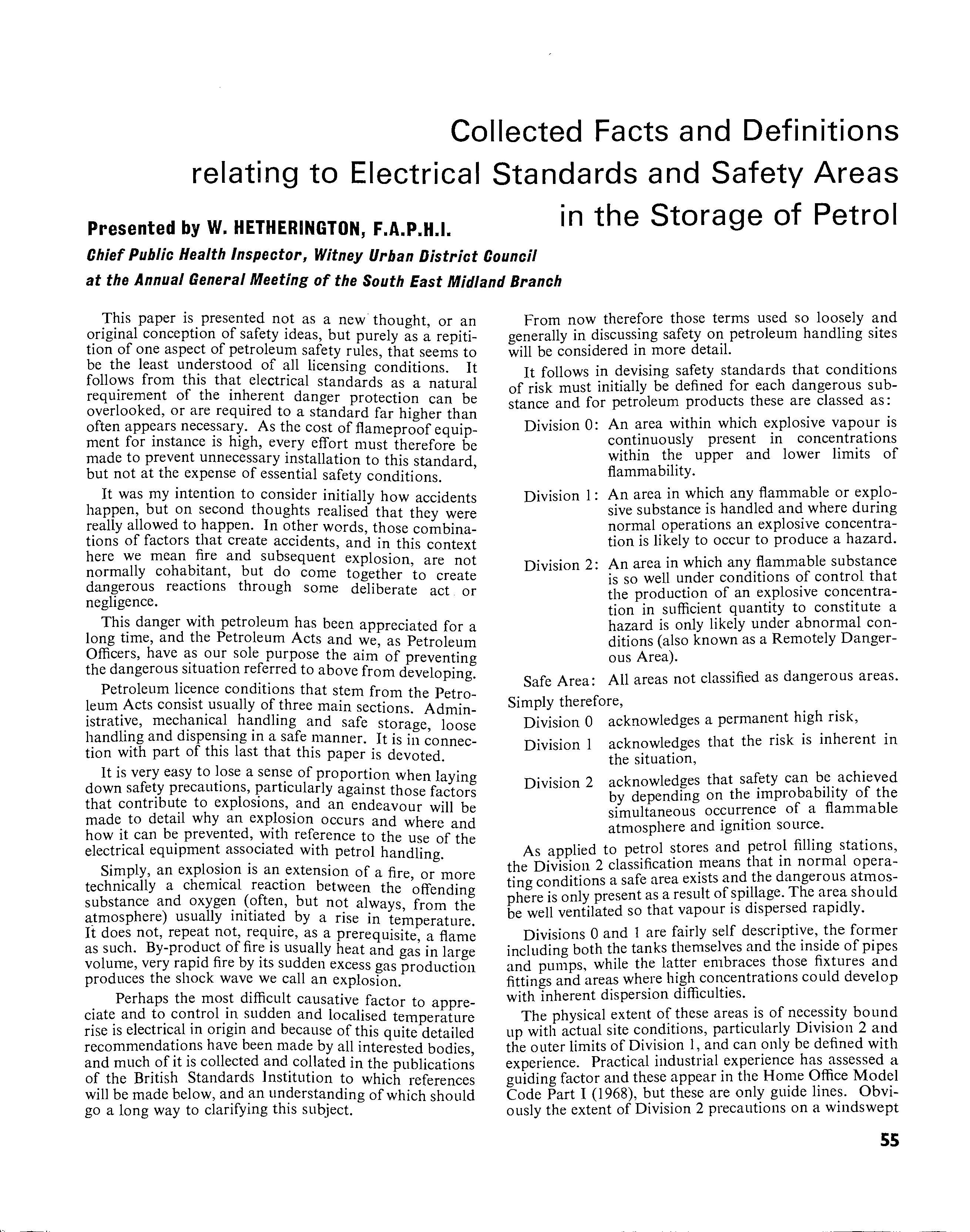
8 minute read
Collected facts and definitions relating to Electrical Standards and Safety Areas in the storage of petrol
by apeauk
Collected Facts and Definitions relating to Electrical Standards and Safety Areas
Presented by W. HETHERINGTON, F.A.P.H.I. in the Storage of Petrol
Advertisement
Chief Public Health Inspector, Witney Urban District Council at the Annual General Meeting of the South East Midland Branch
!~is paper is. presented n<?t as a new thought, or an ongmal concept10n of safety ideas, but purely as a repitition of one aspect of petroleum safety rules, that seems to be the least understood of all licensing conditions. It follows from this that electrical standards as a natural requirement of the in~erent danger protection can be overlooked, or are required to a standard far higher than often appears necessary. As the cost of flameproof equipment for instance is high, every effort must therefore be made to prevent unnecessary installation to this standard but not at the expense of essential safety conditions. '
It was my intention to consider initially how accidents happen, but on second thoughts realised that they were really allowed to happen. In other words, those combinations of factors that create accidents, and in this context here we mean fire and subsequent explosion are not normally cohabi~ant, but do come together 'to create dangerous reactions through some deliberate act or negligence.
