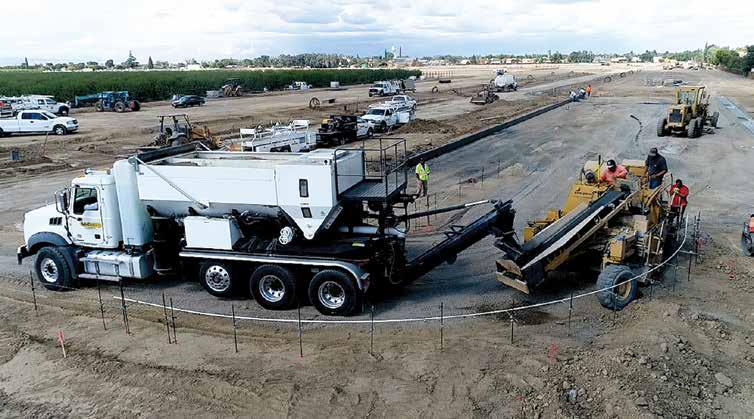
6 minute read
Make More Project Money
Make More Project Money Make More Project Money
BY KRIS MOORMAN
With volumetric mixing, a contractor performing multiple pours of different specifications can toggle through the designs stored in the mixer. That process is controlled through a metered belt system in the aggregate bin, an individual water tank and a dual auger system that measures the cement as it’s poured. Additionally, liquid admixtures are controlled by an electric pump through a flow control valve. Once the curbs, gutters, drains and medians are in place, the contractor can bring in his asphalt crew to pave the roadways. Photos courtesy of Cemen Tech Inc. FFor many asphalt contractors, concrete is a dirty word. But members of the asphalt industry have opened new revenue streams and taken greater control of their job costs by adopting volumetric concrete technology as part of their suite of services. There are benefits to diversifying your operation through the precision, detail and efficiency of volumetric concrete technology, such as eliminating delay costs—both internal and external. By flipping the current asphalt contractor–concrete subcontractor paradigm on its head, asphalt companies can take full control over projects that have curb, gutter, drain, sidewalk and median requirements. That alone can add a direct revenue stream to your operation. Better yet is selection of a volumetric concrete mixer, which adds flexibility to traditional barrel mix technology. With a volumetric concrete mixer, contractors can pour multiple mix designs across several G&T PAVING BEATS THE HEAT WITH VOLUMETRIC CONCRETE In the world of public utility contracting, versatility, speed and efficiency are paramount. Robert Gonzales, the owner of G&T Paving— located along the Mexico border—has learned that lesson over the years as his company was required to complete jobs at multiple sites daily around his community. Gonzales and the G&T team worked to be as nimble as possible, but there were always limitations. In the past, they relied on traditional barrel trucks to deliver concrete, so they would often have the site prepped and ready to go, but they were left waiting for the material to arrive. A lot of time was being wasted, Gonzales said. Additionally, the barrel mixers oftentimes weren’t up to the task of completing multiple pour locations. jobs in the same day that required different concrete mixes, different For example, if a bid for a municipal road project includes curb and pressure requirements, different fiber additions, etc. gutter components, each will likely require a different concrete mix- “Our schedule was completely thrown off,” Gonzales said. “So, we’d ture at different volumes. With a volumetric mixer, the contractor have to come back to the site a second time and even sometimes a third eliminates the need for multiple batches of concrete from a subcon- time because of the way the schedule would go with a barrel truck.” tractor. Through volumetric mixing, he toggles between different mixtures on demand. For many major asphalt contractors, such as G&T ON TOP OF THOSE CHALLENGES WAS WASTE Paving of Brownsville, Texas, the addition of two Cemen Tech C60 vol- “When we were running barrel trucks there were a lot of times we were umetric mixing trucks is netting immediate returns that have allowed moving around to four or five different locations,” Gonzales said. “Evthe company to take on more work while cutting costs in half. ery time that we were moving around, there was a quarter yard here,
and a quarter yard there, a quarter yard there, that we were leaving at every location.”
The realization that something had to change had been percolating for some time, but finally culminated during a trip to Dallas. On that trip, Gonzales noticed companies that were using volumetric concrete mixers. It was technology that he wasn’t familiar with, but he was interested. Upon his return to Brownsville he researched, and he realized the values that volumetric concrete mixing brought to the table were all of the elements G&T Paving needed to thrive.
It didn’t take long for Gonzales, whose father started G&T 50 years ago, to turn the page on a new chapter in G&T’s history. Shortly after the Dallas trip, Gonzales bought his first Cemen Tech C60 Volumetric Concrete Truck. And shortly after that, the results started flowing in.
“Our time savings has been doubled,” Gonzales said. “I can see that production-wise that we have doubled our production within the last six months.”
On any given day, G&T relies on its Cemen Tech trucks to handle multiple work sites, oftentimes with different job requirements and mix styles. It’s handled each and every task, Gonzales said, including toggling between various fiber additions at the touch of a button.
