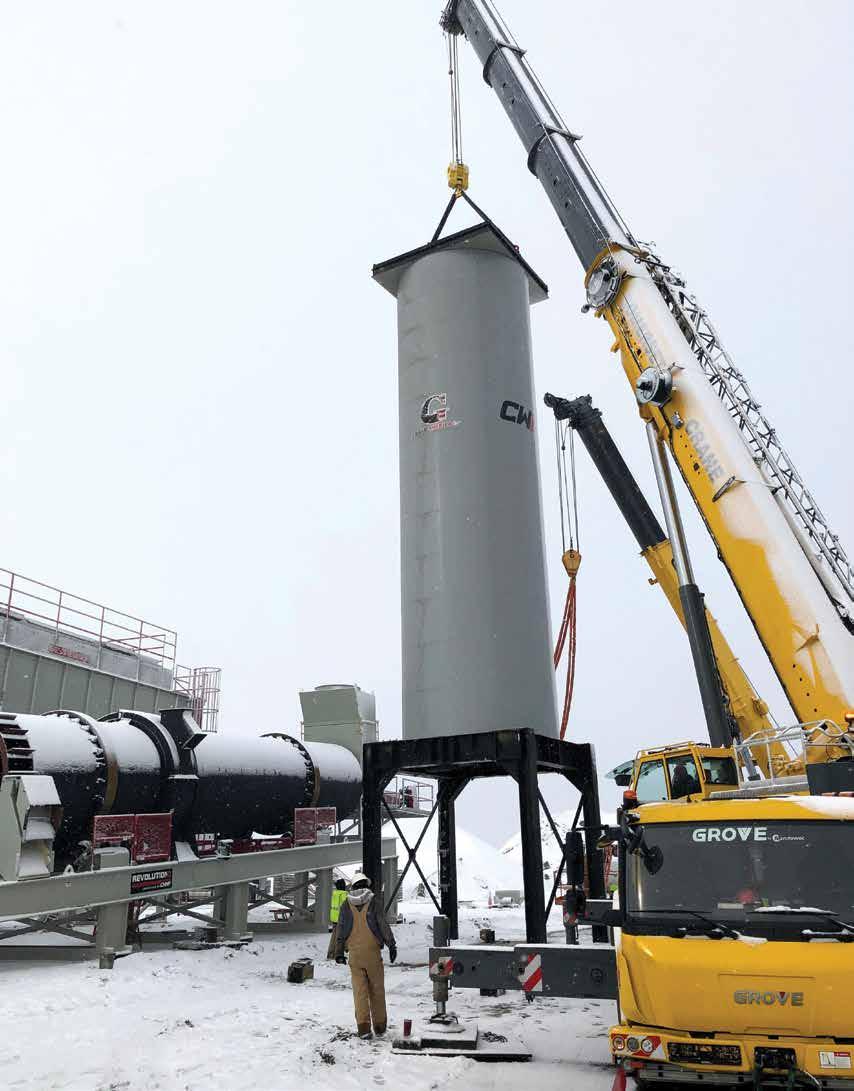
12 minute read
Cooperation Builds New
COOPERATION BUILDS NEW PLANT FOR GERKEN MATERIALS
BY SANDY LENDER
Plant Manager Jan Vajen explained that the team tried to work around predicted snow days, but the weather had other plans. The crew adapted, took delivery of equipment and assembled components no matter the conditions. Photo courtesy of CWMF
SSince the new plant at its Pioneer site came online in late May 2020, Gerken Materials Incorporated has sent more than 80,000 tons of various mixes into the Northwest Ohio marketplace for its crews and customers. The process began in summer 2019 and saw the cooperation of multiple vendors alongside the savvy hot-mix asphalt (HMA) provider to get the environmentally friendly facility up and running. Capable of up to 50 percent recycled asphalt pavement (RAP) content mixes, they’ve incorporated a Revolution-D mixing drum from CWMF Corp.,
Waite Park, Minnesota, among the complementary pieces. Here’s how it all came together.
Gerken Plant Manager Jan Vajen served as the general contractor of the plant build; Gerken Assistant Plant Manager Doug Willeman took on plant set-up and installation responsibilities. Vajen explained that
Gerken supplies a variety of products for the Northwest Ohio market. “We make anything and everything. Polymer-modified, virgin mix,
RAP mix. You specify it, we will make it.”
