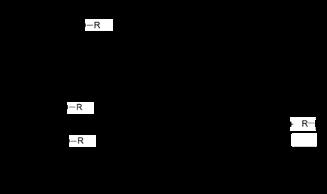
21 minute read
MATÉRIA TÉCNICA
from Ed160
by Aspa Editora
ELASTÔMEROS HYTEMP® HT-ACM: UMA ALTERNATIVA DE ALTO DESEMPENHO PARA AEM
Autor: Mark Nevitt, Zeon Chemicals L.P. , EUA
Advertisement
Este arti go diz respeito ao HyTemp® ACM como uma solução alternati va ao AEM. O elastômero eti leno acrílico, produzido pela Dupont com o nome comercial Vamac, é um óti mo elastômero que, como o ACM, tem sido amplamente uti lizado em aplicações de alta performance em powertrain e transmissão automoti va. O Vamac AEM tem sido usado em componentes automoti vos, mas o fato de vir de uma única fonte e de produção em um único local tem causado muitos desafi os de fornecimento, principalmente durante a pandemia. Como resultado, os fabricantes de peças, fornecedores ti ers e OEMs procuraram o ACM como uma solução em aplicações onde o AEM havia sido especifi cado.
O que é AEM? O que é ACM?
Gostaria de começar fornecendo uma base de como ACM e AEM são semelhantes e como diferem. Ambos ACM e AEM são amplamente conhecidos por terem alta resistência térmica e ao óleo, e são usualmente encontrados em aplicações de powertrain e transmissão automo� va, como juntas da tampa da válvula, vedações do eixo rotacional, mangueira de entrada de ar, dutos e mangueiras de arrefecimento de óleo de transmissão. Embora ambos sejam frequentemente u� lizados em aplicações similares devido às propriedades funcionais que oferecem, são materiais dis� ntos, e é por causa dessas diferenças que o ACM pode não atuar simplesmente como um subs� tuto para atender a uma especifi cação de material elaborada para AEM. As seções seguintes deste ar� go iden� fi carão muitas das principais diferenças ao considerar o uso do ACM como uma alterna� va ao AEM. Vamos examinar as estruturas químicas do ACM e do AEM, como mostrado na fi gura 1. O elastômero de poliacrilato (ACM) é fabricado u� lizando um processo de emulsão-polimerização e consiste na repe� ção de unidades de monômeros de acrilato como o acrilato de e� la, acrilato de bu� la e acrilato de e� la metoxi. Os elastômeros acrílicos de e� leno (AEM), por outro lado, são produzidos usando um processo de polimerização de alta pressão e são classifi cados como copolímeros e terpolímeros, feitos principalmente de acrilato de me� la e monômeros de e� leno. Uma pequena parte, mas crí� ca, do ACM e do AEM são os monômeros do sistema de cura. No caso do HyTemp® HT-ACM (um grade de ACM para alta temperatura) e dos terpolímeros AEM, ambos usam cura� vos do � po diamina e possuem o mesmo mecanismo de re� culação. Um processo de pós-cura resulta na formação de uma estrutura de re� culação estável e resistência térmica tanto para o ACM quanto para o AEM (Figura 2). Embora ACM e AEM contenham monômeros acrilatos em sua estrutura e a mesma química de re� culação, é o componente de eti leno do AEM que contribui para algumas diferenças dis� ntas nas propriedades e desempenho do material em comparação ao ACM. O escopo da discussão e os dados a seguir se concentrarão nas famílias de materiais HyTemp® “HT-ACM” e Vamac ‘Ultra’ AEM de maior desempenho.
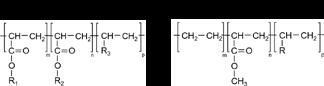
Figura 1: Estrutura química de ACM e AEM.
Poliacrilatos (ACM) Etileno Acrílico (AEM)
Figura 2: Mecanismo de reticulação do HT-ACM e AEM.
