
7 minute read
Wisconsin Job Compares
Wisconsin Job Compares Cold In-Place and Pulverize/Relay
WWhen the asphalt pavement along State Trunk Highway 49 in Wisconsin’s Green Lake County needed to be replaced, the job presented an ideal opportunity for a side-by-side, long-term performance comparison of two asphalt pavement recycling processes: cold inplace recycling (CIR) and pulverize and relay (PR).
“WisDOT wanted to find out which pavement recycling treatment would give them the best pavement life for their investment,” Bryan Schaller said. He was the project construction leader on the STH-49 job for Alfred Benesch & Company, Chicago, Illinois, which acted as WisDOT’s onsite engineering personnel on the project.
The 7.4-mile project would divide the two-lane road into two sections. The north half of the project used CIR, while the southern half was pulverized and overlaid. The average annual daily traffic on this section of STH-49 is 3,800, with roughly 17 percent truck traffic.
“This was a good project to try this on, because traffic is largely consistent between the north and south halves of the project,” Schaller said. Another feature of the project that made it an ideal candidate for this research was that this segment of STH-49 had both higher hill areas and lower swamp areas on both of the test areas, which was important to account for the potential of capillary action in the CIR in the low-lying areas to be able to apply results to a wider variety of projects.
Not least of all, the pavement had also reached the end of its service life and was in need of reconstruction, whether in the form of CIR or PR.
The research project on STH-49 would span 10 years, and began before any work on the pavement had started. WisDOT brought out its falling weight deflectometer (FWD) to measure the modulus of resiliency of the existing pavement along the length of the project. After the pavement had been rehabilitated, they took another measurement over the length of the project, and will continue to take these measurements once a year for the next 10 years to compare the results of the CIR and PR areas.
The prime contractor, Northeast Asphalt, Greenville, Wisconsin, began its work in May 2019. However, the project manager for Northeast Asphalt on this job, Heather Sayler, met with the DOT and engineering staff ahead of time to recommend some changes to the plan. For example, the DOT originally wanted to do a varying width of CIR, specifically in turn lane and intersection areas.
The project on STH-49 aims to compare, side-by-side, the long-term performance of cold in-place recycling with pulverize and overlay.

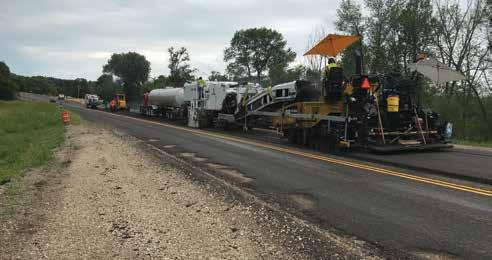

“If you start widening and narrowing with CIR, it’s hard to balance material across wider cuts,” Ric Szalewski, Northeast Asphalt’s lead project manager, said. “If width and depth are constant, you can have a constant flow of material.”
After talking it over with the DOT, it was decided that the subcontractor, W.K. Construction Company Inc., Middleton, Wisconsin, would perform CIR at a constant width of 15 feet on the mainline and bypass lanes after first milling and paving the tapers and intersections using traditional methods. “That allowed us to avoid transitioning in and out of places with CIR, which can be more cumbersome,” Szalewski said.
Another example of teamwork across stakeholders was traffic management. “There was a heavier volume of traffic, especially with the bypass lanes,” Szalewski said. “After talking to the DOT, we were able to close down the outside passing lanes and delineate them with barrels, which meant we only had to flag two lanes of traffic rather than three.”
Northeast started with the CIR section on the northern half of the project. First, Northeast milled off 2 ¾ inches of asphalt with its Wirtgen WR250i. Then, W.K. performed the 4-inch CIR with its Roadtec RX900 mill and Cat 1055F paver with a Weiler SE10 screed.
After taking cores of the existing pavement, W.K. developed the mix design and provided it to the engineers at WisDOT. They determined an optimum binder content of 2.5 percent, with a foaming water content of 3 percent as its stabilizing agent for CIR.
After seven working days, the CIR process was complete. As they waited for the CIR section to cure, the Northeast crew began the PR section. Over five days, Northeast pulverized and blended the existing asphalt to a depth of 6 inches, getting a minimum of at least 2 inches into the base course layer. Szalewski estimated the average to be about 8 inches, performed in one pass.
“For the PR section, the contractor had to get below the bottom of the existing pavement,” Schaller said. With the CIR section, they left a little bit of the existing pavement. “Getting to the material beneath the pavement introduces a whole other variable. We’d have to adjust our application of stabilizing agents. It could present a lot of challenges and variability.”
Northeast paved a 1 ¼-inch lift on the CIR section with its Volvo 7170B paver, equipped with a Carlson EZ4 screed. The crew also used a Weiler 1250 material transfer vehicle throughout the paving aspects of the project.
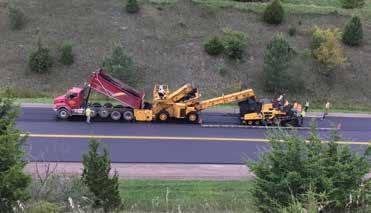

