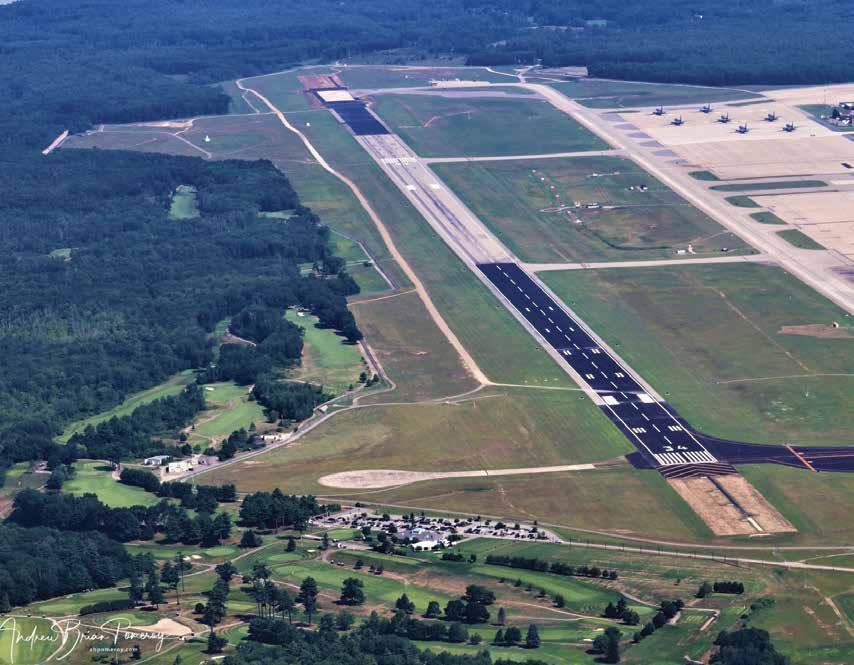
7 minute read
Pike Paves Airport Smoothness
PIKE PAVES AIRPORT SMOOTHNESS FOR YEARS TO COME
BY FLAVIA DE FARIA
TThousands of travelers will soon take to the skies by way of a revamped 11,322-foot by 150-foot runway and taxiway built with nearly 104,500 tons of asphalt supplied by Pike Industries Inc. (Pike), a CRH Company. Pike began construction in 2019 to rebuild the $20 million runway project at Portsmouth International Airport at Pease—formerly known as Pease International Airport—in Portsmouth, New Hampshire. The airport is a joint civil and military facility that serves New Hampshire’s seacoast area. “It has been really exciting to be part of this important project for the region,” Pike President Barry Duffy said. The Federal Aviation Administration (FAA), the New Hampshire Air National Guard, Pease Development Authority and the state’s bureau of aeronautics are paying for the project, which is scheduled to be completed in 2021.
The scope of the work at Pease includes profile milling the existing surface of the runway and replacing approximately 2.7 million square feet of asphalt pavement. The project also includes: • reconstructing four connected taxiways; • upgrading runway edge lights and threshold lights; • replacing airfield guidance signs and runway distance signs with LED signage; • installing two permanent precision approach path indicators; • striping and marking; and • re-grading edges of the runway safety area.
As the main contractor on the job, Pike is working alongside different subcontractors to meet FAA specs required on the project. “It has been an honor to partner with the Pease Development Authority,” Duffy said.
The COVID-19 pandemic didn’t stop the Pike team from making progress on the runway rehabilitation project. “We are extremely proud of our ability to tackle a project of this magnitude and execute safely and successfully even through the pandemic,” Duffy said.
Pike’s safety department has been vital to protect the safety and health of their employees during these unprecedented times. “Our work is essential to sustaining infrastructure and we are fortunate that we can safely execute within the new COVID-19 framework,” said Steve Fuller, safety director at Pike. “We all adapted to the new personal protective equipment (PPE) protocols and safety practices.”
PLANNING, PERMITTING AND PROJECT PHASES
Planning and permitting for the project began in spring 2019 and contains five different project phases. The runway reconstruction is being accomplished in phases to keep the airport open and operational as much as possible. Construction phases include periods of reduced runway length with relocated runway thresholds, periods of overnight runway closures, and up to 14 days of 24hour runway closure to complete the middle section. Here are some details.
