
7 minute read
Alternatives Exist to Source Parts
Here an employee of Stansteel works in the machine shop to perfect a part for a trunnion. Photo courtesy of Hotmix Parts & Service
BY SANDY LENDER
AAt press time, many producers and contractors in North America were gearing up for winter equipment repair. Typically, this is the time of year when seasonal maintenance and planned upgrades get underway. For the 2022 season, producers and contractors alike had to plan out their needs in advance or face the possibility of postponing repairs, upgrades, and maintenance until parts and components can be available.
In November 2021, Ben Brock, president and CEO of BROCK, Chattanooga, Tennessee, explained: “We are out to mid-May 2022 delivery for components, which we define as cold feed bins and/or systems, conveyors, drums, drags, silos, heaters, tanks, etc. The leading manufacturers are out that far or later. The pending highway bill will only keep things going strong. It’s as good a market for hot-mix asphalt plant equipment as I’ve ever seen in my life.”
“As for parts, we are seeing some disruptions due to the well-reported supply chain issues around the globe,” Brock said. “However, we are doing all we can and, in most cases, we are able to meet customer requirements for delivery. A few purchase parts are out to mid-March delivery now, which is amazing to me.”
He outlined the problem succinctly. Between supply chain woes and the potential for continued trucking and shipping industry worker shortages affecting deliveries of parts and materials, suppliers and vendors are getting creative to ensure they have what contractors need. Kenco Engineering Inc., Roseville, California, is located within 42 miles of a UPS shipping center that misplaced three pallets of product during 2021, according to Brian Handshoe, vice president of operations for Kenco. That’s a problem supply chains, port managers and truck drivers can’t solve. It’s a mistake that Handshoe said is probably a function of his product being loaded under some other business’s pallet of goods. Of course, intent doesn’t take away the sting of lost time and expense getting replacement material.
Kenco Engineering designs and manufactures parts and components, but works under the same physical constraints as the rest of the world. “We’re at a 12-week production sequence right now,” Handshoe stated in November. “If contractors have delayed and not purchased by now, they will not get those parts until spring.”
That’s not to say every part must be manufactured at the Kenco facility. “Some things I’m able to order in bulk,” Handshoe said. “We have options.”
Those options and alternatives are what will save the industry this down season.
“We do a lot of custom work and service a lot of older plants,” Handshoe said.
He shared that some plants still in operation today are models of manufacturers no longer in business. This means producers do not have the option of reaching out to the OEM for parts and service. Enter the innovative practices of companies like BROCK, Kenco and Hotmix Parts & Service of Louisville, Kentucky.
Jeremy Miller, the director of sales for Hotmix Parts & Service, detailed the option of mining existing new production machines or used equipment for parts. He used the example of worn silos. “Silos have enough wear on the cone or sides that you may not want to perform another repair if the structural integrity is posing a safety hazard. The same is true of dryers. We have built a business looking at the machine detailed requirements. We can send an engineer out to check the machine and formulate the right solution to retrofit with proven new parts or recondition or replace. You might find and substitute a used piece of equipment instead of waiting on parts for a structurally deficient component.”
If you don’t have perfect psychic abilities, options to acquire parts in time for season start-up include shopping around. Multiple OEMs and parts suppliers braced for this storm.
“At CWMF, we are now stocking large amounts of inventory,” said CWMF Vice President Travis Mick. “We found this necessary after researching which parts our customers needed most in prior years. Knowing past in-demand parts and components allows
us to create the correct volume in our inventory and have them readily available for our customers (i.e., flights, chain and sprockets, trunnions, etc.). We also have two CNC plasma tables, one of which is dedicated to emergency service parts and production overflow. As parts of this proactive plan, we have also created recommended spare parts packages for customers for key components of items we may not stock.”