The research project on STH-49 will span 10 years. WisDOT used its falling weight deflectometer (FWD) to measure the modulus of resiliency of the pavement, before and after the project, and will continue to take these measurements once a year for the next 10 years to compare the results of the CIR and PR areas.
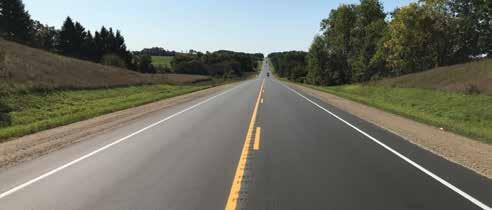
As they worked on the PR section, Northeast’s paving crew began paving a 1 ¼-inch lift of 5 MT 9.5mm mix on the CIR section with its Volvo 7170B paver, equipped with mechanical contact on reference skis for automatics, and Carlson EZ4 screed. The crew also used a Weiler 1250 material transfer vehicle throughout the paving aspects of the project.
“We were paving on some really hot days in August,” Szalewski said. “High heat can sometimes cause CIR to flush.” To avoid picking up any AC from the CIR section, Northeast equipped its paver and MTV with water spray systems.
“The idea behind our schedule was to get the CIR done so we could check moisture on a daily basis as we pulverized,” Szalewski said. Then, they could finish placing the first lift on the CIR section just as they completed the PR section. “Then, we could pave the first lift on the PR side, and then start the final lift on the whole project.”
The crew paved 2 ½ inches of 3 MT 19mm asphalt on the PR section, and then began paving a 1 ½-inch surface course of 5 MT 9.5 mm along the entire project.
In total, the project required 11,800 tons of 3MT and 27,730 tons of 5 MT. The mix was supplied by Northeast Asphalt, which set up its 400-tph Dillman counter-flow portable asphalt plant located half a mile from the job.
Another challenge was paving varying thicknesses over multiple substrates. “We had to figure out how to transition from our PR section to our CIR section,” Schaller said.
If they joined the sections abruptly, Schaller knew they’d end up with a vertical joint failure. They also had to make sure the transition area, which was about 100 feet long, would still be a smooth ride for the traveling public. After reviewing a number of options, they decided to feather out the layers so they crossed into one another. The crew paved 40 feet past the transition point, feathering the lifts down to nothing.
Despite the complexity of the project, Northeast was able to exceed density requirements and achieve a very smooth ride.
The average density of the project was 94.8, 1.8 percent over the target density, and the density didn’t differ much between the two sections. The International Roughness Index (IRI) on the CIR portion was an average of 27, and a 22.2 on the PR section.
“Those are outstanding IRI numbers,” Szalewski said. “And that’s just the average. Some individual segments were in the teens!”
Although only time will tell which treatment comes out on top, the project on STH49 was so successful it was recognized with a National Quality in Construction award at the 2019 National Asphalt Pavement Association Conference and an Innovation award from Wisconsin Asphalt Pavement Association.
“Despite the challenges of combining multiple processes on this research project, the quality of the pavement at the end of the day was outstanding,” said Dan Grasser, Alfred Benesch Division Manager. “That speaks to the collaboration between WisDOT, its regional offices, the contractors, WAPA and our team to make sure we not only achieve our research goals but also end up with a quality roadway.”