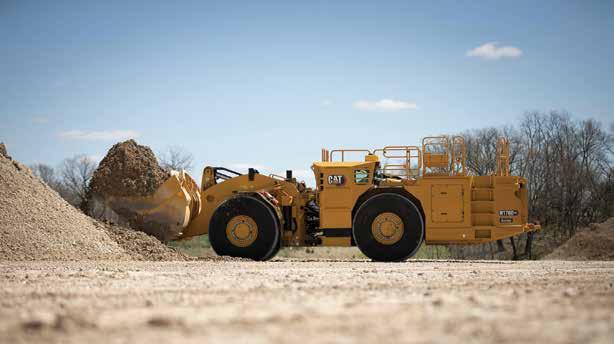
23 minute read
Asphalt Industry Seeks Efficiency in Electric Construction Equipment
BY SANDY LENDER
Leveraging over 400 Caterpillar advanced power system design patents, the new electric Cat R1700 XE LHD offers 100% battery electric propulsion. It is designed to match the performance of the diesel-powered R1700 while using switch-reluctance (SR) technology that draws from Caterpillar’s 15+ years of electric drivetrain experience and thousands of field application operating hours.
Editor’s Note: This article includes opinions of the author.MMany members of the asphalt industry have lately contemplated environmental product declarations, product category rules, life cycle cost analysis or net zero mapping. These tools are part of our vernacular in large part because environmental groups have grown nimble in their ability to point out a pavement’s cradle-to-grave greenhouse gas emissions potential, showing how ingredients have been sourced, crushed, transported, produced, and so on. Our community must often remind others of the recyclability of our product to present a complete LCCA that shows the true resilience of an asphalt pavement system. When it comes to the heart of an electric vehicle, we are often shown the magically appearing lithium-ion (Li-ion) battery pack
“mid-stream.” I dare you to find an episode of “This is Your Life” for this battery. Instead, many blogs bemoan the horrors of the diesel engine as a CO2 emitter and claim: • all-electric equipment is powered by Li-ion battery packs and • all-electric equipment boasts net-zero carbon emissions.
I posit, those two statements offer a dichotomy for us to overcome. It is my understanding that Li-ion battery packs are not a net-zero end game if you are mapping an EPD, LCCA or net-zero plan. A trend I noticed during my research was writers’ propensity to ignore the Tier IV Final advances engine manufacturers have made in recent years. Statements like “[d]iesel-powered vehicles like dump trucks and LHD loaders emit massive amounts of harmful gasses,” courtesy of MarketsAndMarkets, kept catching me by surprise. Our industry has worked overtime to implement EPA emission standards for diesel engines with selective catalytic reduction (SCR) and diesel particulate filters (DPF) where bad actors are converted to harmless water and vapor. In fact, MarketsAndMarkets acknowledged, “as per the US EPA norms, NOx and PM levels have seen a decline of around 95.6% and 96.2%, respectively, from Tier I to Tier IV.” That’s a stat worth shouting from the rooftops.
BATTERY IMPROVEMENTS
Dr. James Edmondson, a senior technology analyst at IDTechEx, specializes in market research for materials and thermal management in electric vehicles and 5G technology. In his look into the portfolio of trends for EV data, published July 8, 2021, he pointed out different material demands between the Li-ion batteries in electric vehicles and the internal combustion engine (ICE) vehicles. He wrote: “Whilst ICE
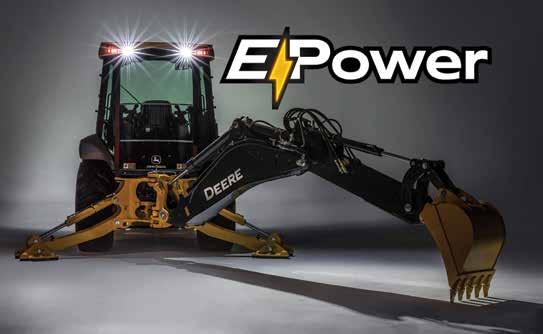
John Deere continues to incorporate the latest innovations and power solutions into its lineup of backhoe loaders including its first-ever joint test of a battery electric backhoe loader with National Grid. Aimed at lowering its carbon footprint and promoting sustainability, the Deere E-Power backhoe loader targets the performance of a 100-horsepower 310L diesel-powered machine, but with zero tailpipe emissions.
drivetrains heavily rely on aluminum and steel alloys, Li-ion batteries also utilize many other materials such as nickel, cobalt, lithium, copper, insulation, thermal interface materials, and much more at a cell- and pack level.”