Weiler, located in Knoxville, Iowa, has also invested in the infrastructure to fabricate parts on demand. “Weiler gives parts availability the highest priority to most effectively serve our customers,” said Weiler Vice President Bill Hood. “Our strategy starts with providing our dealers with individualized suggested inventory lists based on Weiler equipment within their servicing area. The goal is for the dealer to have parts on the shelf and available to the customer same day. If a part is not available at the dealership, parts orders have priority over machine production in our factory.”
The facilities at the Weiler campus are set up to produce almost all their needed steel components in-house so they can control as much of the manufacturing process from start to finish, Hood explained. “Most recently, we have started building specialty electrical harnesses in-house due to increased lead times and unpredictable delivery dates from suppliers. Weiler has always strived to use common components within and across product lines to allow for lower cost and better availability. We are currently constructing an additional building that will allow us to greatly expand our steel processing capacity. For components that we do not build in house, we continually work with current suppliers to provide timely delivery while exploring new vendors that we can partner with to continue manufacturing the highest quality products and parts.”
Miller shared that the Hotmix Parts & Service shop has pre-ordered extra inventory because the company stocks millions of dollars of parts for different brands, not just its sister company’s Stansteel brand.
Miller said it’s true our industry has a few shortages right now, but we also have alternatives. “Other proven parts can offer the same performance. You may not be able to pull a part number out of the book. You may need to measure and let us machine something or swap something that works even better. There have been metallurgy improvements that make this a responsible option. With just a minimal amount of information, we can provide the sprocket, trunnion or the chain be-
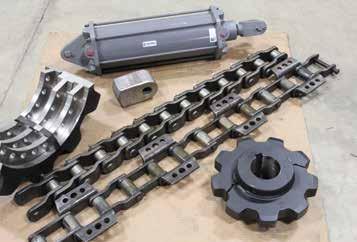
CWMF now stocks large amounts of inventory based on its research of which parts customers have needed most in past off-seasons. Photo courtesy of CWMF
cause we’ve done it hundreds of times. And we stock the interchangeable parts.”
Along with metallurgy improvements, companies like Kenco Engineering have made strides in strengthening parts and components. Kenco’s tungsten carbide impregnated (TCI) technology is designed to offer longer wear life to components. We all understand the benefits behind longer wear life for wheel loader buckets, auger discs, and other parts around heavy equipment.
The concept of switching out a part at the plant or in a piece of paving equipment may make contractors nervous. Even “regular consumers” have been told the best part to put under the hood is a part manufactured by an original car manufacturer so it will fit perfectly and perform at optimum efficiency. During a CASE Construction Equipment live broadcast Nov. 17, experts discussed preparing your equipment for cold weather use and cold weather storage and they reiterated the old mantra that you must use OEM filters and OEM lubricants in OEM equipment.
But is this Gospel?
Consider the competency of parts manufacturers and recognize the need for elements for machines still in service after the OEM has closed its doors. Barber Greene and Ingersoll Rand machines still work on job sites today. Contractors trust the manufacturers of their replacement parts to provide elements that keep equipment in working order.
The team at Hotmix Parts & Service explained, “the manufacturer of the gear reducer you need may no longer be in business. We look at the horsepower and duty rating of the gear reducer and we re-engineer it. We make the new mounting bracket for it and any additional housing required.”
Here’s a quick checklist from Hotmix Parts & Service to help you source your parts in this trying climate: 1. Expand your search beyond the original brand. 2. Check with companies that pre-order extra inventory for any season, especially this one. 3. Double-check federal regulations for your right to repair your equipment with adequate parts. 4. Raid your spare/emergency parts shelf before panicking. 5. Check with companies that have an experienced team and machine shop to accommodate your “less conventional” sizes of parts.
The point is producers and contractors have options available to them when it comes to sourcing parts and components this down season. As you tackle routine maintenance, machine upgrades or surprise repairs, you don’t have to accept the idea that supply chain woes are setting your schedule—thus your ability to bid on highway bill influenced projects—back by months on end. There are options that OEMs and parts suppliers can look into to help you get up and running in a more reasonable timeframe. Explore those options with the vendors willing to help you.