
30 minute read
APEA2009 Conference, Exhibition and Awards Dinner
• The LPG supplier has changed its policy on the inspection of underground pipe work since the incident and has reviewed their underground pipe work inspection procedure. This is to include decommissioning of a line to allow a pressure test.
• Manual recording is not sufficiently accurate to reliably identify stock losses from leaks and consequently the petrol company involved are trialing a new electronic monitoring sheet which would identify leaks on a daily basis. If the trial is successful, the sheet will be rolled out to all sites on the network.
Advertisement
Discussion
The causes of accidents/dangerous occurrences can be classified into immediate, underlying and root causes. By considering these collectively a picture of why the accident occurred can be built up.
Immediate Cause
This is the most obvious reason why an adverse event happens. The immediate cause of the incident was an ongoing leak of LPG gas from a damaged supply pipe which found its way into the base of the electric meter cupboard, forming an explosive mixture which appears to have been ignited by an electrical spark.
Underlying Causes
These are the less obvious system or organisational reasons for an adverse event. In this case the underlying causes are:
1. damage occurring to the underground pipe and this damage going undetected. This initial damage, at least in part, may be due to the pipe not being installed in accordance with the manufacturer’s instructions.
2. the failure to properly identify the cause of the gas smells at the premises during July and August 2008. 3. The ability of the leaked LPG to migrate through ducting and into an area where it could form an explosive mixture and be exposed to a source of ignition.
Root Causes
The Root cause is the initiating events or failings which led to all other causes. These are generally management, planning or organisational failings.
1. Failure during construction to properly manage the installation of the underground pipe and possibly any work subsequent to this installation.
2. There was no system to leak test underground pipe work following repeated reports of LPG smells.
3. Failure during construction and subsequent site checks to ensure ducting leading from the man hole chamber into the building was adequately sealed.
Conclusions and Recommendations
1. The explosion resulted from a damaged and leaking underground pipe which allowed gas to migrate through an unsealed electrical duct into the electrical meter cupboard where it was ignited. Operators and regulators therefore need to ensure that pipework is properly installed and that all ducts and similar pathways are sealed to prevent flammable vapours from migrating into areas where they could cause hazards.
2. It is likely that the damage to the pipe occurred around the time of the construction of the site and that subsequent corrosion allowed gas to leak, probably becoming significant at some point during the first half of 2008.
Consequently, monitoring of the installation and any subsequent ground work or vehicle movements near this type of pipework needs to be carefully managed. 3. Wet stock monitoring systems at the time of the incident were not designed to identify leaks of LPG and ways of improving the sensitivity of this means of identifying leaks should be progressed.
4. At the time of the incident, systems for the inspection and maintenance of the LPG installation at the premises were apparently in line with similar regimes across the industry although there was no satisfactory system to identify the condition and integrity of the underground LPG pipe work.
Failure rates on underground pipes are currently reported to be low, but in the event of such a failure occurring, the potential for high risk situations developing is high. As underground pipe work becomes older, the potential for failures becomes higher due to the effects of corrosion, particularly on defects which occurred during installation or following subsequent damage.
Where there is any uncertainty surrounding emergency response for reported LPG smells it is recommended that the presumed action should lean towards testing underground pipe lines. Routine testing of lines should also be considered as part of a routine maintenance system for the overall LPG installation.
Note
This report is partly based on the internal investigation report provided by the oil company following the incident as the Petroleum Licensing Authority did not investigate until some time after the incident by which time the physical evidence on site was no longer available.
50 APEA tel/fax 0845 603 5507 www.apea.org.uk
Managing the Fuel Requirements of a Local Authority by “Greener” Thinking
By Paul Gillespie CMIOSH
The Wakefield metropolitan district is situated in West Yorkshire (UK) and covers a semi-rural area of 350 square kilometres with a population size of around 315,000. It has a diverse range of city, urban and rural communities.
Wakefield is leading the way in ensuring that natural resources are used efficiently, waste is avoided and that we protect our biodiversity. Our spending decisions are an important instrument in tackling climate change both by reducing carbon emissions and ensuring that our infrastructure is resilient to climate change. Making the right choices now will contribute both to our citizens’ standard of living and quality of life. Wakefield Council operates 209 large goods vehicles, 368 commercial vehicles under 3500kg passenger cars and a large, small plant list, as well as up to 100 hire vehicles, at any one time. Additionally, approximately 3,500 employees use their own cars on Council business.
