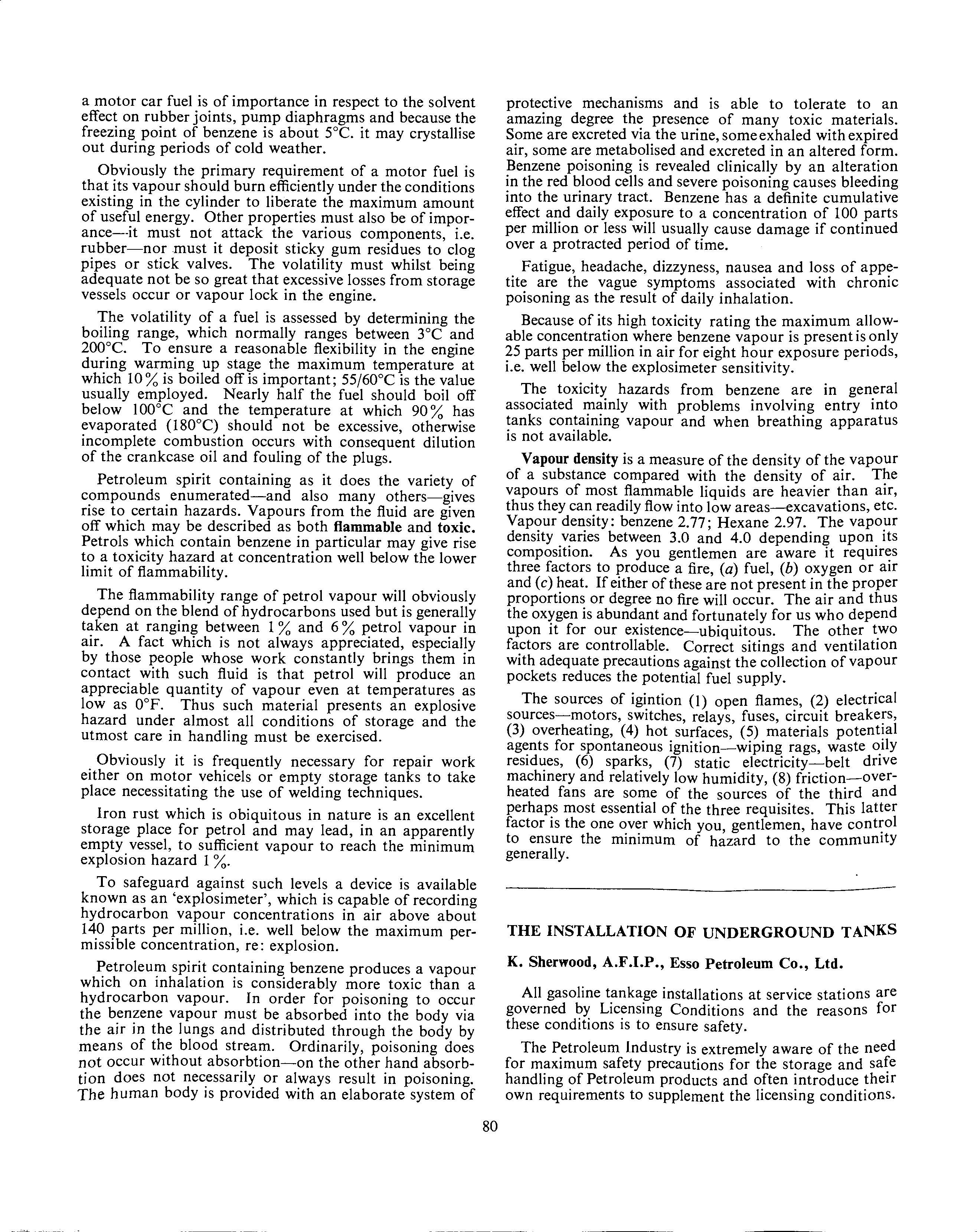
14 minute read
THE INSTALLATION OF UNDERGROUND TANKS-K. SHERWOOD
a motor car fuel is of importance in respect to the solvent effect on rubber joints, pump diaphragms and because the freezing point of benzene is about 5°C. it may crystallise out during periods of cold weather.