HT-ACM ou AEM Agente de Cura Diamina
Amida crosslink Pós-cura
Imida crosslink
Propriedades físicas
Ao comparar os dados do ACM e AEM , uma das diferenças observadas são as propriedades � sicas originais dos materiais. No caso do AEM, o polímero linear, parte polie� leno proporciona uma resistência à tração e alongamento fi nais que geralmente são mais altos do que um composto de ACM de dureza semelhante. Por exemplo, um composto de AEM com dureza de 70 shA desenvolvido para aplicação de mangueiras de turbocharger ou de uma junta de tampa de válvula, geralmente terá uma resistência à tração superior a 14MPa, enquanto a resistência à tração de um composto de ACM de dureza similar está geralmente na faixa de 9~11MPa. As propriedades � sicas � picas de ponto de par� da dos compostos ACM e AEM podem ser vizualizadas na fi gura 3.
Figura 3: Propriedades físicas típicas do ACM e do AEM. Resistência à Tração do HyTemp® ACM e Vamac AEM 70 sh-A Dureza
Resistência à Tração (MPa)
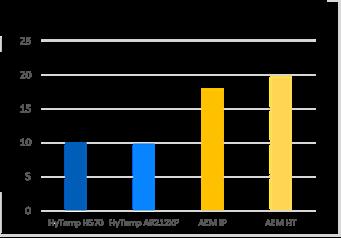

Alongamento (%) Alongamento do HyTemp® ACM e Vamac AEM 70 sh-A Dureza
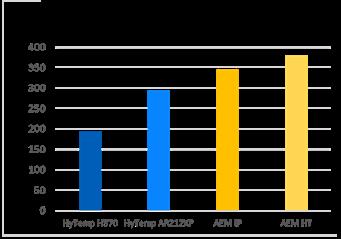
Embora tanto o ACM quanto o AEM sejam usados em muitas aplicações similares ou mesmo idên� cas, o desafi o de usar ACM como um subs� tuto direto do AEM pode vir quando uma especifi cação de material para uma aplicação � ver sido escrita em torno das propriedades materiais apenas para o composto AEM que possui propriedades � sicas originais mais elevadas. Em casos como este, é importante para o engenheiro de projeto e fornecedor de peças analisar a performance funcional e durabilidade na temperatura de aplicação para a qual a peça está trabalhando. Apesar das evidentes diferenças nas propriedades � sicas listadas em uma especifi cação ou datasheet, o desempenho funcional dos dois materiais é muitas vezes muito similar. Razão pela qual ambos normalmente são usados nos mesmos � pos de aplicação. Para explicar, considere novamente a resistência à tração e alongamento dos compostos AEM e ACM quando medidos à temperatura ambiente (como é usado para elaborar uma especifi cação de materiais) comparado com as propriedades medidas à temperatura de trabalho da peça. Quando medido na temperatura de trabalho funcional, como 150o C, o AEM demonstra uma perda enorme das propriedades � sicas devido à parte de e� leno que já não contribui para a resistência do material como fazia em temperaturas mais baixas. Quando trabalha em ambientes de alta temperatura, as propriedades mecânicas dos materiais dependem principalmente da re� culação química que, para todos os fi ns prá� cos, são as mesmas. Figura 4.
Figura 4. Propriedades físicas medidas à temperatura de trabalho funcional. Tensão medida a 22ºC and 150ºC Alongamento medido a 22ºC and 150ºC
Resistência à Tração (MPa) Alongamento (%)
Desempenho em envelhecimento térmico
O alongamento ou retenção do alongamento de um composto elastomérico, após o envelhecimento térmico, pode ser usado como um indicador efi caz de sua resistência térmica. A perda do alongamento geralmente indica uma deterioração da elas� cidade do polímero, prejudicando sua capacidade de atender a função para a qual foi originalmente projetado. Esta é a base primária da norma SAEJ2236, introduzida pela Society of Automoti ve Engineers, que é o método para determinar a temperatura máxima de aplicação de um elastômero ao ar quente por um longo período de tempo. O método de teste é
projetado para iden� fi car a temperatura na qual um composto elastomérico mantém pelo menos 50% de suas propriedades originais de elas� cidade e alongamento após o envelhecimento térmico por seis semanas. No caso do ACM vs. AEM, o desempenho a longo prazo em ambientes de alta temperatura é outra área onde os materiais se diferenciam devido à sua estrutura polimérica. O ACM curado com diamina, com apenas monômeros acrilatos em sua cadeia estrutural, é menos susce� vel à degradação térmica do que o AEM, que contém e� leno. Os dados ilustrados nas fi guras 5 e 6 demonstram a excelente resistência térmica do ACM, pois a retenção de alongamento permanece bem acima de 50% de suas propriedades originais após o envelhecimento térmico a 175oC por 1008h. Em comparação, o AEM, conforme referência do fabricante como adequado para uso con� nuo em aplicações até 165oC (1), apresenta perda signifi ca� va de elas� cidade, com perda maior que 90% do alongamento sob a mesma condição de envelhecimento térmico. Também representado nas fi guras 5 e 6 são referências a uma especifi cação de material OEM dos EUA. A especifi cação lista tanto ACM como AEM como opções para materiais altamente resistentes ao calor para uso em mangueiras de turbocharger com uma temperatura de trabalho permanente de 175oC. É interessante notar que a limitação para alongamento e permissão para perda de alongamento coincide perfeitamente com as propriedades medidas para Ultra HT AEM neste estudo. Embora não mostradas, as propriedades de tração de HT-ACM também são man� das acima do limite de retenção de 50%, conforme descrito pela norma SAEJ2236.