Fleet Procurement
The Council and its partners have recently signed "The Nottingham Declaration" and have set a target for reducing carbon dioxide emissions by 25% by the year 2012.
Wakefield’s Transport Services Team is helping to meet these challenges by championing socially responsible procurement in the vehicle fleet procurement process. The following model (fig 1) outlines the areas being focused on.
It details a new approach to fleet procurement that not only meets Government and European guidelines but is providing significant benefits in both economic and environmental terms for the citizens of its district.
Within procurement, the Government’s definition of ‘best value’ is the “optimum combination of whole life costs and benefits to meet the customer’s requirements. This approach enables sustainability and quality to be taken into account. For example, the consideration of whole life costs”.
Transport Services had always been mindful of the environmental impact and running costs of vehicles in the past, but never before was the evaluation process applied so rigorously. Prospective contractors are now asked to provide the following information as part of the tender process: • Whole Life Cost- Acquisition, ownership and maintenance costs • Carbon emissions
“meet the team” L to R- Brendan McNamara (Transport Technical Manager) Paul Gillespie (Fuel/Safety Officer) Mick Berry (Fleet • Fuel consumption Enforcement & Training Manager) Chris Gray (Fleet Enforcement & Assessment Officer) David Wilcock (Fleet Enforcement & Assessment Officer), Pete Johnson (Transport Services Manager) • Carbon footprint incl. the manufacturing process • Alternative fuel options
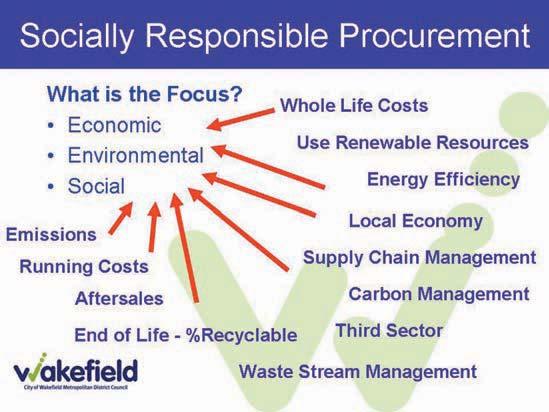
Fleet Re-fuelling Facilities
All sites are overseen and monitored by Paul Gillespie, Transport’s Logistics and Health and Safety Officer, who is well versed in the subject, being APEA trained (Petrol Filling Stations – Risk Assessment, Audit and Inspection/Construction, Safety and Environmental Protection), as well as studying Occupational and Environmental Health and Safety Management at Portsmouth University at MSc level. As well as being a member of the APEA, Paul has been a Chartered Member of the Institution of Occupational Safety and Health (CMIOSH) for over three years and is constantly updating his continued professional development file. Transport Services currently operate fuel dispensing at seven sites. These fuel sites are managed via an IT based Fuel Management System. Each vehicle has an individual key so that its identity and mileage can be verified from a
APEA tel/fax 0845 603 5507 www.apea.org.uk 51
Newton Bar
Castleford
South Kirkby
Normanton
Fitzwilliam Wakefield (Tadman St) Wakefield (TLS)
centrally held asset management system; this prevents abuse of the system. In addition, each of three key types controls the relevant fuel type that is dispensed: • Black Key = Diesel • Red Key = Petrol • Blue Key = Gas Oil & Ad-Blue
The Fuel Management System also monitors wet stock control i.e. the fuel stock levels available. Each tank and site is independently monitored by the system and when any level drops below a predetermined stock level the system automatically notifies Transport Services so that re-orders can be placed. Fuel deliveries are always for the maximum amount of fuel possible which is triggered via the Fuel Management System; this varies from tank to tank, in line with the safe working capacity.
Currently stocks provide a sevenday supply, based on normal service use.
Of the seven re-fuelling sites across the district; four of the sites have underground tanks, aged between fifteen and eighteen years and all are single-skin metallic tanks. The five above ground tanks vary in age from three to fifteen years.
Over the 2008 calendar year, Wakefield Council used 2.5 million litres of diesel, 68,000 litres of unleaded petrol and 445,000 litres of gas oil.
The diesel we use is 5% bio diesel and 95% mineral diesel (ordinary diesel) and obviously
X
conforms to BS EN 590. O u r suppliers, Bayfords Oils UK, import fuel by barge on the Aire a n d Calder Canal which puts money into conserving the environment along the canal but also reduces the need to run trucks on the road, reducing carbon emissions by the equivalent of 30 tanker trips.