Obviously the primary requirement of a motor fuel is that its vapour should burn efficiently under the conditions existing in the cylinder to liberate the maximum amount of useful energy. Other properties must also be of imporance--it must not attack the various components, i.e. rubber-nor must it deposit sticky gum residues to clog pipes or stick valves. The volatility must whilst being adequate not be so great that excessive losses from storage vessels occur or vapour lock in the engine.
Advertisement
The volatility of a fuel is assessed by determining the boiling range, which normally ranges between 3°C and 200°C. To ensure a reasonable flexibility in the engine during warming up which 10 % is boiled stage the maximum temperature at off is important; 55/60°C is the value usually employed. Nearly half the fuel should boil off below I 00°C and the temperature at which 90 % has evaporated (180°C) should not be excessive, otherwise incomplete combustion occurs with consequent dilution of the crankcase oil and fouling of the plugs.
Petroleum spirit containing as it does the variety of compounds enumerated-and also many others-gives rise to certain hazards. Vapours from the fluid are given off which may be described as both flammable and toxic. Petrols which contain benzene in particular may give rise to a toxicity hazard at concentration well below the lower limit of flammability.
The flammability range of petrol vapour will obviously depend on the blend of hydrocarbons used but is generally taken at ranging between 1 % and 6 % petrol vapour in air. A fact which is not always appreciated, especially by those people whose work constantly brings them in contact with such fluid is that petrol will produce an appreciable quantity of vapour even at temperatures as low as 0°F. Thus such material presents an explosive hazard under almost all conditions of storage and the utmost care in handling must be exercised.
Obviously it is frequently necessary for repair work either on motor vehicels or empty storage tanks to take place necessitating the use of welding techniques.
Iron rust which is obiquitous in nature is an excellent storage place for petrol and may lead, in an apparently empty vessel, to sufficient explosion hazard I %. vapour to reach the minimum
To safeguard against such levels a device is available known as an 'explosimeter', which is capable of recording hydrocarbon vapour concentrations in air above about 140 parts per million, i.e. well below the maximum permissible concentration, re: explosion.
Petroleum spirit containing benzene produces a vapour which on inhalation is considerably more toxic than a hydrocarbon vapour. In order for poisoning to occur the benzene vapour must be absorbed into the body via the air in the lungs and distributed through the body by means of the blood stream. Ordinarily, poisoning does not occur without absorbtion-on the other hand absorbti on does not necessarily or always result in poisoning. The human body is provided with an elaborate system of protective mechanisms and is able to tolerate to an amazing degree the presence of many toxic materials. Some are excreted via the urine, some exhaled with expired air, some are metabolised and excreted in an altered form. Benzene poisoning is revealed clinically by an alteration in the red blood cells and severe poisoning causes bleeding into the urinary tract. Benzene has a definite cumulative effect and daily exposure to a concentration of 100 parts per million or less will usually cause damage if continued over a protracted period of time.
Fatigue, headache, dizzyness, nausea and loss of appetite are the vague symptoms associated with chronic poisoning as the result of daily inhalation.
Because of its high toxicity rating the maximum allowable concentration where benzene vapour is present is only 25 parts per million in air for eight hour exposure periods, i.e. well below the explosimeter sensitivity.
The toxicity hazards from benzene are in general associated mainly with problems involving entry into tanks containing vapour and when breathing apparatus is not available.
Vapour density is a measure of the density of the vapour of a substance compared with the density of air. The vapours of most flammable liquids are heavier than air, thus they can readily flow into low areas-excavations, etc. Vapour density: benzene 2.77; Hexane 2.97. The vapour density varies between 3.0 and 4.0 depending upon its composition. As you gentlemen are aware it requir~s three factors to produce a fire, (a) fuel, (b) oxygen or alf and (c) heat. If either of these are not present in the proper proportions or degree no fire will occur. The air and thus the oxygen is abundant and fortunately for us who depend upon it for our existence-ubiquitous. The other t.wo factors are controllable. Correct sitings and ventilation with adequate precautions against the collection of vapour pockets reduces the potential fuel supply.
The sources of igintion (I) open flames, (2) electrical sources-motors, switches, relays, fuses, circuit breake~s, (3) overheating, (4) hot surfaces, (5) materials potent!al agents for spontaneous ignition-wiping rags, waste o.IIY residues, (6) sparks, (7) static electricity-belt dnve machinery and relatively low humidity, (8) friction-overheated fans are some of the sources of the third and perhaps most essential of the three requisites. This latter factor is the one over which you, gentlemen, have cont~ol to ensure the minimum of hazard to the commumty generally.
