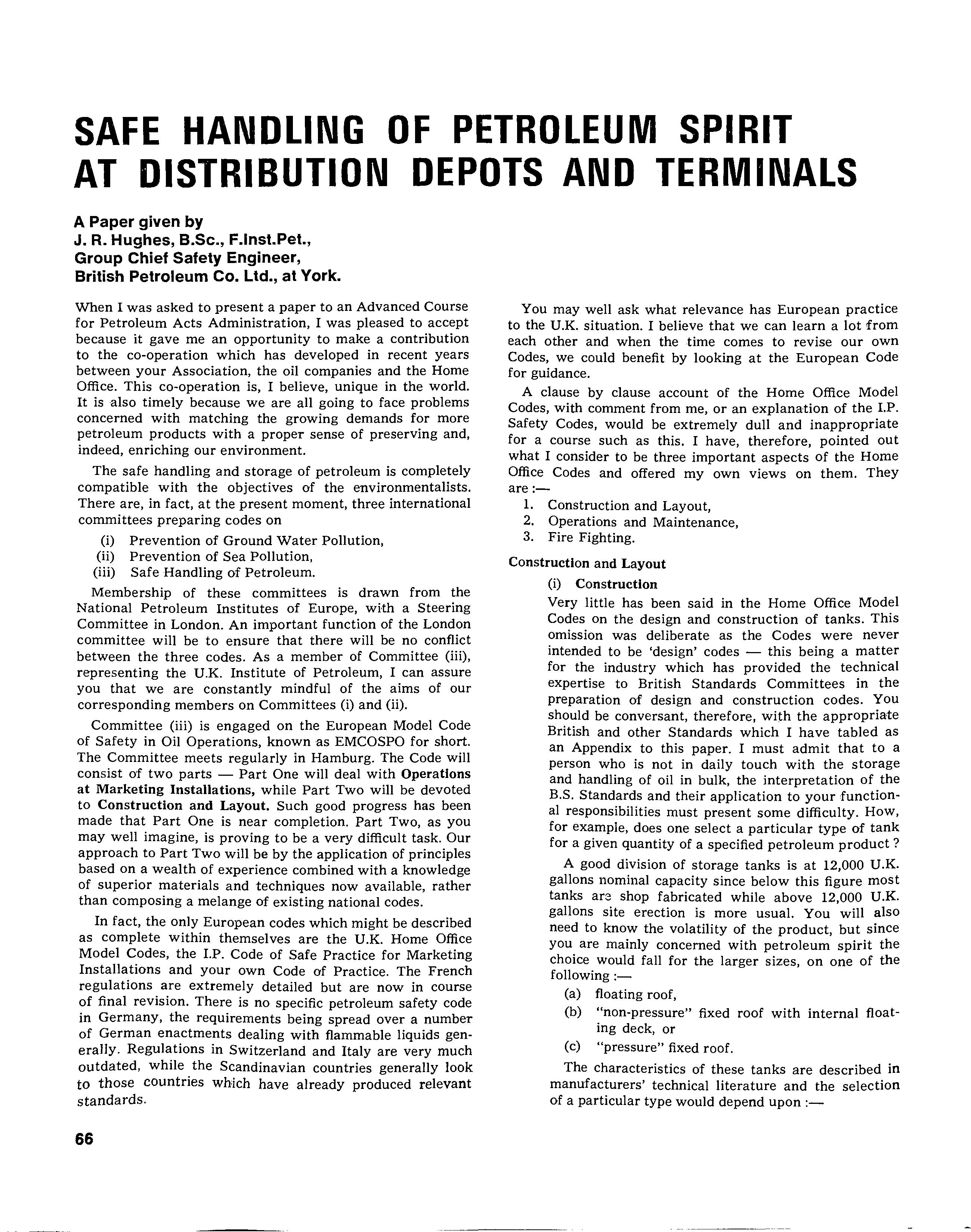
13 minute read
at Distribution Depots
SAFE HANDLING OF PETROLEUM SPIRIT AT DISTRIBUTION DEPOTS AND TERMINALS
A Paper given by J. R. Hughes, B.Sc., F.lnst.Pet., Group Chief Safety Engineer, British Petroleum Co. Ltd., at York.