Bayfords are also planning on installing a blending facility at their Leeds depot, which would allow customers to specify a higher percentage blend of bio diesel; something we will be looking at closely.
Managing the “Wet-Stock”
Obviously due to the age of the tanks, vigilance is vital, meter readings from the pumps are taken daily, furthermore, the competent person will take a dip reading (carbon dip sticks are used in 200 and 150 litre segments) each to establish how much fuel has been issued. The figures are then compared to establish a plus or minus situation.
After several years of monitoring the wet-stock figures for the singleskin metallic tanks, Transport Services have developed a history of “what to expect” when changing weather conditions are experienced. For example, during a warm spell the tank dip will be higher than usual, or from warm to wet and windy the dip will start to show a minus.
Chamber Breathing - the
differences represent changes in air Petrol Diesel Gas Oil Ad-Blue pressure, fuel expansion and contraction distorting the tank X X X X which in turn changes the true stock level of the fuel when measuring by X X X means of the dip stick. As long as X X X the figures even out over a short period of time and go back to X X normal (base line) then all is fine. This type of understanding guides X X the level of concern over measured X X loss or gains of product from the under ground tanks. If discrepancies persist then the first action would be to double check the readings/figures and re-dip the tank. Secondly; confirmation is sought on the amount of fuel that should be present, through the Triscan fuel management system. If all figures and details are still causing concern then the following procedures would be followed: • Senior management informed of the situation, with all details available. • Contact the fuel maintenance contractor (Powerpost) and give them all the relevant information. • Re-dip the tank and collate meter/Tri-scan data every 30 minutes. • Inform the petroleum officer/environment agency of the situation and follow any instructions that are suggested. • The fuel maintenance contractor will arrange relevant specialist help. • After the agreed period of time, if a loss of product from the tank is still proving a cause for concern, the particular tank in question would be pumped out by an approved and competent contractor and the product transferred into one of the other tanks. • Alternatively, if concerns were over additional product in the tank then tests would be conducted to determine if water is present in the tank, by means of green “water finding paste”. • Whatever the outcome of any scenario/situation, a full investigation would take place to establish the cause and a report produced for the relevant Paul Gillespie delivering in house training; fuel deliveries by road tanker authorities.

The diverse nature of the Council’s services and depots determine that there is a high rate of turnover in both operational responsibility and staff. This has to be managed via regular site risk assessment and ensures a steady demand for the training of staff in the safe acceptance of fuel deliveries associated with wet stock control etc.
As well as carrying out the Petrol Filling Stations Operators Fire and Explosion Risk Assessment (FSG 5061d) for each of our three sites that store and deliver petrol, Transport Services deliver an “inhouse” training session for fuel deliveries, wet-stock control, water removal from tank chambers as well as safe use of Ad-Blue.
Training is delivered at Transport Services; Newton Bar from two modern training suites. This site gives hands-on access to the re-fuelling site.
The in-house course lasts three hours and covers an assisted delivery by a competent person with the following subjects/objectives:
• What legislation governs the delivery of fuel:
• The characteristics of Petrol,
Diesel and Gas-Oil:
• Demonstrates competence in the receipt of a fuel delivery:
• The principles of fire and its prevention:
• What action to take in the event of accidents, spillages and other emergencies:
• The principals of vapour recovery:
• Wet-stock control (determine a plus/minus situation and what action to take)
The whole objective of the training is to deliver a competent person status; raising the awareness of what could go wrong at a particular refuelling site for which an individual is responsible and to provide on-site monitoring and knowledge that reflects the competent person’s own site/depot and fuel point operating conditions.
Following the introduction of AdBlue and on examination of fleet procurement profiles, Transport Services estimated that the fleet’s future usage would be around 30,000 litres by 2012.
Initially, 207 litre barrels with a pump or 20 litre containers of AdBlue issued via the stores at different depots were used. As demand grew, we were quickly in the position requiring that we make formal contractual arrangements with the suppliers, to bulk buy via a suitable tank and distribution system.
After talking to our suppliers, contractors and manufacturers we produced a technical specification detailing our Ad-Blue tank requirements and carried out a tender exercise. This resulted in the installation of a 2000 litre tank.
This tank is now operational at the Newton Bar site (the first of three) connected to the fuel management system and all users have received training in its safe use.