THE INSTALLATION OF UNDERGROUND TANKS
K. Sherwood, A.F.I.P., Esso Petroleum Co., Ltd.
All gasoline tankage installations at service stations are governed by Licensing Conditions and the reasons for these conditions is to ensure safety.
The Petroleum Industry is extremely aware of the need for maximum safety precautions for the storage and sa~e handling of Petroleum products and often introduce thelf own requirements to supplement the licensing conditions.
80
I. Tanks
The safety considerations commence with the design and manufacture of the storage tanks. At present these tanks are invariably made of !in. thick M.S. plate welded to B.S.S. 2594. Prior to leaving the manufacturers' works t~e tanks are tested to a pressure of lO p.s.i. They are also given a protective external coating of Bitumastic paint or similar.
The majority of Licensing Authorities require the tanks to be fitted with a manhole and cover. Several European countries will not permit tanks with manholes. There are arguments for and against manholes which can usually lead to lively discussion.
A major consideration could be that the elimination of tank manholes could result in the elimination of ground manhole chambers which without doubt are natural collecting pockets for gasoline vapours.
Each ta~k is supplied with a calibrated brass dipstick for measurmg the tank contents. It should be appreciated that these dipsticks are not accurate measuring apparatus but only approximate the tank contents. Most tankage manufacturers unusual for the batch process the tanks and it is dipsticks to show errors of 2 %-3 %. not
2. Siting
All Licensing Authorities demand that minimum· distances are observed between the tank manhole chambers and public highways and buildings. Normally 20ft. is the acceptable distance.
Bearing these requirements in mind the marketing company must consider operational aspects such as length of suction lines, road tank vehicle access and standing area for product deliveries.
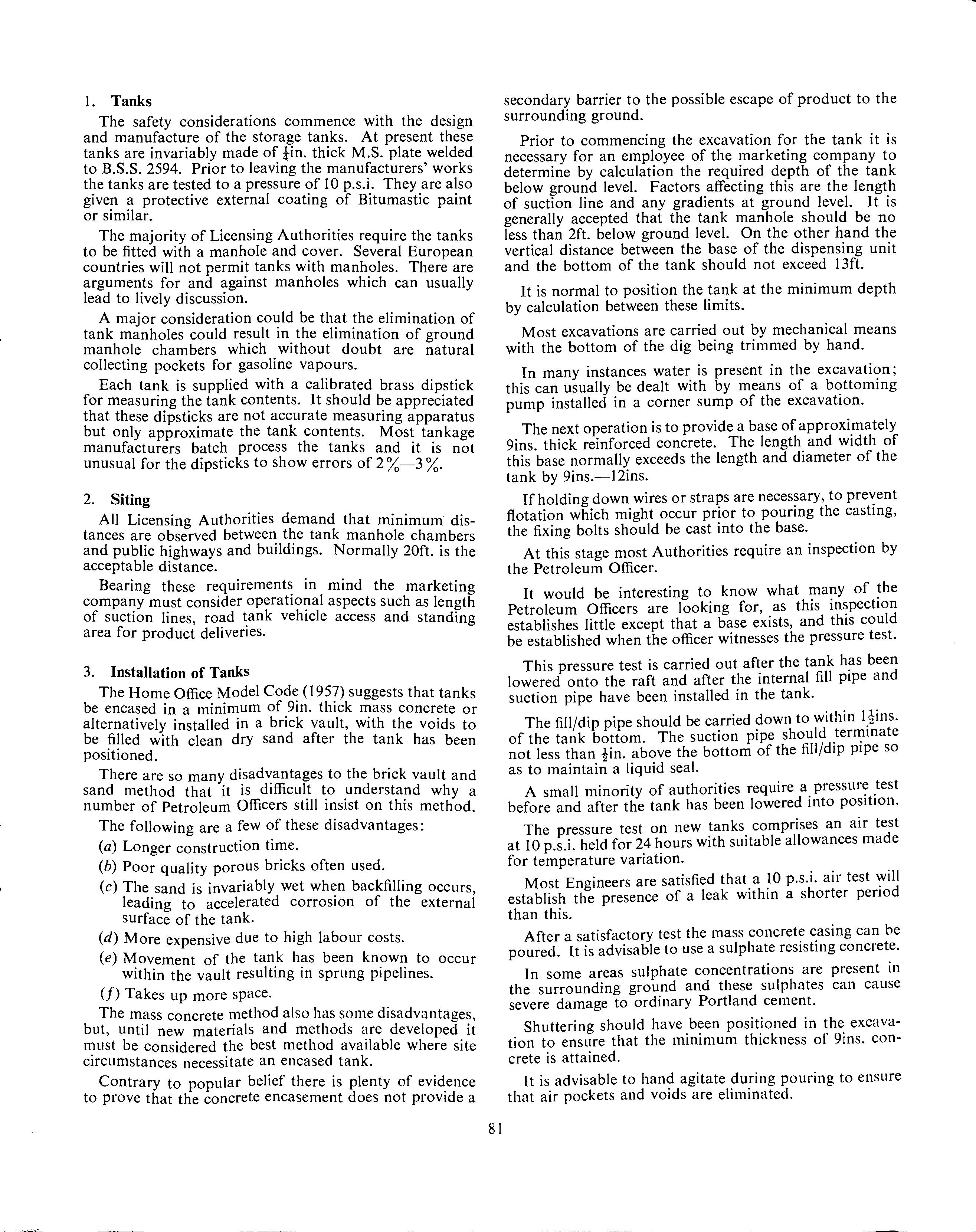
3. Installation of Tanks
The Home Office Model Code (1957) suggests that tanks be encased in a minimum of 9in. thick mass concrete or alternatively installed in a brick vault, with the voids to be filled with clean dry sand after the tank has been positioned.
There are so many disadvantages to the brick vault and sand method that it is difficult to understand why a number of Petroleum Officers still insist on this method.
The following are a few of these disadvantages: (a) Longer construction time. (b) Poor quality porous bricks often used. (c) The sand is invariably wet when backfilling occurs leading to accelerated corrosion of the external surface of the tank. (d) More expensive due to high labour costs. (e) Movement of the tank has been known to occur within the vault resulting in sprung pipelines. (f) Takes up more space.