Designing and making mix isn’t all this team accomplishes in a season. For the winter of 2019-2020, they installed the new plant components under less-than-ideal weather conditions, as you can see by the images here. But they accomplished the goal through weather and pandemic trials and tribulations with hard work and core principles. First, the weather tried to wreak havoc on scheduling when the silo system, supplied by CWMF Corp., arrived for assembly.
Vajen said: “We do this kind of work all of the time. We would prefer to work under better conditions than a driving snow storm. In fact, we moved the delivery in anticipation of dodging the weather, but when the iron shows up, you just got to go to work. Doug Willeman and the
Gerken team is accustomed to this and worked exceptionally well together during this installation, despite the weather challenges.”
CWMF Corp. also provided the drum, baghouse, primary collector and drag slat conveyor for this new site (See sidebar). Meeker Equipment Inc., Belleville, Pennsylvania, provided the liquid asphalt (AC) tanks. Reliable Asphalt Products, Shelbyville, Kentucky, supplied the cold feed system, Vulcan burner, Minds controls and start-up service.
It sounds like a lot of moving parts, but Vajen and team worked with each vendor throughout the process, even when social distancing restrictions cropped up.
Vajen said, “We have been practicing all protocol. Social distancing, face covering, hand sanitizer, publication of all COVID-19 safety precautions. All of this while maintaining the Gerken Materials high standard for worker safety and quality products. Although COVID-19 presented a new list of challenges, the Gerken team has been up to the task.”
DEVELOPING THE PLAN
The conversation between CWMF Corp. and Gerken personnel began August 2019, according to Mike Czeck, the application sales engineer for CWMF Corp. He explained Vajen wanted to update Plant #20 located near Pioneer, Ohio. “The desire was for increased and longer-term asphalt storage capacity. For example, the original two 150-ton storage silos were replaced with two 250-ton silos.” Czeck explained that prior to the August 2019 visit, Reliable Asphalt Products’ Mauzy reached out to CWMF’s Travis Mick “to explore a collaborative opportunity for a new hot-mix plant project with Gerken Materials Inc.”
Mike Mauzy, president of Reliable Asphalt Products, detailed his early participation, where the team assessed which existing components of Plant #20 should remain on site and be incorporated in the new facility. “We had been looking for good used components and Check out the Here’s How it Works feature on Reliable Asphalt Products’ Vulcan Burner at theasphaltpro.com. Photo courtesy of Reliable Asphalt Products
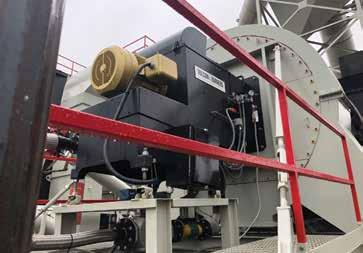
By spring 2020, the Gerken Materials Pioneer site was ready for business. Photo courtesy of CWMF
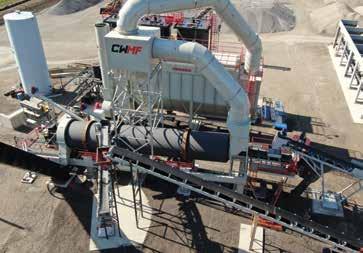
when those options did not materialize, they decided to move forward with new components. The plant was already outfitted with a complete Minds control system and Gerken had purchased a new Meeker vertical tank in 2016, so those items did not need upgrading.
“Mr. Vajen asked me to quote a complete new plant. Although Reliable Asphalt Products has those capabilities, we recognize that others are more geared to supply the larger components of an asphalt plant. I recommended that Gerken explore CWMF…it was recommended that they visit the new CMWF installation at Ajax Paving in Detroit.”
Mauzy also needed to show the new technology of the Vulcan burner to Vajen. “Mr. Vajen traveled with me to inspect our Vulcan burner installation at Sunbelt Asphalt near Auburn, Georgia, during the 2019 summer,” Mauzy explained. “The Vulcan burner installation at Sunbelt yielded extremely low NOx as well as low CO. It was basically the same size burner that Gerken planned to purchase with a similar application burning natural gas. Gerken’s goals were to meet the emission and fuel usage standards that were demonstrated during their inspection. Mr. Vajen specifically requested the Vulcan burner for this new plant installation.”