Advertisement
When I was asked to present a paper to an Advanced Course for Petroleum Acts Administration, I was pleased to accept because it gave me an opportunity to make a contribution to the co-operation which has developed in recent years between your Association, the oil companies and the Home Office. This co-operation is, I believe, unique in the world. It is also timely because we are all going to face problems concerned with matching the growing demands for more petroleum products with a proper sense of preserving and, indeed, enriching our environment.
The safe handling and storage of petroleum is completely compatible with the objectives of the environmentalists. There are, in fact, at the present moment, three international committees preparing codes on (i) Prevention of Ground Water Pollution, (ii) Prevention of Sea Pollution, (iii) Safe Handling of Petroleum.
Membership of these committees is drawn from the National Petroleum Institutes of Europe, with a Steering Committee in London. An important function of the London committee will be to ensure that there will be no conflict between the three codes. As a member of Committee (iii), representing the U.K. Institute of Petroleum, I can assure you that we are constantly mindful of the aims of our corresponding members on Committees (i) and (ii).
Committee (iii) is engaged on the European Model Code of Safety in Oil Operations, known as EMCOSPO for short. The Committee meets regularly in Hamburg. The Code will consist of two parts - Part One will deal with Operations at Marketing Installations, while Part Two will be devoted to Construction and Layout. Such good progress has been made that Part One is near completion. Part Two, as you may well imagine, is proving to be a very difficult task. Our approach to Part Two will be by the application of principles based on a wealth of experience combined with a knowledge of superior materials and techniques now available, rather than composing a melange of existing national codes.
In fact, the only European codes which might be described as complete within themselves are the U.K. Home Office Model Codes, the I.P. Code of Safe Practice for Marketing Installations and your own Code of Practice. The French regulations are extremely detailed but are now in course of final revision. There is no specific petroleum safety code in Germany, the requirements being spread over a number of German enactments dealing with flammable liquids generallY· Regulations in Switzerland and Italy are very much outdated, while the Scandinavian countries generally look to those countries which have already produced relevant standards.
66
You may well ask what relevance has European practice to the U.K. situation. I believe that we can learn a lot from each other and when the time comes to revise our own Codes, we could benefit by looking at the European Code for guidance.
A clause by clause account of the Home Office Model Codes, with comment from me, or an explanation of the LP. Safety Codes, would be extremely dull and inappropriate for a course such as this. I have, therefore, pointed out what I consider to be three important aspects of the Home Office Codes and offered my own views on them. They are:l. Construction and Layout, 2. Operations and Maintenance, 3. Fire Fighting. Construction and Layout (i) Construction Very little has been said in the Home Office Model Codes on the design and construction of tanks. This omission was deliberate as the Codes were never intended to be 'design' codes - this being a matter for the industry which has provided the technical expertise to British Standards Committees in the preparation of design and construction codes. You should be conversant, therefore, with the appropriate British and other Standards which I have tabled as an Appendix to this paper. I must admit that to a person who is not in daily touch with the storage and handling of oil in bulk, the interpretation of the B.S. Standards and their application to your functional responsibilities must present some difficulty. How, for example, does one select a particular type of tank for a given quantity of a specified petroleum product? A good division of storage tanks is at 12,000 U.K. gallons nominal capacity since below this figure most tanks ar3 shop fabricated while above 12,000 U.K. gallons site erection is more usual. You will also need to know the volatility of the product, but since you are mainly concerned with petroleum spirit the choice would fall for the larger sizes, on one of the following :(a) floating roof, (b) "non-pressure" fixed roof with internal floating deck, or (c) "pressure" fixed roof. The characteristics of these tanks are described in manufacturers' technical literature and the selection of a particular type would depend upon :-
size, frequency of oil movement in and out of the tank, vapour pressure, climatic conditions, cost. (ii) Layout Good guidance on layout and spacing of tanks is given in the Home Office Model Codes. In deciding spacing between tanks, height of bund walls and distances of bund walls from the shells of tanks, the Home Office gave particular attention to the ability to contain and extinguish tank fires. Bund walls are intended only to retain spillages - a catastrophic failure of a tank which resulted in the whole of the contents being discharged at once would not be contained, a tidal wave of oil would simply sweep over the bund wall which, in the Model Codes, are more correctly called "fire-walls".