During my research of electric off-highway vehicle (EOHV) batteries, I found a lengthily-titled, 211-page report from MarketsAndMarkets published in September 2020. The paid research portal reported in its summary section of opportunities in development of long-range and fast-charging battery technology: “Most electric off-highway vehicles are currently working on lithium-ion batteries due to their numerous advantages over lead-acid and nickel-metal hydride batteries. However, lithium-ion batteries have several limitations that affect battery performance. Limitations of lithium-ion batteries include issues related to robustness (as they require protection from being overcharged and discharged too far), limited power density, short lifespan (often 500-1,000 charge-discharge cycles before their capacity degrades), performance fluctuations with changing temperatures, rigidness, and high cost.”
The opportunities section of the summary continued: “Solid-state batteries manufactured with stabilized solid electrolytes in lithium metal offer up to 10 times charging capacity compared to graphite-based Li-ion batteries. Moreover, solid-state batteries offer increased energy density, such as double energy for the same volume, and an increased lifespan of up to 10 years. Thus, many electric off-highway vehicle manufacturing companies are investing in the development of solid-state batteries.”
IDTechEx’s Edmondson, and colleague Dr. Alex Holland, shared similar good news, stating in their report, “Materials for Electric Vehicle Battery Cells and Packs 2021-2031,” that the energy density improvements of Li-ion cells might appear to be the most prominent battery improvements in the public eye. “[W]e are also seeing an increase in pack-level energy density at a greater rate than just cell-level improvements,” they wrote.
Something I found echoed in conversations for this article is also found in the Edmondson and Holland report: When improving the battery design, the cell-pack weight can be decreased, which offers a lighter pack and/or multiple packs used in series.
Here’s how the Edmondson and Holland report handled that explanation: “Manufacturers are improving their battery designs, the mass of materials being used around the cells is steadily being reduced, allowing for a lighter battery pack or more cells to be used for the same mass. The choice of materials for several pack components also affects these improvements. More interest is being paid to composite enclosures for light-weighting, fire-retardant materials, thermal interface materials and much more. The thermal management strategy also impacts these choices, with increased energy density and consumer demand for fast charging, the thermal management must be more effective, but also present a smaller and lighter package.”
No one from Caterpillar was available to talk about battery electric vehicles (BEVs) for the construction industry, but information from around the web shows the company invested with Fisker prior to January 2019 with at least one goal of developing a solid-state battery for
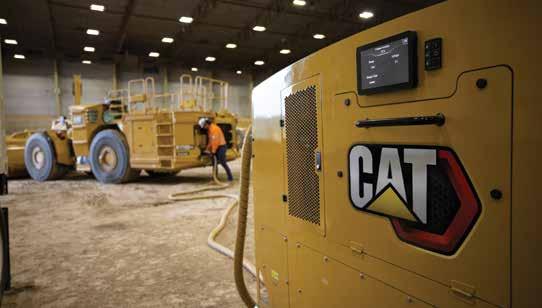
Caterpillar introduced the MEC500 mobile equipment charger during MINExpo September 2021. It’s equipped with a durable skid mount and integrated forklift eyes. It is designed to provide an alternative to expensive static charging station infrastructure, additional batteries, or battery handling and swapping. Specs: 500 kW charging and connector capability; 300 to 1,000 Volt, up to 700 Amp current output; units can be connected in parallel. Contact your Cat dealer for more details.
the purpose of out-performing Li-ion batteries. This positive step is noteworthy. Given the probability that industry will create a better, more sustainable, longer-lasting, recyclable battery, let’s move on to the BEV discussion for the construction industry.
