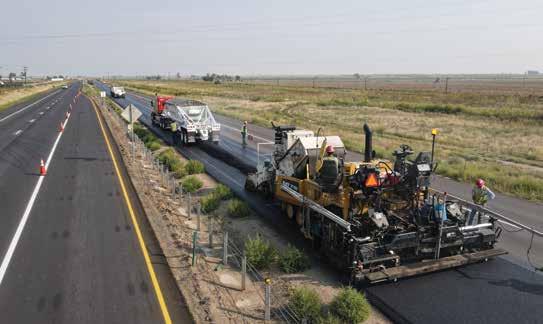
16 minute read
Colorado Puts Experimental Strain-Tolerant Mix to the Test
Known in Colorado as BR-ST (bituminous rich, ST 3/8 minus gradation), this high strain-tolerant mix designed to mitigate cracking through the combination of high polymer binder and specific aggregate structure.
BY SARAH REDOHL
In September 2021, Coulson Excavating Company Inc., Loveland, Colorado, placed an innovative new mix on a 4-mile section of State Highway 85 from Platteville to County Road 22. BR-ST (bituminous rich, ST 3/8 minus gradation) is a high strain-tolerant mix designed to mitigate cracking through the combination of high polymer binder and specific aggregate structure. The mix design has the same binder technology used in reflective crack interlayer (RCI) mixes, only BR-ST is a surface mix.
According to Jeff Weitzel, account manager at Arkema-Road Science, Tulsa, Oklahoma, the Colorado Department of Transportation (CDOT) has used RCI since 2007 but this was the state’s first time using BR-ST.
“CDOT wanted to see how far they could move the threshold for performance of a surface mix,” Weitzel said. “They wanted to see if perhaps [BR-ST] could achieve the same or better performance as RCI followed by Superpave. That’s why they wanted to try this sideby-side comparison in Colorado.”
On the two southbound lanes of U.S. 85, Coulson paved a 1-inch RCI followed by 2.5 inches of SX (12.5 mm) 100 gyration Superpave mix with 70-28 binder. The two northbound lanes were paved with 2.5 inches of SX 75 gyration mix with 70-28 followed by 1.5 inches of BR-ST.
U.S. 85 made for an ideal side-by-side comparison to test out BR-ST’s crack mitigating properties. Several years ago, oil drilling operations for natural gas and crude oil in Weld County increased with the construction of several new wells. As a result, truck traffic in the area increased by 80 percent.
“They needed to find a material that would mitigate cracking and be stable enough to handle the higher traffic loading,” Weitzel said. “That is one of the main reasons why they chose this stretch of roadway for the application.”
Despite severe top-down cracking, general fatigue and several areas requiring patching, the 4-mile stretch of U.S. 85 didn’t have any subgrade failures, said Coulson Excavating Project Manager John Pinello.
“It’s a good road to test this type of mix on,” said Ken Coulson of Coulson Excavating, based on the pavement condition and traffic demands on this stretch of U.S. 85. “CDOT has
done jobs on this road previously using RCI, so that’s nothing new and they’ve held up well.”
Four years ago, Coulson Excavating paved an RCI project on U.S. 85 just south of the BR-ST comparison project that has held up well, after which Arkema-Road Science reached out to the company about the BR-ST mix design it was working on with CDOT and took samples from Coulson Excavating for testing and evaluation.
When Coulson hadn’t heard anything more about the BR-ST mix for several years, he forgot about the experimental mix design until CDOT let the project on U.S. 85. Unbeknownst to Coulson, Arkema-Road Science had continued its work on the new design and its dialogue with CDOT to find an ideal test case.
Coulson Excavating was formed in 1948 by Ken Coulson’s grandfather. The company has two asphalt plants and two crushing spreads running out of its five pits. They do work from north of Denver up to the border with Wyoming, between the west slope and as far east as Nebraska. “Right now, we seem to be in a boom area and there has been an awful lot of work to do,” Coulson said.