Phases 1 and 2 consist of working on the north and south ends of the airfield. To minimize disruptions, Pike removed the existing threshold paint and repainted to make the runway 7,864-feet, essentially closing off one end at a time. The south AT LEFT: Crews at Pike Industries worked through the pandemic to make progress on the runway, which was last rehabilitated in 1995. Photo courtesy of Andrew Brian Pomeroy Photography ABOVE: The leadership team from Pike Industries and the Pease Development Authority welcomed U.S. Senator Jeanne Shaheen (D-NH) to see firsthand the work at Portsmouth International Airport. Photo courtesy of Pike Industries’ Flavia De Faria
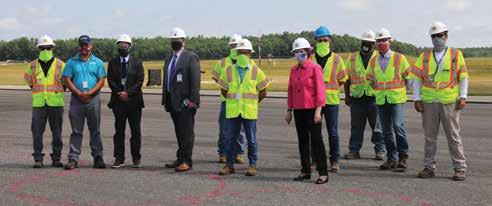
end closed first on April 8, and was opened back up to traffic by June 4. That cleared the team to close the north end on June 5.
Frank Tilton, construction manager at Pike, said, “Just as with roads, in the case of airport runways it is essential that renovation work is completed quickly and efficiently, causing as little air traffic disruption as possible.”
Repaving or reconstructing an airport runway can be one of the most challenging types of construction. According to Tilton, Phases 1 and 2 include removing 36,000 cubic yards of concrete and milling of 180,000 square yards of pavement varying from 2- to 9-inch depths of hot-mix asphalt (HMA).
The construction division placed 46,000 tons of specialty blended P-209 subbase produced at Pike’s quarry in Eliot, Maine. They used a gravel spreader box on a Cat D6 dozer to help increase production and decrease segregation; the subgrade and grade was graded with robotic total stations and laser system.
“We paved the south end first to minimize disruption,” said Tilton. “After concluding the south end, we will be rehabilitating the north end of the runway allowing aircrafts to land safely.”
Phases 3 and 4 consist of rehabilitating the middle of the more than 7,500-foot runway, which will require complete shutdown, planned for mid-September 2020. Pike will lay approximately 60,000 tons of asphalt in 14 days at 6,000-7,000 tons per shift. The project requires four milling crews and three paving crews alongside subcontractors for completion.
Pike is using two asphalt plants to supply HMA for the rehabilitation project. The pavement team gets the material from the Astec SixPack portable asphalt plant on site and additional HMA comes from their Gencor 400 tph drum plant located five miles away from the project.
“This project is a great example that displays the talent of our employees at Pike, the spirit of collaboration through all of our business units showcases the success on this project,” said Alex Phelps, vice president of construction at Pike.
Phase 5 consists of grooving and final painting of the runway, which will take place during 28 days of night work.
In addition to planning and permitting, collaboration between all lines of business has been the key for Pike’s runway rehabilitation success. “Constant communication between dispatch, construction, aggregates, plants and quality control continues to be vital for our success on this project,” said Beth Johnson, transportation manager at Pike. “We have had excellent and constant communication so everyone is on the same page and our plans are executed flawlessly.”
Pike’s crushing division will be supplying approximately 100,000 tons of asphalt aggregates, as well as 46,000 tons of subbase by the end of the project. “We pride ourselves on producing the highest quality materials and providing our customers the best product we can in the field,” Phelps said.
Working on airport pavements requires specialized knowledge due to the stringent specifications regulating this type of project. To minimize longitudinal joints,
Pike Industries used a Wirtgen milling machine to provide a smooth surface on the rehabilitation project. Photo courtesy of Pike Industries’ Flavia De Faria
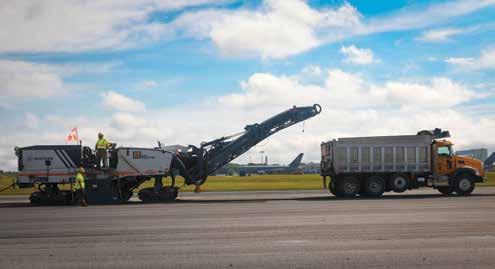
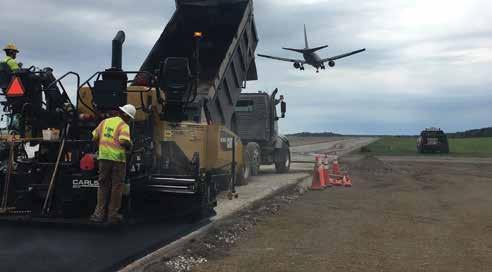
Pike Industries’ paving crews work to eliminate a cold joint to improve durability and longevity of the runway. Photo courtesy of Pike Industries’ Construction Division
Pike Industries has an Astec SixPack portable asphalt plant on site to maximize project efficiency. Photo courtesy of Andrew Brian Pomeroy Photography
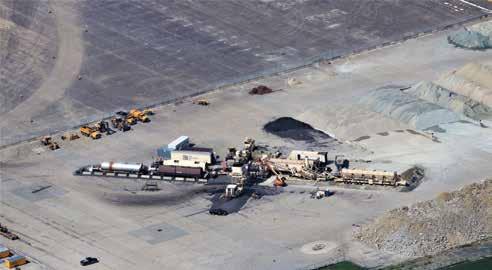
the company used two pavers in echelon for the length of the runway. This technique allowed Pike to eliminate a cold joint while improving durability and longevity of the runway. They achieved a 94.1 percent density on the joint and 95.9 percent on the mat.