Back in 2017, our associate editor Sarah Redohl shared with the industry a report from IDTechEx estimating that more than 165,000 fully electric machines would be operating in the construction, maintenance, agriculture and mining industries by 2027. We’re five years from goal and more than one source has referenced COVID-19 complications as a barrier to EOHV growth. Despite the pandemic’s disruptions, MarketsAndMarkets predicted September 2020 “global electric off-highway vehicle sales are expected to grow at a rate of 22.8% from 2020 to 2025.”
Let’s take a look at how that growth could be assisting the asphalt industry.
ELECTRIC CONSTRUCTION EQUIPMENT JOINS OTHER GREEN OFFERINGS
Shortly before press time, I received word that Zeus Electric Chassis Inc., Minneapolis, Minnesota, had joined forces with EAVX and launched electric vocational trucks in the Zeus Power Platform. The Zeus Z-22 Class 6 electric vocational truck incorporates a Li-ion NMC battery, up to 175 kWh size.*
Bob Grinstead, founder and chief technology officer for Zeus, pointed out the best practices for users to charge the battery and keep the truck at optimum readiness for work. “A simple example is the Zeus 140 kWh battery system scenario,” Grinstead shared. “Our intelligent control system will monitor the battery depth of discharge (DOD) and control temperature to ensure optimum battery life. If we utilize our Level 2, 15-kW, on-board charger and if the fleet facility’s grid supports that power, we can fully charge the vehicle after a full day’s use in under eight hours. Plugging in the vehicle at the end of the day will ensure the battery is ‘topped off’ for the next day.”
The Zeus trucks are designed for easy access to charging infrastructure as well.
“The Zeus truck will interface with standard charging units from any number of suppliers,” Grinstead shared. “We offer an on-board Level 2, 15 kW liquid cooled charger and we interface effectively with DC fast charge options. We have other options for higher power on-board charging power when needed to meet customer specifications.”
A few days later, Volvo Construction Equipment announced its prototype ZEUX© LX03 concept wheel loader, which President Melker Jernberg described this way: “It’s even more cool because it’s not a gadget, it is for real. It’s in the R&D phase and is not commercially available, but still, we will show the first fully autonomous, fully battery electric, and self-learning wheel loader concept. It has a brain to make decisions, to perform tasks and interact with humans.”
Setting aside my Luddite fears of artificial intelligence uprisings, I was pleased to hear a leader of the R&D team speak not only of the system learning from its mistakes and history, but also speaking of
*I am not comfortable trying to summarize the different sub-chemistries available for the Li-ion batteries and the temperature ranges in which each is designed to perform best versus the leaching potential when batteries are disposed of. I’ll leave that rabbit hole to the reader.
the elements a contractor/producer cares about: more tons. Joakim Unnebäck, specialist for machine applications and concepts, shared: “First of all, we are able to carry the material closer to the front axle and do the vertical lift...With that we increase the capacity significantly of the machine. Also do a lot more efficient bucket fill with the machine utilizing the ZEUX function.”
The introduction to the LX03 didn’t provide information on battery capacity, staying power, and so on, but there are specs available for the company’s now commercially available, all-electric wheel loaders— the L20 and L25. Both are listed as operating in temperatures from 14 to 104 degrees F (–10 to 40 degrees C). The spec sheet also says, for a typical stop-start working pattern, the loaders should complete an eight-hour workday on a single charge; the battery also recovers energy during driving conditions while using the brake functions. This regenerative braking energy capture is a common—and important—theme to watch for in the EOHV conversation.
I turned to the May 17, 2021, Volvo CE blog post, “Electric Construction Equipment Vs. Diesel Performance Comparisons” for additional answers. I found: “A final difference between the L25 electric wheel loader models is that in North America, we’re not initially offering a high-speed version of the electric loader in order to better maintain the battery during a full workday. The maximum speed of the electric L25 wheel loader is set at 10 mph (16 kph). The good news is that for most applications, high speed isn’t required. It’s mainly necessary if you have an application where you need to drive from jobsite to jobsite without hauling the machine.”