The Revolution-D mixing drum from CWMF and Vulcan burner from Reliable Asphalt Products are controlled with the Minds plant control system. Vajen said the components have all tied into the Minds system well, exceeding the company’s expectation. Photo courtesy of Reliable Asphalt Products

Meeker Equipment delivered two additional 25,000-gallon hot oil heated asphalt storage tanks with Saf-T-Tread top design for the three-tank farm at the Pioneer site. Photo courtesy of Meeker

Shortly after the inspection of equipment in action, CWMF and Reliable Asphalt Products jointly presented proposals to Gerken. “Reliable Asphalt Products quoted new feed virgin and RAP feed systems, the new Vulcan burner, controls modifications and start-up service,” Mauzy said. “CWMF quoted a new drum mixer, ductwork and primary dust collector, baghouse, drag slat, and two-silo system with transfer conveyor.”
After visiting the plant in Detroit, Gerken management made the decision to move forward with both proposals.
“CWMF and Reliable Asphalt Products had to work in lockstep with one another since the Minds controls supplied and installed by Reliable would be controlling their equipment,” Mauzy said. “Also, because Reliable Asphalt Products was supplying the new burner, both companies had to work together closely to make sure that the burner was delivered to CWMF and that CWMF had the proper information for its installation.”
EXECUTING THE PLAN
The first pieces of the puzzle arrived in January. Steve Meeker of Meeker Equipment explained: “For the Gerken Pioneer location, Meeker Equipment supplied three 25,000-gallon hot oil heated asphalt storage tanks, two with mixers, all tank-jacketed valves and jacketed piping between the tanks. We manufactured and delivered one of the three on site in 2016, so it was there prior to the start of the project. In January of 2020, we delivered tanks two and three.”
The three AC tanks will store 64-22, 70-22 and 76-22, according to Meeker.
Keeping up with innovations, Gerken management was keen to include safety features at the tank farm. “With our square Saf-T-Tread top design, the two newest tanks were able to be installed right next to one another and eliminate the need for a walkway between them,” Meeker explained. “This results in a wide open and safe service area on the top of the tanks. The controls for the tank farm are combined in one cabinet for consolidation of space and ease of use.
“The tanks are insulated with 6 inches on top and the sidewall and 3 inches on the bottom,” Meeker continued. “Our unique double-bottom head design allows for a test port to confirm the integrity of the internal bottom at any time during the life of the tank. The tanks also feature both mechanical level gauges and pressure transmitters for inventory control along with high-limits floats as a redundant safeguard for overfill protection.”
Czeck confirmed more of the timeline: “CWMF began shipping equipment in early February 2020. The baghouse was the first to be tackled by Doug and his team, followed by the drum. Shortly after the
CWMF Spells Out Energy Efficiency
For the Gerken Paving Materials plant build in Pioneer, Ohio, CWMF provided the following components.
• Revolution-D 8-foot, 6-inch by 50-foot counterflow drum
The trunnion-driven Revolution-D drum-mix plant is rated at 300 TPH and capable of up to 50 percent RAP with proper flighting configuration.
• Dust-Eater 70,000-CFM pulse-jet baghouse
16-oz Nomex filtration bags and Viton-sealed Goyen manifold pulse valves; Mike Czeck of CWMF stated: “Jan specifically required 16-oz aramid material bags over the standard 14-oz for cleaning efficiencies and improved air quality.”
• Two 250-ton asphalt storage silos
Dual level indicators and optional AR lined 4-ton batches with patent-pending exterior gate removal for ease of maintenance;
CWMF’s loadout gates are mechanically timed for added safety.
