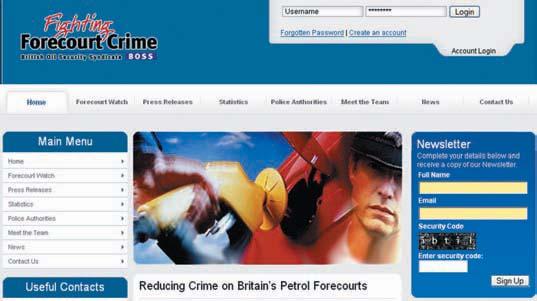
34 minute read
News
BOSS launches new website
The British Oil Security Syndicate (BOSS) has unveiled its new website at www.bossuk.org.
Advertisement
The new site aims to provide BOSS’s police and petrol retail partners with a comprehensive information resource as well as informing visitors about the campaigning work that BOSS undertakes in order to combat crime on petrol station forecourts across Britain.
Kevin Eastwood, executive director of BOSS, said: “We are working hard to increase public awareness of BOSS and the work we carry out with our partners to combat forecourt crime. Our new website is an important part of that effort.”
For more information, please visit www.bossuk.org.
KPS launches nextgeneration pipe for LPG
Market leading petrol pipe manufacturer KPS launches the firstever plastic pipe for LPG. The pipe will break new ground for the company, providing a world market potential valued at €3 million per annum.
KPS has brought its successful, ATEX-compliant pipe technology to the LPG (liquefied petroleum gas) fuel market. The LPG pipe, offering the same unique conductive properties as KPS’s petrol pipes, is set to be the new benchmark on the market.
The pipes presently used for LPG fuel are either made entirely from steel or from steel with a plastic coating, explains Fredrik Hellner, Sales & Marketing Director. Corrosion, both external and internal, is a big problem and poses a significant risk for leakages and damage to cars and dispensers. Our pipes are corrosion-free, and therefore offer considerable advantages in terms of both safety, durability and cost efficiency.
KPS’s LPG pipe is a 100 per cent plastic pipe with a permeation liner and a conductive inner layer. Therefore, they are corrosion free and come at a very competitive price. The semi-flexible pipes are easily rolled out on site from one end to the other, and no welding is needed.
“At a recent installation in France, the installation of our LPG pipes took less than one day, including pressure testing of the pipes”, Fredrik Hellner continues. This represents enormous savings in cost and time compared to other types of pipes.
Substantial growth opportunities
Because of its green properties as a fuel, the market for LPG is growing at a rate of approximately 8 to 10 per cent per year. It is one of the most commonly used green fuels in Italy, Poland and Turkey, and is also on the rise in France, the United Kingdom and Germany – all key markets for KPS.
LPG fuel is available at over 50 000 filling stations globally today, says Fredrik Hellner. Our new LPG pipe thus promises considerable growth opportunities and we estimate the market potential at €3 million per year.
The KPS LPG pipe will be presented at the Petrol Station 2009 exhibition in Warsaw between 6-8 of May and at AEGL in Vienna between 13-15 of May. For more information, please contact: Fredrik Hellner Sales & Marketing Director Fredrik.hellner@kpsystem.com Tel: +46 702 85 75 21
Janet Ashdown appointed president of UKPIA
Janet Ashdown, head of UK Fuels for BP Oil UK, has been appointed President of the UK Petroleum Industry Association, the trade association representing the nine main oil refiners in the UK. She succeeds the outgoing President Nick Thomas of ExxonMobil.
Janet joined BP as a graduate trainee in refining during the 1980s. Since then she has undertaken a number of roles including product trading based in New York, London and Paris, and at BP's Corporate Headquarters in the Gas & Power and European Retail and Commercial Fuels Businesses.
Janet commented “I am delighted to be taking over as President in this the 30th anniversary year of UKPIA’s formation. I look forward to working with my fellow Council members and with the UKPIA Secretariat to address the big challenges facing the UK oil refining industry in continuing to provide the secure fuel supplies that we shall need in the future, as well as meeting the tough targets for greenhouse gas reduction under EU and UK laws.”
Petrol stations to install fume capture systems
The harmful petrol vapour which escapes during the refuelling of cars at service stations will have to be captured according to a deal reached with the Council, which has been confirmed by the European Parliament. Petrol vapour contains benzene, which is known to cause cancer, and contributes to the formation of groundlevel ozone ('smog'), one of the air pollutants most damaging to human health and the environment. The European Parliament confirmed a first-reading agreement reached in informal negotiations with Council which demands that stage II petrol vapour recovery technologies will become compulsory at new or renovated service stations with large throughput as of 1 January 2012. Almost all service stations (small ones will be exempted) will be obliged to install these new technologies by 2018, 2 years earlier than proposed by the Commission. An exception exists also for service stations used exclusively in association with the construction and delivery of new motor vehicles. The Member States will draw drivers’ attention to the recovery systems by appropriate labelling of petrol pumps. They also have to lay down rules on effective, proportionate and dissuasive penalties. According to Commission
22 APEA tel/fax 0845 603 5507 www.apea.org.uk
data, the EU numbers about 110,000 service stations that employ some 440,000 workers and have an annual turnover of some 250 billion euros. The Commission will review the implementation of the directive by end 2014.