There is, I belive, some merit in the use of doubleskin tanks in lieu of single wall plus fire-wall. We are now faced with special problems at some tank farm sites in the Middle East, where it would be practically impossible to build fire-walls to Model Code standard for two reasons :- (a) the tremendous size of a firewall for a 260ft. diameter tank; (b) difficulty in getting suitable impervious material. We are, therefore, seriously considering double-skin floating roof tanks with no fire-walls. This has already been done recently in Germany, with the agreement of the local authority, but mainly on the grounds that there was insufficient space for fire-walls when constructed to contain the capacity of the largest tank. With doubleskin tanks, we have to devise new fire-fighting procedures and there are, of course, certain technical problems concerned with the differential movement which occurs between the skins as the inner tank is filled and emptied.
A sloping site may offer advantages in drainage and lower cost pumping facilities. It also lends itself to taking advantage of an impounding basin in conjunction with diversionary walls instead of fire-walls. In fact, they are on such sites superior to fire-walls, but only if they are soundly constructed and properly maintained.
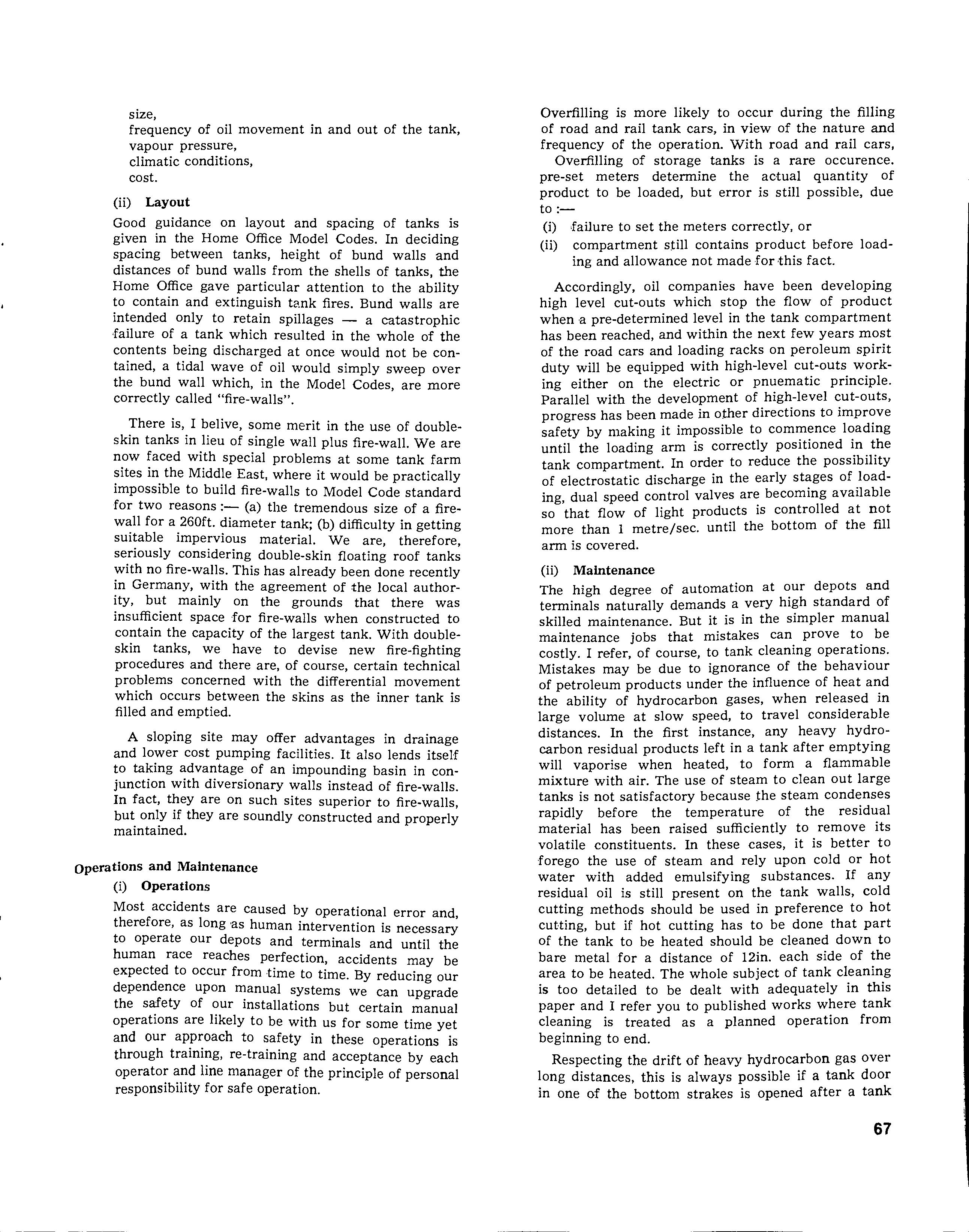
operations and Maintenance (i) Operations Most accidents are caused by operational error and, therefore, as long 'as human intervention is necessary to operate our depots and terminals and until the human race reaches perfection, accidents may be expected to OCcur from time to time. By reducing our dependence upon manual systems we can upgrade the safety of our installations but certain manual operations are likely to be with us for some time yet and our approach to safety in these operations is through training, re-training and acceptance by each operator and line manager of the principle of personal responsibility for safe operation. Overfilling is more likely to occur during the filling of road and rail tank cars, in view of the nature and frequency of the operation. With road and rail cars,
Overfilling of storage tanks is a rare occurence. pre-set meters determine the actual quantity of product to be loaded, but error is still possible, due to:(i) ,failure to set the meters correctly, or (ii) compartment still contains product before loading and allowance not made for this fact.