The m.ass concrete 1~1ethod also has some disadvantages, but, until new matenals and methods are developed it must be considered the best method available where site circumstances necessitate an encased tank.
Contrary to popular belief there is plenty of evidence to prove that the concrete encasement does not provide a secondary barrier to the possible escape of product to the surrounding ground.
Prior to commencing the excavation for the tank it is necessary for an employee of the marketing company to determine by calculation the required depth of the tank below ground level. Factors affecting this are the length of suction line and any gradients at ground level. It is generally accepted that the tank manhole should be no less than 2ft. below ground level. On the other hand the vertical distance between the base of the dispensing unit and the bottom of the tank should not exceed 13ft.
It is normal to position the tank at the minimum depth by calculation between these limits.
Most excavations are carried out by mechanical means with the bottom of the dig being trimmed by hand.
In many instances water is present in the excavation; this can usually be dealt with by means of a bottoming pump installed in a corner sump of the excavation.
The next operation is to provide a base of approximately 9ins. thick reinforced concrete. The length and width of this base normally exceeds the length and diameter of the tank by 9ins.-12ins.
If holding down wires or straps are necessary, to prevent flotation which might occur prior to pouring the casting, the fixing bolts should be cast into the base.
At this stage most Authorities require an inspection by the Petroleum Officer.
It would be interesting to know what many of the Petroleum Officers are looking for, as this in~pection establishes little except that a base exists, and this could be established when the officer witnesses the pressure test.
This pressure test is carried out after the tank h_as been lowered onto the raft and after the internal fill pipe and suction pipe have been installed in the tank.
The fill/dip pipe should be carried down to within lJins. of the tank bottom. The suction pipe should .ternynate not less than tin. above the bottom of the fill/d1p pipe so as to maintain a liquid seal.
A small minority of authorities require a. pressur~ .test before and after the tank has been lowered mto pos1t1011.
The pressure test on new tanks comprises an air test at lO p.s.i. held for 24 hours with suitable allowances made for temperature variation.
Most Engineers are satisfied that. a _10 p.s.i. air test "."ill establish the presence of a leak w1th111 a shorter penod than this.
After a satisfactory test the mass concrete casing can be poured. lt is advisable to use a sulphate resisting concrete.
In some areas sulphate concentrations are present in the surrounding ground and these sulphates can cause severe damage to ordinary Portland cement.
