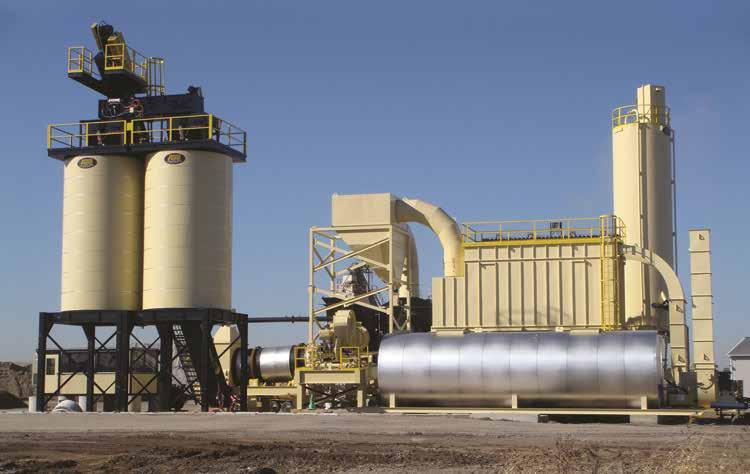
9 minute read
Get the Most Out of
Companies may require up to three employees for a larger sized, higher volume operation that might use the ADM MileMaker Series plants, which run in the 120-425 TPH range. Photos courtesy of ADM
Get the Most Out of Plant Labor During, After COVID-19
WWe all see the pandemic has presented new economic and labor challenges for hot-mix asphalt (HMA) producers. Savvy owners and operators will explore new avenues to overcome the challenges, based on the size of their asphalt operations and revenue potential.
With hiring and layoff legal issues to navigate (see the article titled “Tips to Navigate Re-hiring Workforce After COVID-19” from the September issue) into the 2021 asphalt season, asphalt producers continue their attempts at producing readily available and high-quality mix during challenging times. It is more important than ever that asphalt producers operate for a high return on investment (ROI), which requires they understand the significant role labor plays in ROI.
Employee training is another area that has been impacted during the pandemic. Although many smaller asphalt-production facility employees train in the field, newer, younger workers who may have had the advantage (pre-COVID) of training with more highly skilled workers who did not return to work this year, did not have that advantage, leaving knowledge and skill gaps.
Balancing labor considerations with other operational factors, especially with a potentially shrinking labor pool, can be like walking a tight rope. Labor can be expensive, and many asphalt operations have traditionally kept labor costs low with lower compensation scales, even before the pandemic. Although this approach may be seemingly good for the bottom line, there are pitfalls that also negatively impact ROI and endanger revenue streams in ways that are bad for operations in general.
Regardless of the asphalt-production facility size, choosing to pay workers at lower compensation scales makes it harder to attract more knowledgeable and skilled workers who are more likely to stay with an operation. This opens asphalt facilities up to high turnover, which is itself costly to the bottom line in recruiting and training costs that become a revolving door, and a continual drain on business capital.
Better managed asphalt production companies keep asphalt quality and ready-availability high—both important components to building and retaining lasting customer relationships. It’s more expensive to bring in new hot-mix customers than to keep existing customers coming back.
Ready-availability of quality asphalt saves paving customers time and labor costs for their own businesses, through shorter lines and less down time both picking up asphalt and for workers waiting for hot-mix at the job site. This improves customers’ ROI and keeps them coming back to the production facilities that are helping them achieve a better bottom line. Asphalt producers using less knowledgeable and skilled workers are less likely to provide the quality and ready availability for high paving-customer retention.
Beyond the pay scale for an individual production-facility employee, the number of facility employees necessary to operate an HMA plant is also an important factor in determining and efficiently managing labor costs. Several factors play into how many employees a production facility needs. • The total volume of product being output • Amount of material/type of material being fed into the bins • Size of the loader relevant to bin sizes • How well material needs are managed • Whether hot mix is continuous or batch mix • Number of—or need for—storage silos
When it comes to labor costs, choosing the right size plant to meet production needs benefits smaller and larger operations, alike, as the size of the asphalt plant impacts the number of employees necessary to operate it.
For hot-mix production facilities producing continuous mix asphalt at smaller volumes, the number of employees your operation needs to run the plant is one to two. Smaller-size continuous-operation plants such as the ADM Asphalt Drum Mixers SPL Series (60–160 TPH) and the ADM RoadBuilder Series (110–350 TPH) require one plant operator and one loader operator.
However, there are asphalt operations that may use a plant operator only, if the facility produces just one or two mixes, produces between 50 and 70 tons of asphalt, has storage capabilities, uses the appropriate size feeder for the size of the existing aggregate bins, and employs a plant operator who is experienced in ordering and managing materials.