Prior to paving, Pike used Wirtgen milling machines and a 2200 Wirtgen with a 12foot drum for the 3-inch inlay work in order to provide a smooth surface. A 2100 Wirtgen with a micro drum rehabilitated the runway’s shoulders. CAT F series pavers and Roadtec 2500 shuttle buggies have been key equipment throughout the project.
The Pike team worked in collaboration with subcontractors Weaver Brothers Construction Co. Inc. and Pavilion Drainage Supply Co. Inc. to remove the concrete pavement on the job. “Pavilion used a concrete breaker to fracture the concrete. Pike used a JD 1050 dozer to rip the concrete and pile it up,” said Thomas Doherty, construction superintendent at Pike. “Weaver removed the concrete using an excavator and haul units.
“It has taken a huge amount of coordination from our teams in multiple states (Maine, New Hampshire, and Vermont) to get us where we are today,” Doherty continued.
In early July, Pike’s leadership team welcomed U.S. Senator Jeanne Shaheen (DNH), who wanted to see firsthand the runway rehabilitation project. Duffy, alongside his leadership team, shared how vital it is to have the construction industry safely working to support local and state economies.
The Pike team told Shaheen that in addition to having ample sanitizer on hand for employees, they disinfect equipment in the morning and at night. “When COVID-19 became a concern, the entire Pike team rose to the challenge,” Fuller said. “The team stepped up to ensure we met or exceeded the new safety protocols needed to execute our work. It was great to see how we adapted to change.”
By using its own skilled labor force, Pike has shown control over schedule, cost, quality and safety. “All of us are very proud of being part of the Pike team on such a great project,” Phelps said.
Besides a few night closures and a twoweek shutdown, the runway remains open to its tenants and the Air National Guard during the runway rehabilitation work. “We look forward to completing the remaining phases of the project on time and on budget,” Duffy said.
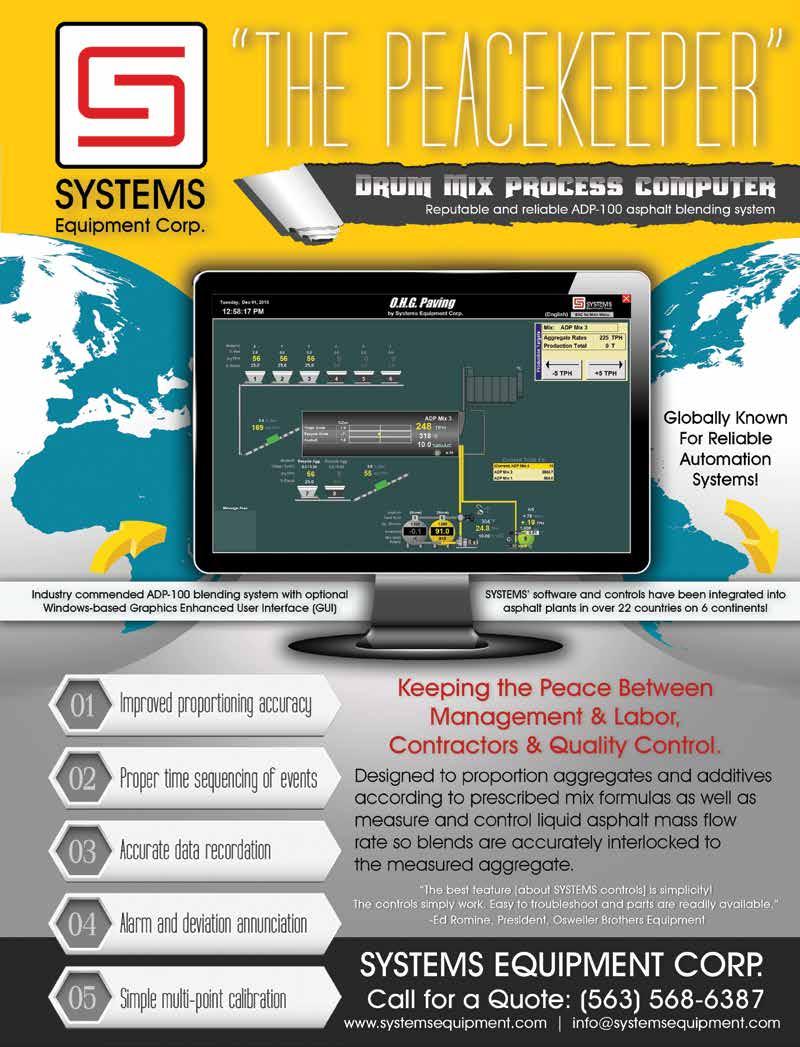