In Conclusion
Emergency Fuel Planning
Transport Services take an active role in the Authority’s Emergency Planning Committee, giving advice and help in the production/updating of the Emergency Fuel Plan.
Two key areas of responsibly fall to Transport Services: i) the provision, operation and maintenance of the Council’s vehicle and plant fleet. ii) to ensure adequate provision of fuel across the district for Council services. These functions would be expected to continue during any civil emergency etc.
News or situations that could affect the service regarding the supply of fuel are constantly monitored.
A good working relationship is maintained with our suppliers, Bayfords Oil UK. The quality and
consistency of the information and advice being provided is good and their contingency planning appears adequate. The public sector business environment is very challenging, current value for money agendas are combined with a requirement for us to lead on environmental matters. Whilst challenged with increasing budgets pressures, we endeavour to reduce our carbon footprint as well as deliver essential Vehicle Fleet Numbers services, all of which whilst planning for future Company 2007 2008 2009 2010 2011 2012 facilities replacement requirements. WMDC 19 33 43 104 118 144 Monitoring the Other Fleet Customers 16 22 34 39 44 49 fuel stocks and ensuring that current legislation Ad-Blue Estimate Usage (Litres) is adhered to is just part of the 12,000 22,000 25,000 30,000 process. The task at hand now involves effective project planning with regard to any major work that may need to be carried out to the fuel sites or the equipment we operate (sustainability). This is supported by a services team which not only manages the logistics of the fuel sites but is responsible for fleet health, safety and environmental issues. The team delivers assessments and training to the end user, “the driver”, to develop “smarter driving techniques” and deliver fuel efficient drivers, a 360 degree service delivery. Service demands are forever changing requiring Transport Services to plan, adapt and react to the changes. This is the nature of the service and facilities we manage. A fuel site can be likened to a living organism, it ages, it needs feeding regularly, needs looking after, medicine when it is ill, it constantly changes with its environment but most crucially if you neglect it…..do not be surprised if it turns around and bites you! “It is not the strongest of the species that survives, nor the most intelligent that survives, it’s the one that is the most adaptable to change” Charles Darwin 1879
Unattended Self Service –Have We Got It Right?
By Brian Baker, Milton Keynes Council
The concept of Unattended Self Service Petrol Stations has been with us for many years. In fact its method of operation evolved from its early appearance in the early 1950s in Europe that saw its popularity spread to all parts of that continent and beyond.
The concept, as most of us know, is that the site can remain open for fuel without staff present and the pioneer sites saw the introduction of note or even coin dispensers where the amount of fuel according to the amount of cash dispensed was supplied. It was as simple as that.
Motorists could obtain fuel outside of normal opening hours and safety came in the form of a dedicated telephone inside a wooden box to call the emergency services as well as conveniently containing a portable fire extinguisher, some limited instructions of what to do and of course a handy isolation switch for the motorist to operate and shut down the electrical supply to the pumps.
The introduction of Attended Self Service, extended opening hours, the mass use of credit and debit cards and the introduction of the high street supermarkets retailing fuel combined to see the Unattended Self Service reduce in number to only a couple of hundred sites, mostly in rural areas.
Growth in UK Unattended Sites
There now exists a drive to return to the Unattended Self Service site, lead by the same high street supermarkets and it must be said here that across Europe and Scandinavia in particular unattended sites are the norm rather than the exception.
Having modified the Petroleum Circular in 2005 PETEL 65/59a it was thought that the risk assessment approach specific to each site would allow greater flexibility under the Dangerous Substances and Explosives Atmospheres Regulations 2002 (DSEAR)
After a few years, some petroleum licensing authorities felt uncomfortable with the concept and unsure that the claimed control measures were effective, particularly in an emergency situation. Following discussion at the Chief Fire Officers Association
Petroleum and Explosives Working Group and with the support of Petroleum Enforcement Liaison Group (PELG) it was decided that a national campaign be commenced over a short defined period to try and establish whether these sites were operating in accordance with their licensing conditions and risk assessments. The exercise took place in early 2009 and produced some alarming findings.

Early Findings and Conclusions
To begin with, each known national Unattended Self Service operator was contacted in writing about the impending campaign and that in addition to a routine inspection, an unannounced inspection may also take place to sample accurately the safe operating conditions of that particular site were in place. The operators gave full cooperation and provided lists of their sites which operate in USS mode.
