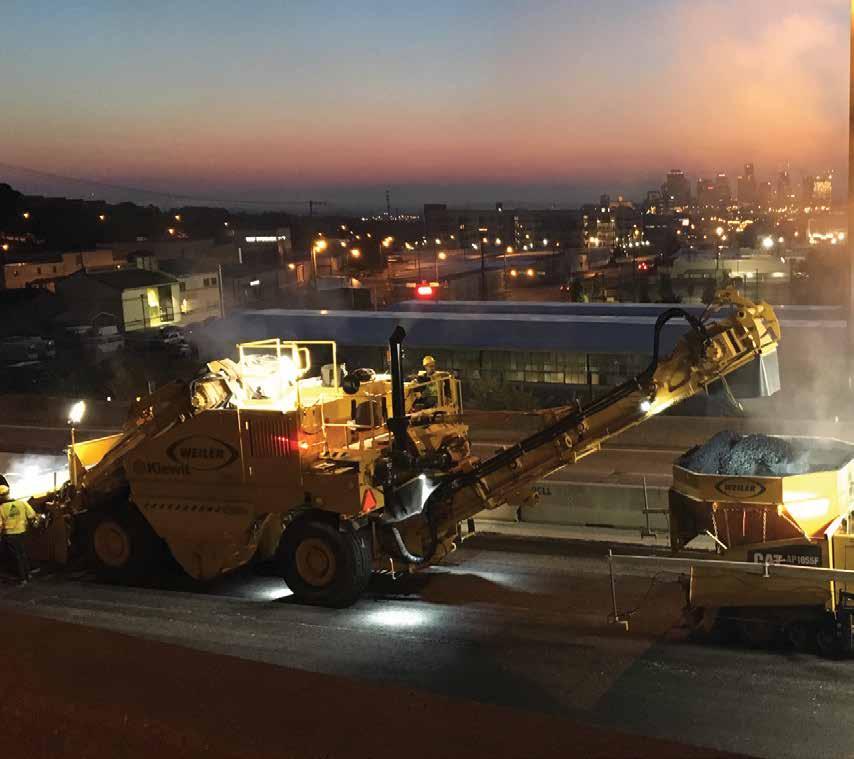
7 minute read
Kiewit Keeps to Tight Schedules
BY SARAH REDOHL
In June 2020, Kiewit Infrastructure South Co. finished the reconstruction of I-440 in Nashville, the largest project in the history of the Tennessee Department of Transportation.
IIn June 2020, Kiewit Infrastructure South Co. completed the largest “The life-cycle of the existing concrete pavement had expired, and the project in the history of the Tennessee Department of Transporta- roadway had become dilapidated and laden with potholes,” Gregg said. tion—a month ahead of schedule. The $154.8 million reconstruction The existing I-440 corridor was constructed in the mid-1980s and project took place on I-440, a 7-mile connector loop that runs south of consisted of two lanes of 10-inch jointed concrete pavement in each downtown Nashville. direction, separated by a raised grass median to provide a parkway feel.
“Nashville is one of the fastest growing cities in the country, with As the prime contractor, Kiewit widened the existing corridor into an average of 100 people moving to the city every day,” Kiewit Project the grass median, adding a third lane in each direction, with final sepaManager Jordan Gregg said. “The I-440 corridor is a major artery used ration provided by a concrete median wall. The existing pavement was for commuter traffic in the city and sees a daily traffic volume in excess rubblized and overlaid with asphalt. of 100,000 vehicles per day.” The project also included widening three bridges by one lane in
In addition to expanding the roadway to accommodate Nashville’s each direction and bridge deck repairs and overlays; installation growing population, the road had reached the end of its service life. of upgraded and additional storm drainage; placement of new
guardrails, signage, lighting and striping; repair of existing sound walls and installation of new sound walls; and upgrading the roadway’s existing intelligent transportation system.
