
6 minute read
GTR in SMA Makes Missouri Job Special
Here the N.B. West crew has closed down one ramp for nighttime mill and fill work on I-44 going over the Meramec River Bridge. Photo courtesy of N.B. West personnel
BY SANDY LENDER
For a single-lift, mill and fill project on Interstate 44 (I-44) during 2020, the team at N.B. West Contracting, Pacific, Missouri, made great use of the Missouri Department of Transportation’s (MoDOT) performance job special provision (JSP). The state didn’t exactly have a balanced mix design (BMD) spec, per se, at the time, but used the performance JSP to allow contractors to influence multiple facets of a mix—achieving cracking and rut-resistance characteristics and meeting volumetric specs during design and production. To share their process and success incorporating ground tire rubber (GTR) in a stone mastic asphalt (SMA) design, Quality Control Manager Joe Schroer, P.E., and General Manager Steve Jackson, P.E., discussed the project.
Schroer had worked with recycled materials in roadways at MoDOT before joining the N.B. West team in 2014, thus he is wellversed in the department’s design process and performance goals. He spoke of the JSP allowing GTR for the I-44 project bringing new technology to the table, which is in accordance with the Federal Highway Administration’s (FHWA) Every Day Counts program. N.B. West incorporated Elastiko® ECR, an engineered crumb rubber product from Asphalt Plus, Barrington, Illinois.
“I had suggested the idea of using a GTR process to enhance the performance of the SMA after visiting the Asphalt Plus and Liberty Tire booths at the 2019 World of Asphalt,” Schroer explained. “I was interested in the dry process of adding the GTR due to ease of adding the product and it not requiring the blending tank and agitation generally associated with GTR use in the past. Plus, only one binder grade would be required to fill multiple roles at the plant.”
The dry process removes terminal blending and multiple liquid storage tanks from the equation. The Asphalt Plus blog explains that a chemically-engineered crumb rubber product is fed into the plant—like a fine aggregate—at the production stage. The heated AC then reacts with the crumb rubber product during mixing, storage and transport to the paving site.
They produced the mix at their new Astec portable Double Barrel™ with V-pack™ at its St. Clair location. Damon Feldman was the plant operator who executed production while implementing a performance job special provision. The team ran Hamburg Wheel Tracker tests and
BUILT TO CONNECT
Efficiency and Productivity
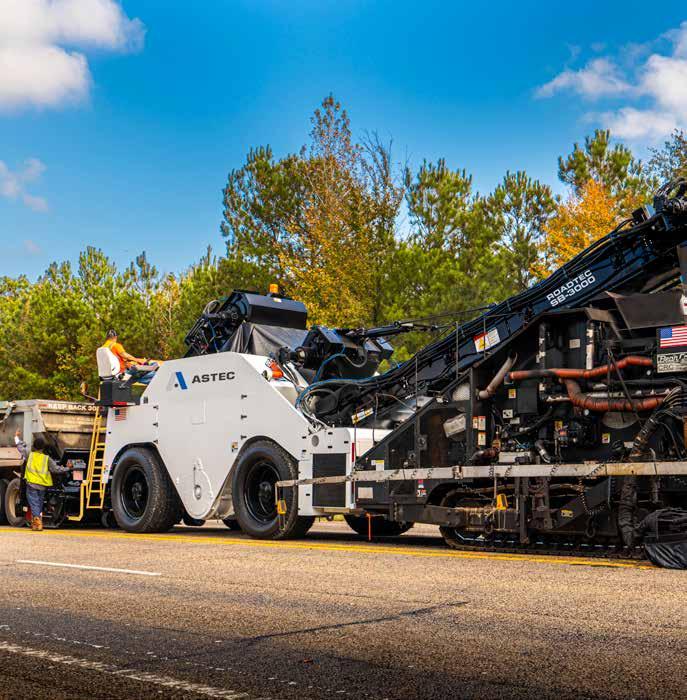
Designed with safety and operator comfort in mind, the Shuttle Buggy® SB-3000 material transfer vehicle features adaptive cruise control, bright LED lighting, four-wheel steering for easy transport and ground-level maintenance access for added convenience. Operators can rely on clear sightlines and the ground operator is safely protected inside the structure of the machine. The Roadtec SB3000 is the perfect blend of traditional craftsmanship and modern technology.
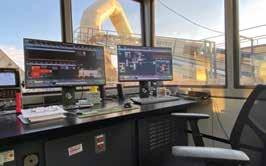
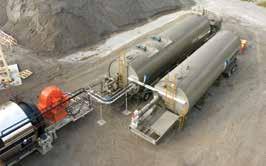
LEFT: N.B. West’s portable plant is rated at 400 tons per hour with up to 50 percent recycled asphalt pavement (RAP). Photo courtesy of N.B. West personnel. RIGHT: This example of the portable heli-tank from Astec Industries, Chattanooga, Tennessee, seen in the background of this picture, offers producers a way to “split” a larger tank to hold two liquid AC products. You can see the motors—the green cylinders—for the agitators atop the two chambers. The tank in the foreground is for fuel. Photo courtesy of Astec
Indirect Tensile Cracking Test at Intermediate Temperature (IDEAL-CT) tests to field-evaluate the mixes during production.