The exercise was aimed at gathering information on the effectiveness of the control measures identified by the operators as being in place to reduce risks associated with USS operating mode at their petrol filling stations. • Of the 101 sites visited by 21 different Petroleum Licensing
Authorities from the Highlands of
Scotland to the extremities of
Cornwall, 60 were found to fail in one or more of the control measures that they stated were in place.
• Failures fell into three distinct categories:
(i) The emergency procedure failed due to a communication problem which was either the emergency phone did not function, or the emergency phone did function but did not call a location from which an emergency response was available
(ii) Staff who were contacted were not Competent to deal with an emergency on the forecourt
(iii)Forecourt engineered arrangements were not satisfactory. This was any or some of the following:
I. Lighting to the dispensing area or cabinet location inadequate
II. Latch pins on nozzles in place.
III. Certain dispensing units not operating
IV. Too many dispensers available. at any one time
V. Signage – emergency action notices and use of containers not displayed
VI. Emergency cabinet not visible from dispensing location
VII.Difficulty in opening emergency cabinet
VIII.Availability and type of fire extinguishers was not adequate
IX. Emergency switches not operating to isolate dispensers
X. Closed circuit TV not functioning or monitoring
As a result of the national exercise, 14 Prohibition Notices and 1 Improvement Notice were served on the Licensees. The net result of the 101 sites inspected saw 41 sites Pass but worryingly 60 sites failed.
Partly as a result of this exercise, and partly due to other factors including the availability of new
technology, a change in banking practices (age of persons able to obtain credit and debit cards), and proposals for remotely located unmanned petrol stations, a Sub Group has been set up between Licensing Authorities represented at PELG and the major Operator’s to find more acceptable solutions. Issues that this group need to address are;
• Under Age Sales - How will these be managed effectively?
• How will the use of Approved
Containers be managed?
• Phase 1 of the Risk Assessment must be site specific and based on good local information, and not rely on Company Policy • The Attendance Time for a
Competent Person to deal with an Emergency should be clearly established. It should be varied according to the location, the risk locally, the realistic control measures. Who calls the
Emergency Services? Is the CCTV working properly?
• What facilities exist for customers splashed with petrol/fuel?
• Staff Training should be improved so that duty staff should be able to attend and deal with an emergency such as someone doused with fuel, first aid incidents, access to personal protective equipment, split fuel lines and fuel tanks, overfills and so on.
• The correct type and number of portable fire extinguishers should be provided and available
• Should the emergency switch (button) be activated deactivating the dispensers, a audible and visual signal should be relayed at the forecourt monitoring point?
• CCTV. There is no point in having this installed if it is not monitored for emergency response purposes. There may be differing levels of monitoring and sophistication such as mass detection, smoke detection, vapour detection
• Use of a handover book and check list which should be used daily
• There should be a designated phone In-store
• Devices such as glass bolts should be obvious on how to use
• At present, some sites that have emergency telephones could be used by the customer and the site operator is unaware that the emergency services have been called!
• Possibly person monitoring CCTV should be able to deactivate the dispensers therefore reducing the risk of vandalism, cars entering the site on fire, suicide attempts, under age sales and use of illicit containers
The exercise results will be a major factor in making some alterations on how Unattended Sites may operate in the future. Have we got it right? Not yet but we are getting there.
Acknowledgements; As a regulator in a local authority the names of all parties concerned have been excluded. Once issues on this topic are concluded it may be possible to publish all participants.
