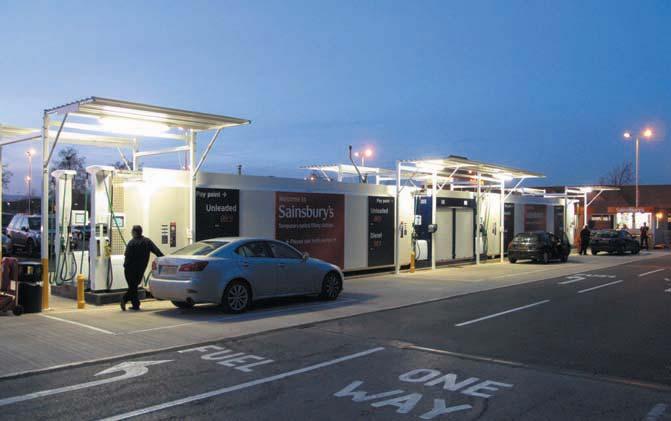
9 minute read
APEA Abbreviated accounts for the year ended December 2008
ridden. The Scully system, an industry standard over the last 30 years, met all requirements and is now incorporated in the specification
The TPFS at Taunton always received manned deliveries and it was agreed that the installation and training on the Scully system would be carried out when the TPFS arrived at Preston. The system operates with a probe in the top of the compartment with a prism which continually self checks 30 times per second. On the Sainsbury TPFS project it is effective when the fuel delivery operator misses the overfill alarm and continues to fill. Each compartment has a probe which is linked to the corresponding uplift pump; if the fuel exceeds the high level alarm and reaches the probe, the operational pump will completely shut down preventing any further fuel from being delivered to the compartment. Each compartment has its own designated uplift pump and the Scully will only shut down the pump that relates to the specific compartment being filled allowing other pumps to other compartments to continue filling. This system has
Advertisement
been adopted at Bunsfield and meets SEL 2 safety requirements.
“The delivery of this project involved a wide and dedicated team managed by myself with Martindales responsible for the design and logistical implementation of this facility. Williams Southern were instrumental in ensuring this was delivered to market as an operational solution. We sought advice from our Lead Petroleum Officer Ray Blake and were also superbly supported by our fuel supplier.
The tanks and supporting systems are robust and Terence Barker Ltd worked hard in ensuring we could deliver to the required market within the required time frame. The system is versatile and can be used in various layouts where a permanent overground tank solution is required and Sainsbury’s were impressed with the manufacturing process, advice and professionalism of Terence Barker Limited. The facility we installed at Taunton performed very well and if well managed is capable of trading in excess of 300,000 litres per week – far more than some permanent petrol filling stations.” ALAN HOWARD, SAINSBURY’S SDG
To conclude, the TPFS has been considered a success by all those involved and now there is a proven system on the ground, with a second to follow; the TPFS is an alternative to the more traditional fuel storage options available in the UK without the risk of groundwater pollution.
Interview with John Boudry PetroTechnik Ltd
By Brian Baker
PetroTechnik are a household name in the UK downstream industry and particularly noted for its UPP Pipe work system. The company is headed by John Boudry and despite his trips in and out of the UK I managed to catch up with him between journeys
Q John, I have been trying to get hold of you to actually conduct this interview and my first question is where were you born?
A I was born in Belgium, Jupille -
Liege to be precise opposite a brewery. Soon after I was born my parents emigrated to the
Congo where I spent the first 10 years of my life. when did you enter the downstream industry?
A I came to the UK to learn English and decided I liked the country too much to want to live anywhere else. I first joined
Cookson and Zinn in 1975,
Q So when was Petrotechnik and how did it come about?
A I left CZ to work for a large dished end manufacturer but was headhunted back by Tony Cookson, the then CZ owner, to become Sales Director and then MD. That is when the first double skin tanks were launched in the UK. Jamie Thompson introduced me to UPP, a then Swedish owned product. The owner were interested in CZ taking the product on but there was a conflict of interest between steel (tanks) and plastic (pipes). I took the gamble of launching UPP in the UK having formed my own company and resigned from CZ in1991. In 1992 my company acquired UPP from the Swedish owners. The rest is history.

Q What are the full range of products you sell and how big would you say your market is?