A source I’m protecting shared a particular OEM’s anecdotes that included driving an electric haul truck up a hill, maxing out its battery and requiring recharging prior to working a shift. This demonstrates, to my mind, the necessity for attention to charging infrastructure, regenerative power on-board, “quick” battery swapping, or other accommodations for heavy equipment working in severe operating conditions.
We’re telling crews they can work longer because the work is quieter, but the battery only lasts five to eight hours under the conditions of our industry. I’m not making up those numbers. In a Jan. 29, 2019, article titled “Caterpillar unveils an all-electric 26-ton excavator with a giant 300kWh battery pack,” Electrek’s Fred Lambert reported, “They believe that the battery capacity can enable between five and seven hours of use before needing to charge, which can be done overnight.” We’ll dive into charging and the infrastructure for that shortly.
But let’s look at more equipment before we look into how to recharge it.
Tangentially related to EOHV, Curry Supply Co., Martinsburg, Pennsylvania, offers a crash attenuator truck featuring the TrafFix Scorpion TMA Model TL-3 attenuator (and Wanco arrow board), which plug into vocational trucks. Jeff Shaw, VP of sales and marketing, explained the Curry Supply equipment is mounted on the electric vehicle chassis. He estimated the crash attenuator and solar panel boards can run three days on their own solar battery power and plug into the BEV for support. “Our equipment doesn’t draw much power from the chassis,” he said. If the workers fail to recharge the arrow board battery for whatever reason prior to arrival on a jobsite, plugging it into the BEV to recharge the battery doesn’t pose a heavy load for the truck.
John Deere is currently testing its 310L backhoe loader with E-Power in the field. The company stated: “As a commitment to the next generation of backhoe loaders, John Deere has begun joint-testing its first-ever battery electric backhoe loader with National Grid, an electricity, natural gas and clean energy delivery company. Aimed at lowering its carbon footprint and promoting sustainability, the Deere E-Power backhoe loader targets the performance of a 100-horsepower 310L diesel-powered machine, but with zero tailpipe emissions.” The design is intended to provide lower daily operating costs, lower jobsite noise, enhanced machine reliability, and zero tailpipe emissions.
Wirtgen Group, Antioch, Tennessee, currently offers a hybrid of a different nature, and its intriguing asphalt compactor deserves more than a footnote in this discussion of clever energy use. The HAMM HD+ 90i PH tandem roller combines a conventional ICE with a hydraulic accumulator, letting the diesel engine of 55.4 kW output handle the base load of the 9-metric-ton roller. Then the hydraulic system kicks in to handle peak loads.
The smaller diesel engine meets Tier 4 standards, meaning it does not require an SCR catalytic converter, requires no DEF, is a quieter engine for the operator, and so on. Hamm Applications Support Manager Tim Kowalski said the HD+ 90i PH includes two hydraulic pressure tanks; the hydraulic accumulators and hydraulic pressure start up the vibration when it’s needed, which means less horsepower is drawn from the motor. The system regenerates the pressure during driving. He explained that municipalities can get “green” points or LEED credits for using lower emission equipment such as the HD+ 90i PH.
Sweeper OEMs are also looking at ways to reduce emissions on job sites. M-B Companies Inc., Chilton, Ohio, offers the Schmidt eSwingo 200+ compact electric sweeper, which the company claims can operate up to 10 hours without recharging, and then recharges in four hours. The machine specs list the battery capacity at 75 kWh, but no one got back to me on battery type.
Caterpillar celebrated a worldwide release of the Cat® R1700 XE underground battery electric LHD at MINExpo 2021 in September. The machine will be commercially available in select markets starting in the first quarter of 2022. The electric LHD vehicle features a “thermally stable Lithium Iron Phosphate battery system” to offer “15 tonnes (33,069 pounds), 18 kph (11.2 mph) fully loaded top speed and 2.5 hours of aggressive run time between charges.”