• 400-TPH drag slat conveyor
96-foot C-C 100-horsepower, Ni-hard, Hi-chrome, “L” shaped floor liners
• 14-foot transfer conveyor
CCO 2-way directional flop-gate assembly, Ni-hard, Hi-chrome,
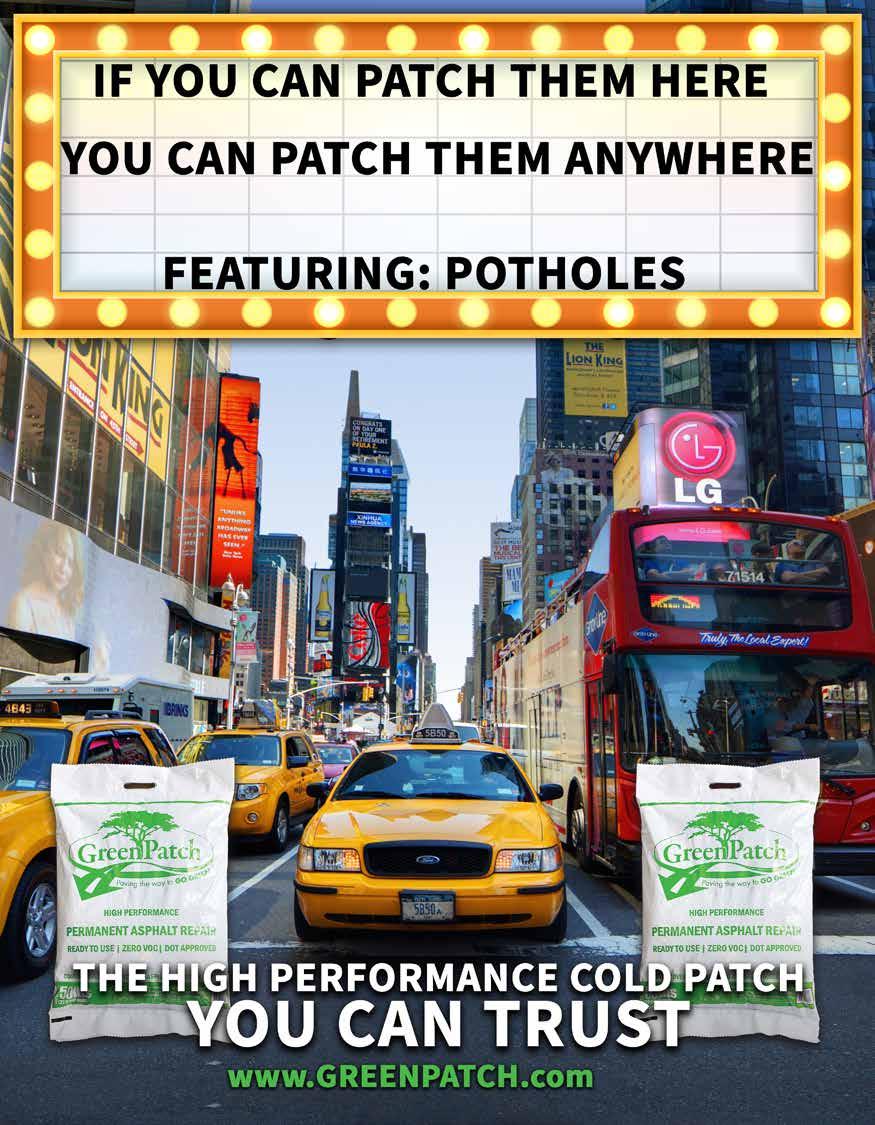
Despite COVID-19 restrictions, the team was able to install and commission the new plant for Gerken Materials and it is now in full operation. Jan Vajen spoke highly of his Gerken crew, specifically: “We have been practicing all protocol. Social distancing, face covering, hand sanitizer, publication of all COVID-19 safety precautions. All of this while maintaining the Gerken Materials high standard for worker safety and quality products. Although COVID-19 presented a new list of challenges, the Gerken team has been up to the task.” Photo courtesy of CWMF
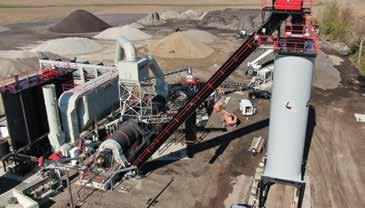
silos arrived, and were set on a snowy February day with the drag slat immediately following.”
Mauzy said equipment delivery continued into April. “Obviously, installation and on-site technician support was hampered by COVID-19 restrictions. Over the course of May, installation was completed, the plant was commissioned and is now in full operation.” Getting it started took the same cooperation the team saw all along.
“Working in conjunction with CWMF, the installation of the burner in their new drum went very smoothly,” Mauzy said. “This installation was conducted in the CWMF factory. Reliable Asphalt Products worked in conjunction with the owners of Vulcan Burner in Ireland to deliver the burner from overseas to the CWMF factory. Locating some of the fuel components took some additional engineering but ultimately, the installation went smoothly, especially considering this was the first Vulcan burner installed on a new drum. The test firing and the first firing, as well as all of the components from both companies, went extremely smooth.”
“We haven’t had any issues with the burner,” Vajen agreed. “The efficiency rating is up, proving more efficient than the previous installation.”
Czeck saw Gerken’s use of the new burner as an innovation. “Matching up Reliable’s new-to-market Vulcan burner and our proven Revolution-D mixing drum plant components and tying it all together with Minds control system resulted in bottom line more efficient asphalt production.”
Vajen said the components have all tied into the Minds system well, exceeding the company’s expectation. “David Towers, the Gerken Pioneer plant operator, was already familiar with the Minds system since it was installed on the previous plant,” Vajen said. (Reliable Asphalt Products sold the previous plant to Super Asphalt in Puerto Rico. See sidebar.) “David Towers was already familiar with the controls so that made the transition to the new plant even easier,” Vajen said.