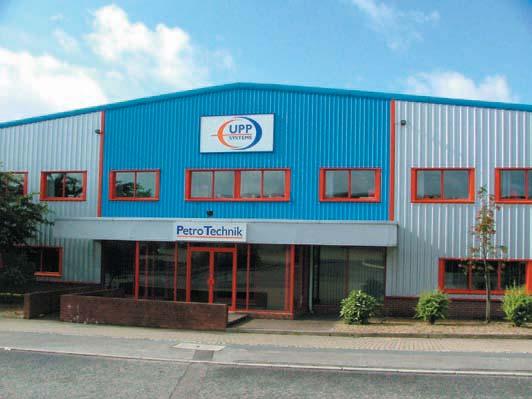
A We sell the complete UPP
Pipework system, primary and secondary together with a compatible range of PE sumps and chambers all designed with
FEA, to over 148 countries around the world. We operate under full ISO 9001:2008 QA system. Our market is close to US 45
Million with offices in
China, India, France, USA,
Brazil, Australia,
Scandinavia. We also manufacture in Brazil,
China and India as well as
Europe of course.
Our offices manage their regional distributors. For instance France manages over 30 countries and French dominions or overseas territories.
Australia manages New Zealand, etc, etc.
Q Where do you see the company going from here?
A We shall have a major announcement concerning new products to make in the near future. This will revolutionise the industry and will enable us to maintain our number one spot which we have occupied for over 15 years.
Q I guess with a global downturn over the last year or so I expect you and all your competitors are finding tough at the moment.
Tell us how you think it will go for out industry? Q I see yet again you are a major sponsor for the APEA at this year’s Conference & Exhibition.
You must think highly of the
Association and indeed your support over many years now has been most appreciative. Do you see the Association developing further or indeed what would you like to see happen?
A The APEA is the only body which represents all aspects of the industry and I include the local authorities and other legislative bodies in this. We all sing from the same hymn sheet as a result.
Training is more and more important as time goes on and H & S is vital.
Q So tell as a bit bout your life when not heading the company. Do you have any pastimes or hobbies or for that matter any passions away from the office?
Q We are starting to see movement in the above ground tank storage market, are you getting enquiries on this and in particular provision of above ground pipe work systems? ASaltwater fly fishing, gauge 1 model trains, sitting on my tractor working a few acres of
Suffolk, doing a little boating in
France and being the obedient husband of Vanessa are all passions away from the office. I need the mixture of lone and social interests as it is when I am alone away from it all that I can think, sort and prioritise what needs to be discussed with the team back at the office.
A No. Usually these units are self contained and little pipework is involved. Furthermore there is little scope for plastic pipework use above ground.
Q I see Alex, your son is getting more of a profile within the company. It must bring immense pleasure to see him showing interest in following in your footsteps, is that right? Q Finally, what changes would you like to see in the industry?
A We have just completed another financial year and finished several percentage point ahead compared to the previous year. Having said that it is clear that things are tightening up. This is why we have invested US $ 500,000,00 in India, US$ 500,000.00 in China and US$ 1,000,000.00 in the new product I mentioned before. Once the dust will have settled we will probably see another round of acquisitions of weakened or s m a l l e r companies by the bigger boys. We are also likely to see an even greater fragmentation of the
Operator / End Users for our products with OilCos divesting themselves frantically of their retail network worldwide. A Alex is good at what he does but then so is everyone else in the business or they wouldn’t be employed. He is not being groomed to take over from me.
Neither he or I believe that it is the right thing to do. As I get older I realise that a younger and more professional manager will be required to head the business in the future and I can think of three or four likely candidates
within the business who probably have what is required. A I think the changes taking place today are both inevitable and of great benefit for those who wish to progress the industry as a whole. It was the disappearance of a few management layers in the major OilCos a few years ago which enabled companies like ours to become “supply partners” taking on more responsibilities rather than remain a small link in the supply chain. A structured approach to training by the major operators with a common focus would greatly help too. Thanks for taking some time out on this interview John it has been a real pleasure and hope we can catch up again in the near future.
64 APEA tel/fax 0845 603 5507 www.apea.org.uk
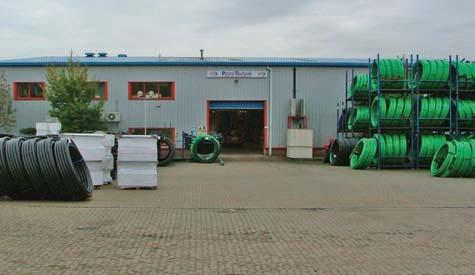
The APEA Eastern Branch factory visit to the ZVA nozzle factory 19/20th May, 2009
APEA and Eastern Branch members visited the Elaflex Hiby nozzle factory on May 19th & 20th 2009. Elaflex and Hiby are a partnership company (ETT) that amalgamates the sales and production of ZVA nozzle, petrol dispensing hoses, SSB nozzle safety break couplings and refuelling accessories.