For operations that produce more than 70 tons, where both a plant operator and loader operator are necessary, the responsibilities for each break down as follows. The plant operator is responsible for the smooth operation of the plant and continuous flow of HMA. To achieve this, the plant supervisor’s responsibilities include pre- and post-startup, maintenance, and supervision of the loader operator.
As part of the plant operator’s supervisory responsibility, pre- and post-startup and maintenance may be shared functions between the
NOW RENTING PUGMILL PLANTS
931-388-0626 • PUGMILLSYSTEMS.COM • Columbia,TN
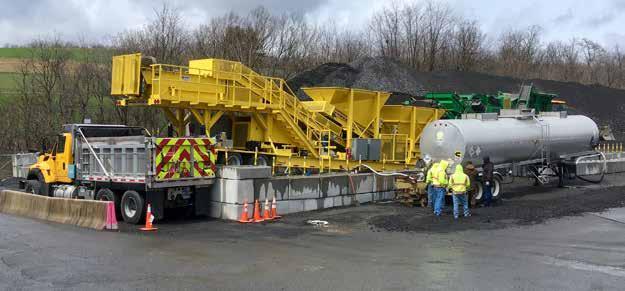
For a larger sized, higher volume operation that might use an EX Series plant, which operates in the 120-425 TPH range, the company might employ the plant operator, loader operator and grounds operator.
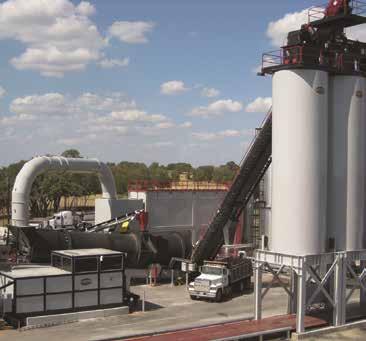
plant and loader operators. Regardless of who performs these duties, pre-startup includes turning on the plant; checking oil levels, belts, and fluids (including for any leaks); turning on the air compressor (if applicable); and performing the regularly scheduled maintenance checklist. Post-startup includes checking, fixing, or replacing any broken parts and cleaning up the plant.
Once the plant is running, the plant operator’s primary responsibilities are to keep the plant operating, continuously monitoring any automation functions, making repairs or overseeing any breakdown repairs, and to load out trucks picking up asphalt.
The loader operator’s main responsibility is to determine the type of aggregate that goes into which bins, load the aggregate into the bins, and ensure the bins are kept full. When the loader operator is not driving around the site performing these functions, he is responsible to walk the site to observe whether any plant issues have occurred that may require maintenance or repair, and to communicate any issues by two-way radio to the plant operator.
The number of employees needed for a larger sized, higher volume operation, using plants such as the ADM MileMaker Series (160–425 TPH) or the EX Series (120–425 TPH), may require up to three employees, consisting of the plant operator, loader operator, and grounds operator.
The grounds operator is responsible to walk the site to observe plant issues that may have occurred and require maintenance or repair, to communicate these issues by two-way radio to the plant operator, and assist with maintenance and repair as the grounds operator’s capabilities allow and the plant operator sees fit. The grounds-operator position is necessary for high-production facilities where the loader operator is kept busy, full time, driving and loading bins, and is unable to park and inspect the grounds, to help prevent any failure for asphalt to flow.
If the production facility is running batch mix, another operator, in addition to the plant operator, may be necessary to coordinate and handle loadout. This position is responsible to communicate with each individual driver for their particular mix need, whether it’s a 50/50 sand-to-gravel mix, a 48/50 sand-to-gravel mix, or numerous other potential mix combinations. Then, the loadout operator communicates the need to the plant operator to change the mix design specifications or continue to run the current mix. Clear communication from loadout operator to truck driver, and from loadout operator to plant operator is paramount for getting trucks loaded properly and timely when there are constantly changing mix needs.
Lastly, much larger production facilities may also require an asphalt lab technician, whether the position is outsourced (off-site) or an on-site employee. The lab technician understands the properties, advantages and disadvantages of asphalt mixes such as Marshall and Superpave mixes and the way they are best applied. He is responsible to check the quality of raw materials for damage, moisture, loss, or other problems before the material is used to produce hot-mix. A highly knowledgeable and experienced plant operator may be able to fill this need, for greater ROI.
Beyond labor costs, labor efficiency may also contribute to greater production-facility ROI. Scrimping on the number of employees or attendant salaries commensurate with skills, may interfere with total production output and potential revenue. Greater revenues can lead to greater ROI, even with labor costs higher than an operation might prefer.