THE BACKGROUND OF BR-ST
The idea for such a high strain-tolerant mix originated from the need for a high performance mix for bridge decks in New Jersey and Virginia, Weitzel said. “We got to work testing various aggregate structures and high strain-tolerant binders,” he added. Ultimately, they were able to design a mix that they think combines the flexibility required to minimize cracking while retaining the strength to prevent rutting.
About five years ago, Arkema-Road Science began discussing its new mix concept with CDOT. “They were very interested in learning more about it and investigating the possibility of doing a test section in Colorado,” Weitzel said. Arkema-Road Science worked with CDOT to determine a path forward, submitting the mix design and data from bridge deck mixes placed on the East Coast to CDOT’s materials committee for approval to perform a pilot project. “We started those conversations in 2016. That’s how long it took for this experimental project to come to fruition.”
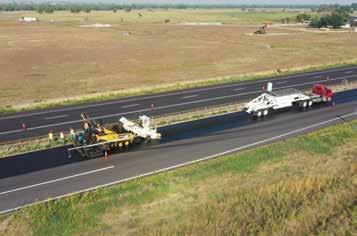
U.S. 85 made for an ideal side-by-side comparison to test out BR-ST’s crack mitigating properties. Several years ago, oil drilling operations for natural gas and crude oil in Weld County increased with the construction of several new wells. As a result, truck traffic in the area increased by 80 percent.
BR-ST contains 18 percent ½-inch rock, 51 percent crusher fines, 30 percent washed crusher fines, and 1 percent hydrated lime, with a binder content of 7 percent.
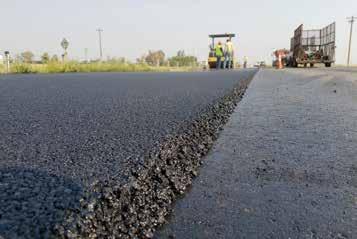
Although the U.S. 85 project was the first time the BR-ST high strain-tolerant mix was used in Colorado, the success of a pilot project performed near Topeka, Kansas, gave the company confidence in its new design. “That project went really well and the state was really impressed with how it went down and the test results it achieved after,” said Mike Longshaw, Arkema-Road Science’s lead field engineer for its RCI and high strain-tolerant mixes.
Throughout 2021, Kansas did five more projects using the same type of mix. For example, a project on U.S. 54 in Butler County, Kansas, will be comparing normal Superpave mix with high strain-tolerant asphalt
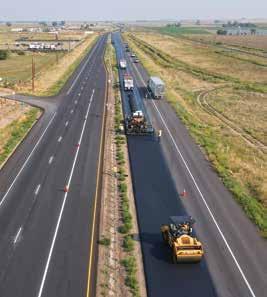
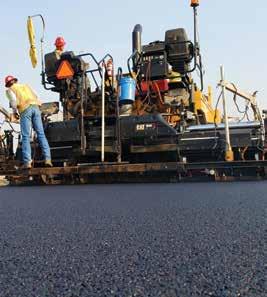
LEFT: In total, the job required 45,600 tons: 30,900 tons of SX 70-28; 5,800 tons of RCI; and 8,900 tons of BR-ST. RIGHT: Coulson Excavating paved the U.S. 85 project with its Caterpillar AP-1000 D and Caterpillar AP-655 C pavers.
mix. “In addition, the test sections will compare different thicknesses of the mixes to determine if the higher quality mix can meet or exceed the performance of the normal mix at a different thickness,” Longshaw said.
“Kansas has been utilizing RCI topped with Superpave for 20 years,” Longshaw said. “They’ve milled off the surface course 10 years after both had been placed to find that the RCI had not experienced any cracking, so they’d leave it in place and pave a new surface course on top.”
It made sense to the state, Longshaw said, to see if it could achieve that same flexibility it’s seeing in RCI mixes in a surface course to eliminate or delay cracking and extend the life of the pavement.