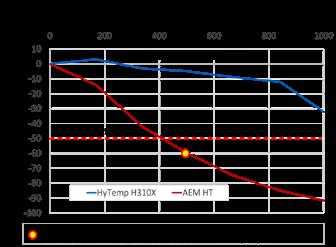
Figura 5: Alongamento após o Envelhecimento Térmico, 175oC/1008h.
Alongamento na Ruptura, Envelhecimento com ar quente a 175ºC
Alongamento na Ruptura (%)
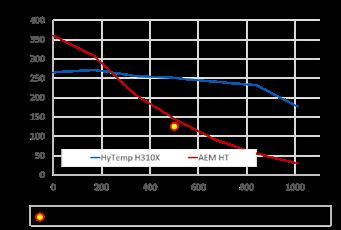
Tempo de Envelhecimento (hrs) Figura 6: Variação de Alongamento após Envelhecimento Térmico, 175oC/1008h.
Variação do Alongamento, Envelhecimento com ar quente a 175ºC
Variação do Alongamento (%) Tempo de Envelhecimento (hrs)
Discu� mos como ACM e AEM são usados em aplicações similares e podem ser encontrados na mesma especifi cação de material. A seguir, mostrarei uma comparação qualita� va dos componentes ACM e AEM produzidos comercialmente e usados na mesma aplicação ao mesmo tempo. A fi gura 7 representa o esquema de uma plataforma de motor 2022MY, US OEM gas turbocharged. O conjunto de admissão CAC (charged air cooler) do lado quente u� liza mangueiras ACM e AEM dis� ntas, ambas produzidas por um fabricante líder da indústria de mangueiras automo� vas. Conforme destacado na ilustração, a mangueira ACM, mostrada em vermelho, é usada na saída do turbocharged, enquanto a AEM, em laranja, é usada no fl uxo inferior do conjunto. Embora tenha sido comprovado que os dois materiais atendem aos requisitos funcionais de longo prazo da aplicação apresentada, corpos de prova para teste foram re� rados de cada mangueira e envelhecidos esta� camente a 175oC por 1008h para determinar sua resistência a altas temperaturas a longo prazo. Após o período de envelhecimento e condicionamento, as amostras envelhecidas foram analisadas qualita� vamente através de fl exão em um equipamento de teste de três pontos de fl exão, monitorando o desenvolvimento de rachaduras à medida que as amostras eram fl exionadas a uma taxa constante. Como observado na fi gura 8, a amostra ACM manteve excelente maleabilidade e pôde ser fl exionada repe� damente a 180o, sem nenhuma rachadura observada. A amostra de mangueira AEM, refl e� ndo a alta perda de alongamento, como explicado anteriormente, quebrou-se rapidamente no início do teste de fl exão.
Figura 7: ACM e AEM em Aplicação de Mangueira de Turbocharger.
Figura 8: Corpo de prova de mangueiras ACM e AEM, Envelhecimento Térmico 175oC/1008h, Teste de exão.