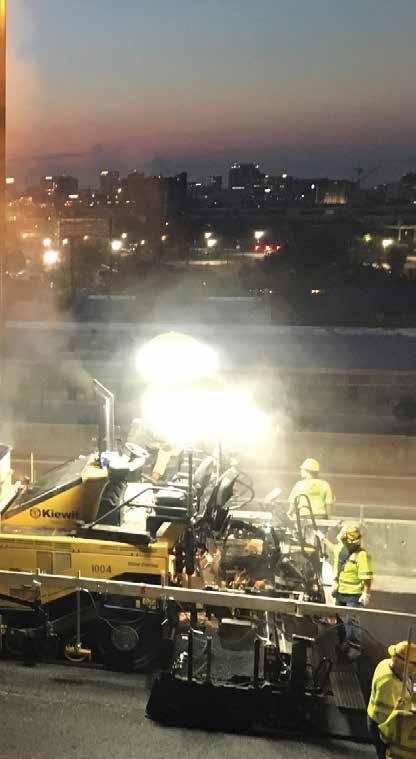
The western terminus of the project was the junction of I-40/I-440 and the eastern terminus of the project was the junction of I-24/I-440. The project was approximately 7 miles westbound and 5 miles eastbound.
The procurement utilized by TDOT was the A+B method, which requires contractors to submit a dollar bid for labor and materials (the “A” part) and estimate a total number of days to complete the project (the “B” part). In A+B bidding, bids are scored based on both The I-440 corridor is a major artery used for commuter traffic in the city and sees a daily traffic volume in excess of 100,000 vehicles per day.
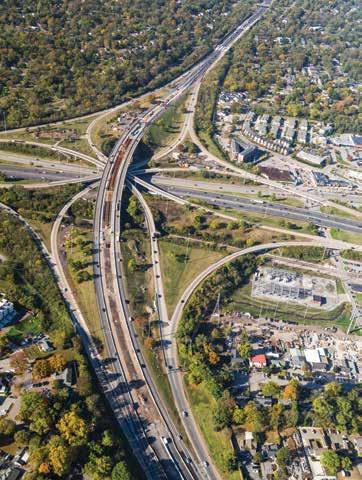
the A and B bid. For the I-440 project, Kiewit came in with the lowest score and was awarded the design-build project in the summer of 2018.
Kiewit bid 708 calendar days to complete the project, setting their deadline for July 24, 2020. Each day was valued at $100,000. The liquidated damages for the project were $100,000 per day for every day beyond the deadline outlined in the bid for the first 30 days past July 24; increasing to $400,000 per day after that.
Although Kiewit was concerned how the COVID-19 pandemic might impact this project, Gregg said they were able to continue working as an essential business while strictly following all guidelines and completing the project without significant issues.
“This project was the largest project TDOT had ever done in terms of project value and was also a fish-bowl job in terms of the traveling public,” Gregg said. “Expectations were extremely high.”
Pair these factors with the high value TDOT placed on schedule and liquidated damages, and scheduling became an extremely important factor on the project. To accomplish the scheduling constraints, Kiewit broke down the 7-mile corridor into smaller sections of work to clearly identify its critical path. They supplemented the overall schedule with 90-day schedules, three-week schedules and daily schedules so they could continually track their progress toward the critical path schedule.
As the prime contractor, Kiewit widened the existing corridor into the grass median, adding a third lane in each direction, with final separation provided by a concrete median wall. The existing pavement was rubblized and overlaid with asphalt.

“When an owner places a liquidated damage of $100,000 per day to a project, it keeps us, as a contractor, focused on schedule throughout the entire project and forces us to make recovery or acceleration decisions early on in the project if we see any schedule slip, versus waiting until later in the project to react, which is often too late,” Gregg added.
Additionally, the project required that two lanes of traffic be kept open in each direction throughout construction. This could be reduced to one lane per direction between 9 p.m. and 5 a.m. Kiewit carefully phased the project so I-440 could continue to accommodate 100,000 vehicles per day.
The phasing consisted of two major phases, and a smaller final phase. During the first phase, traffic was shifted onto the outer lanes and outside shoulders so the Kiewit crew could build additional lanes in the former grass median, construct the new concrete median, and reconstruct the existing inside lanes. During the second phase, traffic was moved onto the new lanes so the outer lanes, shoulders and ramp tie-ins could be reconstructed. The final phase consisted of paving the top mat of asphalt over the entire corridor.