56 APEA tel/fax 0845 603 5507 www.apea.org.uk
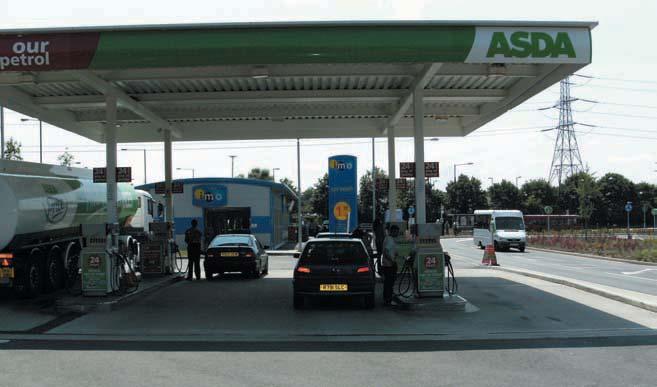
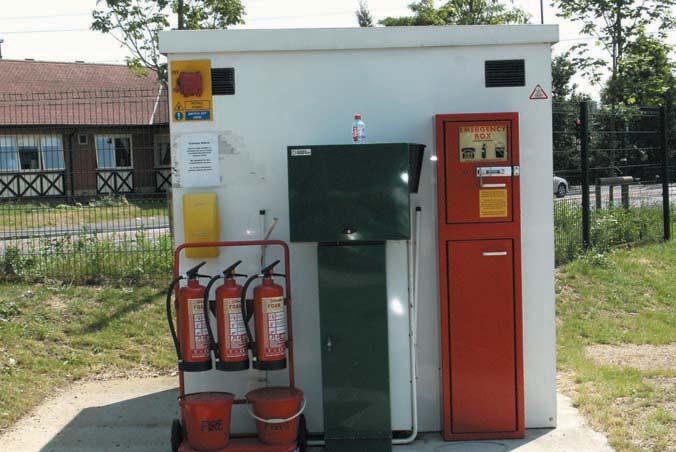
By Brian Baker
The Association were recently requested to provide bespoke training for the second time to the Bahrain Petroleum Oil Company (BAPCO) and a team of 4 Trainers were despatched in early June to deliver this specialised presentation over 3 days whilst residing at BAPCO’s own training facility based at Alawi.
The Kingdom of Bahrain has a population of about 1.2m people and car ownership per head of
population is one of the highest in the world at to over of 500,000 cars.
In all there are 46 Service Stations all selling the BAPCO brand where the Company are State owned and are the sole distributors for the country.
In Bahrain, the capital is Manama which is densely populated compared to all other parts of the country. Throughputs per site are large compared to most stations in Europe with some sites reaching 40 m litres per year.
The training provided to the company was a more advanced course than that provided two years ago and concentrated on greater detail to site layout and planning, fire safety by design in respect of passive and active fire safety measures to be considered at design stage. There was also detailed input and discussions on vapour recovery design in terms of Stage 1b and 2. The sessions closed with a day committed to wet stock management
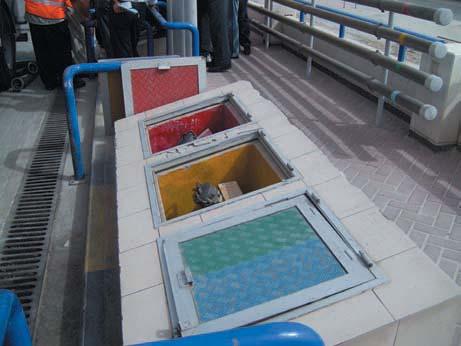
that was of immense benefit to the company illustrating some measures to reduce wet stock losses. It needs to be recognised that stock losses are much higher
than Europe mainly due to the high temperatures of the region.
The day we were on the sites a reading of 46 degrees centigrade was recorded and following a print out from electronic gauges recorded temperature of product in the tanks in excess of 37 degrees!
This undoubtedly increases evaporation and present unique challenges to Bahrain and for that matter the whole region.
With the exception of diesel, two other grades are sold – “Mumtaz” which has a rated octane number of 95 and “Jayyid” which has a rating of 91. The interesting point here is that the rough translation from Arabic to English means “Excellent” or “Perfect “grades”
At the time of our visit, BAPCO are
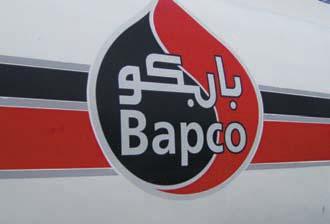
Tanker logo Colour coding of grades
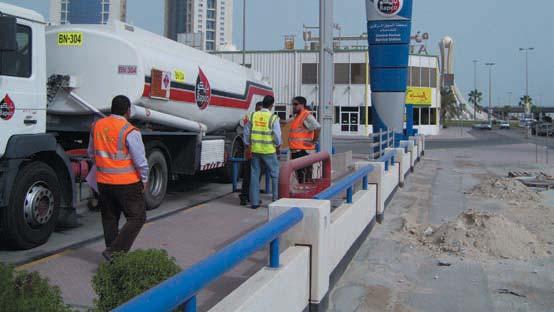

Congestion at the Hooma site
Tanker delivery
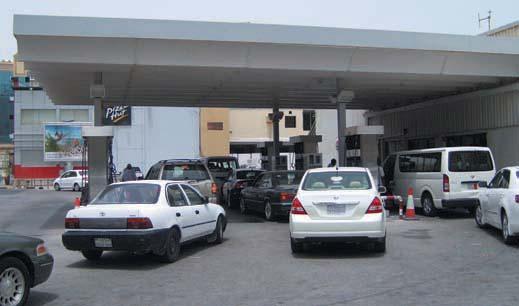
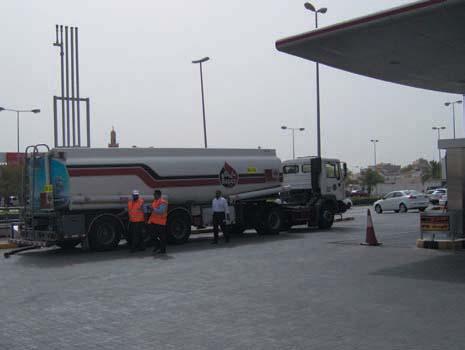
preparing to transfer their 16 owned company operated sites to the private sector and some investment will be needed in the future. That said there are signs that similarities are occurring to that of the USA and Europe where sites often have other facilities such as Vehicle Repair Workshops and Convenience Stores that offer a wide selection of goods but one fundamental difference is that all sites are Attended Service,
