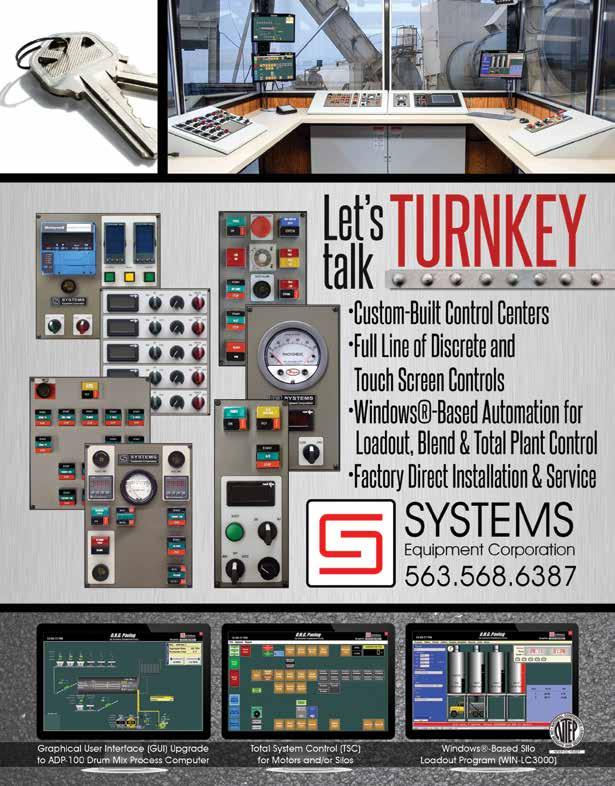
4 minute read
Overcome Software Integration Challenges
IIn today’s market we have more choices than ever when it comes to purchasing decisions. While not the primary focus of many paving companies, considering what software packages to use should be a top decision. There seem to be two general approaches in the market from software providers—the “one stop shop” or the “hub and spoke model.”
ONE STOP SHOP
A software package that can handle everything has certain attractions. Having the employees of the company only need to understand how to use one system creates significant economies of scale. Project managers can trust real time feedback in the system as being accurate and complete information with no concerns of missing data.
Accounting is often the primary driver of choosing the main Enterprise Resource Planning (ERP). In construction, many employees need to have access to the ERP for various reasons. For example, project managers, project executives or project administrators all need access to gain information as to the status of their projects on a daily basis. Estimating and job costing are integral to a paving company running efficiently. Some ERPs have estimating, job costing, payroll and accounting integrated. These fully integrated one-stop-shop models allow for all users to log into one system and not have to piecemeal information together from multiple software packages.
Ensuring a “clean” handoff of information from estimating to job costing is essential. A best practice is to estimate a job the same way the company charges costs to a job. This allows for the team to conduct a post close job review where the original estimate is compared to the final results. If certain costs are used in the estimate but not actually charged to the job, the project results will be skewed by those factors. For instance, if an equipment charge is used as part of the estimate, but not part of the actual job cost, then the project should come in more profitable than the original estimate.
Having an integrated ERP that has both estimating and job costing allows for a better chance that the contractor will have a consistent approach to job costing and estimating. When using multiple software products, the estimate is done in one software, transferred to the accounting software and, finally, the field reports in a third software.
Asphalt plants have similar challenges in multiple software products. Plant controls and plant loadout software packages can come from different software providers. Having a consistent software among both platforms has its benefits, however certain companies excel at plant controls and others excel at plant loadout. Understanding how seamless it is to get the information from the plant loadout to the accounting ERP can play a critical role in a company’s decision on what software to use for the loadout side.
It is even more critical for the plant operator that the plant controls and loadout software integrate with each other. For instance, if the loadout system doesn’t communicate with the operations the tonnage in each silo count could get off, and that could lead the operator to make mistakes and either have an empty silo or an overfilled silo.
Human resources information systems (HRIS) are also considerations for tie into the ERP. Does the system have tracking for things like payroll, benefits, PTO accruals, employment application monitoring, etc. A true HRIS can be robust and certain ERPs may have some of the capabilities of the HRIS platform; however, an HRIS developed specifically for HR commonly has a much deeper bench of tools for tracking.
HUB AND SPOKE
There are several benefits of the hub and spoke model; however, one major drawback can be data redundancy. Maintaining multiple software packages creates the need to have “unique identification keys” throughout the packages. For instance, to have the plant loadout software track tickets, that information contains a customer identification number; it may not be what the accounting team uses for the billing software. The information is exported from the loadout system and into the accounting ERP. Both systems need to use the same customer ID number to have a match of data and ensure the information from the loadout software makes it accurately to the accounting ERP. When new customers are added, they need to be set up in both systems. In a fully integrated one stop shop scenario, the customer information is entered one time and updated and tracked throughout all systems ensuring consistency in the information.
For the hub and spoke model, when information is taken from the spoke software and sent back to the hub, is it a live connection or a static connection? If a company uses a software in the field to track payroll, equipment hours and cost code information, how does that information make it back to the accounting ERP? Is there a live connection that can identify all changes and import that information to the accounting ERP? Does it require a static (point in time) export and import of information and if so, what happens when information is changed in the field software after the import? Does the company just accept the information mismatch at that point or is there a way to efficiently go back and validate all the data to ensure there is no mismatch?
These concepts can be far reaching and span across many different software platforms for consideration. A general recommendation would be for all data to end up in one centralized location, regardless of software model used, to allow for efficiencies in internal and external reporting.
– BY SEAN RIZER
Sean Rizer is the CFO for Harding Group, Indianapolis, Indiana, which performs asphalt services, supplies hot-mix asphalt and provides dump truck transportation. Prior to joining Harding Group, Rizer spent over 10 years in public accounting, providing operational and transactional consulting. He graduated from Valparaiso University with a bachelor’s degree in both accounting and finance.