“We are implementing performance specifications/balanced mix design in Missouri,” Jackson explained. “We wanted to use the performance specifications, Hamburg and IDEAL-CT on this project. We thought that the GTR would provide a benefit on the crack resistance and we knew through years of performance that the SMA mixes wouldn’t rut. The challenge was that we didn’t have any IDEAL-CT criteria established with the MoDOT performance specification for SMA.”
The proactive company is a problem-solver and offered a solution. “We proposed some values to use for this project and the department accepted them,” Jackson said. “MoDOT didn’t want to take a huge risk with the SMA mix on an interstate, so we used a standard SMA mix, including cellulose fibers, with the GTR. The next step would be to see if we could maintain the same performance and optimize the mix, maybe by removing the cellulose fibers to make the mix a better value for MoDOT.”
Schroer discussed the testing parameters.
“We followed testing protocols for the mixture using specimens with a target air void content of 7.0%. Due to the SMA mixture having interconnected air voids at that level, it was difficult to hit the target void level without using vacuum sealing on the specimens. In hind-sight, we would promote using a target void level of 6.0% air voids for SMA as in AASHTO T283 for moisture susceptibility.
“The increased density is an FHWA push from Every Day Counts but didn’t apply to the SMA because MoDOT determined it already has a 94% of Gmm minimum density requirement and 95% density.”
“MoDOT had developed performance-based specifications for surface Superpave mixtures, which did not include SMA. Through our testing results and results of MoDOT and other contractors, cracking limits were developed using IDEAL-CT for SMA by comparing to previously acceptable limits using the Illinois Flexibility Index Test, I-FIT. The revised JSP was the basis for a Value Engineering proposal to allow the dry-process GTR mixture modification. The use of performance testing specifications permits use of GTR to modify or enhance an asphalt mixture’s performance without extensively
DATA FROM PRODUCTION SAMPLES:
Mix Type Date Sampled Tonnage CT Index
Hamburg Rutting
PG64-22 + GTR 20-Aug 0-5000 220 6.2 PG64-22 + GTR 31-Aug 5000-10000 392 5.1 PG64-22 + GTR 3-Sep 10000-15000 742 8.3 PG64-22 + GTR 21-Sep 15000-20000 587 7.6 PG64-22 + GTR 23-Sep 20000-25000 590 8.9 PG64-22 + GTR 25-Sep 25000-30000 599 7.7 PG64-22 + GTR 1-Oct 30000-35000 741 9.3
testing binder blends and inferring how the GTR will perform in the mix based on the binder tests.”
N.B. West’s plant includes a 30,000-gallon liquid asphalt cement (AC) tank, which Jackson explained can be split into two 15,000-gallon tanks. “The second benefit was that we could use the same binder for the SP 19.0-mm mix and the 12.5-mm SMA mix by using GTR. Using a dry process GTR allowed us to not have to empty out the AC tank every time that we need to switch mixes,” Jackson said.
Schroer explained the project incorporated revisions that weren’t previously part of MoDOT’s performance JSP. This introduced a “balance” to the design. “The balance part of our design process was that we were able to improve the cracking characteristics of the mix while maintaining a rut-resistant mix. The mixture still had to meet all the volumetric controls during design and production of the mixture.”
Not only did the N.B. West team offer MoDOT a well-designed mix, it also lowered environmental impact with both materials and resources. “By not using a highly polymerized AC, we were able to use a lower storage temperature,” Jackson said. “This allowed us to conserve fuel and cut our emissions from the asphalt heater.”
“Every one of us that has purchased new tires has seen the environmental recovery fee for the disposal of our old tires and wondered if they ever did anything with the tires,” Jackson said. “This project showed us that we could reuse the tires and provide a substantial benefit in pavement performance.”
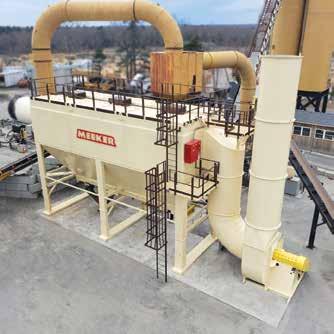
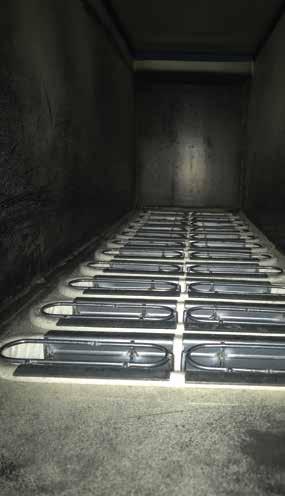
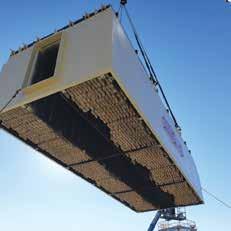