Accordingly, oil companies have been developing high level cut-outs which stop the flow of product when a pre-determined level in the tank compartment has been reached, and within the next few years most of the road cars and loading racks on peroleum spirit duty will be equipped with high-level cut-outs working either on the electric or pnuematic principle. Parallel with the development of high-level cut-outs, progress has been made in other directions to safety by making it impossible to commence loadmg until the loading arm is correctly positioned in the tank compartment. In order to reduce the possibility of electrostatic discharge in the early stages of loading, dual speed control valves are becoming available so that flow of light products is controlled at not more than 1 metre/sec. until the bottom of the fill arm is covered.
(ii) Maintenance The high degree of automation at our depots and terminals naturally demands a very high standard of skilled maintenance. But it is in the simpler manual maintenance jobs that mistakes can prove to be costly. I refer, of course, to tank cleaning operations. Mistakes may be due to ignorance of the behaviour of petroleum products under the influence of heat and the ability of hydrocarbon gases, when released in large volume at slow speed, to travel considerable distances. In the first instance, any heavy hydrocarbon residual products left in a tank after emptying will vaporise when heated, to form a flammable mixture with air. The use of steam to clean out large tanks is not satisfactory because the steam condenses rapidly before the temperature of the residual material has been raised sufficiently to remove its volatile constituents. In these cases, it is better to forego the use of steam and rely upon cold or hot water with added emulsifying substances. If any residual oil is still present on the tank walls, cold cutting methods should be used in preference to hot cutting, but if hot cutting has to be done that part of the tank to be heated should be cleaned down to bare metal for a distance of 12in. each side of the area to be heated. The whole subject of tank cleaning is too detailed to be dealt with adequately in this paper and I refer you to published works where tank cleaning is treated as a planned operation from beginning to end.