Background
Petrol contains volatile organic compounds (VOCs) that evaporate inside the fuel tank, filling the empty space in the tank above the fuel. As a vehicle is refuelled, these vapours are pushed out of the tank by the incoming fuel and, unless captured, escape into the atmosphere out of the top of the vehicle filler pipe. New technologies allow capturing this escaping vapour. This is done by creating a vacuum to suck back the vapour through the dispensing hose and nozzle, either to the station's underground storage tank or directly back to the fuel pump. Petrol vapour recovery technologies are currently being introduced by several European countries.
An existing directive (1994/63) is already regulating the control of VOCs emissions from the storage of petrol and its distribution from terminals to service stations.
The report was adopted with 598 votes in favour, 13 against and 15 abstentions. Contact : Constanze BECKERHOFF E-mail: envipress@europarl.europa.eu
Hytek launches new Alpha pump
Hytek have launched a brand new version of their reliable Alpha fuel pump. The Alpha Mk2 incorporates over 13 improvements to the original Alpha design, whilst retaining the robust stainless steel cabinet design which has made Alpha fuel pumps so reliable since they were first launched in 2002.
Available in a choice of 50, 70 or 90 litres per minute pumping speed, Alpha Mk2 now comes with the option of a front nozzle holster which is ideal for use in tank cabinets, or where space is limited. Other improvements include a new aluminium nozzle holster, and a new nozzle switch that no longer needs a magnet in the nozzle trigger guard to operate. For safety, an optional built in hose retractor is also available.
Andy Seal, Sales Director for Hytek, explained the reasons for launching Alpha Mk2 by saying “over 1300 Alphas have been installed over the last 7 years, and with the new Mk2 version we have listened to customer feedback, and incorporated new design features which make the Alpha pump even easier to install and use.”
The backlit LCD display has a new opto-isolated relay to allow connection to all fuel management systems, and a reed relay option is still available. A new electronic calibration feature also means that the number of decimal places shown and pulse output type can be changed without having to draw a 20 litre measure to recalibrate.
For installers, Hytek has improved side and rear access with new panel mounts, and a new outlet pipe has been designed to take the strain away from the meter outlet. There is also easier access to both mains and pulser junction boxes with larger terminals allowing faster connection.
The Alpha is also available in a new B100 biodiesel version, and an Adblue version was also launched recently. Standard Alphas will pump diesel and up to B30 biodiesel, and there’s a resale model available too.
Nation’s First Class C UST operator training now on-Line
Petroleum Training Solutions (PTS) announced another on-line training course for underground storage tank systems, this time for Class C
operators. The course, called Fueling Station Safety is designed specifically for convenience store employees but is suited for anyone who may respond to an alarm or spill incident at a UST with fueling dispensers. Class C operators are required to be trained in most states by August of 2012. In Oregon and California, that requirement is already in effect. By the end of 2009, Wyoming and Colorado Class C operators must be trained as well. Utah and New Mexico are looking to adopt earlier training deadline also. A class C operator is anyone who is employed at a UST site whose duties may include identifying or responding to an alarm or emergency situation such as a spill or fire. PTS created the course to fill the need for Class C training where UST owners needed a simple, standardized on-line solution. The course takes about 20 minutes and covers the basics of fueling hazards, and emergency and alarm response. Students answer a series of questions, interact with scenarios and take a quiz at the end. Those who pass can print a certificate of completion. User data and scores are maintained in the PTS on-line database. The course retails for $12.99 per user. However, the Colorado Wyoming Petroleum Marketers Associations (CWPMA) and the Oregon Petroleum Association (OPA) have teamed up with PTS to help sponsor the course in their states. Members of those groups get a 3-dollar per user discount. And PTS offers bulk discount for companies with large number of class C operators. Mark Larson, executive director of CWPMA, said “Because of the turnover retailers experience with employees, the Class C operator training will be the most frequently utilized program. PTS understands this and has developed a comprehensive, yet simple… and almost entertaining…product that anyone can use anytime, day or night. Say “Goodbye” to any concerns you had about repetitive Class C operator training!” Dave Dodson of Sheetz , Altoona,
24 APEA tel/fax 0845 603 5507 www.apea.org.uk

PA, said “The program is awesome. It is very accurate and covers all of the requirements in an easy to use format that is understandable for all types of store employees. The timing and pace is fine. I think you guy's hit a home run with this approach.”
Recently, Petroleum Training Solutions launched the nation’s first ever state-approved on-line operator training for Class A and B operators in Colorado. Instructor and PTS partner Ben Thomas led about 50 attendees through 8 hours worth course material May 5-6, 2009. To learn more about the course, go to www.petroleumtrainingsolutions.co m/classc.html For more information about our webinars, call 001 866-301-8265 or email Ben@PetroleumTrainingSolutions.com
New scheme launched to drive down forecourt crime
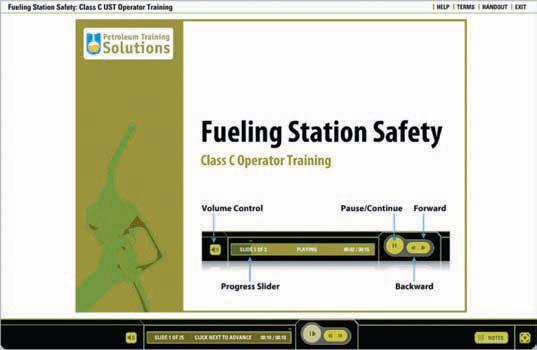
Thieves who fill up and drive-off from petrol stations are the target of a new scheme launched by police and industry partners.