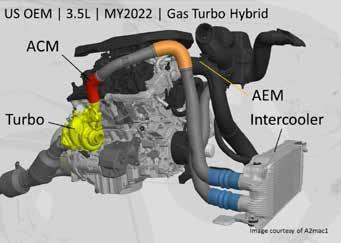
US OEM 3.5L 2022MY gas turbocharger hose Aged 1008hr at 175ºC
Desempenho em baixa temperatura
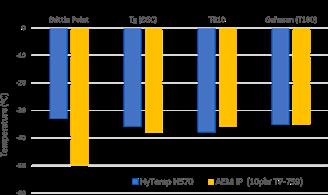
Os materiais elastoméricos para aplicações sob o capô do veículo devem não apenas suportar um ambiente de alto calor a longo prazo, mas também manter suas propriedades elastoméricas a temperaturas tão baixas quanto -40 graus. Ao considerar o desempenho do material para serviço à baixa temperatura, dois pontos principais devem ser levados em consideração: (1) o(s) método(s) de teste no qual as propriedades de baixa temperatura são medidas para uma determinada aplicação, e (2) a estabilidade das propriedades à baixa temperatura quando usada(s) em ambientes por longo prazo e a altas temperaturas. Quando um cliente está interessado em subs� tuir o AEM por ACM, não é raro descobrir que a exigência à baixa temperatura em uma especifi cação de AEM é determinada pelo impacto a baixa temperatura (Bri� leness), independentemente da aplicação. Embora o britt le point seja uma ferramenta ú� l para medir a adequação de materiais que servem em aplicações sujeitas a impactos severos, tais como uma coifa ou uma vedação de ambientes, pode não ser o melhor método a ser usado para componentes sob o capô de veículos, tais como vedações ou mangueiras. No caso do AEM, descobrimos que a parcela de e� leno do polímero contribui para um excelente ponto de fragilidade à baixa temperatura, muito parecido com o de um plás� co de impacto modifi cado, embora as propriedades elastoméricas, ou fl exibilidade à baixas temperaturas, muitas vezes não são refl e� das pelos valores superiores de britt le point do AEM quando comparado ao ACM. Para medir a fl exibilidade de um elastômero à baixas temperaturas, métodos como a temperatura de retração (TR10), Gehman, dobramento em mandril à baixa temperatura e até mesmo a temperatura de transição vítrea (Tg ) serviriam como melhores ferramentas em comparação ao ponto de fragilidade. Na fi gura 9 é demonstrada a comparação entre um composto de ACM e um de AEM usando vários métodos de medição padrão da indústria para determinar as propriedades à baixa temperatura de um material elastomérico. Embora possa ser um desafi o para o ACM atender aos limites de especifi cação estabelecidos para um composto AEM em relação ao britt le point, que muitas vezes está a -40 graus ou abaixo, outros métodos para determinar as propriedades elastoméricas à baixa temperatura demonstram que o ACM e o AEM são bastante similares.
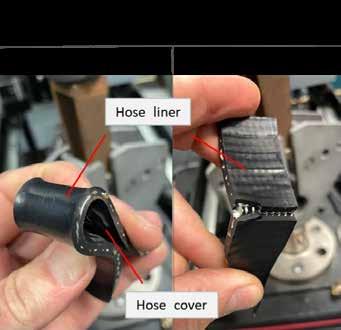
Figura 9: Comparação das propriedades à baixa temperatura do ACM e AEM.
Cold Temperature Properties of ACM and AEM
Seguindo adiante, ao considerar peças elastoméricas trabalhando em ambientes de alta temperatura, é igualmente importante entender como um elastômero manterá seu desempenho à baixa temperatura após a exposição ao calor. O ACM, que deriva principalmente tanto sua resistência térmica quanto seu desempenho à baixa temperatura de sua cadeia polimérica ao invés de carregar com plas� fi cante, demonstra uma melhor retenção de sua capacidade de serviço à baixa temperatura após o envelhecimento térmico, quando comparado ao AEM (Figura 10).
Figura 10: Propriedades à baixa temperatura do ACM e AEM após o envelhecimento térmico.