To assist with charging, Cat also introduced the Cat MEC500 mobile equipment charger during MINExpo. I think this boxy-looking device could be a game-changer. Here’s what I know: “When charging the R1700 XE, the mobile charger immediately recognizes the loader, and all charging functions can be managed from the keypad at the MEC500 or LHD. Allowing for constant communication between the charger
Some Abbreviations of Note
BEV = Battery Electric Vehicle DOD = Depth of Discharge EOHV = Electric Off-highway Vehicle EV = Electric Vehicle HEV = Hybrid Electric Vehicle ICE = Internal Combustion Engine kWh = Kilowatt hour LCO = Lithium Oxide Cobalt (a battery chemistry) LFP = Lithium Iron Phosphate (a battery chemistry) Li-ion = Lithium-ion MPGe = Miles per Gallon Equivalent NMC = Lithium Nickel Manganese Cobalt Oxide (a battery chemistry) PHEV = Plug-in-hybrid Electric Vehicle SCR = Selective Catalytic Reduction SLA = Sealed Lead Acid (a battery chemistry)
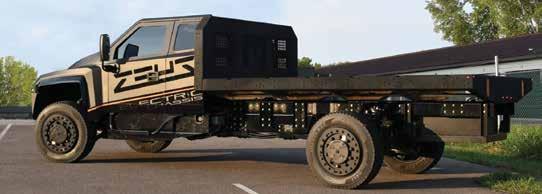
The non-exclusive collaboration agreement between Zeus Electric Chassis Inc. and EAVX announced October 2021 will focus on integration of the JB Poindexter & Co (JBPCO) commercial truck bodies, utility truck bodies, and vehicle cargo management systems with the Zeus Power Platform. Zeus offers a fully configurable class 4-6 all-electric vocational work truck cab-chassis. The core of their business model is to align with market leading vocational work truck body manufacturers and enable them to bring highly effective EV solutions to industry fleets. “As EAVX works with the most advanced alternative energy chassis producers, having a partner like Zeus is beneficial, with their holistic approach to integration of systems between the cab-chassis and the body,” said EAVX chief operating officer and general manager, Mark Hope. “Zeus will enable us to demonstrate innovative severe-duty EV work truck solutions in 2022 with plans for commercialized units.”
and the R1700 XE, the battery-powered vehicle management system dictates the exact amount of charge needed throughout the cycle, optimizing battery longevity.” The press release says this mobile unit can deliver a charge to the LHD in less than 30 minutes; if two units are connected in parallel, the charge time is less than 20 minutes.
It would be a boon to the industry if Cat’s mobile charging unit can be “taught” to charge other Caterpillar EOHVs and/or other OEMs’ equipment, because it is designed to protect the battery from overcharging and the degradation that comes with such practices. The team at Zeus has already “taught” its batteries how to perform: “The battery efficiency does not change from hour one to hour eight if you size the capacity and power output properly up front,” Grinstead shared. “The battery capacity for the Zeus Power Platform™ is configurable to meet the demands of the job. We first understand requirements for desired range and energy demand for all auxiliary and work functions over an eight-hour day (as an example). In addition, we thermal manage the battery packs, keeping them in their optimum temperature range for performance and life.”
CHARGING INFRASTRUCTURE
So far, we’re talking about charging heavy equipment at the shop or in the quarry. And that makes sense, given the nature of asphalt production and paving. In the EV conversation, consumers need a way to measure and understand energy consumption.
Andrew Ganz shared in his article, “Your complete guide to MPGe, the electric equivalent of miles per gallon,” for Kelley Blue Book, Sept. 8, 2021, that the Environmental Protection Agency (EPA) developed the MPGe to offer a comparable unit of measure for an electric car’s energy consumption to a traditional car’s. “When the EPA devised MPGe in the early 2000s, the government agency calculated that 33.7 kilowatt-hours (kWh) of electricity is comparable to a gallon of fuel in terms of its energy content,” Ganz wrote.