Norfolk Constabulary has joined forces with The British Oil Security Syndicate (BOSS) and independent retailers to introduce Forecourt Watch across the county.
The scheme creates a closer link between police, BOSS and retail staff to increase awareness, prevention and the reporting and recording of incidents.
The Norfolk Forecourt Watch scheme, being rolled out to more than 40 key stations across the county, is the latest addition to the 70 schemes already operating throughout the UK.
Marking the launch of the scheme at Shell Sweet Briar petrol station in Norwich, Chief Superintendent Bob Scully said: “Norfolk Constabulary is committed to working in partnership with others to reduce crime and bring criminals to justice. Fuel theft is not a victimless crime and has an impact on consumers, retailers and the police. “Forecourt watch is the first operation in the county between police, BOSS and independent petrol retailers and will lead to positive changes in the way we manage forecourt crime –driving down fuel theft, increasing the number of detections and making this business environment a safer place for staff and customers alike.”
Between September 2007 and 2008, there were 499 recorded incidents of making off without payments – known as ‘bilkings’ –across Norfolk, with a key period for offences shown as late afternoon and early evening.
Research also shows that bilking offences are often linked to offenders or vehicles involved in other types of crime and to disqualified drivers, those without insurance, tax or MOT, or vehicles with false number plates.
BOSS Forecourt Watch documentation for the recording and notifying of ‘drive-offs’ and ‘no means of payment’ incidents will be provided to staff at all forecourts taking part in the scheme. This enables petrol service stations to work in conjunction with police and BOSS to help bring offenders to justice.
High visibility stickers and posters on the forecourt itself will raise awareness among customers and potential thieves that Forecourt Watch is in operation and making off without payment is a criminal offence.
Service stations registered with the scheme will also benefit from sharing information with police and each other on suspects, vehicles and known offenders – to maximise disruption and detection of offences.
Tom Sterling, BOSS Regional Coordinator, says: “Drive-offs and No Means of Payment incidents cost the UK petrol industry approximately £30 million every year. By building successful partnerships with local police, petrol retailers and other agencies through initiatives such as the BOSS Forecourt Watch schemes, we are able to deter and prevent crime on petrol forecourts. Our aim is to maintain petrol stations as a safe environment for customers and staff.”
The scheme will be rolled out at stations identified by police analysis as vulnerable, either through location or recorded incidents.
For further information about BOSS please visit www.bossuk.org

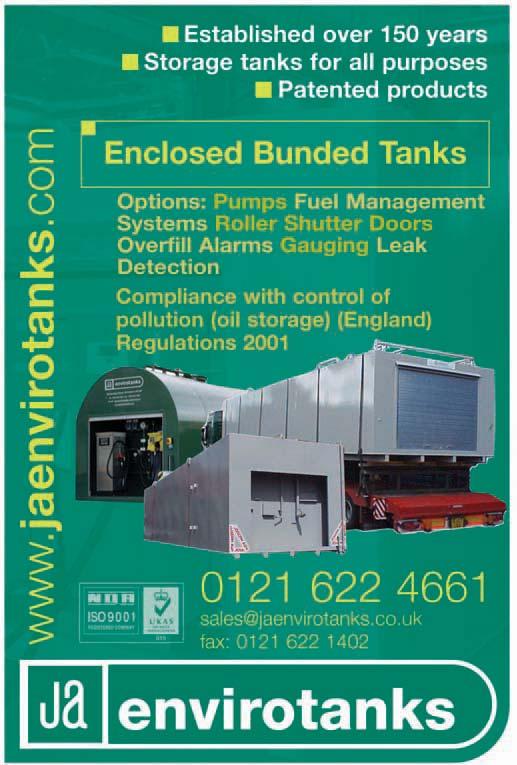
Cameron Forecourt Ltd appoint Martyn Gent as Sales & Marketing Manager
The directors of Cameron Forecourt Ltd are delighted to announce that Martyn Gent has joined their senior management team in the capacity of Sales and Marketing Manager.
Martyn, who will be known to many of you from his 22 years with Meggitt Petroleum Services as Business Development Director and more recently his service with Gilbarco Veeder Root as UK Commercial Manager brings much valuable experience to the company.
Cameron Forecourt offers a turnkey package of high quality design, installation and maintenance services to both the retail and commercial sectors of the industry. Managing Director, Tony Jenner, says “Our Company has always been lead from an engineering and q u a l i t y perspective, with sales and marketing being very much a secondary activity. With Martyn on board we can adopt a progressive sales policy which will give the company the exposure that it deserves”.
Martyn is very enthusiastic about his new role, and explains “Having worked with large organisations I am really looking forward to the more flexible approach to business adopted by the team at Cameron Forecourt. The company, which employs approximately 50 staff, is just the right the size to be able to adapt to the ever changing requirements of its many customers. I’m sure that by introducing and maintaining a focused approach to sales and marketing I will be able to make a real difference to the fortunes of the company”. For further details of the full range of products and services offered by Cameron Forecourt please contact:martyngent@cameronforecourt.co.uk www.cameron-forecourt.co.uk
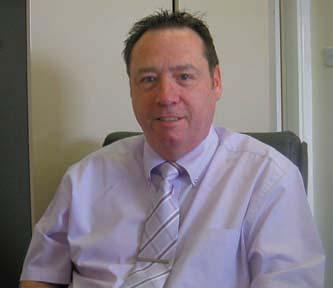
Adler & Allan 2009 contract wins
Adler and Allan, one of the UK’s oil and environmental service groups is delighted to announce three major customer contract renewals. This proves once again that ‘speed, service and environmental integrity’ are key to best customer practice and our on-going success.