According to Weitzel, Arkema-Road Science anticipates its high strain-tolerant mixes to delay cracking twice as long as normal Superpave mixes. “Superpave mixes are relatively dry, and while they achieved performance in terms of rutting, there have been some problems with cracking,” he said. “Everything will crack eventually, but we anticipate this material will double the life expectancy of the roadway in most cases.”
WHAT MAKES A MIX STRAIN-TOLERANT?
Coulson Excavating produced the BR-ST mix at its Brownwood pit, close to Loveland, Colorado, and a 25-mile haul to the U.S. 85 project. “One reason we chose our Brownwood pit plant to produce the BR-ST mix is that it also produced the RCI mix in the past without any problems,” Pinello said.
However, from a production and paving perspective, Coulson said the mix reminded him more of a finely graded stone mastic asphalt (SMA) than RCI. “The BR-ST looks like SMA,” he said. BR-ST contains 18 percent ½-inch rock, 51 percent crusher fines, 30 percent washed crusher fines, and 1 percent hydrated lime, with a binder content of 7 percent. “BR-ST has a lot of fractured faces in it—about 90 to 95 percent fractures.”
The big difference is in the binder. Weitzel said that the higher binder content, and the resulting temperature sensitivity and stickiness of the mix, is why BR-ST is reminiscent of SMA mixes. “SMAs also contain a lot of crushed aggregate, so there are similarities from that perspective as well,” Longshaw added.
During production, Coulson Excavating found they had to run the mix a bit hotter than usual—320 degrees Fahrenheit, compared to the usual 290 to 300 degrees Fahrenheit—to get the modified PG70-28 binder to mix well.
The company dedicated its Brownwood pit plant to producing only BR-ST mix during that portion of the U.S. 85 job. “It was really the best way to do it with this mix,” Pinello said. “If you were to put this mix up into a silo to switch to another mix, I’m not sure you’d be able to get it out of the silo easily.”
“This is a thicker binder, and when it cools it doesn’t flow through the plant nearly as well,” Longshaw said, stressing the importance of keeping the binder at the correct temperature.
Because the mix was so reminiscent of SMA, and Coulson Excavating has frequently worked with SMA in the past, Pinello said the BR-ST mix didn’t present any other surprises at the plant. “Anything that did take us by surprise, we were able to learn during the control strip,” Coulson said.
CDOT requested the control strip to check the mix properties and establish a rolling pattern for the BR-ST mix. Coulson Excavating paved the strip on the haul road coming into its pit plant.
“Since BR-ST hadn’t been done before in Colorado, we didn’t want to take it out on the road if we didn’t know how it was going to work,” Coulson said. “By paving a control strip, we could resolve any problems before going into full production.”
BINDER SUPPLY SOLUTIONS
“The biggest challenge we faced on this job was making sure our binder was available when we thought we’d need it,” Coulson said. “There were no other projects in the state using the types of binders we needed for the RCI and BR-ST mixes at that time, so our suppliers didn’t have them on hand.”
Coulson Excavating worked closely with its suppliers, Blue Night and Suncorp, on the timeline to receive the binder for its RCI and BR-ST mixes. In the meantime, Coulson Excavating patched several parts of U.S. 85 where the last overlay had experienced some segregation, which required a total of 1,400 tons of asphalt, and performed bridgework along the project.
Subcontractor Alpha Milling Company Inc., Arvada, Colorado, then milled 1 inch off all four lanes of the project and Coulson Excavating paved 2.5 inches of SX 75 on the northbound lanes—the side that would be topped with BR-ST—with its Caterpillar AP-1000 D and Caterpillar AP-655 C pavers.
By then, the binder for the RCI lift on the southbound lanes had arrived. Its crews then paved the 1-inch RCI lift and 2.5 inches of SX 75. By the time the southbound lanes were complete, Arkema-Road Science had furnished Coulson Excavating’s binder suppliers with the modifiers needed for the BR-ST binder. The crew was able to return to the northbound lanes to pave 1.5 inches of BRST just after Labor Day.