Shuttering should have been positioned in the excavation to ensure that the minimum thickness of 9ins. concrete is attained. lt is advisable to hand agitate during pouring to ensure that air pockets and voids are eliminated.
81
4. Pipelines
After the tank has been encased the suction and vent lines can be installed.
The pipes and fittings ~hould be to B.S.S. _1387, tho~e for gasoline being galvamsed and those for diesel fuel in black iron.
The following recommendations are made in respect of vent pipes: (a) Each tank or compartment should have a vent pipe not less than liins. in diameter. (b) The upper end of the pipe should discharge upwards in the open air, out of reach, be at least 12ft. above ground level and should not be located within 5ft. of opening windows or other openings. On new installations 180° return bend vent heads which deflect vapours downwards should be discouraged. (c) There should be no entry to basements or below ground areas within 5ft. of a point vertically below the vent discharge point. (d) Electrical fittings within 5ft. of the vent discharge
point should be to Divis~on I ~tand~r~s_. Elsew~ere, within 5ft. of the vent nser pipe Division 2 fittings should be used. (e) Vent pipes should be installed no closer than 5ft. to a boundary except where this is a solid wall extending for 5ft. beyond the vent discharge point and down to ground level.
Suction lines up to approximately 80ft. in length should normally be run in 1 !ins. pipe, unless it is intended to connect two pumps to the same suction in which case the pipe should be 2ins. bore.
The sizes of the external fill pipes vary from 2ins.-4ins., dependent upon the operational policy of the marketing company concerned. The majority are 3ins. bore.
Many authorities have an aversion to offset fill pipes and yet if correctly installed they can be as safe, if not safer than the conventional argu~ that offset fills facilitate ground chambers. the possibility of a Some spillage at the underground tank, but if a hydrostatic contents gauge is used instead of a dipstick and all other openings sealed then a spillage at the tank is impossible.
When the installation is complete each tank should be numbered and its dipstick should be stamped with the same number.
Mention was made earlier that concrete encasement for tankage installation must be considered the best method until new materials and methods have been developed.
Over the past two years there has been international interest in storing gasoline in tanks made of plastic materials and fibreglass reinforced polyester tanks have been tested and installed in U.S.A., Canada and probably other countries. Similar road vehicle tanks have been used in Belgium for several years.
In J 965 Esso Petroleum Company Limited obtained a plastic tank of the following dimensions: Length I 3ft. I OMns. Diameter 7ft. Oins. Wall thickness i (nominal). Nominal capacity 3,000 imperial gallons.
Moulding was by hand lay up of glass reinforcement in the form of a mat, on top of the resin gel coat on a mould. The second resin was then applied to the reinforcement. The tank was manufactured in three cylindrical sections, joined together at stiffener rings, fitted with dished ends. At the stiffener rings the sections were butted together overlaid with glass mat and resin. Stiffener rings were formed with paper rope and overlaid with more glass m_at and resin. The inside of the finished tank is smooth while the outside is a close grained "patchwork of resin impreg-nated glass strands". Tests
The following tests were carried out: (1) Hydraulic pressure test for 24 hours at 10 p.s.i. A vertical pipe was fitted on the tank vent and the water level was steadily increased in this pipe to allow the behaviour of the tank to be examined at 2.5, 5, 7.5 and 10 p.s.i. The tank successfully withstood this test and no detectable changes in diameter and circumference occurred. The average hoop tensile stress in this case is about 2,000 lbs. per sq. in. (2) Torque test on fittings. Each of the pipe connection entries was made by using flanges on the outside and inside of the tank. Any torque applied to the piping was therefore transferred to the tank via a set of fixing studs or bolts, arranged on a substantial pitch circle diameter. This test was therefore limited to testing whether individual bolts set in the plastic material wo~ld resist the normal torque associated with tightening nuts with spanners. These fittings resisted a steady torque of 50lbs. ft. applied through a torque wrench. (3) Handling Test. The tank weighs 850lbs. when empty. It was lifted by a single hook on a crane using two rope slings. It was also lifted by a fork lift truck. It was pushed along on a trolley 2ft. x 4ft. suppor~ed on four small wheels and prevented from t1ppmg by the men who were handling it. ( 4) Material test: (a) Resistance to product: Pieces approximately 4ins. x 2ins. were immerse? at room temperature in various aliphatic/aromatic hydrocarbon mixtures at a W/V ratio of 1/10. After 76 days in benzene large amounts of plastic were flaking off the surface. The resins contained chlorinated wax and antimoxy oxide mixture as fire retardant additives. With these omitted further tests were successfully carried out. (b) Physical: Laboratory tests were carried out to determine the ultimate tensile strength and Young's Modulus of the materials from which the tank is made.