Thi~ danger with petroleum has been appreciated for a long time, and the Petroleum Acts and we, as Petroleum Officers, have <l;S ou.r sole purpose the aim of preventing the dangerous s1tuat10n referred to above from developing.
Petroleum lic::ence conditions that stern from the Petroleum Acts consist usually of three main sections. Adrninistrati~e, mech.anical. h3;ndling and safe storage, loose handlmg and d1spensmg m a safe manner. It is in connection with part of this last that this paper is devoted.
It is very easy to l?se a sen~e of proportion when laying down safe~y precaut10ns, J?articularly against those factors that contribute to explos10ns, and an endeavour will be made. to detail why an exp.losion occurs and where and how 1t can be prevented, with reference to the use of the electrical equipment associated with petrol handling.
Simply, an explosion is an extension of a fire or more technically a chemical reaction between the 'offending substance and oxygei: ~<?ften, but not always, from the atmosphere) usually 11111Iate? by a rise in temperature. It does not, repeat not, req~ure, as a prerequisite, a flame as such. By-pro~uct of fir~ is usually heat and gas in large volume, very rapid fire by its sudden excess gas production produces the shock wave we call an explosion. . Perhaps the mo~t difficult causative factor to apprec!at~ and t~ c01~trol .1~ sudden and localised temperature nse 1s electnc~l m on gm and because of this quite detailed recommendatlons have been made by all interested bodies and much. ~fit is collected and. col_lated in the publication~ of the Bnt1sh Standards lnstltution to which references will be made below, and an understanding of which should go a long way to clarifying this subject.
From now therefore those terms used so loosely and generally in discussing safety on petroleum handling sites will be considered in more detail.
It follows in devising safety standards that conditions of risk must initially be defined for each dangerous substance and for petroleum products these are classed as:
Division 0:
Division 1:
Division 2: An area within which explosive vapour is continuously present in concentrations within the upper and lower limits of flammability. An area in which any flammable or explosive substance is handled and where during normal operations an explosive concentration is likely to occur to produce a hazard. An area in which any flammable substance is so well under conditions of control that the production of an explosive concentration in sufficient quantity to constitute a hazard is only likely under abnormal conditions (also known as a Remotely Dangerous Area).
Safe Area: All areas not classified as dangerous areas. Simply therefore,
Division O acknowledges a permanent high risk,
Division 1 acknowledges that the risk is inherent in the situation,
Division 2 acknowledges that sa\ety can b.e. achieved by depending on the 1mprobab1hty of the simultaneous occurrence of a flammable atmosphere and ignition source.
As applied to pe~rol ~tares and petr~l filling stations, the Division 2 class1ficat10n means that m normal operating conditions a safe area exists and. the dangerous atmosphere is only present as a result of ~p1l~age. The ar~a should be well ventilated so that vapour 1s dispersed rapidly.
Divisions O and 1 are fairly self descriptive, the former including both the tanks themselves and the inside of pipes and pumps, while the la~ter embraces _those fixtures and fittings and are<1;s whe.re h1~h con~entrat10ns could develop with inherent d1spers10n d1fficult1es.