IWJS, the water jetting and industrial cleansing division of the Adler and Allan Group were awarded the water jetting contract with Anglian Water continuing a 20 year relationship. National Grid awarded a 5 year contract to Adler and Allan for spill response and hazardous waste across the UK and BP Logistics awarded a 3 year contract for emergency response.
Henry Simpson, Commercial Director said: “This is very good news for us and reinforces our position in the market across a number of different sectors. This is what we are best at, providing a range of solutions and delivering compliant and efficient service.”
Henry added: “We were also delighted to win a term contract with Esso for Tier 2 response to UK terminals and pipelines and an extension to our Environment Agency Southern Region hazardous waste contract. And with a number of other potential contracts in the pipeline, we can expect a good 2009.”
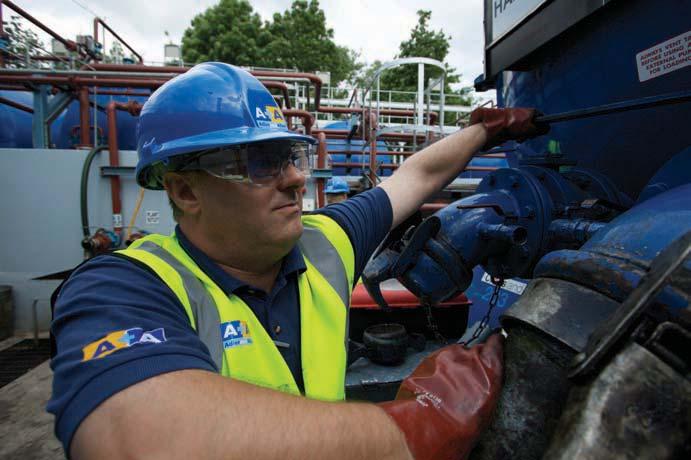
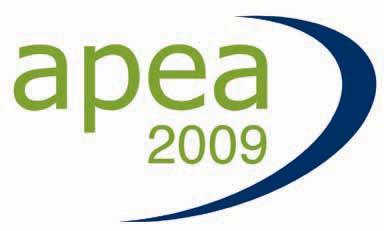
15th October The Ricoh Arena, Coventry, UK
The Ricoh Arena, Coventry, is set to open its doors to the APEA’s annual conference, exhibition and awards dinner on 15th October 2009. More than 300 delegates from oil companies, retailers, supermarkets, consultancies, contractors, regulators and suppliers are all signed up to take part in this year’s prestigious industry event.
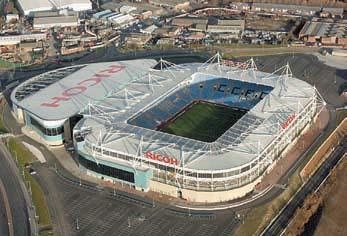
event program..
0900 Registration and exhibition opens 1000 Conference opens
conference
What’s Coming Next? Strategies for the Downstream Fuel Industry
Opening Remarks Gareth Bourhill, APEA Chairman
Developing the infrastructure for UK light vehicle electrification Andrew Haslett, Strategy Director, Energy Technologies Institute
The European BioFuels Directive and its impact on filling stations Hugh Tucker, Technical Director, UKPIA
BP and Biofuels: lessons learned so far Rex May, European Logistics Engineering Authority, BP UK
Oil and groundwater don’t mix! Protecting groundwater from hydrocarbon storage Mark Morton, Policy Advisor, The Environment Agency
Shop-Fabricated Aboveground Storage Tanks: The Florida Experience Marshall Mott-Smith, President, Mott-Smith Consulting Group, LLC
The Above ground fuelling station Roger Wyatt, Terence Barker
1230 Conference closes 1300 Lunch 1330 APEA AGM 1600 Exhibition closes 1830 Exhibition re-opens for Welcome Drinks around the exhibition stands 2000 Awards dinner 0100 Carriages Conference Sponsored by
Exhibiting Companies ... Abfad Adler & Allan ARID CSD Sealing Systems D. Berry & Co (PFS) D P Fuel Tank Services Dresser Wayne Durapipe ELAFLEX Energy Level Systems E&S Environmental Services Eurotank Environmental Fairbanks Franklin Fueling Systems Gilbarco Veeder-Root Graphite (UK) Hytek Inspectahire King Tanktechnic KPS LCM Environmental Ledbury Welding & Engineering Leighton O’Brien LIS (North Western) Nupigeco S.P.A. OAMPS Petrocom Petroman Environmental Services PetroTechnik PFS Pumptronics Risbridger Scheidt & Bachmann SLR Consulting Suresite Tanknology Terence Barker Tokheim Torex Toureen Mangan Urgent technologies
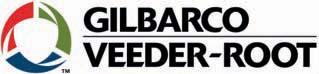
With an ever-increasing demand for environmental solutions, this year’s conference kicks off with a presentation from Andrew Haslett of Energy Technologies Institute. Andrew will be discussing the challenges faced for UK light vehicle electrification, addressing the issue of “how to make battery vehicles and hybrids attractive to UK consumers”
UKPIA’s Hugh Tucker will look at the supply of road fuels and the use of Biofuels over the next 10 years and the challenges this will bring to the downstream oil industry. Whilst Hugh looks into the future, our next speaker Rex May of BP UK, will be assess the lessons learnt so far from Biofuels and whether being Green can ever be easy
Mark Morton at The Environment Agency will draw our focus to protecting current sources from pollution, the risks to groundwater from hydrocarbon storage and how the Environment Agency is working with the industry. Mark predicts that this may be a contentious issue with competing regulation and differing needs from a variety of sectors.