We left after four days and experienced some wonderful hospitality from our hosts and the working relationship we forged back in 2007 was again enhanced and the trainers involved, Bob Conlin, Jamie Thompson, Rodney Carter and myself, believe we have furthered the Association’s growing reputation outside the UK. Who knows, maybe one day we will see a Branch inaugurated in Bahrain.

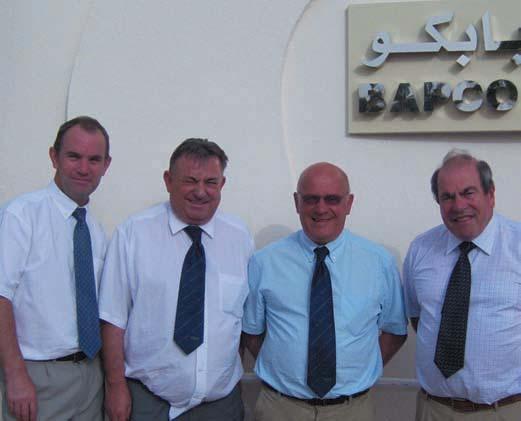
Typical attended site at Central Market Left to right: Bob Conlin, Brian Baker, Jamie Thompson, Rodney Carter
Temporary Petrol Filling Station, a Success…
By Jacquie Holt, Terence Barker Ltd
In 2006 we designed on paper, a modular aboveground fuel station; the idea a modular unmanned, self service fuel station using the Convault aboveground protected fuel tank; the safety of the tanks already proven as they are in use at US military bases across the UK and Europe. Our hope, this fuel station could answer the problems that people living in rural areas are now faced with regarding the distance driven to a fuel station to refuel. The intention, that the unit could be erected on an owner's prepared base in a matter of days; civil engineering works would be minimal and an advantage, avoiding the potential risk to pollute the soil and groundwater. They were designed as free standing, debit / credit card operated, able to hold up to 3 products and allow 4 vehicles to fill simultaneously.
Two years later in the Autumn of 2008 we were approached by Williams Southern Ltd with regard to producing a Temporary Petrol Filling Station (TPFS) for Sainsbury’s based around the Convault Above Ground Protected Tank. The idea was that the TPFS would be on site and dispensing fuel whilst the existing fuel forecourt was being refurbished by Williams Southern Ltd, the lead contractors, for a period of about 13 weeks. It was Sainsbury’s intention, to move the TPFS to other stores around the country where further forecourt refurbishments work would take place.
We attended the first meeting at Martindales’ offices at Oakington in early November 2008 attended by Alan Howard of Sainsbury’s; representatives from Martindales & Williams Southern Ltd and the electrical contractors, T E Ramm and Co.
It was agreed that two 41,600 litre bunded Convault Tanks with two compartments in each were required; each Convault would hold Petrol and Diesel. Also required as part of the project would be the gauging system, the tanks fitted with OPW contents gauges which indicate any water detected in the fuels together with high level alarm with audible warning.
Also required, a secure cabinet containing the uplift pumps, the electrics and the Stage IB vapour collection point, the dispensing pumps were supplied by Sainsbury’s, each tank suppling fuel to four Dresser Opus 9000 twin nozzle


dispensers, eight in total, all of which have built-in Stage II vapour recovery.