The physical extent of ~hese area.s is of nec.e~s~ty bound up with actual site cond1t10ns, particularly D1v1s10n 2 a!ld the outer limits of Division 1, and can only be defined with experience. Practical industrial experience has assessed a guiding factor and these appear in the Home Office Model Code Part l (1968), but these are only guide lines. Obviously the extent of Division 2 precautions on a windswept
SS
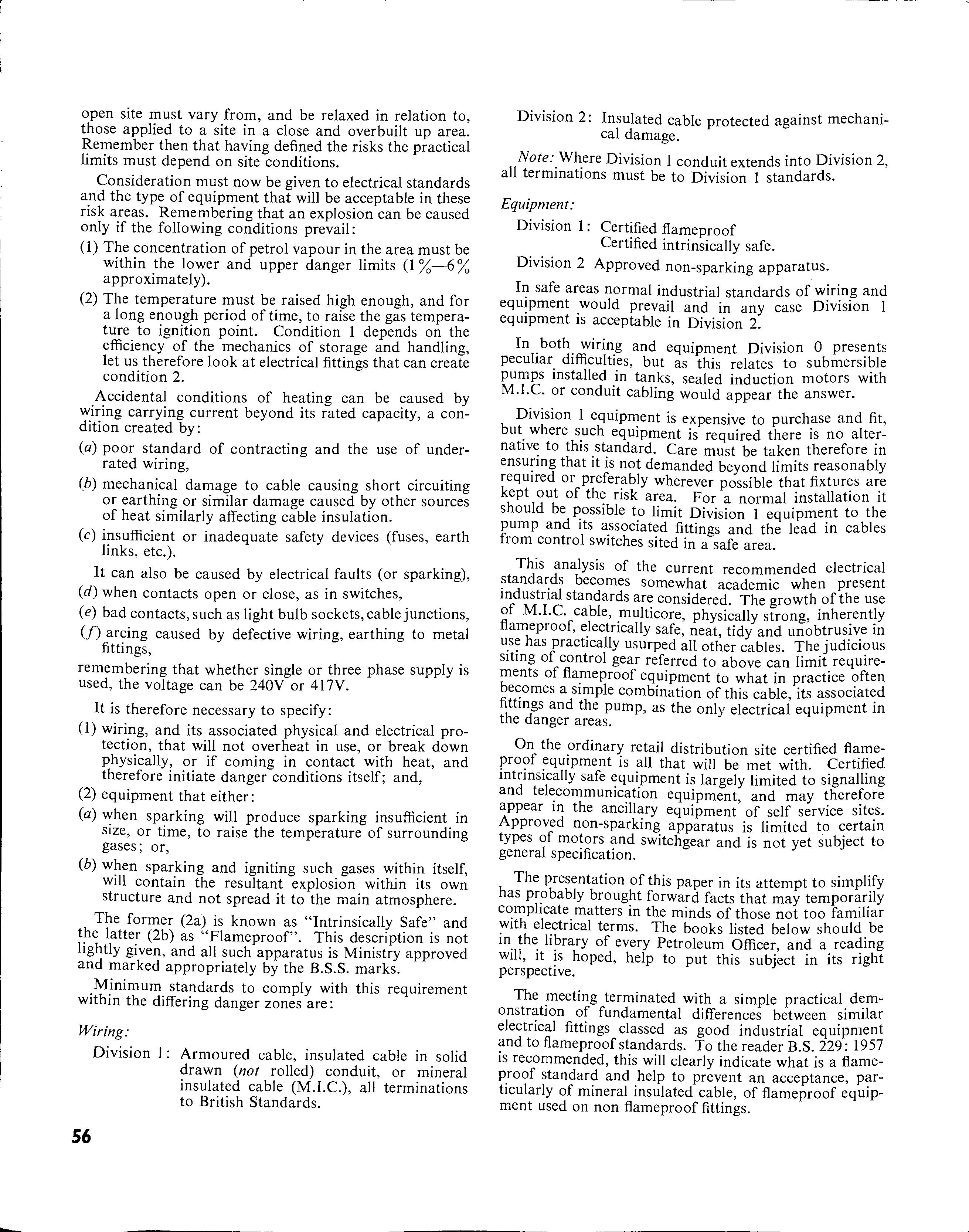
open site must vary from, and be relaxed in relation to, those applied to a site in a close and overbuilt up area. Remember then that having defined the risks the practical limits must depend on site conditions.