Andrew Haslett Energy Technologies
Marshall Mott-Smith of Mott-smith Consulting Group will give us an insight into the US experience of shop-fabricated tanks for emergency power generation while Roger Wyatt on behalf of Terence Barker will talk about the use of aboveground tank systems suitable for forecourts here in the UK.
Roger Wyatt Terence Barker
new exhibitors for 2009...
The growth and popularity of the APEA exhibition is demonstrated this year by a raft of new exhibitors, proving that even in these economic times, this event is an important date on the industry calendar.
KPS is one of the leading manufacturers of flexible petrol pipes. Based in Sweden, the company has offices and distributors across the globe and founded its UK operation in 1990.They will be exhibiting their full range of conductive single wall and double wall petrol piping, leak detection systems, and the world’s first LPG plastic pipe system. Stand B3
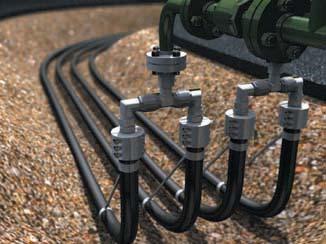
First-time exhibitors from Australia, Leighton O’Brien provide total tank management solutions for the global petroleum industry. They offer a unique consolidated service that allows clients to outsource the management of their storage tank network. Find out about their range of 4 interlocking services on stand B7.
ARID Technologies, based in the US, is recognised for its PREMEATOR unit which reduces gasoline evaporative losses from storage tanks. It’s a “back-end” vapour containment system with an overall vapour recovery efficiency of 99.3% as confirmed by third-party testing. View the system on stand C4.
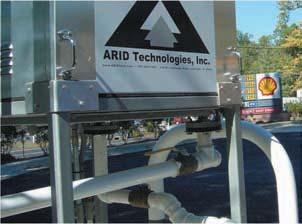
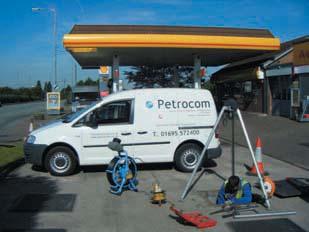
Petrocom (stand C8) will be launching some new services including a pipe line inspection system that can monitor the deterioration of a pipe from the inside, the dewatering of underground storage tanks and remote tank cleaning without the need to remove the tank lid. The environment is a key factor in the way the company operates and they are delighted to be sponsoring the Environment Award. “Retailers and contractors have a huge responsibility to protect the environment and sponsoring this award gives us the opportunity to recognise the tremendous effort made by companies large and small that often goes unnoticed” Louise Morgan, Petrocom.
your chance to enter the awards..
Nominations for the APEA industry awards have kicked off to a good start, with the new online entry procedure making it even easier for your company to be recognised for its achievements. The Customer Care Award is sponsored by Torex: “As a supplier to the petroleum and convenience sector, we see the importance of customer service. Indeed, at the heart of our performance promise is the belief that the better the service our clients receive from us, the better the service their customers will receive from them. This award highlights how customer service impacts on the business, which in turn brings customer loyalty.” Richard Quarmby, Vice President Petroleum & Convenience The entry deadline is 7th September and entries can be submitted online at: www.apea.org.uk.

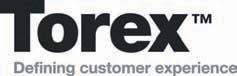

an evening of entertainment..
The welcome drinks, sponsored by Eurotank Environmental, will take place for the first time around the exhibition stands. This format allows the exhibitors access to around 600 dinner guests, providing “healthy networking opportunities” says Edward Wheeler, Managing Director, Eurotank.
PetroTechnik will again be sponsoring the post-dinner entertainment and this year they have personally selected the act, promising a fantastic evening. As a major sponsor, PetroTechnik will also be participating in the exhibition with a showcase of their complete liquid-tight underground fuel system. This includes their tank-top chambers which can be preinstalled, fitted out and tightness tested onto Cookson and Zinn tanks before arriving at site which reduces site downtimes and costs and eliminates the problem of flooded chambers.
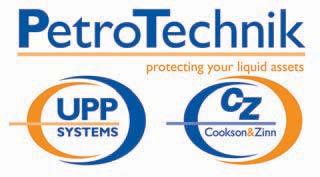
where to stay...
Over 600 rooms of varying budget ranges have been reserved for APEA delegates within a 10minute drive of the conference centre. Booking your accommodation this year couldn’t be easier: go to www.conferencebookings.co.uk/delegate/CVNAPEA2009 or email Jackie on j.fallon@cvone.co.uk or call 02476 607 010 (quoting APEA).