“What I like about it is that we can get it on site and my utility crew, if they need a yard of concrete, we can jump in and get it done right there,” he said. “Before, we were waiting hours, sometimes days to get that material out there because they wouldn’t bring us that small quantity.”
QUALITY UNDER PRESSURE
In addition to efficiency and time savings, G&T has seen an increase in overall quality of its product. That was an initial concern, based on the company’s high standard on quality control, but the results have exceeded internal expectations, as well as rigorous testing by inspectors and utility engineers.
The quality stands up in the south Texas heat, too. A regularly-occurring issue with traditional concrete trucks in intensely hot climates is the inability to pour when the mercury levels rise into the 90s. Even engineers were dubious of the fact that G&T’s Cemen Tech truck could pour at high noon, with the sun beating down and 100 degrees on the thermometer without needing to add ice or a temperature-retardant chemical to the concrete mix.
“A lot of guys here are used to pouring with a barrel truck. They start pouring at 3 a.m. because they want to beat that sun. They want to beat that heat at 10 o’clock when it is already 100 degrees. I don’t have to do that. I don’t have to get up at five in the morning to pour concrete. I can pour at any time I want. With my truck I am ready to go. And, I get the temperature that I want and the quality that I want.”
The latest generation of Cemen Tech C60 mixers feature easy-to-use electronic controls, with the ability to use pre-programmed mix designs for one-button operation. This technology is designed to make it easy to produce fresh, quality concrete to spec—on the spot—with one piece of equipment, unlimited by travel time, distance or location. Less waste puts you more in complete control of every aspect of your projects.
Kris Moorman is the marketing manager for Cemen Tech Inc.
WINTER MAINTENANCE


www.tarmacinc.com
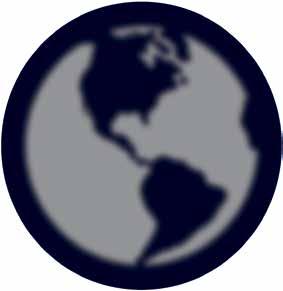
Is it TIME TO REPLACE YOUR WORN OUT CHAIN, FLIGHTS, FILTERBAGS, OR OTHER PARTS? CALL DALE. contact tarmac at 816-220-0700 or info@tarmacinc.com

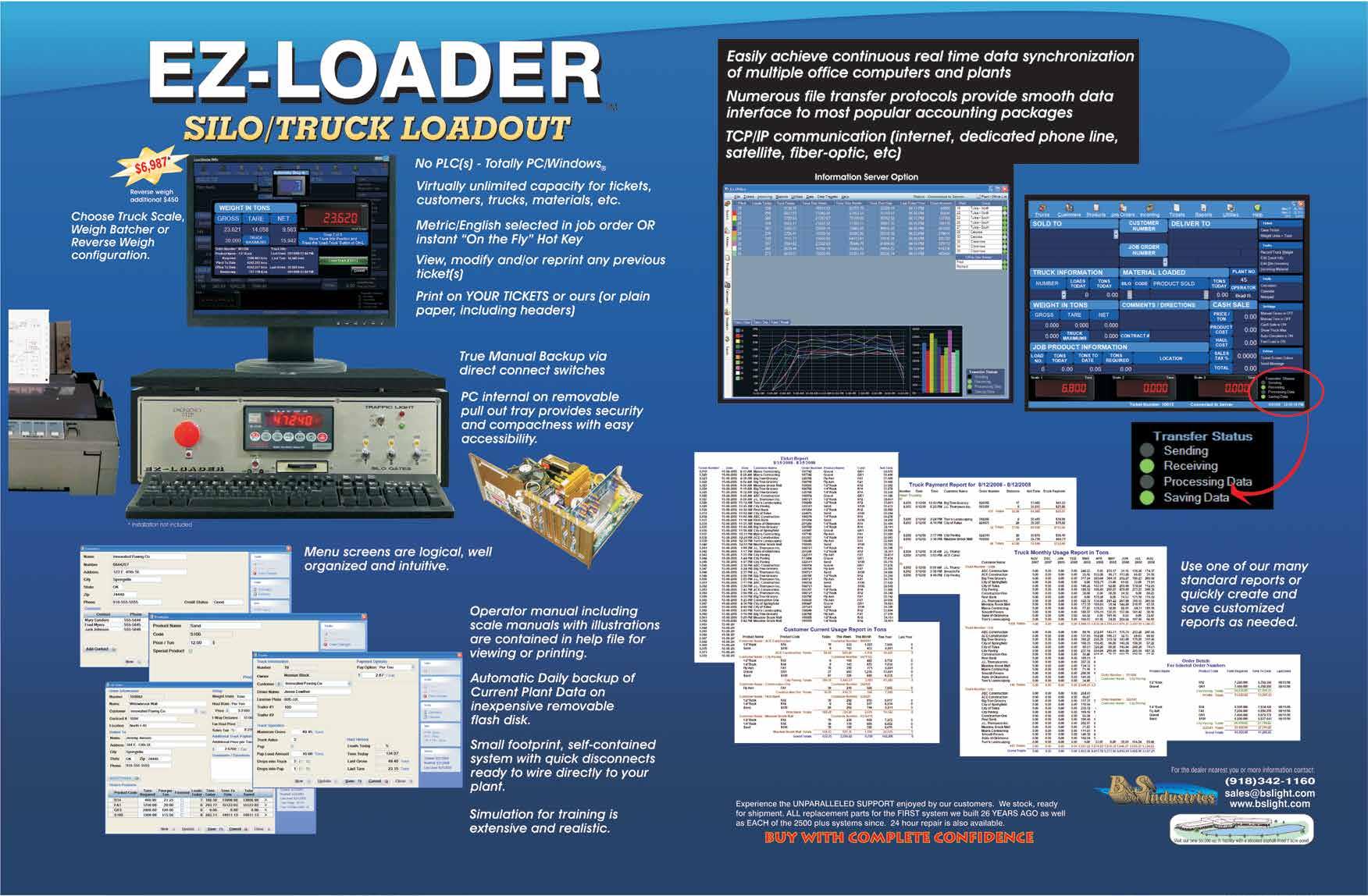
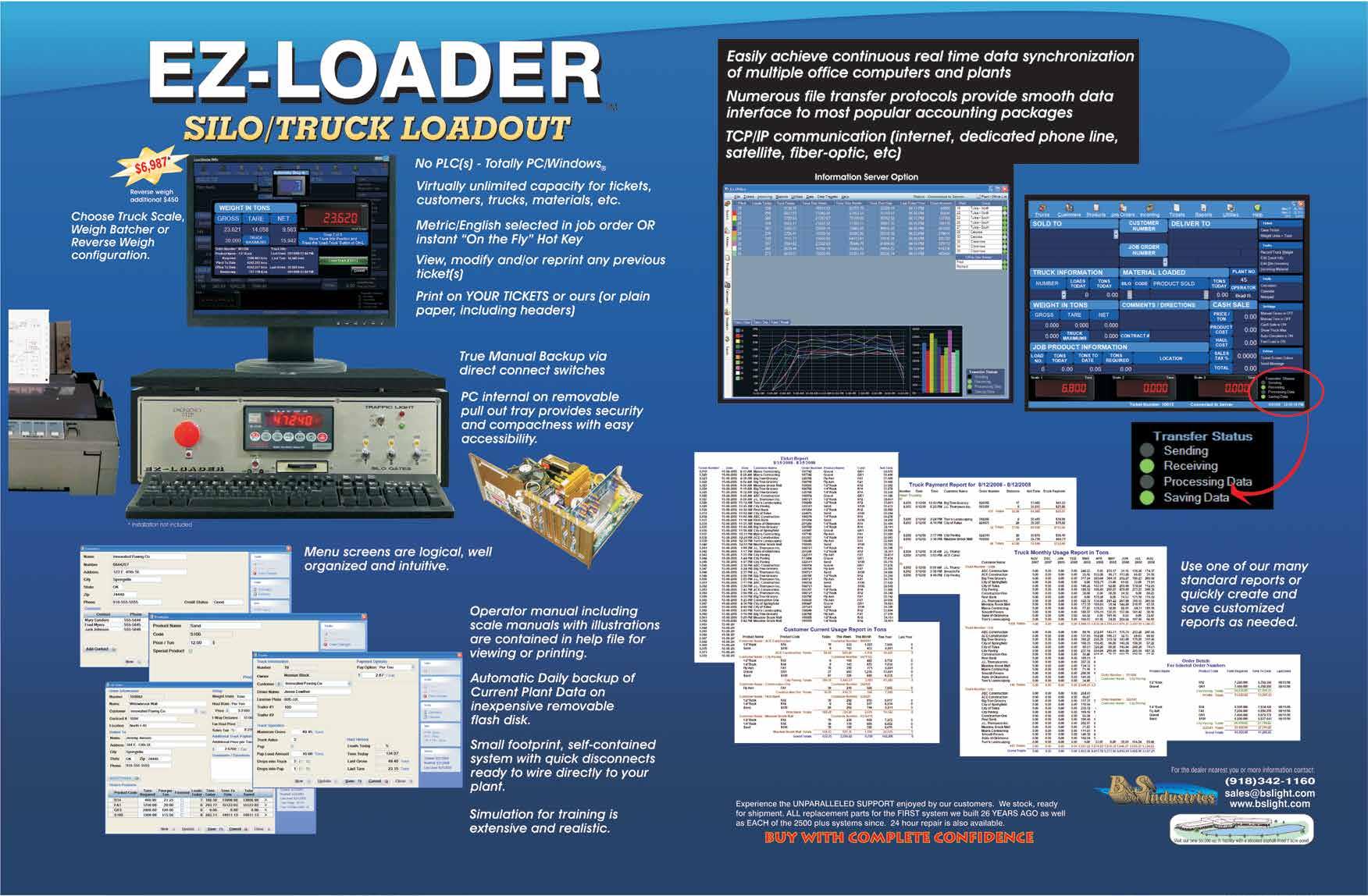