Respecting the drift of heavy hydrocarbon gas over long distances, this is always possible if a tank door in one of the bottom strakes is opened after a tank
67
which has petroleum spirit has been emptied. I recall one instance in Turkey when petroleum spirit vapour travelled 136ft. in a bunded area, to be ignited by a non-flameproof starter switch of an electric stripping pump. The man operating the switch was burned to death in the flash fire which burned back to the open door in the bottom strake of the tank being pumped out (below door level). Escaping gas continued to burn at this door opening, the consumed gas being replaced by air admitted through the roof vents, until the atmosphere inside the tank entered the explosive range. When this occurred, the tank roof (fixed) was blown off, killing another man. The men endeavoured to extinguish the fire at the open shell door by means of foam. This was, of course, useless as foam will never extinguish a vapour fire - foam acts by smothering a liquid surface to prevent vapour escape and also acts as a coolant to reduce vaporisation. In the incident quoted, a curtain of dry chemical across the open door would have been successful as, at that time, the vapour inside the tank was too rich to bum. 3. Fire Fighting
You will be aware that the licensee of a distributing depot or major installation is required only to provide fire fighting equipment and materials adequate to combat a fire in its initial stages. In general, the licensee exceeds this requirement, certainly at the larger installations, and has spent considerable sums of money in fire tenders and associated fire fighting equipment. This is in addition to his not insignificant contribution to the rates for the authority in which his instillation is located. The Fire Authority is, by the Fire Services Act, 1947, charged with the duty of extinguishing fires and advising on fire prevention measures and by Section 30(3) of the Act, "the senior brigade officer present at a fire shall have the sole charge and control of all operations for the extinction of fire". It is clearly in our interests to have an efficient means of extinguishing fires and considerable progress has been made in the past ten years in both firefighting techniques and materials, due largely to the collaboration of the oil companies with equipment manufacturers. Because our depots and terminals are lightly manned, we welcome the arrangements made with
Fire Authorities by which their expertise is combined with the best available equipment for fire fighting.
Joint exercises are now common and we believe that these exercises are of very great importance. The vulnerability of fixed equipment on tanks is now fully appreciated and the sequence of order for provision of foam as stated in the Model Code, namely:1. mobile appliances, 2. fixed connections, or 3. a combination of 1 and 2, was not selected by chance. Priority is given to mobile appliances because of their ability to apply massive quantities of foam where it is most required. Whereas the major oil companies carry large stocks of foam compound in mobile bowsers (2,000 U.K. gallons), in addition to drum storage, it is disturbing to find that the Home Office stocks are in small individual drums which require to be loaded and subsequently off-loaded before transfer to foammaking machines. Much of the strategic value of these reserves is thereby lost. By and large, the oil companies enjoy very good relationships with the Fire Authorities. We believe, however, that there is room for more effective mutual aid schemes whereby assistance to, say, a small installation or depot could be obtained from better equipped larger installations. The Institute of Petroleum has recently produced recommended procedures for mutual aid in emergencies and I expect that these recommendations will be put before your Association for comment before publication. The main points of this presentation are summarised in the Appendix. APPENDIX 1 1. B.S. 2594: 1955 (Amendment No. 3 1964) - Horizontal mild steel welded storage tanks. 2. B.S. 2654 - Vertical mild steel storage tanks with buttwelded shells for the petroleum industry. Part I, 1965 - Design and fabrication. Part 2 1961 (Amendment
No. 2 1965) - Site erection, inspection and testing. 3. B.S. 1500: 1958 - Fusion welded pressure vessels for use in the chemical, petroleum and allied industries. 4. B.S. 1515: 1965 - Fusion welded pressure vessels (advanced design and construction) for use in the chemical, petroleum and allied industries. Part 1,
Carbon and ferritic alloy steels. 5. AMSE Code for Boiler and Pressure Vessels, Sec. VIII, 1962 345 East-47th Street, New York 17, New York. 6. API Recommended Practice RP 2000 - Guide for Tank
Venting. API 1271 Avenue of the Americas, New York 20.N.Y. 7. NFPA No. 30 - Flammable and Combustible Liquids
Code 1966. National Fire Protection Association, 60
Batterymarch Street, Boston, Mass. 8. API Standard 650 - Welded Steel Tanks for Oil
Storage. 9. API Standard 620 - Recommended Rules for Design and Construction of Large Welded Low-pressure Storage Tanks. 10. B.S. 2762: 1956 - Notch ductile steel for general structural purposes. 11. API Standard 2510 - The Design and Construction of
Liquefied Petroleum Gas Installations at Marine and
Pipeline Terminals, Natural Gas Processing Plants,
Refineries and Tank Farms. 12. Institute of Petroleum Safety Codes, 61 New Cavendish Street, London, W.!.