After landing in Dusseldorf we
embarked on a pleasant coach journey through the picturesque Sauerland countryside arriving in the small town of Plettenberg. Following a traditional lunch we visited the foundry, “factory One”, which much to everyone’s surprise was situated in the centre of the town and painted brown and cream. The foundry, the machining and the assembling are organised in accordance with the “Toyota production concept”. We viewed the preparation of the nozzle core production and its complexities which gave us an appreciation of the casting process in the smelting furnace. We saw the extensive test facilities. The small volume production nozzles including the new ZVG-2 LPG nozzle, ZVA 25 & 32 high flow nozzles and speciality nozzles such as the ZVA for AdBlue, the ZVA VA Stainless Steel nozzle for alcohols, and over-wing aircraft refuelling nozzles ZVF25 & ZVF 40.
The foundry has an integrated mould and tool construction with an automatic moulding line with sand castings. The strength of the foundry lies in the use of complex core moulds and the possibility of completing multiple and differing complex cores in a single box unit. It can cast parts, thin walled, 2-3mm almost free from burrs, and pressure sealed up to 6 bar. Small cast small quantities ( 50 – 100 pcs ) are also possible as well as mass production
up to 100.000 pcs. The surface quality of the products is smooth and can be optimised by further special treatments, such as polishing with balls or granules. The foundry also cast components of a high performance cooling-system, assembled into one of the top German sports cars. The evening was rounded of with a splendid dinner hosted by Elaflex and Hiby and our thanks and appreciation goes to them for the kindness and hospitality extended to us during our visit. Next day we went to “factory Two” and the main manufacturing and large volume assembling plant
APEA tel/fax 0845 603 5507 www.apea.org.uk 65
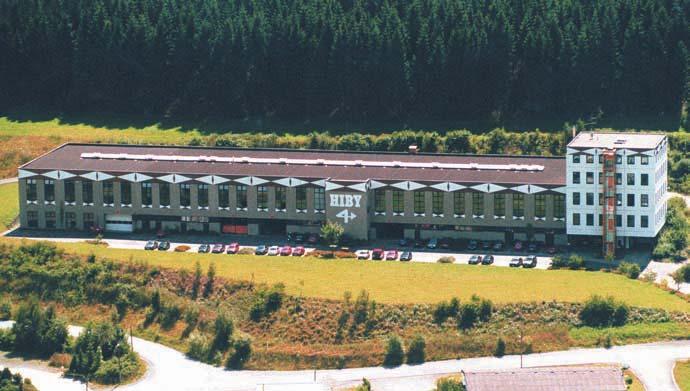
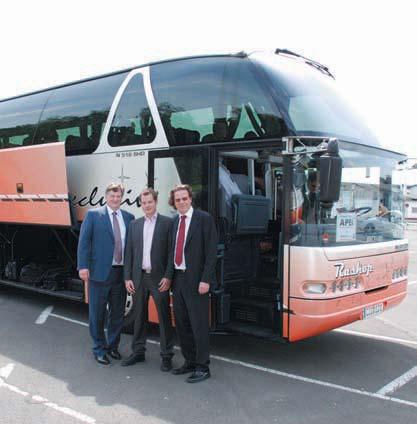
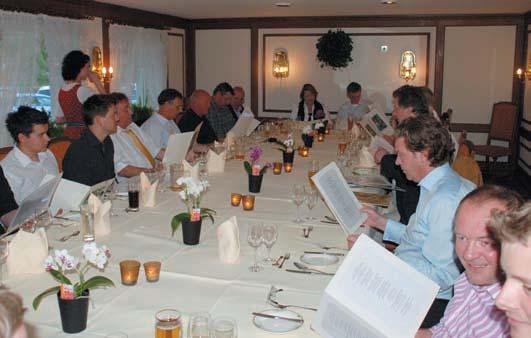
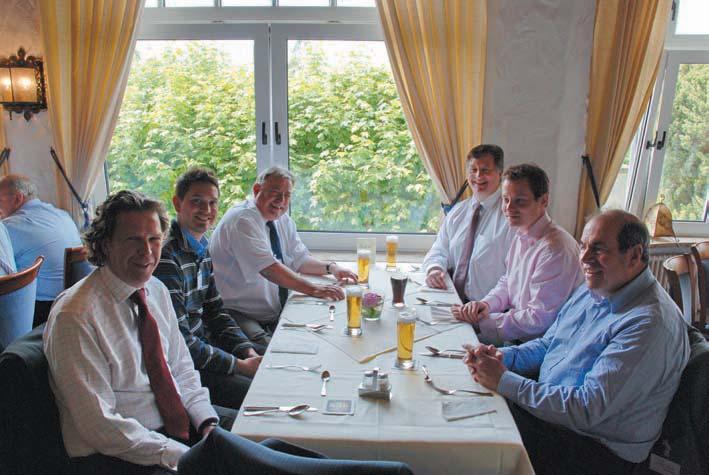