Cold Temperature Properties aft er Heat Aging, 160ºC / 1008hr
Resistência à vedação de fl uidos e fl uidos

Devido à polaridade conferida pelo componente éster dos monômeros acrílicos, tanto o ACM quanto o AEM possuem uma resistência natural a fl uidos não polares à base de hidrocarbonetos, como óleos de motor e fl uidos de transmissão. O ACM, que consiste principalmente do teor de acrilato em sua cadeia principal, exibe excelente resistência a muitos dos lubrifi cantes u� lizados nos atuais powertrains e drivetrains automo� vos. Conforme indicado pelos valores de variação de volume dos materiais mostrados na fi gura 11, o ACM geralmente exibe resistência similar ou melhor a muitos fl uidos automo� vos de referência e de primeiro enchimento, quando comparado ao AEM.
Figura: 11: Variação de volume de ACM e AEM em óleo de motor e ATF. Volume Change of ACM and AEM in Engine Oil and ATF, 150ºC / 168hr

Tanto o ACM quanto o AEM são usados há décadas em aplicações de vedação de fl uidos automo� vos, tais como juntas de tampa de válvulas e juntas de bandeja de óleo, bem como vedações de eixos rota� vos de motores e transmissões. Dois dos principais métodos de teste para medir o desempenho da vedação a longo prazo de um material são a deformação permanente à compressão e o compression stress relaxati on (CSR). Enquanto ACM e AEM frequentemente demonstram desempenho semelhante usando teste de deformação permanente à compressão em fl uidos (Figura 12), o AEM normalmente tem maior retenção de força ao medir pelo método de teste CSR. Apesar desta diferença entre os dois materiais, o AC provou atender aos requisitos de vedação a longo prazo estabelecidos em muitas especifi cações OEM para CSR, que frequentemente requerem uma retenção de força de vedação de 10-30% após o envelhecimento no fl uido por 1008h à temperatura prescrita (Figura 13). Muitos requisitos de testes OEM automo� vos para deformação permanente à compressão e CSR representam a pior condição de envelhecimento acelerado, como por exemplo 150oC por 1008h. Entretanto, a capacidade de vedação do HyTemp® ACM também tem sido avaliada por um período de tempo muito maior. A pedido do cliente, a temperatura real máxima de trabalho do óleo do motor na plataforma do motor diesel do OEM foi usada como condição de teste e o tempo de teste estendido para a “vida ú� l” completa da peça, durante o período programado para reparo da manutenção do motor. Como demonstrado na fi gura 14, o ACM mantém um bom desempenho de vedação durante todo o teste de 8.000 horas a 125oC.
Figura 12: Deformação Permanente à Compressão do ACM e do AEM em óleo de motor e ATF.
Compression Set of ACM and AEM in Oil and ATF, aged 168hr / 150ºC, ISO-815
Figura 13: CSR do ACM e AEM em SF105 Óleo de referência. CSR (Dyneon), aged 150ºC, SF105 Reference Oil
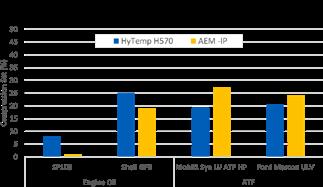
Figura 14: Compression Stress Relaxation (CSR) para aplicação de vedação em motores diesel industriais. CSR (Dyneon) HyTemp® H570 aged in Diesel Engine Oil, 10W30, 125ºC
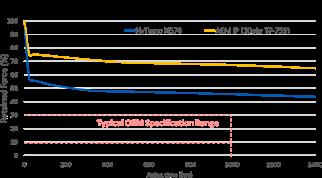
O equilíbrio de boas propriedades de vedação a longo prazo, retenção de propriedades � sicas e desempenho à baixa temperatura após o envelhecimento fazem do ACM um excelente material tanto para aplicações de vedação está� ca como dinâmica. Isto tem sido demonstrado por sua longa história e uso expansivo em uma ampla gama de aplicações de vedação. As fi guras 15 e 16 ilustram exemplos onde o ACM é u� lizado não apenas para a vedação de baixa viscosidade, óleos sinté� cos em motores de combustão, mas também em aplicações de vedação de transmissão que requerem resistência aos mais novos fl uidos de transmissão agressivos contendo adi� vos e óleos de engrenagem u� lizados tanto em ICE (Internal Combus� on Engine/ Motor de Combustão Interna) quanto em EV (Veículos Elétricos).

Figura 15: Vedação da tampa da válvula em ACM.

Figura 16: Aplicação de Vedação ACM em Drivetrain automotivo.