In total, the job required 45,600 tons: 30,900 tons of SX 70-28; 5,800 tons of RCI; and 8,900 tons of BR-ST.
Weitzel’s top tip is that contractors bidding these types of projects look at their materials early in order to have ample time to make adjustments as needed. Pinello seconded the importance of ample lead time.
“When you’re working with a brand new mix design, I think it’s important to have four months if not longer to develop the mix design ahead of production,” Pinello said. “It may take a while for the materials engineer to analyze the new mix, and there are many things that could slow the process down.”
In the case of this project, CDOT had a tight specification of 3 mm on the asphalt pavement analyzer rutting test. “There was a lot of work put into meeting that 3 mm rutting spec,” Pinello said.

CLEAR THE AIR AT YOUR ASPHALT PLANT

The Blue Smoke Control system from Butler-Justice, Inc., captures and filters blue smoke from emission points in your plant — with 99.9% overall efficiency. We can incorporate this system into new plants or retrofit your existing plant with minimal modification.

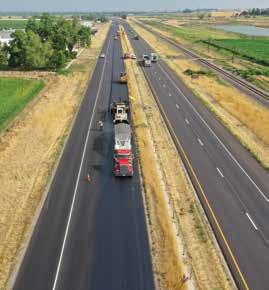
LEFT: Coulson Excavating found that they needed to wait until the material got down to 140 to 150 degrees Fahrenheit before its crew could perform any finish rolling. RIGHT: By the time Coulson Excavating had paved 2.5 inches of SX 75 on the northbound lanes, the binder for the RCI lift on the southbound lanes had arrived. Coulson Excavating worked closely with its suppliers, Blue Night and Suncorp, on the timeline to receive the binder for its RCI and BR-ST mixes.
According to Longshaw, this was made possible by replacing all the rounded sand from the mix with crushed aggregate. “CDOT worked closely with us on any issues and adjustments so we could ultimately meet the tough requirements within their specifications,” he said.
“The CDOT personnel were outstanding on this job,” Pinello said. “The project engineer [Allen Wood] went above and beyond on communication and assisting us with coordination and approvals.”
“[Wood] is a real up-and-comer,” Coulson added. “He’s decisive, he puts the job first, and he does all he can to keep the job moving. Working with him is a big help.”
SOLUTIONS FOR TEMPERATURE-SENSITIVITY
The specifications of the U.S. 85 job required that the temperature be 50 degrees and rising. During the weeks that Coulson’s crew paved this project, the temperatures were around 60 degrees when they began work each morning and reached 85 degrees by the end of the day.
“The BR-ST mix is really sticky, but that isn’t a problem as long as the weather is good,” Coulson said. “It’s very temperature-sensitive and weather-sensitive because of the use of highly modified binder, but also because on this job we were paving such a thin lift.”
When the wind picked up on one day the crew was paving with BR-ST, the mix was sticking in Coulson’s belly-dump trailers and they weren’t hitting their densities so they paused work until conditions improved. Because Coulson had decided to produce mix at a pace that matched the rate it was being paved, they didn’t have mix waiting in the silos when the plant stopped its production until the wind died down.
“I think you’re going to see a shorter paving season with BR-ST compared to other mixes,” Coulson said, suggesting it would probably be feasible to pave BR-ST with a 25-mile haul distance from June through mid-September.
As a result of the mix’s temperature sensitivity, Pinello said, it was imperative that the mix be delivered directly to the job— no stops, no detours. Coulson Excavating uses the tool KeepTrucking to locate its trucks and make sure everyone is sticking to the haul route. “The reliability of our own trucks delivering the mix no doubt made the project go better,” Pinello said.