ASPHALT TESTING EQUIPMENT F R O M AT S
Bending Beam Rheometer 2S (BBR2S) Performs flexural tests on asphalt specimens
UPGRADE YOUR ASPHALT LAB WITH ATS TEST EQUIPMENT
Pyro-Clean®
Safely cleans lab equipment by pyrolysis.
www.atspa.com
Bending Beam Rheometer 3 (BBR3)
Performs flexural tests on asphalt specimens with integrated touch screen display.
Vacuum Degassing Oven (VDO Touch)
Removes air bubbles created during the in-service oxidative aging of asphalt binder by the PAV.
Rolling Thin Film Oven (RTFO Touch)
Simulates short-term aging of asphalt.
Pressure Aging Vessel (PAV4) Simulates in-service oxidative aging of asphalt.
A GOOD TEAM OVER THE YEARS
Not only have the members of the Gerken team worked well together within the Gerken Materials Inc., they’ve had good partnerships with the vendors who helped them bring the new plant online.
“Meeker Equipment has been an asphalt equipment supplier to Gerken Materials since the early 1990s,” Meeker said. “Our relationship has grown steadily over the years. We started our relationship early on, providing some used equipment pieces, then reclaimed used oil systems and most recently multiple asphalt tanks at their many asphalt plant locations. The people of Gerken Materials are great to work with and many of them are Ohio State Buckeye fans, so we like that as well!”
Mauzy also spoke of his friendship with Gerken personnel. “Reliable Asphalt Products has developed a strong relationship with Gerken and most of that relationship had historically centered on transacting used asphalt plant equipment. Reliable Asphalt Products has sold equipment to and for Gerken Materials. The first new equipment transaction Reliable Asphalt Products conducted with Gerken was the sale of a new control house equipped with a complete Minds control system several years ago.”
CWMF was new to Gerken Materials, Czeck explained, “So we had to go the extra mile, ensuring the project was mutually successful for all parties involved, especially the customer. This was a unique opportunity for us to develop a continued relationship for years to come.”
Out with the Old
Mike Mauzy of Reliable Asphalt Products, Shelbyville, Kentucky, was one of the first equipment and service providers to assess the needs of the Gerken team’s Pioneer site. He explained: “One of the stipulations for the installation of the new plant was the sale of Gerken’s existing plant that was on site at the Pioneer location. Super Asphalt in Puerto Rico has been one of Reliable Asphalt Products’ very good customers over the past decade or longer. Miguel Suria, Super Asphalt’s general manager, had communicated with me his need for a portable 250-300 tph counterflow plant for some of the rebuilding work resulting from the recent devastating hurricane in Puerto Rico. I contacted Miguel while on site inspecting Gerken’s plant with Jan Vajen and sent Miguel pictures during my inspection. Miguel confirmed that the plant seemed to meet their needs. I met Miguel in Pioneer about a week later and made the deal to move the plant to Puerto Rico. While on site inspecting the plant, Mr. Suria inspected the Minds control system that was running the plant and decided to equip this plant with Minds technology in Puerto Rico.”
WEB EXTRA: Read “Ajax Materials Corporation Manages New Plant Build” at theasphaltpro.com.
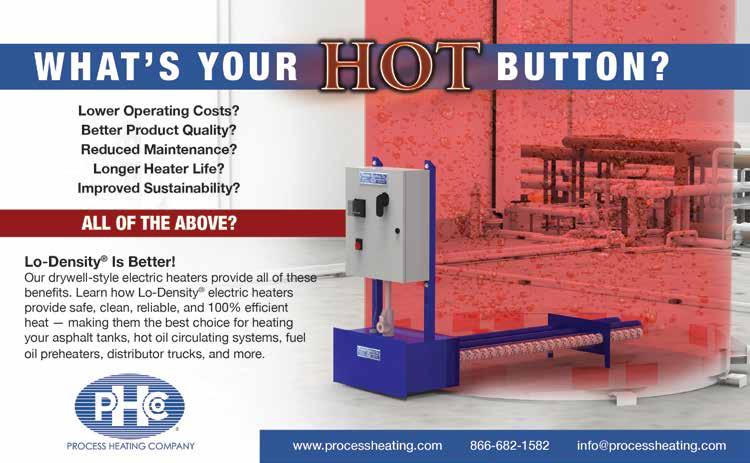