To book your place at the event, visit www.openroomevents.com or email hannah@openroomevents.com
The prestigious APEA Awards, now in their fourth year, continue to recognise and reward those organisations and individuals who demonstrate excellence in their areas of expertise. However in response to your constructive feedback we are introducing some improvements this time around..
“The panel was drawn from different branches of the industry so that we had a variety of opinions from regulators, manufacturers and retailers which led to a healthy debate and a balanced assessment of the submissions”.
“I have very much enjoyed being part of the judging panel for the APEA Awards and am glad that I have been able to make a practical contribution to the work of the organisation in this way”.
“To participate as a judge is a privilege as well as both challenging and rewarding”.
“As far as the judging panel is concerned, every application stands the same chance of success, irrespective of the size of the organisation involved but, crucially, final decisions are made on the depth of the information provided in support of the application. The scoring system, in combination with final round table discussion, provides both the focus and fairness necessary to determine the worthy winner”.
“The process has been very open with every judge having the time to express their opinion, and having it taken into account. I think the idea of giving marks out of, particularly fair and democratic with every judge’s views given precisely equal weight”.
• Application on the web. This year there will be two ways to submit your application; in addition to completing the downloadable form as in previous years you will now be able to register online and complete your applications on the APEA website allowing you to save your work and return later to finish your submission. Our aim is to make the application process as straightforward as possible.
• APEA Award judged by APEA members. The APEA Award does belong to all members, so this year we are introducing a members voting system whereby you will be invited to select your favourite from the shortlist. This will take place in advance of the Awards event with individual members and corporate member nominated persons being eligible to vote by email or fax.
• Self nominate or be nominated. Several members have expressed their reluctance to promote themselves, but would gladly complete the application form if a 3rd party thought they were good enough and contacted the APEA to nominate them. We also feel that there are many worthy entries amongst our members which would otherwise remain unpublicised. So we will be encouraging all members who are customers, service users, other stakeholders or 3rd party observers to identify organisations, individuals, projects and initiatives which merit recognition and to simply nominate them. We will do the rest.
• Increased coverage. All shortlisted entries will be featured in the Bulletin, on the website and throughout the Awards ceremony
• Who are the Judges. We had an excellent response to our invitation to members to become Awards Judges to ensure a healthy turnover on the judging panel. There are 15 judges who each sit on 2 or 3 category panels; our process is highly transparent and judging entirely democratic.
Thank you to all of our judges who give freely of their time and expertise; they are: Louise Morgan (Petrocom) Daniel Nolan (Toreen Mangan) Peter Murfitt (Coteba) Anton Martinuissen (Elaflex) Richard Quarmby (Torex) Bryan Catcheside (Fire Risk Management) Steve Wenham (Environment Agency) John Hazeldean (The HSE) Peter Brough (Manor Service Stations) Rob Tunnicliff (P.O & Environmental Health) Brian Baker (P.O. & Building Control) Phil Monger (PRA & PEIMF) Geoff Lee (Cookson & Zinn) Nobby Clarke (E&S Env Services) Mark J Orr (LCM Environmental).
Erskine - Chosen Charity for APEA 2009 Dinner-15th Oct

Founded in 1916, Erskine is one of the largest ex-Service charities in the United Kingdom, with five care homes, four commercial businesses that provide employment to disabled veterans and 57 cottages. Every year the charity cares for over 1350 veterans young and old covering a range of conflicts from WWII up to and including the current operations in Iraq and Afghanistan. Over the past 93 years more than 75,000 ex-Service personnel have been cared for.
As a charity they rely heavily on the voluntary support of individuals and business organisations to ensure that our ex-Service men and women receive the care they so richly deserve. As shown in the personal stories below, Erskine provides a haven for our heroes of the past and the present.
Stephen Keeling, RN, aged 88
Stephen Keeling’s wartime experiences are a testament to the courage and determination of our ex-Service men and women to fight for freedom at all costs. Now 88, Stephen began his naval career at the tender age of 15, joining up before the war in 1937. He became an Able Seaman on his eighteenth birthday.
When war broke out in 1939 his ship was lying in Alexandra Harbour and Stephen still thinks about it to this day. His first job was to paint the ship in camouflage and load supplies and food onto the ship before they set sail for Scotland and Northern Patrol.
The ship patrolled the area between Scotland and Iceland, stopping food and supplies going into Germany.
Stephen served as an Anti-Aircraft Gunner at this time and he remembers two very important missions amongst the convoy patrols and escorts: bringing King Haakon to safety from Norway to Scotland after the German invasion and escorting Winston Churchill across the Atlantic.
After this the crew went back to Plymouth and received orders to intercept a German convoy.
Stephen said: “Our ship, which was named HMS Charybdis from Greek mythology, was hit by two torpedoes. It sunk and 500 men died as a result. I was one of the lucky ones who survived. I was picked up drifting in the water.”
Stephen was sent on survivors’ leave and in 1941 retrained as a diver in the Navy in Scotland. It was his job to go under water and free wires that had been tangled up in the screws of ships.
After his spell in Scotland, Stephen was sent to the port at Colombo, Ceylon, which came under attack from the Japanese and was heavily bombed. Stephen and his fellow divers were involved in a rescue mission to salvage a sunken Hectors ship blocking the entrance to the harbour.