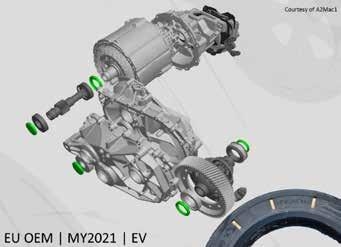
Formulação e Processamento
Ao longo deste ar� go, demonstrei como ambos ACM e AEM são usados em aplicações similares ou idên� cas, apesar de algumas diferenças na composição química e nas propriedades � sicas. A composição e o processamento destes materiais também se encaixarão ocasionalmente dentro deste mantra. Vamos começar com a composição do material. Devido à natureza similar e química de cura do ACM e AEM, os ingredientes
usados na formulação do composto destes dois elastômeros são muito similares na maioria dos casos. No entanto, os níveis � picos de carga de adi� vos e cura� vos para ACM e AEM podem ser bastante diferentes. Como descrito anteriormente, as propriedades � sicas do ACM são proporcionadas pelo próprio polímero e normalmente não se benefi ciam de altos níveis de cargas ou plas� fi cante. Uma comparação para receitas como ponto de par� da com compostos ACM e AEM de 70 shore A é apresentada na Tabela 1.
Tabela 1: Formulação Típica de 70 shore A de dureza para ACM e AEM.

Para o processamento do material, deve-se notar primeiramente que tanto o AEM quanto o ACM são processados em equipamentos convencionais de produção e composição de borracha. De fato, muitos fornecedores do setor frequentemente misturam, moldam ou extrudam esses materiais nas mesmas linhas de produção. Embora as mudanças nos equipamentos de produção muitas vezes não sejam necessárias, os engenheiros de processo geralmente descobrem que algum ajuste ou ajuste fi no dos parâmetros do processo é de se esperar quando se muda de um composto de AEM para um de ACM. Na maioria dos casos, um composto de AEM geralmente terá uma viscosidade Mooney mais baixa do que um composto de ACM com dureza similar, resultando em diferentes perfi s de preenchimento do molde ou pressões geradas no molde de injeção ou no equipamento de extrusão. Apesar da leve diferença na viscosidade, os compostos ACM têm sido bem sucedidos em uma grande parte dos try-outs de molde e extrusão para subs� tuição do AEM usando ferramentas de molde existentes e matrizes de extrusão originalmente projetadas para o AEM. Entretanto, quando projetando novas ferramentas de molde especifi camente para ACM, as formas ou matrizes de molde são � picamente dimensionados de 1,5 a 2 vezes o tamanho das matrizes usados para um composto AEM comparável. Para obter informações técnicas detalhadas sobre recomendações de compostos, processo de mistura e processamento do ACM, a ZEON recebe com sa� sfação a oportunidade de trabalhar com os clientes no desenvolvimento de formulações o� mizadas de compostos e processos de produção efi cientes.
Fornecimento global de ACM
No início deste ar� go, mencionamos que os processos de polimerização para ACM e AEM são diferentes. Embora este ar� go não explore os detalhes da fabricação de cada material, vale ressaltar que a ZEON produz ACM em quatro plantas globalmente (Figura 16), oferecendo um fornecimento de material robusto a seus clientes. Em 2021, a ZEON iniciou a produção em série do ACM em sua nova unidade da Zeon Asia na Tailândia, demonstrando ainda mais o inves� mento con� nuo e o compromisso de fornecer ACM a seus clientes em uma base global. Ao concluir este ar� go, podemos nos perguntar por que escolhi escrever sobre um tema que discute principalmente a alta resistência térmica e ao óleo para motores de combustão interna quando tanta atenção e inves� mento tem sido feito no futuro dos veículos elétricos. Embora a ZEON esteja, de fato, dedicando recursos e desenvolvimento especifi camente para EV (talvez um tópico para outro ar� go que está por vir), os desafi os que enfrentamos com relação ao fornecimento de material estão acontecendo no momento. Além disso, embora seja verdade que muitos dos recursos de desenvolvimento das OEM’s estejam mudando para o EV, não podemos ignorar o fato de que o uso de tecnologias de motores híbridos turbocharged e efi cientes em termos de combus� vel con� nuará a compar� lhar uma parcela signifi ca� va do mercado automo� vo. Seja uma exigência de alta resistência térmica para veículos híbridos elétricos, ou a vedação de lubrifi cantes de alto desempenho em transmissões elétricas a bateria, a necessidade de fornecimento confi ável de elastômeros de alto desempenho como o ACM con� nuará bem no futuro.