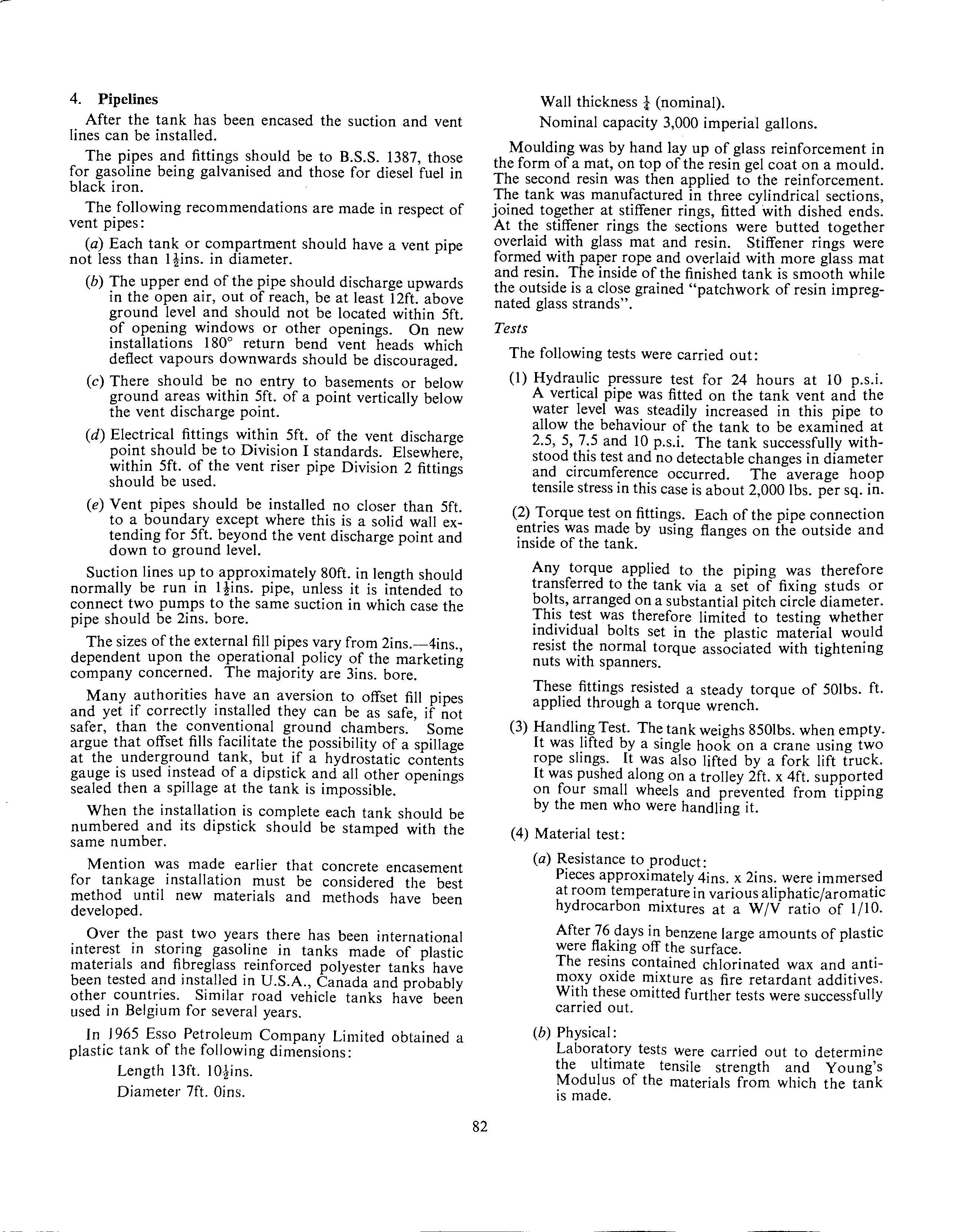
82