The example we’ll follow is, “a car that uses 33.7 kWh of electricity to travel 100 miles rates 100 MPGe.” What Ganz pointed out, and what we’ll look at next in terms of electric equipment, is “MPGe cannot offer...a price comparison since the cost of a kWh varies considerably by location.”
Looking at the cost of electricity in a residential setting, we see that the national average August 2021 was 10.42 cents per kWh. You can follow pricing trends day by day and state by state at EnergyBot.com. (Woe to Hawaii where the cost in August was 30.55 cents per kWh.) As experts are quick to point out, the utility company will likely offer a rate plan based on your level of use and/or time of use.
HMA plant owners are familiar with this concept. Electricity used during peak-demand hours will cost more than electricity used during off-peak hours of low demand. It makes sense, then, to work with your utility to determine the best block of hours for recharging EVs, EOHVs and backup batteries.
Let’s say you have a piece of equipment that requires eight hours to recharge. The Volvo CE blog recommended: “To have an optimal charging time for the machines, it’s strongly recommended to have a 240-volt, Level 2 A/C setup—the same as for electric cars. This is because on the L25, for example, charging time would take approximately 24 hours on a common household 120-volt network. We highly recommended customers be prepared with a 240-volt, 32 amp charging infrastructure to accommodate electric Volvo construction equipment.
“As for when to charge, this takes a bit of a change in mindset. These machines can perform on one charge all day during a typical application, like utility work—but if they’re used in harsher environments, it may require a quick charge over lunch to ensure it’s ready to go for the afternoon. It’s important to have the right charging infrastructure available in these types of instances.”
Keep in mind, the runtimes I’ve listed above of eight-hour shifts is no longer based on a solid eight hours after you’ve put the key in the ignition. EOHVs don’t accumulate hours when idle.
From the Volvo CE blog post referenced above, “With diesel construction equipment, operating time is defined by the engine runtime, and a lot of those hours are counted while the machine is idle. With elec-
tric, as soon as the operator stops working (e.g. a landscaper waiting for pipe to be placed in a trench he’s just dug), the motors turn off and no operating hours are accumulated. So when you think about it, jobs over time that can rack up 10,000 hours on a diesel machine might only add 6,000 or 7,000 hours to a comparable electric machine. These saved hours lower operating costs, and in turn lower total cost of ownership.”
It’s also important to have the right battery for the equipment application. In his October 2021 article for Interact Analysis, Senior Research Director Alastair Hayfield wrote, “there is good news on battery pricing for off-highway equipment. Our latest research has found that the industry expects prices to decline at a rate of 7-10% per year out to 2030 as the already evident boom in the electric passenger car market drives down the cost of cells and demand for off-highway vehicles increases.”
Hayfield’s article, “Will Automotive Help Off-Highway Slash the Price of Electrified Components?,” showed a clear path to reduced battery costs due to economies of scale. It’s the concept of buying in bulk to get a better deal and he posits it will work for battery components, traction inverters for heavy machinery, and, to a lesser extent, some motors. “Larger motors used in heavy equipment such as big excavators offer the most scope for price declines,” he explained in his article. The concept is sound. The more OEMs can purchase/source their batteries, inverters, and motors from “cheaper and better” established experts, the better the pricing will be.
POWER UP, OFF, ON
As Ganz shared in his Kelley Blue Book article, “pulling 33.7 kWh of electricity from the grid in a place dependent on coal power is not quite the same as using wind power.”
Whether he realized it or not, Ganz made a critical point that the BEV discussion needs to incorporate.
“You’re saving the planet at your immediate point in time,” Kowalski said of the Li-ion battery. “But what happened before that point and what’s happening in the near future because of this product?”
If producers and contractors are comfortable with advances toward battery sustainability and incorporate the charging infrastructure necessary to keep equipment at-the-ready, what landmines await? Will EOHVs be ready to go to work on a muggy summer morning if the power grid became overtaxed and failed during the night?