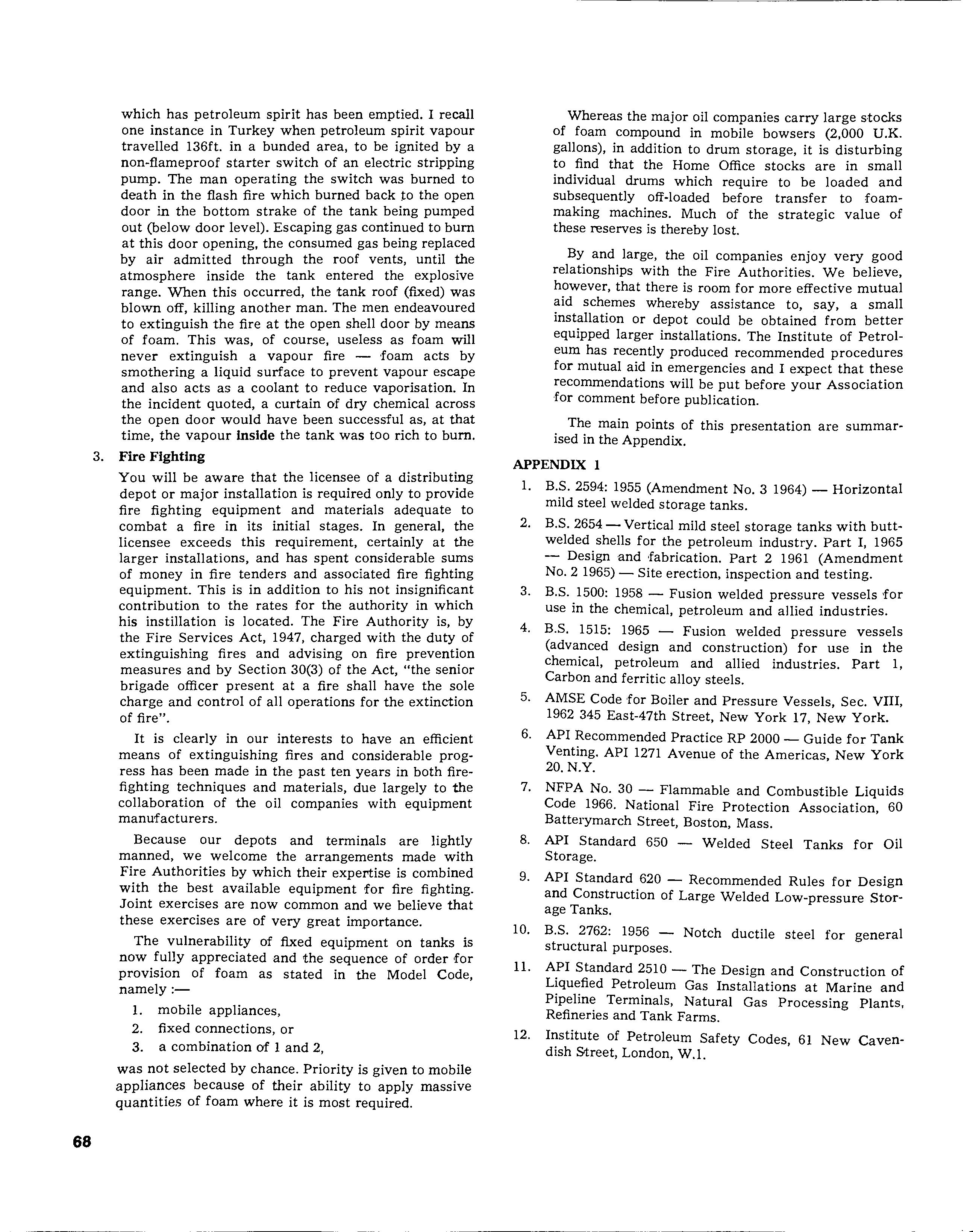