Consideration must now be given to electrical standards and the type of equipment that will be acceptable in these risk areas. Remembering that an explosion can be caused only if the following conditions prevail: (1) The concentration of petrol vapour in the area must be within the lower and upper danger limits (1 %-6 % approximately). (2) The temperature must be raised high enough, and for a long enough period of time, to raise the gas temperature to ignition point. Condition I depends on the efficiency of the mechanics of storage and handling, let us therefore look at electrical fittings that can create condition 2.
Accidental conditions of heating can be caused by wiring carrying current beyond its rated capacity, a condition created by: (a) poor standard of contracting and the use of underrated wiring, (b) mechanical damage to cable causing short circuiting or earthing or similar damage caused by other sources of heat similarly affecting cable insulation. (c) insufficient or inadequate safety devices (fuses, earth links, etc.).
It can also be caused by electrical faults (or sparking), (d) when contacts open or close, as in switches, (e) bad contacts, such as light bulb sockets, cable junctions, (f) arcing caused by defective wiring, earthing to metal fittings, remembering that whether single or three phase supply is used, the voltage can be 240V or 4 I 7V.
It is therefore necessary to specify: (1) wiring, and its associated physical and electrical protection, that will not overheat in use, break down physically, or if coming in contact with heat, and therefore initiate danger conditions itself; and, (2) equipment that either: (a) when sparking will produce sparking insufficient. in size, or time, to raise the temperature of surroundmg gases; or, (b) when sparking and igniting such gases within itself, will contain the resultant explosion within its own structure and not spread it to the main atmosphere.
The former (2a) is known as "Intrinsically Safe" and the latter (2b) as "Flameproof". This description is not lightly given, and all such apparatus is Ministry approved and marked appropriately by the B.S.S. marks.
Minimum standards to comply with this requirement within the differing danger zones are:
Wiring:
Division J : Armoured cable, insulated cable in solid drawn (not rolled) conduit, or mineral insulated cable (M.J.C.), all terminations to British Standards. Division 2: Insulated cable protected against mechanical damage.
Note: Where Division I conduit extends into Division 2, all terminations must be to Division I standards.
Equipment:
Division I : Certified flameproof Certified intrinsically safe.
Division 2 Approved non-sparking apparatus.
In safe areas normal industrial standards of wiring and equipment would prevail and in any case Division I equipment is acceptable in Division 2.
In _both. wirin_g and equipment Division 0 peculiar drfficult1es, but as this relates to submersible pumps installed in tanks, sealed induction motors with M.I.C. or conduit cabling would appear the answer.
Division 1 equipment is expensive to purchase and fit, but where such equipment is required there is no alternative to this standard. Care must be taken therefore in that it is not demanded beyond limits reasonably reqmred or preferably wherever possible that fixtures are kept out of the risk area. For a normal installation it should be possible to limit Division 1 equipment to the pump and its associated fittings and the lead in cables from control switches sited in a safe area.
This analysis of the current recommended electrical standards becomes somewhat academic when present industrial standards are considered. The growth of the use of M.J.C. cable, _multicore, physically strong, flameproof, electrically safe neat tidy and unobtrusive m use has practically usurped other cables. The judicious siting of control gear referred to above can limit requirements of flameproof equipment to what in practice often becomes a simple combination of this cable its associated fittings and the pump, as the only electrical equipment in the danger areas.
On the ordinary retail distribution site certified flameproof equipment is all that will be met with. Certified intrinsically safe equipment is largely limited to signalling and equipment, and may ore appear m the ancillary equipment of self service Approved non-sparking apparatus is limited to certam types of motors and switchgear and is not yet subject to general specification.
The presentation of this paper in its attempt to has probably brought forward facts that may temporarily complicate matters in the minds of those not too familiar with electrical terms. The books listed below should be in the library of every Petroleum Officer, and a reading will, it is hoped, help to put this subject in its right perspective.
The meeting terminated with a simple practical demonstration of fundamental differences between similar electrical fittings classed as good industrial equipment and to flameproof standards. To the reader B.S. 229: 1957 is recommended, this will clearly indicate what is a flameproof standard and help to prevent an acceptance, particularly of mineral insulated cable, of flameproof equipment used on non flameproof fittings.