Another unique aspect of the project was the rolling pattern. “You have to watch the rolling temperatures of BR-ST more closely so you’re not compacting at too high a temperature,” Weitzel said.
Coulson Excavating found that they needed to wait until the material got down to 140 to 150 degrees Fahrenheit before its crew could perform any finish rolling. “Otherwise, the material would move around too much,” Coulson said. “The rollers had to stay back further than they were used to—about 1,000 feet. We learned that on the day we paved the control strip.”
Originally, Coulson thought they would only use static rollers on the BR-ST as they did on the RCI lift, but found on the control strip that they would need some vibratory rollers to reach the specified densities between 92 and 96 percent.
The rolling pattern for the RCI lift was five passes with a large 84-inch Caterpillar CB634 D roller in static mode. The BR-ST lift required
two passes in vibratory mode and two passes in static mode.
“Coulson did a great job on this project,” Longshaw said. “They’re great to work with, they did a great job with laydown, and the road looks great.”
One tip Longshaw recommends for any crew paving with a high strain-tolerant mix is to use a good truck bed release agent so it comes out of the truck more easily. “We also encourage them to use fabric softener in the water on their rollers to keep it from sticking to the drums as they heat up,” Longshaw said. “Anything you can do to keep it from sticking is a good idea.”
Arkema-Road Science plans to draft a construction guideline for the high strain-tolerant surface mix, similar to their existing guide for RCI, Weitzel said.
THE FUTURE OF BR-ST IN COLORADO
Although there are no other BR-ST projects slated in Colorado at this time, the job on U.S. 85 will provide the data CDOT needs to compare the experimental mix against the RCI-and-Superpave combination with which they are familiar.
“We’d love to see CDOT continue to use this mix, but it’s early,” Weitzel said. “I think we will see them evaluate over a period of time and look at its performance against the RCI before moving forward, but my hope is that they will continue to trial it in other areas and expand it to other regions of the state.”
“It’s great to have the performance testing we’ve done in the lab, but it eventually comes down to how it performs in the field,” Longshaw added. “We need to make sure the performance tests from the lab are equivalent to what we see happening in the field. Hopefully it performs well and we’ll be seeing a lot more of it.”
Colorado may be a particularly attractive state for the use of high strain-tolerant mixes with its recent adoption of Buy Clean legislation demanding reduced greenhouse gas (GHG) emissions. “One way to do that is to utilize materials that will extend the life of the pavement,” Weitzel said. He also sees broad potential for high strain-tolerant mixes in the future, particularly as the industry moves towards a balanced mix design approach.
“With balanced mix design on the horizon, I know more states will be looking at the life cycle of a pavement and searching for ways to extend that life,” Weitzel said. “A high strain-tolerant mix could give states the flexibility they need for longer lasting pavements.”
“The project on U.S. 85 was an ideal opportunity to test this experimental mix on a road that was in poor shape,” Longshaw said. “Not only is this project a good candidate to see how these mix designs comparatively perform, but if [BR-ST] can make a roadway in that type of shape last longer, that’s another feather in CDOT’s cap.”
TURN ON THE HEAT: REALIZE THE REWARDS
Lower Your Operating Costs Improve Your Product Quality Reduce Your Maintenance Needs Enjoy Decades of Trouble-Free Efficiency Improve Your Sustainability
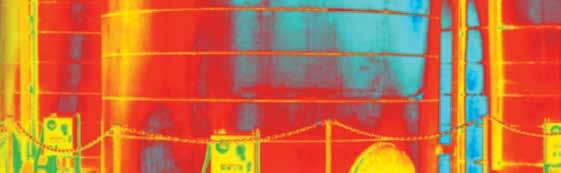
100%-Efficient Lo-Density®
Drywell-style electric heaters for asphalt tanks, hot oil systems, fuel oil preheaters, and distributor trucks.
