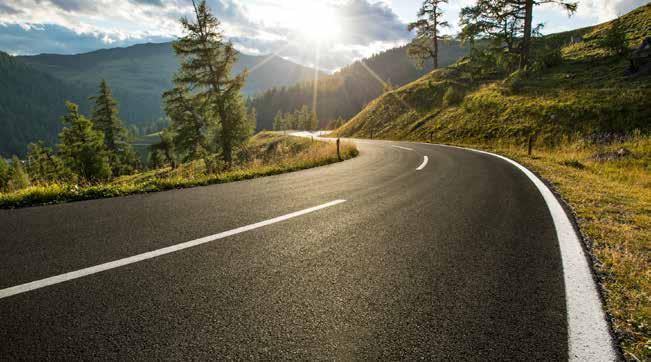
4 minute read
7 Equipment Setup Tips for Sealing Success
BY ASPHALTPRO STAFF
Ensuring that chip sealing and fog sealing equipment is properly set up is key to a quality product. However, according to Scott Shuler of Shuler Consultants LLC, Fort Collins, Colorado, improper equipment setup is quite common.
Shuler is one of the authors behind the Transportation Research Board (TRB) “Guide Specifications for the Construction of Chip Seals, Microsurfacing and Fog Seals” (NCHRP 14-37), alongside R. Gary Hicks of R. Gary Hicks LLC, Chico, California.
During a recent TRB webinar, the pair shared some best practices for setting up your equipment—and your crew—for chip seal and fog seal success.
EQUIPMENT REQUIREMENTS
A chip sealing operation requires a broom, an asphalt distributor, an aggregate spreader and compaction equipment.
The asphalt distributor should be calibrated, accurately control application rate, provide uniform coverage in both transverse and longitudinal directions, and hold a specific temperature. It should also have an adjustable spray bar and correct nozzles to allow for double to triple overlap, Hicks said.
The aggregate spreader should be calibrated, adjust to varying widths, distribute the aggregate uniformly in transverse and longitudinal directions, and deliver the desired application rate using computerized controls.
The job will also require several rollers, Shuler said. “I don’t know how many projects I’ve seen where they only have two or even one roller trying to keep up with that distributor truck and spreader,” he said.
Shuler also said it’s important to wait until 85 percent of the moisture within the chip or fog seal has evaporated before sweeping to ensure the emulsion has enough adhesive power to keep the chips in place. Hicks adds that the broom should be motorized, with plastic bristles and vertical control pressure.
1. TAKE THE EMULSION’S TEMPERATURE.
Emulsion should be around 180 degrees Fahrenheit or above. “If the emulsion is too cold, it will not spray well,” Shuler said.
2. CHECK YOUR NOZZLE SIZE.
It’s important to use the right nozzle for the job. “Various distributor manufacturers indicate what sort of nozzle should be used for various shot rates,” Shuler said. These guidelines may be in the equipment manual, or in some cases, may be mounted directly on the distributor truck itself. It’s also important to ensure nozzles aren’t clogged to prevent uneven application.
3. ENSURE PROPER NOZZLE PLACEMENT.
It’s also important that your nozzles are placed correctly, at an angle between 15 and 30 degrees. The truck often comes with a wrench designed to turn that nozzle to the correct angle. “Very often, the operator of that distributor truck may not know that and uses a crescent wrench or something else and does this by eye,” Shuler said. “That’s possible if you’ve got an experienced operator, but it’s much better to use the wrench that comes with the truck.”
4. ADJUST THE HEIGHT OF THE SPRAY BAR.
If the distributor truck’s spray bar is set too high, you’ll get streaks as a result of overlap. If the bar is set too low, there may be streaks of uncoated pavement between the nozzles. Shuler reminds us that if we’re seeing streaks of any kind, it’s important to stop and make the proper adjustments. The binder should double- or triple-overlap, Hicks added.
5. CHECK YOUR SPRAY RATE.
Some operators may be surprised to learn that they shouldn’t be relying on the gauge on the back of their distributor truck to know how much material they’re spraying. “All that gauge is for is to tell you if you’re empty or not,” Shuler said. “Don’t think you’re measuring gallons with this.”
The only way to tell if a truck has sprayed the correct rate is to dipstick the tank, Shuler said. That’s why every truck comes with a dipstick. “I don’t know how many times the operator didn’t even know there was a dipstick up there,” he added. The operator should dipstick before starting to spray, spray a set area for which the distance and width is known, then dipstick again to determine spray rate.
Because the tank gauge is a ball float style of gauge with a large pointer and an engraved dial, the numbers are often close together which makes it tough to read, said Brian Horner, field sales manager at E.D. Etnyre, Oregon, Illinois.
“The other issue is the pointer itself can be grabbed by anyone and possibly moved,” he said, “so the measuring stick is more accurate and reliable.” Etnyre is currently working on new digital tank gauges that will display the gallons in the tank on the computer screens at the rear and cab.
6. CALIBRATE THE SPREADER.
“A really simple way to tell if the aggregate is spread uniformly is to look at the veil,” Shuler said. If you want to measure the amount of chips, which Shuler recommends, measure the distance and width to get rid of two or three truckloads to get your chip spread rate.
7. USE THE RIGHT NUMBER AND TYPE OF ROLLERS.
“Those chips need to see that roller more than once in order to embed,” Shuler said. He recommends a speed below 3 miles per hour with a rubber-tire roller with equal tires and equal tire pressure.
“Steel does not conform to the chip shape like rubber and tends to crush the chip,” Shuler said. “This changes the shape, size and texture of the chip, all of which are undesirable. Some chips can withstand this abuse, but many cannot.”
Hicks recommends that the first pass be within two minutes of applying the aggregate and that there be at least three complete passes.