Additionally, the better managed an asphalt-production facility is as a business, the greater the likelihood for greater labor efficiency. Production facilities that do the following are likely to realize better than average ROI. • Use good-quality materials and good equipment upon which plant and loader operators can rely. • Keep up with material management, ensuring materials are ordered and delivered on a timely basis to prevent plant shut down due to material outages. • Find the proper balance with material inventory, not just preventing material outages, but preventing having too much aggregate on site that can get in the way of operations and require additional and unnecessary movement of material. • Know the knowledge levels and limits of personnel to staff accordingly, reduce the possibility of breakdowns, and provide customers with high quality mix that keeps them coming back.
Regardless of an asphalt-production facility’s size, by understanding the new labor and economic issues that are impacting hot-mix production during these uncertain times, asphalt producers can work toward greater ROI to help offset any current revenue losses.
They can also build for future revenue potential by understanding how the COVID economy is affecting supply and demand of workers and asphalt, alike, specifically in their local municipalities, and scale their businesses up or down accordingly. Producers should also understand that by following many of the same labor principles (outlined in this article) that may contribute to ROI now, will also benefit their businesses in the future, for a brighter future to come.
–BY CARLOS CARDENAS
AND WE DO THIS... CONTROLS ULTRA-PORTABLE ASPHALT PLANTS INSPECTION SERVICES CONFIGURATION CONFIGURATION
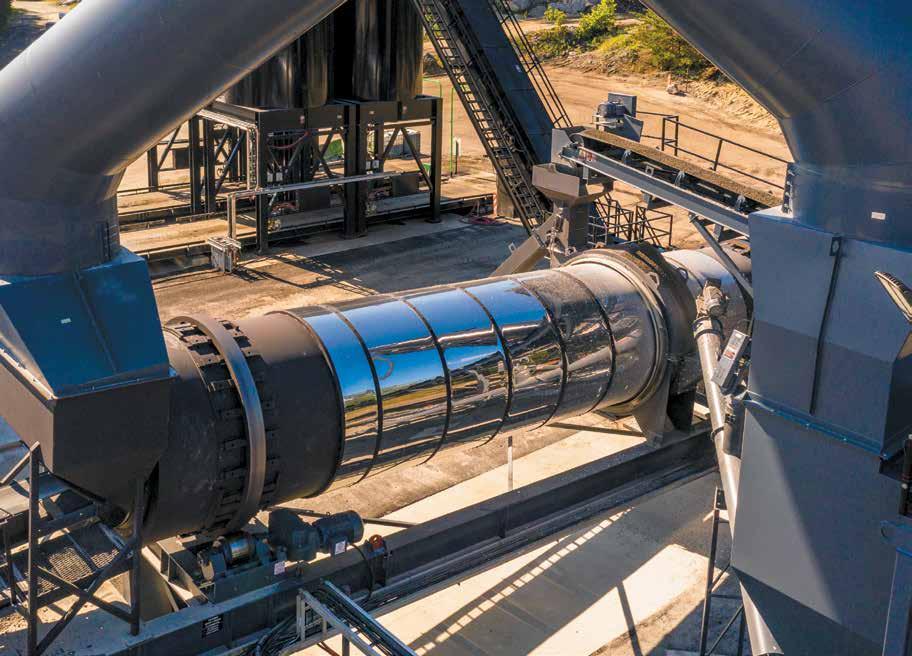
DRUM REPLACEMENT
A dependable mixing drum is fundamental to maintain the productivity of an asphalt plant. Replacing an older drum offers opportunities to both maintain operation and improve performance. Astec works with you to integrate a new drum into your existing operation and supports each drum replacement with service and parts.
PARTS: 800.251.6042
MOBILITY
CAPACITY
HEATERS
No other North American manufacturer
offers more options than Astec. CONTROLS ULTRA-PORTABLE ASPHALT PLANTS INSPECTION SERVICES MOBILITY
HEATERS
ENGINEERING
4 DRUM OPTIONS
Double Barrel // DBX // DBXHR // UniDrum CONTROLS INSPECTION SERVICES ULTRA-PORTABLE ASPHALT PLANTS
ENGINEERING
Astec offers complete engineering services
CONTROLS INSPECTION SERVICES ULTRA-PORTABLE ASPHALT PLANTS
LOGISTICS
Astec can coordinate, plan and schedule shipment to your site
CONTROLS INSPECTION SERVICES CONSTRUCTION ULTRA-PORTABLE ASPHALT PLANTS Skilled setup crews available to install replacement drums