“To utilize and recycle as much of the existing material as possible, a rubblize and overlay approach was utilized where adjustments to the existing vertical profile were possible,” Gregg said. Kiewit’s rubblizing subcontractor, Antigo Construction Inc., Antigo, Wisconsin, used a multi-head breaker to rubblize the existing concrete pavement to a depth of 10 inches, averaging one lane mile per shift.
There were a number of segments of the project where a rubblize and overlay approach wouldn’t be possible, including beneath several overhead bridges with clearances limitations and several bridges on I-440 where the roadway had to tie into the existing bridge deck. As a result, only 40 percent of the existing roadway could be rubblized and overlaid. The rest of the project required full-depth removal and reconstruction.
In areas where existing concrete pavement had to be removed, it was taken to an on-site Kleemann 130 mobile impact crusher, where it was made into aggregate base course that was then used as the sub-base layer for the widened roadway and full-depth reconstructed sections. “Ultimately, we were able to crush and produce approximately 210,000 tons of usable aggregate base product,” Gregg said.
To stay on schedule, the crews had to pave 240,000 tons of asphalt between June and November 2019, and 60,000 tons of asphalt between March and June 2020. “Due to the schedule-critical nature of this project, the project was paved in various phases and not always in linear sequence,” Gregg said.
Although the 2020 paving section of the project occurred during the height of the COVID-19 pandemic, Gregg said reduced traffic didn’t have much impact on the speed at which they were able to complete the project. “The majority of the heavy-lifting on the project had been accomplished prior to the start of the pandemic, and it did not provide us any relief regarding lane closure restrictions, work hours, etc.” Gregg said. “It did, however, likely provide us with a safer work environment towards the end of the project as the volume of traffic traveling through our work zone decreased.”
The paving was performed by one full-time Kiewit crew, one fulltime crew from subcontractor Vulcan Materials Company, Birmingham, Alabama, and a second Vulcan crew when required. Material transfer vehicles (MTVs) were used throughout the paving; Kiewit used a Weiler MTV and Cat 1055 paver and Vulcan primarily used Roadtec Shuttle Buggies and pavers. Hamm rollers equipped with Intelligent Compaction (IC) capabilities were used to compact the mat, alongside a pneumatic roller when needed.
In total, the project consisted of 42 lane-miles requiring 300,000 tons of asphalt. All asphalt for the project was produced by Vulcan Materials, mostly out of its Danley Quarry plant, with supplemental supply coming from its River Road and Hermitage plants.
“The asphalt section and design varied throughout the corridor based on existing geotechnical considerations, widening sections versus existing reconstruct sections, and rubblize and overlay sections versus full-depth reconstruct sections,” Gregg said.
Typically, the full-depth sections consisted of 6 inches of cement-treated aggregate base course (CTB), 3 inches of asphalt drainage layer (AS-Mix), 3 ½ inches of asphalt base layer (A-Mix), 3 more inches of A-Mix, 2.5 inches of asphalt binder layer (BM-2 Mix), and finally, 1 ¼ inches of asphalt surface layer (D-Mix.)
The rubblize and overlay sections typically required 10 inches of rubblized existing concrete as a drainage layer, 4 inches of A-Mix, 3 inches of BM-2 Mix, and the same 1 ¼ inches of D-Mix as the fulldepth sections.
When all was said and done, Kiewit was able to complete the project a month ahead of schedule, with all lanes opening by the end of June 2020.
“Resources, including crews, equipment and material, were vital to ensure that schedule could be met,” Gregg said. Past experience on A+B projects also helped. Kiewit has completed several A+B projects for the Arkansas Department of Transportation. In Tennessee, they’ve completed two previous major projects for TDOT utilizing alternative delivery. “This project brought both of those worlds together, utilizing the alternative delivery design-build method, and the A+B, schedule critical procurement.”