The uplift pumps deliver the fuel into the tanks from a gravity feed tanker via an 800 LPM centrifugal ATEX approved uplift pump. It takes approximately10 minutes to off load 7,500 litres of fuel, and while fuel deliveries are taking place the site is closed.
It was a specific requirement that each of the four compartments, two holding unleaded petrol and two road diesel, would have its own designated uplift pump, but in the event of an emergency it would be possible to divert the fuel into the other appropriate compartment holding like fuel. To ensure no cross contamination would take place the pumps, corresponding pipework and compartments are all clearly labelled; also, each compartment within the Convault is built as an individual tank and tested as an individual tank. The tanks remain under pressure for a minimum of 5 days until after the inner tanks have been encased in concrete and the mould holding the concrete released.
We received the order in early December for delivery to site on the 1st March this year so that the TPFS could be operational on Monday 16th March at 8.00 a.m. We were very conscious that this would be a very sharp learning curve appreciating that we would need to rely heavily on the experts to ensure the project would be approved with all the necessary safety mechanisms in place.
“The Petroleum Group of the London Fire and Emergency Planning Authority (LFEPA) working under the Lead Authority Partnership agreement they have with Sainsbury’s liaised with the architects, consultants, contractors, the fuel supplying oil company and the local Petroleum Licensing Authority from the inception of the project to ensure that the Mobile Temporary Petrol Filling Station (MTPFS) complied with national guidance and was suitable for licensing under the Petroleum (Consolidation) Act 1928. Documentation listing all the equipment used to construct the MTPFS, and the arrangements to that must be agreed locally with each Petroleum Licensing Authority has been produced. The main local arrangements be considered are: location, imperforate forecourt area with suitable drainage to a Class I separator, tanker route, and the site specific risk assessments.
The LFEPA oversaw the construction and the first installation of the MTPFS to be satisfied of compliance, and has advised on improvements and modifications that have been found to be necessary or desirable once the unit was brought into use.” Ray Blake HEAD OF PETROLEUM LONDON FIRE BRIGADE
Working closely with Ray Blake regarding licensing issues, late January he raised a valid question, in the event of the transfer pump failing midst delivery what would the tanker driver do with the fuel in his line? This potential problem was overcome with the help of Roger Wyatt, our fuel consultant, who suggested a modification to the pump tanker connection. Roger helped design a means of draining out the fuel lines with the aid of ATEX approved hand pumps, one for Derv and one for petrol, the fuel to be drained into small dump tanks positioned at the rear of the uplift pump cabinet. Each one of these two dump tanks was to be fitted with an air-operated pump for returning the fuel back into the appropriate compartment. The dump tanks were installed, each
had a capacity of 40 litres with an 80mm filling point, this could also be used when weights and measures carried out checks on the dispensing pumps, the fuel could be returned to the dump tanks via a funnel and returned to the main tanks in the same way. A few weeks after the TPFS had been installed our fitters returned to Hankridge Farm, and replaced the 40 litre tanks with larger tanks of 225 litre capacity, this simple system has been working perfectly since. Each 41,600 litre Convault Tank used in this project contains 18 fi cubic metres of concrete, weighs 48 tonnes and is 10.7 metres in length. The component parts consisting of two of these tanks, a large selfcontained uplift pump lockable cabinet, fascias, stands and pipework were loaded in our yard on the afternoon of Friday 27th February and arrived on site at Taunton on Sunday, 1st March at 7.00 pm and by midnight were off-loaded and in position in the car park of the superstore. The units took up 32 car park spaces to one end of the car park, Sainsbury’s also installed two kiosks for easy payment for their customers; fundamentally it was important that Sainsbury’s’ very valuable customers were not inconvenienced and could refuel their vehicles at the same time as buying their weekly shop. Sainsbury’s were not prepared to lose valuable customers to the competition with both the fuel trade and supermarket trade. The site at Taunton is manned and open for fuel sales 24 hours a day. The TPFS was in use from Monday 16th March until our fitters started to dismantle on the 8th July ready for transporting to the second site for renovation, Deepdale Preston. Before being transported to Preston the tanks and dispensers were drained down; de-gassing was not a requirement. The only requirement necessary was that the drivers needed ADR licenses to carry the tanks on the road. Continually reviewing the design of the project with all involved it became apparent that there was a requirement to eliminate the ‘human element’ with the potential to overfill the tank, options were reviewed and it was decided that the uplift pumps needed a failsafe cut-off system that would shut the active uplift pump down when the tank reached its safe working capacity and more importantly, a system that could not be over-