Referências
1. DuPont. “DUPONT™ VAMAC® ETILENO ACRÍLICO ELASTÔMERO PROSPERA EM
UM MUNDO ÁSPERO”. 2018. www.dupont.com/content/dam/dupont/amer/ us/en/transportation- industrial/public/documents/en/Vamac-at-a-Glance-
Brochure.pdf
DupontTM e Vamac® são uma marca registrada da E.I. du Pont de Nemours & Co.
Faça parte das nossas publicações e fique sempre bem informado! Faça sua assinatura!
11 97353-8887
Figura 17: Locais de fabricação global do ACM da ZEON.
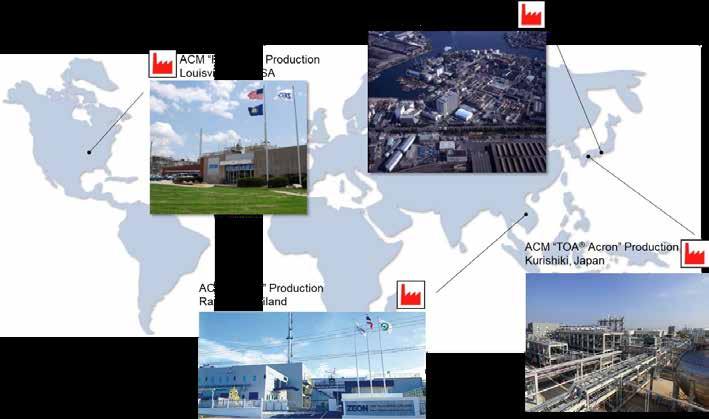
Inversor de carboneto de silício impulsiona carros de alto desempenho
A BorgWarner fez parceria com duas marcas de carros de alto desempenho para fornecer um novo inversor de carboneto de silício (silicon carbide - SiC) de 800 volts. Como um dos principais componentes em um novo sistema de energia, os inversores não apenas convertem a energia CC (corrente con� nua) armazenada na bateria em energia CA (corrente alternada), mas também convertem a energia CA recuperada durante o processo de frenagem de volta para a bateria. Atualmente, a maioria dos veículos elétricos está equipada com um sistema de 400 volts. Como se espera que os veículos totalmente elétricos forneçam autonomia estendida e atendam a requisitos mais altos para desempenho de carregamento, é necessário um material semicondutor mais efi ciente para aumentar a densidade de potência dos inversores e conjuntos de acionamento elétrico. Com isso em mente, a BorgWarner assumiu a liderança na construção de tecnologia avançada para permi� r a aplicação de carboneto de silício em veículos elétricos, desenvolvendo um inversor SiC de refrigeração dupla face com alta potência que pode ser aplicado a sistemas de 800 volts. “Estamos honrados em ganhar a confi ança das duas marcas de carros de alto desempenho como seu principal fornecedor de sistemas de propulsão eletrônica”, afi rma Stefan Demmerle, presidente e gerente geral da BorgWarner PowerDrive Systems. “Como líder neste mercado altamente compe� � vo, a BorgWarner con� nua a desenvolver tecnologias inovadoras que mudam o jogo para veículos elétricos; nossa solução de inversor de carboneto de silício de 800V é um ó� mo exemplo.” Este novo inversor SiC foi projetado usando o módulo de alimentação SiC 800V “Viper” patenteado da BorgWarner, o que resultou na economia de uso de semicondutores e materiais SiC. A tecnologia de refrigeração de lado duplo no módulo de energia ajudou a reduzir o peso do produto em 40%, o tamanho em 30% e aumentar a densidade de energia em 25% em comparação com os inversores tradicionais baseados em Silício (Si). Graças ao design do Viper, a solução é escalável para atender às demandas em constante mudança e se adapta a sistemas de tensão mais baixa e mais alta, facilitando o gerenciamento das várias classifi cações de tensão exigidas por PHEVs e EVs. Os dois SUV’s elétricos equipados com o mais recente inversor de carboneto de silício de 800 volts da BorgWarner estão programados para iniciar a produção em 2023 e 2024.