Diesel Technology Forum wrote Oct. 19, 2021, on its Policy Insider blog that “[t]he best insurance policy against electrical grid supply disruptions is having your own backup electrical supply, such as a diesel generator. Data centers, residence owners, manufacturing and healthcare facilities, and critical government services have all invested in diesel backup generators as insurance to protect against economic and other losses that routinely occur from grid instability.” The Forum’s executive director, Allen Schaeffer, Frederick, Maryland, addressed consumer confidence in diesel backup systems considering power companies’ failures. Check out his guest commentary here.
In addition to the re-growing BEV market post-COVID, the diesel engine is seeing growth as we head into 2022 thanks to environmentally friendly refinements. The Diesel Technology Forum reported in late October 2021 that the machines and equipment used to build and maintain our infrastructure have been critical during the pandemic.
At its Policy Insider blog, the Forum wrote: “Most of these machines and equipment are powered by diesel and are all expecting growth in 2021 with sales of earthmoving equipment projected to be up 20 percent, material handling equipment up 30 percent and agricultural equipment up 10 percent. Tremendous investment in compact construction equipment in 2020 drove sales up 10 percent, sustaining the equipment sector that saw drop offs in other larger machine categories. In the ag sector, sales of tractors under 40 hp was higher in 2020 and is expected to level out in 2021. Future drivers include the overall state of the economy, federal spending and the potential for investment from the infrastructure bill now in Congress. (Data source: yengstassociates.com)”
To wrap this all up, I feel as if I’ve thrown everything but the kitchen sink into this discussion. I don’t want readers to leave the piece with a negative view of EOHVs; I think anything our industry can do to alleviate noise and air pollution, or further reduce GHGs is a step in the right direction. EOHVs are a step in the right direction.
What I’d like to see is the growth of Hayfield’s economies of scale for safely-sourced battery materials. I’d like to see OEMs demanding excellence in performance from long-lived battery cell packs so producers and contractors can have the lengthy, quiet, fume-free shifts of heightened productivity that our industry needs to produce the tons and pavements for a tax base that’s paying attention.
Charging Infrastructure
The Florida Department of Transportation hosted an Electric Vehicle Workshop Oct. 21 in which multiple stakeholders discussed private heavy-duty fleets, long-haul trucks, construction vehicles, and other vehicles that would place charging demands on the state’s highway system. Charging while driving with in-road wireless charging using inductive loop technology would require electric vehicles (EVs) to have on-board equipment for this purpose, but is on the DOT’s radar now. Extreme Fast Charging (XFC) for heavy-duty vehicles, those requiring >150kW support, will get their own dedicated charging network under the plans being considered.
Trucks traveling to and from work sites would hardly benefit from this technology, but something a haul truck driver might benefit from, if he or she has not planned ahead, is having a pull-off area where the construction vehicle can recharge before traveling back to the plant. Track with me here. While no paving foreman wants to see a haul truck driver stop along the route for any reason, if electric haul trucks join the fleet, there could be a propensity for drivers to forget proper charging protocol.
The American Trucking Association’s Law Enforcement Advisory Board’s (LEAB) mission is to strengthen relationships between the trucking industry and law enforcement organizations across the country. To that end, safety, education and compliance take precedent when LEAB identifies and prioritizes industry issues. For example, LEAB invests resources and combined member expertise to address the industry need to increase truck parking capacity and ensure driver safety at rest stops.
Fred Fakkema, vice president of safety and compliance at Zonar and vice chair of LEAB added, “In addition to LEAB’s existing efforts to increase awareness of this safety issue, infrastructure investments are being made at the Federal level in the proposed Truck Parking Safety Improvement Act. We aim to help prioritize investments and ensure that they don’t supersede or compete with the current dire needs of the industry. However, investments in EV charging stations for cars and trucks are also highlighted in proposed infrastructure investments and are certainly a need as fleets adopt more electric vehicles. As we consider improvements to infrastructure, Federal legislation should aim to find dual use for rest stops, with more EV charging stations for commercial vehicles at these pull off areas. This will not only improve safety on the roads by allowing truck drivers to take necessary rest stops to avoid driver fatigue, but it will also support EV infrastructure and the innovations/advancement in trucking technology.”