When the atom bombs were dropped on Japan, Stephen was on HMS Glenairn. He said: “This event signalled the end of the war. We sailed to the port of Kure which was approximately one kilometre from Hiroshima. We were unaware that the fallout of the atom bomb was dangerous and during this time I surveyed the sunken Japanese ships that had been bombed.”
Now living at the Edinburgh Erskine Home, Gilmerton, Stephen enjoys the camaraderie of the ex-Service community. He said: “There is a common bond between us. We don’t speak much of our experiences but we’ll always remember doing our bit and serving our country. It’s a far cry from the life of young people today.”
Flight Lieutenant Joanna Martin PMRAFNS (RAuxAF) (retired) was a member of 612 (County of Aberdeenshire) Squadron, Royal Auxiliary Air Force for 9 years.
Initially she joined the Squadron as a Staff Nurse, Specialising in Intensive Care Nursing, then following her commission, became a Nursing Officer.
In 2003 she was “called up” to active service (Deployed) as part of Operation TELIC 1 (2nd Gulf War) and served in Kuwait and Iraq for 3 months. In her civilian career, Flt Lt Martin was a senior nurse manager in the ICU Department of the Golden Jubilee Hospital in Clydebank. Joanna was a keen and loyal member of the Royal Auxiliary Air Force and was due to be “called up” again for further service in Iraq in Dec 2005.
However, in December 2005 she sustained an accident during military training, the severity of which resulted in her confinement to a wheelchair. A very fit and sports loving person before her accident, Joanna has carried this on since and her current training and fitness regime is much admired and an example to all!
Joanna has been an inspiration to everyone who knows her, by the resolute and determined manner in which she has fought back from her injury with the greatest of courage and fortitude. She remained a member of the Squadron until her discharge on medical grounds in January 2007 and in March 2007 she was formally “Dined out” by the 612 Squadron Officers at their dinner in the Officers Mess at RAF Leuchars, where she was presented with a miniature medal and a Squadron Plaque. 612 Squadron fundraising efforts, spearheaded by Cpl Steve Stewart (Medical Assistant – 612 Sqn) culminated in the presentation of a cheque to Joanna.
Joanna, who spent two years rehabilitating at The Erskine Home, Bishopton, now leads an independent lifestyle within her own specially-adapted home. She also continues to work with Erskine in a voluntary capacity as well as supporting its efforts to care for exService men and women.
Company Number: 2261660
ABBREVIATED ACCOUNTS
For the year ended 31 December 2008
I N D E X (page 1)
Page No:
1 INDEPENDENT AUDITOR’S REPORT TO THE COMPANY
2 ABBREVIATED BALANCE SHEET
3/4 NOTES TO THE ABBREVIATED ACCOUNTS
INDEPENDENT AUDITOR'S REPORT TO THE ASSOCIATION FOR PETROLEUM AND EXPLOSIVES ADMINISTRATION
UNDER SECTION 247B OF THE COMPANIES ACT 1985
We have examined the abbreviated accounts set out on pages 2 to 4, together with the financial statements of The Association for Petroleum and Explosives Administration for the year ended 31 December 2008 prepared under Section 226 of the Companies Act 1985.
This report is made solely to the company, in accordance with Section 247B of the Companies Act 1985. Our work has been undertaken so that we might state to the company those matters we are required to state to it in a special auditor's report and for no other purpose. To the fullest extent permitted by law, we do not accept or assume responsibility to anyone other than the company for our audit work, for this report, or for the opinions we have formed.
RESPECTIVE RESPONSIBILITIES OF THE DIRECTORS AND THE AUDITOR
The directors are responsible for preparing the abbreviated accounts in accordance with Section 246 of the Companies Act 1985. It is our responsibility to form an independent opinion as to whether the company is entitled to deliver abbreviated accounts prepared in accordance with Sections 246(5) and (6) of the Act to the Registrar of Companies and whether the accounts to be delivered are properly prepared in accordance with those provisions and report our opinion to you.
BASIS OF OPINION
We have conducted our work in accordance with Bulletin 2006/3 “The special auditor’s report on abbreviated accounts in the United Kingdom” issued by the Auditing Practices Board. In accordance with that Bulletin we have carried out the procedures we consider necessary to confirm, by reference to the financial statements, that the company is entitled to deliver abbreviated accounts and that the abbreviated accounts to be delivered are properly prepared. The scope of our work for the purpose of this report did not include examining or dealing with events after the date of our report on the financial statements.
OPINION
In our opinion the company is entitled to deliver abbreviated accounts prepared in accordance with Sections 246(5) and (6) of the Companies Act 1985, and the abbreviated accounts have been properly prepared in accordance with that provision.
ENSORS Chartered Accountants & Registered Auditors 46 St Nicholas Street IPSWICH IP1 1TT
As at 31 December 2008
FIXED ASSETS
Tangible Assets Note 2008 2007 £ £
2 2,147 1,349
CURRENT ASSETS
Debtors 50,295 73,974 Cash at bank and in hand 285,242 270,201
335,537 344,175
CREDITORS: amounts falling due within one year 113,112 114,720
NET CURRENT ASSETS
222,425 229,455
NET ASSETS
224,572 230,804
CAPITAL AND RESERVES
Capital reserve 8,840 8,840
Profit and loss account 215,732 189,598
MEMBERS’ FUNDS
224,572 198,438
These abbreviated accounts have been prepared in accordance with the special provisions for small companies under Part VII of the Companies Act 1985.