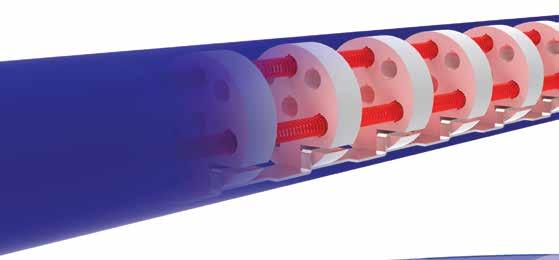
Booth #3119
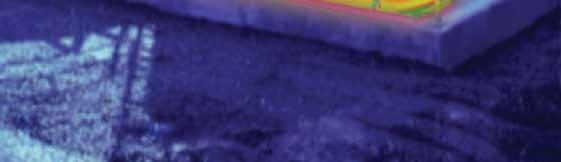
866-682-1582 info@processheating.com
PROCESS HEATING COMPANY www.processheating.com
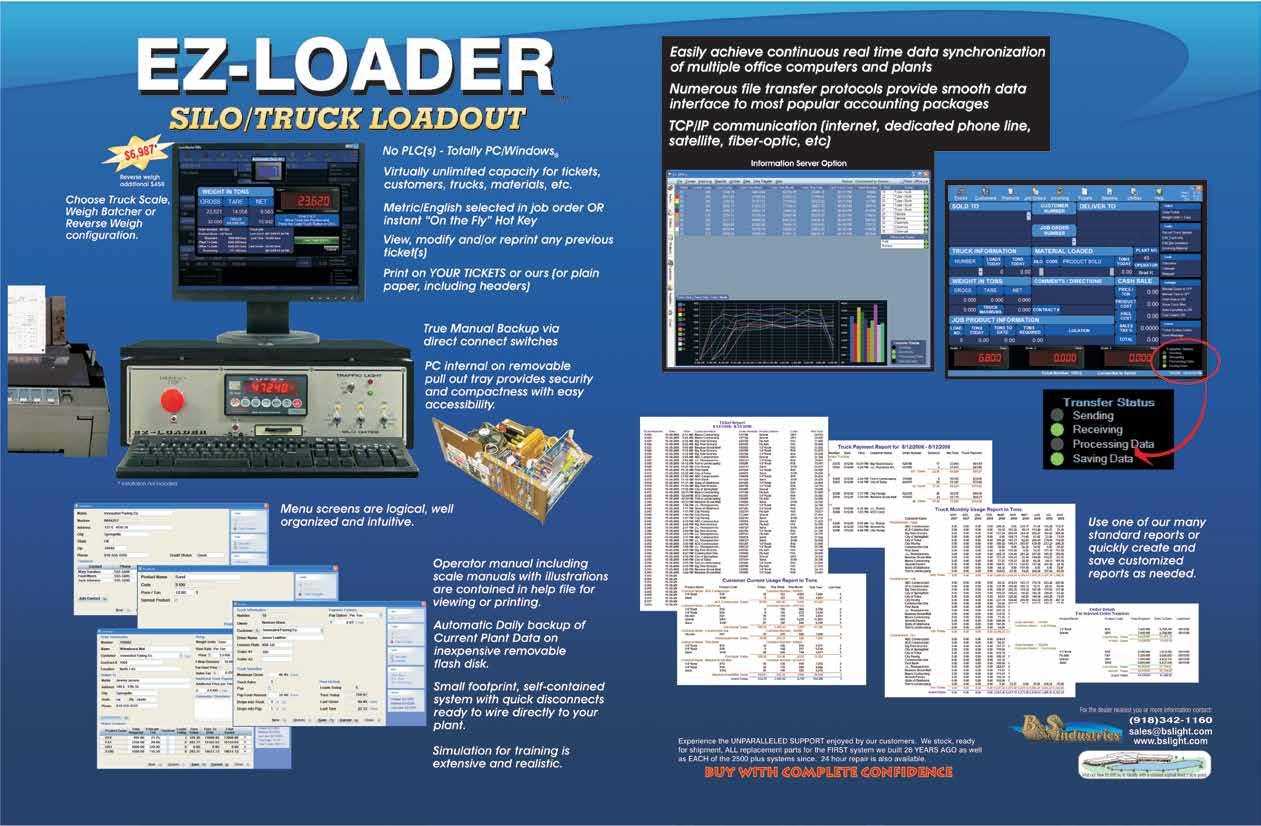
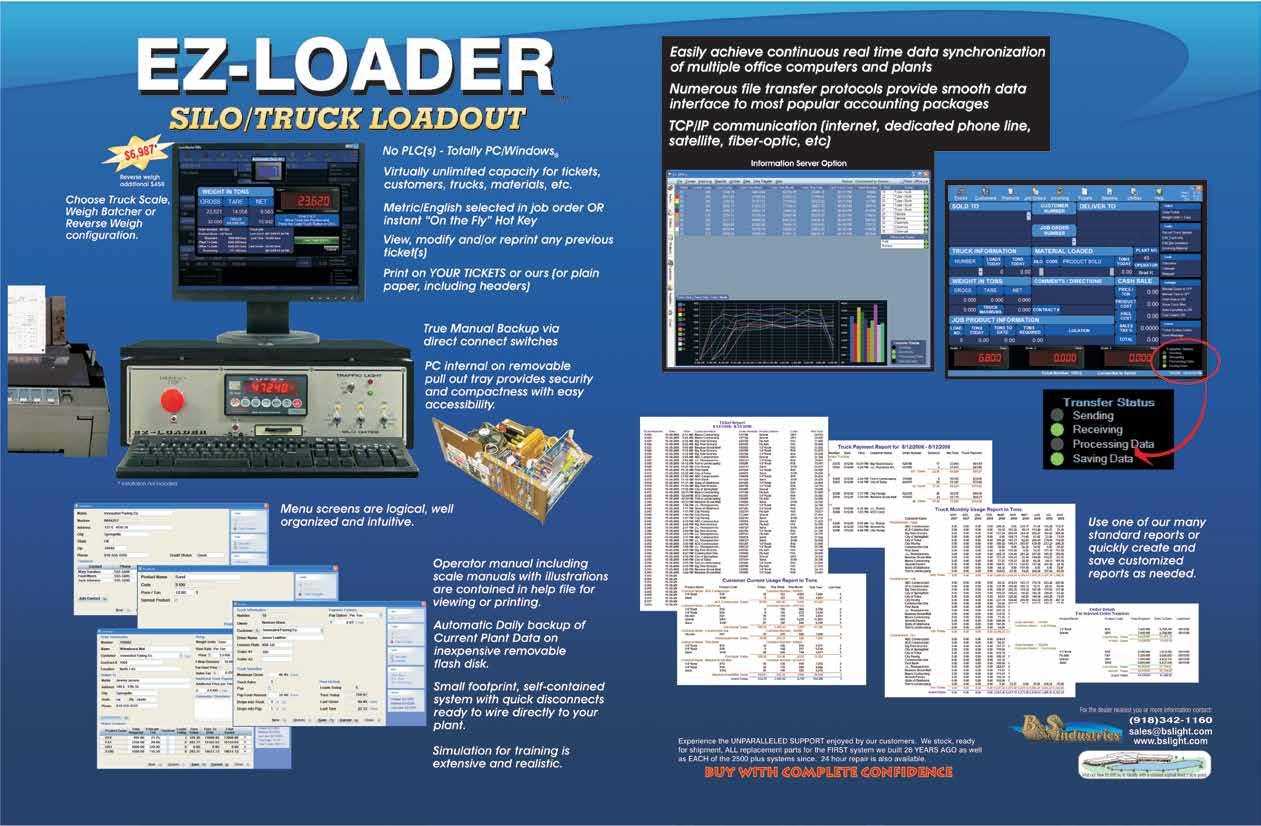