Approved by the board on 27 May 2009 and signed on its behalf:
M J Silmon Director
For the year ended 31 December 2008
1. ACCOUNTING POLICIES
a) Basis of Accounting
The financial statements are prepared under the historical cost convention and in accordance with the Financial Reporting Standard for Small Entities (effective January 2007).
b) Tangible Fixed Assets
Depreciation is provided at the following annual rates in order to write off the cost of each asset over its estimated useful life:
Computer and Office Equipment – 33 1/3% on cost Fixtures and Fittings – 25% Reducing Balance
c) Foreign Currencies
Assets and liabilities denominated in foreign currencies are translated at the rate of exchange ruling at the balance sheet date. Transactions in foreign currencies are translated at the rate ruling at the date of the transaction. All differences are taken to the profit and loss account.
d) Cash Flow Statement
The company qualifies as a small company under the Companies Act 1985. The directors have elected to take advantage of the exemption under FRS1 not to prepare a cash flow statement.
e) Financial instruments
Financial instruments are classified and accounted for, according to the substance of the contractural arrangement, as either financial assets, financial liabilities or equity instruments. An equity instrument is any contract that evidences a residual interest in the assets of the company after deducting all of its liabilities.
NOTES TO THE ABBREVIAED ACCOUNTS (page 4)
For the year ended 31 December 2008
2. TANGIBLE FIXED ASSETS
Computer & Office Fixtures & Chairmans’ Equip Fittings Jewel Total £ £ £ £
Cost
At 1 January 2008 5,568 5,679 - 11,247 Additions - - 1,346 1,346
At 31 December 2008 5,568 5,679 1,346 12,593
Depreciation
At 1 January 2008 5,269 4,629 - 9,898 Charge for the year 150 263 135 548
At 31 December 2008 5,419 4,892 135 10,446
Net Book Value
At 31 December 2008 149 787 1,211 2,147
At 31 December 2007 299 1,050 - 1,349
3. COMPANY LIMITED BY GUARANTEE
The company is limited by guarantee. In the event of the company being wound up, each member has undertaken to contribute such amount as may be required, but not exceeding £1, to the assets of the company.
History of Petrol Stations Part 11 – Canopies
By Brian Baker
Of all the components that make up a standard petrol filling station, the feature known as the canopy has got to be regarded as the
youngest to appear in the early 1950’s when it was thought that by providing a little weather protection above the centrally mounted “kiosk”, the attendant would at least have some protection against the
elements such as wind, rain and snow. Prior to this most petrol was sold from hardware shops.
Perhaps the big change came about when attended self service was introduced into the UK in 1963 at Plymouth and shortly afterwards at Southwark Bridge road in London. The attended self service method of operation originated from Stockholm in Sweden in 1960 but no confirmation can be established except from a reprint of a “Bulletin” article from late 1963 but it is safe to assume the timings are about right. One of the early designs was the “Gullwing” canopy This was to see the first “raised” s t r u c t u r e appearing on a forecourt. The concept was quickly copied and in this time, the late 1960’s, it was established that not only were customers afforded some protection against bad weather but each of the oil companies could develop its own brand and image making them instantly recognisable to the motorist, especially after decades of attended service.
Throughout the 1970’s and 1980’s these same oil companies established their branding along w i t h enhancing t h e presence of the pole sign, another key feature in branding and the promotion of the high street petrol retailer. One notable feature was the use of three polygon rings developed by Mobil that made that particular brand stand out until 1985 at Romford when a burger van converted from a London ambulance entered the site to re-fuel whilst the pilot light to its cooking range remained alight. An ignition of vapour occurred that rapidly spread to a dispenser and support column and soon after caused ignition to the canopy and polygon rings within
a few minutes which in turn caused burning droplets of ignited plastic to fall onto the forecourt giving an increased risk of fire and explosion to the fuel installation on site.
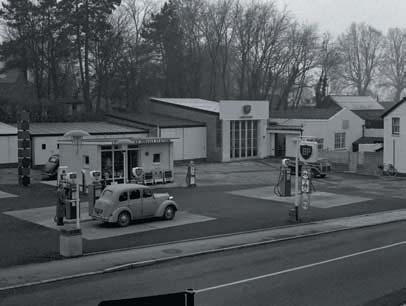
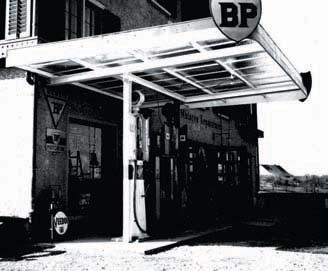
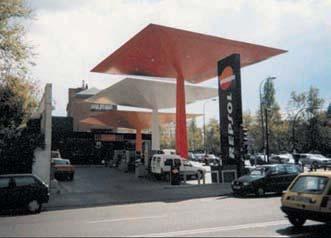

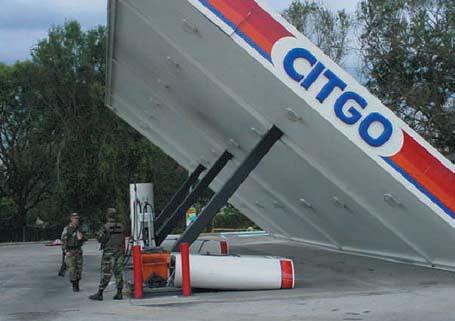

